液压传动——液压传动系统设计与计算
液压系统设计计算实例

12.13,液压缸的工况图如图12.8所示。
➢ 设计内容与方法
4.拟定液压系统原理图
➢ 设计内容与方法 5.液压元件选择
(1)选择液压泵 ①液压泵最高工作压力 管路总压力损失ΣΔp初步按
0.6MPa估算,有Pp≥pmax+ΣΔp=(4.5+0.6)MPa=5.1MPa ②液压泵最大供油量 取K=1.1,有
➢ 设计内容与方法
3.液压缸参数确定
(5) 采最用低无稳杆定腔速进度油验,算单向最行低程速调度速为阀工调进速时,vm查in=得5最0m小m稳/m定in流,量工进时,
qmin=0.1×10-3m3/min,则
A1≥ qmin 0.1106
vm in
ቤተ መጻሕፍቲ ባይዱ
50
mm2=2 000mm2 满足最低速度要求。
(6) 绘制液压缸工况图 计算各工况下的压力、流量和功率汇总于表
液压与气动控制
F 33667 p 4.5106
4A 4 7482106
3.14
➢ 设计内容与方法
3.液压缸参数确定
( (12) )选 确4 定 定工 液作 压4压 缸力 有效p 工根作据面表积1A2.3和表12.4,初选工作压力p=4.5MPa。
4
4
A= 4 m24=7 482×10-6m2
(3)确定缸筒内径D、活塞杆直径d
➢ 设计内容与方法 5.液压元件选择
①油管 初步选取v=4m/s,则d=m=14.5×103m=14.5mm 查手册确定采用φ18×1.5的紫铜管。 ②滤油器 采用XU-J40×80型过滤器。 ③油箱容积的确定 V=(5~7)qP=(5~7)×20L=(100~140)L
➢ 设计内容与方法
液压传动系统设计计算例题
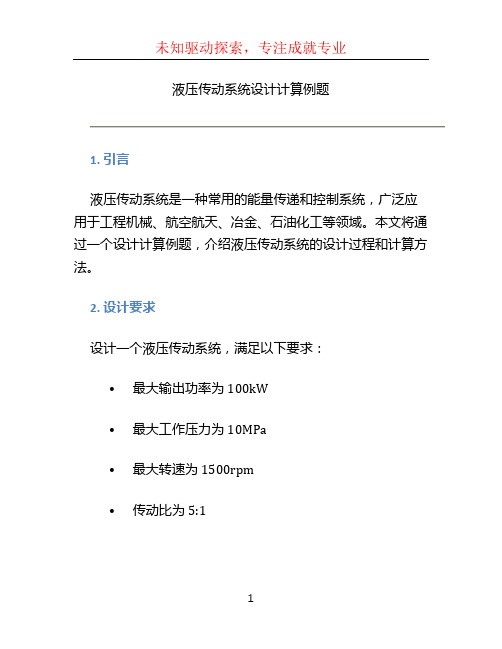
液压传动系统设计计算例题1. 引言液压传动系统是一种常用的能量传递和控制系统,广泛应用于工程机械、航空航天、冶金、石油化工等领域。
本文将通过一个设计计算例题,介绍液压传动系统的设计过程和计算方法。
2. 设计要求设计一个液压传动系统,满足以下要求:•最大输出功率为100kW•最大工作压力为10MPa•最大转速为1500rpm•传动比为5:13. 功率计算根据设计要求,最大输出功率为100kW,转速为1500rpm,可以通过以下公式计算液压机的排量:功率(kW)= 排量(cm^3/rev) × 转速(rpm) × 压力(MPa) × 10^-6由于传动比为5:1,液压泵的排量为液压马达的5倍,因此液压泵的排量为:排量(cm^3/rev) = 功率(kW) / (转速(rpm) × 压力(MPa) × 10^-6 × 5)= 100 / (1500 × 10 × 10^-6 × 5)= 0.133 cm^3/rev4. 泵和马达的选择根据计算结果,液压泵的排量为0.133 cm^3/rev。
在实际中,可以选择一个接近或等于该排量的标准泵来满足需求。
假设我们选择了一台0.15 cm^3/rev的液压泵。
由于传动比为5:1,液压马达的排量为液压泵的1/5,因此液压马达的排量为:排量(cm^3/rev) = 液压泵排量 / 5= 0.15 / 5= 0.03 cm^3/rev同样地,我们可以选择一个接近或等于该排量的标准马达。
5. 油液流量计算油液流量可以通过以下公式计算:流量(L/min) = 排量(cm^3/rev) × 转速(rpm) / 1000液压泵的流量为:流量(L/min) = 0.15 × 1500 / 1000= 0.225 L/min液压马达的流量为:流量(L/min) = 0.03 × 1500 / 1000= 0.045 L/min6. 液压系统元件选择在设计液压传动系统时,除了液压泵和液压马达,还需要选择其他的液压元件,如油箱、油管、阀门等。
液压传动系统设计
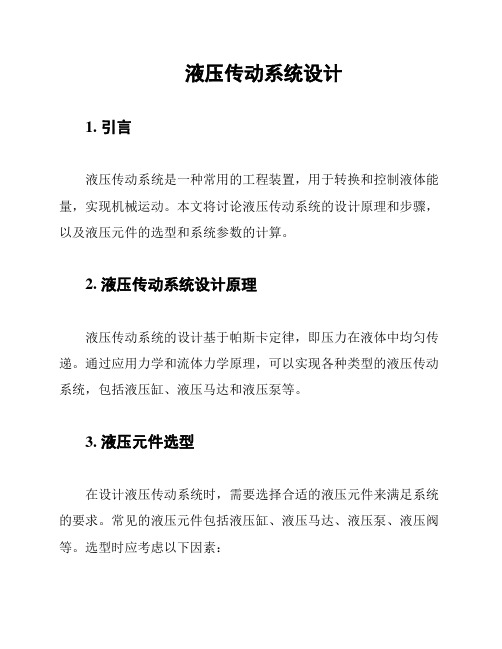
液压传动系统设计
1. 引言
液压传动系统是一种常用的工程装置,用于转换和控制液体能量,实现机械运动。
本文将讨论液压传动系统的设计原理和步骤,以及液压元件的选型和系统参数的计算。
2. 液压传动系统设计原理
液压传动系统的设计基于帕斯卡定律,即压力在液体中均匀传递。
通过应用力学和流体力学原理,可以实现各种类型的液压传动系统,包括液压缸、液压马达和液压泵等。
3. 液压元件选型
在设计液压传动系统时,需要选择合适的液压元件来满足系统的要求。
常见的液压元件包括液压缸、液压马达、液压泵、液压阀等。
选型时应考虑以下因素:
- 载荷和工作压力
- 流量和速度需求
- 空间和尺寸限制
- 可靠性和维护性
4. 液压系统参数计算
设计液压传动系统时,需要计算和确定一些基本参数,以保证系统的性能和稳定性。
这些参数包括:
- 液压流量:根据工作负荷和速度需求计算
- 压力损失:考虑管道和元件的摩擦损失
- 油液温升:根据功率损失和流量计算
- 液压缸和液压马达的力和速度关系:根据帕斯卡定律计算
5. 结论
通过本文的讨论,我们了解了液压传动系统设计的基本原理和步骤。
在实际设计中,应根据具体要求选择合适的液压元件,同时进行必要的参数计算,以确保系统的性能和可靠性。
> 注意:本文所提供的信息仅供参考,具体设计时还需考虑其他因素,并进行详细分析和验证。
参考文献
- [reference 1]
- [reference 2]
- [reference 3]。
液压系统设计篇

液压系统设计篇----4ffaa03a-7161-11ec-876d-7cb59b590d7d液压传动系统设计,除了应符合其主机在动作循环和静、动态性能等方面所提出的要求外,还必须满足结构简单、使用维护方便、工作安全可靠、性能好、成本低、效率高、寿命长等条件。
液压传动系统的设计一般依据流程图见图4-1的步骤进行设计。
图4-1液压传动系统设计流程图第一节明确设计要求要设计一个新的液压系统,首先必须明确机器对液压系统的动作和性能要求,并将这些技术要求作为设计的出发点和基础。
需要掌握的技术要求可能包括:1.机器的特性(1)充分了解主机的结构和总体布置,机构与从动件之间的连接条件和安装限制,以及其用途和工作目的。
(2)负载种类(恒定负载、变化负载及冲击负载)及大小和变化范围;运动方式(直线运动、回转运动、摆动)及运动量(位移、速度、加速度)的大小和要求的调节范围;惯性力、摩擦力、动作特性、动作时间和精度要求(定位精度、跟踪精度、同步精度)。
(3)原动机类型(电机、内燃机等)、容量(功率、速度、扭矩)和稳定性。
(4)操作方式(手动、自动)、信号处理方式(继电器控制、逻辑电路、可编程控制器、微机程序控制)。
(5)系统中每个执行器的动作顺序和动作时间之间的关系。
2.使用条件(1)设置地点。
(2)环境温度、湿度(高温、寒带、热带),粉尘种类和浓度(防护、净化等),腐蚀性气体(所有元件的结构、材质、表面处理、涂覆等),易爆气体(防爆措施),机械振动(机械强度、耐振结构),噪声限制(降低噪声措施)。
(3)维护程度和周期;维修人员的技术水平;保持空间、可操作性和互换性。
3.适用的标准和规则根据用户要求采用相关标准、法则。
4.安全性、可靠性(1)用户在安全方面是否有特殊要求。
(2)指定保修期和条件。
5.经济不能只考虑投资费用,还要考虑能源消耗、维护保养等运行费用。
6.工况分析液压系统的工况分析是为了找出各执行机构在各自工作过程中的速度和负载变化规律。
液压机构传动效率计算公式

液压机构传动效率计算公式液压传动是一种常见的动力传动方式,它利用液体的压力来传递动力。
液压传动系统通常由液压泵、液压缸、液压阀等组成,其中液压机构是实现动力传递和控制的重要部分。
在液压机构中,传动效率是一个重要的性能指标,它反映了液压机构在能量传递过程中的损失情况。
传动效率的计算对于液压机构的设计和优化具有重要意义。
传动效率的计算公式可以通过能量平衡来推导。
液压机构的传动效率可以定义为输出功率与输入功率的比值,即:η = (输出功率 / 输入功率) × 100%。
其中,η表示传动效率,输出功率和输入功率分别表示液压机构的输出功率和输入功率。
在液压机构中,输出功率可以通过液压缸的工作速度和工作压力来计算,输入功率则可以通过液压泵的流量和压力来计算。
因此,传动效率的计算公式可以进一步表示为:η = (输出流量×输出压力×缸有效面积 / 输入流量×输入压力×泵有效面积) × 100%。
在这个公式中,输出流量表示液压缸的工作流量,输出压力表示液压缸的工作压力,缸有效面积表示液压缸的有效工作面积;输入流量表示液压泵的流量,输入压力表示液压泵的压力,泵有效面积表示液压泵的有效工作面积。
传动效率的计算公式可以帮助工程师和设计师在液压机构的设计和优化过程中进行合理的能量平衡分析,从而选择合适的液压元件和参数,提高液压机构的传动效率。
传动效率的计算公式也可以用于液压机构的性能测试和评估,帮助用户了解液压机构的实际工作情况。
在实际工程应用中,传动效率的计算还需要考虑一些实际因素的影响,例如液压元件的摩擦损失、密封件的泄漏损失、管路的压降损失等。
这些因素会对传动效率产生影响,因此在进行传动效率计算时需要进行适当的修正和补偿。
除了传动效率的计算公式外,还可以通过实验方法来测定液压机构的传动效率。
通过在实验台上搭建液压传动系统,可以通过测量输入功率和输出功率来计算传动效率,从而验证计算公式的准确性,并对液压机构的传动效率进行评估和优化。
液压传动系统设计与计算

液压传动系统设计与计算一、液压缸的设计计算1.初定液压缸工作压力液压缸工作压力主要根据运动循环各阶段中的最大总负载力来确定,此外,还需要考虑以下因素:(1)各类设备的不同特点和使用场合。
(2)考虑经济和重量因素,压力选得低,则元件尺寸大,重量重;压力选得高一些,则元件尺寸小,重量轻,但对元件的制造精度,密封性能要求高。
所以,液压缸的工作压力的选择有两种方式:一是根据机械类型选;二是根据切削负载选。
如表9-2、表9-3所示。
表9-2 按负载选执行文件的工作压力表9-3 按机械类型选执行文件的工作压力2.液压缸主要尺寸的计算缸的有效面积和活塞杆直径,可根据缸受力的平衡关系具体计算,详见第四章第二节。
3.液压缸的流量计算液压缸的最大流量:qmax=A·vmax (m3/s) (9-12)式中:A为液压缸的有效面积A1或A2(m2);vmax为液压缸的最大速度(m/s)。
液压缸的最小流量:qmin=A·vmin(m3/s) (9-13)式中:vmin为液压缸的最小速度。
液压缸的最小流量qmin,应等于或大于流量阀或变量泵的最小稳定流量。
若不满足此要求时,则需重新选定液压缸的工作压力,使工作压力低一些,缸的有效工作面积大一些,所需最小流量qmin也大一些,以满足上述要求。
流量阀和变量泵的最小稳定流量,可从产品样本中查到。
二、液压马达的设计计算1.计算液压马达排量液压马达排量根据下式决定:vm=6.28T/Δpm*ηmin(m3/r) (9-14)式中:T为液压马达的负载力矩(N·m);Δpm为液压马达进出口压力差(N/m3);ηmin为液压马达的机械效率,一般齿轮和柱塞马达取0.9~0.95,叶片马达取0.8~0.9。
2.计算液压马达所需流量液压马达的最大流量:qmax=vm·nmax(m3/s)式中:vm为液压马达排量(m3/r);nmax为液压马达的最高转速(r/s)。
液压传动系统设计与计算-说明书
如果忽略切削力引起的颠覆力矩对导轨摩擦力的影响,并设液压缸的机械效率=0.9,根据上述负载力计算结果,可得出液压缸在各个工况下所受到的负载力和液压缸所需推力情况,如表1所示。
表1 液压缸总运动阶段负载表〔单位:N〕3 负载图和速度图的绘制根据负载计算结果和的个阶段的速度,可绘制出工作循环图如图1〔a〕所示,所设计组合机床动力滑台液压系统的速度循环图可根据的设计参数进行绘制,快进和快退速度3.5快进行程L1=100mm、工进行程L2=200mm、快退行程L3=300mm,工进速度80-300mm/min 快进、工进和快退的时间可由下式分析求出。
快进工进快退根据上述数据绘制组合机床动力滑台液压系统绘制负载图〔F-t〕b图,速度循环图c图.ab c在此处键入公式。
4 确定液压系统主要参数4.1确定液压缸工作压力由表2和表3可知,组合机床液压系统在最大负载约为16000时宜取3MPa。
表2按负载选择工作压力表3 各种机械常用的系统工作压力4.2计算液压缸主要结构参数根据参数,液压缸无杆腔的有效作用面积可计算为A1=Fmas/P1-0.5P2=16000/3X10^6那么活塞直径为mm根据经验公式,因此活塞杆直径为d=58.3mm,根据GB/T2348—1993对液压缸缸筒内径尺寸和液压缸活塞杆外径尺寸的规定,圆整后取液压缸缸筒直径为D=80mm,活塞杆直径为d=56mm。
此时液压缸两腔的实际有效面积分别为:根据计算出的液压缸的尺寸,进一步计算液压缸在各个工作阶段中的压力、流量和功率值,如表4所示。
表4 各工况下的主要参数值5 液压系统方案设计根据组合机床液压系统的设计任务和工况分析,所设计机床对调速范围、低速稳定性有一定要求,因此速度控制是该机床要解决的主要问题。
速度的换接、稳定性和调节是该机床液压系统设计的核心。
此外,与所有液压系统的设计要求一样,该组合机床液压系统应尽可能结构简单,本钱低,节约能源,工作可靠5.1确定调速方式及供油形式由表4可知,该组合机床工作时,要求低速运动平稳行性好,速度负载特性好。
液压系统的设计计算步骤和内容
• 最大负载值是初步确定执行元件工作压力和结构尺寸的依据。 • 液压马达的负载力矩分析与液压缸的负载分析相同,只需将上述负载
设计计算
步骤和内容
4~5
>5~7
18
系统工作压力的确定
表9-3 按主机类型选择系统工作压力
设备 类型
磨床
机床
组合机床 牛头刨床
插床 齿轮加工
机床
车床 铣床 镗床
珩磨 拉床 机 龙门 床 刨床
农业机械 汽车工业 小型工程 机械及辅 助机械
工程机械 重型机械 锻压设备 液压支架
船用 系统
压力 /MPa
摆动缸
单叶片缸转角小于300°,双叶片缸转角小于150°
往复摆动运动
齿轮、叶片马达 轴向柱塞马达 径向柱塞马达
结构简单、体积小、惯性小 运动平稳、转大、转速范围宽 结构复杂、转大、转速低
设计计算
步骤和内容
高速小转矩回转运动 大转矩回转运动 低速大转矩回转运动
7
负载分析
• 负载分析就是通过计算确定各液压执行元件的负载大小和方向,并分 析各执行元件运动过程中的振动、冲击及过载能力等情况。
设计计算
步骤和内容
2
1.1 液压系统的设计依据和工况分析
液压系统的设计依据
• 设计要求是进行工程设计的主要依据。设计前必须把主机对液压系统 的设计要求和与设计相关的情况了解清楚,一般要明确下列主要问题:
中英文文献翻译-液压传动系统设计与计算
英文原文Hydraulic actuation system design and computation1. clearing about the design request to carry on the operating mode analysis.When design hydraulic system below, first should be clear about the question, and takes it as the design basis.Main engine use, technological process, overall layout as well as to hydraulic gear position and spatial size request; The main engine to the hydraulic system performance requirement, like the automaticity, the velocity modulation scope, the movement stability, the commutation pointing accuracy as well as the request which to the system efficiency, warm promotes; Hydraulic system working conditions, like temperature, humidity, vibration impact as well as whether has situation and so on corrosiveness and heat-sensitive material existence.In in the above work foundation, should carry on the operating mode analysis to the main engine, the operating mode analysis including the movement analysis and the mechanical analysis, also must establish the load and the operating cycle chart to the complex system, from this understood the hydraulic cylinder or the oil motor load and the speed change as necessary the rule, below makes the concrete introduction to the operating mode analysis content1.1 movements analysesThe main engine functional element according to the technological requirement movement situation, may use the displacement circulation chart (L—t), the speed circulation chart (v—t), or the speed and the displacement circulation chart indicated, from this carries on the analysis to the movement rule.1.1.1 displacements circulation attempts L—tThe chart 1.1 is the hydraulic press hydraulic cylinder moves the circulation chart, the y-coordinate L expression piston moves, the x-coordinate t expression starts from the piston to the reposition time, the rate of curve expression movement of plunger speed.`Chart 1.1 displacements circulation chart1.1.2 speeds circulation chart v—t (or v—L)In the project the hydraulic cylinder movement characteristic may induce is three kind of types. The chart 1.2 is three kind of types hydraulic cylinders v —t chart, the first kind of like chart 1.2 center solid lines show, the hydraulic cylinder starts to make the uniform accelerated motion, then uniform motion,Chart 1.2 speeds circulation chartFinally uniform retarded motion to end point; The second kind, the hydraulic cylinder preceding partly makes the uniform accelerated motion in the overall travelling schedule, in another one partly makes the uniform retarded motion, also the acceleration value is equal; The third kind, the hydraulic cylinder one most above makes the uniform accelerated motion in the overall travelling schedule by a smaller acceleration, then uniform decelerates to the travelling schedule end point. V —t chart three velocity curve, not only clearly has indicated three kind of types hydraulic cylinders movement rule, also indirectly has indicated three kind of operating modes dynamic performance. 1.2 mechanical analyses1.2.1 hydraulic cylinders loads and duty cycle chart 1.2.1.1 hydraulic cylinders load strength computationsWhen the operating mechanism makes the straight reciprocating motion, the hydraulic cylinder must overcome the load is composed by six partsb m g i fc F F F F F F F +++++= (1.1)In the formula: F c In order to resistance to cutting; F f In order to friction drag; F i For inertia resistance; F gFor gravity; F m In order to seal the resistance; F b In order to drain the oil the resistance. 1.2.1.2 hydraulic cylinders cycle of motion various stages overall load strengthThe hydraulic cylinder cycle of motion various stages overall load strength computation, generally includes the start acceleration, quickly enters, the labor enters, quickly draws back, decelerates applies the brake and so on several stages, each stage overall load strength has the difference.(1) starts the acceleration period: By now the hydraulic cylinder or the piston were in from static enough to starts and accelerates to the certain speed, its overall load strength including guide rail friction force, packing assembly friction force (according to cylinder mechanical efficiency ηm =0.9 computation), gravity and so on item, namely:b m g i f F F F F F F ++++= (1.2)(2) fast stage:bm g f F F F F F +++=(3) the labor enters the stage:b m g fc F F F F F F ++++= (1.4)(4)decelerates:b m g i f F F F F F F ++++= (1.5)To the simple hydraulic system, the above computation process may simplify. For example uses the single proportioning pump to supply the oil, only must calculate the labor to enter the stage the overall load strength, if the simple system uses the limiting pressure type variable displacement pump or a pair of association pumps for the oil, then only must calculate the fast stage and the labor enters the stage the overall load strength.1.2.2 oil motors loadWhen the operating mechanism makes the rotary motion, the oil motor must overcome the outside load is: i f e M M M M ++= (1.6)1.2.2.1 operating duties moment of force Me. The operating duty moment of force is possibly a definite value, also possibly as necessary changes, should carry on the concrete analysis according to the machine working condition.1.2.2.2 friction moments. In order to revolve the part journal place friction moment, its formula is: )(M N GFR M f ⋅= (1.7)In the formula: G is revolves the part weight (N); F is the rubbing factor, when the start for the factor, after the start for moves the rubbing factor; R is the journal radius (m).1.2.2.3 moment of inertiaM i . The moment of inertia which in order to revolve the part acceleration or decelerates when produces, its formula is:)(M N t J M i ⋅∆=ε (1.8)In the formula: ε Is the angle acceleration (r/s 2);t∆is the acceleration or decelerates the time (s); J isrevolves the part rotation inertia (2m Kg ⋅),G GD J 412=In the formula: 2GD In order to rotate the part the flywheel effect (2M N ⋅).Each kind may look up <Machine design Handbook>According to the type (1.6), separately figures out the oil motor in a operating cycle various stages load size, then may draw up the oil motor the duty cycle chart 2 determinations hydraulic system main parameter 2.1 hydraulic cylinders design calculations2.1.1 initially decides the hydraulic cylinder working pressureIn the hydraulic cylinder working pressure main basis cycle of motion various stages biggest overall load strength determined, in addition below, but also needs to consider the factor: 2.1.1.1 each kind of equipment different characteristic and use situation.2.1.1.2 considerations economies and the weight factor, the pressure elects lowly, then part size big, the weight is heavy; The pressure chooses high somewhat, then part size small, the weight is light, but to the part manufacture precision, the sealing property requests high.Therefore, the hydraulic cylinder working pressure choice has two ways: One, elects according to the mechanical type; Two, according to cuts the load to elect.If the table 2.1, the table 2.2 shows.The table 2.1 presses the load to choose the execution file the working pressureLoad /N <5000500~10000 10000~20000 20000~30000 30000~50000 >50000Working pressure /MPa≤0.8~1 1.5~22.5~33~44~5>5The table 2.2 presses the mechanical type to choose the execution file the working pressureMechanical typeEngine bedFarm machineryProject machineryGrinderAggregate machine-toolDragon Gate digs the bed Broaching machineWorking pressure /MPaa≤23~5≤88~1010~1620~322.2 oil motors design calculation2.2.1 computations oil motor displacementUnder oil motor displacement according to the type decided that,)(28.63min r m P T V m m η∆= (2.1)In the formula: T is the oil motor load moment of force (N ·m);Pm∆For oil motor import and exportpressure difference (n/m3);is the oil motor mechanical efficiency, the common gear and the plunger motor takes 0.9 ~ 0.95, the leaf blade motor takes 0.8 ~ 0.9.2.2.2 computations oil motor needs the current capacity oil motor the maximum current capacity )(3max max s m n V q m = (2.2)In the formula: Vmis the oil motor displacement (m 3/r); nmaxis the oil motor highest rotational speed(r/s).3 hydraulic pressure parts choice3.1 hydraulic pumps determinations with need the power the computation3.1.1.1 determines the hydraulic pump the biggest working pressure. The hydraulic pressure pumping station must the working pressure determination, mainly acts according to the hydraulic cylinder in the operating cycle various stages to have most tremendous pressure p1, in addition the oil pump loses Sigma Delta p the oil mouth to the cylinder place always pressure ΣΔp , namely ∑∆+=PP P B 1 (3.1)∑∆P loses, the pipeline including the oil after the flow valve and other parts local pressures along theregulation loss and so on, before system pipeline design, may act according to the similar system experience to estimate, common pipeline simple throttle valve velocity modulation system ΣΔp is (2 ~ 5) ×105Pa, with the velocity modulation valve and pipeline complex system∑∆P is (5 ~ 15) ×105Pa, ∑∆P also may onlyconsider flows after various control valves pressure loss, but ignores the circuitry along the regulation loss, various valves rated pressure loses may searches from the hydraulic pressure part handbook or the product sample, Also may refer to the table 1.3 selectionsThe table 3.1 is commonly used, the low pressure each kind of valve pressure loses (Δp n ) ValveΔp n (×105Pa)Valve Δp n (×105Pa)Valve Δp n (×105Pa)Valve Δp n (×105Pa)Cone-wa y valve 0.3~0.5Cone-way valve 3~8 Cone-w ay valve 1.5~2 Cone-w ay valve 1.5~2 Cross valve1.5~3 Cross valve2~3 Cross valve1.5~3 Cross valve3~5 3.1.2 determines the hydraulic pump current capacityqBPumps the current capacity qBbasis functional element operating cycle must the maximum currentcapacityqmaxand the system divulges the determination3.1.2.1 At the same time when more than hydraulic cylinders movement, the hydraulic pump current capacity must be bigger than the maximum current capacity which at the same time the movement several hydraulic cylinders (or motor) needs, and should consider the system divulging wears the volumetric efficiency drop after the hydraulic pump, namely )()(3maxs m q K q B ∑= (3.2)In the formula: K is the system leakage coefficient, generally takes 1.1 ~ 1.3, the great current capacity takes the small value, the small current capacity takes the great value ∑)max(q ; For at the same timemovement hydraulic cylinder (or motor) is biggest (m 3/s). 3.1.2.2 chooses the hydraulic pump the specification Table 3.2 hydraulic pumps overall effectiveness indicesHydraulic pump typeGear pumpThe screw rod pumpsVane pumpRam pumpOverall effectiveness index0.6~0.70.65~0.80 0.60~0.75 0.80~0.85Rotational speed and pumps which according to the above power, may select the standard electric motor from the product sample, again carries on, causes when the electric motor sends out the maximum work rate, in permission scope. 3.2 valves class parts choice 3.2.1 choices basesThe choice basis is: Rated pressure, maximum current capacity, movement way, installment fixed way, pressure loss value, operating performance parameter and working life and so on. 3.2.2 selector valves class parts should pay attention question3.2.2.1 should select the standard stereotypia product as far as possible, only if does not have already time only then independently designs special-purp3.2.2.2 valves class parts specification main basis class after this valve fat liquor most tremendous pressure and maximum current capacity selection. When chooses the overflow valve, should according to the hydraulic pump maximum current capacity selection; When chooses the throttle valve and the velocity modulation valve, should consider its minimum stable current capacity satisfies the machine low-speed performance the request 3.3 accumulators choices3.3.1 accumulators use in to supplement when the hydraulic pump supplies the oil insufficiency, its dischargeable capacity is )(3m t q K L A V Bii -=∑ (3.3)In the formula: A is the hydraulic cylinder active surface (m 2); L is the hydraulic cylinder travelling schedule (m); K is the hydraulic cylinder loss coefficient, when the estimate may take K = 1.2; Supplies the oil current capacity for the hydraulic pump (m 3/s); T is the operating time (s). 3.3.2 accumulators make the emergency energy, its dischargeable capacity is: )(3m t q L A V Bii -=∑ (3.4)When the accumulator uses in absorbs the pulsation to relax the hydraulic pressure impact, should take it as in the system a link if to be connected partially together synthesizes considers its dischargeable capaciAccording to the dischargeable capacity which extracts and considered other requests, then chooses the accumulator the form 3.4 pipelines choices 3.4.1 drill tubings types choiceIn the hydraulic system uses the drill tubing divides the hard tube and the hose, the choice drill tubing should have enough passes flows the section and the bearing pressure ability, simultaneously, should reduce the pipeline as far as possible, avoids the extreme turn and the section sudden change.3.4.1.1 steel pipes: Center the high tension system selects the seamless steel pipe, the low pressure system selects the welded steel pipe, the steel pipe price lowly, performance good, the use is widespread3.4.1.2 copper pipes: The copper tube working pressure below 6.5 ~ 10MPa, the instable tune, is advantageous for the assembly; Yellow copper pipe withstanding pressure higher, reaches 25MPa, was inferior to the copper tube is easy to be curving. Copper pipe price high, earthquake resistance ability weak, is easy to cause the fat liquor oxidation, should as far as possible little use, only uses in the hydraulic unit to match meets not the convenient spot.3.4.2 drill tubings sizes determination3.4.2.1 drill tubings inside diameters d presses down the type computationIn the formula: Q is passes the drill tubing the maximum current capacity (m 3/s); V speed of flow which permits for the pipeline in (m/s). The common oil suction pipe takes 0.5 ~ 5 (m/s); The pressure oil pipe takes 2.5 ~ 5 (m/s); The oil return pipe takes 1.5 ~ 2 (m/s). 3.4.2 drill tubings δ sizes determination)(2σδdp∙≥(3.5) In the formula: P is in the tube the biggest working pressure; When n is the safety coefficient, steel pipe p < 7MPa, takes n=8; When p < 17.5MPa, takes n=6; When p > 17.5MPa, takes n=4.According to drill tubing inside diameter and wall thickness which calculates, looks up the handbook selection standard specification drill tubing 3.5 fuel tank designThe fuel tank function is the oil storage, disperses the oil discharge the quantity of heat, in the precipitation oil the impurity, is leisurely in the oil the gas 3.5.1 fuel tanks designs main point3.5.1.1 fuel tanks should have the enough volume to satisfy the radiation, simultaneously its volume should guarantee in the system the fat liquor completely flows when the fuel tank does not seep out, the fat liquor liquid level should not surpass the fuel tank highly 80%.3.5.1.2 suction boxes tubes and the oil return pipe spacing should be as far as possible big3.5.1.3 fuel tanks bases should have the suitable ascent, releases the oil mouth to set to the most low spot, in order to drains the oil 3.6 oil filters choicesChooses the oil filter the basis to have following several 3.6.1 bearing capacitiesAccording to system pipeline working pressure determination. 3.6.2 filters the precision:According to is protected the part the precision request determination3.6.3 flow the ability:According to through maximum current capacity determination. 3.6.4 resistance pressure drops:Should the satisfied filter material intensity and the coefficient request. 4 hydraulic systems performanceIn order to judge the hydraulic system the design quality, needs to lose to the system pressure, to give off heat , the efficiency and system dynamic characteristic and so on 4.1 circuitries pressure losesAfter hydraulic pressure part specification model and pipeline size determination, may the more accurate computing system pressure loss, the pressure loss include: The oil loses , L P ∆the local pressure after the pipeline C P ∆ along the regulation pressure damages flows after the valve class part pressure loss V P ∆, namely:V C L P P P P ∆+∆+∆=∆ (4.1) System adjustment pressure:P P P ∆+≥10 (4.2)In the formula: P 0For hydraulic pump working pressure or leg adjustment pressure; P 1In order to execution working pressure.If calculates P ∆in the primary election system working pressure time the is sketchier than designation pressure to lose is much bigger than, should remove entire related part, auxiliary specification, again definite pipeline size.4.2 systems give off heatThe system gives off heat originates from the system interior energy loss, like the hydraulic pump and the functional element power loss, the overflow valve overflow loses, the hydraulic valve and the pipeline pressure loss and so on.The system gives off heat the power P computation))(1(W P P B η-= (4.3) In the formula: PB is the hydraulic pump power input (W); η Is the hydraulic pump overall effectiveness indexIf in a operating cycle has several working procedures, then may act according to each working procedure the calorific capacity, extracts the system unit time the average calorific capacity:)()1(11W t P T P i ni b i η-=∑= (4.4)In the formula: T is the operating cycle cycle (s); t i For i working procedure operating time (s); p i is in the circulation the i working procedure power input (W).4.3 systems efficiencyThe hydraulic system efficiency is by the hydraulic pump, the functional element and the hydraulic pressure return route efficiency determinedThe hydraulic pressureηcreturn route efficiency generally may use the type to calculate:2221...........2211b b b b c q p q p q p q p +++=η (4.5)In the formula: p 1,q 1;p 2,q 2;…… For each functional element working pressure and current capacity; p B1,q B1;p B2,q B2 is each hydraulic pump supplies the oil pressure and the current capacity.Hydraulic system overall effectiveness index:c m B ηηηη++= (4.6)In the formula: B η For hydraulic pump overall effectiveness index; m ηIn order to functional element overall effectiveness index; c η For return route efficiency5 draws up the regular worker mapping and the compilation technology documentPasses through after the hydraulic system performance and the essential revision, then may draw up the regular worker mapping, it including plan hydraulic system schematic diagram, system pipeline assembly drawing and each kind of non- standard part design drawing.In the official hydraulic system schematic diagram must mark various hydraulic pressure part the model specification. Regarding automaticity higher engine bed, but also should include the movement part the cycle of motion chart and the electro-magnet, the pressure switch active status. 5.1 determinations hydraulic system parameterMay know by the operating mode analysis in, the labor enters the stage the load strength to be biggest, therefore, the hydraulic cylinder working pressure according to this load strength computation, according to the hydraulic cylinder and the load relations, p 1=40×105Pa. This engine bed for the drill hole aggregate machine-tool, for prevented drills through before when occurs flushes the phenomenon, the hydraulic cylinder oil discharge cavity should have the back pressure, 、p 2 =6×105Pa, for causes quickly to enter quickly draws back the speed to be equal, selects 212A A = the differential motion cylinder, the hypothesis quickly enters the oil discharge pressure which, quickly draws back to lose for Δ p=7×105Pa. 5.2 choices hydraulic pressure part5.2.1 chooses the hydraulic pump and the electric motor 5.2.1.1 determines the hydraulic pump the working pressure.Front had determined the hydraulic cylinder the biggest working pressure for 40×105Pa, selects the intake pipe road pressure to lose Δp=8×105Pa, its adjustment pressure is generally bigger than the system biggest working pressure 5×105Pa, therefore pumps working pressure P B = (40 + 8 + 5) ×105 = 53×105PaThis is the working pressure which the high-pressured small current capacity pumps.The hydraulic cylinder quickly draws back when the working pressure quickly enters when is bigger than, takes its pressure to lose Delta p ' = 4×105Pa, then quickly draws back time pumps the working pressure is: P B =(16.4+4)×105=20.4×105PaThis is the working pressure which the low pressure great current capacity pumps.5.2.1.2 hydraulic pumps current capacities. Quickly enters when the current capacity is biggest, its value is30L/min, the quantity enters when the labor, its value is 0.51L/min, takes K = 1.2,Then: q B=1.2×0.5×10-3=36L/minBecause time the overflow valve steady work most is small is 3L/min, therefore slightly pumps the current capacity to take 3.6L/minCalculates according to above, selects the YYB-AA36/6B double joint vane pump5.2.1.3 definite pipelines sizes: According to the working pressure and the current capacity, according to the type (3.5), the type (3.6) determine the pipeline inside diameter and wall thickness. (Omits)5.2.1.4 determinations fuel-tank capacity fuel-tank capacity may according to the empirical formula estimate, take V = (5 ~ 7) q. In this example: V = 6q = 6 (6 + 36) = 252L related system performance omits.中文翻译液压传动系统设计与计算1. 明确设计要求进行工况分析在设计液压系统时,首先应明确以下问题,并将其作为设计依据。
液压系统设计计算举例
(9.20)
设计计算
步骤和内容
6
液压系统的发热功率
(3) 溢流阀的损失功率
k
Py
pYi qYi
式中
i 1
pYi ——各溢流阀的调整压力;
qYi ——各溢流阀的溢流量;
k——溢流阀数量。
(4) 节流功率损失
(9.21)
式中
k
Pj pji qji i 1
p ji ——各流量阀进出口压差;
q ji ——通过各流量阀的流量;
表9-5 液压缸在各工作阶段的负载值
工况 起动
负载组成 F= Ffs
负载值F/N 1962
推力 /N
F
2180 m
加速
F = Ffd + Fm 1564
1500
快进 工进 快退
F =Ffd F =Ffd + Ft F =Ffd
981 31449 981
1090 34943 1090
设计计算
设计实例
22
1 液压传动系统的设计计算步骤和内容
• 液压系统设计步骤如下: • (1) 明确液压系统的设计要求及工况分析; • (2) 主要参数的确定; • (3) 拟定液压系统原理图,进行系统方案论证; • (4) 设计、计算、选择液压元件; • (5) 对液压系统主要性能进行验算; • (6) 设计液压装置,编制液压系统技术文件。
设计计算
设计实例
19
负载分析
1. 工作负载
由切削原理可知,高速钢钻头钻铸铁孔时的轴向切削力Ft与钻头直径D(mm)、每转进给量s(mm/r) 和铸件硬度HB之间的经验计算式为
Ft 25.5Ds0.8 (HB)0.6 (9.27)
根据组合机床加工的特点,钻孔时的主轴转速n和每转进给量s
- 1、下载文档前请自行甄别文档内容的完整性,平台不提供额外的编辑、内容补充、找答案等附加服务。
- 2、"仅部分预览"的文档,不可在线预览部分如存在完整性等问题,可反馈申请退款(可完整预览的文档不适用该条件!)。
- 3、如文档侵犯您的权益,请联系客服反馈,我们会尽快为您处理(人工客服工作时间:9:00-18:30)。
第九章液压传动系统设计与计算液压系统设计的步骤大致如下:1.明确设计要求,进行工况分析。
2.初定液压系统的主要参数。
3.拟定液压系统原理图。
4.计算和选择液压元件。
5.估算液压系统性能。
6.绘制工作图和编写技术文件。
根据液压系统的具体内容,上述设计步骤可能会有所不同,下面对各步骤的具体内容进行介绍。
第一节明确设计要求进行工况分析在设计液压系统时,首先应明确以下问题,并将其作为设计依据。
1.主机的用途、工艺过程、总体布局以及对液压传动装置的位置和空间尺寸的要求。
2.主机对液压系统的性能要求,如自动化程度、调速范围、运动平稳性、换向定位精度以及对系统的效率、温升等的要求。
3.液压系统的工作环境,如温度、湿度、振动冲击以及是否有腐蚀性和易燃物质存在等情况。
图9-1位移循环图在上述工作的基础上,应对主机进行工况分析,工况分析包括运动分析和动力分析,对复杂的系统还需编制负载和动作循环图,由此了解液压缸或液压马达的负载和速度随时间变化的规律,以下对工况分析的内容作具体介绍。
一、运动分析主机的执行元件按工艺要求的运动情况,可以用位移循环图(L—t),速度循环图(v—t),或速度与位移循环图表示,由此对运动规律进行分析。
1.位移循环图L—t图9-1为液压机的液压缸位移循环图,纵坐标L表示活塞位移,横坐标t表示从活塞启动到返回原位的时间,曲线斜率表示活塞移动速度。
该图清楚地表明液压机的工作循环分别由快速下行、减速下行、压制、保压、泄压慢回和快速回程六个阶段组成。
2.速度循环图v—t(或v—L)工程中液压缸的运动特点可归纳为三种类型。
图9-2为三种类型液压缸的v—t图,第一种如图9-2中实线所示,液压缸开始作匀加速运动,然后匀速运动,图9-2 速度循环图最后匀减速运动到终点;第二种,液压缸在总行程的前一半作匀加速运动,在另一半作匀减速运动,且加速度的数值相等;第三种,液压缸在总行程的一大半以上以较小的加速度作匀加速运动,然后匀减速至行程终点。
v —t 图的三条速度曲线,不仅清楚地表明了三种类型液压缸的运动规律,也间接地表明了三种工况的动力特性。
二、动力分析动力分析,是研究机器在工作过程中,其执行机构的受力情况,对液压系统而言,就是研究液压缸或液压马达的负载情况。
1.液压缸的负载及负载循环图(1)液压缸的负载力计算。
工作机构作直线往复运动时,液压缸必须克服的负载由六部分组成:F=F c +F f +F i +F G +F m +F b (9-1)式中:F c 为切削阻力;F f 为摩擦阻力;F i 为惯性阻力;F G 为重力;F m 为密封阻力;F b 为排油阻力。
图9-3导轨形式①切削阻力F c :为液压缸运动方向的工作阻力,对于机床来说就是沿工作部件运动方向的切削力,此作用力的方向如果与执行元件运动方向相反为正值,两者同向为负值。
该作用力可能是恒定的,也可能是变化的,其值要根据具体情况计算或由实验测定。
②摩擦阻力F f :为液压缸带动的运动部件所受的摩擦阻力,它与导轨的形状、放置情况和运动状态有关,其 计算方法可查有关的设计手册。
图9-3为最常见的两种导轨形式,其摩擦阻力的值为: 平导轨: F f =f∑Fn (9-2) V 形导轨: F f =f∑Fn/[sin(α/2)] (9-3)式中:f 为摩擦因数,参阅表9-1选取;∑Fn 为作用在导轨上总的正压力或沿V 形导轨横截面中心线方向的总作用力;α为V 形角,一般为90°。
③惯性阻力F i 。
惯性阻力F i 为运动部件在启动和制动过程中的惯性力,可按下式计算:()i G vF ma N g t ∆==∆ (9-4)导轨类型导轨材料运动状态摩擦因数(f)滑动导轨铸铁对铸铁启动时低速(v<0.16m/s)高速(v>0.16m/s)0.15~0.20 0.1~0.12 0.05~0.08滚动导轨铸铁对滚柱(珠)淬火钢导轨对滚柱(珠)0.005~0.020.003~0.006静压导轨铸铁0.005为重力加速度,g=9.81 (m/s2);Δv为速度变化值(m/s);Δt为启动或制动时间(s),一般机床Δt=0.1~0.5s,运动部件重量大的取大值。
④重力F G:垂直放置和倾斜放置的移动部件,其本身的重量也成为一种负载,当上移时,负载为正值,下移时为负值。
⑤密封阻力Fm:密封阻力指装有密封装置的零件在相对移动时的摩擦力,其值与密封装置的类型、液压缸的制造质量和油液的工作压力有关。
在初算时,可按缸的机械效率(ηm=0.9)考虑;验算时,按密封装置摩擦力的计算公式计算。
⑥排油阻力F b:排油阻力为液压缸回油路上的阻力,该值与调速方案、系统所要求的稳定性、执行元件等因素有关,在系统方案未确定时无法计算,可放在液压缸的设计计算中考虑。
(2)液压缸运动循环各阶段的总负载力。
液压缸运动循环各阶段的总负载力计算,一般包括启动加速、快进、工进、快退、减速制动等几个阶段,每个阶段的总负载力是有区别的。
①启动加速阶段:这时液压缸或活塞处于由静止到启动并加速到一定速度,其总负载力包括导轨的摩擦力、密封装置的摩擦力(按缸的机械效率ηm=0.9计算)、重力和惯性力等项,即:F=F f+F i±F G+F m+F b (9-5)②快速阶段: F=F f±F G+F m+F b (9-6)③工进阶段: F=F f+F c±F G+F m+F b (9-7)④减速: F=F f±F G-F i+F m+F b (9-8)对简单液压系统,上述计算过程可简化。
例如采用单定量泵供油,只需计算工进阶段的总负载力,若简单系统采用限压式变量泵或双联泵供油,则只需计算快速阶段和工进阶段的总负载力。
(3)液压缸的负载循环图。
对较为复杂的液压系统,为了更清楚的了解该系统内各液压缸(或液压马达)的速度和负载的变化规律,应根据各阶段的总负载力和它所经历的工作时间t或位移L按相同的坐标绘制液压缸的负载时间(F—t)或负载位移(F—L)图,然后将各液压缸在同一时间t(或位移)的负载力叠加。
图9-4负载循环图图9-4为一部机器的F—t图,其中:0~t1为启动过程;t1~t2为加速过程;t2~t3为恒速过程; t3~t4为制动过程。
它清楚地表明了液压缸在动作循环内负载的规律。
图中最大负载是初选液压缸工作压力和确定液压缸结构尺寸的依据。
2.液压马达的负载工作机构作旋转运动时,液压马达必须克服的外负载为:M=M e +M f +M i (9-9) (1)工作负载力矩M e 。
工作负载力矩可能是定值,也可能随时间变化,应根据机器工作条件进行具体分析。
(2)摩擦力矩M f 。
为旋转部件轴颈处的摩擦力矩,其计算公式为:M f =GfR(N·m) (9-10)式中:G 为旋转部件的重量(N);f 为摩擦因数,启动时为静摩擦因数,启动后为动摩擦因数;R 为轴颈半径(m)。
(3)惯性力矩M i 。
为旋转部件加速或减速时产生的惯性力矩,其计算公式为:M i =Jε=J t ω∆∆(N·m) (9-11)式中:ε为角加速度(r/s 2);Δω为角速度的变化(r/s);Δt 为加速或减速时间(s);J 为旋转部件的转动惯量(kg·m 2),J=1GD 2/4g 。
式中:GD 2为回转部件的飞轮效应(Nm 2)。
各种回转体的GD 2可查《机械设计手册》。
根据式(9-9),分别算出液压马达在一个工作循环内各阶段的负载大小,便可绘制液压马达的负载循环图。
第二节 确定液压系统主要参数一、液压缸的设计计算1.初定液压缸工作压力 液压缸工作压力主要根据运动循环各阶段中的最大总负载力来确定,此外,还需要考虑以下因素:(1)各类设备的不同特点和使用场合。
(2)考虑经济和重量因素,压力选得低,则元件尺寸大,重量重;压力选得高一些,则元件尺寸小,重量轻,但对元件的制造精度,密封性能要求高。
所以,液压缸的工作压力的选择有两种方式:一是根据机械类型选;二是根据切削负载选。
如表9-2、表9-3所示。
负载/N<5000500~1000010000~2000020000~3000030000~50000>50000工作压力/MPa≤0.8~1 1.5~2 2.5~3 3~44~5 >5机械类型机 床农业机械 工程机械磨床 组合机床 龙门刨床 拉床工作压力/MPaa≤2 3~5 ≤8 8~10 10~16 20~32缸的有效面积和活塞杆直径,可根据缸受力的平衡关系具体计算,详见第四章第二节。
3.液压缸的流量计算液压缸的最大流量: q max =A·v max (m 3/s) (9-12)式中:A 为液压缸的有效面积A1或A2(m 2);v max 为液压缸的最大速度(m/s)。
液压缸的最小流量: q min =A·v min (m 3/s) (9-13) 式中:v min 为液压缸的最小速度。
液压缸的最小流量q min ,应等于或大于流量阀或变量泵的最小稳定流量。
若不满足此要求时,则需重新选定液压缸的工作压力,使工作压力低一些,缸的有效工作面积大一些,所需最小流量q min也大一些,以满足上述要求。
流量阀和变量泵的最小稳定流量,可从产品样本中查到。
二、液压马达的设计计算1.计算液压马达排量液压马达排量根据下式决定:v m=6.28T/Δp mηmin(m3/r) (9-14)式中:T为液压马达的负载力矩(N·m);Δp m为液压马达进出口压力差(N/m3);ηmin为液压马达的机械效率,一般齿轮和柱塞马达取0.9~0.95,叶片马达取0.8~0.9。
2.计算液压马达所需流量液压马达的最大流量:q max=v m·n max(m3/s)式中:v m为液压马达排量(m3/r);n max为液压马达的最高转速(r/s)。
第三节液压元件的选择一、液压泵的确定与所需功率的计算1.液压泵的确定(1)确定液压泵的最大工作压力。
液压泵所需工作压力的确定,主要根据液压缸在工作循环各阶段所需最大压力p1,再加上油泵的出油口到缸进油口处总的压力损失ΣΔp,即pB =p1+ΣΔp (9-15)ΣΔp包括油液流经流量阀和其他元件的局部压力损失、管路沿程损失等,在系统管路未设计之前,可根据同类系统经验估计,一般管路简单的节流阀调速系统ΣΔp为(2~5)×105Pa,用调速阀及管路复杂的系统ΣΔp为(5~15)×105Pa,ΣΔp也可只考虑流经各控制阀的压力损失,而将管路系统的沿程损失忽略不计,各阀的额定压力损失可从液压元件手册或产品样本中查找,也可参照表9-4选取。
阀名Δp n(×105Pa) 阀名Δp n(×105Pa)阀名Δp n(×105Pa)阀名Δp n(×105Pa)单向阀0.3~0.5 背压阀3~8 行程阀 1.5~2 转阀 1.5~2 换向阀 1.5~3 节流阀2~3 顺序阀 1.5~3 调速阀3~5B B max的泄漏确定。