焦炉气生产200kt_a甲醇弛放气联产80kt_a合成氨初步设计
80kt/a合成氨变压吸附脱碳装置技术改造

80kt/a合成氨变压吸附脱碳装置技术改造小氮肥第39卷第8期2011年8月80kt/a合成氨变压吸附脱碳装置技术改造0前言洪鉴(云南云天化国I~.,fG_r--有限责任公司红磷分公司开远661600)云天化国际化工有限责任公司红磷分公司的合成氨装置于1999年建成投产,原设计能力为30kt/a合成氨,以焦碳,白煤为原料制气,脱碳采用变压吸附工艺,配套的变压吸附脱碳装置(简称1脱碳装置)设计处理能力25000In/h(标态).2001年,合成氨装置产能扩至80kt/a,新增1套设计处理能力25000in/h(标态)的变压吸附脱碳装置(简称2脱碳装置).在运行过程中,2套脱碳装置的氢损失都比较大,1脱碳装置氢损失高达4%~6%(体积分数,下同),2脱碳装置氢损失达3%,严重影响了合成氨的消耗.为此,经多方论证,在2007年对2套脱碳装置进行了技术改造.1合成氨脱碳系统工艺流程和主要设备1.11脱碳装置1脱碳装置工艺流程见图1.来自变换系统的变换气在一定压力和环境温度下,由管道进入气水分离器,将原料气中的游离水分离掉,分离出的水通过排污阀排出,分离水后的原料气通过管道进入吸附塔;脱碳后的产品净化气从出口管弓9出,进入净化气缓冲罐,然后与2脱碳装置净化气汇总到三段进口总管.吸附后的吸附剂需要进行解析再生,吸附塔的解吸气分两部分排出:一部分为吸附塔逆向放压时的排出气;另一部分为真空解吸气,由真空泵抽空后进入抽空气放空总管排出.该套变压吸附装置设计吸附压力~0.8MPa,由52只程控阀,2只终充阀及1只出口压力调节阀组成.工艺运行方式为8-3-2和6—2—2两种运行方式,8—3.2即8塔运行,3塔同时吸附,2次均压,每塔的循环步骤为:吸附,一均降,二均降,逆放,抽真空,二均升,一均升,终充.6—2-2即6塔运行,2塔同时吸附,2次均压,每塔的循环步骤为:吸附,一均降,二均降,逆放,抽真空,二均升,一均升,终充.6-2-2作为低负荷或其中一塔阀门有故障时进行调节.1脱碳装置主要设备参数见表1.1.22脱碳装置2脱碳装置工艺流程见图2.该套装置设计吸附压力为一0.7MPa,由46只程控阀,1只终充阀和1只出口压力调节阀组成.工艺运行方式为8.3.3和6-2.2两种.83.3即8塔运行,3塔同时吸附,3次均压,在抽真空时还带有1~2S冲洗.l专.钕接挺接挺穗撂:睡唾唾睡唾夔.留翟.._●●IlID+D+哇9.o+D+口+D+.;图11脱碳装置工艺流程冲罐口口l0表11脱碳装置主要设备参数设备名称设备参数吸附器气水分离器净化气缓冲罐真空泵452600mm×22mm×7980mm.吸附剂装填量29m,8台451000mm×12mm×3180mm,1台3500mm×14mm×16275mm,1台SK一120,n:390r/min,排气压力0.10~0.12MPa,抽气量7200m/h,5台小氮肥第39卷第8期2011年8月每塔的循环步骤为:吸附,一均降,二均降,三均降,逆放,抽真空一,反洗,抽真空二,三均升,二均升,一均升,终充.6.2_2即6塔运行,2塔同时吸附,2次均压,每塔的循环步骤为:吸附,一均降,二均降,逆放,抽真空,二均升,一均升,终充.6-2-2作为低负荷或其中一塔阀门出现故障时进行调节.2脱碳装置主要设备参数见表2.表22脱碳装置主要设备参数设备名称设备参数吸附器气水分离器净化气缓冲罐真空泵452600mm×24mm×9560mm.吸附剂装填量36m,8台1000mm×12mm×3180mm,1台3500mm×14mm×16275mm,1台SK-400,n=390r/min,排气压力0.10~0.12MPa,抽气量96m/min,4台2存在问题及原因分析2套脱碳装置在运行时,都体现出了操作便捷,开停车方便等优点,但存在氢等有效气体损失大,2脱碳装置阀门故障时会造成全系统憋压等问题.2.11脱碳装置1脱碳装置自1999年投产以来,实际运行处理气量比设计值低5000~8000m/h(标态),氢损失高达4%一6%,比设计值高1.5%一2.5%. 主要原因:①1脱碳装置在1997年设计时,由于对吸附工作压力与吸附效果的关系认识不足,在确定设计条件时考虑不周,吸附压力设计得过高(0.78MPa),但实际操作过程中,吸附压力仅为0.62MPa左右,与装置实际所能达到的吸附压冲罐力偏差较大.变压吸附的主要特点是吸附压力越高,吸附效果越好,处理能力越大,由于在设计时对装置的操作弹性也考虑不到位,由此造成1脱碳装置虽然设计原料气处理能力为25000m/h (标态),但实际上最高仅能达到20000m./h(标态)左右;②塔设计容量过低,吸附剂装填量过少.因设计压力的高低与吸附剂的装填量成对应关系,由于设计压力过高,导致吸附剂装填量过少,降低了脱碳系统的处理能力.由于以上2个原因,导致1脱碳装置负荷过重,只得依靠减少吸附时间来保证1脱碳装置的处理能力,各个循环步骤的时间相应减少,最终导致1脱碳装置的抽真空度降低,吸附剂再生效果不好;单位时间内放空次数增多,放空压力增大, 导致氢损失增大.2.22脱碳装置2脱碳装置自2002年投产以来,实际处理原料气气量比设计值高9000ITI/h(标态),出口气中(CO:)高达0.35%,比设计值高0.05%;氢损失高达3%,比设计值高1%.主要原因:①脱碳装置需要处理气量54000in/h(标态)左右,但由于1脱碳装置处理能力达不到设计要求,导致2脱碳装置负荷增加9000Ill/h(标态)左右的气小氮肥第39卷第8期2011年8月量,超出了2脱碳装置的负荷设计值,只能同样减少2脱碳装置吸附时间来提高该脱碳的处理能力,随着吸附时间的减小,各个循环步骤的时间相应减少,2脱碳装置单位时间内放空次数随之增加,放空压力增大,氢损失增大.2脱碳装置因逆放步骤和抽真空步骤共用1只阀门,每个系列配1只逆放总阀,阀门出现故障时,全系统易造成憋压,所以必须停运2台压缩机和2脱碳装置, 系统卸压后才能恢复生产.由于装置负荷太重,循环周期时间太短,1和2脱碳装置往往只能实现2次均压或3次不彻底的均压,从而出现放空压力高,放空次数多及气体损失大等问题.为此,经收集,查阅相关资料,并多次向部分相关单位进行调研,最终确定选用四川开元科技有限责任公司提供的改造方案.3技改情况最终确定的改造方案是将原有1和2脱碳装置由8.3.2和8—3.3流程均改造为lO-4-4&2PP/ VP流程.新工艺流程步骤为:吸附(A),顺放一(PP1),一均降(E1D),二均降(E2D),三均降(E3D),四均降(FAD),顺放二(PP2),逆放(D),抽真空一(V),反洗,抽真空二(V),四均升(FAR),三均升(E3R),二均升(E2R),一均升(E1R),终充(FR).具体改造方案:①增加顺放和抽空冲洗步骤,1和2脱碳装置都分别再增加2台吸附塔及相应装填量的吸附剂(1脱碳装置为29m塔,2脱碳装置为36m塔),同时,将现有的产品气缓冲罐改作均压罐,2脱碳装置新增加单独的.8只逆放阀,同时各增加3只程控阀(顺放一总阀,顺放二总阀,三均总阀),控制系统采用现有的罗斯蒙特A V7.4DCS系统,并增加相应的开关量及模拟量控制模块和仪器仪表;②改造后本装置可实现在1塔出现故障时,由10塔流程切换至9塔及8塔2种流程下运行;③根据新的工艺要求,对DCS重新进行组态;④1和2脱碳装置改造后均改为10—4-4&2PP/VP流程,即10塔运行,4塔同时吸附,4次均压,增加了冲洗再生步序及2次顺放.4塔同时吸附可减小吸附操作下的空塔线速度,改善吸附效果,增加1次均压和2次顺放后,降低放空压力,延长抽空时间,改善吸附剂再生效果,有利于吸附塔循环吸附操作.通过以上多方面改进后,有效提高装置有效气体回收率,减少气体损失.2套脱碳装置改造与2007年5月合成氨装置停车大修时同步组织实施完成,并在2007年5月20日与合成氨主装置大修后同步投入运行. 4改造后工艺流程经过技术改造后,1和2脱碳装置的工艺流程一致,各套系统工艺流程与技改前基本一致,但是在此基础上增加了气体的回收流程.改造后工艺流程见图3.图3改造后工艺流程吸附流程:来自变换系统的原料气首先进入气水分离器,将原料气中的冷凝水分离掉,经原料气进口阀进入吸附塔,在塔中原料气的杂质组分被吸附剂吸附,净化气则从净化气出口阀引出,经计量并通过出口压力调节阀后输出界区外进入压缩机三段进口.再生流程:吸附塔吸附步骤结束后,进行吸附剂的再生过程.吸附塔依次经顺放一,一均降,二均降,三均降,四均降,顺放二,逆放,抽真空及抽真空冲洗,四均升,三均升,二均升,一均升,终充等步骤完成吸附剂的再生和吸附塔的升压过程, 其中一均降气体均往一均升,二均降气体均往二均升,三均降气体均往均压罐,三均升的气体由均压罐来,四均降气体均往四均升,顺放一的气体作为净化气,顺放二的气体送到气柜进行回收.本装置主流程采用10_44&2PP/VP(简称10V)工艺.当某1台吸附塔上的程控阀因外部元件故障导致程控阀不能正常开关时,流程可由lOV工艺切换为9-4-4&2PP/VP(简称9V)或8—34&2PP/VP(简称8V)工艺运行.即切除掉故障阀门所在的吸附塔,切换后处理原料气负荷会有所降低.阀门故障处理完毕后,再由9V或8V工艺切换为10V工艺,装置恢复正常生产.125装置改造后运行情况及效果装置改造后于2007年5月20日投入运行,至2007年6月6日以后装置一直在满负荷下稳定运行.从运行情况来看,放空压力对比改造前大幅度降低,有效地减少了放空气量.通过放空小氮肥第39卷第8期2011年8月压力的降低,可以很直观地反映出装置在改造后气体损失大大减少,有效气体的回收率有所提高.1和2脱碳装置改造前,后的运行参数对比见表3.1和2脱碳装置改造前,后各步骤时间对比见表4.表31和2脱碳装置改造前,后的运行参数对比注:每个周期放空1次;2脱碳装置程控阀出现故障时,不会出现系统憋压. 表41和2脱碳装置改造前,后各步骤时间对比项目APPlEIDE2DE3DE4DPP2DVE4RE3RE2RE1RFR(1)放空压力对比改造之前大幅度降低(1脱碳装置放空压力为0.10~0.11MPa,2脱碳装置放空压力为0.09~0.10MPa),放空压力均减少了0.04~0.06MPa,有效减少了放空气量.通过放空压力的降低,可以很直观地反映出装置在改造后气体损失大大减少,有效气体的回收率有所提高.(2)2套变压吸附脱碳装置改造后,净化气出口气中CO,指标控制平稳,并且在相同分周期时间条件下,净化气中CO2含量可控制在比改造前更低的水平上;同样以改造前装置的净化气中CO 含量为控制指标时,改造后装置分周期时间比改造前延长了.改造前,1脱碳装置净化气中CO含量由0.60%~0.70%(体积分数,下同)降为0.35%~0.45%,2脱碳装置净化气中CO2含量由0.35%~0.45%降为0.30%一O.40%.脱碳装置出口气中CO含量降低后,可降低精炼负荷,减少精炼自用氨消耗.(3)改造后,设计了9_44和8.3_4流程作为辅助流程.在l0塔流程下运行时遇某程控阀外部元件出现故障时可在线切换至944流程下运行, 在切换过程中装置可保持原有负荷继续运行,对合成氨整套装置的生产负荷不造成影响,待故障元件恢复使用后又可在线切换回l044流程下运行.2脱碳装置不会出现系统憋压,不会引起系统大减量,不会出现急停2台压缩机的情况,整个系统操作压力平稳.(4)装置改造后,增加了抽真空压力联锁和逆放压力联锁,不会因阀门故障造成高压抽真空的情况出现,使装置在运行中切实起到了保护真空泵和吸附剂的作用,保证了装置的运行安全. (5)改造后,变换进口压力略有下降;脱碳系粥"如加无无"无加H∞∞∞无,无无"无加无"拍加如无:无∞m∞1223前后前后改改改改技技技技置置装装碳碳脱脱##l,_小氮肥第39卷第8期2011年8月XCP一2008型节能盘根在离心泵上的应用常金唱申延鹏(河南晋开集团延化化工有限公司延津453200) O前言河南晋开集团延化化工有限公司(以下简称延化公司)现有24台12SH.13型离心泵,6台350S-44(A)型离心泵和4台12SH一11型脱硫再生泵,泵轴密封原采用石棉盘根密封,其轴套磨损大,寿命短,每年需要更换2—3次;盘根每1—2个月就需要更换,且轴封渗漏现象严重.为此,延化公司采用XCP一2008型节能密封填料技术对密封函进行改造,产生了很好的经济效益.1密封原理离心泵泵轴密封大多采用石棉盘根密封.此密封方式是靠填料压盖螺栓的预紧力,通过填料压盖作用在填料上,在预紧力的作用下填料受力统出口压力略有上升,即压缩机二段出口和三段进口的压差略有降低.若再适当减少分周期时间,压缩机二段出口和三段进口的压差还可降低,但系统氢损失将会增加一些.(6)改造后,抽真空度降低,吸附剂再生效果好;吸附时间加长,单位时间内放空次数减少;吨氨半水煤气消耗下降约100m(标态).通过对原有系统技改后,使氢气回收率提高约2.95%,平均可多回收H780m/h(标态),可节约原料煤(实物)518.7kg/h和燃料煤(实物)62.4kg/h.年节约原料煤(实物)4108t,按原料煤价660t计,年节约原料煤支出271.13万元;年节约燃料煤(实物)494t,按燃料煤200Yv_/t计,全年节约原料煤支出9.88万元.共计节约支出约281.01万元,经济效益显着.6存在问题(1)装置试运行过程中,净化气指标存在波13变形,从而充满填料室内填料与轴套,填料与填料函内壁2个问隙,阻止了介质的泄漏,达到密封目的.压紧力需要超过阻力传递到每道填料上,产生大小不等方向相同的径向力,且所产生的径向力大于介质压力时才能达到阻止介质泄漏的目的.石棉盘根密封压力分布见图1.径向力ffIl▲预紧力三囟囟囟囟囟三介质压_L_U一一(I图1石棉盘根密封压力分布这种密封方式是靠压盖预紧力挤压使填料发生形变,充实2个间隙来实现密封的.对泵轴而言,会产生较大的摩擦力,该摩擦力不但会增加能量损耗,还易使轴套磨损,影响其使用寿命;且极动较大的现象,主要出现在新,旧吸附塔吸附步序切换后,旧塔吸附剂与新塔吸附剂性能差距较大, 该现象在1脱碳装置体现得尤为明显.当旧塔吸附的时候,由于吸附剂吸附性能下降,造成吸附时间缩短,进而抽真空时间随之缩短,吸附剂再生效果差,不利于装置循环吸附.(2)装置运行时真空度较差(1脱碳装置真空度为一0.04一一0.05MPa,2脱碳装置真空度约为一0.06.MPa),尤其1脱碳装置表现明显,除上述提及的原因,还因真空泵叶轮腐蚀严重,导致间隙过大,真空泵极限真空严重下降(1脱碳装置真空泵极限真空约为一0.06MPa,2脱碳装置真空泵极限真空约为一0.08MPa),引起真空泵抽空能力下降,吸附剂再生效果差,不利于循环吸附. (3)有部分旧程控阀存在内漏或外漏,影响了装置的正常工艺操作,这也是导致装置气体损失的又一因素.(收稿日期2011-04—12)。
年产20万吨合成氨合成工艺设计

年产20万吨合成氨合成工艺设计年产20万吨合成氨合成工艺设计The Process Design of 200kt/a of Synthetic AmmoniaSynthesis目录摘要 (I)Abstract.................................................. I I引言 (1)第一章综述 (2)1.1 氨的研究背景 (2)1.2 氨的用途 (2)1.3 氨的生产方法的选择 (3)第二章氨合成过程的步骤及工艺流程 (5)2.1 氨合成的步骤 (5)2.2 氨合成工艺流程简述 (6)第三章工艺计算 (9)3.1 原始条件 (9)3.2 物料衡算 (9)3.2.1 合成塔物料衡算 (9)3.2.2 氨分离器气液平衡计算 (10)3.2.3 冷凝塔气液平衡计算 (11)3.2.4 液氨贮槽气液平衡计算 (12)3.2.5 液氨贮槽物料计算 (14)3.2.6 合成系统物料计算 (15)3.2.7 合成塔物料计算 (16)3.2.8 水冷器物料计算 (17)3.2.9 氨分离器物料计算 (18)3.2.10 冷凝塔物料计算 (19)3.2.11 氨冷器物料计算 (21)3.2.12 冷凝塔物料计算 (23)3.2.13 液氨贮槽物料计算 (24)3.3 热量衡算 (26)3.3.1合成塔热量计算 (26)3.3.2 废热锅炉热量计算 (28)3.3.3 热交换器热量计算 (29)第四章设备的计算与选型 (31)4.1 已知条件 (31)4.2 计算并初选换热器规格 (31)4.3 校核总传热系数K (31)4.3.1官内给热系数α计算 (31)4.3.2 管外给热系数αo (35)4.3.3 总传热系数K (38)4.4 管子拉脱力的计算 (38)4.5 计算是否安装膨胀节 (39)4.6 换热器主要结构尺寸和计算结果 (41)结论 (42)致谢 (43)参考文献 (44)附录 (45)附录A:工艺流程图 (45)附录B:设备图 (45)年产20万吨合成氨合成工段工艺设计摘要:合成氨是化学工业的基础,也是我国化学工业发展的重要先驱,其中氨合成工段是合成氨工艺的中心环节。
甲醇弛放气制合成氨

甲醇弛放气制合成氨彭奕;黄维柱;李林;艾军【摘要】介绍以焦炉气生产甲醇过程中产生的弛放气与甲醇装置空分系统副产的氮气为原料,生产合成氨的新工艺及其技术性能、能耗和经济指标。
【期刊名称】《化工设计》【年(卷),期】2013(000)006【总页数】3页(P12-13,21)【关键词】驰放气;合成氨;新工艺【作者】彭奕;黄维柱;李林;艾军【作者单位】四川天一科技股份有限公司成都 610225;四川天一科技股份有限公司成都 610225;四川天一科技股份有限公司成都 610225;河北旭阳焦化有限公司定州 100107【正文语种】中文目前合成氨生产的主要原料有天然气、石脑油、重质油和煤等,其工艺技术成熟、可靠,而利用焦炉气制甲醇的驰放气生产合成氨成则为合成氨生产的全新原料路线。
现以某焦化公司甲醇驰放气为原料生产100kt/a液氨项目为例。
该项目利用焦炉气生产甲醇过程中产生的弛放气以及甲醇装置空分系统的氮气为原料生产液氨。
利用焦炉气制甲醇装置的弛放气制合成氨的项目属于典型的废气利用项目,这种生产液氨的新工艺方案,其生产技术、能耗及经济指标均处于较先进水平,具有良好的经济效益。
1 工艺方案和装置能耗指标来自于甲醇装置的驰放气经过变压吸附提取氢并除去对合成催化剂有害的一氧化碳、二氧化碳和氧。
来自空分的氮气压缩之后进行脱氧,再与氢气混合后进行干燥,除去水分。
干燥后的混合气进入联合压缩机,加压后进氨合成系统。
变压吸附的解吸气和氨合成系统放空气都去燃气管网。
原料气的净化流程见图1。
图1 原料气的净化流程方框图项目原料气净化部分采用变压吸附提氢技术以及等压干燥的专有技术,深度净化后的新鲜气当量氧原子小于等于10ppm,合成系统的惰性气体含量极低,这样合成系统氨净值高,吹除气量很小。
以煤、气、油为原料制合成气的净化工艺通常采用甲烷化工艺来脱除微量碳,由于甲烷化反应本身要消耗一些氢气,同时生成的甲烷又作为惰性气体混入新鲜合成气中,惰性气体含量越高,吹除气量越大,原料气损失越多,氨净值降低。
200kt/a合成氨装置脱碳系统改造总结

吸收塔 出 口工 艺气 C 含 量 容 易 超 标 ,并 且 导 O
致 系统能 耗增 加 。 为此 ,公 司于 2 0 0 9年制 定 了 对 合成 氨 装 置 进 行 增 产 ( 0 ) 节 能 降 耗 的技 3% 术 改造方 案 。改 造采 取分步 进行 ,首先 对一 段炉 和脱 碳系 统进行 改造 。为使 脱碳 系统 能够满 足合
9 . % 的再生塔 出塔 气送尿 素装 置作 为生产 尿 素 85 的原料 。从 2 0 0 5年 开始 ,脱 碳 系统 运 行 过 程 中 存 在贫 液 和 半 贫 液 再 生 差 、转 化 率 ( 液 中 总 溶
KC , 成 K O O 变 HC 的分率 ) 高 的 情况 ,造 成溶
伍建 国 ,刘 健康 。何 玉涛
( 川化股份有 限公 司,四川 成都 600 ) 13 1
.
[ 中图分 类号 ]T 1.6 [ Q 132 4 文献标 识码 ]B [ 文章编号 ]10 9 3 ( 0 1 O —02 0 04— 9 2 2 1 ) 1 0 3— 2
我公 司 的 20k/ 0 ta合成 氨装 置是 我 国第 1套
碳酸钾 溶液 ,将再 生塔 、吸 收塔 的散堆鲍 尔环 填
料更换 为规 整填料 ,同时对塔 内的除沫 网 、气 液
分布器进 行 了更换 。 1 近年 来脱碳 系统 的 问题 及处 理
循环过 滤 ;后 来 又对再 生塔 喷射蒸 汽发生 器和再
沸器 的热 负荷进行 了调 整 。
脱碳 系统 贫液 和半贫 液转化 率 的设 计值 分别 为 02 .5和 04 。从 20 .2 05年开始 ,脱碳 贫液 和半 贫液 的再 生情况 就一 直不好 ,表 1是近 几年脱 碳 贫 液和半 贫 液 的转 化 率数 据 。从 表 1 以看 出 , 可 脱碳 贫 液 和 半 贫 液 的转 化 率 一 直 在 上 升 ,20 04
甲醇驰放气制合成氨工艺分析
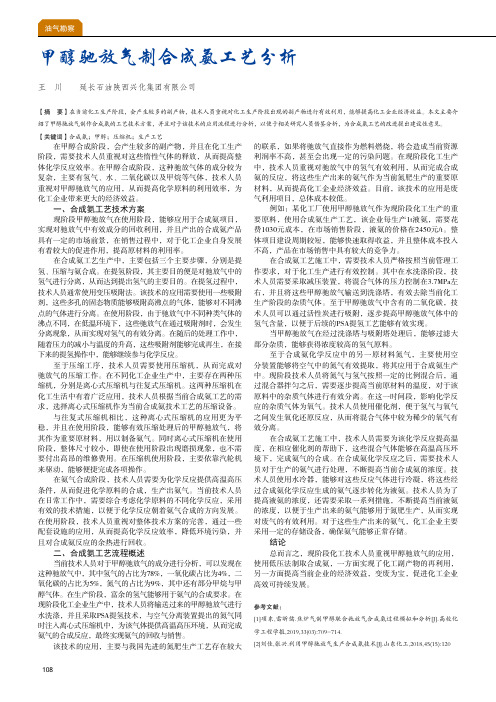
108在甲醇合成阶段,会产生较多的副产物,并且在化工生产阶段,需要技术人员重视对这些惰性气体的释放,从而提高整体化学反应效率。
在甲醇合成阶段,这种驰放气体的成分较为复杂,主要有氢气、水、二氧化碳以及甲烷等气体,技术人员重视对甲醇驰放气的应用,从而提高化学原料的利用效率,为化工企业带来更大的经济效益。
一、合成氨工艺技术方案现阶段甲醇驰放气在使用阶段,能够应用于合成氨项目,实现对驰放气中有效成分的回收利用,并且产出的合成氨产品具有一定的市场前景,在销售过程中,对于化工企业自身发展有着较大的促进作用,提高原材料的利用率。
在合成氨工艺生产中,主要包括三个主要步骤,分别是提氢、压缩与氨合成。
在提氢阶段,其主要目的便是对驰放气中的氢气进行分离,从而达到提出氢气的主要目的。
在提氢过程中,技术人员通常使用变压吸附法。
该技术的应用需要使用一些吸附剂,这些多孔的固态物质能够吸附高沸点的气体,能够对不同沸点的气体进行分离。
在使用阶段,由于驰放气中不同种类气体的沸点不同,在低温环境下,这些驰放气在通过吸附剂时,会发生分离现象,从而实现对氢气的有效分离。
在随后的处理工作中,随着压力的减小与温度的升高,这些吸附剂能够完成再生,在接下来的提氢操作中,能够继续参与化学反应。
至于压缩工序,技术人员需要使用压缩机,从而完成对驰放气的压缩工作。
在不同化工企业生产中,主要存在两种压缩机,分别是离心式压缩机与往复式压缩机。
这两种压缩机在化工生活中有着广泛应用,技术人员根据当前合成氨工艺的需求,选择离心式压缩机作为当前合成氨技术工艺的压缩设备。
与往复式压缩机相比,这种离心式压缩机的应用更为平稳,并且在使用阶段,能够有效压缩处理后的甲醇驰放气,将其作为重要原材料,用以制备氨气。
同时离心式压缩机在使用阶段,整体尺寸较小,即使在使用阶段出现磨损现象,也不需要付出高昂的维修费用。
在压缩机使用阶段,主要依靠汽轮机来驱动,能够便捷完成各项操作。
在氨气合成阶段,技术人员需要为化学反应提供高温高压条件,从而促进化学原料的合成,生产出氨气。
200kt/a聚丙烯装置的试生产

1 预 聚合和 聚合 反应 的压 力等 级 提高 , 使 ) 可 环管 反应器 中的氢气 含量增 高 ,扩大熔 体流 动速
率 的范 围 , 加 了产 品 的 强 度 , 善 产 品 的 性 能 ; 增 改 2 以双 环 管 反 应 器 构 型 为 基 础 , 以 生 产 宽 ) 可 相 对 分 子 质 量 分 布 的 “ 峰 ” 品 , 可 以 生 产 窄 双 产 也 相 对分子质量分 布的产 品。 该 装 置 可 以 生 产 挤 热 成 型 、 塑 、 维 、 注 纤 双 向拉伸 聚 丙烯 ( O P 膜 、 延 膜 等 5 B P ) 流 6个 牌 号 的 产 品 。 置 一 次 开 车 成 功 后 试 生 产 了 T 0 、3 F 装 3ST6 、 Y 5 G、 9 D 0 H3S牌 号 的 产 品 ,产 品 各 项 技 术 指 标 全 部 达到要求 。 1 装 置 试 生 产 情 况
表 2 试 生 产期 间聚 丙 烯 粉 料分 析 数 据
从 表 3中可 以看 出 ,试 生产 期间 使用 B sl ae l 公 司 Z — 催 化剂 生产 的聚丙 烯 粉料 粒度 分 布 N M1
较 好 , 多 数 为 80 I 以 上 的 颗 粒 , 料 较 少 , 大 5 m x 底
( 国石 油大 连 石 化 分 公 司有 机 合 成 厂 , 连 , 1 0 1 中 大 l6 3 )
摘
要 : 介 绍 了 2 0 k/ 丙 烯 装 置 试 生 产情 况 。 对 生 产 的 聚 丙 烯 牌 号 T 0 T 6 、 D 0 H 9 0 t a聚 3 S、 3 F Y 5 G、 3 S产 品 的 工
特 别是生 产 T 0 3S产 品时 , 底料不 到 1 %。
焦炉气制甲醇驰放气合成氨技术
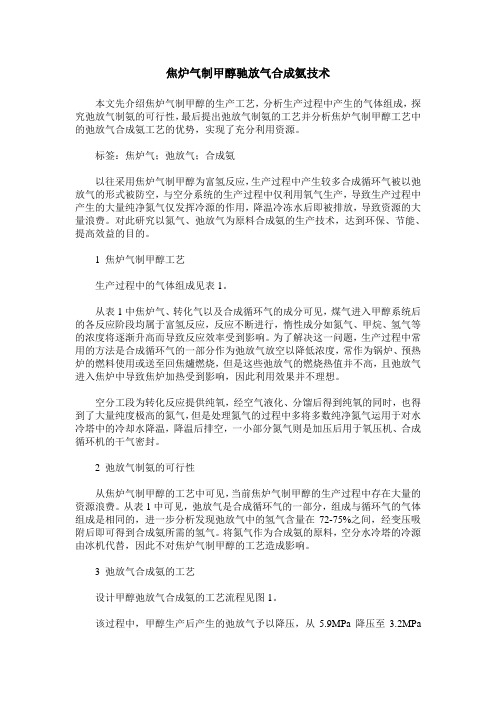
焦炉气制甲醇驰放气合成氨技术本文先介绍焦炉气制甲醇的生产工艺,分析生产过程中产生的气体组成,探究弛放气制氨的可行性,最后提出弛放气制氨的工艺并分析焦炉气制甲醇工艺中的弛放气合成氨工艺的优势,实现了充分利用资源。
标签:焦炉气;弛放气;合成氨以往采用焦炉气制甲醇为富氢反应,生产过程中产生较多合成循环气被以弛放气的形式被防空,与空分系统的生产过程中仅利用氧气生产,导致生产过程中产生的大量纯净氮气仅发挥冷源的作用,降温冷冻水后即被排放,导致资源的大量浪费。
对此研究以氮气、弛放气为原料合成氨的生产技术,达到环保、节能、提高效益的目的。
1 焦炉气制甲醇工艺生产过程中的气体组成见表1。
从表1中焦炉气、转化气以及合成循环气的成分可见,煤气进入甲醇系统后的各反应阶段均属于富氢反应,反应不断进行,惰性成分如氮气、甲烷、氢气等的浓度将逐渐升高而导致反应效率受到影响。
为了解决这一问题,生产过程中常用的方法是合成循环气的一部分作为弛放气放空以降低浓度,常作为锅炉、预热炉的燃料使用或送至回焦爐燃烧,但是这些弛放气的燃烧热值并不高,且弛放气进入焦炉中导致焦炉加热受到影响,因此利用效果并不理想。
空分工段为转化反应提供纯氧,经空气液化、分馏后得到纯氧的同时,也得到了大量纯度极高的氮气,但是处理氮气的过程中多将多数纯净氮气运用于对水冷塔中的冷却水降温,降温后排空,一小部分氮气则是加压后用于氧压机、合成循环机的干气密封。
2 弛放气制氨的可行性从焦炉气制甲醇的工艺中可见,当前焦炉气制甲醇的生产过程中存在大量的资源浪费。
从表1中可见,弛放气是合成循环气的一部分,组成与循环气的气体组成是相同的,进一步分析发现弛放气中的氢气含量在72-75%之间,经变压吸附后即可得到合成氨所需的氢气。
将氮气作为合成氨的原料,空分水冷塔的冷源由冰机代替,因此不对焦炉气制甲醇的工艺造成影响。
3 弛放气合成氨的工艺设计甲醇弛放气合成氨的工艺流程见图1。
该过程中,甲醇生产后产生的弛放气予以降压,从5.9MPa降压至3.2MPa后,进入变压吸附系统,经吸附、多级压力均衡降低、顺放、逆放、冲洗、多级压力均衡升高以及最终升压等多个步骤最终得到H2原料用于制氨。
甲醇驰放气制合成氨项目基本方案及经济效益分析

唐山佳华5万吨/年甲醇驰放气制合成氨工程项目基本方案及经济效益分析本着“发展循环经济、延伸煤化工产业链、综合利用、变废为宝”的原则,为合理利用甲醇装置副产的驰放气和空分装置副产的高纯氮气,现提出建设“唐山佳华5万吨/年甲醇驰放气制合成氨工程”的简要方案,对项目的可行性进行综合分析。
一、氨的主要性质氨,在常温下是无色气体,具有刺激性气味,极易溶于水,氨水中的氨极易挥发,氨水呈弱碱性。
在溶解时放出大量热。
液氨为无色液体,气化时吸收大量的热。
广泛应用于化工、轻工、化肥、制药、合成纤维、塑料、染料、制冷剂等。
二、氨的生产方法 1、氰化法CaO+3CCaC 2+CO CaC 2+N 2 CaCN 2+C CaCN 2+3H 2O CaCO 3+2NH 31905年在德国建成第一套氰化法制氨工业装置,一次大战期间德国、美国主要采用此法制氨,用于制造炸药。
每吨氨要消耗能量190GJ ,能量利用率非常低,己逐渐被历史淘汰。
2、直接法+=NH3ΔH?298=-kJ?mol -1此法是在高压、高温和有催化剂时,氮气和氢气直接合成氨的一种生产方法。
氢气和氮气合成氨是放热,体积缩小的可逆反应,其反应热不仅与温度有关,还与压力和组成有关。
目前工业上合成氨基本上都用此法。
三、合成氨的产能情况据有关资料统计,世界合成氨产能已超过亿吨/年,目前合成氨主要生产能力分布在中国、俄罗斯、美国、印度等国,约占世界总产量的一半以上。
近年来合成氨装置大型化是世界合成氨的主流发展趋势,目前世界最大单系列合成氨装置规模已达130万吨/年。
该装置属于Ferti Nitro公司。
Ferti Nitro公司是委内瑞拉、美国、意大利四个国家的合资企业,该公司还有1套150万吨/年大颗粒尿素装置。
2009年我国合成氨产能为5950万吨。
居世界第一位。
占世界总产量的%,表观消费量约万吨,尿素实物产量万吨,合成氨产品完全满足国内化肥和工业需要,部分化肥产品如尿素开始向国外出口。
- 1、下载文档前请自行甄别文档内容的完整性,平台不提供额外的编辑、内容补充、找答案等附加服务。
- 2、"仅部分预览"的文档,不可在线预览部分如存在完整性等问题,可反馈申请退款(可完整预览的文档不适用该条件!)。
- 3、如文档侵犯您的权益,请联系客服反馈,我们会尽快为您处理(人工客服工作时间:9:00-18:30)。
氮肥技术我国目前以焦炉气为原料气生产甲醇的厂家很少,生产能力在100kt/a以上已投产的仅有两家:上海焦化有限公司,1800kt/a冶金焦焦炉气生产200kt/a甲醇(单醇);山西焦化集团有限公司,1500kt/a冶金焦焦炉气生产120kt/a甲醇(联醇)。
国内焦化厂大多数厂家“只焦不化”,作为副产的焦炉气没有得到充分利用。
规模较大的焦化厂,焦炉气作为燃料气或城市煤气烧掉;规模比较小的焦化厂则干脆把焦炉气点了“天灯”,既浪费资源,又污染空气。
有关资料表明,我国煤炭资源大省山西省,2003年焦产量超过80000kt,排放的焦炉气达2×1010m3,比“西气东送”工程的总量还多,但综合利用率却不到10%。
如果能充分利用这些焦炉气,仅山西省每年就可生产7000~8000kt甲醇。
随着国家对环境保护的日益加强、甲醇生产关键设备(合成塔)国产化能力的提高及甲醇汽油的推广,焦炉气生产甲醇将越来越具有优势。
本文以1套2000kt/a冶金焦副产的焦炉气为原料生产200kt/a甲醇及其弛放气联产80kt/a合成氨装置为例,谈一下初步设计方案。
1焦炉气生产甲醇方案1.1焦炉气成分(%)H245~60CO5~9CO22.0~3.5CH422~28N22~3O20.1~1.0其他1.5~3.0总硫1~7g/m31.2甲醇生产工艺路线焦炉气经湿法初脱硫后,增压至2.1MPa,经干法脱硫后进行纯氧转化,转化气回收热量后,进行精脱硫,使总硫降至0.1×10-6以下,然后增压至5.3MPa,进行低压甲醇合成。
粗甲醇精馏后得精甲醇。
工艺流程图见图1。
1.3甲醇生产工艺过程特点(1)焦炉气硫含量高,平均达5g/m3左右,有机硫含量比其他原料气高。
有机硫对铜基催化剂的毒害比H2S大得多,对焦炉气进行湿法初脱硫时,选择脱硫剂很重要。
不同的脱硫工艺对进脱硫塔原料气H2S含量的要求也不同:ADA法4~5g/m3;栲胶法2.5~3g/m3;PDS法<2g/m3;“888”法1~10g/m3。
选用“888”法湿法初脱硫,既可脱除无机硫,又可脱除有机硫,有机硫脱除率达50%~80%,为后部精脱硫减轻负荷。
精脱硫是将原料气中的总硫(H2S、CS2、COS)脱至0.1×10-6以下,可选用湖北省化学研究所研制的常温精脱硫工艺技术。
(2)焦炉气纯氧转化。
选用四川天科工程有限公司推出的“纯氧转化”工艺技术,该工艺在催空分装置焦炉气湿法脱硫甲醇精馏压缩干法脱硫纯氧转化甲醇合成精脱硫压缩弛放气!!!!!!!!!!!!!!!!!!!!!!!!!!!!!!!!!!!!!!!!!!!!!"!!!!!!!!!!!!"!!!!!!!!!!!!!!!!!!!!!!!!!!!!!!!!!!!!!!!!!!!!!"!!!!!!!!!!!!"焦炉气生产200kt/a甲醇弛放气联产80kt/a合成氨初步设计方案冯学明(中吴集团宜化有限责任公司河北张家口075105)摘要简要介绍了以焦炉气为原料联醇和联氨工艺的初步设计方案。
关键词焦炉气甲醇联产初步设计图1焦炉气产甲醇工艺流程图2006年第27卷4化剂层以上进行燃烧反应,在催化剂层中发生,转化及变换反应:H2+1/2O2=H2O-Q(1)CO+1/2O2=CO2-Q(2)CH4+1/2O2=CO+2H2-Q(3)CH4+H2O=CO+3H2+Q(4)2CO+H2O+1/2O2=2CO2+H2-Q(5)气体到达催化剂床层时,O2几乎耗尽。
“纯氧转化”进行的是自热反应,无需外界供给热量。
根据合成甲醇气体成分要求[(H2-CO2)/(CO+CO2)]及催化剂床层温度变化、转化气甲烷含量调节O2流量大小。
(3)甲醇合成选用铜基催化剂,采用低压合成工艺。
甲醇合成塔可选用南化机制造的管壳式合成塔,其Φ4.09m,塔的设计能力为200kt/a,现已在上海焦化有限公司使用,其结构特点为:①管壳式结构;②集反应器与废热锅炉于一体;③转化率高;④循环量低。
(4)合成气及循环气采用蒸汽透平驱动离心式压缩机,可大大节省电力。
(5)循环气与新鲜气比例为(4.5~5)∶1。
(6)甲醇合成弛放气和空分装置的N2联产合成氨。
2甲醇弛放气联产合成氨方案2.1弛放气、新鲜气中惰性气体含量甲醇联产合成氨,甲醇合成不是生产的终端,甲醇分离器后惰性气体可控制在10%~15%左右,弛放气量V放=(V新×I新)÷I放式中V放、V新———弛放气、新鲜气量,m3/h;I放、I新———弛放气、新鲜气中惰性气体含量,%。
甲醇新鲜气、弛放气成分含量如表1。
其新鲜气和弛放气流量分别为57500m3/h和28750m3/h。
甲醇生产一般要求:(H2-CO2)/(CO+CO2)=2.05~2.1,以焦炉气为原料联醇生产,本方案(H2-CO2)/(CO+CO2)控制在2.4左右。
2.2合成氨生产工艺流程甲醇弛放气和空分装置生产的氮充分混合后,进入低变炉进行CO变换,然后进行脱碳。
脱碳气含有微量的CO2、CO,加压至11MPa进行甲烷化,出甲烷化炉后,加压至15MPa进行低压合成,弛放气去氢回收。
流程示意图如图2。
2.3物料衡算结果(1)补充N2量根据甲醇弛放气体成分及甲醇合成反应式计算得:补充N2量约为5090m3/h;合成氨原料气量为33840m3/h。
(2)氨产量吨氨消耗原料气定额值3300m3氨产量10.25t/h年产量80kt/a(3)弛放气补N2后气体成分(%)如下:H265.91CO25.77CO2.63N223.64CH41.53其他0.52(4)以焦炉气为原料生产甲醇联产合成氨时,通常采用稀氨水吸收法脱除CO2,副产肥料NH4HCO3。
CO2量按5.584t/h计,根据反应式NH3+CO2+H2O=NH4HCO3可计算出:液氨消耗2.157t/h,副产NH4HCO310.026t/h。
如果用碳丙液脱除CO2,可联产工业级或食品级CO240kt/a。
3结语(1)以焦炉气为原料生产200kt/a甲醇,其弛放气可联产80kt/a合成氨、40kt/a二氧化碳或项目H2COCO2N2O2CH4其他新鲜气68.6722.134.62.670.31.63弛放气77.543.096.7910.171.80.61低变炉甲醇合成弛放气脱碳甲烷化合成氨空分装置N2产品NH4HCO3燃料尾气氢回收甲醇工序弛放气氢气稀氨水产品液氨表1甲醇新鲜气、弛放气成分(%)图2弛放气联产合成氨工艺流程图第4期冯学明:焦炉气生产200kt/a甲醇弛放气联产80kt/a合成氨初步设计方案5氮肥技术套工业性的示范装置于2002年在陕西城固化肥厂开车运行,80kt/a合成氨的气化装置很快就要在天津开车。
中科院煤化所还进行了粉煤与烃类气体共转化、焦炭粉与纯氧、CO2气体的气化探索性试验,均取得较好的数据。
目前正在兴建2.5MPa下的气化试验装置,原计划2005年底试运行。
2.2CO的分离技术方案中所用的PSA-CO技术是由北大先锋科技公司开发的具有自主知识产权的专利技术,第一套工业性的示范装置于2002年2月开车并投入运行,目前还有几套工业装置正在建设中。
该技术中所用的PU-I吸附剂已获得中国、美国、加拿大专利,获得1991年国家新产品证书。
它同5A分子筛相比,尤其是从含N:的混合气体中分离CO时,前者CO回收率≥85%,而后者约为40%,前者纯度可达98.5%,后者约为96%,且有设备费用少、电耗低的优点。
羰基合成醋酸对CO质量要求较高,要求CO含量≥98%,CO2含量≤5×10-6,对N2、H2、CH4也有一定的要求,否则影响反应的经济性。
北大先锋科技公司的PSA-CO技术可满足这些要求。
2.3羰基合成醋酸和醋酐技术我国对于羰基合成醋酸和醋酐技术的研究与开发始于上世纪80年代,是“八五”攻关项目之一。
中科院化学所经过多年的工作,在催化剂的制造、性能测试、合成工艺与设备等方面均取得了一定的成果,研制出的催化剂的某些性能已超过国外水平。
其第—套工业性示范装置,即丹化集团20kt/a醋酐装置于2003年5月投产,经过1a多的试运行,指标达到了设计要求。
西南化工研究院用自己开发的技术设计的两套200kt/a羰基合成醋酸装置目前也正在兴建中。
用国内技术设计羰基合成醋酸装置与醋酐装置已成为现实,我国也由此成为世界上拥有该技术的少数国家之一。
2.4其他技术方案中用的制O2、净化、合成甲醇以及压缩机等国内均已有成熟技术配套。
3方案分析(1)目前我国的醋酸工业正处于快速发展时期,改变生产规模小、原料路线落后的状况是首要解决的课题。
本方案不仅从根本上解决了这两大问题,且采用了国内近几年来开发的羰基合成及相关的煤气化、PSA-CO、低压合成甲醇技术,它将使我国煤化工十大产业化体系技术之一的醋酸—醋酐及乙酰化学品体系工艺技术实现国产化,并迅速向世界先进行列迈进。
(2)方案以粉煤为原料,不仅使原料成本大大下降,且可实现醋酸工业向煤源丰富的地区转移。
华北和中原地区是我国煤的重要产地,相对而言醋酸工业却较薄弱,方案为这些地区发展醋酸工业提供了可行的技术。
(3)甲醇、醋酸上下游产品实现一体化,可降低原料成本,提高醋酸的市场竞争能力。
(4)选用灰熔聚粉煤气化技术,可实现CO2返炉作为气化剂;选用PSA-CO技术减轻了变换负荷,重新回收醋酸合成后排放气中CO,其尾气作为合成甲醇原料气。
这些技术方案的选择不仅使资源得到了合理的利用,而且减少了污染物排放,将使未来的醋酸工业成为环境友好工程。
4结语我国的醋酸工业正在调整原料和生产工艺路线,调整中充分利用了我国煤源丰富的优势,用粉煤为原料,生产甲醇、CO,再采用羰基合成法生产醋酸,这是发展煤基能源化工的一条可行之路,且可实现原料本地化、上下游产品一体化的发展战略。
它的实现必将推动醋酸工业的升级换代,提高醋酸产品在国内外市场的竞争能力。
(收稿日期:2005-10-21)60kt/a液氨及副产80kt/a碳酸氢铵产品。
(2)醇氨比可以根据焦炉气气量大小及甲醇系统、合成氨系统状况调节。
(3)生产装置可完全国产化。
参考文献1宋维瑞,等.甲醇工学[M].北京:化学工业出版社,1991.2冯元琦.甲醇联产[M].北京:化学工业出版社,1994.3冯元琦.甲醇生产操作问答[M].北京:化学工业出版社,20034李贤报.氮肥工艺设计手册[S].北京:化学工业出版杜,1989.(收稿日期:2005-10-21)2006年第27卷(上接第3页)!!!!!!!!!!!!!!!!!!!!!!!!!!!!!!!!!!!!!!!!!!!!6。