挤出机螺杆熔融段的优化设计
双螺杆挤出机的螺杆设计(实用精典)
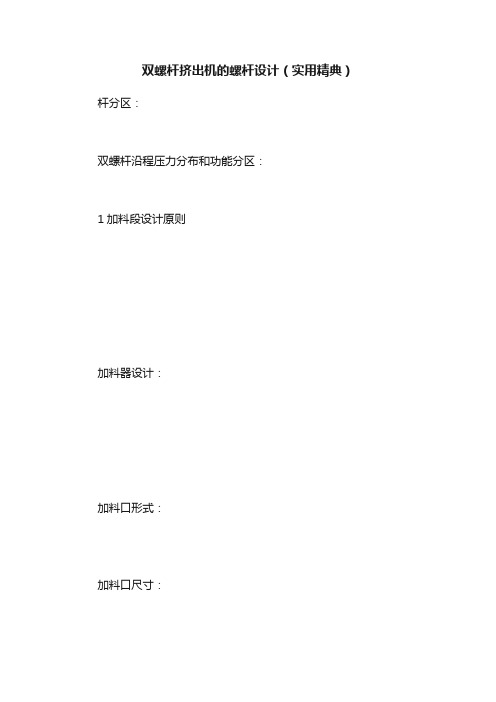
双螺杆挤出机的螺杆设计(实用精典)杆分区:
双螺杆沿程压力分布和功能分区:
1加料段设计原则
加料器设计:
加料口形式:
加料口尺寸:
粉体加料:
挤出机输送能力:
2熔融段设计原则
挤出机越大,外加热所占比越小熔融区螺杆组合设计:
3排气段设计原则:
特种工程塑料需要侧排气口:4计量段设计原则:
计量段中熔体的流动:
熔体的输送与螺纹导程的关系:螺杆头的影响:
混合型螺杆头:
5螺杆组合设计的注意事项:防止损坏或磨损:
同向双螺杆的分离力:
不同元件产生的分离力比较:内向挤压力的产生:
螺杆组合-芯轴变形的补偿:芯轴的变形及磨损:
(来源:韧科技)。
单螺杆挤出机螺杆的结构设计与优化研究

单螺杆挤出机螺杆的结构设计与优化研究[摘要]单螺杆挤出机,其属于现阶段所广泛应用的一种混合输送及挤出设备,可有效应用至食品及塑料加工相关行业当中,为确保其应用作用得到更好地发挥,便需对单螺杆挤出机内部螺杆结构实施科学合理地设计与优化。
鉴于此,本文主要检索国内关于单螺杆挤出机内部螺杆结构相关设计资料,积极探讨单螺杆挤出机内部螺杆结构总体设计及其优化[关键词]挤出机;单螺杆;螺杆结构;设计优化;前言:伴随现代加工技术及设备不断地更新优化,对单螺杆挤出机内部螺杆结构也提出更高的要求,为能充分满足其使用需求,便需对其螺杆结构实施有限元基础分析及优化设计。
因而,对单螺杆挤出机内部螺杆结构总体设计及其优化开展综合分析,有着一定的现实意义和价值。
1、关于单螺杆挤出机内部螺杆结构及其设计优化必要性分析单螺杆挤出机,其属于阿基米德的一根螺杆放置于加热料筒当中旋转所构成,其内含主轴及带座轴承、动力输入系统装置、螺杆、机筒及机架等。
螺杆,它属于单螺杆挤出机内部一个重要部件[1]。
传统设计手段之下所设计螺杆,其往往重量偏大且尺寸结构缺乏合理性,材料及其应用成本相对较高,故对单螺杆挤出机内部螺杆结构实施设计优化较为必要且重要。
2、设计优化分析2.1 在螺杆优化前期有限元基础分析层面一是,在静力学层面。
单螺杆挤出机内部,螺杆材料选取45号钢,弹性模量为210GPa,密度为7800kg·m-3,泊松比为0.3。
45号钢呈较高强度、优良机械加工操作性能,广泛应用至螺杆相关零件当中。
单螺杆挤出机,其内部螺杆结构极具复杂性,网格划分期间需着重考虑四面体的网格单元等向细化这一特点,以四面体为方式,促使网格生成。
网格单元为6mm,经划分过后,网格的节点数及其单元数分别是125176、67737,将螺杆的有限元基础模型确立起来。
结合螺杆和轴承、驱动轴相互间的配合方式,把螺杆处于轴承部位安装位置上轴向及其径向位移均设为零,并对该螺杆体则施加相应的恒定扭矩,结合各项资料,螺杆上面扭矩确定为30N·m。
挤出机螺杆的性能评价和设计

一
的8 0 % 以上 的 塑料 产 品 都是 由塑 料 制 品 炼均 匀性不 好 ,就会导 致产 品质量下 降 ,
、
螺杆 性能 的评 价指标
1 产 量与成本 。挤 出机 的产量 主要是 由螺杆决 定着 ,也是 对其进行 综合 评价 的 个重要 指标 之一 。而除此 之外 ,它 的功 率 也是衡 量产 量与 成本 的参 考物 。这些都 是 在生 产 中决 定其优 劣好 坏的标 准 。 因此 , 我 们要 着重对 其进行 对 比。 2螺 杆 的质量 问题 。在 生产 成品 中 , 成 品 的质量一 般来说 是有 外观 ,尺寸等决
2 0 1 4 N O. 0 3( 上) 的性能评价和设计
于 文 娟
( 沧州 东塑集团明珠公 司薄膜事业部 ,河北 沧州 0 6 1 0 0 1 )
摘 要. 挤 出机 螺杆 的作 用是使 胶料 随螺 杆 旋转运 动逐 渐 变为直 线运 动 , 向机 头方向推 移 , 并与机 身相 配合 , 实现压 缩 生热 、 软化搅拌 ,混合胶料等。文章结合 实际,分析 了螺杆性能的评价指标等 ,在此基础上 ,阐述了挤 出机螺杆的设计要领 , 供 大 家参 考 。 关键 词 :挤 出机螺 杆 ;熔 融 ;混 炼 ;流 变;计 量
中 图分类 号 :T Q 3 2 文 献标 识码 :A
据 目前 不 完全 统 计 ,现在 我 们 使 用 中挤 出成 型法生 产 的。而挤 出成型法 主要 是 由螺杆 挤 出机 进行 操作 ,可 以这 样说 , 挤 出机螺 杆在 实际生 产中起着 最 为重要 的 作 用 ,所 以我们 平 时要对挤 出机螺 杆性 能 进 行设计 并作评 价 ,来不 断满 足 日益生 产
一
6它 的混炼 元件分 析 。为了减 少普通 螺 杆混 炼不够 均匀 ,出现分 散混炼 现象 , 促使 产品性 能不均 匀 ,更会影 响外观 的质 我 们必须 在螺 杆 中设 置混炼 元件 。而分 散 量。 混炼元 件是有 U C 式 、E g a n 式 以及 三角槽 再次是 它 的熔 体流 变性 。一般来说 , 式屏 障段等组 成 。这 样 的作 用就 是要减 少 熔体 流变性 是指 粘性与 弹性 。粘性 是随着 熔 体 的径 向温 差 。 剪切 速率 的提高 而降低 ,根据 离模 膨胀来 7设 置开槽 衬套 或齿轮 泵时 的螺杆设 确定 熔体 的弹性 。而粘 度是 由分子 量觉得 计 分析 研究 。在进料 机筒 内设置 开槽强 制 的 ,分子量 多粘 度就会 增加 。 进料衬 套 , 主要是用 来提 高挤 出机 的性能 , 二 、螺杆 的设计分 析研究 满足实 际需要 。但是 要注 意在开 槽衬套 挤 1 第一 ,螺杆 直径 的选择 。它 的选择 出机 时候 ,要 满足较 高 的固体输 送能力 。 直接 决定着 制 品的质量 。在操 作 中要把握 这样做 的 目的是 因为在开 槽进料 段建立 了 好 直径 的选 择 ,不能 忽视 。所 以 ,螺杆直 7 0 一 l O O M p a 高 压 ,所 以要 加 以注 意 。 径 D指 螺杆螺 纹 的外 径 。螺杆有 效长 度 L 我 们 可 以这 样 操 作 ,第 一 ,螺 杆 选 指 螺杆工作 部分 长度 。有效 长度和 螺杆 总 取时 ,我们 应采用 较小 的压缩 比,压 缩 比 长 不 同。长径 比就是 螺杆有 效长 与直径 的 最 好是 1 . 第 二 ,不 断 提 高 螺 杆 的熔 融 和 比值 。 早 期的拚 出机 螺杆 的一 长径 比较小 , 混炼 能力 ,特别是 要设 置分流混 炼元 件 。 只有 1 2 — 1 6 。随着 塑料 成 型加 工工业 的发 主要 目的是 发挥开 槽衬套 段较 高的 固体输 展 ,挤 出机螺杆 的长 径 比逐 渐增大 ,目前 送能 力 。 常用 的为 1 5 、2 0 、2 5 ,最大 可达 4 3 。 为 了 提 高挤 出过 程 的稳 定 性 ,我 们 2影 响因素 的判定 。这 个判定 主要 是 可 以在 挤 出机 与机 头 之 间装设 有齿 轮 泵 。 有 排 气 口影 响 螺杆 的结 构 与 长 径 比来 定 我 们可 以让 螺杆 仅 需建 立 2 — 3 . 5 M p a 的压 的。对排 气式挤 出机 ,螺杆 要采 用多 阶结 力 ,就可 把熔体送 入齿 轮泵 中 。因此 ,螺 构 。设置 一个排 气 口 ,螺杆 为双 阶结构 ; 杆计 量段 也可采用 较深 的螺槽 ,另外 ,我 设 置两个 排气 口则为 三 阶结 构 , 以此类推 。 们 还可 以增 强螺杆 的熔融 与混 炼能 力这个 3固态塑料 的判定 。这 个主要 是指料 指标 ,这样 在实 际生产 中可 以不断 提高挤 粒间 的空隙在 内 的塑 料密度 。在 生产 中如 出机的产 量与质 量 。 果 松 密度 高于 实 际 密 度 的 5 0 %,那 么 在 参考 文献 输送过程 中就 会很 容易输 送 。原 因是螺 杆 … 1李振军 . 单 螺杆 挤 出机 螺 杆 几何 形状 进料段 螺槽 深度应 该在 0 - 1 — 0 . 2 D;压缩 在 对 熔 体 温 度 分 布 的 影 响 卟 塑胶 工 业 ,
挤出机螺杆设计问题

挤出机螺筒内装塑料并与螺杆紧密配合,为了正常操作,应注意以下重要特性。
1.螺筒要直。
2.螺筒的设计应能经受挤出机的工作压力。
这些压力可能高达
70-140MPa(10000-20000psi),在注塑中还要更高些。
3.螺筒内壁面应比挤出机螺杆更耐磨,因为螺杆比螺筒易更换,重新加工也比螺筒便宜。
4.螺筒后端的支撑应采用滑动支撑,当螺筒被加热时允许其膨胀。
刚性的支撑会引起螺筒的弯曲,可能导致螺杆和螺筒严重损坏。
5.为了改进团体输送,螺筒的加料段可以开槽。
开槽加解段应保证良好的冷却能力,以带走高摩擦产生的热,并阻止槽内堆积物料的熔融。
另外,沟槽应倾斜开,深度逐渐变浅,最大限度地减小物料在构糟内的挂料机会。
6. 如果没有搭气口,应偏置,并且开口侧壁与螺筒内壁相切,以减小塑料熔体挂在排气口前沿的机会,见图2.20。
较传统的对称式排气口设计,易使物料在排气口的底部不断堵塞。
排气口的开口处可以设计成向下倾斜的,以避免冷却物流人挤出机螺筒。
挤出机螺杆产品中心:恒锐机械。
双螺杆挤出机螺杆局部构型设计

螺杆局部构型设计根据捏合同向双螺杆挤出过程一般由固体输送、熔融、熔体输送、混合、排气等区段组成,以及同向双螺杆是组合式,即整根螺杆是由完成不同功能的螺杆区段组合而成的特点,因而整根螺杆的组合应包括两方面:一是完成不同局部功能的各种螺杆区段(即局部构型)设计,二是针对整个挤出过程完成的任务,整根螺杆的组合设计。
这里先讨论螺杆的局部构型设计。
1.加料段:此处所指的加料段,是指第一(或主)加料口下方对着的螺杆区段。
对这一段的主要要求是能顺利地、多适应性地加入物料,包括能适应各种形状的粒料、低松密度的粉料、含有纤维状添加组分的物料的加入。
据此,大螺距、正向螺纹输送元件用在此处可获得最大的加料能力。
有资料推荐这一段也可采用加大螺槽深度的螺纹元件,可使其容积输送能力超过一般标准螺纹元件,因而也可获得较大的加料能力。
下图表示的为Berstorff公司的加料段螺杆槽深度的变化情况。
对于ZE-A系列,在给定的中心距下,果敢外径D 于螺杆的根径d的比值由ZE系列的D/d=1.24加大到1.43,其后来的ZE-R 系列其D/d=1.74,这比ZE型的体积增加了2.3倍。
2.用于压缩物料的螺杆局部结构:像单螺杆挤出过程一样,在固体输送段要将松散的粉状物料压实或提高粒状料在螺槽中的充满程度。
以利于促进物料的熔融、塑化,就要设置能实现这一要求的螺杆局部结构。
分段改变螺距,使螺距由大到小,这是当前流行的组合式双螺杆通常采用的方法。
应当指出,加工低松密度的粉状物料,在组合不同导程螺纹元件时一般不会出现什么问题;但若加入的是颗粒料,则相接螺纹元件导程的变化有时会导致挤出机过载,为此在设计相邻导程变化的程度时要考虑到这点阶跃式导程变化对充满度的影响3.用于熔融塑化的螺杆局部构型:熔融塑化给定聚合物的最佳螺杆构型取决于物料的比热容、熔点、熔体粘度以及聚合物在固体状态时粒子的大小。
用于熔融、塑化的局部螺杆构型设计的目标是在设定的温度下将固体物料均匀、快速熔融。
挤出机螺杆熔融段的优化设计

πW L 2 HpL 2 2 2 ( D b - 2 H - 2δ ) + S b = [ l +π ( D b W +e l 式中 L2 — — — 螺杆熔融段长度 ; δ ) t an θ; l— — — 螺纹升程 ,l = π( D b - 2 δ— — — 螺纹顶与机筒内壁的间隙 。 式 ( 6) 中 ,机筒速度方向与物料流动方向的夹 角φ 可定义为 φ = sin - 1
V bz = Vb + V Vz =
2 2
z
根据前述的聚合物物料塑化熔融机理及目标 函数可知 ,该段的几何参数中 ,起始端槽深 H1 和 末端槽深 H3 、 棱顶宽度 e 以及螺纹升角θ对聚合 物物料塑化熔融过程影响甚大 。因此 ,取 H1 , H3 , e 和θ为设计变量 ,于是 θ,e ,H1 ,H3 ] T ( 10) X = [ x1 ,x2 ,x3 ,x4 ] T = [
212 优化结果
根据本优化设计数学模型的特点 , 应选择约 束复合形法进行寻优 ,程序采用 C + + 语言编写 , 其优化设计流程如图 3 所示 。其中 , n1 为设计变 量 ,k 为复合形顶点数 ε , 为迭代精度 α , 为反射系 数δ , 1 为容差 。设计示例为 Φ70 m m 单螺杆挤出 机 。螺杆材料用 38 CrM oA lA 氮化钢 , 取 [τ] = 7 8 4 M Pa 。 挤 出 机 技 术 参 数 为 : n m ax = 1 2 0 ε r・ m i n - 1 , N m ax = 30 k W , p = 1 ,L/ D s = 20 , 1 =
橡 胶 工 业 2002 年第 49 卷 606
(完整word版)双螺杆挤出机螺杆局部构型设计

螺杆局部构型设计依据捏合同向双螺杆挤出过程一般由固体输送、熔融、熔体输送、混淆、排气等区段构成,以及同向双螺杆是组合式,即整根螺杆是由达成不一样功能的螺杆区段组合而成的特色,因此整根螺杆的组合应包含双方面:一是达成不一样局部功能的各样螺杆区段(即局部构型)设计,二是针对整个挤出过程达成的任务,整根螺杆的组合设计。
这里先议论螺杆的局部构型设计。
1.加料段:此地方指的加料段,是指第一(或主)加料口下方对着的螺杆区段。
对这一段的主要要求是能顺利地、多适应性地加入物料,包含能适应各样形状的粒料、低松密度的粉料、含有纤维状增添组分的物料的加入。
据此,大螺距、正向螺纹输送元件用在此处可获取最大的加料能力。
有资料介绍这一段也可采纳加大螺槽深度的螺纹元件,可使其容积输送能力超出一般标准螺纹元件,因此也可获取较大的加料能力。
下列图表示的为 Berstorff 企业的加料段螺杆槽深度的变化状况。
关于 ZE-A 系列,在给定的中心距下,勇敢外径 D 于螺杆的根径 d 的比值由 ZE 系列的 D/d=1.24 加大到 1.43,以后来的 ZE-R 系列其 D/d=1.74,这比ZE 型的体积增添了 2.3 倍。
2.用于压缩物料的螺杆局部构造:像单螺杆挤出过程同样,在固体输送段要将松懈的粉状物料压实或提升粒状料在螺槽中的充满程度。
以利于促使物料的熔融、塑化,就要设置能实现这一要求的螺杆局部构造。
分段改变螺距,使螺距由大到小,这是目前流行的组合式双螺杆往常采纳的方法。
应当指出,加工低松密度的粉状物料,在组合不一样导程螺纹元件时一般不会出现什么问题;但若加入的是颗粒料,则相接螺纹元件导程的变化有时会致使挤出机过载,为此在设计相邻导程变化的程度时要考虑到这点阶跃式导程变化对充满度的影响3.用于熔融塑化的螺杆局部构型:熔融塑化给定聚合物的最正确螺杆构型取决于物料的比热容、熔点、熔体粘度以及聚合物在固体状态时粒子的大小。
用于熔融、塑化的局部螺杆构型设计的目标是在设定的温度下将固体物料平均、迅速熔融。
单螺杆挤出机螺杆的结构设计与优化

( College of Transportation and Automobile Engineeringꎬ Panzhihua Universityꎬ Panzhihua 617000ꎬ China)
Abstract: Aiming at the problem of large screw weight and unreasonable size structure of screw of the single screw extruder under
效果 [9] ꎮ
上述研究都致力于单螺杆挤出机的机筒或螺杆力
模态分析ꎬ 求解出螺杆的固有频率和相应的模态振型
学性能研究和分析ꎬ 但对螺杆的优化研究较少ꎮ 本文
云图ꎬ 以所生产的产品表面质量为目标ꎬ 对螺杆进行
以单螺杆挤出机螺杆为研究对象ꎬ 首先对螺杆进行静
优化ꎬ 提高了螺杆的可靠性
[6]
ꎮ 孟祥凯以某膨化机
the traditional design methodꎬ which could increase the cost of material and manufactureꎬ the topology optimization method was
introduced into the screw design and optimization of the single screw extruder. The solid model of the screw was establishedꎬ the
Keywords: Single Screw Extruderꎻ Screwꎻ Finite Element Analysisꎻ Topology Optimization
- 1、下载文档前请自行甄别文档内容的完整性,平台不提供额外的编辑、内容补充、找答案等附加服务。
- 2、"仅部分预览"的文档,不可在线预览部分如存在完整性等问题,可反馈申请退款(可完整预览的文档不适用该条件!)。
- 3、如文档侵犯您的权益,请联系客服反馈,我们会尽快为您处理(人工客服工作时间:9:00-18:30)。
πD b Fb yω 60 φ = S bγ bμ bcos
( 5) ( 6)
式中 Fb y — — — 机筒施加给物料的力 ; μb — — — 机筒壁面处聚合物的粘度 ;
Sb — — — 聚合物与机筒的接触面积 。 S b 可由下式确定 : )2 + 2 H - 2δ
X < R
4
( 16 )
图3 挤出机熔融段螺杆优化设计流程
s. t . gi ( X ) ≥0 ( i = 1 , 2 , …, 11 )
式 ( 16) 表明 , 本优化设计属于四维非线性数 学规划问题 。
2 结果与讨论 211 优化方法
烯 ( HDPE) , 取 φ = 17 . 7° , 挤出操作温度为 180 ℃。 设计参数的取值范围为 : e = ( 0 . 08 ~ 0 . 12 ) D s ; H3 = ( 0 . 025~0 . 07) D b ;θ= 17~30° 。
V z sinθ V bz ( 8)
( 7)
单位产量的能耗最小为螺杆熔融段几何结构参数 设计的优化目标 。即 ( 9) f ( x ) = E/ Q s
113 设计变量
式中 V bz — — — 物料沿流动方向上的速度 ; Vz — — — 物料沿流道方向上的速度 。
V bz和 Vz 的计算公式为
图2 熔融模型
1— 螺棱 ;2 — 机筒 ;3 — 固体床 ;4 — 分界面 ;5 — 熔膜 ;6 — 熔池
sinφ ) sin (φ + θ
( 4)
ρ 式中 — — 固体物料的密度 ; s — p— — — 螺纹头数 ;
W — — — 螺槽的法向宽度 , W = n— — — 螺杆转速 ;
渐变浅以及螺槽与机筒间的剪切作用 ,熔池逐渐扩 大 ,而固体床则相应地缩小直至消失 , 熔料进入螺 杆的计量段 。在一般的挤出过程中 ,聚合物熔体的 剪切流动大致上服从幂律 ,其于机筒壁面处的剪切 粘度 ηb 与剪切速度和温度的关系可以表述为 γb ηb = ηr ( ) γr
熔融段是普通单螺杆挤出机中重要的功能段 之一 。聚合物物料在通过该段时 , 受到机筒和螺 杆强烈的剪切和挤压 ,完成物料混合和塑化过程 。 由于物料发生从固态 ( 固体床) 到液态 ( 熔池) 的相 变 ,因此需消耗大量的热能和机械能 ,尤其是粘弹 性较高的无定形聚合物 。通常 , 熔融段螺杆长度 占螺杆总长度的 50 %~ 60 % 。由此可见 , 该段几 何结构设计合理与否 , 直接关系到制品的质量和 生产成本 。近 30 年来 ,不少研究者探讨过挤出机 的熔 融 混 合 和 塑 化 机 理 , 提 出 了 一 些 理 论 模 型 。前文 曾用解析法和实验结果分析方 法讨论了熔融段螺杆主要几何结构参数的优化 。 本研究应用计算机技术对熔融段螺杆主要的几何 结构参数进行优化设计 。
mm 时 , H13 / D b = 0. 185 。本研究中 , 螺杆直径为 70 mm ,取 H13 = 14 mm , 即 H13 / D b = 0. 20 , 符合
值范围 。 致谢 : 华南理工大学工控系 1997 级本科生陈竹和 2000 级研究生李峰华参与了本课题的部分工作 , 谨表谢意 。 参考文献 :
1 数学模型的建立 111 理论分析
[ 1~6 ] [7 ]
图1 挤出机螺杆结构示意
πD bω ( 1) 60 则机筒壁面处的剪切速率 γb 可由下式表示 : πD bω γb = ( 2) 60 H
Vb =
普通挤出机螺杆的结构示意如图 1 所示。从 图 1 可以看出 ,熔融段的螺槽深度逐渐变浅 ,这主 要是为了强化剪切塑化的功能 。由于机筒与螺杆 之间的相对运动 , 聚合物物料在机筒内受到强烈 的挤压和剪切运动 , 由固体床的柱塞运动逐渐形 成熔料的剪切流动 。机筒相对螺杆的速度 V b 可 由下式确定 :
n m ax — — — 螺杆最高转速 。
为了使物料得到足够的压缩作用 , 以便排气 和致密性好 , 应满足如下的压缩比条件 : ( D s - H1 ) H1 g2 ( x ) = - 1 ≥0 ( 12 ) ( D s - H3 ) H3ε 1
g3 ( x ) = 1 ( D s - H 1 ) H1 ≥0 ( D s - H3 ) H3ε 2 ( 13 )
[ 1 ] Tadmor Z ,Duvdevani I I , Klein J . Melting in plasticating extrud2 ers : Theory and experiments[J ] . Polym. Eng. Sci. ,1967 ,7 (3) : 198. [ 2 ] Kuhnle H. Calculation and optimization of melt extruders[J ] . J . Polym. Eng. ,1986 ,6 (124) :51. [ 3 ] Rauwendaal C. Melting t heory for temperature dependent fluids , exact analytical solution for power law fluids [ J ] . Adv. Polym. Tech. ,1991/ 1992 ,11 (1) :19. [ 4 ] Rauwendaal C. Conveying and melting screw extruders wit h axi2 al screw movement [J ] . Int . Polym. Process ,1992 ,11 (1) :26. [ 5 ] Potent H , Hanhart W. Design and processing optimization of ex2 truder screws[J ] . Polym. Eng. Sci. ,1994 ,34 (11) :937. [ 6 ] 梁基照 . 轻工机械优化设计 [ M ] . 广州 : 华南理工大学出版社 , 1995. 150. [ 7 ] 梁基照 . 挤出机螺杆熔融段几何参数的优化设计 [J ] . 轻工机
第 10 期 梁基照 1 挤出机螺杆熔融段的优化设计 603
挤出机螺杆熔融段的优化设计
梁基照
( 华南理工大学 工业装备与控制工程系 ,广东 广州 510641)
摘要 :讨论了挤出机螺杆熔融段的优化设计问题 。以单位产量能耗最小为优化目标 ,建立简化的挤出机熔融段螺 杆优化设计的数学模型 ,应用复合形法求解 。结果表明 ,计算所得熔融段起 、 末端的螺槽深度 、 螺纹顶宽度和螺纹升角 均位于或接近文献中所建议的最佳取值范围 。 关键词 :挤出机 ; 螺杆 ; 优化设计 中图分类号 :TQ330. 4 + 4 文献标识码 :B 文章编号 :10002890X(2002) 1020603204
V bz = Vb + V V塑化熔融机理及目标 函数可知 ,该段的几何参数中 ,起始端槽深 H1 和 末端槽深 H3 、 棱顶宽度 e 以及螺纹升角θ对聚合 物物料塑化熔融过程影响甚大 。因此 ,取 H1 , H3 , e 和θ为设计变量 ,于是 θ,e ,H1 ,H3 ] T ( 10) X = [ x1 ,x2 ,x3 ,x4 ] T = [
2 2 δ )2] l +π ( D b - 2
πW L 2 HpL 2 2 2 ( D b - 2 H - 2δ ) + S b = [ l +π ( D b W +e l 式中 L2 — — — 螺杆熔融段长度 ; δ ) t an θ; l— — — 螺纹升程 ,l = π( D b - 2 δ— — — 螺纹顶与机筒内壁的间隙 。 式 ( 6) 中 ,机筒速度方向与物料流动方向的夹 角φ 可定义为 φ = sin - 1
n max ( D b - 2 x 3 ) 3 [ 1 - (
≥0
( 11 )
第 10 期 梁基照 1 挤出机螺杆熔融段的优化设计 605
τ] — 式中 [ — — 许用剪切应力 ; N m ax — — — 电机最大额定功率 ; μ— — — 机械效率 ,一般取 0. 8 ;
H = H1 + H3
2
式中 , H1 和 H3 分别为加料段螺槽深度和计量段 螺槽深度 。 熔融理论主要是基于热力学和流变学而建立 的 。聚合物挤出过程中典型的熔融模型如图 2 所 示 。首先 , 与热机筒接触的固体床表面逐渐形成 一层薄的熔膜 。当熔膜厚度超过螺杆与机筒间隙 δ时 , 螺棱把熔膜从机筒内壁径向地刮下 , 并汇聚 于螺纹推进面而形成环流区 ( 熔池) 。随着螺槽逐
114 约束条件
θ - 2 V b V z cos
Vb
sinθ
根据高产 、 优质和低能耗的设计原则 ,选择以
g 1 ( x ) = [τ] -
由受力分析可知 ,螺杆在工作时受弯 、 扭和压 的作用 ,其中以扭转作用最大 。由此得强度约束 条件 :
496 000μN max 3 . 15 )4] Db - 3 x3
式中 Ds — — — 螺杆外径 ; ε , 2— — — 压缩比的上 、 下限 。 1ε 此外 ,几何结构参数有一定的取值范围 。若 取 Xi H和 Xi L 分别为设计变量的上 、 下限值 , 则有 如下的边界约束条件 : xi ( 14) g4 ( x) = - 1≥ 0 (i = 1 ,2 ,3 ,4) Xi L Xi H ( 15) g5 ( x) = - 1≥ 0 (i = 1 ,2 ,3 ,4) xi 115 数学模型 根据上述讨论 , 可得挤出机熔融段螺杆优化 设计的数学模型 : πD b Fb yω min f ( x ) = sinφ 60ρH1 p W V b ・ ( ) sin φ + θ