主轴加工工艺
车床主轴的加工工艺
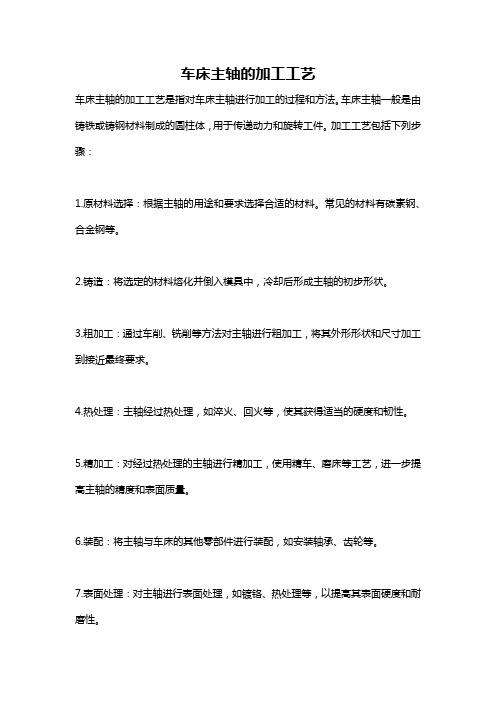
车床主轴的加工工艺
车床主轴的加工工艺是指对车床主轴进行加工的过程和方法。
车床主轴一般是由铸铁或铸钢材料制成的圆柱体,用于传递动力和旋转工件。
加工工艺包括下列步骤:
1.原材料选择:根据主轴的用途和要求选择合适的材料。
常见的材料有碳素钢、合金钢等。
2.铸造:将选定的材料熔化并倒入模具中,冷却后形成主轴的初步形状。
3.粗加工:通过车削、铣削等方法对主轴进行粗加工,将其外形形状和尺寸加工到接近最终要求。
4.热处理:主轴经过热处理,如淬火、回火等,使其获得适当的硬度和韧性。
5.精加工:对经过热处理的主轴进行精加工,使用精车、磨床等工艺,进一步提高主轴的精度和表面质量。
6.装配:将主轴与车床的其他零部件进行装配,如安装轴承、齿轮等。
7.表面处理:对主轴进行表面处理,如镀铬、热处理等,以提高其表面硬度和耐磨性。
8.检测:对加工完成的主轴进行检测,包括尺寸、形状、硬度等的检测,确保其达到设计要求。
以上是车床主轴加工的一般工艺流程,具体的加工工艺还会根据不同的要求和设计进行调整和改进。
C6150车床主轴箱箱体加工工艺及工装夹具设计

C6150车床主轴箱箱体加工工艺及工装夹具设计1.C6150车床主轴箱箱体加工工艺主轴箱箱体一般由铸铁材料制成,其加工工艺主要包括以下几个步骤:(1)铸造准备:对铸铁材料进行熔炼、净化和浇铸前的处理,确保铸件质量。
(2)铸件浇铸:将熔化的铸铁材料倒入模具中,使其冷却、凝固成型。
(3)铸件脱模:待铸件冷却后,从模具中取出,进行清理和修整。
(4)精密加工:对铸件进行加工,包括切割、铣削、钻孔等工序,以使得箱体尺寸和形状精确到达要求。
(5)表面处理:对箱体表面进行打磨、抛光,以提高外观质量。
(6)检测和装配:对加工好的主轴箱箱体进行检测,确保质量达到要求,然后进行组装。
在主轴箱箱体的加工过程中,合理设计工装夹具可以提高加工效率和加工质量,减少劳动强度。
(1)定位夹具设计:主要用于确定箱体的位置和角度,以保证加工精度。
定位夹具可以根据箱体形状和尺寸设计,一般采用刚性夹具,如V型块。
(2)夹紧夹具设计:用于夹紧箱体,以防止其在加工过程中发生松动或位移。
夹紧夹具可以采用螺栓和垫圈进行固定,或者采用气动或液压夹紧装置。
(3)切削夹具设计:用于加工箱体的切削过程,包括刀具和刀架的选择和安装。
切削夹具要根据加工要求和箱体材料的切削特性来设计,以保证加工质量和效率。
(4)保护夹具设计:用于保护箱体的外表面和内孔。
保护夹具可以采用橡胶垫和保护套等材料进行设计,以确保箱体不被切削工具碰伤。
(5)检测夹具设计:用于检测箱体的尺寸和形状,以确保其符合加工要求。
检测夹具可以采用测量工具和传感器等设备进行设计,以确保检测的准确性和可靠性。
总之,C6150车床主轴箱箱体加工工艺和工装夹具设计是车床加工中的重要环节,可以通过合理的工艺和夹具设计来提高加工效率和加工质量。
主轴的加工工艺路线
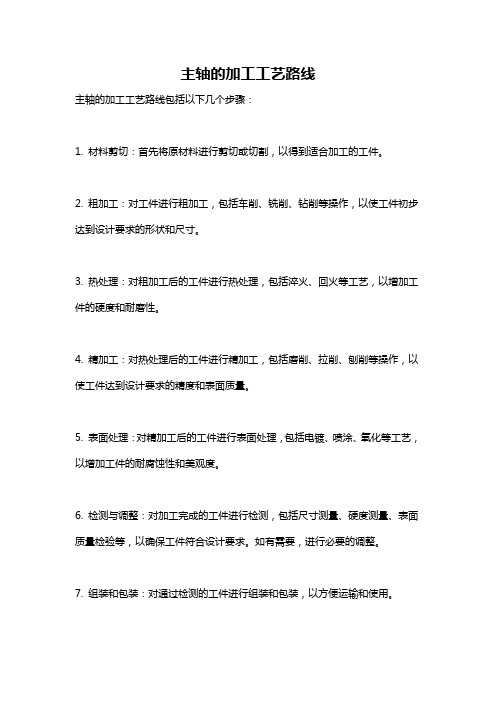
主轴的加工工艺路线
主轴的加工工艺路线包括以下几个步骤:
1. 材料剪切:首先将原材料进行剪切或切割,以得到适合加工的工件。
2. 粗加工:对工件进行粗加工,包括车削、铣削、钻削等操作,以使工件初步达到设计要求的形状和尺寸。
3. 热处理:对粗加工后的工件进行热处理,包括淬火、回火等工艺,以增加工件的硬度和耐磨性。
4. 精加工:对热处理后的工件进行精加工,包括磨削、拉削、刨削等操作,以使工件达到设计要求的精度和表面质量。
5. 表面处理:对精加工后的工件进行表面处理,包括电镀、喷涂、氧化等工艺,以增加工件的耐腐蚀性和美观度。
6. 检测与调整:对加工完成的工件进行检测,包括尺寸测量、硬度测量、表面质量检验等,以确保工件符合设计要求。
如有需要,进行必要的调整。
7. 组装和包装:对通过检测的工件进行组装和包装,以方便运输和使用。
8. 质量控制:对整个加工过程进行质量控制,包括使用符合要求的设备和工具、制定合理的工艺流程、操作规范等,以确保加工出的主轴达到设计和客户要求的质量标准。
45钢车床主轴加工工艺路线
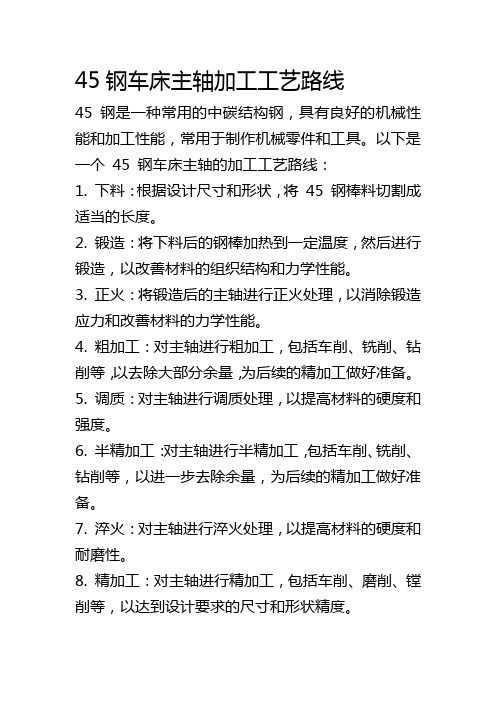
45钢车床主轴加工工艺路线
45 钢是一种常用的中碳结构钢,具有良好的机械性能和加工性能,常用于制作机械零件和工具。
以下是一个45 钢车床主轴的加工工艺路线:
1. 下料:根据设计尺寸和形状,将45 钢棒料切割成适当的长度。
2. 锻造:将下料后的钢棒加热到一定温度,然后进行锻造,以改善材料的组织结构和力学性能。
3. 正火:将锻造后的主轴进行正火处理,以消除锻造应力和改善材料的力学性能。
4. 粗加工:对主轴进行粗加工,包括车削、铣削、钻削等,以去除大部分余量,为后续的精加工做好准备。
5. 调质:对主轴进行调质处理,以提高材料的硬度和强度。
6. 半精加工:对主轴进行半精加工,包括车削、铣削、钻削等,以进一步去除余量,为后续的精加工做好准备。
7. 淬火:对主轴进行淬火处理,以提高材料的硬度和耐磨性。
8. 精加工:对主轴进行精加工,包括车削、磨削、镗削等,以达到设计要求的尺寸和形状精度。
9. 珩磨:对主轴进行珩磨处理,以提高表面质量和精度。
10. 检验:对主轴进行检验,以确保其符合设计要求和质量标准。
11. 包装:对主轴进行包装,以方便运输和储存。
需要注意的是,具体的加工工艺路线可能因不同的加工要求和设备条件而有所不同,以上仅为参考。
同时,在加工过程中还需要注意安全和环保问题。
电机主轴加工工艺

电机主轴加工工艺电机主轴加工工艺是电机制造过程中不可或缺的一环。
主轴作为电机的核心部件之一,其加工工艺直接关系到电机的使用效果和寿命。
本文将从主轴加工的工艺流程、加工方法和注意事项三个方面进行探讨。
一、主轴加工的工艺流程1.原材料选购主轴加工的第一步是原材料的选购。
通常情况下,主轴的材质要求为优质合金钢或不锈钢。
原材料的选购要求材质均匀、无气孔、无裂纹等缺陷。
2.粗加工粗加工是主轴加工的第二步。
主要的粗加工方法有车削、铣削、钻削等。
粗加工时要注意加工精度和表面光洁度。
3.热处理热处理是主轴加工的重要步骤之一。
通过热处理可以改善主轴的机械性能和物理性能,并且可以提高主轴的硬度和耐磨性。
4.精加工经过热处理后的主轴需要进行精加工。
主要的精加工方法有磨削、拉削、镗削等。
精加工时要注意加工精度和表面光洁度。
5.表面处理表面处理是主轴加工的最后一步。
通过表面处理可以提高主轴的耐腐蚀性和美观度。
主要的表面处理方法有喷漆、电镀、阳极氧化等。
二、主轴加工的方法1.车削法车削法是主轴加工中最常用的一种方法。
其优点是加工精度高、效率高、成本低。
但是需要注意的是车削法容易产生划痕和表面粗糙度较高的问题。
2.磨削法磨削法是主轴加工中另一种常用的方法。
其优点是加工精度高、表面光洁度高、不易产生划痕等问题。
但是磨削法的成本较高,加工效率也较低。
3.拉削法拉削法是主轴加工中一种比较新颖的方法。
其优点是加工效率高、表面光洁度高、不易产生划痕等问题。
但是需要注意的是拉削法需要专门的设备和技术,成本较高。
三、主轴加工的注意事项1.加工前要对原材料进行检查在加工前要对原材料进行检查,排除材料的缺陷和不合格问题。
2.加工时要注意加工精度和表面光洁度加工时要注意加工精度和表面光洁度,尽可能减少划痕和表面粗糙度。
3.热处理时要注意温度和时间的控制热处理时要注意温度和时间的控制,以确保主轴的机械性能和物理性能得到有效的改善。
4.表面处理时要注意材料的选择和表面光洁度表面处理时要注意材料的选择和表面光洁度,以确保主轴的耐腐蚀性和美观度得到有效的提高。
电机主轴加工工艺

电机主轴加工工艺1. 引言电机主轴是电机的核心部件,其加工工艺直接影响电机的性能和质量。
本文将详细介绍电机主轴的加工工艺,包括材料选择、加工方法、表面处理等方面内容。
2. 材料选择电机主轴通常采用高强度、高硬度的合金钢作为材料。
常见的材料有45#钢、40Cr、42CrMo等。
材料选择需要综合考虑电机使用环境、承载能力和加工难度等因素。
3. 加工方法3.1 切削加工切削加工是电机主轴最常用的加工方法之一。
其常见的切削方式包括车削、铣削和钻削等。
具体步骤如下: 1. 车削:通过车床将材料转动起来,利用刀具对其进行切削。
2. 铣削:利用铣床或数控铣床进行切削,可实现复杂形状的加工。
3. 钻削:通过钻床或数控钻床进行孔径加工。
3.2 精密磨削精密磨削是电机主轴加工的重要环节,可提高主轴的加工精度和表面质量。
常见的磨削方法包括平面磨削、外圆磨削和内圆磨削等。
3.3 热处理电机主轴在加工完成后需要进行热处理,以提高其硬度和耐磨性。
常见的热处理方法有淬火、回火和表面渗碳等。
具体步骤如下: 1. 淬火:将主轴加热至临界温度,然后迅速冷却,以获得高硬度。
2. 回火:将淬火后的主轴再次加热至一定温度,并保持一段时间,然后冷却至室温。
此过程可减少主轴的脆性。
3. 表面渗碳:通过在主轴表面添加含碳物质,并进行加热处理,使其表层获得高硬度。
4. 表面处理为了提高电机主轴的耐腐蚀性和摩擦特性,常常需要进行表面处理。
常见的表面处理方法有镀铬、喷涂和氮化等。
1. 镀铬:利用电镀技术,在主轴表面形成一层铬镀层,增加其硬度和耐磨性。
2. 喷涂:通过喷涂工艺,在主轴表面形成一层耐磨涂层,提高其摩擦特性。
3. 氮化:将主轴加热至高温,并与氮气反应,使其表面形成氮化层,提高硬度和耐磨性。
5. 质量控制为了确保电机主轴的质量,需要进行严格的质量控制。
常见的质量控制方法包括尺寸检测、硬度检测和金相分析等。
1. 尺寸检测:通过三坐标测量仪、千分尺等工具对主轴的尺寸进行检测,确保其符合设计要求。
主轴的热处理工艺

主轴的热处理工艺主要包括粗加工阶段的正火或退火,半精加工阶段的调质热处理(淬火+高温回火),以及精加工阶段的淬火和回火等步骤。
在粗加工阶段,主轴通常会进行正火或退火处理。
这两种处理方式的目的都是消除锻造应力,细化晶粒,使金属组织均匀化,以利于切削加工。
退火的具体工艺为:加热温度Ac3+(30~50)℃,保温时间120min,冷却方式为随炉冷却。
正火的具体工艺为:加热温度Ac3+(30~50)℃,保温时间120min,冷却方式为空冷。
在半精加工阶段,主轴会进行调质热处理(淬火+高温回火)。
具体的热处理工艺为:870℃淬火,保温70min,油淬,500℃回火,保温100min,油淬。
如果调质热处理不当,可能会导致钢中存在较多的网络状、块状游离铁素体,从而使钢材的强度和冲击韧性下降。
因此,淬火温度偏低,回火温度过高是主要的不当操作。
淬火时冷却速度缓慢时,铁素体会从原奥氏体晶界优先析出,形成网状铁素体;钢在加热过程中,由于加热温度偏低或保温时间不足时,铁素体未完全溶于奥氏体中,淬火后形成块状游离铁素体。
在精加工阶段,主轴通常会进行淬火和回火处理。
淬火的具体工艺为:加热温度偏低,回火温度过高是主要的不当操作。
淬火时冷却速度缓慢时,铁素体会从原奥氏体晶界优先析出,形成网状铁素体;钢在加热过程中,由于加热温度偏低或保温时间不足时,铁素体未完全溶于奥氏体中,淬火后形成块状游离铁素体。
需要注意的是,不同的主轴材料和热处理工艺会产生不同的效果。
例如,对于45钢制造的主轴,其工艺路线为下料→锻造→正火→粗加工→调质→半精加工(花键除外)→局部淬火(内外圆锥面)+低温回火→粗磨→铣花键→花键感应淬火+低温回火→精磨。
整体调质硬度可达到220~250HBS;内外圆锥面采用盐。
以上就是主轴的热处理工艺的基本内容,具体的工艺可能会根据主轴的材质、形状尺寸和使用环境等因素有所不同。
主轴工艺

机床主轴的加工工艺流程
(1)整体淬火主轴:下料→锻造→正火或退火→粗机械加工(粗车,留精车量为3~6mm)
→去应力退火或调质处理→精机械加工(精车,留磨量为0.4~0.8mm)→整体淬火→粗磨(留精磨量为0.15~0.20mm)→低温时效→精磨→成员。
对于开关简单、精度要求不高、不经锻造及不需预先热处理及低温时效时,其加工工艺流程可简化为:下料→切削加工→淬硬→磨削至尺寸。
(2)渗碳淬火主轴:下料→锻造→正火→精机械加工(精车,留磨量子为0.40~0.80mm)
→渗碳→经车削加工去除非需渗碳部位→淬火、低温回火→精磨(留下精磨量为0.15~0.20mm)→低温时效→精磨至尺寸。
(3)表面淬火主轴:下料→锻造→退火或正火→粗机械加工(粗车,留粗量子为3~6mm)
→调质处理→精机械加工(精车,留磨量0.5~0.6mm)→表面淬火、低温回火→粗磨(留下精磨量为0.15~0.25mm)→低温时效→精磨至尺寸。
对于形状简单、精度要求不高、不需锻造、预先热处理及低温时效时,其加工工艺流程可简化为:下料→粗机械加工(粗车)→调质处理→精机械加工(精车)→表面淬火→磨至尺寸。
(4)渗氮主轴:下料→锻造→退火或正火→粗机械加工(粗车,留粗量子为4~6mm)→
调质处理(切割样品检查金相组织)→精机械加工(精车,留磨量0.9~1.0mm)→去应力退火→精磨(留下精磨量为0.06~0.10mm;非渗氮处每面留磨量0.40mm以上或镀镍等防渗层)→渗氮→精磨至尺寸。
应当说明,以上主轴,当精度要求很高时,还可适当增加去应力退火及低温时效次数。
- 1、下载文档前请自行甄别文档内容的完整性,平台不提供额外的编辑、内容补充、找答案等附加服务。
- 2、"仅部分预览"的文档,不可在线预览部分如存在完整性等问题,可反馈申请退款(可完整预览的文档不适用该条件!)。
- 3、如文档侵犯您的权益,请联系客服反馈,我们会尽快为您处理(人工客服工作时间:9:00-18:30)。
主轴加工工艺的研究与探讨
主轴的功用、精度:
1.功用:
在一般的金属切削机床中,主轴把旋转运动及扭矩通过主轴端部的夹具或刀具。
在工作中,主轴不但承受扭转力矩,而且承弯曲力矩。
所以要求机床主轴的扭转刚度和弯曲刚度都很高。
2.机床主轴精度:(机床精度的重要组成部分)
即输出旋转精度,也为主轴的工作表面精度。
下面仅真对主轴自身的关键精度而言:
1)主轴支承轴径、轴肩端面的精度:
●主轴支承轴径的制造精度(椭圆度、锥度、不同轴
度、不垂直度等)
●主轴轴肩端面对主轴回转轴心线的不垂直度
2)主轴工作表面的精度:
●内外锥面的尺寸精度、几何形状精度、光洁度和接触
精度;
●定心表面相对与支承轴径表面的同轴度;
●定位端面相对与支承轴径轴心线的垂直度。
注:机床主轴的工作表面指主轴的莫氏锥孔、轴端外锥或法蓝外圆等。
3.主轴材料、热处理及作用
材料:45#,65Mn,40Cr,38CrMoAl(氮化钢),20Cr或20Cr MnTi(渗碳钢)等
热处理:退火,正火,调质,高频淬火,渗碳,氮化,
热处理作用:提高主轴强度,刚性,表面硬度,及耐疲劳强
度、尺寸稳定性等综合机械性能。
退火及正火:降低材料硬度,改善切削加工性能,消除锻造
内应力,细化晶粒,并使金属组织均匀。