机床夹紧、进给液压传动系统设计
YT4543型组合机床动力滑台液压传动系统设计

广州城建职业学院毕业设计题目YT4543型组合机床动力滑台液压传动系统设计所在系机电与信息工程学院专业班级 11机电一体化1班学生姓名学生学号指导老师广州城建职业学院教务处制YT4543型组合机床动力滑台液压传动系统设计摘要组合机床是由通用部件和部分专用部件组成的高效、专用、自动化程度较高的机床。
它能完成钻、扩、铰、镗、铣、攻丝等工序和工作台转位、定位、夹紧、输送等辅助动作,可用来组成自动线。
这里只介绍组合机床动力滑台液压系统。
动力滑台上常安装着各种旋转着的刀具,其液压系统的功用是使这些刀具作轴向进给运动,并完成一定的动作循环。
动力滑台是组合机床的一种通用部件。
在滑台上可以配置各种工艺用途的切削头,例如安装动力箱和主轴箱、钻削头、铣削头、镗削头、镗孔、车端面等。
YT4543型组合机床液压动力滑台可以实现多种不同的工作循环,其中一种比较典型的工作循环是:快进一工进二工进死挡铁停留快退停止。
关键词:组合机床;动力滑台;液压绪论 (3)第一章液压传动的发展及优缺点 (4)第二章 YT4543型动力滑台液压系统原理分析 (6)(一) YT4543型动力滑台液压系统基本回路 (7)1.速度控制回路: (7)2.换向回路:三位五通电液换向阀自动化、大流量液体换向、平稳无冲击。
(7)3.顺序动作回路 (7)4.卸荷回路 (7)5.止挡块停留 (7)(二)YT4543型动力滑台液压系统系统组成 (8)1.由限压式变量叶片泵供油, (8)2.用电液换向阀换向, (8)3.用行程阀实现快进速度和工进速度的切换, (8)4.用电磁阀实现两种工进速度的切换, (8)5.用调速阀使进给速度稳定。
(8)(三) YT4543型液压系统工作原理以及液压原理图 (9)(四)动力滑台液压系统工作分析 (9)1.快进:按下启动按钮,使电磁阀A的1Y A得电吸合 (9)2.当快进到指定位置 (10)3.第一次工作进给到位 (11)4.当II工进完成后 (12)5.快退 (13)6.原位停止 (14)7..以上工作环节遵循以下工作原理图 (14)结论 (15)致谢 (15)参考文献: (16)绪论组合机床动力滑台液压系统,能实现的工作循环是:快速前进→工作进给→快速退回→原位停止,液压技术是机械设备中发展速度最快的技术之一。
液压传动课程设计-卧式单面多轴钻孔组合机床动力滑台的液压系统
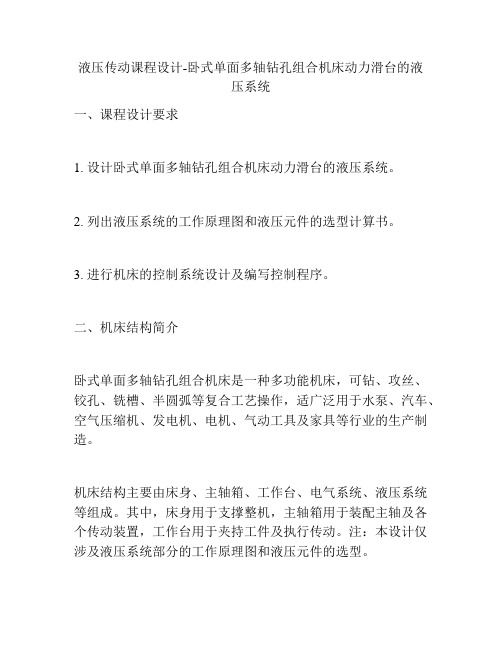
液压传动课程设计-卧式单面多轴钻孔组合机床动力滑台的液压系统一、课程设计要求1. 设计卧式单面多轴钻孔组合机床动力滑台的液压系统。
2. 列出液压系统的工作原理图和液压元件的选型计算书。
3. 进行机床的控制系统设计及编写控制程序。
二、机床结构简介卧式单面多轴钻孔组合机床是一种多功能机床,可钻、攻丝、铰孔、铣槽、半圆弧等复合工艺操作,适广泛用于水泵、汽车、空气压缩机、发电机、电机、气动工具及家具等行业的生产制造。
机床结构主要由床身、主轴箱、工作台、电气系统、液压系统等组成。
其中,床身用于支撑整机,主轴箱用于装配主轴及各个传动装置,工作台用于夹持工件及执行传动。
注:本设计仅涉及液压系统部分的工作原理图和液压元件的选型。
三、液压系统工作原理图液压系统主要用于机床的升降、夹紧、进给等控制操作。
下面的工作原理图展示了该机床的主要液压系统结构。
液压油泵为双联泵,分别提供高压和低压液压油,高压系统主要用于机床的动力传输和工作台的升降,低压系统则用于工作台和主轴箱的夹持、进给和径向递进。
四、液压元件的选型计算本文中设计的液压系统主要包括液压油泵、液压缸、液压阀、液压滤清器、液压压力表等液压元件。
针对所需控制的液压作用,根据相应的公式和数据手册,进行液压元件的选型计算。
液压元件选型计算书如下:五、控制系统设计本设计中,机床的控制系统主要由PLC控制器、触摸屏、传感器、执行器和电磁阀等组成,通过编写相应的控制程序,实现机床的高效稳定运行。
液压系统的控制程序中主要包括如下控制命令:1. 单向液压缸的伸出和缩回控制命令。
2. 双向液压缸的伸出和缩回控制命令。
3. 液压油泵的控制启停命令。
4. 电磁阀的开关控制命令。
5. 液压滤清器的定期清洗命令。
通过不同的控制命令组合,可以实现机床的不同运动状态和操作需求,从而提高机床的生产效率和工作质量。
六、总结本文对卧式单面多轴钻孔组合机床动力滑台的液压系统进行了详细介绍,并给出了液压系统的工作原理图和液压元件的选型计算书,同时简要讲述了机床的控制系统设计流程和控制命令。
第十二讲 机床进给传动系统设计

数控伺服进给系统
三、进给伺服系统传动机构
2、滚珠丝杠副原理、特点及分类
消除轴向间隙、调整预紧力方式
通过调整双滚珠螺母的轴向相对位置,使两个螺母的滚珠分别压向螺 旋滚道的两侧面。但滚珠丝杠螺母机构间隙调整的精度要求高,要求能作 微调以获得准确的间隙预紧量。 常用的方法: a、垫片调隙;
b、螺纹调隙;
Metal Cutting & Machine Tools
机床内联系传动链
内联系传动链,是从保证传动精度进行设计的。因此,内联系传动 链的设计原则,与外联系传动链是不同的 。
一、误差来源与传递规律
2、误差传递规律
传动链中,各传动件的误差 在整个传动链中按传动比依次传 递,最后反映到末端件上,使工 件或刀具产生传动误差。 把越靠近末端件的传动副的 传动比安排得越小,对减小其前 面各传动件的误差影响的效果越 显著,这样,就可以有效地减小 传递到末端件的总误差.
概述
一、进给系统类型及其应用
进给传动系统—用来实现机床的进给运动和辅助运动。 机床进给传动类型: 2)液压传动
采用油液作介质,通过液压元件传递动力和运动。传动结构简单 ,工作可靠,传动平稳,便于实现自动化,应用日益广泛。
3)电气传动
采用可调速电动机,直接驱动执行件,或经简单的齿轮变速箱,驱 动执行件。机械结构简单,可在工作中无级变速,便于自动控制,但成 本较高。
Metal Cutting & Machine Tools
数控伺服进给系统
二、伺服电动机
1、步进电机
步进电机又称脉冲电机,每接受数控装置所输出的一个电脉冲信号 ,电机轴就转过一定的角度,称为步距角。步进电机的角位移与输入脉 冲个数成正比,在时间上与输入脉冲同步。
双头车床液压系统的设计

课程设计说明书课题名称:液压与气压传动课程设计学院:专业班级:学号:学生:指导老师:《液压与气压传动课程设计》评阅书题目液压与气压传动课程设计学生姓名学号指导教师评语及成绩指导教师签名:年月日答辩评语及成绩答辩教师签名:年月日教研室意见总成绩:室主任签名:年月日摘要本文是关于双头车床液压系统设计过程的阐述。
主要包括系统方案的确定、液压集成块与控制系统的设计几个方面的内容。
双头车床加工时,由于零件较长,拟采用零件固定,刀具旋转和进给的加工方式,其加工动作循环方式是:快进→工进→快退→停止,同时要求各个车削头能单独调整。
显而易见,采用双头车床能使原需多道工序的产品能一次切削完成,使工序简化,生产效益大大提高。
且这种设计所产生的产品对成均匀,精度高。
对于双头车床的动力执行部分,本设计采用液压伺服机构。
液压伺服机构较其他机构有传动平稳、噪音小、驱动力大等优点,同时也存在漏油、爬行、体积大等缺点。
为了尽量避免液压系统的上述缺点,系统设计时用集成块来代替管路,在液压系统采用液压阀集成配置,可以显著减少管路联接和接头,降低系统的复杂性,增强现场添加和更改回路的柔性,具有结构紧凑、安装维护方便、泄漏少、振动小、利于实现典型液压系统的集成化和标准化等优点。
关键词:双头车床液压系统液压伺服机构目录摘要 (I)目录 01设计任务 (1)2 液压回路的工况分析 (2)2.1确定对液压系统的工作要求 (2)2.2参数拟定液压系统工作原理图 (2)3 计算和选择液压元件 (5)3.1 原始数据 (5)3.2 确定液压缸参数 (5)3.3 液压系统计算与选择 (9)总结 (15)参考文献 (16)1设计任务液压系统设计计算是液压传动课程设计的主要内容,包括明确设计要求进行工况分析、确定液压系统主要参数、拟定液压系统原理图、计算和选择液压件以及验算液压系统性能等。
本次设计的是一台立式双轴钻孔组合机床动力滑台液压系统。
要求设计的动力滑台实现的工作循环是:根据加工要求,刀具旋转由机械传动来实现;主轴头沿导轨中心线方向的“快进(Fast Feed)一工进(Working Feed)—快退(Fast Return)—停止(Stop)”工作循环拟采用液压传动方式来实现。
组合机床液压系统设计

组合机床液压系统设计1 方案的确定1.1整体性分析要求此液压系统实现的工作循环是:工件夹紧工作台快进工作台1工进工作台2工进工作台快退工件松开。
运动部件重5800N,工作台快进、快退的速度4。
8m/min,工进的速度60—960mm/min,最大行程640mm,工进行程240mm.最大切削力8000N.夹紧缸行程30mm,夹紧力35000N.对于铣削专用机床的液压系统而言,加工的零件需要精度高,定位准确。
所以整个系统的设计要求定位精度高,换向速度快。
在设计阀的时候,考虑这些方面变的尤其重要,要考虑到工作在最低速度时调速阀的最小调节流量能否满足要求.在行程方面,应该比要求的工作行程大点,包括工作行程、最大行程和夹紧缸行程,主要是考虑到在安全方面和实际运用中。
在压力方面也要考虑到满足最大负载要求。
而且在液压系统能满足要求的前提下,使液压系统的成本较低。
1。
2 拟定方案由上述分析可得以下两种方案:方案一液压系统中工作台的执行元件为伸缩缸,工件的夹紧用单杆活塞缸;工作台采用节流阀实现出油口节流调速,用行程阀实现工作台从快进到工进的转换,压力继电器控制一工进与二工进的转换,在工进回路上串接个背压阀;为了防止工件在加工过程中松动,在夹紧进油路上串接个单向阀;工作台的进、退采用电磁换向阀;夹紧缸的夹紧与放松用电磁阀控制。
方案二液压系统中工作台的执行元件为单杆活塞缸,工件的夹紧也采用单杆活塞缸;工作台采用调速阀实现进油口节流调速,也采用行程阀实现工作台从快进到工进的转换,压力继电器控制一工进与二工进的转换,工进时,为了避免前冲现象,在回路上串接个背压阀;夹紧缸上串接个蓄能器和单向阀,避免工件在加工过程中松动;工作台的进、退换向采用电液换向阀,工作台快进时,采用差动连接;夹紧缸的夹紧与放松用电磁阀控制。
方案比较:单杆活塞缸比伸缩缸结构简单,价格便宜,易维护,而且也能满足要求;调速阀的性能比节流阀稳定,调速较好,用于负载变化大而运动要求稳定的系统中;采用出油口调速回路中油液通过节流阀产生的热量直接排回油箱散热;夹紧缸进油口处串接蓄能器,更好的保证工件的夹紧力,使工件在加工过程中始终在夹紧状态。
卧式双面铣削组合机床液压系统设计.doc

卧式双面铣削组合机床液压系统设计合肥工业大学课程设计任务书《卧式双面铣组合机床液压系统设计成果》主要内容是尝试设计卧式双面铣组合机床液压系统。
机床的加工对象是铸铁齿轮箱。
动作顺序为夹紧缸夹紧→工作台快速接近工件→工作台进给→工作台快速后退→夹紧缸松开→原位停止。
工作台运动部件的总重力为4000牛顿,加减速时间为0.2秒,采用平面导轨,静动摩擦系数μs=0.2,μd=0.1。
夹紧缸行程为30毫米,夹紧力为800牛顿,工作台快进行程为100毫米,快进速度为3.5米/分钟。
工作进展如下:设计课题:卧式双面铣组合机床液压系统设计32工况分析32.1负荷分析33液压系统方案设计43.1液压缸参数计算43.2绘制液压系统原理图63 3液压元件的选择93.3.2阀门元件和辅助元件的选择103.3.3油管的选择114液压系统性能校核计算124.1检查系统压力损失并确定压力阀的调整值124.2油145设计概要参考文献146机床的加工对象是铸铁齿轮箱。
动作顺序为夹紧缸夹紧→工作台快速接近工件→工作台进给→工作台快速后退→夹紧缸松开→原位停止。
工作台运动部件的总重力为4000牛顿,加减速时间为0.2秒,采用平面导轨,静动摩擦系数μs=0.2,μd=0.1。
夹紧缸行程为30毫米,夹紧力为800牛顿,工作台快进行程为100毫米,快进速度为3.5米/分钟。
工作进展如下:设计课题:卧式双面铣组合机床液压系统设计32工况分析32.1负荷分析33液压系统方案设计43.1液压缸参数计算43.2绘制液压系统原理图63 3液压元件的选择93.3.2阀门元件和辅助元件的选择103.3.3油管的选择114液压系统性能校核计算124.1检查系统压力损失并确定压力阀的调整值124.2油145设计概要参考文献146机床的加工对象是铸铁齿轮箱。
动作顺序为夹紧缸夹紧→工作台快速接近工件→工作台进给→工作台快速后退→夹紧缸松开→原位停止。
工作台运动部件的总重力为4000牛顿,加减速时间为0.2秒,采用平面导轨,静动摩擦系数μs=0.2,μd=0.1。
液压传动课程设计题目
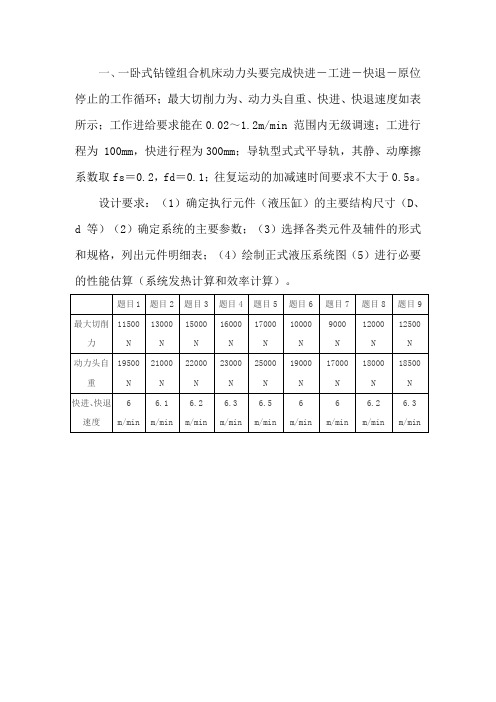
工作台导轨采用平 导轨,导轨间静摩擦系数 fs=0.2,动摩擦系数
fd=0.1,要求工作台能在任意位置上停留,其它参数如表所示。
设计任务:(1)确定执行元件(液压缸)的主要结构尺寸(D、
d 等);(2)确定系统的主要参数;(3)选择各类元件及辅件的形
式和规格,列出元件明细表;(4)绘制正式液压系统图;(5)进行
最大切 9000 8000 9100 9200 9300 7000 9000 9500 9400
削力
N
N
N
N
N
N
N
N
N
工作
台、夹 4000 3500 4100 4200 4300 3000 4000 3500 4000
具的总 N
N
N
N
N
N
N
N
N
重量
快进速 4.5
4
5
5.5
6
4.5
6
4.5
5
度 m/min m/min m/min m/min m/min m/min m/min m/min m/min
工进行程 100 mm 50 mm 80 mm 90 mm 100 mm 70 mm 80 mm 80 mm 85 mm
六、设计一台专用铣床,工作台要求完成快进——工作进给——
快退——停止的自动工作循环。工件夹具重量为 1500N,工作进给速
度为 0.06~1m/min,往复运动加、减速时间为 0.05s,工作采用平
切削阻 30468 30468 35000 30468 35000 30468 30000 31000 31500
力
N
N
N
N
N
N
N
液压传动课程设计

【液压传动课程设计说明书设计题目:半自动液压专用铣床液压系统[工程技术系机械设计制造及其自动化4班。
设计者指导教师2016 年 12 月 1 日摘要、液压系统设计计算是液压传动课程设计的主要内容,包括明确设计要求进行工况分析、确定液压系统主要参数、拟定液压系统原理图、计算和选择液压件以及验算液压系统性能等。
现以半自动液压专用铣床液压系统为例,介绍液压系统的设计计算方法。
设计一台多用途大台面液压机液压系统,适用于可塑材料的压制工艺,如冲压、弯曲翻边、落板拉伸等。
要求该机的控制方式:用按钮集中控制,可实现调整,手动和半自动,自动控制。
要求该机的工作压力、压制速度、空载快速下行和减速的行程范围均可根据工艺要求进行调整。
主缸工作循环为:快降、工作行程、保压、回程、空悬。
顶出缸工作循环为:顶出、顶出回程(或浮动压边)。
关键字:液压; 快进; 工进; 快退{前言本课程是机械设计制造及其自动化专业的主要专业基础课和必修课,是在完成《液压与气压传动》课程理论教学以后所进行的重要实践教学环节。
本课程的学习目的在于使学生综合运用《液压与气压传动》课程及其它先修课程的理论知识和生产实际知识,进行液压传动的设计实践,使理论知识和生产实际知识紧密结合起来,从而使这些知识得到进一步的巩固、加深和扩展。
通过设计实际训练,为后续专业课的学习、毕业设计及解决工程问题打下良好的基础。
,(1) 液压传动课程设计是一项全面的设计训练,它不仅可以巩固所学的理论知识,也可以为以后的设计工作打好基础。
在设计过程中必须严肃认真,刻苦钻研,一丝不苟,精益求精。
(2) 液压传动课程设计应在教师指导下独立完成。
教师的指导作用是指明设计思路,启发学生独立思考,解答疑难问题,按设计进度进行阶段审查,学生必须发挥主观能动性,积极思考问题,而不应被动地依赖教师查资料、给数据、定方案。
(3) 设计中要正确处理参考已有资料与创新的关系。
任何设计都不能凭空想象出来,利用已有资料可以避免许多重复工作,加快设计进程,同时也是提高设计质量的保证。
- 1、下载文档前请自行甄别文档内容的完整性,平台不提供额外的编辑、内容补充、找答案等附加服务。
- 2、"仅部分预览"的文档,不可在线预览部分如存在完整性等问题,可反馈申请退款(可完整预览的文档不适用该条件!)。
- 3、如文档侵犯您的权益,请联系客服反馈,我们会尽快为您处理(人工客服工作时间:9:00-18:30)。
液压传动课程设计
中国矿业大学机电学院
选修课
设计参数:
不计惯性负载
题目:在某专用机床上有一夹紧进给液压系统,完成工件的先夹紧后、后进给任务,工作原理如下:
夹紧油缸:
快进→慢进→达到夹紧力后启动进给油缸工作
进给油缸:
快进→慢进→达到进给终点→快速退回
夹紧油缸快速退回。
夹紧缸快进速度:0.05m/s
夹紧缸慢进速度:8mm/s
最大夹紧力:40KN
进给油缸快进速度:0.18m/s
进给油缸慢进速度:0.018m/s
最大切削力:120KN
夹紧缸行程:用行程开关调节(最大250mm)
进给缸行程:用行程开关调节(最大1000mm)
一、工况分析:
1.负载分析
已知最大夹紧力为40KN,则夹紧油缸工作最大负载
140
F KN =
已知最大切削力为120KN,则进给油缸工作最大负载
2120
F KN
=
根据已知负载可画出负载循环图1(a)
根据已知快进、快退速度及工进时的速度范围可画出速度循环图1(b)
图1(a)
图1(b)
2.确定液压缸主要参数
根据系统工作原理可知系统最大负载约为120KN 参照负载选择执行元件工作压力和主机类型选择执行元件工作压力最大负载宜选取18p MPa =。
动力滑台要求快进、快退速度相等,选用单杆液压缸。
此时液压缸无缸腔面积1A 与有缸腔面积2A 之比为2,即用活塞杆直径d 与活塞直径D 有d=的关系。
为防止液压缸冲击,回油路应有背压2P ,暂时取MPa P 6.02=。
从负载循环图上可知,工进时有最大负载,按此负载求液压缸尺寸。
根据液压缸活塞力平衡关系可知:
M
e
F A p A p η+=
2211 212A A =
其中,M η为液压缸效率,取95.0=M η 2
46
2
111046.8910)3.04(95.031448)2
(m p p F A M e
-⨯=⨯-=
-
=
η
m A D 1067.014
.31046.894441
=⨯⨯==
-π m D d 075.0707.0==
将D 和d 按GB2348-30圆整就近取标准值,即
D=0.11m=110mm d=0.08m=80mm 液压缸的实际有效面积:
2
42
222
42
11077.444
1003.954
m d D A m D A --⨯=-=⨯==
πππ 确定了液压缸结构尺寸,就可以计算在各工作阶段中压力、流量和功率。
依据计算结果画工况图如表2。
表2液压缸在不同工作阶段的压力、流量和功率值
图3液压缸工况
四:拟定基本回路:
从主机工况可知,该液压系统应具有快速运动、换向、速度换接和调压、卸压等回路,同时为尽可能提高系统效率可以选择变量液压泵或双泵供油回路,此列选择双泵供油。
1.选择各基本回路:
(1)双泵供油的油路回路。
双泵油源包括低压大流量泵和高压小流量泵。
液压缸快速运动时,双泵供油;工作进给时,高压小流量泵供油,低压大流量泵卸荷;由溢流阀调定系统工作压力,如图4所示
(2)快速运动和换向回路
这一回路采用液压缸差动连接实现快速运动,用三位五通电液阀实现换向,并能实现快进时,液压缸的差动连接,如图5所示
图4 液压源
图5 换相回路
图6 速度换接回路
(3)速度换接回路
为提高换接的位置精度,减小液压冲击,应采用行程阀与调速阀并联的转换回路。
同时,电液换向阀的换向时间可调,保证换向过程平稳,如图6所示
(1)卸荷回路:
在双泵供油的油源回路中,可以利用卸荷阀(外控顺序阀)实现低压大流量泵在工进和停止时卸荷。
2.将各基本回路综合成液压系统
把上述各基本回路组合画在一起,得到如图7所示的液压系统原理图(不包括圆框内的元件)。
将此图仔细检查一遍,可以发现,这个图所示系统在工作中还存在问题,必须进行修改和整理:
图7 液压回路的综合和整理
1-双联叶片泵;1A-小流量液压泵;1B-大流量液压泵;
2-三位五通电液阀;3-行程阀;4-调速阀;5-单向阀;6-液压缸;
7-卸荷阀;8-背压阀;9-溢流阀;10-单向阀;11-过滤器;
12-压力表接点;a-单向阀;b-顺序阀;c-单向阀;d-压力继电器;修改如下:
(1)滑台工进时,液压缸的进、回油路相互接通不能实现工进,应该在换向回路中串联单向阀a,将进、回油路隔断,
如图7所示。
(2)为实现液压缸差动连接,应该在换向回路上串接一个顺序阀b,阻止油液流回油箱。
(3)滑台工进后应能自动转为快退,因而需在调速阀出口处
接压力继电器d。
(4)为防止空气进入液压系统,在回油路上接一单向阀c。
(5)将顺序阀b与背压阀8的位置对调,将顺序阀与油源处的卸荷阀合并,省去一个元件。
综合后整理得到如图8所示的液压系统:
图8 整理后的液压系统原理图
1-双联叶片泵;1A-小流量液压泵;1B-大流量液压泵;
2-三位五通电液阀;3-行程阀;4-调速阀;5-单向阀;6-单向阀;
7-卸荷阀;8-背压阀;9-溢流阀;10-单向阀;11-过滤器;
12-压力表接点;13-单向阀;14 -压力继电器;。