《FMEA失效模式及效应分析》讲义
HFMEA失效模式及效应分析案例医学知识讲解讲义

2、等级医院评审标准中对高危药品使用管理有严格要求。
检核以下条件:
□警讯事件显示该事件会危及病人安全
∨内部异常事件报告显示经常发生或高严重度
□外部的资料显示该事件经常发生或高严重度
□欲导入一个新系统或新流程
其他 无
步骤2:组成团队
FMEA团队名称 晨曦团队
Healthcare FMEA 工作单
YES
YES
三、填写HFMEA工作单
Healthcare FMEA工作单
1. 流程步骤
B2护士处理医嘱
2. 可能失效模式 3. 造成失效的原因
核对错误 专业知识欠缺
未核对
工作不认真
4. 严重程度 5. 发生频率 6. 严重指数 7. 决策(行动或停止) 8. 行动(排除、控制、接受) 9. 描述所采取的行动内涵
明确进针角度
E3-6:抽取相应胰岛素剂量
E3-7:胰岛素注射
三、填写HFMEA工作单
Healthcare FMEA工作单
1. 流程步骤
A1主治医生查房告知住院医师并记录
2. 可能失效模式 3. 造成失效的原因 4. 严重程度 5. 发生频率 6. 严重指数 7. 决策(行动或停止) 8. 行动(排除、控制、接受) 9. 描述所采取的行动内涵 10. 成效量测 11. 负责人 12. 管理阶层是否同意该措施
闫瑞英
12. 管理阶层是否同意该措施
YES
YES
知识欠缺 3 2 6
停止
三、填写HFMEA工作单
Healthcare FMEA工作单
1. 流程步骤
E3胰岛素注射流程
2.
可能失效模式
注射胰岛素技 术欠规范
{品质管理FMEA}FMEA失效模式与效应分析讲义大全

此处是大标题样稿字样十五字以内講授內容A、入門班頁次一· 產品風險與可靠度------------------------------------------- 1二 · FMEA基本的概念-------------------------------------------- 5三 · 設計FMEA表填寫說明--------------------------------------- 20四 · 製程FMEA表填寫說明--------------------------------------- 41五 · FMEA實施步驟----------------------------------------------- 56B、實用班六 · FMEA精義與要項說明-------------------------------一、產品風險與可靠度1、什麼是QS-9000?Quality System 9000是美國汽車工業的品質管理系統,以持續改善為目標,強調缺點預防,降低品質差異,減少生產線的浪費與廢棄物。
QS-9000訂定了美國三大汽車公司,福特,克萊斯勒,通用汽車公司,以及卡車製造業者,和其他相關產業,的品質標準,作為內外服務、零件、材料供應的要求規範。
福特 Q -101品質管理系統標準通用汽車 NAOTargets for Excellence克萊斯勒供應商品質保證手冊一、產品風險與可靠度1. 面對市場開放與日本車的競爭壓力,美國福特汽車、克萊斯勒、與通用汽車等三大車廠共同主導制訂QS 9000品質系統,並結合美國品管學會(ASCQ)與車輛工程學會(SAE),開始研究如何將可靠度之失效預防觀念工程技術導入車輛業。
↖善用現有之可靠度工程分析工具 (如FMEA、FTA 等) 作為前端工程作業,以提供開發產品過程中之工程決策支援,並發展新的前端工程分析工具。
FMEA失效模式与效应分析课件

該方法 的檢測 能力有 多好?
12
功能方塊圖範例
原子筆範例
墨水 墨水管
筆蕊頭
筆蕊
筆管
尾蓋
筆前蓋
13
原子筆功能方塊圖範例
完整功能範圍
作記號 適合手指運用 顯示資訊
墨水管
儲存墨水 輸送墨水 配合筆蕊頭
墨水
作記號 維持順暢
筆蕊頭
固定墨汁管 固定筆蕊心 輸送墨水 配合筆管
筆管
固定筆蕊頭 固定尾蓋 顯示資訊 適合手指運用
(16)
(16)
(17)
(18)
(19)
(20)
(21) (22) (22) (22) (22)
11
FMEA表各欄位關連性說明.
項目 功能 潛在 失效模式 潛在 失效效應
後果是 什麼?
嚴重 度 分類 (S)
有多 糟糕?
潛在原因/ 設備失效
發生 度(O)
現行管制 預防 檢測
難檢 風險優先數 度 RPN (D)
8
國際間採用FMEA之狀況.
1.ISO 9004 8.5 節FMEA作為設計審查之要項。
2. CE標誌認證,以FMEA作為安全分析方法。 3.ISO 14000,以FMEA作為重大環境影響面分 析與改進方法。 4.QS 9000 以FMEA作為設計與製程失效分析方法。
9
FMEA作業流程
組成FMEA小組 資料蒐集 釐訂FMEA計畫 建立功能方塊圖 產品結構樹 可靠度展開(QFD) 決定分析之項目功能 FMEA報告 N 設計審查 Y 紀錄保存
流出源>>
2.對失效的產品進行分析,找出零組件之 失效模式,鑑定出它的失效原因,研究 該項失效模式對系統會產生什麼影響。
FMEA失效模式与效应分析(ppt 108页)

大綱
一、簡介(含起源、目的及思考方向) 二、FMEA方法介紹(含目的、表格及欄位說明、分析領域) 三、FMEA實施流程(含單機及系統) 四、FMEA實例說明(水供應系統、DAP製程、氣瓶櫃系統) 五、FMEA分組演練(DAP製程) 六、JSA補充說明 七、危害分析方法於工廠之應用(輔以DAP製程說明) 八、FMEA結語
危險性工作場所FMEA
一、簡介危害分析方法之起源
起源及實施之產業 (1)起源核能電廠、飛彈系統(1950年代) (2)高危害製造廠石油煉製廠、化工廠、半導體廠、光電廠 (3)製造廠鋼鐵廠、造紙廠….等 (4)非製造型產業(部分實施)
銀行、保險、證券、律師事務所…等 (5)政府單位之業務執掌(少部分實施) 救災體系、疾病管制局、衛生單位..等,事前之分析與對策。
(一)設備資料…等:
(1)硬體示意圖(含硬體元件相關資料) (2)空白表格 (3)製程條件相關資料 (4)維修制度及記錄 (Alarm及Interlock系統)
(二)參與人員
FMEA分析人員、製程工程師、維修工程師
危險性工作場所FMEA
三、FMEA實施流程 (三) 系統運作流程:
(1)元件功能說明 (2)元件功能關聯性說明 (3) Alarm及Interlock系統之運作 (3) 製程與設備維修制度之關聯運作流程
等,製程物質之毒性、爆炸性、酸鹼、腐蝕..等) (5)人為操作教育訓練、SOP以及稽核(考績配合) (6)外力環境(外人、外物、外在因素) (7)天然災害(地震、颱風、天候、溫濕度)
危險性工作場所FMEA
一、簡介危害點之思考方向
人為操作思考方向 作業型態:
(1)正常作業 (2)異常作業 (3)維修作業 (4)其它影響系統之重大作業
FMEA失效模式与效应分析课件(PPT 82张)

过程流程图
• 初始过程流程图 从预料的材料和产品/过程方案中得出 的预期加工过程的描述 • 过程流程图 描述材料的整个加工流程,包括任何 的返工和修理操作
prepared by liuliangcheng, Not copy without permission.
什么是 FMEA ?
1 . 对失效的产品进行分析,找出零组件之失效模 式,鑑定出它的失效原因,研究该项失效模式对系 统会产生什么的影响。
2. 失效分析在找出零组件或系统的潜在弱点,提供 设计,制造,品保等单位采取可行之对策。
prepared by liuliangcheng, Not copy without permission.
prepared by liuliangcheng, Not copy without permission.
典型的FMEA s
系统
部件 子系统 主系统
注意:将系统的 失效模式降为最小
设计
部件 子系统 主系统 注意:将设计的 失效模式降为最小
过程
人 机 料 法 环 测
注意:将全过程的 失效模式降为最小 目标:最大化的 全过程质量、 可靠性、成本 和可维护性
prepared by liuliangcheng, Not copy without permission.
Agenda
• • • • • 掌握FMEA的概念和运用时机。 D- FMEA填写说明 P- FMEA填写说明 FMEA范例解说 Q&A
prepared by liuliangcheng, Not copy without permission.
prepared by liuliangcheng, Not copy without permission.
讲义-Fmea-失效模式效应分析1019台中班

FMEA的基本概念
哪一個 零組件? 會有什麼 效應(後果)? 後果有多糟? 有什麼改善方法? -設計變更 -製程變更 -特別的管制 -變更標準、程序 或規範
這個失效模式整 體風險高嗎? 有什麼 功能 有哪些 原因呢? 這個原因 常發生嗎?
有什麼問題(失效)? -沒有功能 -功能衰減 -不希望的功能
10 9 8 7 6 5 4 3 2 1
34
潛在失效模式(Potential Failure Mode)
零件: 1F16 晶粒 效應: 造成表面電 場不均,形成 尖端放電 後果有多糟? S=8 有什麼改善方法? -設計變更 -製程變更 -特別的管制 -變更標準、程序 或規範
功能:整流
有哪些 原因呢?
發現、評價產品/製程中潛在的失效及其效應。 找到能夠避免或減少這些潛在失效發生的措施。 書面總結上述過程。 著重預防的工具,在於確保客戶滿意。
產品設計開發初期,分析潛在失效模式與產 生原因,提出未來注意事項,建立有效的管 制計劃。
DFMEA在APQP的第二階段產品設計開發階段完成。 PFMEA在APQP的第三階段製程設計開發階段完成。
汽車產品 汽車 動力系統 引擎系統 供油系統 制動系統 電機系統 照明系統 空調系統 車身系統 前車 後車
22
核心小組(Core Team)
以設計工程師為主導集合 相關的人員 工程 生產 品質 採購 客服 等人員共同將可能發 生的問題挖掘出來。 列出參與這項工作人員姓 名、部門和電話號碼等。
備註:
不建議修改評分準則中9,10的值。 嚴重度為1分的不需要更進一步的分析。
32
潛在失效效應
效應一
嚴重度分數
針對最嚴重的 那個效應評分
FMEA失效模式与效应分析课件
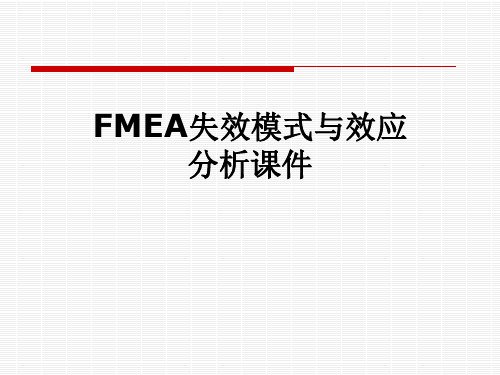
FMEA填寫說明
(10)DFMEA潛在失效模式
潛在失效模式是零件、子系統、或系統於符合設計意圖過程中 可能失效的種類。潛在失效模式也可能是較高階子系統或系統之失 效原因,或較低階零組件的失效效應。
列出特別項須發生的。
一般的失效模式包含下列各項,但不限於此:破碎的、變形 、鬆弛、洩漏、黏著、短路、生銹氧化、龜裂。
磨損。
不適當的維護作業。
金屬疲勞。
缺乏環境保護。
裝備欠流暢。
錯誤的算法。
腐蝕。
超過壓力。
25
FMEA填寫說明
(15)發生度
參考下列各要素,決定發生度等級值(1~10):
1.相似零件或子系統的過去服務歷史資料和相關經驗? 2.零件、上一階零件或分系統是否滯銷? 3.上一階零件或分系統改變程度的大小? 4.零件與上一階零件,基本上是否有差異? 5.零件是否為全新的產品? 6.零件使用條件是否改變? 7.作業環境是否改變? 8.是否運用工程分析去預估,應用此零件之發生度?
破碎的、變形、彎曲、裝訂捆綁、短路、工具磨損、不正確的 安裝、灰塵。
20
FMEA填寫說明
(11)DFMEA潛在失效效應
為被客戶查覺在功能特性上失效模式的效應。也就是失效模 式一旦發生時,對系統或設備以及操作時使用的人員所造成的影 響。一般在討論失效效應時,先檢討失效發生時對於局部所產生 的影響,然後循產品的組合架構層次,逐層分析一直到最高層級 人員、裝備所可能造成的影響。例如:由於某個間歇性的系統作 業造成某個零組件的破碎,可能造成於組合過程的震動。這個間 歇性系統作業降低了系統功效,最後引起客戶不滿意。
有三種設計管制或特徵: (1)預防原因/設備,或失效模式/效應發生,或降低發生比率。 (2)偵測原因或設備,並提出矯正措施。 (3)偵測失效模式。
失效模式与效果分析《FMEA》课件
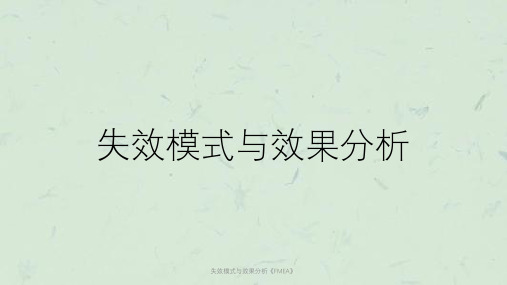
1.4 为目什的么: 进行FMEA
使用系统性FMEA方法减少潜在的失效模式和与之相关 的各种原因从而达到降低或消除过程、产品和服务中各类潜 在问题带来的负面影响。
原因1
原因2 原因3
失效模式
负面影响
失效模式与效果分析《FMEA》
1.4 为什么进行FMEA FMEA为什么? 问题: 1、某机型计划在下个月导入一种新主板,不知走目前的导入流 程/测试项目是否能保证其导入后不出现质量波动?
FMEA
DFMEA PFMEA
失效模式与效果分析《FMEA》
1.3 FMEA的重要的特征
特征1:防患于未然
设计时预见水烧干了 ,没发现!
设计时增加震片报警
开始烧水时预见水烧 干了,没发现!
增加每5分钟就去看 一次的步骤
失效模式与效果分析《FMEA》
1.3 FMEA的重要的特征
特征1:防患于未然
失效发现得太迟的后果?
4
每 2 小时测一 7
196
加 控 制 工程
加设备
714
间过短
路,半焊
次
装 置 2009/10/3 CPK 1.56
/SPC
3、浸锡角 短路增加 7 II 传送带角度变 1
NO
10
70
每 3 天 工程
概率低,难 7 1 6
度过小
化
测 一 次 2009/9/30 度大,暂不
角度
处理
板弯
4
IQCห้องสมุดไป่ตู้
5
140
1960 1974 1976 70后期 80前期 80中期 1991 1994
失效模式与效果分析《FMEA》
- 1、下载文档前请自行甄别文档内容的完整性,平台不提供额外的编辑、内容补充、找答案等附加服务。
- 2、"仅部分预览"的文档,不可在线预览部分如存在完整性等问题,可反馈申请退款(可完整预览的文档不适用该条件!)。
- 3、如文档侵犯您的权益,请联系客服反馈,我们会尽快为您处理(人工客服工作时间:9:00-18:30)。
FMEA分析流程
先期規劃
2. 資料收集 一般而言在執行FMEA之前應掌握以下 几個方面的資料﹕ A.有關產品設計方面的資料。 B.有關制造工藝方面的資料。 C.有關使用維修方面的資料。 D.有關環境方面的資料。
FMEA分析流程
先期規劃
3. 訂定FMEA執行方案 根據FMEA之實際需要或合約的要求擬 定FMEA執行方案﹐據以執行FMEA﹐ 并隨制程之修正而更新FMEA﹐且將分 析結果提供作為制程設計參考。通常 FMEA執行方案中要規定的項目說明如 下﹕
FMEA分類
• SYSTEM FMEA:主要用于系統方面潛在 失效模式分析. • DESIGE FMEA:主要用于產品制造前設 計階段失效模式分析 • PROCESS FMEA:主要用于產品制造及 裝配階段失效模式分析 • SERVICE FMEA:主要用于產品送到客 戶前所有服務失效模式分析
FMEA分析流標准要求
• 4.2.3.4 產品安全性 供方在設計控制(要素4.4)和過程控制(4.9)的方 針及規程中, 必須考慮適當的安全防護和產品 安全性,. 供方應促使內部人員了解其產品的安 全因素. • 4.2.3.5 過程失效模式及后果分析(PFMEA) PFMEA必須考慮所有的特殊特性, 必須努力 改進過程,以防止發生缺陷, 而不是找出缺陷. 某 些顧客要求在生產件批準前進行FMEA評審和 批準(見第II部分),參見潛在失效模式及後果分 析參考手冊.
FMEA使用時機
1. 一般的原則, FMEA之使用要越早越好,如此才能 消除或減少設計錯誤的發生 2. 當設計新的系統、產品、零件、製程、設備時,在 作概念設計或草圖時即可開始作 FMEA
3. 當系統、產品、零件、製程、設備有變更時
4. 當現有的系統、產品、零件、製程、設備有新的應 用時 5. 當現有的系統、產品、零件、製程、設備被考慮要 改善時
FMEA之應用
QS9000標准要求
• 4.2.3.1 產品質量先期策劃(APQP) • 供方必須建立和實施產品質量先期策劃程 序. 供方應建立內部多功能小組, 為新產品或更 改產品進行生產準備. 這些小組應采用產品質 量先期策劃和控制計劃參考手冊中適當的技術, 也可采用能達到同樣效果的類似技術. • 小組活動應包括: 特殊特性的開發和最終確定(見附錄C) 失效模式及后果分析的開發和評審 制定措施,優先減少高風險順序數的潛在失效 模式 控制計劃的制定或評審
FMEA之歷史
• 同時代初期﹐美國軍方也開始應用FMEA技 朮﹐并于1974年出版軍用標准 MIL-STD1629A﹐沿用至今。目前此標准仍為全世界重 要之FMEA參考標准之一。 • 1970年代,美國汽車工業受到國際間強大的競 爭壓力﹐不得不努力導入國防與太空工業之可 靠度工程技朮FMEA﹐以提高產品品質可靠度.
FMEA之應用
在品質管理應用
預見問題
設計
1$
解決問題
開發 制造
發現問題
用戶端
1000$
10$
100$
DFMEA
PFMEA
FMEA之應用
在品質管理應用
產品設計 DFMEA(ODM) 產品工程評估(OEM) 模具設計(DFMEA) 模具工程評估 制程設計評估(CAE/DOE) PFMEA(持續) TVR 工程量試品質分析改善 生產量試品質分析改善 FAI CPK GRR \SPC\模具可靠性稽核 RMA\FAE\供應商管理
FMEA之歷史
• 1985年由國際電工委員會(IEC)所出版之 FMEA國際標准<<IEC 812>>即為參考美 軍標准MIL-STD-1629A加以部分修改而 成之FMEA作業程序。 • 除此之外﹐目前的國際品質系統ISO9000 及歐洲產品CE標志之需求﹐都將FMEA 視為重要的設計管制分析方法。
先期規劃
FMEA分析流程
分析制程特性 定義製造流程 分析失效模式 分析失效原因 分析發生率 分析現行控制方法 分析難檢度 計算風險優先數
主流程
分析產品特性
分析失效效應 分析嚴重度
決定優先改善之失效模式
建議改善措施
改善實施
失效模式及效應分析表單格式
_______系統
_______子系統
2 3 _______零件部______ 設計責任______ 5 機型/料號________ 6 關鍵日期______ 1 FMEA編號______
( )
9
10
11
12
13
14
15
16
17
18
19
20
21
22
失效模式及效應分析表單格式
•1.FMEA編號:填入FMEA文件的編號,以便查詢; •2.項目:填入所分析的系統、子系統或零件的過 程名稱、編號; •3.設計/過程責任:部門、小組還應包括供方的名 稱; •4.填入負責準備FMEA工作的工程師姓名、電話 及所在公司名稱; •5.機型/料號:填入將使用和正被分析的設計過程 影響的預期的機型和料號;
FMEA 失效模式與影響分析
(Failure Mode & Effect Analysis)
內容提要
• FMEA之歷史
• FMEA之應用 • FMEA之定義 • FMEA使用時機 „ FMEA分類 • FMEA分析流程 • 失效模式及效應分析表單格式 • 設計 FMEA之作業程序 • 制程 FMEA之作業程序
內容提要
„嚴重度S • 發生率O • 難檢度D • 風險優先數(關鍵性指數)RPN
• • • • •
FMEA的益處 實施FMEA應注意的問題 設計FMEA與制程FMEA之區別 FMEA在FOXCONN FMEA的作業范例
FMEA之歷史
„亡羊補牢 ,猶未為晚(出自“戰國策” ) “我聽說過,看見兔子牙想起獵犬,這還不 晚﹔羊跑掉了才補羊圈,也還不遲。……” “亡羊補牢”這句成語,便是根據上面約兩句 話而來的,表達處理事情發生錯誤以后, 如果趕緊去挽救,還不為遲的意思。例如一個 事業家,因估計事情的發展犯了錯誤,輕舉冒 進,陷入失敗的境地。但他并不氣餒,耐心地 將事情再想了一遍,從這次的錯誤中吸取教 訓,認為“亡羊補牢”,從頭做起,還不算晚 呢!
FMEA分析流程
先期規劃
3. 訂定FMEA執行方案 A.表格形式 B.分析硬品或制程之層次 I.分析最低層次以能夠對其功能做完 整描述為准。 II.從高層之分析結果判斷。 III.根據以往經驗決定分析的最低層次。 IV.以剛好高于維修保養的最低層次為主
FMEA分析流程
3. 訂定FMEA執行方案 C.編碼系統 D.失效定義 E.成果整合 F.時程
FMEA之應用
QS9000標准要求
4.4.5.1設計輸出補充 供方的設計輸出必須是如下過程的結果﹐包 括﹕ • 努力簡化、優化、創新及減少浪費(如QFD、 DFM/DFA、VE、DOE、公差研究、響應面方法或其 它適當的替代方法) • 需要時﹐使用幾何尺寸和公差 • 成本/性能/風險的權衡分析 • 使用試驗、生產和現場的反饋信息 • 使用設計FMEA
失效模式及效應分析表單格式
•14.潛在失效的起因/機理 •潛在失效起因是指一個設計/工藝薄弱部分的跡象,其作用 結果就是失效模式 •15.頻度(0):頻度是指某一特定失效起因或機理(已列於前 欄中)出現的可能性. •16.現行設計/工藝控制; •17.探測度(D) •18.風險順序數RPN •19.建議措施: • 如果對某一特定原因無建議措施,那麼就在該欄中寫 “無”
FMEA之應用
技術發展現狀
• 目前﹐FMEA已經廣泛應用在航空﹑航 天﹑電子﹑機械﹑電力﹑造船和交通運 輸等產業﹐根據美國國防部所屬的112個 單位進行的調查顯示﹐有87個單位認為 FMEA是一種有效的可靠度分析技朮﹐ 值得推廣。
FMEA之應用
• • • • •
技術發展與應用
可靠性分析技術 系統化工程設計輔助工具 利用表格進行工程分析 在設計階段早期發現問題 及早謀求解決措施
失效模式及效應分析表單格式
•10.潛在失效模式: • 對一個特定項目及其功能,列出每一個潛在失效模式, 前提是這種失效可能發生,但不一定發生; •11.潛在失效后果: • 潛在失效后果,就是失效模式對系統功能的影響; •12.嚴重度(S) •13.分級(重要程度) • 用於對另件、子系統或系統的產品特性分級:關鍵、 主要、 重要、生點等;
先期規劃
主流程 結果應用
FMEA分析流程
組成FMEA團隊
產品設計 制造工藝 使用維修 環境
先期規劃
資料收集
表格格式 分析層次
訂定執行方案
失效定義
成果整合 時機
FMEA分析流程
先期規劃
1. 組成FMEA團隊 FMEA為一系統化輔助工具﹐此一失效 分析工具必然會牽涉到公司內很多部 門﹑人員與各種技朮﹐因此有必要利用 團隊方式進行。
FMEA之應用
美國三大汽車公司之要求
• 八十年代后﹐許多汽車公司開始開發內部之 FMEA手冊﹐并逐步將其分為設計FMEA和制 程FMEA﹐并開始要求供應商對其所供應的零 件進行設計FMEA和制程FMEA﹐并將其視為 供應商的重點考核項目。但由于各公司的要求 不同﹐造成供應商的額外負擔和困擾﹐因此為 改善這一現象﹐福特﹑克萊斯勒﹑通用汽車等 三家汽車公司在美國品管學會和汽車工業行動 組的協助下﹐整合各汽車公司之規定與表格﹐ 在1993年完成失效模式與效應分析參考手冊﹐ 確立胃FMEA在汽車的必要性﹐并統一了其分 析程序與表格。
FMEA之定義
FMEA: Failure Mode and Effects Analysis
• FMEA是一種以失效為討論重點的設計輔助工 具﹐系利用表格方式進行工程分析﹐在工程設 計時早期發現潛在缺陷及其影響程度﹐以便及 早謀求解決之道﹐避免失效之發生或降低其發 生時產生之影響。 • 目的---防患於未然 • 本質------工程分析