铸件常见问题及改善
铸造的问题汇总 和处理

常见铸造问题汇总砂孔一、气孔铸件表面不规则的分布了许多细小呈圆形的针孔。
#形成原因不适当的铸造/石膏温度。
在铸造时过高的温度导致石膏内硫酸钙分解,释放出二氧化硫。
由于重量较髙的产品能储存更多的热量,所以在重量较高的产品上更容易找到这些气孔。
旧物料受到污染。
铸造物料受到污染在铸造时受热分解出气体,进而在铸件表面形成气泡。
过高的温度让石膏产生分解,过低的温度又令金属浇铸不到位。
故在此平衡的过程中,水口的粗细及水口的数量就成为平衡的关键。
收缩砂孔铸件表面上出现一些十分细小、几乎看不到的小孔。
形成原因1.水口的位置或水口的粗细不够,在凝固时,水口周围的金属首先凝固,导致铸件未能在有效凝固前充满,进而形成收缩沙孔。
2.尽量避免突然转弯以减少湍流,水口太粗或太细都容易产生收缩砂孔。
三,氧化砂孔K金铸件,在表面打磨后出现很多孔洞。
形成原因1.铸件混用旧料或易氧化补口,在浇铸时高温分解,产生气体进而在产品内部产生砂眼。
使用火枪或没有保护气体覆盖下的熔铸金属,容易产生此类砂孔。
四、包含物砂孔在铸件表面形成一些不规则的孔洞。
形成原因1.物料内混入硼砂等杂质,形成包含物砂孔。
铸料使用前尽量清洁干净,熔料时尽量少用或不用硼砂。
—、结晶面在厚身的铸件表面上出现一些结晶状粗糙面。
形成原因1.铸料内金料与其它物质熔融时产生合金,合金结晶时会呈现锯齿形状,正常铸造时流动的金液对结晶缝隙进行填充,若浇铸温度过高,会造成石膏分解产生气体,此气体挤压金液,进而呈现出结晶金属原本的锯齿状外形。
厚身铸件出现结晶面时需要降低铸造及石膏盅温度,同时如有必要须加阔水口以补偿温度降低带来的流动性降低。
薄身铸件则需要降低温度的同时加压以补偿温度降低带来的流动性降低。
铸造铸件常见缺陷原因与解决方法分析

铸造铸件常见缺陷原因与解决方法分析前言铸造工艺过程复杂,影响铸件质量的因素很多,往往由于原材料控制不严,工艺方案不合理,生产操作不当,管理制度不完善等原因,会使铸件产生各种铸造缺陷。
常见的铸件缺陷名称、特征和产生的原因,详见下表。
★ 常见铸件缺陷及产生原因★缺陷名称特征产生的主要原因气孔在铸件内部或表面有大小不等的光滑孔洞①炉料不干或含氧化物、杂质多;②浇注工具或炉前添加剂未烘干;③型砂含水过多或起模和修型时刷水过多;④型芯烘干不充分或型芯通气孔被堵塞;⑤春砂过紧,型砂透气性差;⑥浇注温度过低或浇注速度太快等缩孔与缩松缩孔多分布在铸件厚断面处,形状不规则,孔内粗糙①铸件结构设计不合理,如壁厚相差过大,厚壁处未放冒口或冷铁;②浇注系统和冒口的位置不对;③浇注温度太高;④合金化学成分不合格,收缩率过大,冒口太小或太少砂眼在铸件内部或表面有型砂充塞的孔眼①型砂强度太低或砂型和型芯的紧实度不够,故型砂被金属液冲入型腔;②合箱时砂型局部损坏;③浇注系统不合理,内浇口方向不对,金属液冲坏了砂型;④合箱时型腔或浇口内散砂未清理干净粘砂铸件表面粗糙,粘有一层砂粒①原砂耐火度低或颗粒度太大;②型砂含泥量过高,耐火度下降;③浇注温度太高;④湿型铸造时型砂中煤粉含量太少;⑤干型铸造时铸型未刷涂斜或涂料太薄夹砂铸件表面产生的金属片状突起物,在金属片状突起物与铸件之间夹有一层型砂①型砂热湿拉强度低,型腔表面受热烘烤而膨胀开裂;②砂型局部紧实度过高,水分过多,水分烘干后型腔表面开裂;③浇注位置选择不当,型腔表面长时间受高温铁水烘烤而膨胀开裂;④浇注温度过高,浇注速度太慢铸件沿分型面有相对位置错移①模样的上半模和下半模未对准;②合箱时,上下砂箱错位;③上下砂箱错型未夹紧或上箱未加足够压铁,浇注时产生错箱冷隔铸件上有未完全融合的缝隙或洼坑,其交接处是圆滑的①浇注温度太低,合金流动性差;②浇注速度太慢或浇注中有断流;③浇注系统位置开设不当或内浇道横截面积太小;④铸件壁太薄;⑤直浇道(含浇口杯)高度不够;⑥浇注时金属量不够,型腔未充满浇不足铸件未被浇满裂纹铸件开裂,开裂处金属表面有氧化膜①铸件结构设计不合理,壁厚相差太大,冷却不均匀;②砂型和型芯的退让性差,或春砂过紧;③落砂过早;④浇口位置不当,致使铸件各部分收缩不均匀★ 常见铸件缺陷及预防措施★序缺陷名称缺陷特征预防措施1 气孔在铸件内部、表面或近于表面处,有大小不等的光滑孔眼,形状有圆的、长的及不规则的,有单个的,也有聚集成片的。
常见压铸件缺陷解决方法
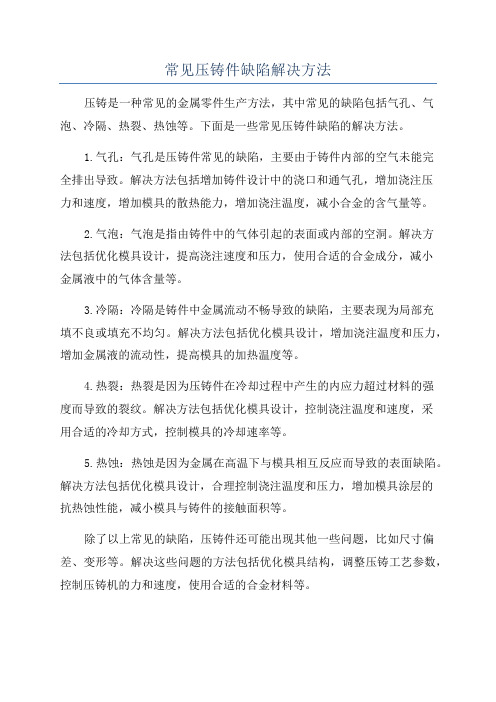
常见压铸件缺陷解决方法
压铸是一种常见的金属零件生产方法,其中常见的缺陷包括气孔、气泡、冷隔、热裂、热蚀等。
下面是一些常见压铸件缺陷的解决方法。
1.气孔:气孔是压铸件常见的缺陷,主要由于铸件内部的空气未能完
全排出导致。
解决方法包括增加铸件设计中的浇口和通气孔,增加浇注压
力和速度,增加模具的散热能力,增加浇注温度,减小合金的含气量等。
2.气泡:气泡是指由铸件中的气体引起的表面或内部的空洞。
解决方
法包括优化模具设计,提高浇注速度和压力,使用合适的合金成分,减小
金属液中的气体含量等。
3.冷隔:冷隔是铸件中金属流动不畅导致的缺陷,主要表现为局部充
填不良或填充不均匀。
解决方法包括优化模具设计,增加浇注温度和压力,增加金属液的流动性,提高模具的加热温度等。
4.热裂:热裂是因为压铸件在冷却过程中产生的内应力超过材料的强
度而导致的裂纹。
解决方法包括优化模具设计,控制浇注温度和速度,采
用合适的冷却方式,控制模具的冷却速率等。
5.热蚀:热蚀是因为金属在高温下与模具相互反应而导致的表面缺陷。
解决方法包括优化模具设计,合理控制浇注温度和压力,增加模具涂层的
抗热蚀性能,减小模具与铸件的接触面积等。
除了以上常见的缺陷,压铸件还可能出现其他一些问题,比如尺寸偏差、变形等。
解决这些问题的方法包括优化模具结构,调整压铸工艺参数,控制压铸机的力和速度,使用合适的合金材料等。
总的来说,解决压铸件缺陷的方法需要综合考虑材料、模具设计、工艺参数等多个因素,通过不断的实验和改进来提高铸件的质量。
常见压铸件缺陷及解决方法
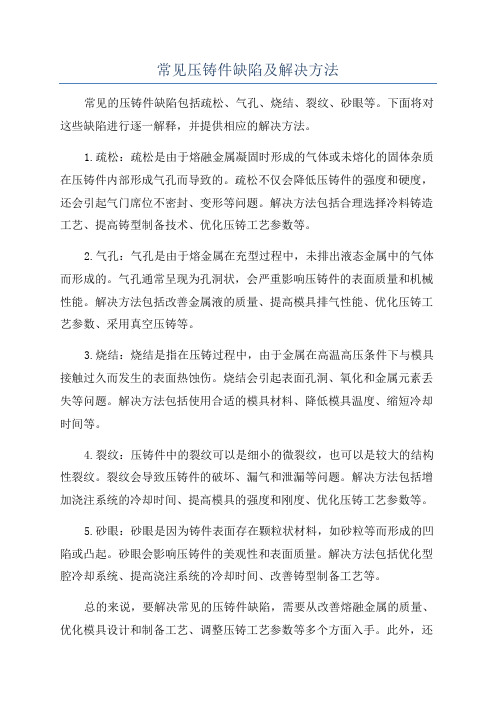
常见压铸件缺陷及解决方法常见的压铸件缺陷包括疏松、气孔、烧结、裂纹、砂眼等。
下面将对这些缺陷进行逐一解释,并提供相应的解决方法。
1.疏松:疏松是由于熔融金属凝固时形成的气体或未熔化的固体杂质在压铸件内部形成气孔而导致的。
疏松不仅会降低压铸件的强度和硬度,还会引起气门席位不密封、变形等问题。
解决方法包括合理选择冷料铸造工艺、提高铸型制备技术、优化压铸工艺参数等。
2.气孔:气孔是由于熔金属在充型过程中,未排出液态金属中的气体而形成的。
气孔通常呈现为孔洞状,会严重影响压铸件的表面质量和机械性能。
解决方法包括改善金属液的质量、提高模具排气性能、优化压铸工艺参数、采用真空压铸等。
3.烧结:烧结是指在压铸过程中,由于金属在高温高压条件下与模具接触过久而发生的表面热蚀伤。
烧结会引起表面孔洞、氧化和金属元素丢失等问题。
解决方法包括使用合适的模具材料、降低模具温度、缩短冷却时间等。
4.裂纹:压铸件中的裂纹可以是细小的微裂纹,也可以是较大的结构性裂纹。
裂纹会导致压铸件的破坏、漏气和泄漏等问题。
解决方法包括增加浇注系统的冷却时间、提高模具的强度和刚度、优化压铸工艺参数等。
5.砂眼:砂眼是因为铸件表面存在颗粒状材料,如砂粒等而形成的凹陷或凸起。
砂眼会影响压铸件的美观性和表面质量。
解决方法包括优化型腔冷却系统、提高浇注系统的冷却时间、改善铸型制备工艺等。
总的来说,要解决常见的压铸件缺陷,需要从改善熔融金属的质量、优化模具设计和制备工艺、调整压铸工艺参数等多个方面入手。
此外,还需要采用适当的检测手段,如金相分析、X射线检测、超声波检测等,对压铸件进行质量检验,及时排除可能存在的缺陷。
铸造中常见缺陷及其处理方法
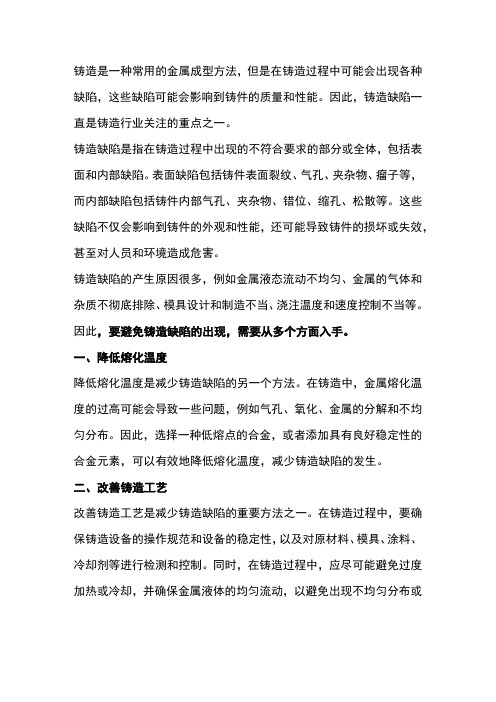
铸造是一种常用的金属成型方法,但是在铸造过程中可能会出现各种缺陷,这些缺陷可能会影响到铸件的质量和性能。
因此,铸造缺陷一直是铸造行业关注的重点之一。
铸造缺陷是指在铸造过程中出现的不符合要求的部分或全体,包括表面和内部缺陷。
表面缺陷包括铸件表面裂纹、气孔、夹杂物、瘤子等,而内部缺陷包括铸件内部气孔、夹杂物、错位、缩孔、松散等。
这些缺陷不仅会影响到铸件的外观和性能,还可能导致铸件的损坏或失效,甚至对人员和环境造成危害。
铸造缺陷的产生原因很多,例如金属液态流动不均匀、金属的气体和杂质不彻底排除、模具设计和制造不当、浇注温度和速度控制不当等。
因此,要避免铸造缺陷的出现,需要从多个方面入手。
一、降低熔化温度降低熔化温度是减少铸造缺陷的另一个方法。
在铸造中,金属熔化温度的过高可能会导致一些问题,例如气孔、氧化、金属的分解和不均匀分布。
因此,选择一种低熔点的合金,或者添加具有良好稳定性的合金元素,可以有效地降低熔化温度,减少铸造缺陷的发生。
二、改善铸造工艺改善铸造工艺是减少铸造缺陷的重要方法之一。
在铸造过程中,要确保铸造设备的操作规范和设备的稳定性,以及对原材料、模具、涂料、冷却剂等进行检测和控制。
同时,在铸造过程中,应尽可能避免过度加热或冷却,并确保金属液体的均匀流动,以避免出现不均匀分布或过热的情况,从而减少铸造缺陷的发生。
三、质量检测和控制质量检测和控制是减少铸造缺陷的关键步骤之一。
在铸造完成后,应对铸件进行全面的检测和控制包括X射线检测、超声波检测、金相分析、硬度测试等。
通过这些检测和控制方法,可以及时发现铸造缺陷,及时采取措施进行修复或重新铸造,从而保证铸件的质量和稳定性。
四、培养专业人才铸造行业的专业人才对于减少铸造缺陷的重要性不言而喻。
铸造行业需要拥有一批专业的技术人员和工人,他们能够理解和掌握铸造技术的各个方面,并能够在实践中灵活应对各种情况。
因此,铸造企业应该加强人才培养和引进工作,提高行业整体素质,从而减少铸造缺陷的发生。
铸造工艺缺陷及解决措施
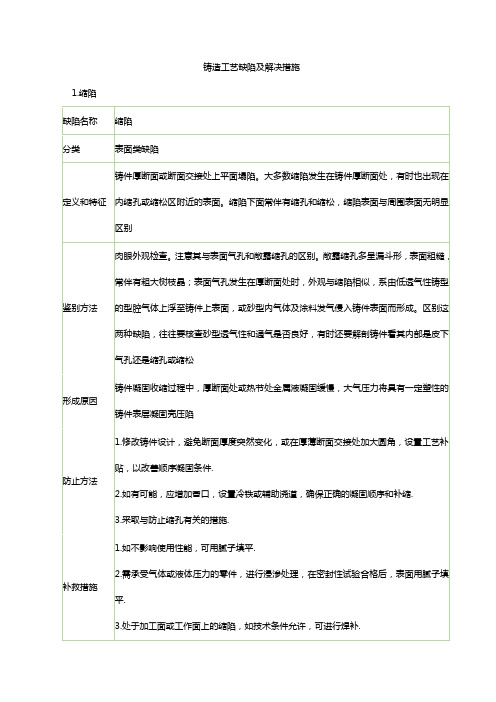
1.使用耐火度高的细粒原砂.
2.采用再生砂时,去除过细的砂粒、死烧粘土、灰分、金属氧化物、废金属、铁包砂及其他有害杂质,提高再生砂质量。定期补充适量新砂.
3.水是强烈氧化剂,应严格控制湿型砂水分,加入适量煤粉、沥青、碳氢化合物等含碳材料,在砂型中形成还原性气氛。但高压造型时应减少含碳材料加入量,以减少发气量.
防止方法
浇注前浇包中应备有足以充满铸型的金属液;浇注速度适当,浇注操作遵守工艺规程.
补救措施
概率因子
0.7
缺陷名称
未浇满
分类
残缺类缺陷
定义和特征
鉴别方法
形成原因
上箱过矮,金属的静压力小,易发生未浇满.
防止方法
保证有足够的液态金属压头充满型腔.
补救措施
浇注前浇包中应备有足以充满铸型的金属液;浇注速度适当,浇注操作遵守工艺规程
保证压铁的重量,箱夹的强度,数量足够,并选择合适的位置.
补救措施
概率因子
0.5
缺陷名称
跑火
分类
残缺类缺陷
定义和特征
鉴别方法
形成原因
金属液充型剧烈,易使型芯破裂造成跑火缺陷
防止方法
控制浇温,充型要平稳.
补救措施
概率因子
0.3
4.脉纹
缺陷名称
脉纹
分类
多肉类缺陷
定义和特征
鉴别方法
形成原因
硅砂在573℃发生相变膨胀,浇注时铸型表面易产生裂纹.
概率因子
3.跑火
缺陷名称
跑火
分类
残缺类缺陷
定义和特征
鉴别方法
形成原因
砂箱的接合面未清理干净封箱不妥等因素使跑火缺陷容易发生
防止方法
铸造件问题原因及措施
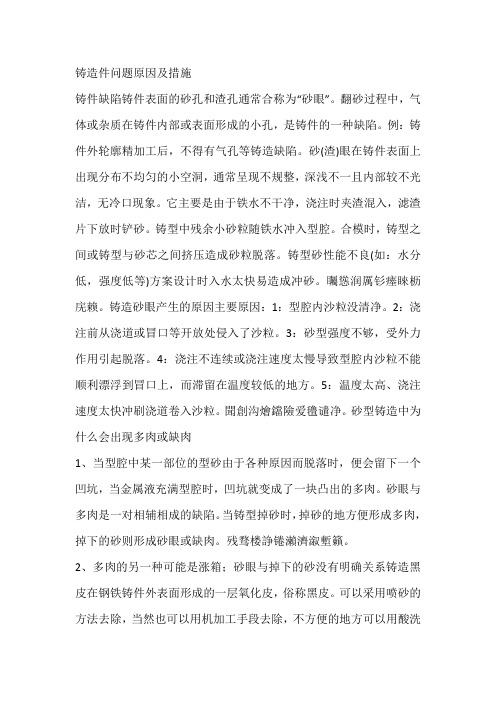
铸造件问题原因及措施铸件缺陷铸件表面的砂孔和渣孔通常合称为“砂眼”。
翻砂过程中,气体或杂质在铸件内部或表面形成的小孔,是铸件的一种缺陷。
例:铸件外轮廓精加工后,不得有气孔等铸造缺陷。
砂(渣)眼在铸件表面上出现分布不均匀的小空洞,通常呈现不规整,深浅不一且内部较不光洁,无冷口现象。
它主要是由于铁水不干净,浇注时夹渣混入,滤渣片下放时铲砂。
铸型中残余小砂粒随铁水冲入型腔。
合模时,铸型之间或铸型与砂芯之间挤压造成砂粒脱落。
铸型砂性能不良(如:水分低,强度低等)方案设计时入水太快易造成冲砂。
矚慫润厲钐瘗睞枥庑赖。
铸造砂眼产生的原因主要原因:1:型腔内沙粒没清净。
2:浇注前从浇道或冒口等开放处侵入了沙粒。
3:砂型强度不够,受外力作用引起脱落。
4:浇注不连续或浇注速度太慢导致型腔内沙粒不能顺利漂浮到冒口上,而滞留在温度较低的地方。
5:温度太高、浇注速度太快冲刷浇道卷入沙粒。
聞創沟燴鐺險爱氇谴净。
砂型铸造中为什么会出现多肉或缺肉1、当型腔中某一部位的型砂由于各种原因而脱落时,便会留下一个凹坑,当金属液充满型腔时,凹坑就变成了一块凸出的多肉。
砂眼与多肉是一对相辅相成的缺陷。
当铸型掉砂时,掉砂的地方便形成多肉,掉下的砂则形成砂眼或缺肉。
残骛楼諍锩瀨濟溆塹籟。
2、多肉的另一种可能是涨箱;砂眼与掉下的砂没有明确关系铸造黑皮在钢铁铸件外表面形成的一层氧化皮,俗称黑皮。
可以采用喷砂的方法去除,当然也可以用机加工手段去除,不方便的地方可以用酸洗的方法去除。
有这层氧化皮后,由于这层氧化皮可能脱落,外观变得不好看,不易采取油漆电镀等防腐措施,如果浸在液体中使液体出现杂质。
应该讲没有多少正面作用。
酽锕极額閉镇桧猪訣锥。
1、提高浇铸温度,采用保温冐口,铁水防氧化保护。
适当增加加工余量2、有可能是加工时刀具磨损过度导致刀具和零件产生摩擦产生的。
请检查更换刀具。
3、适当增加加工余量1常见的铸造缺陷有哪些形成的原因及解决办法一、气孔形成原因:1.液体金属浇注时被卷入的气体在合金液凝固后以气孔的形式存在于铸件中2.金属与铸型反应后在铸件表皮下生成的皮下气孔3.合金液中的夹渣或氧化皮上附着的气体被混入合金液后形成气孔解决方法及修补1.浇注时防止空气卷入2.合金液在进入型腔前先经过滤网以去除合金液中的夹渣、氧化皮和气泡3.更换铸型材料或加涂料层防止合金液与铸型发生反应4.在允许补焊部位将缺陷清理干净后进行补焊二、疏松形成原因1.合金液除气不干净形成疏松2.最后凝固部位不缩不足3.铸型局部过热、水分过多、排气不良解决方法及修补1.保持合理的凝固顺序和补缩2.炉料静洁3.在疏松部位放置冷铁4.在允许补焊的部位可将缺陷部位清理干净后补焊三、夹杂形成原因1.外来物混入液体合金并浇注人铸型2.精炼效果不良3.铸型内腔表面的外来物或造型材料剥落解决方法及修补1.仔细精炼并注意扒查2.熔炼工具涂料层应附着牢固3.浇注系统及型腔应清理干净4.炉料应保持清洁5.表面夹杂可打磨去除,必要时可进行补焊四、夹渣形成原因1.精炼变质处理后除渣不干净2.精炼变质后静置时间不够3.浇注系统不合理,二次氧化皮卷入合金液中2.4精炼后合金液搅动或被污染解决方法及修补1.严格执行精炼变质浇注工艺要求2.浇注时应使金属液平稳地注入铸型3.炉料应保持清洁,回炉料处理及使用应严格遵守工艺规程五、裂纹形成原因1.铸件各部分冷却不均匀2.铸件凝固和冷却过程受到外界阻力而不能自由收缩,内应力超过合金强度而产生裂纹解决方法及修补1.尽可能保持顺序凝固或同时凝固,减少内应力2.细化合金组织3.选择适宜的浇注温度4.增加铸型的退让性六、偏析形成原因合金凝固时析出相与液相所含溶质浓度不同,多数情况液相溶质富集而又来不及扩散而使先后凝固部分的化学成分不均匀解决方法1.熔炼过程中加强搅拌并适当的静置2.适当增加凝固冷却速度七、成分超差形成原因1.中间合金或预制合金成分不均匀或成分分析误差过大2.炉料计算或配料称量错误3.熔炼操作失当,易氧化元素烧损过大4.熔炼搅拌不均匀、易偏析元素分布不均匀解决方法1.炉前分析成分不合格时可适当进行调整2.最终检验不合格时可会同设计使用部门协商处理八、针孔形成原因合金在液体状态下溶解的气体(主要为氢),在合金凝固过程中自合金中析出而形成的均布形成的孔洞解决方法及修补1.合金液体状态下彻底精炼除气2.在凝固过程中加大凝固速度防止溶解的气体自合金中析出3.3铸件在压力下凝固,防止合金溶解的气体析出4.炉料、辅助材料及工具应干燥彈贸摄尔霁毙攬砖卤庑。
常见铸件缺陷及其预防措施

铸件缺陷常见铸件缺陷及其预防措施1).冷紋:原因:熔汤前端的温度太低,相叠时有痕迹.改善方法:1.检查壁厚是否太薄(設計或制造) ,较薄的区域应直接充填.2.检查形狀是否不易充填;距离太远、封閉区域(如鳍片(fin) 、凸起) 、被阻挡区域、圆角太小等均不易充填.並注意是否有肋点或冷点.3.缩短充填时间.缩短充填时间的方法:…4.改变充填模式.5.提高模温的方法:…6.提高熔汤温度.7.检查合金成分.8.加大逃气道可能有用.9.加真空裝置可能有用.2).裂痕:原因:1.收缩应力.2.頂出或整缘时受力裂开.改善方式:1.加大圆角.2.检查是否有热点.3.增压时间改变(冷室机).4.增加或缩短合模时间.5.增加拔模角.6.增加頂出銷.7.检查模具是否有錯位、变形.8.检查合金成分.3).气孔:原因:1.空气夾杂在熔汤中.2.气体的来源:熔解时、在料管中、在模具中、离型剂.改善方法:1.适当的慢速.2.检查流道转弯是否圆滑,截面积是否渐減.3.检查逃气道面积是否够大,是否有被阻塞,位置是否位於最后充填的地方.4.检查离型剂是否噴太多,模温是否太低.5.使用真空.4).空蚀:原因:因压力突然減小,使熔汤中的气体忽然膨胀,冲击模具,造成模具損伤.改善方法:流道截面积勿急遽变化.5).缩孔:原因:当金属由液态凝固为固态时所占的空间变小,若无金属补充便会形成缩孔.通常发生在较慢凝固处.改善方法:1.增加压力.2.改变模具温度.局部冷却、噴离型剂、降低模温、.有时只是改变缩孔位置,而非消缩孔.6).脫皮:原因:1.充填模式不良,造成熔汤重叠.2.模具变形,造成熔汤重叠.3.夾杂氧化层.改善方法:1.提早切換为高速.2.缩短充填时间.3.改变充填模式,浇口位置,浇口速度.4.检查模具強度是否足夠.5.检查銷模裝置是否良好.6.检查是否夾杂氧化层.7).波紋:原因:第一层熔汤在表面急遽冷却,第二层熔汤流過未能将第一层熔解,却又有足夠的融合,造成組织不同. 改善方法:1.改善充填模式.2.缩短充填时间.8).流动不良产生的孔:原因:熔汤流动太慢、或是太冷、或是充填模式不良,因此在凝固的金属接合处有孔.改善方法:1.同改善冷紋方法.2.检查熔汤温度是否稳定.3.检查模具温充是否稳定.9).在分模面的孔:原因:可能是缩孔或是气孔.改善方法:1.若是缩孔,減小浇口厚度或是溢流井进口厚度.2.冷却浇口.3.若是气孔,注意排气或捲气問题.10).毛边:原因:1.鎖模力不足.2.模具合模不良.3.模具強度不足.4.熔汤温度太高.11).缩陷:原因:缩孔发生在压件表面下面.改善方法:1.同改善缩孔的方法.2.局部冷却.3.加热另一边.12).积碳:原因:离型剂或其他杂质积附在模具上.改善方法:1.减小离型剂喷洒量.2.升高模温.3.选择适合的离型剂.4.使用软水稀釋离型剂.13).冒泡:原因:气体捲在铸件的表面下面.改善方式:1.減少捲气(同气孔).2.冷却或防低模温.14).粘模:原因:1.鋅积附在模具表面.2.熔汤冲击模具,造成模面损坏.改善方法:1.降低模具温度.2.降低划面粗糙度.3.加大拔模角.4.镀膜.5.改变充填模式.6.降低浇口速度序缺陷名称缺陷特征预防措施1气孔在铸件内部、表面或近于表面处,有大小不等的光滑孔眼,形状有圆的、长的及不规则的,有单个的,也有聚集成片的。
- 1、下载文档前请自行甄别文档内容的完整性,平台不提供额外的编辑、内容补充、找答案等附加服务。
- 2、"仅部分预览"的文档,不可在线预览部分如存在完整性等问题,可反馈申请退款(可完整预览的文档不适用该条件!)。
- 3、如文档侵犯您的权益,请联系客服反馈,我们会尽快为您处理(人工客服工作时间:9:00-18:30)。
铸件成型不良原因 及解决对策 -------不良点、 原因分析、 改
善对策
第 一 章
铸件成 型不良 点
1、 消水 崩模(增肉) 2、裂痕 浇口杂质 3、断裂 BOSS 消水 4、顶凸 顶出针异常 NG 5、凹陷 变形
原因分析 原因分析 原因分析 原因分析 原因分析 原因造成
10、
11、
12、
13、
14、
6、断柱 桔皮
15、
7、黏模 吃肉
原因分析
16、
原因造成
8、尺寸 NG 气孔 9、顶针下沉 气泡
原因造成
17、
18、
返 回 主 页
第二章
铸件成型不良原因分析
1-1、 可能造成消水的原因
1)
金属液温度太低
对策
2)
模具温度太低
对策
3)
料管与鹅颈管温度偏低
对策
4)
压铸设备磨损老旧
对策
5)
射控功能不正常
对策
6)
压铸压力太低
对策
7)
最大压铸流量太小
对策
8)
金属液供料不足
对策
9)
流道设计不良
对策
10) 铸件厚度过薄
对策
11) 离型剂未喷干
对策
12) 离型剂倍数过浓
对策
13) 无溢流井致使冷料排出不足
对策
14) 顶出针下沉过多
对策
15) 模穴漏水或漏油
对策
16) 镁汤料质不佳(氧化物)
对策
17) 溢流井过大造成拉料
对策
返回上一
返 回 主 页
2-1、可能造成裂痕的原因:
1)汤流交汇;
2)铸件上有不当之直角;
3)铸件冷裂痕;
4)汤流太强;
5)铸件拉模;
6)铸件肉厚不均;
3-1、可能造成断裂的原因1)结构强度不良
2)铸件顶出不均
3)溢流井过大或过小
4)铸件拉料
5)铸件拖痕造成断裂
6)拔模角度不够7)产品肉厚不均
8)流道设计不良
9)产品造型复杂
4-1、可能造成顶凸的原因1)模具侧墙BOSS肋骨放电花粗糙或倒包
2)模具顶针分布不均
3) 模具上拔模角度太小
5-1、可能造成凹陷的原因1)铸件肉厚不均
2)铸件压力太低
3) 铸件公模拉模
6-1、可能造成断柱的原因1)消水造成断柱
2)人员摆置方向(全检)3)调平手法
4)抛光撞击断柱
5)拔模角度不佳
6)底部未加R角
7)模具放电倒包
7-1可能造成黏模的原因1)造型复杂
2)放电痕粗糙
3)拔模斜度过小
4)研磨抛光精度不够
5)特征处未打顶出针或顶出针太小
6)人为因素敲伤
7)汤流激射造成黏模
8)铸件肉厚不均
9)崩模造成黏模
8-1可能造成尺寸NG的原因
1)芯轴尺寸NG
2)铸件肉厚NG
3)铸件上BOSSNG
4)铸件长宽NG 5)铸件肋骨NG
9-1、可能造成顶出针下沉的原因
1)模具顶针太长,造成铸件顶出针下沉太多
2)模具顶出针断掉
3)模具顶针太短造成铸件顶针上浮太多
10-1、可能造成崩模的原因
1)模具结构太弱2)模具靠破面太小
3)模具冲蚀
4)模具硬度不够
5)模具老化
6) 焊补后崩模
11-1、可能造成杂质的原因1)镁料杂质
2)炉底杂质
3)镁汤表面浮渣
4)坩锅密合不良。