液压系统计算
液压计算常用公式

溢流阀的保养及故障排除减压阀的保养及故障排除流量控制阀的保养及故障排除方向控制阀的保养及故障排除的油封漏油B 机械操作的阀芯不能动作1、排油口有背压2、压下阀芯的凸块角度过大3、压力口及排油口的配管错误同上凸块的角度应在30°以上。
修正配管。
C 电磁阀的线圈烧坏1、线圈绝缘不良2、磁力线圈铁芯卡住3、电压过高或过低4、转换的压力在规定以上5、转换的流量在规定以上6、回油接口有背压更换电磁线圈。
更换电磁圈铁芯。
检查电压适切调整。
降下压力,检查压力计。
更换流量大小的控制阀低压用为1.0kgf/cm²,高压用为kgf/cm²回油口直接接回油箱,尤其是泄油(使用外部泄油)D 液控阀不会作动1、液控压力不足2、阀芯胶着,分解清理之,洗净3、灰尘进入,分解清理之,洗净液控压力为3.5kgf/cm²以上,在全开或中立回油阀须加装止回阀使形成液控压力。
分解清理之,洗净。
电磁阀的保养及故障排除故障原因处置A 动作不良1、因弹簧不良致滑轴无法恢复至原位置2、阀芯的动作不良及动作迟缓3、螺栓上紧过度或因温度上升至本体变形4、电气系统不良更换弹簧。
1、洗净控制阀内部除去油中的混入物。
2、检查过滤器,必要时洗涤过滤器或更换液压油。
3、检查滑轴的磨耗情形,必要时须更换。
松开螺栓上紧程度(对角交互上紧) 检查插入端子部的接触状态,确认电磁线圈的动作是否正常,如果线圈断线或烧损时须更换。
B 磁力线圈噪音及烧损1、负荷电压错误2、灰尘等不纯物质进入3、电磁线圈破损,烧损4、阀芯的异常磨耗检查电压,使用适当的电磁线圈。
除去不纯物。
更换更换C 内部漏油大外部漏油1、封环损伤2、螺栓松更换再上紧液压机器其他故障及排除共振、振动及噪音故障原因处置A 弹簧与弹簧共振二组以上控制阀的弹簧的共振(如溢流阀及溢流阀、溢流阀及顺序阀、溢流阀及止回阀)1、将弹簧的设定压力错开,10kgf/cm²或10%以上。
液压系统计算公式汇总

风冷计算 H=Qa*ρ k*Cp·Δ t(J/h) Qa——风扇风量(m3 / h) ρ k——空气密度(取ρ k=1.29kg/m3) Cp——空气比热容(取Cp=1008J/kg· K)
Δ t——散热温差(取Δ t=10K) 水冷计算 H=Qa*ρ k*Cp·Δ t(J/h) Qa——冷却水量(m3 / h) ρ k——水密度(取ρ k=1000kg/m3) Cp——水比热容(取Cp=4186.8J/kg· K) Δ t——进出水温差
油箱热平衡 油箱总体积V (L) 油箱传热系数 k 油比热( 1.7~2.1 KJ/(kg*K) 环境温度T0 (K) 设定油温 T (K) 油箱散热面积(m2) 系统温升(冷却时间) t(min) 系统热平衡温度(K) 风冷计算 风量(m3 / h) 散热温差t (K) 散热功率 (Kw) 水冷计算 冷却水量(m3 / h) 进出水温差t (K) 散热功率 (Kw) 温度换算 摄氏度 华氏度
2000 8 1.9 30 55 16 122.47 115.94
系统发热功率(Kw) 加热功率(Kw) 冷却功率(Kw) 油质量(kg) 油箱散热面积(m2)≈ 油箱冷却功率(Kw) 油箱壁厚(mm) 油箱重量(Kg)≈
11 0 0 1440 10.57 3.20 6.5 770.63
4000 10 14.45
通风条件 差 良好 风冷冷却 循环水冷却
系数k 8~9 15 23 110~174
24 2 55.82
204 200
ห้องสมุดไป่ตู้——〉华氏度 ——〉摄氏度
399.20 93.33
kA t H T T0 1 e C m k A
当t →∞ 时,系统热平衡公式
液压系统设计计算公式
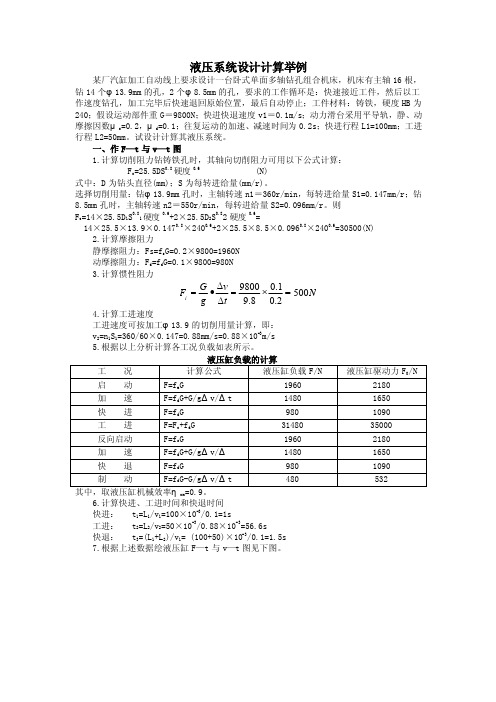
液压系统设计计算举例某厂汽缸加工自动线上要求设计一台卧式单面多轴钻孔组合机床,机床有主轴16根,钻14个φ13.9mm 的孔,2个φ8.5mm 的孔,要求的工作循环是:快速接近工件,然后以工 作速度钻孔,加工完毕后快速退回原始位置,最后自动停止;工件材料:铸铁,硬度HB 为240;假设运动部件重G =9800N ;快进快退速度v1=0.1m/s ;动力滑台采用平导轨,静、动摩擦因数μs =0.2,μd =0.1;往复运动的加速、减速时间为0.2s ;快进行程L1=100mm ;工进行程L2=50mm 。
试设计计算其液压系统。
一、作F —t 与v —t 图1.计算切削阻力钻铸铁孔时,其轴向切削阻力可用以下公式计算:F c =25.5DS 0.8硬度0.6(N)式中:D 为钻头直径(mm);S 为每转进给量(mm/r)。
选择切削用量:钻φ13.9mm 孔时,主轴转速n1=360r/min ,每转进给量S1=0.147mm/r ;钻8.5mm 孔时,主轴转速n2=550r/min ,每转进给量S2=0.096mm/r 。
则F c =14×25.5D 1S 0.81硬度0.6+2×25.5D 2S 0.82硬度0.6=14×25.5×13.9×0.1470.8×2400.6+2×25.5×8.5×0.0960.8×2400.6=30500(N) 2.计算摩擦阻力静摩擦阻力:Fs=f s G=0.2×9800=1960N 动摩擦阻力:F d =f d G=0.1×9800=980N 3.计算惯性阻力4.计算工进速度工进速度可按加工φ13.9的切削用量计算,即:v 2=n 1S 1=360/60×0.147=0.88mm/s=0.88×10-3m/s 5.根据以上分析计算各工况负载如表所示。
液压系统发热量的计算
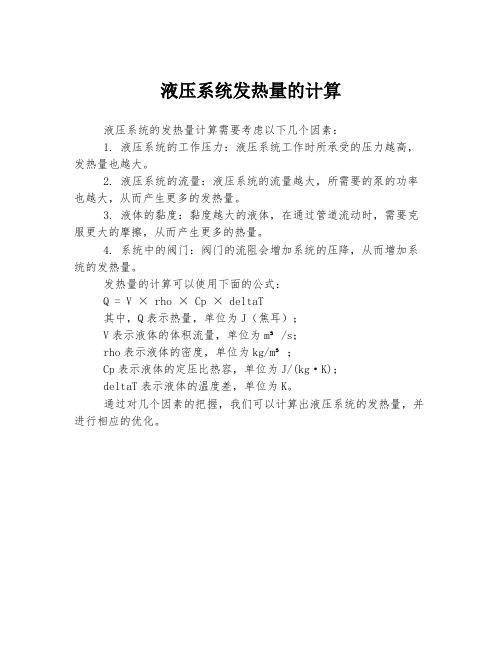
液压系统发热量的计算
液压系统的发热量计算需要考虑以下几个因素:
1. 液压系统的工作压力:液压系统工作时所承受的压力越高,发热量也越大。
2. 液压系统的流量:液压系统的流量越大,所需要的泵的功率也越大,从而产生更多的发热量。
3. 液体的黏度:黏度越大的液体,在通过管道流动时,需要克服更大的摩擦,从而产生更多的热量。
4. 系统中的阀门:阀门的流阻会增加系统的压降,从而增加系统的发热量。
发热量的计算可以使用下面的公式:
Q = V × rho × Cp × deltaT
其中,Q表示热量,单位为J(焦耳);
V表示液体的体积流量,单位为m³/s;
rho表示液体的密度,单位为kg/m³;
Cp表示液体的定压比热容,单位为J/(kg·K);
deltaT表示液体的温度差,单位为K。
通过对几个因素的把握,我们可以计算出液压系统的发热量,并进行相应的优化。
液压系统设计计算实例(共18张PPT)优秀
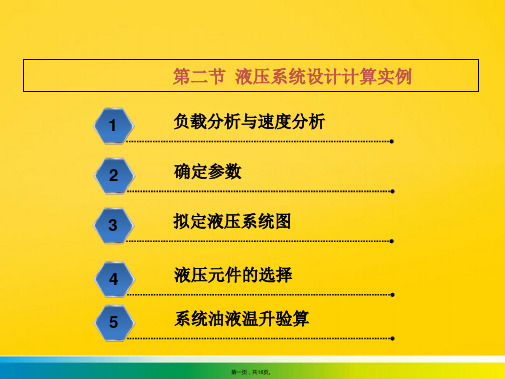
3)计算液压缸在工作循环各阶段的压力、流量和功率 值
差动时液压缸有杆腔压力大于无杆腔压力,取两腔间回路及阀的压 力损失为0.5MPa,则p2= p1+0.5MPa。计算结果见表9.5。
由教材中9-5表即可画出液压缸的工况图(略)。
第七页,共18页。
表9-5:液压缸工作循环各阶段压力、流量和功率值
工作循环 计算公式 量 输入功率
负载
P kW
快 启动加速
p1=F+A2(p2-p1) 3289
A1 -A2
q1=(A1 -A2)v1
p2= p1+0.5
进恒速
P= p1 q1
2178
回油背进油压力 输入流
p1MPa
q110-3 m3/s
-
0.88
0.50
0.44
p1= F+ A2p2
20mm/min~120mm/min按上述分析可绘制出负载循环图和速度循环图(略)
。
第三页,共18页。
第四页,共18页。
2.确定参数
1)初选液压缸的工作压力
由最大负载值查教材中表9-3,取液压缸工作压力为4MPa。
2)计算液压缸结构参数
为使液压缸快进与快退速度相等,选用单出杆活塞缸差动连接的方式实现快进
采用平(导轨4,)其换摩擦向系回数f=路0. :为了换向平稳,选用电液换向阀。为便于实现液压缸中位停止和
0大0流31量泵的输差入动功0率.连经接计算,为采70.用三位五通阀。
(5)压力控制回路:系统在工作状态时高压小流量泵的工作压力由溢 流阀调整,同时用外控顺序阀实现低压大流量泵卸荷。
第九页,共18页。
(3 据此选用Y112M—6—B5立式电动机,其额定功率为2.
液压计算公式单位换算方法
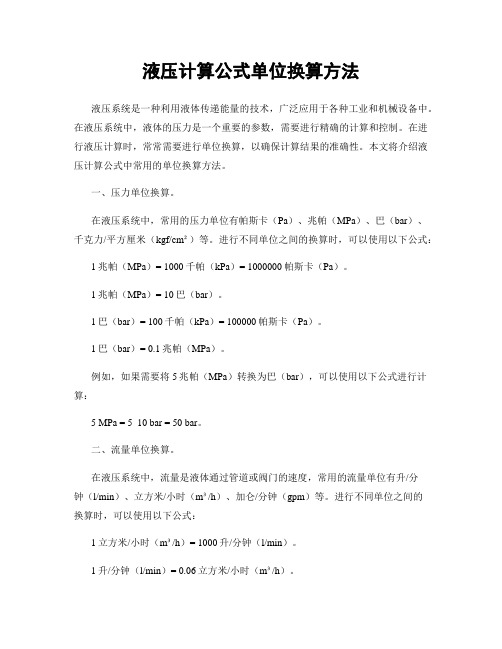
液压计算公式单位换算方法液压系统是一种利用液体传递能量的技术,广泛应用于各种工业和机械设备中。
在液压系统中,液体的压力是一个重要的参数,需要进行精确的计算和控制。
在进行液压计算时,常常需要进行单位换算,以确保计算结果的准确性。
本文将介绍液压计算公式中常用的单位换算方法。
一、压力单位换算。
在液压系统中,常用的压力单位有帕斯卡(Pa)、兆帕(MPa)、巴(bar)、千克力/平方厘米(kgf/cm²)等。
进行不同单位之间的换算时,可以使用以下公式:1兆帕(MPa)= 1000千帕(kPa)= 1000000帕斯卡(Pa)。
1兆帕(MPa)= 10巴(bar)。
1巴(bar)= 100千帕(kPa)= 100000帕斯卡(Pa)。
1巴(bar)= 0.1兆帕(MPa)。
例如,如果需要将5兆帕(MPa)转换为巴(bar),可以使用以下公式进行计算:5 MPa = 5 10 bar = 50 bar。
二、流量单位换算。
在液压系统中,流量是液体通过管道或阀门的速度,常用的流量单位有升/分钟(l/min)、立方米/小时(m³/h)、加仑/分钟(gpm)等。
进行不同单位之间的换算时,可以使用以下公式:1立方米/小时(m³/h)= 1000升/分钟(l/min)。
1升/分钟(l/min)= 0.06立方米/小时(m³/h)。
1加仑/分钟(gpm)= 3.785升/分钟(l/min)。
例如,如果需要将200升/分钟(l/min)转换为立方米/小时(m³/h),可以使用以下公式进行计算:200 l/min = 200 0.06 m³/h = 12 m³/h。
三、功率单位换算。
在液压系统中,功率是指单位时间内所做的功,常用的功率单位有千瓦(kW)、马力(hp)等。
进行不同单位之间的换算时,可以使用以下公式:1千瓦(kW)= 1.36马力(hp)。
1马力(hp)= 0.74千瓦(kW)。
液压系统设计计算
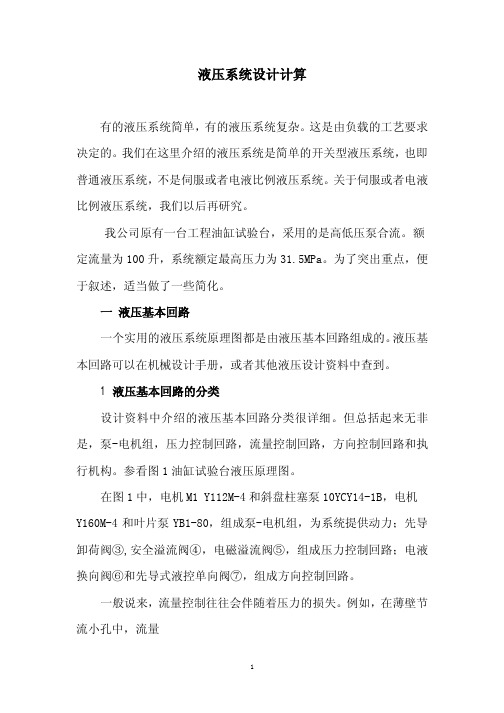
液压系统设计计算有的液压系统简单,有的液压系统复杂。
这是由负载的工艺要求决定的。
我们在这里介绍的液压系统是简单的开关型液压系统,也即普通液压系统,不是伺服或者电液比例液压系统。
关于伺服或者电液比例液压系统,我们以后再研究。
我公司原有一台工程油缸试验台,采用的是高低压泵合流。
额定流量为100升,系统额定最高压力为31.5MPa。
为了突出重点,便于叙述,适当做了一些简化。
一液压基本回路一个实用的液压系统原理图都是由液压基本回路组成的。
液压基本回路可以在机械设计手册,或者其他液压设计资料中查到。
1 液压基本回路的分类设计资料中介绍的液压基本回路分类很详细。
但总括起来无非是,泵-电机组,压力控制回路,流量控制回路,方向控制回路和执行机构。
参看图1油缸试验台液压原理图。
在图1中,电机M1 Y112M-4和斜盘柱塞泵10YCY14-1B,电机Y160M-4和叶片泵YB1-80,组成泵-电机组,为系统提供动力;先导卸荷阀③,安全溢流阀④,电磁溢流阀⑤,组成压力控制回路;电液换向阀⑥和先导式液控单向阀⑦,组成方向控制回路。
一般说来,流量控制往往会伴随着压力的损失。
例如,在薄壁节流小孔中,流量d Q C A = (1) 此公式的使用条件为0.5l d≤。
式中Q —经过薄壁小孔的流量,3/m s ;d C —薄壁小孔流量系数,对于紊流,0.600.61d C = ; 0A —孔口面积,2m ; ρ—流体的密度,3/kg m ; p ∆—压力差,12p p p ∆=−,Pa ;d —小孔的直径,m ; l —小孔的长度,m 。
这种压力能损失往往转化为热能,使液压系统升温。
在理论上,变量泵不会因为流量或压力的变量产生能量损失。
2 液压基本回路的联结液压基本回路,特别是液压元件,在液压原理图中的联结,要么是并联,要么是串联。
二 液压系统原理图1 液压系统原理图应该包括的的基本内容一个符合要求的液压原理图除了表示系统外,还应该包括两个基本内容:液压元件明细表和电磁铁动作顺序表。
液压油量计算
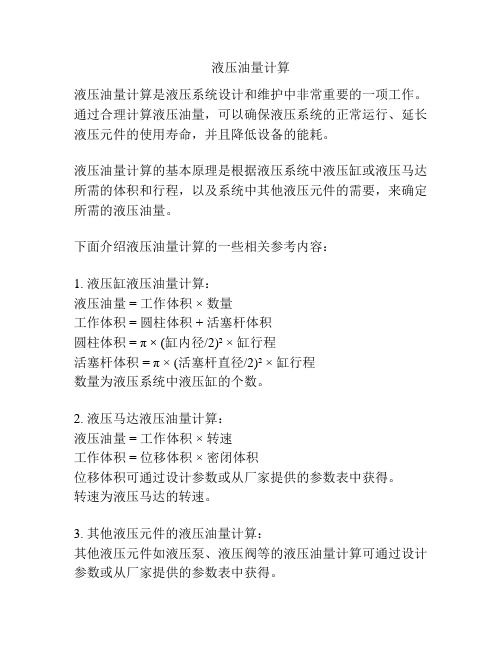
液压油量计算液压油量计算是液压系统设计和维护中非常重要的一项工作。
通过合理计算液压油量,可以确保液压系统的正常运行、延长液压元件的使用寿命,并且降低设备的能耗。
液压油量计算的基本原理是根据液压系统中液压缸或液压马达所需的体积和行程,以及系统中其他液压元件的需要,来确定所需的液压油量。
下面介绍液压油量计算的一些相关参考内容:1. 液压缸液压油量计算:液压油量 = 工作体积 ×数量工作体积 = 圆柱体积 + 活塞杆体积圆柱体积= π × (缸内径/2)² ×缸行程活塞杆体积= π × (活塞杆直径/2)² ×缸行程数量为液压系统中液压缸的个数。
2. 液压马达液压油量计算:液压油量 = 工作体积 ×转速工作体积 = 位移体积 ×密闭体积位移体积可通过设计参数或从厂家提供的参数表中获得。
转速为液压马达的转速。
3. 其他液压元件的液压油量计算:其他液压元件如液压泵、液压阀等的液压油量计算可通过设计参数或从厂家提供的参数表中获得。
4. 液压系统总油量计算:液压系统总油量 = 所有液压元件需求的液压油量之和通过以上计算方法得到各个液压元件需要的液压油量,将其累加得到液压系统的总油量。
在实际液压系统设计中,还需要考虑一些额外因素,例如润滑油的损耗和密封元件容纳的余量等。
这些因素可以根据具体的液压系统要求进行调整和计算。
总之,液压油量计算需要综合考虑液压系统中各个液压元件的需求,通过合理计算液压油量,可以确保液压系统的正常运行、延长液压元件的使用寿命,并且降低设备的能耗。
以上所提到的液压油量计算方法可以作为液压系统设计和维护的参考内容。
- 1、下载文档前请自行甄别文档内容的完整性,平台不提供额外的编辑、内容补充、找答案等附加服务。
- 2、"仅部分预览"的文档,不可在线预览部分如存在完整性等问题,可反馈申请退款(可完整预览的文档不适用该条件!)。
- 3、如文档侵犯您的权益,请联系客服反馈,我们会尽快为您处理(人工客服工作时间:9:00-18:30)。
注:油箱公称容量大于本系列10000L时,应按GB/T 321 油箱空气容量 10%~15%
流速 v(m/s) 高压胶管通径:6/8/10/13/16/19/22/25/32/38/45/51 钢管通径:3/4/5;6/8/10;12/15/20/25/32/40/50/65
管子承受的压力 安全系数S
说明:对于压力管,当压力高、流量大管路短时取大值 P=2.5~14MPa时,取v=3~4m/s,当p>14MPa时,取v
散热系数 K
W/(m2*℃) 15
环境温度 t2 ℃ 25
油箱散热面积 A=PL/(K*Δt)
m2 0.01
油液最高允许温度 t1 ℃ 40
油箱散热系数K(液压工程师手册) 油箱散热情况 整体式,通风差 单体式,通风较好 上置式,通风好 强制通风式
液压泵站油箱公称容量 系列(JB/T 7938— 2010) /L
2.5、4.0、6.3、10 16、25、40、63、100 160、250、315、400、500、630、800、1000 1250、1600、2000、2500、3150、4000、5000、6300、8000、
10000
吸油管
油箱散热量 PT kw 0
冷却介质温度 t1+t2 ℃ 30
PC=PL-PT kw 30
平均温度差 T=[(T1+T2)-(t1+t2)]/2
℃ 12.5
油的比热容 C
kJ/(kg*℃) 1.88
水的比热容 Cs
kJ/(kg*℃) 4.2
冷却器热交换量 PC=PL-PT kw 4.4
平均温度差 T=[(T1+T2)-(t1+t2)]/2
液压油进口温度 T1 ℃ 55
冷却水量
油的流量 Q
L/min 232 水的流量
Qs=C*ρ*ΔT/(Cs*ρs*Δt)
m3/h 8.41
风冷却器散热面积
系统发热量 PL=P*(1-η)
kw 4.4 液压油温度 T1+T2 ℃ 40
PT kw 0 液压油出温度 T2 ℃ 40
油的密度 ρ
kg/m3 900 水的密度 ρs kg/m3 1000
液面高 C=V*10^6/(A*B)
mm
容积 V=Q*a
L 2400.00
高 C mm 690
回油管路内径 d=4.61*(Q/2)^0.5
mm 65.2
承受压力 P Mpa 25
油箱散热面积
允许温升
输出功率
Δt
P
℃
kw
10
10
油箱自然通风最小有效容积
输出功率
总效率
P
η
kw
30
0.87
散热系数
℃ 10
系统压力 经验系数a
体积 V=A*B*C/10^6
L 745.2
有效容积 V1=V*0.85
L 633.42
吸油管路内径 d=4.61*(Q/0.8)^0.5
mm 102.9
管子内径 d mm 60
管内流速
管路内径 d mm 90
壁厚 Δ= P*d*S/(2*σb-P*S)
mm 6.04
流速 4Q/(πd^2)
散热系数K(液压工程师手册) 散热系数K 11~28 29~57 58~74 142~341
散热系数K(液压元件与系统) 散热系数K 8~10 14~20 20~25 110~175
种类
散热系数K
列管式 波纹板 风冷 机械制冷
350~580 230~815 116~175 冷却效果最好
润滑系统 25~30
压油管
0.5~1.5
2~6
通径:6/8/10/13/16/19/22/25/32/38/45/51
:3/4/5;6/8/10;12/15/20/25/32/40/50/65/80/100
回油管 1.5~2.5
短管及局部收缩处 ≤10
P<7MPA 8
P<17.5MPA 6
P>17.5MPA 4
对于压力管,当压力高、流量大管路短时取大值,反之取小值;当系统压力p<2.5MPa时,取v=2m/s,当 ~14MPa时,取v=3~4m/s,当p>14MPa时,取v≤5m/s;对于行走机械,当P>21MPa时,取v≤5~6m/s
m2 3.79
A≈PC/(T*k) m2 6.86
冷却介质出口温度 t2 ℃ 40
水冷却式
风冷却式 制冷
行走机械 1~2
p≤2.5MPa 2~4
2.5MPa<p≤6.3MPa 5~7
p>6.3MPa 6~12
公称容量大于本系列10000L时,应按GB/T 321—2005《优先数和优先数系》中R10数系选择。
油液温升
K
Δt=t1-t2
W/(m2*℃)
℃
8
15
水冷却器散热面积
系统发热量
油箱散热量
系统损失功率 PL=P*0.15 kw 1.5
系统损失功率 PL=P*(1-η)
Kw 3.9 油箱散热容积
V≈10^3*{[PL/(0.065*K*(t1-t2))]^3}^0.5
m3 353.55
冷却器热交换量
PL=P*(1-η) kw 30
容积计算
经验系数 a
6
体积计算
长 A mm 1200
管路内径
系统流量 Q
L/min 400.00
管道壁厚
安全系数 S
3
液面高度差计算
无杆腔体积 v L
0.50
流量 Q
L/min 400.00
宽 B mm 900
压力管路内径 d=4.61*(Q/4)^0.5
mm 46.1
20#钢抗拉强度 σb Mpa 410
油箱散热系数K(液压元件与系统) 通风条件
差 良好 风扇却 循环水冷却
散热系数
散热面积
种类
k W/(m2*℃)
350 冷却介质进口温度
t1 ℃ 30
油进出口温度差 ΔT=T1-T2 ℃ 15
水进出口温度差 Δ t=t2-t1 ℃ 10
散热系数 k
W/(m2*℃) 116
散热面积 A≈PC/(T*k)