Multi-Criterion Optimal Design of Automotive Door Based on Metamodeling Technique and Genetic Al
多目标遗传算法

Abstract: In this paper we propose the use of the genetic algorithm (GA) as a tool to solve multiobjective
optimization problems in structures. Using the concept of min-max optimum, a new GA-based multiobjective optimization technique is proposed and two truss design problems are solved using it. The results produced by this new approach are compared to those produced by other mathematical programminቤተ መጻሕፍቲ ባይዱ techniques and GA-based approaches, proving that this technique generates better trade-o s and that the genetic algorithm can be used as a reliable numerical optimization tool.
参数化白车身结构轻量化多目标优化

参数化白车身结构轻量化多目标优化作者:王传青董传林马亮来源:《计算机辅助工程》2018年第01期摘要:利用SFE Concept建立某轿车白车身的参数化模型,采用有限元法对白车身的静态弯曲和扭转刚度、主要低阶模态进行分析,并将仿真结果与试验结果进行对比。
将参数化白车身与动力总成、底盘、闭合件连接后,仿真分析整车正面100%碰撞安全性能并验证有限元模型的有效性。
提出通过相对灵敏度分析确定白车身非安全件设计变量的方法,采用最优拉丁超立方方法生成样本点,基于径向基神经网络方法拟合近似模型,以白车身非安全件和正碰安全件为轻量化对象,通过第二代非劣排序遗传算法对白车身进行多目标优化设计。
结果表明:在白车身静态弯曲刚度降低3.60%、静态扭转刚度降低3.91%、一阶弯曲模态固有频率降低0.09%、一阶扭转模态固有频率上升1.26%、正碰安全性能基本不变的情况下,白车身质量减少24.17 kg,减重7.42%,轻量化效果显著。
关键词:轿车;参数化;白车身;轻量化;多目标优化;灵敏度中图分类号:U463.1;TP31文献标志码:B文章编号:1006-0871(2018)01-0015-07Abstract: The parametric model of passenger car body-in-white is built by SFE Concept. The static bend and torsion stiff, and the main modality of body-in-white are analyzed. The simulation result is compared with the test result. The body-in-white is connected with power assembly, chassis and closure members. The carload safety performance of 100% frontal impact is simulated and analyzed. The effectiveness of the finite element model is validated. A new method is presented, and the design variables of body-in-white unsafe parts are confirmed using relative sensitivity analysis. The sample points are generated using the optimal Latin hypercube method. The approximation model is fitted based on radial basis neural network method. The multi objective optimization design on body-in-white is carried out using NSGA-Ⅱ algorithm. The results show that the mass of body-in-white is reduced 24.17 kg(7.42%) on the conditions that the bend stiff is reduced by 3.60%, the torsion stiff is reduced by 3.91%, the bend modal frequency is reduced by 0.09%, the torsion modal frequency is increased by 1.26%, and the front impact performance is not changed obviously. The lightweight efficiency is significant.Key words: passenger car; parameterization; body-in-white; lightweight; multi objective optimization; sensitivity0 引言车身质量约占汽车总质量的30%~40%,在空载情况下,70%的油耗浪费在车辆自身质量上。
Multiobjective Optimal topology design of structures

Multiobjective optimal topology design of structures T.-Y.Chen,S.-C.WuAbstract The multiobjective topology optimization de-signs have been tried in this paper.The minimum com-pliance and the maximum fundamental eigenvalue are the two objectives pursued.The constraint is the amount of material which is allowed to use in a speci®ed design space.The design variables are the normalized densities of the®nite elements in the design space.To minimize the number of elements whose design variables have values between0and1,penalties are added to those design variables to force them to be either0(nonexistence)or1 (existence).The timing of adding the penalty is also studied.Topologies obtained in two dimensional design space with or without penalty and using different timing approaches are compared and discussed.1IntroductionThe topology optimization is different from the conven-tional shape optimization.It does not generate the opti-mum shape from an initial shape.As a result,the in¯uence of the initial design on the optimum shape can be com-pletely eliminated.The optimum shape obtained by to-pology optimization is thus regarded as the true optimum in a design space for a speci®c application.In recent years a lot of research papers such as Bendsùe and Kikuchi (1988),Mlejnek(1992),Yang and Chung(1994)and Ma et al.(1993)have been published in this area.In general two types of approaches have been used to®nd the opti-mum topologies of the structures.One is the homogeni-zation method developed by Bendsùe and Kikuchi(1988). This method assigned three design variables to each®nite element.Two of the design variables represent the length of the two sides of the rectangular hole in the square2-dimensional®nite element and the other one design variable is for the orientation of the rectangular hole.This formulation leads to anisotropic material property for each element and the solution process becomes compli-cated.The other method used is the so-called density method.An assumed formula for Young's modulus was introduced by Mlejnek(1992).The material property re-mains isotropic in the whole design process.Althoughthere is lack of strong theoretical base for the Young's modulus assumption,the application of this approach ismuch easier.The topologies generated by these two approaches often include some elements with design variable values notequal0or1.These elements are shown by gray colors inthe topology plots and their existences are uncertain.Toget useful topologies,the post processing work of pro-ducing clear topologies is necessary.Penalty functions are employed to penalize the design variables which are not0or1.Adding the penalty terms to the objective function forces most design variables to approach either0or1 gradually.A clear topology thus appears.The topology optimizations are usually applied to single objective optimization problems.The most popular ob-jective is either the minimization of the compliance or the maximization of the eigenvalue of the structures.The topologies for the two objectives in the same design spaceare usually dissimilar.A compromised optimum topologymust be sought if the two objectives are pursued simul-taneously.The purpose of this paper is to®nd optimum topologiesfor minimizing the compliances and maximizing the fun-damental eigenvalues of the structures.The constraint isthe limitation of material usage in a design space.In solving these multiobjective optimization problems,a penalty function is also added to the objective function to minimizethe number of unclear elements in the®nal solution.2Multiobjective optimization formulationIn dealing with multiobjective optimization,the Pareto optimal solutions are sought.The meaning of Pareto op-timal solution is as follows:XÃis a Pareto optimal solutionif there exists no feasible X which can decreasesome objective functions without at least one objective function increase.Figure1shows the Paretooptimal solutions for a two criterion problem.To obtain the Pareto optimal solutions,many methodscan be used.These include the sequential optimization method,the constraint method,the weighting method,the minimax approach,the compromise programming,thegoal programming,the method of pairwise comparisons,the trade-off method and the surrogate-worth trade-off method.The weighting method is the easiest one to be Computational Mechanics21(1998)483±492ÓSpringer-Verlag1998483Communicated by S.N.Atluri,24January1998Ting-Yu Chen,Shyh-Chang WuDepartment of Mechanical Engineering,National Chung Hsing University,Taichung,Taiwan40227,R.O.C.This research was supported by National Science Council of the Republic of China under contract No.NSC85-2212-E-005-013. The authors also want to express their appreciation for the comments made by the reviewer.implemented.However,this method does not ensure®nding the whole Pareto optimal set for nonconvex problems.Dhingra(1990),Grandhi et al.(1993)and Kuppuraju and Mistree(1986)implemented some appli-cations of multiobjective optimizations.Since compromise programming formulation is more general,it is used in this paper.Save and Prager(1985)de®ned the objective function for the compromise programming in general form to bel Xki 1w p if i X Àf if maxiÀf minip231p1where f i X is the i th objective function;f mini and f maxiarethe minimal value and the worst value obtainable for f i, respectively.w i is the weight for the i th objective f i Y p in-directly controls the weight of each objective.For p 1,it is simply the weighting method.For p3I,it is the minimax approach.For2p`I,the larger values in the parentheses carry greater weights.The objective functions to be optimized in this research contains the minimum compliance and the maximum fundamental eigenvalue.The constraint is the limited material being used in the prescribed design space.The design variable is the normalized density which is de®ned asq i q ii02where q i is the density used in the®nite element analysis and q i0is the true density of the material used.The multiobjective topology design problem using compromise programming can be formulated as follows.Minimize w p1C q ÀC minC maxÀC minpw p2k maxÀk qk maxÀk minp451p3 Subject toni 1q i m i M 4 0q i1Y i 1Y F F F Y n 5 where q is the design variable vector;C q represents the compliance function;C min and C max are the minimum and the worst obtainable compliances,respectively;k X is the fundamental eigenvalue function;k max and k min are the maximum and the worst obtainable eigenvalues,respec-tively;q i is the i th design variable which is associated with the i th®nite element;m i is the mass of the i th®nite ele-ment when q i 1;M is the amount of material allowed to use in the design space.n is the number of®nite elements in the design space.C min and k max in equation(2)are obtained by solving the following single-objective optimization problems. Minimize C q 6 Subject toni 1q i m i M 7 0q i1Y i 1Y F F F Y n 8andMinimizeÀk q 9 Subject toni 1q i m i M 10 0q i1Y i 1Y F F F Y n 11C max and k min in equation(3)are the compliance and the eigenvalue obtained by using the optimal design variable vectors for k max and C min,respectively.In order to minimize the number of unclear elements in the®nal topology,penalties are added to those design variables which do not have value of0or1.The penalty function is de®ned asni 1R sin q i p 12where R is a given penalty parameter which can vary it-eration by iteration and q i is the i th design variable. The reason for choosing sinusoidal function is that the function is continuous and differentiable and also it is symmetric about the most unwanted design variable value of0.5.Another advantage is due to the nonlinear nature of the function.Heavier penalties are automatically imposed on those design variables whose values are very close to 0.5.As we can see from the function that when q i equals0 or1,there is no penalty at all since this value clearly in-dicates the nonexistence or existence of the®nite element. Because the design variable value of0.5is the most dif®-cult value for the determination of the existence of a®nite element,it is given the largest penalty.The sum of the penalties is an indicator for the clearness of the topology. It is obvious that the indicator value will be small if most design variables are close to0or1.To produce the penalty effect,the penalty function of equation(12)is added to the objective function.To have a minimum value for the penalized objective function,both the penalty term and the original objective function have to be minimized.The smaller the penalty term,the clearer the topology.The multiobjective topology design problemnow becomes484Minimize @w p1C q ÀC minmax minp4w p2k maxÀk qk maxÀk minp51pni 1R sin q i pA13Subject toni 1q i m i M 14 0q i1Y i 1Y F F F Y n 15Although the purpose of adding the penalty to the design variables is to get a clear topology,the adding of penalty should not begin at the®rst iteration.Adding the penalty at the beginning of the iteration process not only causes premature convergence but also makes the design vari-ables dif®cult to cross0.5value in the early stage.The effect of adding penalty term to the objective function at early stage is equivalent to limiting the variations of de-sign variables implicitly.The topologies thus obtained may not be the optimum solutions.Two timings of adding the penalty to the objective function are proposed.The ®rst timing of adding the penalty is at the®fth iteration. This is based on numerical experiences that the rough topologies have been formed for most problems after®rst several iterations.This timing of adding penalty will be named penalty I in later discussions.The other timing to add the penalty to the objective function is at the time when the number of design variables having values greater than0.95and less than0.05is over50%of the total number of design variables.This approach assumes that the rough topology has been formed when half of elements having design variables of0or1and it gives half of the design variables plenty of time to become0or1 freely.After that the design variables are forced to ap-proach0or1.This timing will be called penalty II in later text.The density approach is used to do the topology opti-mization.The Young's modulus of each®nite element in the optimization process is assumed to vary according to the following formula.E i q a i E i0 16 where q i is the design variable;E i is the Young's modulus used in the computations;a is a given value usually be-tween2and4to penalize the small q i values;E i0is the real Young's modulus of the material.From this equation it is obvious that when q i equals 1,the real Young's modulus is used.i.e.the®nite ele-ment exists.On the other hand if q i equals0,the Young's modulus equals0.The®nite element does not exist.For the design variable having value between0and 1,a corresponding Young's modulus is still given to the ®nite element according to equation(16).However,in reality there may not exist material having such Young's modulus.This is the reason why penalties are proposed in this paper to make the design variables be either0or1.3Sensitivity analysisTo solve the multiobjective optimization problems using mathematical programming method,the sensitivity of the objective function(13)has to be computed.The®rst de-rivatives of the compliance and the eigenvalue can be obtained by the following derivations.The compliance function C q is de®ned asC q f P g T f U g 17 where f P g is the static force vector and f U g is the dis-placement vector;T means the transpose of the vector andq is the design variable vector.Taking derivatives of equation(17)with respect to the design variable q i giveso Co q if Pg To f U go q i18and o f U g a o q i is well known to beo f U go q iÀ K À1o Ko q if Ug 19where K is the stiffness matrix of the structure. Substituting(19)into(18)yieldso Co q iÀf P g T K À1o Ko q if U gÀf U g To Ko q if Ug Àf U g To k io q if Ug 20where k i is the i th element stiffness matrix and thismatrix can be expressed ask i E k i0 21 where k i0 is obtained by dividing k i by Young's modulusE.Plugging equations(16)and(21)into(20)results ino Co q iÀf U g Ta k iq if Ug 22Since MSC/NASTRAN is employed to do the®nite ele-ment analysis in this paper and the software provides el-ement strain energy,equation(22)is therefore convertedto the following form to simplify the computations.o Co q iÀ2a ESE iq i23where ESE i 1a2f U g T k i f U g is the element strainenergy given by MSC/NASTRAN.The®rst derivative of the fundamental eigenvalue canbe obtained by the following equation developed by Foxand Kapoor(1968).o k1o q if/1g To Ko q if/1gÀk1f/1g To Mo q if/1g 24where k1is the fundamental eigenvalue of the structure;f/1g is the orthonormal eigenvector of the®rst mode; Mis the mass matrix of the structure.485The design variable q i is assumed to be related to the element mass matrix asm i q i m i0 25 where m i is the element mass matrix used in the opti-mization process; m i0 is the real mass matrix of the i th element.Substituting equations(21)and(25)into(24)giveso k1 o q i2a EMSE iq iÀk1f/1g T m i0 f/1g 26where EMSE i 1a2f/1g T k i f/1g element modal strain energy.After linearizing the objective function,the sequential linear programming(SLP)is used to solve the multiob-jective optimization problems.4Numerical examplesTwo numerical examples are illustrated.The®rst example has a design space of16Â10inch shown in Fig.2.The ®nite element mesh contains32Â20quadrilateral plate elements.The four sides of the design area are®xed.A concentrated force of180lbs is perpendicularly acting on the center point of the design space.The design space has a constant thickness of0.1in.The material used is steelhaving Young's modulus30Mpsi,weight density0X283lb/in3and Poisson's ratio0.3.The material which is allowed to use in the design space to construct the opti-mum structure is50%of the total material in the design space.The initial value for the design variables is0.35. Before®nding the multiobjective solutions,the single-objective optimizations are executed®rst to®nd k max and C min values.k min and C max are obtained separately by two extra®nite element analyses using the two optimum variable vectors obtained previously.Table1gives the single-objective extreme values.Figures3and4show the topologies for the minimum compliance design.Figure3is obtained without adding penalties to the design variables.Figure4is the result using penalty I.It can be seen from the®gures that adding penalties to the design variables do not yield different topologies for this example problem.This is because most elements approach0or1very quickly before penalty is ing penalty II also yields a similar topology as Fig.4.Figures5and6are the topologies of maximum eigen-value design.Without penalty Fig.5shows a vague to-pology.Figure6is the topology obtained using penalty I. It is obvious that this topology is clearer than the one shown in Fig.5.Figures7and8record the histories of eigenvalue variations and the percentage variations ofel-Table1.Extreme values for compliance and eigenvalue ofexample1Penalty C min(in A lb)C max(in A lb)k min k maxNo9.6176868.314695079671615Penalty I9.601421374708422500769Penalty II9.6015390.6470842.34822708486ements having design variable values close to0or1.It is observed that more than98%of design variables reach0 or1when penalties are given.Without penalty only80%of design variables reach their extreme values.The dropping of the eigenvalues when penalties are used is found in Fig.7.This is reasonable because adding penalty forces the design variables to approach0or1and these design variable changes make the design deviate from the theo-retical optimum solution.For multiobjective optimization,Table2shows the parameter values which appear in equation(13).Table3 lists the pareto optimal solutions obtained by different parameters.Figures9through12show the topologies obtained by different parameters and penalties.In these®gures w1is the weight for the compliance and w2is the weight for the eigenvalue.p is chosen to be50because of computational limitation.Figures9and10compared with Fig.11and12 contain many unclear elements since no penalties are added.Almost all topologies are dominated by eigenvalue topology.The compromised topology which takes care of the needs for compliance and eigenvalue is not found.The reason is due to the normalization of C q and k q in the multiobjective function(13).Table3shows that the ratios of C max a C min for all cases are much greater than the ratios of k max a k min and this causes the normalized compliance term to be much less than the normalized eigenvalue term in the multiobjective function.The importance of the compliance in the multiobjective function thus becomes negligible.Figure11is the only topology showing some material in the central part to support the static force.The parameters used for this case are p 50Y w1 0X8and w2 0X2.Because these parameters heavily emphasize the importance of the compliance,the compromised topology is roughly formed.Figures13through16record the his-tories of compliance and eigenvalue variations.Figure13 shows the increase of compliances since the topology is gradually formed toward the eigenvalue topology.Fig-ure14shows the stable increases of eigenvalues.Figure16Table2.Parameter valuesw1,w2w1,w2w1,w2p=10.2,0.80.5,0.50.8,0.2p=500.2,0.80.5,0.50.8,0.2487shows the initial increases and followed by decreases of eigenvalues.This is because penalty forces the design variables to deviate from their theoretical optimum values. The second example has the same design space as in example1.Instead of constraining four sides,only four corner points of the design area are formed.A concen-trated force of40lbs is perpendicularly acting on the center point of the design space.The design space has a constant thickness of0.1in.The material used is steel having Young's modulus30Mpsi,weight densityTable3.Pareto optimal solutions of example1w1,w2p=1p=500.5,0.50.8,0.20.2,0.80.5,0.50.8,0.20.2,0.8 NP C min9.617049Compliance458.825175.1161365.321298.57543.7323052.86C max6868.299Eigenvalue875971476944459295130828885572998808894849k min1469507Iterations404040404040k max9671615(0+1)%0.745310.795310.782810.796880.770310.77969 PI C min9.601126Compliance9515.086396.717917.619870.16036.0919870.1C max42136.88Eigenvalue439888035617104484053447744429721514477444k min470842.3Iterations412840404040k max2500769(0+1)%0.985940.984380.984380.984380.984380.98438 PII C min9.601126Compliance1010.11543.832786.892388.81213.498296.3C max5390.589Eigenvalue316005533109514937704294316430704143095761k min470842.3Iterations555445516655k max4822708(0+1)%0.985940.984380.985940.984380.984380.98594 NP±no penalty,PI±penalty I,PII±penaltyII 4880.283lb/in3and Poisson's ratio0.3.The material which is allowed to use in the design space to construct the optimum structure is also50%of the total material in the design space.The initial value for the design variables is0.35.The extreme values of compliance and eigenvalue are listed in Table4.Some Pareto optimal solutions are shown in Table5.Figures17and18show the topologies for the minimum compliance and the maximum eigenvalue designs without penalty,respectively.Figures19and20are the topologies for the multiobjective designs using penalty I and II,res-pectively.A compromised topology is found in Fig.19when heavier weight is given to the compliance along with penalty I.If weights for the compliance and the eigenvalue are switched,the topology will be dominated by the ei-genvalue.The eigenvalue-dominated topology is also found in Fig.20even compliance weighting is larger when penalty II is used.In addition to the weighting effects,the major reason for obtaining this eigenvalue-dominated to-pology originates from the normalizations of the two ob-jectives in equation(9).Using penalty I approach the ratios of C max a C min and k max a k min are21.63and1.495, respectively.As a result the normalized compliance be-comes very small compared with the normalized eigen-value.The situation is even worse when penalty II is used. The two respective ratios for penalty II are973.6and2.38. The eigenvalue dominates the cost function in both cases and therefore the eigenvalue oriented topology is obtained no matter what the weights are.Figures21to24show the variations of the compliances and eigenvalues according to their weights in the cost function.The larger the weight,the better the result for the corresponding objective.In this example checkerboard patterns are observed. Diaz and Sigmund(1995)pointed out that this isbecauseTable4.Extreme values for compliance and eigenvalues of ex-ample2Penalty C min(in A lb)C max(in A lb)k min k maxNo 5.21998379379135599 Penalty I 6.192133.966008689858 Penalty II 6.8466664.745920109501489Table5.Pareto optimal solutions of example2w1,w2p=1p=500.5,0.50.8,0.20.2,0.80.5,0.50.8,0.20.2,0.8 NP C min 5.21856Compliance52.315630.402123.53123.30364.873284.244C max982.955Eigenvalue129248126712133927128489123047132211k min79379.1Iterations404040404040k max135599(0+1)%0.868750.820310.881250.803130.698440.84844 PI C min 6.19242Compliance46.75248.72760240.1428.3087.662781106.82C max133.959Eigenvalue10647096756.511719310082886755.8119158k min60086.1Iterations625039525253k max89857.5(0+1)%0.984380.985940.984380.984380.984380.9875 PII C min 6.8455Compliance2813.03969.9483865.62867.542453.974975.50C max6664.7Eigenvalue124988128968125344114480113554127314k min45920.1Iterations575057575857k max109501(0+1)%0.985940.98750.98750.98750.98750.9875 Np±no penalty,PI±penalty I,PII±penaltyII 490the four-node quadrilateral elements result in a numeri-cally induced arti®cially high stiffness in this pattern. Using higher order elements will eliminate this pattern. Figure25shows the topology for minimum compliance using eight-node quadrilateral elements.The checkerboard pattern becomes insigni®cant.Based on the numerical examples given,the proposed approaches of adding penalties to the design variables indeed raise the percentage of design variables having values0or1up to98%.As a result the clearer topologies are seen.Although the boundary conditions and the loading for the two examples are symmetric in the design space,the complete models in stead of quarter models are used because it is afraid that if the arbitrarily speci®ed amount of material is not enough,the symmetric to-pologies could not be formed.Although good results ap-peared in the examples,more extensive tests are still needed to con®rm the robustness of the method. Because the single-objective topologies for the mini-mum compliance and the maximum eigenvalue are so different for the two examples,it is not an easy job to get compromised topologies in multiobjective optimization.It is found that the multiobjective topologies are dominated by the eigenvalue objective in the examples due to nor-malizations of the objectives.Some methods can beused491to overcome this problem.The®rst way is to use adaptive weighting which deliberately balances the two objectives in the multiobjective cost function.The second way is to build an unchangeable compromised base structure in the design space before the multiobjective optimization is performed.The third way is to add a lumped mass at the static loading point to simulate a dynamic inertia when doing the maximum eigenvalue design.Figure26shows the topology for maximum eigenvalue with a lumped mass at the static loading point and the topology is similar to the one for minimum compliance.ConclusionsThe multiobjective topology optimization in two dimen-sional design space has been explored in this paper.If the optimum topologies for individual objectives are very different,the topology obtained for the multiobjective design may be dominated by one of the single-objective topologies.To get a useful or compromised topology for multiobjective design,a proper treatment of adjusting the relative weights in the multiobjective function is highly recommended.Adding penalty to the design variables indeed pro-duces clearer topologies for both single and multiobjec-tive optimizations.However the timing of adding the penalty to the objective function may affect the topology obtained.Penalty II is more cautious than penalty I.It gives ample time to the design variables to change freely. Therefore the topologies generated by penalty II are usually similar to the ones without penalty.To reduce the inteference of penalty term in the process of forming topologies,penalty II is generally recommended unless the percentage of0and1elements never reaches®fty percent.ReferencesBendsùe MP,Kikuchi N(1988)Generating optimal topologies in structural design using a homogenization put. Meth.Appl.Mech.and Eng.71:197±224Dhingra AK,Rao SS,Miura H(1990)Multiobjective decision making in a fuzzy environment with applications to helicopter design.AIAA J.28:703±711Diaz A,Sigmund O(1995)Checkerboard patterns in layout op-timization.Structural Optim.10:40±45Fox RL,Kapoor MD(1968)Rates of change of eigenvalues and eigenvectors.AIAA J.6:2426±2429Grandhi RV,Bharatram F,Venkayya VB(1993)Multiobjective optimization of large-scale structures.AIAA J.31:1329±1337 Kuppuraju N,Mistree F(1986)Compromise:An effective ap-proach for solving multiobjective structural design problems. Comput.Struct.22:857±865Ma ZD,Kikuchi N,Hagizara I(1993)Structural topology and shape optimization for a frequency response put. Mech.13:157±174Mlejnek HP(1992)Some aspects of the genesis of structures. Struct.Optimi.5:64±69Save M,Prager W(1985)Mathematical programming,New York: Plenum pressYang RJ,Chung CH(1994)Optimal topology design using linear put.Struct.52:265±275 492。
多目标优化相关书籍

多目标优化相关书籍多目标优化(Multi-Objective Optimization)是指在优化问题中,同时考虑多个冲突的目标函数,并寻求一组最优解,这些解组成了所谓的“非支配解集”(Pareto-Optimal Set)或“非支配前沿”(Pareto-Optimal Frontier)。
多目标优化在实际问题中的应用非常广泛,例如工程设计、投资组合管理、交通规划等等。
以下是几本与多目标优化相关的书籍,包含了各种多目标优化方法和技术:1. 《多目标决策优化原理与方法》(Principles of Multi-Objective Decision Making and Optimization)- by Hai Wang这本书介绍了多目标决策优化的基本原理和方法,包括多目标决策的概述、非支配排序算法、进化算法等。
书中还通过案例研究和Matlab代码实现来说明方法的应用。
2. 《多目标优化的演化算法导论》(Introduction to Evolutionary Algorithms for Multi-Objective Optimization)- by Carlos A. Coello Coello, Gary B. Lamont, and David A. Van Veldhuizen这本书详细介绍了演化算法在多目标优化中的应用,包括遗传算法、粒子群优化等。
书中提供了大量的案例研究和实验结果,帮助读者理解演化算法的原理和使用。
3. 《多目标优化的进化算法理论与应用》(Evolutionary Algorithms for Multi-Objective Optimization: Methods and Applications)- by Kalyanmoy Deb这本书提供了一些最新的多目标优化的进化算法技术,包括NSGA-II算法、MOEA/D算法等。
书中还介绍了多目标问题建模和评价指标,以及一些应用案例。
浅析多目标优化问题

浅析多目标优化问题作者:张淑艳段鹏松邹卫琴来源:《科技视界》 2013年第14期张淑艳1 段鹏松1 邹卫琴2(1.郑州大学软件技术学院,河南郑州 450000;2.江西理工大学软件学院,江西南昌330000)【摘要】本文介绍了多目标优化问题的问题定义。
通过对多目标优化算法、评估方法和测试用例的研究,分析了多目标优化问题所面临的挑战和困难。
【关键词】多目标优化问题;多目标优化算法;评估方法;测试用例多目标优化问题MOPs (Multiobjective Optimization Problems)是工程实践和科学研究中的主要问题形式之一,广泛存在于优化控制、机械设计、数据挖掘、移动网络规划和逻辑电路设计等问题中。
MOPs有多个目标,且各目标相互冲突。
对于MOPs,通常存在一个折衷的解集(即Pareto最优解集),解集中的各个解在多目标之间进行权衡。
获取具有良好收敛性及分布性的解集是求解MOPs的关键。
1 问题定义最小化MOPs的一般描述如下:2 多目标优化算法目前,大量算法用于求解MOPs。
通常,可以将求解MOPs的算法分为两类。
第一类算法,将MOPs转化为单目标优化问题。
算法为每个目标设置权值,通过加权的方式将多目标转化为单目标。
经过改变权值大小,多次求解MOPs可以得到多个最优解,构成非支配解集[1]。
第二类算法,直接求解MOPs。
这类算法主要依靠进化算法。
进化算法这种面向种群的全局搜索法,对于直接得到非支配解集是非常有效的。
基于进化算法的多目标优化算法被称为多目标进化算法。
根据其特性,多目标进化算法可以划分为两代[2]。
(1)第一代算法:以适应度共享机制为分布性策略,并利用Pareto支配关系设计适应度函数。
代表算法如下。
VEGA将种群划分为若干子种群,每个子种群相对于一个目标进行优化,最终将子种群合并。
MOGA根据解的支配关系,为每个解分配等级,算法按照等级为解设置适应度函数。
NSGA采用非支配排序的思想为每个解分配虚拟适应度值,在进化过程中,算法根据虚拟适应度值采用比例选择法选择下一代。
热处理专业名词英文翻译

1、整体热处理 bulk heat treatment2、表面热处理 surface heat treatment3、化学热处理 thermo-chemical treatment4、预备热处理 conditioning heat treatment5、局部热处理 local heat treatment6、可控气氛热处理 heat treatment in-controlled atmosphere7、真空热处理 vacuum heat treatment008、离子热处理 ion heat treatment9、高能束热处理high energy density heat treatment10、形变热处理 thermomechanical treatment11、复合热处理 complex heat treatment12、流态床热处理 heat treatment in fluidized beds13、吸热式气氛 endothermic atmosphere14、放热式气氛 exothermic atmosphere15、放热-吸热式气氛 exo-endothermic atmosphere16、滴注式气氛 drip feed atmosphere17、氮基气氛nitrogen-base atmosphere18、合成气氛artificial atmosphere019、直生式气氛 direct prepared atmosphere20、淬火冷却介质 quenching media21、淬火冷却烈度 quenching severity22、淬透性 hardenability23、淬硬性 hardening capacity24、端淬试验Jominy test25、奥氏体化austenitizing26、等温转变isothermal transformation27、连续冷却转变 continuous cooling transformation28、退火 annealing29、完全退火full annealing30、不完全退火 incomplete annealing31、去应力退火 stress relieving annealing32、球化退火spheroidizing033、正火 normalizing34、等温正火isothermal normalizing35、淬火 quenching harding36、等温淬火austempering37、分级淬火martempering38、亚温淬火intercritical hardening39、冷处理 subzero treatment40、深冷处理cryogenic treatment41、马氏体临界冷却速度 critical colding rate42、有效淬硬深度 effective hardening depth043、回火tempering44、低温回火 low temperature tempering045、高温回火high temperature tempering46、自回火 self tempering47、回火脆性temper brittlement48、淬冷畸变quenching distortion49、氢脆 hydrogen embrittlement50、残留应力residual stresses51、热应力 thermal stresses52、相变应力transformation stresses53、固溶处理solution treatment54、时效 ageing055、沉淀硬化precipitation hardening56、氧化 oxidation57、脱碳 decarburizing58、内氧化 internal oxidation59、渗碳 carburizing60、固体渗碳pack carburizing61、气体渗碳gas caiburizing62、液体渗碳liquid carburizing63、真空渗碳vacuum carburizing64、离子渗碳plasma carburizing065、复碳 carbon restoration66、碳势 carbon potential67、露点 dew point68、强渗期 carburizing period69、扩散期 diffusion period70、载气 carrier gas71、富化气 enrich gas72、渗氮 nitriding73、液体渗氮liquid nitriding74、气体渗氮gas nitriding75、离子渗氮ion nitriding076、退氮 denitriding77、渗氮化合物层 compound layer78、氨分解率ammonia dissociation rate79、渗金属 metal cementation80、多元共渗multicomponent cementation81、碳氮共渗carbonitriding082、氮碳共渗nitrocarburizing83、流氮共渗sulpho-nitriding84、氧氮共渗oxynitriding85、化学气象沉淀 chemical vapor deposition86、物理气相沉淀 physical vapor deposition87、相phase88、组织 structure89、晶粒 grain90、晶界 grain boundary91、晶粒度grain size92、晶粒度等级 grain size number93、共晶组织 eutectic-structure094、共析组织 eutectoid structure95、层片状组织 lamellar-structure96、弥散相dispersed phase97、亚组织substructure98、位错 dislocation099、结构 texture机械专业名词金属切削 metal cutting机床 machine tool金属工艺学 technology of metals 刀具 cutter摩擦 friction联结 link传动 drive/transmission轴 shaft弹性 elasticity频率特性 frequency characteristic 误差 error响应 response定位 allocation机床夹具 jig动力学 dynamic运动学 kinematic静力学 static分析力学 analyse mechanics拉伸 pulling压缩 hitting剪切 shear扭转 twist弯曲应力 bending stress强度 intensity三相交流电 three-phase AC磁路 magnetic circles变压器 transformer异步电动机 asynchronous motor几何形状 geometrical精度 precision正弦形的 sinusoid交流电路 AC circuit机械加工余量 machining allowance 变形力 deforming force变形 deformation应力 stress硬度 rigidity热处理 heat treatment退火 anneal正火 normalizing脱碳 decarburization渗碳 carburization电路 circuit半导体元件 semiconductor element 反馈 feedback发生器 generator直流电源 DC electrical source门电路 gate circuit逻辑代数 logic algebra外圆磨削 external grinding内圆磨削 internal grinding平面磨削 plane grinding变速箱 gearbox离合器 clutch绞孔 fraising绞刀 reamer螺纹加工 thread processing螺钉 screw铣削 mill铣刀 milling cutter功率 power工件 workpiece齿轮加工 gear mechining齿轮 gear主运动 main movement主运动方向 direction of main movement进给方向 direction of feed进给运动 feed movement合成进给运动 resultant movement of feed合成切削运动 resultant movement of cutting合成切削运动方向 direction of resultant movement of cutting 切削深度 cutting depth前刀面 rake face刀尖 nose of tool前角 rake angle后角 clearance angle龙门刨削 planing主轴 spindle主轴箱 headstock卡盘 chuck加工中心 machining center车刀 lathe tool车床 lathe钻削镗削 bore车削 turning磨床 grinder基准 benchmark钳工 locksmith锻 forge压模 stamping焊 weld拉床 broaching machine拉孔 broaching装配 assembling铸造 found流体动力学 fluid dynamics流体力学 fluid mechanics加工 machining液压 hydraulic pressure切线 tangent机电一体化 mechanotronics mechanical-electrical integration 气压 air pressure pneumatic pressure稳定性 stability介质 medium液压驱动泵 fluid clutch 液压泵 hydraulic pump阀门 valve失效 invalidation强度 intensity载荷 load应力 stress安全系数 safty factor可靠性 reliability螺纹 thread螺旋 helix键 spline销 pin滚动轴承 rolling bearing 滑动轴承 sliding bearing 弹簧 spring制动器 arrester brake十字结联轴节 crosshead 联轴歧 coupling链 chain皮带 strap精加工 finish machining粗加工 rough machining变速箱体 gearbox casing腐蚀 rust氧化 oxidation磨损 wear耐用度 durability随机信号 random signal离散信号 discrete signal超声传感器 ultrasonic sensor 集成电路 integrate circuit 挡板 orifice plate残余应力 residual stress套筒 sleeve扭力 torsion冷加工 cold machining电动机 electromotor汽缸 cylinder过盈配合 interference fit热加工 hotwork摄像头 CCD camera倒角 rounding chamfer优化设计 optimal design工业造型设计 industrial moulding design有限元 finite element滚齿 hobbing插齿 gear shaping伺服电机 actuating motor铣床 milling machine钻床 drill machine镗床 boring machine步进电机 stepper motor丝杠 screw rod导轨 lead rail组件 subassembly可编程序逻辑控制器 Programmable Logic Controller PLC 电火花加工 electric spark machining电火花线切割加工 electrical discharge wire - cutting 相图 phase diagram热处理 heat treatment固态相变 solid state phase changes有色金属 nonferrous metal合成纤维 synthetic fibre电化学腐蚀 electrochemical corrosion 车架 automotive chassis悬架 suspension转向器 redirector变速器 speed changer板料冲压 sheet metal parts孔加工 spot facing machining车间 workshop工程技术人员 engineer气动夹紧 pneuma lock数学模型 mathematical model画法几何 descriptive geometry机械制图 Mechanical drawing投影 projection视图 view剖视图 profile chart标准件 standard component零件图 part drawing装配图 assembly drawing尺寸标注 size marking技术要求 technical requirements刚度 rigidity内力 internal force位移 displacement截面 section疲劳极限 fatigue limit断裂 fracture塑性变形 plastic distortion脆性材料 brittleness material刚度准则 rigidity criterion垫圈 washer垫片 spacer直齿圆柱齿轮 straight toothed spur gear 斜齿圆柱齿轮 helical-spur gear直齿锥齿轮 straight bevel gear运动简图 kinematic sketch齿轮齿条 pinion and rack蜗杆蜗轮 worm and worm gear虚约束 passive constraint曲柄 crank摇杆 racker凸轮 cams共轭曲线 conjugate curve范成法 generation method定义域 definitional domain值域 range导数\微分 differential coefficient求导 derivation定积分 definite integral不定积菲 indefinite integral曲率 curvature偏微分 partial differential毛坯 rough游标卡尺 slide caliper千分尺 micrometer calipers攻丝 tap二阶行列式 second order determinant 逆矩阵 inverse matrix线性方程组 linear equations概率 probability随机变量 random variable排列组合 permutation and combination 气体状态方程 equation of state of gas 动能 kinetic energy势能 potential energy机械能守恒 conservation of mechanical energy 动量 momentum桁架 truss轴线 axes余子式 cofactor逻辑电路 logic circuit触发器 flip-flop脉冲波形 pulse shape数模 digital analogy液压传动机构 fluid drive mechanism机械零件 mechanical parts淬火冷却 quench淬火 hardening回火 tempering调质 hardening and tempering磨粒 abrasive grain结合剂 bonding agent砂轮 grinding wheel。
几种多目标进化算法简介
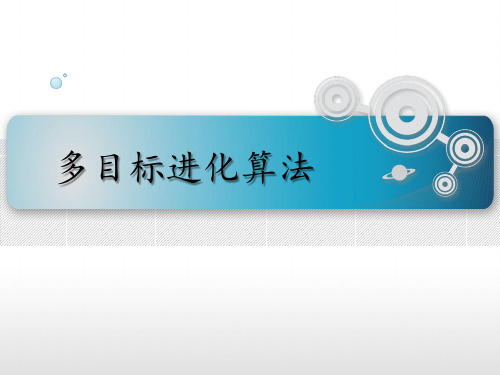
绪 论 – 问题描述
假设有 r 个优化目标,则目标函数表示为:
f ( X ) ( f1 ( X ), f 2 ( X ),
约束条件:ຫໍສະໝຸດ , f r ( X ))gi ( X ) 0 i 1, 2, hi ( X ) 0 i 1, 2,
* * 任务:寻求目标集合 X * ( x1 , x2 , 足约束条件的同时获得最优解
小生境技术的基本思想是将生物学中的小生境概念应 用于进化计算中,将进化计算中的每一代个体划分为若 干类,每个类中选出若干适应度较大的个体作为一个类 的优秀代表组成一个群,再在种群中,以及不同种群之 间,杂交、变异产生新一代的个体种群。
小生境(niche)
小生境计数(Niche Count) 用来估计个体 i 所有邻居(小生境内)的拥挤程度
帕累托(Pareto)最优解
多目标优化的解称为 Pareto 最优解(1896年,Vilfredo Pareto) 给定一个多目标优化问题 f ( X ) , 最优解定义为:
f ( X * ) opt f ( X )
X
其中, f :
{X
Vilfredo Pareto 意大利 经济学家
NPGA-共享机制
NPGA-Selection
NPGA – 总结评价
1. 选择一定数目的个体之后 2. 利用交叉变异等方法产生一个新的种群 3. 并循环,直至达到一定条件结束 优点:能够快速找到一些好的非支配最优解域 能够维持一个较长的种群更新期 缺点:需要设臵共享参数,比较困难 需要选择一个适当的锦标赛机制
09_AIAA_ga

2 MULTI-LINK SUSPENSION SYSTEM AND ITS DESIGN PROBLEM
As aforementioned, the reason why multi-link suspension systems are introduced mainly for high-grade cars is the high degree of design freedom for various function items. The essential difference between design problems for simple systems and ones for complicated systems is that in the former cases the mapping from design items to function items is relatively independent and it is possible to separately determine respective items, and that in the latter cases the interactions between all items are complicated as well as their structure and configuration and the tradeoff among function items is not straightforward. This tendency seems to have become more obvious under the up-to-date technologies that try to condense more functions into a certain size of a system. The above context can be found in the design problem of multi-link suspension systems used in automobiles. The fundamental functions of an automobile are to run straight, to turn and stop, and to run on both good and bad roads. That is, they consist of various operation modes. While there are a variety of suspension types (Dixon, 1996), their performance depends on both the selection of their types and the adjustment of their component link sizes. When focusing on a specific operation mode, the suspension geometry of simple types can be relatively easily determined to be ideal, since the relationship between link sizes and the specific function is straightforward. However, it is necessary to introduce complicated suspension types for realizing totally superior performance against all operation modes (Ushio et al., 1991), and the corresponding design problem of suspension geometry is not so easy due to the aforementioned nature of complicated systems design. Under these points, the multi-link suspension system that this paper is going to discuss is principally a parallel six-bar universal linkage. It is generally impossible to understand the immediate relationships between link sizes and respective function items. So, the conventional design situation requires many times of try-and-errors for finding a superior design solution. If the design problem can be mathematically formulated and the optimization algorithm suitable for its characteristics is organized, such a design method can be effective.