天然气制氢培训课件
最新制氢培训讲义

制氢培训讲义制氢装置设计及改造情况1、大连西太平洋石油化工有限公司制氢装置规模为6×104Nm3/h。
两套加氢、脱硫、转化炉、中变采用国内技术;净化系统为变压吸附法,技术为德国林德(Linde)公司专利,引进控制计算机、成套阀门、管线、仪表和吸附剂,吸附罐为国内制作,林德公司制造技术。
设计单位为中国石化北京设计院。
本装置由下列五部分组成:(1)原料油干法加氢、脱硫部分(2)转化及相应对流段热回收部分(3)中温变换及变换气换热冷却部分(4)PSA中变气净化部分(5)开工及循环氢压缩机及酸性水汽提部分装置的加氢、脱硫、转化、中变过程采用两个系列。
PSA部分则为一个系列。
原料设计时以轻质油(重整拔头油或轻石脑油)为主,同时应用少量液化气和ARDS装置弛放干气。
98年7月至今,由于重整装置停工未开,制氢原料改为重整精制油。
产品纯度为H2>99.9%。
产品主要供常渣油加氢脱硫(ARDS)装置、蜡油加氢精制装置及煤柴油加氢精制装置、聚丙烯用。
施工图设计于1992年12月末完成,1995年末基本建成,1997年7月正式投产。
1998年2月经标定达到设计规模,生产稳定,质量良好。
2.生产装置工艺原理本制氢工艺采用以轻质油(重整拔头油或轻石脑油)为原料.经干法加氢、脱硫后与水蒸汽混合,经催化剂转化产生H2、CO及CO2。
转化气再经中温变换将CO与转化气中水蒸汽反应成CO2同时再产生部分H2。
中变气经换热、冷却分液后进往PSA吸附部分脱除中变气的CH4、CO和CO2,生产纯度为99 9%(v)的氢。
RS+H2→R+H2SH2S+Z n O→Z n S+ H2 OR+ H2 O→CH4+CO+CO2CH4+ H2 O→3 H2+CO-QCO+ H2 O→H2+CO2+Q3.生产装置工艺流程详述本装置设计原料主要是重整拔头油,工艺流程大致可分为五部分:(设计条件)(1)原料脱硫部分(分A、B两系列,以A系列为例,下同)40℃的重整拔头油自装置外进原料缓冲罐D-101,经原料泵P-101/1升压至4.0MPa。
制氢操作培训课件
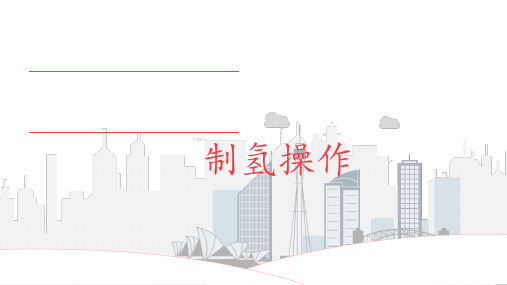
脱硫单元
• 系统循环量的控制 • 出系统粗氢气产品质量的控制 • 系统腐蚀的控制 • 胺液的降解 • 消泡剂的添加 • 气化脱硫与MDEA脱硫对比
脱硫单元
• (1)系统循环量的控制
•
富液循环量要<543m3/h,流速过快容易导致腐蚀
•
变换装置出口至T4201该段管线伴热不用投用
尽可能低,减少饱和水夹带以及灰尘夹带。(带水意味着带灰)
待蒸汽超过临界值后随着系统温度的升高压力会逐渐稳定。
• (2)进料温度控制
•
主要从系统物料平衡考虑
• (3)出料温度的监控
•
T4103出口温度
磷酸盐加药装置操作
• 低于30cm配置药剂,最终加水量控制在100cm。 • 搅拌器待药剂完全溶解后停运。 • 加药量根据系统补水负荷、排污量、磷酸根含量、PH及时调整。
引申:
系统压力的控制
1、系统气量 2、变换反应的好坏 3、脱硫循环量、溶剂温度的控 制、再生效果的好坏。 4、VPSA/PSA的有效吸附。 5、压缩机的运行情况。
变换催化剂的维护
• 4催化剂毒物
•
砷含量(煤中含有砷元素)
•
砷的主要来源为原料煤,气化装置使用的烟煤中砷的含量一般为
0.75~176ppm。工艺气中的砷含量为煤中所含砷的14%~22%,其余存在于粗渣
合物发生了分子链的无规则断裂、侧基和低分子的消除反应,致使聚合度
和相对分子质量下降。
•
①温度高降解
•
128℃,设计采用150℃ 蒸汽,待压缩单元正常运行后采用的是200℃
蒸汽。温度的控制要严格执行工艺指标。
•
②与氧气接触降解
脱硫单元
• (5) 消泡剂的添加 • 在胺液运行过程中加入消泡剂应慎重考虑。必须在确认溶剂已经发泡后
制氢培训讲义
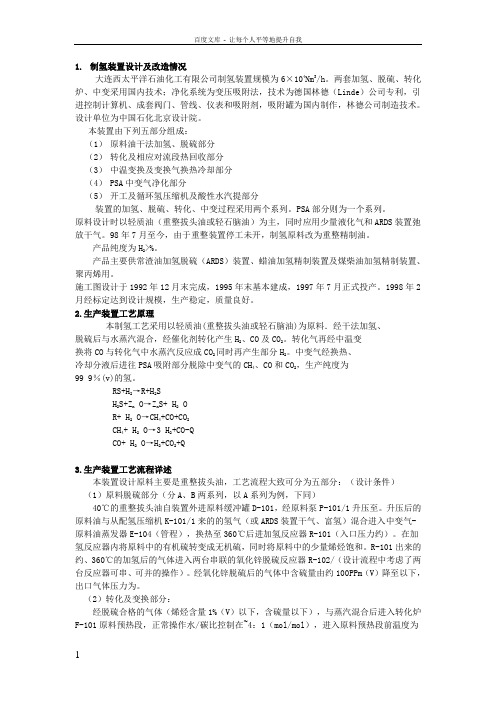
1.制氢装置设计及改造情况大连西太平洋石油化工有限公司制氢装置规模为6×104Nm3/h。
两套加氢、脱硫、转化炉、中变采用国内技术;净化系统为变压吸附法,技术为德国林德(Linde)公司专利,引进控制计算机、成套阀门、管线、仪表和吸附剂,吸附罐为国内制作,林德公司制造技术。
设计单位为中国石化北京设计院。
本装置由下列五部分组成:(1)原料油干法加氢、脱硫部分(2)转化及相应对流段热回收部分(3)中温变换及变换气换热冷却部分(4)PSA中变气净化部分(5)开工及循环氢压缩机及酸性水汽提部分装置的加氢、脱硫、转化、中变过程采用两个系列。
PSA部分则为一个系列。
原料设计时以轻质油(重整拔头油或轻石脑油)为主,同时应用少量液化气和ARDS装置弛放干气。
98年7月至今,由于重整装置停工未开,制氢原料改为重整精制油。
产品纯度为H2>%。
产品主要供常渣油加氢脱硫(ARDS)装置、蜡油加氢精制装置及煤柴油加氢精制装置、聚丙烯用。
施工图设计于1992年12月末完成,1995年末基本建成,1997年7月正式投产。
1998年2月经标定达到设计规模,生产稳定,质量良好。
2.生产装置工艺原理本制氢工艺采用以轻质油(重整拔头油或轻石脑油)为原料.经干法加氢、脱硫后与水蒸汽混合,经催化剂转化产生H2、CO及CO2。
转化气再经中温变换将CO与转化气中水蒸汽反应成CO2同时再产生部分H2。
中变气经换热、冷却分液后进往PSA吸附部分脱除中变气的CH4、CO和CO2,生产纯度为99 9%(v)的氢。
RS+H2→R+H2SH2S+Z n O→Z n S+ H2 OR+ H2 O→CH4+CO+CO2CH4+ H2 O→3 H2+CO-QCO+ H2 O→H2+CO2+Q3.生产装置工艺流程详述本装置设计原料主要是重整拔头油,工艺流程大致可分为五部分:(设计条件)(1)原料脱硫部分(分A、B两系列,以A系列为例,下同)40℃的重整拔头油自装置外进原料缓冲罐D-101,经原料泵P-101/1升压至。
天然气制氢简介演示
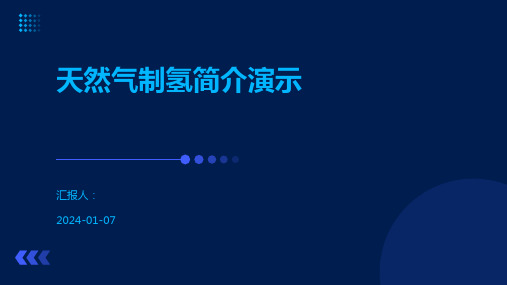
THANKS
谢谢您的观看
甲醇生产
甲醇是重要的化工原料, 也是燃料添加剂,天然气 制氢可用于甲醇的生产。
石油工业
在石油工业中,天然气制 氢可用于石油加工和裂化 等过程,提高石油产品的 质量和产量。
氢能源汽车
燃料电池汽车
氢燃料电池汽车是未来可持续交 通的重要组成部分,天然气制氢 可以为燃料电池汽车提供清洁的 能源。
混合动力汽车
将天然气经过净化处理,除去 其中的硫、氯等杂质,得到纯
净的甲烷气体。
反应
将纯净的甲烷气体与水蒸气在 催化剂的作用下进行反应,生
成氢气和二氧化碳。
产物分离
通过一系列的物理和化学方法 ,将生成的氢气和二氧化碳进 行分离,得到高纯度的氢气。
氢气压缩
将得到的氢气进行压缩,以便 于储存和运输。
02
天然气制氢的技术
天然气制氢的原理
天然气的主要成分是甲烷(CH4), 在一定条件下,甲烷与水蒸气反应生 成氢气和二氧化碳,反应方程式为: CH4 + (x+1)H2O → H2 + CO2 + xH2O。
反应过程中需要使用催化剂来加速反 应,同时需要控制反应温度和压力。
天然气制氢的工艺流程
01
02
03
04
原料准备
天然气制氢简介演示
汇气制氢的技术 • 天然气制氢的应用 • 天然气制氢的挑战与前景 • 天然气制氢的案例分析
01
天然气制氢概述
天然气制氢的定义
• 天然气制氢:是指利用天然气为原料,通过化学反应将天 然气中的主要成分甲烷转化为氢气的过程。
资源消耗
大规模的天然气制氢需要大量的水资 源和土地资源,对环境产生一定压力 。
制氢车间HAZOP培训课件
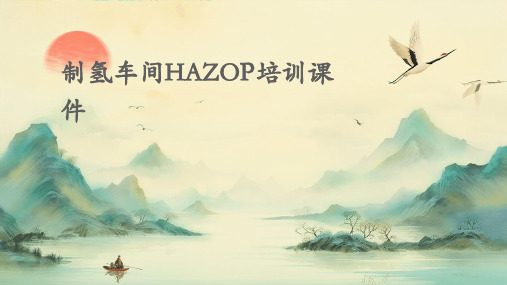
执行分析
按照分析计划,对制氢车间的工 艺流程进行逐一分析,使用引导 词系统对每个节点进行偏差识别 和风险评估。
风险矩阵与安全措施评估
根据分析结果,制定风险矩阵, 对每个风险进行等级划分,评估 现有安全措施的有效性,并提出 相应的改进建议。
引导词系统与使用
定义引导词 根据制氢车间的工艺特点和操作 条件,选择合适的引导词,如流 量、压力、温度、液位等,用于 描述工艺参数的偏差。
培训安排
为期一周的集中培训,每天6小时,共 计30小时。培训对象为制氢车间的操 作员、工艺工程师和技术人员。
培训效果评估与改进
评估方式
通过理论考试、小组讨论和个人报告等形式对培训效果进行评估。
改进措施
根据评估结果,对培训内容和方式进行改进,以提高培训效果和质量。同时, 定期组织复训和更新培训课件,以适应制氢车间工艺和安全要求的变化。
制氢车间HAZOP培训课 件
• HAZOP简介 • HAZOP基本概念 • HAZOP分析方法 • HAZOP分析实践 • HAZOP培训与提升 • HAZOP应用与发展趋势
01
HAZOP简介
HAZOP的定义
是一种基于风险的评估方法,用于识别和评估工艺系统中的潜在危险和操 作问题。
通过分析工艺流程图和操作规程,HAZOP研究确定可能发生的偏离,并 评估这些偏离对人员、环境和设备的影响。
分析实施与记录
成立分析小组
组建具备HAZOP分析经验和制氢 车间知识的专业团队。
实施分析
按照HAZOP分析的步骤和方法, 对制氢车间的工艺流程、设备、 操作等进行全面分析,识别潜在 的危险和操作偏差。
记录分析结果
详细记录每个偏差及其潜在的风 险和后果,为后续评估和报告编 写提供依据。
天然气制氢

天然气制氢1.制氢原理1.天然气脱硫本装置采用干法脱硫来处理该原料气中的硫份。
为了脱除有机硫,采用铁锰系转化吸收型脱硫催化剂,并在原料气中加入约1~5%的氢,在约400℃高温下发生下述反应:RSH+H2=H2S+RHH2S+MnO=MnS+H2O经铁锰系脱硫剂初步转化吸收后,剩余的硫化氢,再在采用的氧化锌催化剂作用下发生下述脱硫反应而被吸收:H2S+ZnO=ZnS+H2OC2H5SH+ZnO=ZnS+C2H4+H2O氧化锌吸硫速度极快,因而脱硫沿气体流动方向逐层进行,最终硫被脱除至0.1ppm以下,以满足蒸汽转化催化剂对硫的要求。
2 蒸汽转化和变换原理原料天然气和蒸汽在转化炉管中的高温催化剂上发生烃---蒸汽转化反应,主要反应如下:CH4+H2O→CO+3H2-Q (1)一氧化碳产氢 CO + H2O----CO2 + H2+Q (2)前一反应需大量吸热,高温有利于反应进行;后一反应是微放热反应,高温不利于反应进行。
因此在转化炉中反应是不完全的。
在发生上述反应的同时还伴有一系列复杂的付反应。
包括烃类的热裂解,催化裂解,水合,蒸汽裂解,脱氢,加氢,积炭,氧化等。
在转化反应中,要使转化率高,残余甲烷少,氢纯度高,反应温度就要高。
但要考虑设备承受能力和能耗,所以炉温不宜太高。
为缓和积炭,增加收率,要控制较大的水碳比。
3 变换反应的反应方程式如下:CO+H2O=CO2+H2+Q这是一个可逆的放热反应,降低温度和增加过量的水蒸汽,均有利于变换反应向右侧进行,变换反应如果不借助于催化剂,其速度是非常慢的,催化剂能大大加速其反应速度。
为使最终CO浓度降到低的程度,只有低变催化剂才能胜任。
高低变串联不仅充分发挥了两种催化剂各自的特点,而且为生产过程中的废热利用创造了良好的条4改良热钾碱法改良热钾碱溶液中含碳酸钾,二乙醇胺及V2O5。
碳酸钾做吸收剂、二乙醇胺做催化剂、它起着加快吸收和解吸的作用。
V2O5为缓蚀剂,可以使碳钢表面产生致密的保护膜,从而防止碳钢的腐蚀。
制氢培训
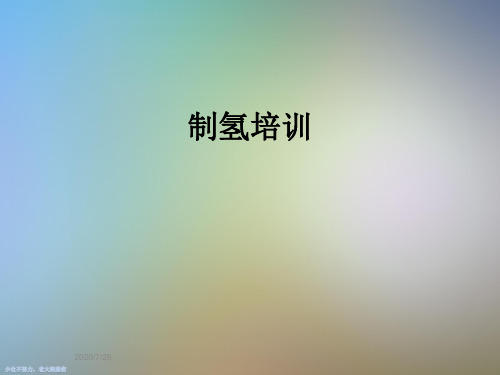
2020/7/28
工艺:路线制氢装的置选原择料和及优工化艺方案
一、制氢技术的多样化 二、轻烃蒸汽转化制氢技术方案多样化 三、制氢装置原料的多样化 四、含烯烃原料的烯烃饱和技术 五、蒸汽转化工艺条件的选择 六、中温变换工艺技术 七、关键设备:转化炉
2020/7/28
工艺路线 :
一、制氢技术的多样化
2020/7/28
制气工段
: 原料的杂质
1.1 硫含量 (进转化炉前〈0.2ppm) 1.2 氯含量 (进转化炉前〈0.2ppm) 1.3 砷含量 (进转化炉前〈1ppb) 1.4 烯烃含量(进转化炉前〈1%) 1.5、脱盐水的硫含量
2020/7/28
原料的产氢率的要求
原料的氢碳化与理论产氢量的关系
工艺技术方案的选择
2020/7/28
)
2020/7/28
制气工段 : 三、制氢装置原料的多样化
(一)原料的要求 在制氢装置的氢气成本构成中,原料和燃料费 用约占60~85%,其余水电、催化剂及化学药 剂消耗、工资、大修折旧、车间经费等只占15 ~40% 原料规格要求 原料组成 同炭数的烃类其积炭倾向为:烯烃>芳香烃>环 烷烃>烷烃 商业化的转化催化剂对原料的要求一般为:烯 烃<1%mol;芳烃含量<13%。环烷烃<36%,轻 油干点<210℃。
较为简单,主要发生上述反应,最终产品
气组成由反应②③平衡决定。
2020/7/28
蒸汽转化过程反应原理
而轻石脑油,由于其组成较为复杂,有烷 烃、环烷烃、芳烃等,因此,除上述反应外, 在不同的催化床层,还发生高级烃的热裂解、 催化裂解、脱氢、加氢、积炭、氧化、变换、 甲烷化等反应,最终产品气组成仍由反应②③ 平衡决定。
《制氢工艺技术》课件
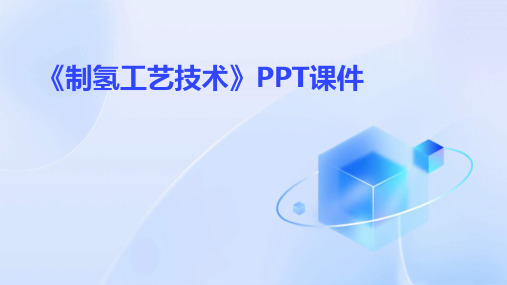
目 录
• 制氢工艺技术概述 • 制氢工艺的主要类型 • 制氢工艺技术的经济性分析 • 制氢工艺技术的发展趋势与展望
01
制氢工艺技术概述
氢气的性质与用途
氢气的性质
氢气是一种轻质、易燃易爆、无色无 味的可燃气体,具有很高的热值和能 量密度。
氢气的用途
氢气是重要的工业原料,广泛应用于 化工、石油、冶金等领域,同时也是 燃料电池的主要燃料。
环境压力
传统化石能源的使用对环境造成了巨大的压力, 发展制氢技术有助于减少温室气体排放,缓解环 境压力。
产业升级
制氢技术的发展对于推动相关产业升级和转型具 有重要意义,能够带动一系列产业链的发展。
02
制氢工艺的主要类型
天然气制氢
天然气蒸汽转化制氢
将天然气与水蒸气在高温下反应,通过转化反应将天然气转 化为氢气和一氧化碳的混合气体,再通过一氧化碳变换反应 进一步制取高纯度氢气。
制氢技术的经济性评价方法
投资回收期法
通过计算投资回报率来评估技术的经济性。
净现值法
考虑资金的时间价值,通过比较不同方案的 净现值来选择最优方案。
内部收益率法
计算投资方案的内部收益率,以评估其盈利 能力。
制氢工艺技术的经济性比较与选择
1
比较不同制氢技术的成本与效益,选择经济性更 优的方案。
2
考虑环境影响,权衡经济效益与环境成本。
开发新型反应器结构
研究新型反应器结构,提高反应器的传热、 传质性能。
加强副产物的回收与利用
副产物分离与回收
研究高效的副产物分离和回收技术, 提高副产物的回收率。
副产物资源化利用
将副产物转化为有价值的资源,实现 副产物的资源化利用。
- 1、下载文档前请自行甄别文档内容的完整性,平台不提供额外的编辑、内容补充、找答案等附加服务。
- 2、"仅部分预览"的文档,不可在线预览部分如存在完整性等问题,可反馈申请退款(可完整预览的文档不适用该条件!)。
- 3、如文档侵犯您的权益,请联系客服反馈,我们会尽快为您处理(人工客服工作时间:9:00-18:30)。
蒸汽转化过程反应原理
而轻石脑油, 由于其组成较为复杂, 而轻石脑油 , 由于其组成较为复杂 , 有烷 烃、环烷烃、芳烃等,因此,除上述反应外, 环烷烃、芳烃等,因此,除上述反应外, 在不同的催化床层,还发生高级烃的热裂解、 在不同的催化床层,还发生高级烃的热裂解、 催化裂解、脱氢、加氢、积炭、氧化、变换、 催化裂解、脱氢、加氢、积炭、氧化、变换、 甲烷化等反应,最终产品气组成仍由反应②③ 甲烷化等反应,最终产品气组成仍由反应②③ 平衡决定。 平衡决定。 烃类水蒸汽转化反应是体积增大的强吸热反 应,低压、高温、高水碳比有利于上述反应的 低压、高温、 进行。 进行。 工程设计选择:高压、高温、 工程设计选择:高压、高温、低水碳比
4、变温加氢工艺
220℃
350 ~ 380℃
原料气
适用原料: 适用原料: 烯烃含量不 限制
去转化炉 原料预热炉 变温加氢反应器 绝热加氢反应器 氧化锌脱硫反应器
绝热加氢工艺流程图
1、绝热加氢工艺
250 ~ 390℃ 原料气 320 ~ 370℃
适用原料: 适用原料: 烯烃含量小 于7%一下 一下
轻烃蒸汽转化制氢工艺流程图 轻烃蒸汽转化制氢工艺流程图
确定流程: 确定流程:
蒸气 原料 (天然气 干气 轻石脑油) 轻石脑油) 稀烃 饱和 中变 PSA 高纯氢气
脱硫
转化
燃料气
典型的制氢装置转化工艺流程图(PSA提纯法) 典型的制氢装置转化工艺流程图(PSA提纯法) 工艺流程图(PSA提纯法
原料烯烃饱和、加氢脱硫原理 原料烯烃饱和、
2、转化温度的选择
1)入口温度:500-650 °C(取决于原料) 对原料的影响 对转化反应的影响:降低了转化炉的热负荷 对燃料消耗的影响:降低燃料消耗 对外输蒸汽的影响:降低外输蒸汽量 预转化工艺的应用 2)出口温度 提高原料的转化率 降低残余甲烷含量 对转化炉炉管材料的要求 目前国内:820-860 °C
2.脱硫部分 2.脱硫部分 进入脱硫部分的原料气,进入加氢反应器 (R4001),先在加氢催化剂的作用下,发生 (R4001),先在加氢催化剂的作用下,发生 烯烃饱和反应同时发生有机硫转化反应和 有机氯的转化反应,使有机硫转化为无机 硫,有机氯转化为无机氯被脱除。然后在 进入氧化锌脱硫反应器(R4002A/B),在此氧 进入氧化锌脱硫反应器(R4002A/B),在此氧 化锌与硫化氢发生脱硫反应,脱除原料中 的硫,精制后的气体硫含量小于0.5PPm。 的硫,精制后的气体硫含量小于0.5PPm。
3 .转化部分 .转化部分 精制后的原料气在进入转化炉(F4002)之前,按一 精制后的原料气在进入转化炉(F4002)之前,按一 定的水碳比与3.5Mpa的水蒸气混合,在进转化炉 定的水碳比与3.5Mpa的水蒸气混合,在进转化炉 对流段(原料预热段)预热到500℃ 对流段(原料预热段)预热到500℃,由上集合管 500 进入转化炉辐射段。转化炉管内装有催化剂,在 催化剂的作用下,原料气与水蒸气发生复杂的转 化反应,整个反应过程表现为强吸热过程,反应 所需热量由转化炉燃烧气提供。出转化炉的高温 转化气经转化蒸汽发生器发生中压蒸汽后,温度 降至360-380℃进入中温度变换部分. 降至360-380℃进入中温度变换部分概述 5000m3N/h焦化干气制氢装置由浙江美阳国际石 5000m3N/h焦化干气制氢装置由浙江美阳国际石 化医药工程设计有限公司承担设计,由中国化学 工程第十一建设公司施工。装置由原料气压缩、 原料气精制、转化、中变、PSA、锅炉等部分组 原料气精制、转化、中变、PSA、锅炉等部分组 成.装置能力为5000-5500Nm3/h,装置设计年运转时 装置能力为5000-5500Nm3/h,装置设计年运转时 间为8000小时,年产工业氢3600T。可以满足30万吨 间为8000小时,年产工业氢3600T。可以满足30万吨 /年加氢精制装置需求。装置概算投资4200万元 。 年加氢精制装置需求。装置概算投资4200万元 工程于2004年破土,于2005年 月竣工、投产. 工程于2004年破土,于2005年9月竣工、投产.
含烯烃原料:催化干气、焦化干气
焦化干气: 焦化干气: 一般含有13~ 的氢气; ~ 的烯烃( 一般含有 ~20%的氢气;5~10%的烯烃(主要为乙烯 的氢气 的烯烃 和丙烯);其余为甲烷等饱和烷烃, );其余为甲烷等饱和烷烃 和丙烯);其余为甲烷等饱和烷烃,杂质含量中主要为有机 经过湿法脱硫后,一般含有50~ 的总硫。 硫,经过湿法脱硫后,一般含有 ~200ppm的总硫。 的总硫 催化干气: 催化干气: 一般含有20 40%的氢气 15~20%的烯烃 20~ 的氢气; 的烯烃( 一般含有20~40%的氢气;15~20%的烯烃(主要为乙烯 );15%左右的氮气,其余为甲烷等饱和烷烃, 15%左右的氮气 );15%左右的氮气,其余为甲烷等饱和烷烃,杂质含量中主 要为无机硫,经过湿法脱硫后,一般含有10 20ppm的总硫 10~ 要为无机硫,经过湿法脱硫后,一般含有10~20ppm的总硫 。 气体品质:焦化干气由于催化干气 气体品质:
3、水碳比 :影响装置能耗和催化剂的积炭 3.0-3.5(mol)(PSA工艺流程) ( 工艺流程) ) 工艺流程 4.0-5(mol)(常规工艺流程) ( ) 常规工艺流程) 4、转化催化剂 : 国内:Z417W/Z418W;Z413/Z414////Z403 ; 国内 国外: 国外: ICI ///// RNKR 。
4.中温变换部分 4.中温变换部分 由转化气蒸汽发生器(E4001)来的360-380℃ 由转化气蒸汽发生器(E4001)来的360-380℃ 转化气进入中温变换反应器,在催化剂的 作用下发生变换反应,将变换气中CO降至 作用下发生变换反应,将变换气中CO降至 3%左右。中变气经锅炉给水第二预热器预 3%左右。中变气经锅炉给水第二预热器预 热锅炉给水,锅炉给水第一预热器预热锅 炉给水,除盐水预热器预热除盐水回收大 部分预热后,在经中变器水冷器降温至40℃ 部分预热后,在经中变器水冷器降温至40℃, 并经分水后进入PSA部分。 并经分水后进入PSA部分。
去转化炉 原料预热炉 加氢反应器 氧化锌脱硫
绝热加氢工艺流程图
1、转化的基本原理
转化型式:一段转化+二段转化;一段转化
烃类水蒸汽转化主要反应有: CnHm+nH2O=nCO+(n+m/2)H2 ① CO+3H2=CH4+H2O △Ho298 =-206kJ/mol ② CO+H2O=CO2+H2 △Ho298 =-41kJ/mol ③ 以甲烷为主的气态烃,蒸汽转化过程 较为简单,主要发生上述反应,最终产品 气组成由反应②③平衡决定。
3.变压吸附(PSA) 3.变压吸附(PSA) 变压吸附是对气体混合物进行分离提纯的工艺过 程,该工艺是多孔性固体物质内部表面对气体分 子的物理吸附。混合气体中的杂质组分在高压具 有较大的吸附能力,低压下具有较小的吸附能力, 就是利用这种原理吸附剂吸附,解析达到循环吸 附解析过程 分子筛对一般气体分子的吸附顺序: 分子筛对一般气体分子的吸附顺序: H2<N2<CH4<CO<CO2 活性炭对一般气体吸附顺序: 活性炭对一般气体吸附顺序: H2<N2<CO<CH4<CO2
生产工艺过程
工艺流程简述
1.原料气压缩部分 1.原料气压缩部分 来自装置外的焦化干气进入原料油缓冲罐 (V4001),经原料气压缩机(C4001)升压后进入原 (V4001),经原料气压缩机(C4001)升压后进入原 (C4001) 料预热炉(F4001),预热至300℃ 料预热炉(F4001),预热至300℃进入脱硫部分。 本装置的备用原料为来自装置外的石脑轻油, 进入原料缓冲罐(V4002),经原料泵升压后与装 进入原料缓冲罐(V4002),经原料泵升压后与装 置外来的循环氢混合进料原料预热炉(F4001), 置外来的循环氢混合进料原料预热炉(F4001), 预热至380℃ 预热至380℃.
噻吩加氢: 噻吩加氢: C4H4S+4H4=C4H10+H2S 二硫化碳加氢:CS2+H2=CH4+H2S 二硫化碳加氢:CS2+H2=CH4+H2S 氧化锌脱硫: H2S+ZnO=ZnS+H20 2.2烃类的蒸汽转化是将烃类与蒸汽转化为H2和 2.2烃类的蒸汽转化是将烃类与蒸汽转化为H2和 CO少量残余CH4 CO少量残余CH4 CH4+H20=CO+H2 CO+H20 =CO2+H2 2.3 CO中温变换是将转化气中的CO与水蒸气继续 CO中温变换是将转化气中的CO与水蒸气继续 反应生成CO2和氢气 反应生成CO2和氢气
典型的烯烃、有机硫加氢反应有: 典型的烯烃、有机硫加氢反应有: 乙烯: 乙烯: C2H4+H2→C2H6 硫醇: 硫醇: RSH+H2→RH+H2s 硫醚: 硫醚: R1SR2+2H2→R1H+R2H+H2S 二硫醚: 二硫醚: R1SSR2+3H2→R1H+R2H+2H2S 噻吩: 噻吩: C4H4S+4H2→C4H10+H2S 氧硫化碳: 氧硫化碳: COS+H2→CO+H2S 二硫化碳: 二硫化碳: CS2+4H2→CH4+2H2S 氧化锌脱硫原理 脱氯原理 ZnO(固)+H2S=ZnS(固 ZnO(固)+H2S=ZnS(固)+H2O △ Ho 298 =-76.62kJ/mol
2. 制氢的化学反应机理 2.1 原料烃中的硫化物以多种形态存在,一般分为无机硫 化物和有机硫化物, 化物和有机硫化物, 有机硫化物不能在氧化锌脱硫剂上直 接反应被脱除,必须经加氢生成无机硫化物方可被氧化锌 脱硫及吸附脱除,有机硫化物在原料中一般由硫醇、硫醚、 二硫化物和环状硫化物等,原料气中的硫化物绝大部分是 有机硫化物。 加氢过程同样是有机氯转变为无机氯,采用高活性的金 属氧化物为活性组分,脱氯剂与氯化氢反应,被固定载体 上,达到脱出氯化物目的。 硫醇加氢: R硫醇加氢: R-SH+H2=RH+H2S 硫醚加氢: R硫醚加氢: R-S-R’+H2=RH+R’H+H2S +H2=RH+R’