汽车尺寸工程设计RPS设计
什么是RPS
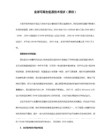
当有两个零件组装时,将标出两个零件相互间的公差,在组装之后,两个坐标系中的一个零件的原点失去其功能,这样新的部件重新只用一个部件型基准坐标来描述,两个参照系中的一个被取消。
在基准点系统中确定基准点时,始终考虑的是尺寸稳定性。首先由同步工程小组尽可能早的决定,主要选择原则有:
l 3-2-1规则
北美和欧洲的厂商定位倾向与实际保持一致,日本厂家的定位是用来研究如何保证零件的质量,而韩国厂家则是通过定位来压迫零件变形,使之达到要求。大众汽车则最终发展成了所要讲的RPS系统。
RPS简单的讲,就是指基准一致性。它是指一种统一的和通用的,并带有相应公差范围的,在空间固定部件的基准体系,要求产品设计,制造和质量保证中使用一样的、共同适用的定位。RPS根据一系列原则,制定一些从开发到制造,检测直至批量装车各环节所有涉及到的人员共同遵循的定位点及其公差要求。
RPS也存在一些问题。简单的讲,它的一些原则,如:确保尺寸稳定性、相对整车坐标等,会引起以下问题:检测不合格的零件装车合格;检测合格的零件,装车不合格。而坐标平行规则,在结构空间设计日趋多样化的今天,会对产品结构、工装结构、工艺工序的设计和优化产生阻碍。
l 坐标平行规则
l 统一性规则
l 尺寸标注规则
此外,基准点还要求选择功能性最强的稳定区。基准点系统的重要作用是减少公差的累积,这可以通过在制造过程中避免基准变换实现。基准点的确定可以通过同步工程小组的协作,在开发的前阶段加以考虑,甚至也可以在概念设计阶段。因为在这一阶段几乎不发生更改成本;在样车试制阶段,基准点定位的变更,就已经可能造成工夹具的变更,从而带来较高成本的浪费。
什么是RPS(REFERENZPUCKTSYSTEM)?(Reference Point System)
关于汽车行业RPS介绍

保障尺寸精度的RPS系统长期以来,大量的尺寸超差给汽车制造企业带来重大的损失:不仅严重影响零件功能的发挥,而且经常导致零件报废使得汽车成本增加。
尺寸偏差大给整车匹配带来的麻烦更大:间隙和平度不合格而且原因的查找又非常困难。
因而保证零件尺寸精度是每一个汽车制造企业所追求的目标。
那么谁是保证零件尺寸精度的主角?人们往往认为这是生产部门和质量保证部门的事情,而开发部门只要完成理论和概念设计就大功告成了。
随着汽车工业技术的进步和业内人士思想观念的转变,零件尺寸精度的保证已不再仅仅是生产部门和质量保证部门的事情,而是要从产品开发阶段就开始考虑了。
RPS系统就是出于这种思想被发明出来并被世界各大汽车公司投入到使用当中。
发明者是率先采用流水线作业而带来世界汽车工业革命的美国福特公司。
在大众公司,RPS系统被制定成公司标准VW01055。
RPS是德语单词Referenzpunktsystem(定位点系统)的缩写。
从A4车开始,没有填写RPS表格的图纸就得不到认可的批准。
由此可见RPS系统的重要地位。
下面从几个方面对RPS系统作以介绍,以便与大家共享。
一 RPS系统的定义和作用RPS.......................................系统就是规定一些从开发到制造、检测直至批量装车各环节所有涉及到的人员共同遵循的定位点及其公差要求............。
在确定这些定位点时必须遵循RPS系统的规则。
RPS系统的作用主要体现在下面三个方面:1.避免了由于基准点的变换造成零件尺寸公差加大。
例如:要在板件上钻孔B和C,这两个孔与其它件上销钉配合,公差越小越好。
零件上还需要钻出孔D,见图1、图2。
下面用两种方式加工:(1)加工时基准点发生变换步骤1 用孔A定位钻出孔B和孔D公差 A…B = +/-0.1A…D = +/-0.1步骤2 用孔D定位钻孔C (这时基准由孔A变为孔D)图 1 加工时基准点发生变换图2 加工时基准不变化公差 D …C = +/-0.1孔B 、孔C 距离公差结果A …B = +/-0.1 A …D = +/-0.1 D …C = +/-0.1B …C = +/-0.3(2) 加工时基准不变化步骤1 用孔A 定位钻出孔B 和孔D公差 A …B = +/-0.1 A …D = +/-0.1步骤2 板件仍以孔A 定位钻孔C (基准没有变化)公差 A …C = +/-0.1孔B 、孔C 距离公差结果A …B = +/-0.1 A …C = +/-0.1B …C = +/-0.2比较两种情况可以看出,加工孔C 时基准不变比基准变换造成的公差减小了+/-0.1mm上面例子给我们的提示是:为避免基准变换,必须事先规定好在制造和测量过程中的基准点。
车身RPS系统理论基础知识

RPS 系 统 理 论
实施基准点系统:同步工程小组,由所有专业部门包括供应商在内的代表组成。小组成员包括产 品部(Entwicklung)、规划部(Fertigungsplannung)、质保部(Qualitaetsicherung)、生 产部门(Fertigung)及供应商(Zulieferer)
RPS 系 统 理 论
基准点系统的特征:具有多功能的点 (1) 作为加工和测量的统一支承 (2) 保证在每个加工工艺中的尺寸稳定性
基准点系统的出发是避免基准变换 基准变换会产生如下问题:
(1)公差累计 (2)测量和加工结果因支承和基准的变换而发生变化,无法保证尺寸稳定性 (3)尺寸精度不稳定,使得尺寸分析难度加大
(1)限制物体运动方向最多的基准点作为主支承点——RPS1
H: 孔
xy: x向和y向 F: 平面 Z: z向 (2)长孔作为副支撑点——RPS2 H:孔
(3)RPS3Fz 简单支承点
F:平面 Z:z向 (4)RPS4Fz 简单支承点
X:x向
F:平面 Z:z向
RPS 系 统 理 论
RPS的字母含义
所有RPS点都必须纳入零件图中。
PMP:
PMP的全称是Pruefmerkmalsplan——检测特征规划。
在单件的PMP里面,除了规定为满足功能性要求(功能尺寸构 成点)、上级总成装配要求(上级总成PMP点)的检测点外,还 有一部分控制自身尺寸质量的重要特征检测点。所有的这些检测 点都有详细测量方法的描述。PMP点是我们对零件尺寸进行监控 的重要检测点。
RPS 系 统 理 论
基准点应尽可能按照DIN01077和DIN01078中的规定的标准形式和尺寸 实施,优先选择孔,其次是面,最后为棱边。如果在零件中提不出孔,则 必须选择平面或棱边作为所确定的基准点。
车身钣金件RPS设计规范
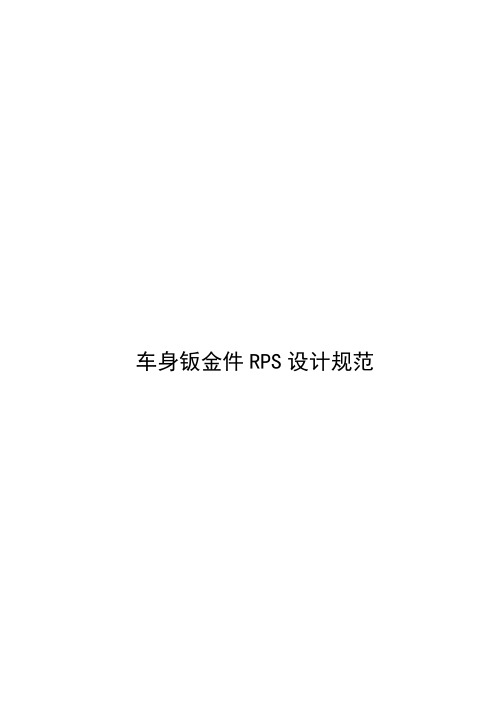
车身钣金件RPS设计规范车身钣金件RPS设计规范1范围本标准适用于汽车车身,零件及装配部件在产品设计阶段中的尺寸及公差标注、制造阶段中的主控点选择和检验阶段中的基准点确认,使设计部门,制造部门及检验部门具有同一定位基准,保证相同的尺寸关系。
2规范性引用文件下列文件对于本文件的应用是必不可少的。
凡是注日期的引用文件,仅注日期的版本适用于本文件。
凡是不注日期的引用文件,其最新版本(包括所有的修改单)适用于本文件。
AERI-I-027 白车身RPS点冻结流程3术语和定义3.1 RPS系统RPS起源于大众公司,是德语REFERENZPUCKTSYSTEM的缩写,英文名称为Reference Point System。
RPS系统就是规定一些从开发到制造、检测直至批量装车各环节所涉及到的人员共同遵循的定位点及其公差、要求。
4 RPS 规范性表示方式4.1 RPS编号规则如图1所示:图14.2 RPS图形表示方法4.2.1定位孔的图形表示要求如下:a、图形大小需与零件定位孔同径,内部填充辐射线;b、定位孔图形所在平面与零件定位孔所在平贴合,如图2所示:图24.2.2定位面的图形表示要求如下:a、图形形状、大小统一为10X10方形,内部填充网格线;b、 RPS面与圆角边距离x>3mm;c、正方形一条边方向需与圆角边切线平行;d、 RPS面与零件型面贴合,如图3所示:图34.2.3定位切边的图形表示要求如下:a、图形形状、大小统一为10X10方形,内部填充网格线;b、图形所在面需与切边所在面垂直,长度方向与零件切边平行,如图4所示:图45. RPS定位系统5.1 RPS定位系统的基本原理每个刚性物体在三维空间中皆具有六个自由度,其中三个沿X,Y,Z坐标轴的移动自由度,三个围绕X,Y,Z坐标轴转动自由度,如图5所示。
在加工时要确定刚体的位置,必须限制其6个自由度。
对于非刚性的零件来说,需要在非刚性方向额外增加约束,以确保零件在空间的稳定性。
第二章.2-车身尺寸工程A
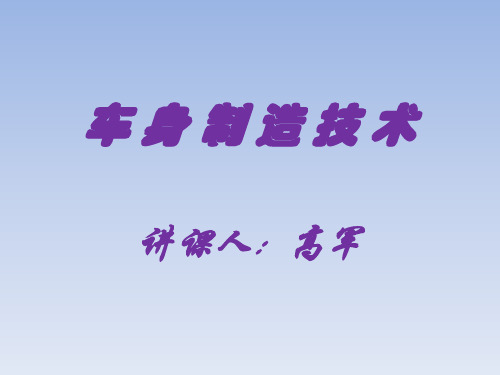
上都要使用RPS点作为支点。 如图所示:
输送装置使用RPS点作为支点
基准点系统
• 合理的定位系统保证了装配的一致性
主定位孔
过孔
副定位孔
31
基准点系统
合理的定位系统保证了装配的一致性
主定位孔 华普车副车架
紧固件用孔
副定位孔
32
翻边孔的应用
承受强度较高的零件 直边长度大于2mm 设置时需要注意料厚方向
特公司。 下面从几个方面对RPS系统作以介绍,以便大家更好地了解
和使用这个系统
二、车身尺寸工程
RPS是德语单词 Referenzpunkt-System (定位点系统)的缩写。
RPS系统就是规定一些从开发到制造、检测直至批量
装车各环节所有涉及到的人员共同遵循的定位点及其公 差与配合的要求。 在确定这些定位点时必须遵循RPS系统的规则,这 一点后面会详细论述。
12
基准点系统
⑹、基准点的特点:
基准点是建立在汽车坐标系中的单位矢量 单位矢量方向尽量与汽车坐标轴重合 每个零件只有一个基准点
所有的基准点以及相关的规定形成了基准点系统
基准点系统是一种标准
RPS点是模具、工装、检具的定位点。为了实现统一的定位技
术规则,必须保证模具、工装、检具都按照RPS点来制造。这一点
1、车身尺寸工程的作用
汽车设计中的基准点系统 定义了产品设计、公差分配、工艺、检测和装配的定位系统 车身公差分配 依据产品外观和功能的要求,并经济地考虑到制造系统的能力, 合理地给零部件制定公差。 统计误差分析 基本统计量、导出量和基本方法 测量系统评估 量具、量仪和检具重复性精度
2、基准点系统
原则的运用。
下图是总成焊接前各零件RPS点的分布情况。
汽车设计尺寸工程之RPS系统基础及设计流程培训

RPS系统的主旨是通过避免基准转变来保证制造工艺过程的可靠性和可重复 利用的精确性。
RPS系统的统一性规则要求从产品开发阶段直到批量生产,RPS点的使用 贯彻始终。
当然不是所有的RPS点都一直使用下去,那样的话在总成零件上就会有许 多点是重复的。
下面从纵梁到地板总成的焊接流程来看RPS点按统一性原则的运用。
B…C = +/-0.3
汽车技术培训-汽车设计尺寸工程之RPS系统基础及制定原则培训
4
汽车技术培训-
GD&T 形状及位置公差分析-RPS系统的定义和作用
(2) 加工时基准不变化
步骤1 用孔A定位冲出孔B和孔D
公差 A…B = +/-0.1 A…D = +/-0.1
步骤2 板件仍以孔A定位冲孔C (基准没有变化) 公差 A…C = +/-0.1 孔B、孔C距离公差结果 A…B = +/-0.1 A…C = +/-0.1
为了获得准确的结果,定位点应当是平行于坐标轴的。
汽车技术培训-汽车设计尺寸工程之RPS系统基础及制定原则培训
18
汽车技术培训-
GD&T 形状及位置公差分析-RPS系统的五条原则
不过在有些零件上是找不到与坐标轴平行的平面做RPS点的;
如图11
图11 零件上没有与Z轴平行的平面做定位点
汽车技术培训-汽车设计尺寸工程之RPS系统基础及制定原则培训
汽车技术培训-汽车设计尺寸工程之RPS系统基础及制定原则培训
2
汽车技术培训-
GD&T 形状及位置公差分析-RPS系统的定义和作用
一、RPS系统的定义和作用
RPS是德语单词Referenzpunkt-System(定位点系统)的缩写。
什么是RPS
什么是RPS(REFERENZPUC KTSYSTEM)?2007-08-08 10:10RPS即汽车设计制造过程中贯穿前后的基准点系统,是目前在大众汽车中应用的一种的定位体系,它被利用来保证汽车零部件尺寸稳定性和零部件功能,保证产品质量稳定性方面。
汽车是一个极其复杂的产品,其质量关注点很多,包含方方面面,如:漏水,关紧力大,风噪,配合差,异响,刮漆,阻滞等等,但实际调查表明,超过85%的问题是由制造过程中的尺寸问题引发地。
如何使产品从开始设计到制造过程中的各个环节,尽可能的减少尺寸偏差累积,是提高最终产品质量的一个关键要素。
在这一点上,各大汽车厂商走出了相近,但又有所不同的路,即引入GD&T(或类似),及基准一致性原则,但应用上有所差异。
北美和欧洲的厂商定位倾向与实际保持一致,日本厂家的定位是用来研究如何保证零件的质量,而韩国厂家则是通过定位来压迫零件变形,使之达到要求。
大众汽车则最终发展成了所要讲的RPS系统。
RPS简单的讲,就是指基准一致性。
它是指一种统一的和通用的,并带有相应公差范围的,在空间固定部件的基准体系,要求产品设计,制造和质量保证中使用一样的、共同适用的定位。
RPS根据一系列原则,制定一些从开发到制造,检测直至批量装车各环节所有涉及到的人员共同遵循的定位点及其公差要求。
按照大众内部的传统做法是,一辆汽车是借助于总坐标系(数学汽车坐标系)来确立的,坐标系的原点建立在汽车轿轴上的中心;而对于基准点系统来说,同时又在总坐标系中建立相对坐标系即部件型坐标系,其原点是那个部件的某个定位点即主要基准点,再将部件型坐标系附加到总坐标系。
部件型坐标系的原点相对于总坐标系原点本身无公差,但在处理相应基准点的加工尺寸时,相对尺寸自然是带公差的.由此,任意一个零件都坐落在自身的坐标系中。
当有两个零件组装时,将标出两个零件相互间的公差,在组装之后,两个坐标系中的一个零件的原点失去其功能,这样新的部件重新只用一个部件型基准坐标来描述,两个参照系中的一个被取消。
RPS设计指南_大众_西雅特_斯柯达_奥迪培训资料
第一步:
以A孔固定,在钢板上钻B和D 公差: A…B=±0.1 A…D=±0.1
第二步:
继续以A孔定位(基准无变换),在钢板上钻C孔 公差: A…C=±0.1
结果:
公差: B…C A…B ±0.1 A…C ±0.1 B…C ±0.2
25
二、RPS是什么?
基准变换的方式:
以A孔定位,钻B和D孔 以D孔定位,钻C孔 公差: B…C=±0.3mm
一、为什么使用RPS ?
哎!RPS已经讨论过相当 长时间了! 问题是当作为基准一致使 用时,有人不用它
我们老板很清楚
15
一、为什么使用RPS ?
RPS系统的另一个优势:
RPS能用于直接装配,从而大幅度削减定位样板的
使用
除了样板本身的成本,样本的使用导致装配需求的增
加,导致操作时间的增加
用这些没用的样板, 你能坚持多久? 借我用一个手怎么样?
注(对于刚性体而言)。
每一种定位形式将用字母表示:H代表孔和销,F代表面和边,
T代表理论点;定位方向(x,y,z)用小写字母标识。例如:RPS3Fz
额外的支撑点也这样标准,但用小写字母表示定位形式; 对于旋转的坐标系,定位方向用小写的a,b,c表示(见3-2-1
法则)
31
二、RPS是什么?
28
二、RPS是什么?
为了保证RPS点在实际生产中能切实使用,定义 RPS点时必须遵循某些规则,如下:
1 3-2-1法则 2 坐标系平行原则
3 连续一致原则
4 基于尺寸计算原则
5 RPS尺寸公差表
29
二、RPS是什么?
1 3-2-1法则
为了把这个刚性体确确实实地定位住,必须Fra bibliotek定六个方向 的移动
RPS系统规范及使用说明
BYD-AFCS01.024—2009 单件 RPS 图,主要表达单个零部件从车身零部件总成所继承的要素及其相应的功能与要求。在进行
零部件 RPS 基准设定时,遵循由上到下的原则,即首先确定大总成的定位基准,再确定各级分总成的定 位基准,最后完成单个零部件的基准设定,保证整个零部件系统的 RPS 基准顺利完成。最终,单个零部 件的主定位基准都必须源于其上级总成的定位基准,即各级总成所用的定位基准都在其下级分总成或零 部件的定位基准中选取,以保证零部件定位基准的前后一致性。
RPS 系统所设定的基准信息都必须纳入零部件/零部件总成 RPS 图中,其主要定位方式标记字母的 定义说明如下: 5.3.1 H/ h
表示孔/销定位 5.3.2 F/ f
表示平面/球面/顶点定位 5.3.3 E/ e
表示棱边 5.3.4 P/ p
表示理论点 5.3.5 x/y/z
用于表示平行于基本坐标系的三个坐标方向,通常用来表示 RPS 点所限制的自由度方向,适用于零 部件坐标系相对整车坐标系平行移动的转化。 5.3.6 a/b/c
因此,设定车身各大零部件系统重要总成及单个零部件的 RPS 图,作为车身零部件的设计基准,对 零部件的制造、检测和装配等生产过程进行相应的管控,来保证车身各大系统的精度和配合质量。
车身零部件单件的定位基准必须考虑后续总成的定位基准继承情况,保证总成的定位基准来源于各 级分总成的定位基准,各级分总成的定位基准来源于各零部件的定位基准,这也是整个 RPS 系统的目的 所在。通过零部件单件与总成的基准统一,可以实现零部件整个生产过程的基准继承,减少由于各个工 艺过程的基准不一致带来的误差。
比亚迪汽车
设计规范文件
BYD-AFCS01.024—2009
RPS在车身设计过程中的应用
或 3个 以上 定位 面 构成 ,焊接 时焊 装 夹具 对 每一 定位
面采 用一 块 标准 的支 撑块 ,支 撑 定位 。
l ×1 0 0等 。
对 于大 的刚度 不 足 的零件 ,在保 障 3 2 1原则 的 _—
前 提 下 , 需 要 附加 的定位 点来 保证 零件 的平衡状 态 , 还
位置 精度 。 内部 的结构 件一 般 用孔 定位 较 多 。 可用 2个 孔 定 位 ,1个 圆 孔做 主 定位 ,1个 圆 孔 或 长 圆 孔 做 辅
当零件 1的 定位 销 要 穿过零 件 2时 ,零 件 2上 的
孔 为 D, D + 。如 图 8所 示 。 _ 3
一
5 — 8
22 坐标 平行原则 .
-— 原 表 示 形 式 : 平 面 2 ×2 ; 平 面 2 ×1 ; 平 面 称 之 为 N 2 1 则 。 0 0 0 0
6 )符号 。如 图 1 示 ,H,h=孔 / 定位 ;F 所 销 ,
在 设计 的过程 中经 常会 遇到 如 图 3 示 的问题 : 所
5 — 7
.
2 1 年 8月 0 1
24 定位距 离应大 于零部件 长度的 6 % , 0 图 5中 1 2为设 计初 期 的 2个 定位 孔 ,孔距 / 和 总
长 l4 /。将 会 导 致 :1 由于 质 量 的 作用 ,零 件 右 端 )
下 沉变 形 ;2 )增 加 零件 的散差 。
.卜 一
I I
个 刚体 的平 行 移动 和转 动 共有 6个 自由度 , 限
制 6个 自由度 刚体 才 能保 持平 衡 。按 照 32 1 则 , —— 原
保 持 刚 体 平 衡 状 态 需 要 6个 定 位 点 。 如 图 2所 示 ,
- 1、下载文档前请自行甄别文档内容的完整性,平台不提供额外的编辑、内容补充、找答案等附加服务。
- 2、"仅部分预览"的文档,不可在线预览部分如存在完整性等问题,可反馈申请退款(可完整预览的文档不适用该条件!)。
- 3、如文档侵犯您的权益,请联系客服反馈,我们会尽快为您处理(人工客服工作时间:9:00-18:30)。
8
2、坐标平行规则
在测量和加工时,RPS点的设置必须保证得到准确的结 果,定位点应当是平行于坐标轴的。
14
零件坐标系是以整车坐标系为基础建立起来的,有下面两种 建立方式:
Ø 通过在整车坐标系中平移建立,这是通常的情况。
图4 在整车坐标系中平移建立零件坐标系
15
Ø 通过在整车坐标系中旋转建立零件坐标 系的情况。
图5 通过在整车坐标系旋转建立零件坐标系
16
(1) 通过平移建立零件坐标系的尺寸标注规则 按照零件特性选择三个与整车坐标轴平行的平面并求其交点, 这个交点定义为RPS系统的基准点。基准点相对于整车坐 标没有公差,零件尺寸以基准点为起点标注。
零件仅发生平移
对比显示,倾斜放置导致的严重后果: Ø尺寸合格的零件被错误的当成废品。 Ø模具根据错误的测量结果在X/Z方向修改,其实Z向没有偏差,X向的测量结果 也是错误的。 Ø焊接总成的生产散差扩大,功能尺寸无法保证。 Ø工装被不正确的调整了。 Ø通过上述方法导致后来生产的产品都是废品。 为获得准确的结果,定位点应当是平行于坐标轴的。
汽车尺寸工程设计 RPS设计
目录
一 RPS定位系统基本概念简介 Title 二 RPS定位系统设计遵循的原则d Title 三 RPS定位系统应用介绍e 四 内容回顾le
1
一、RPS系统简介
对零部件影响
长期以来,大量的尺寸超差给汽车制造企业带来重 大的损失:不仅严重影响零件功能的发挥,而且经 常导致零件报废使得汽车成本增加。
平面定位方向 平面定位点标记字母 孔限位方向 孔定位点标记字母 带有序号的RPS点名称
3
一、RPS定位系统—作用
1、避免了Байду номын сангаас于基准点的变换造成零件尺寸公差加大
BC公差 +/- 0.3
BC公差 +/- 0.2
例1:加工基准点发生变换时
例2:加工基准点不发生变化时
4
一、 RPS定位系统—作用
2、避免了模板的使用
6
1、3-2-1原则
一个刚体的平行移动和转动共有六个自由度,限制六个自由 度刚体才能保持平衡。按照3-2-1原则,保持刚体平衡状态需 要六个定位点。如图所示:三个定位点在Z方向;两个定位点 在Y方向;一个定位点在X方向;
Z
X
Y
3-2-1原则由此得来,这些点就是RPS系统定位点,称为 RPS点。
7
对于没有孔的零件,六个RPS点是必须的。而有孔的零件,往往将孔设为 RPS点。 对于单个零件,主副RPS点选择两个圆孔或一个圆孔(RPS1)和一个腰形孔 (RPS2)。 对于大的刚度不足的零件,在保障了3-2-1原则的前提下,还需要附加的定 位点来保证零件的平衡状态,称之为N-2-1原则。
17
Ø 在零件坐标系中一个点相对于基准点的距离称为名义尺寸。 名义尺寸可以通过减法算出绝对值。
Ø 例如:基准点在整车坐标系中的坐标为 X=400 Y= -65 Z=100
Ø 定位点RPS3Fz整车坐标为 X=550 Y= -95 Z=100 如图6所示
18
零件坐标系
整车坐标系
移动
基准点
起点 图6 名义尺寸举例
12
系统的统一性规则还要求所有工艺流程中的输送装置原则 上都要使用RPS点作为支点,如图3所示。
图3输送装置使用RPS点作为支点
13
4.尺寸标注规则
Ø 在零件图纸中画出整车坐标是有意义的--这可以确定零件 在整车中的位置,这是零件设计过程中重要的基础。
Ø 可是对于零件的制造和测量,采用整车坐标会带来很多困 难。RPS系统要求建立起零件自身的坐标系--零件坐标系, 并以此作为基础。
3、RPS点是模具、工装、检具的定位点
为了实现统一的定位技术规则,必须保证通用性 ,也就是模具、 工装、检测和安装工序都按照RPS点来制造。
这一点是RPS系统最重要的作用。
5
二、RPS定位系统编制遵循的原则
为了使RPS系统在实际当中发挥作用,必须遵守下面五 条规则: Ø 3-2-1规则 Ø 坐标平行规则 Ø 统一性规则 Ø 尺寸标注规则 Ø RPS尺寸图
10
3、统一性原则
Ø RPS系统的主旨是通过避免基准的转换,进而保证制造工艺 的可靠性和可重复性利用的精确性。
Ø RPS系统的统一性原则要求从产品开发阶段直至批量生产,RPS点的使 用贯彻始终。当然不是所有的RPS点一直使用下去,那样在总成 上有很多点都是重复的。 Ø 选取刚性足够且不变形的RPS基准点。
下面从纵梁到地板总成的焊接流程来看RPS点按统一性原 则的运用。图1是总成焊接前各零件RPS点的分布情况。
11
图1 焊接前RPS点分布情况
图2 第一道焊接工序后RPS点重新确定的情况
图2是第一道焊接工序后RPS点重新确定的情况。可以看到地 板总成上有3个RPS点是沿用合成前零件上已有的:总成上的 RPS1点是单件左纵梁上的RPS1点,总成上的RPS3点是单件 前地板上的RPS3点,总成上的RPS4点是单件右纵梁上的 RPS1点。
对整车影响
尺寸偏差大给整车匹配带来的麻烦更大:间隙和平 度不合格而且原因的查找又非常困难。
大众公司 RPS管理
在大众公司,RPS系统被制定成公司标准VW01055。 从A4 车开始,没有填写RPS表格的图纸就得不到认 可的批准。由此可见RPS系统的重要地位。
2
一、RPS定位系统—定义
定义:RPS(英文Reference Point System)参考点系统, 是规定一些从开发到制造、检测直至批量装车各环节所涉 及到的人员共同遵循的定位点及其公差要求。 RPS点的标注方式:
下面通过两种定位系统的对比,来说明此规则的重要性。 合格零件放在两种定位系统中,零件空间位置一致。
推荐
不推荐
9
当发生生产散差,零件不合格,在X方向存在偏差,如红 色件所示下图为在两种定位系统中零件的空间位置对比:
制造误 差X mm
测量结果 X mm
制造误差 X mm
零件发生旋转
测量 结果 M mm
19
(2)通过旋转建立的零件坐标系规则 Ø 有些零件按照平移建立零件坐标系是不合理的,而必须进