滚动轴承疲劳寿命试验台的设计
轴承滚子四线摩擦副滚动接触疲劳寿命试验台架设计

旦 E ̄。 b /1. ,l 一 'p :r3 6 Q
力推导出计算公式为
.
\ ( 5 , )
( 6 )
, () 7
对 于 钢制 滚 子 , 据 以上 线 接 触 最 大 接 触 应 根
3 () 5 ,
间存在滚滑状态 , 这会降低滚子 的接触疲劳寿命 ,
导致测试结果的不确定性 。 J
现研 制 了四线摩 擦 副 接触 式 纯 滚 动 强 化疲 劳
荷、 速度等) 不会发生变化; 由于试验机 系统 的一
些基本零部件及加载机构 同样存 在破 坏 的问题 ,
寿命试验机 , 其克服 了传统试验机的缺点 , 可用 于
的速度关 系不 恒 定 , 以试 验 滚 子 与 陪 试 滚 子 之 所
l 试 验 机 总体 设 计
通 常要求 滚 动接 触疲 劳 寿 命试 验 机 具 有一 些
特殊 的性能 , 以达 到对 滚动疲劳寿命 较精确 的测 量。每次试验时试验机都要作长 时间的运转, 这 就要求试 验机 在无人监 控时 , 其试验参数 ( 如载
蓬 I }
0. 5 1O . 2O . 30 .
2 5
_ 1 ■9 蟹0n x 39 28 蚕X li 一l - 1 m0 11 8n n3 ia an -. l n
40 .
子 的疲劳寿命 , 可以更好地分析滚子的失效原 因。
u l_
p ro a c tb a i g r l r d r m i e e tmae a s ef r n e o e r ol s ma e f m n e o df r n t r . f i l
推进中国轴承行业轴承寿命试验系统技术的进步——访杭州轴承试验研究中心(HBRC)李兴林博士

华企业的不断增多,S F K  ̄ 华寻
.
流外,还就下 ・ 步的合作意向进行
r 好的交流 。 友
求研发及质检的合作伙伴,以满足 在华企业 日 益增长的技术支撑和合 作的需求。
Po. t hs o n i s 国 rfSa i Ia n e是英 t d
H R :推进中国轴承 B C 行业轴承寿命试验系统技术 的进步
化, 轴承寿命强化试验系统技术已 被业内和轴承用户广泛认可并申请 了发明专利 ,他感到非常欣慰。这
次 访问 ,寅 主除在技 术方面进行 交
承动态性能和疲劳寿命的研究以及
滚动轴承相关产品开发、检测和试 验等工作。拥有国际上比较先进的 测试仪 器 和设备, 技术力量雄厚 ,
多 项科研成 果在 全 国 广应用。 推
19 年1 月 ,李兴林博 士作 90 0 为中国轴承行业的惟一代表,参加
了在 日本举行的五年 一次的 国际摩
擦学大会I C 19 N g y ,宣 T 90 a o a
( 现为S FS E R K T Y )、美国的S F K
H R 的A L 试验现场 B C BT
读了自己的论文并实地考察了日 本
的复杂性、高成本以及试验结果的
滞后性,使得该类模拟试验技术丧 失了一定的优势。 目前 轴承行业广泛采用的 可 靠性强化试验技术是依据故障物理 学,把故障或失效 当作研究的主 要对 象,通过发现 、研究和根 治 故障达到提高可靠性的 目的 实
动轴承疲劳寿命强化试验机,大大 地推进了中国轴承行业轴承寿命试 验系统技术的进步。
的性能 明 落后干试 验发展需 要 而从美 国引进 的F M ”新 型滚动 & 5
任 ,浙江大学博士后联 系 教授,河
轮对轴承跑合试验台技术部分

1技术条件1.1 适用范围主要适用于主要应用于轨道车辆转向架制造、检修时轮对轴承组装完成后的轮对轴承跑合试验,是检查轮对轴承组装质量的主要工艺手段和设备。
本试验台为具有轮对轴承正反转跑合、轮对轴承温升监控等功能的综合试验台。
1.2 适用环境环境温度:-20℃~+55℃海拔高度:≤2000m相对湿度:≤80%使用电源:AC380V±10%,50Hz1.3 设备的基本要求1.3.1 设备的总体要求1.3.1.1 该设备可应用于轮对滚动轴承跑合作业。
1.3.1.2 该设备为离线停留式1.3.1.3 该设备关键部件材质均采用国内外业界著名厂商生产的合格产品,性能指标都达到或者超过相关标准的要求。
1.3.1.4 该设备具备的功能:●能对轮对轴承进行跑合试验。
●可输入轮对轴号。
●有软起动、变速、制动功能。
●摩擦压力、制动力可调。
●跑合作业时间可调。
●每端两点远红外测温。
●超温报警。
●转速可测。
●计算机显示屏显示检测数据并存储,可随时输出。
●能自动判别跑合是否合格。
●基础数据长期存储和恢复功能。
●遇见紧急情况时设备具有急停功能。
1.3.1.5 该设备是完整的、全新的,并且具有合理的结构、高的稳定性、可靠性和耐久性,具有足够的刚度和强度,程序简单易懂,操作、维修方便。
1.3.1.6 该设备设有安全保护联锁装置和短路、断路及漏电保护装置,停电或意外停机时的保护装置。
具有完善、可靠的联锁、安全保护和故障报警等功能。
1.3.1.7 该设备的零部件选用优质材料制造,所选用的机械、液压、电气元器件和控制系统是先进的、优质的、可靠的系列产品。
1.3.1.8 提供该设备必要的易耗品和备件,所需数量应满足两年的正常使用。
1.3.2 选用材料的技术要求该设备及工装的零部件所用材料的牌号符合图纸所规定的牌号,符合GB1591-88、GB699-88、GB700-88之规定,进厂原材料有质量合格证件,属国家大型钢铁企业的产品。
滚动轴承疲劳寿命试验台的设计

第1章绪论1.1课题研究的目的和意义滚动轴承是机器运转中重要的零部件,是旋转结构中的重要组成部分之一,具有承受载荷和传递动运动的作用。
可是,滚动轴承是机器运转时主要故障来源之一,有数据结果分析表明:旋转机器中有35%的故障都与轴承的失效相关,轴承能够使用多久和可靠性的大小直接影响到机器系统的整体性能。
为此在对轴承的加速老化试验和加速寿命试验,对于研究轴承的故障演变规律和失效原理有着很重要的意义。
在20世纪前期,Lundberg和Palmgren对5210的滚动轴承做了很多试验,根据1400多套滚子轴承、球轴承的寿命试验结果,在Weibull分布理论的基础上,通过研究得到了寿命与负载的方程式,称为L-P公式。
伴随我国轴承制造技术的不断发展,轴承的几何结构和制造精度得到了相当高的提升和改进。
目前,在市场上有几百种不一样型号的滚动轴承。
现在的5210轴承钢的材料和制造精度比以前的要好,而且现在在材料的选择上已近不局限于轴承钢。
现在生产轴承的原料包括合金钢,陶瓷,轴承钢和塑料等。
为此,为了评估新材料的处理工艺,新材料和新几何结构的滚动轴承的磨损寿命,还得对滚动轴承做疲劳寿命试验。
另外由于加工技术的提高和材料科学的发展,使用时润滑条件的改善,轴承能够使用的时间越来越长。
来自工业和武器等方面的需求也助推了滚动轴承箱相当好的方向发展。
比如发电设备,排水设备等要求轴承工作时间连续不间断的十几二十几的小时不间断的无故障运行10000-20000个小时,折算一下相当于与连续工作11-22年并且中间没有出现任何故障,即使是电动工具、一般机械和家用电器等对寿命的要求相对较低的使用场景也要求轴承无故障的间断或不间断的工作4000-8000小时。
因此,在很多情况下,研究轴承的寿命必须利用加速疲劳寿命试验方法来获得轴承在高应力的疲劳寿命,并且通过加速实验的结果来估计不一样应力水平下的疲劳寿命,以减少试验时的成本和时间。
1.2 国内疲劳试验台的现状国内最早的疲劳寿命试验平台产品都是从前苏联引进,采用剖分式试验主体,在国内称之为第一种机型。
传动轴(等速万向节)扭转疲劳试验台方案
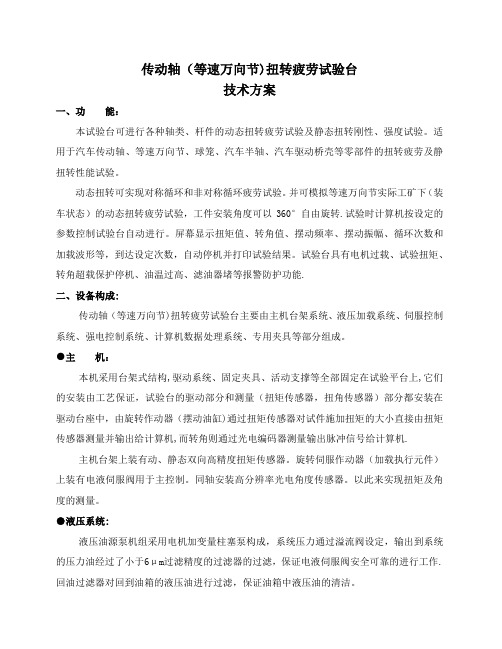
传动轴(等速万向节)扭转疲劳试验台技术方案一、功能:本试验台可进行各种轴类、杆件的动态扭转疲劳试验及静态扭转刚性、强度试验。
适用于汽车传动轴、等速万向节、球笼、汽车半轴、汽车驱动桥壳等零部件的扭转疲劳及静扭转性能试验。
动态扭转可实现对称循环和非对称循环疲劳试验。
并可模拟等速万向节实际工矿下(装车状态)的动态扭转疲劳试验,工件安装角度可以360°自由旋转.试验时计算机按设定的参数控制试验台自动进行。
屏幕显示扭矩值、转角值、摆动频率、摆动振幅、循环次数和加载波形等,到达设定次数,自动停机并打印试验结果。
试验台具有电机过载、试验扭矩、转角超载保护停机、油温过高、滤油器堵等报警防护功能.二、设备构成:传动轴(等速万向节)扭转疲劳试验台主要由主机台架系统、液压加载系统、伺服控制系统、强电控制系统、计算机数据处理系统、专用夹具等部分组成。
●主机:本机采用台架式结构,驱动系统、固定夹具、活动支撑等全部固定在试验平台上,它们的安装由工艺保证,试验台的驱动部分和测量(扭矩传感器,扭角传感器)部分都安装在驱动台座中,由旋转作动器(摆动油缸)通过扭矩传感器对试件施加扭矩的大小直接由扭矩传感器测量并输出给计算机,而转角则通过光电编码器测量输出脉冲信号给计算机.主机台架上装有动、静态双向高精度扭矩传感器。
旋转伺服作动器(加载执行元件)上装有电液伺服阀用于主控制。
同轴安装高分辨率光电角度传感器。
以此来实现扭矩及角度的测量。
●液压系统:液压油源泵机组采用电机加变量柱塞泵构成,系统压力通过溢流阀设定,输出到系统的压力油经过了小于6μm过滤精度的过滤器的过滤,保证电液伺服阀安全可靠的进行工作.回油过滤器对回到油箱的液压油进行过滤,保证油箱中液压油的清洁。
在输送到作动器的进、回油路上装有蓄能器,减小液压冲击对试验的影响。
油源的冷却采用传统的循环水冷却方式,选用高效率的热交换元件,使液压油的工作温度能够保证在其正常工作范围.(水源用户自备,入口温度不超过30℃)●伺服控制系统:本测控系统采用动态电液伺服控制技术,实现全数字闭环控制,主要测量通道采用交流放大器、宽范围、不分档,连续全程测量,采用大规模可编程门阵列(FPGA)硬件实时跟踪、积分累加原理(∑—Δ)并采用同步采集、及数据预处理。
滚动轴承加速寿命试验技术研究_徐东

收稿日期: 2010- 05- 26 基金项目: 国家自然科学基金资助项目( 50705096) ; 国家部委基金资助项目( 06KG0187) 作者简介: 徐东( 1982 ) , 男, 博士生。
徐 东, 等: 滚 动轴承加速寿命试验技术研究
123
本文通过对滚动轴承加速寿命试验标准和已有加速寿命试验技术的分析, 结合实际滚动轴承加速 寿命试验设计和实施中积累的经验, 提出一套切实可行的滚动轴承加速寿命试验方案。
第 32 卷第 6 期
国防科技大学学报 JOURNAL OF NATIONAL UNIVERSITY OF DEFENSE TECHNOLOGY
文章编号: 1001- 2486( 2010) 06- 0122- 08
滚动轴承加速寿命试验技术研究
Vol. 32 No. 6 2010
徐 东1 , 徐永成1 , 陈 循1, 李兴林2 , 杨拥民1
滚动轴承可分为闭式和开式轴承, 闭式轴承内已注入润滑剂, 在运转过程中不再采用其他方式进行 润滑; 开式一般采用油浴、油雾、滴入润滑油等润滑方式进行润滑, 且根据滚动轴承的运转速度、承载大 小选择相应标号的轴承润滑油, 如高速采用低标号润滑油, 高负载采用高标号润滑油等。
2 5 加速寿命试验基本假定
( 1. 国防科技大学 机电工程与自动化学院, 湖南 长沙 410073; 2. 杭州轴承试验研究中心有限公司, 浙江 杭州 310022)
摘 要: 为了有效地获取滚动轴承具有可比 性的加速寿命试验数据, 利用已有加速寿命试验相关标 准, 结 合实际滚动轴 承加速寿命试验设计和实 施中积 累的经 验, 深 入分析 滚动轴 承加速寿 命试验 过程中 遇到的 各 种问题, 提出一套完整的滚动轴承加速寿命试验 方法。该方法对相 关标准没 有涉及的试 验前检查、试验条 件 一致性分析和 试验数据的处理方法进行 了补充 并对加 速寿命试 验进行 深入分 析, 形 成完整 的滚动 轴承加 速 寿命试验解决方案, 可以有效地指导滚动轴承加 速寿命试验的设计和实施。
滚针轴承使用寿命的研究设计

理论上IKO滚针轴承CF10BUURM的使用寿命20000~80000小时,但是,实际的寿命取决于许多因素——过早的轴承失效会导致代价高额的设备停工,有时甚至还会导致更严重的后果。
令人满意的IKO滚针轴承使用寿命始于正确的轴承选择。从一开始,轴承设计师通过为不同应用选择正确的轴承来延长轴承使用寿命和设备性能。这个过程要考虑许多因素,例如载荷、硬度、轴承寿命预测、运行环境等等。
摘 要
滚动轴承的寿命定义为从轴承开始工作到轴承滚道轮或滚动体的表面,因疲劳最先出现表面剥落的总转数(或者在一定转数下的总旋转时间)。但是,即使尺寸、结构、材料、热处理完全相同条件的轴承运行时,寿命也会有所不同,不是一定的。这是因为材料的疲劳限度本身就存在差异。
这正文中我们将从设计入手,以CF10BUURM螺栓轴承为例。通过对外圈、螺栓轴、保持架的设计与研究与CNC编程探索IKO轴承的秘密。在尺寸精度上,将尺寸控制在公差范围内,保证滚针轴承转动时游隙和摩擦系数。
在这里我们主要讨论的是标准凸轮从动轴承CF。CF10BUURM,这里的10是代表尺寸,也就是杆端直径的大小。B代表的是杆端顶部带六角孔。UU代表的轴承带密封圈密封,R是指外圈外径面是球面。M这里代表细牙螺纹。
这个轴承可以分为外圈、螺栓轴、密封垫片、侧板、保持架、滚针、螺母七个部分,其中螺母是标准件,不需设计其他的我们将在正文中一一计算与设计。其中外圈和螺栓轴将进行数控车编程。
We also need to consider somethings ,such asstoring it in a professional room,surface cleaning, bearing selection, the preparation before installation, installation and dismantlementcarefully , and correct lubrication.
滚动接触疲劳试验机技术简介
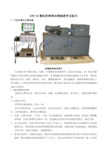
GPM-30微机控制滚动接触疲劳试验台1、产品外观及主要用途济南益华技术简介本试验台用于模拟轴承、轮箍、轧辊等滚动接触零件工况的失效试验,将一恒定的载荷施加于滚动或滚动加滑动接触的试样,使其接触表面受到循环接触应力的作用。
通过控制和改变负荷、速度、滑差率、时间、摩擦配偶材料、表面粗糙度、硬度等参数的情况下进行测试,以评定试样材料的综合使用性能。
满足标准GB10622-89金属材料滚动接触疲劳试验方法要求。
2、基本结构及原理试验台主要由主机、静压作动器、油源、电器测控系统、软件部分、电脑及辅件等组成。
2.1试验台主机采用卧式框架结构。
机电一体。
主机主要由机架、主动运动机构、陪试运动机构、试验力加载机构、试验参数测量部分、试件副盘部分、辅件部分等组成:机架。
主要由机架、工作台、支架、运动连接机构、底板等部分组成。
机架由工程钢整体焊接,各部分紧固的安装在一起。
机架满足结构空间和试验刚性要求,稳定可靠。
主动运动部分。
此部分卧式安装于主机工作台之上,伺服电机驱动主动轴带动主试件做旋转运动,其间串联动态扭矩传感器和弹性联轴器。
试验过程中恒扭矩输出,旋转速度无级可调,试验过程稳定、控制精度高。
陪试运动部分。
伺服电机驱动,通过同步圆弧齿型带传递带动传动轴以及陪试主轴同步旋转,传动轴通过轴承座体固定于工作台上,陪试主轴安装于杠杆保持架一端,杠杆保持架可以传动轴为支点做杠杆运动以施加试验力。
伺服控制系统调控试验转速。
主动和陪试双伺服电机控制,可获得宽范围的滑差率。
试验力加载机构。
采用液压作动器加载机构,位于主机下部,由静压油源和作动器组成,并具有长时保压调节功能。
试验时油缸活塞向上推动杠杆保持架一端,则另一端陪试主轴带动陪试件施加向下的压力于主动轴连接的主试件。
主、陪试件之间可产生最大试验力30kN,油压传感器测量试验负荷。
液压站和作动器特殊设计制造,整个加载试验过程平稳、可靠。
试验参数测量部分。
采用油压传感器测量试验负荷,串联于主动轴上的扭矩传感器动态测量试验扭矩。
- 1、下载文档前请自行甄别文档内容的完整性,平台不提供额外的编辑、内容补充、找答案等附加服务。
- 2、"仅部分预览"的文档,不可在线预览部分如存在完整性等问题,可反馈申请退款(可完整预览的文档不适用该条件!)。
- 3、如文档侵犯您的权益,请联系客服反馈,我们会尽快为您处理(人工客服工作时间:9:00-18:30)。
第1章绪论1.1课题研究的目的和意义滚动轴承是机器运转中重要的零部件,是旋转结构中的重要组成部分之一,具有承受载荷和传递动运动的作用。
可是,滚动轴承是机器运转时主要故障来源之一,有数据结果分析表明:旋转机器中有35%的故障都与轴承的失效相关,轴承能够使用多久和可靠性的大小直接影响到机器系统的整体性能。
为此在对轴承的加速老化试验和加速寿命试验,对于研究轴承的故障演变规律和失效原理有着很重要的意义。
在20世纪前期,Lundberg和Palmgren对5210的滚动轴承做了很多试验,根据1400多套滚子轴承、球轴承的寿命试验结果,在Weibull分布理论的基础上,通过研究得到了寿命与负载的方程式,称为L-P公式。
伴随我国轴承制造技术的不断发展,轴承的几何结构和制造精度得到了相当高的提升和改进。
目前,在市场上有几百种不一样型号的滚动轴承。
现在的5210轴承钢的材料和制造精度比以前的要好,而且现在在材料的选择上已近不局限于轴承钢。
现在生产轴承的原料包括合金钢,陶瓷,轴承钢和塑料等。
为此,为了评估新材料的处理工艺,新材料和新几何结构的滚动轴承的磨损寿命,还得对滚动轴承做疲劳寿命试验。
另外由于加工技术的提高和材料科学的发展,使用时润滑条件的改善,轴承能够使用的时间越来越长。
来自工业和武器等方面的需求也助推了滚动轴承箱相当好的方向发展。
比如发电设备,排水设备等要求轴承工作时间连续不间断的十几二十几的小时不间断的无故障运行10000-20000个小时,折算一下相当于与连续工作11-22年并且中间没有出现任何故障,即使是电动工具、一般机械和家用电器等对寿命的要求相对较低的使用场景也要求轴承无故障的间断或不间断的工作4000-8000小时。
因此,在很多情况下,研究轴承的寿命必须利用加速疲劳寿命试验方法来获得轴承在高应力的疲劳寿命,并且通过加速实验的结果来估计不一样应力水平下的疲劳寿命,以减少试验时的成本和时间。
1.2 国内疲劳试验台的现状国内最早的疲劳寿命试验平台产品都是从前苏联引进,采用剖分式试验主体,在国内称之为第一种机型。
经过改造,在我国重要的轴承试验台生产厂先后制造出了名为ZS系列的轴承寿命试验台,以满足当下我国轴承生产公司对轴承使用时间的要求,以此,同时为刚刚开始不久的我国轴承疲劳寿命试验累积了一定的试验参考依据。
第一个试验台机型结构包括径向加载油缸、轴、中承载体、2个端承载体和试验主轴。
试验台的主要结构拼接后安装在主体被剖分了的底座内,试验主轴由联轴器和传动主轴连接,传动主轴的动力经过带轮靠电机带动变速传动。
竖向和横向的施加载荷的油缸依次同手动加压缸结合,利用扭转促使手动加压缸活塞得到不一样的压力。
这种试验台在我国使用比较广泛,为轴承制造业的进步发挥了很大的作用。
这种试验台的优点在于:容易保障试验精度,结构简单;传动结构是皮带传动,由带轮来改变速度,结构单一;加载是手动加压缸增加压力,能量消耗少;试验主轴和传动主轴由联轴器连接在一起,布局正当,容易获得高速转动,可是不好的地方:载荷和转速的调整,温度数据的采录和检测振动都是要人工操作,试验员工作量较大;传动结构的皮带易打滑易发热而造成危险;加压油缸在试验时容易泄露从而引起压力不足或发热引起压力变高时必须人为的更改,小轴承试验支撑之间的距离比较大,不能实现较大载荷实验。
1.3 我校实验室的试验台情况之前设计的试验台如图1-1,这个试验台结构包括主实验结构、固定框架、径向加压结构和驱动电机,驱动电机安装在固定的机架下面,主结构安装于机架的上面。
主实验结构由主轴、被测轴承和支撑轴承构成。
支撑轴承安置在主轴的中心位置,试验轴承安置在主轴的一端,驱动电机由同步带带着主轴旋转,径向加载依靠液压泵提供载荷,安装在支架的底下。
通过控制液压泵对被测轴承施加径向压力。
这个试验台采用的是液压加载,有利于加载载荷大小的控制,主轴和电动机通过带传动,能够实现过载保护,主轴和被测轴承之间用锥形结构连接,一边实现轴承的快换。
图1-1滚动轴承试验台1、驱动电机2、同步带3、主轴4、支撑轴承的安装位5、支撑轴承6、支撑轴承的安装位7、螺栓8、轴套9、温度传感器10、加速度传感器11、被测轴承座12、被测轴承13、锥型套14、轴承端盖15、固定框架16、液压缸17、上输油管18、下输油管19、二通阀20、压力表21、液压泵22、支撑轴承图1-2试验台布局图图 1-3 试验台受力图如上图在实验的过程中,由于受力不平衡造成了一个弯矩使支撑轴承出现偏移,支撑轴承的外圈出现过度磨损。
这可能是由于布局的不规范和设计的不合理导致试验台的寿命过短,没有起到很大的实际作用,而且又要长时间的不间断工作,导致液压加载系统漏油,不能施加稳定的载荷,是实验的结果得不到很好的保证。
1.4 本文研究的内容本文主要研究内容如下:(1)研究并确定轴承试验台的总体设计思路。
(2)试验台结构设计:包括支撑轴承的选用,主轴设计、传动轴设计、带及带轮的设计并完成试验台的PRO/E三维造型。
(3)加载方式设计:确定施加载荷的形式、设计施加载荷方案、绘制原理图。
(4)建立主轴的力学模型,来校验试验台的设计是不是合理,满足设计的要求。
第2章试验台总体方案设计滚动轴承试验台应该包括机械系统、传动系统、加载系统及辅助设备。
机械系统由试验部分、支撑部分及传动部分组成。
2.1 轴承概况滚动轴承通常包括外圈、内圈、滚动体及保持架。
在特殊情况时,可以没有外圈和内圈,由其他相应的零部件替代。
为了需要,有的轴承装有防尘套、安设调节用的紧定套和密封圈。
2.1.1 套圈轴承的内圈一般装配在轴上,和轴一起转动。
轴承外圈一般装在机壳或轴承座内起支撑作用,有些轴承是内圈固定起支撑作用,外圈转动。
比如汽车轮毂轴承。
如图2-1所示。
a)深沟球轴承内圈b)深沟球轴承外圈图2-1 轴承内外圈2.1.2 滚动体滚动轴承中滚动体是绝对少不了的零件,只有通过滚动体才能形成滚动摩擦。
滚动体的类型有圆柱滚子、钢球、圆锥滚子、滚针和球面滚子。
圆柱滚子可以分为空心圆柱滚子、长圆柱滚子和端圆柱滚子;球面滚子可以分为非球面滚子和球面滚子。
滚顶体是数量及体积能够影响到轴承的承载能力。
图2-2是滚动轴承的滚动体。
a)钢球b)圆柱滚子和滚针c)球面滚子d)圆锥滚子图 2-2 滚动体2.1.3 保持架保持架的功用是将轴承里面的滚动体依次按比例的分离,使滚动体与内圈或外圈独立组成组合件,使滚动体在轨道上的运动时是正确的,能够提高轴承里面的润滑和载荷分配能力。
附带保持架的轴承摩擦小,更多用于高速旋转的情况下。
保持架有两种,一种是实体保持架,另一种是冲压保持架。
实体保持架通常用压铸、车制、注塑等方法制成。
冲压保持架通过金属板材的冲压形成,结构有冠形、浪形、和窗形。
保持架的原料一般有铜铝合金、铸铁、钢和工程塑料等。
图 2-3为普通滚动体保持架。
图 2-3 保持架2.1.4 密封圈和防尘盖密封圈的作用是将轴承内部和外界隔离开来,对滚动体、滚道和保持架形成封闭的环形罩。
一部分可以装配在轴承的支撑部位上,另一部分固定在垫圈或套圈上,也可以直接装配在轴承上。
结构有两类,一类是接触式,另一类是非接触式密封。
接触式密封的轴承和密封圈接触,封闭效果良好,但是摩擦力矩比较大,温度升高较快;非接触式密封采用的是小缝隙的封闭方式,摩擦小,因此温度升高较慢而且没有磨损,比较适合于高速转动。
密封圈的取材一般为橡胶。
2.2 被测轴承的参数被测轴承参数表如下表2-1所示。
被测轴承模型如图2-4。
表2-1 6205滚动轴承参数表内径mm 外径mm宽度mm基本额定动载荷KN/基本额定静载荷KN/最大工作转速min/r25 52 15 14.0 7.88 12000图 2-4 6205滚动轴承2.3 实验室电机参数实验室电机数据表如下表2-2所示。
电机模型如图2-5。
表 2-2 Y系列电动机技术数据电动机型号额定功率KW/满载转速(min/r)堵转转矩最大转矩质量kg/额定转矩额定转矩同步转速3000r/min,2极Y80M1-2 0.75 2825 2.2 2.3 16图 2-5 Y80M1-2电机2.4 试验台方案设计及选用轴承试验台的机械部分重要组成结构包括:试验台支架、加载结构、传动体系、实验主轴等其他辅助设备等。
轴承试验台方案一如下图2-6所示:1、试验轴承2、试验轴2、支撑轴承4、支撑轴承5、联轴器6、电机图 2-6 试验台方案一由图2-6 所示,试验台选用了卧式的布局,主轴由两个滚动轴承支撑,左端装上被测的实验轴承,右端与联轴器连接,联轴器和电机连接。
主轴只做旋转运动,不直接加载任何压力,载荷加载在试验轴承的外圈上,试验轴承可以更换。
动力由电机通过联轴器传递给主轴。
加载方式通过杠杆施加径向载荷。
受力分析如下图2-7所示:试验主轴左端受向下的径向力,由两个支撑轴承提供两个相反的支反力。
由于电机转动,试验主轴同时也受到由联轴器传过来的扭矩。
通过分析可知,试验主轴受到的弯矩不平衡,试验主轴有向左下方倾斜的趋势,这不利于试验正常的运行,会缩短试验台的寿命,使试验结果得不到很好的保证,所以此方案不过合理。
图 2-7 试验主轴受力分析图轴承试验台方案二如下图2-8所示:图 2-8 试验台方案二如上图所示,试验台采用的也是卧式结构,主要由试验部分和传动部分构成。
试验主轴被两个滚动轴承支撑,左右两端各装配了一个试验轴承。
试验主轴和传动轴通过联轴器连接来传递运动,传动轴也由一对滚动轴承支撑着,中间通过键槽装配一个带轮,带轮经由皮带与电动机上的带轮相连,从而传递运动。
试验主轴和传动轴没有直接施加任何压力,压力通过杠杆加载在试验轴承的外圈上,载荷为径向载荷,试验轴承能够替换。
试验主轴受力如下图2-9所示:图 2-9 试验主轴受力图由上试验主轴受力图可知,试验主轴两端受到相同的向下的压力,中间由一对滚动轴承提供了两个支反力。
试验主轴由于通过传动轴来获得动力,所以所受扭矩主要由传动轴来承受,试验主轴几乎不受任何扭矩影响。
所以方案二的有点在于:试验主轴受力分布较合理,没有向任何方向倾斜的趋势,带轮传动能够起到良好的过载保护。
经过反复研究和讨论,选用第二类方案。
PRO/E三维造型如下图2-10所示。
图 2-10 试验台传动结构模型2.5 试验台的测试系统试验台的测试结构由数据收集部分和数据分析部分组成。
数据收集部分由加速传感器和温度传感器两部分构成;加速度传感器和温度传感器安装在试验轴承箱上,通过数据线将加速度传感器和温度传感器分别与加速度和温度数据采集系统相连接,通过数据线将加速度和温度数据采集系统和电脑计算机输入接口连接,从而获得加速度信号和温度信号。
2.6 加载结构的确定滚动轴承试验台的实际要求是要完成在被试轴承施加径向压力4KN,径向压力的方向竖直向下,压力稳定不变。