数控机床夹具工件编程零点的确定
五轴加工中心数控编程技巧分析
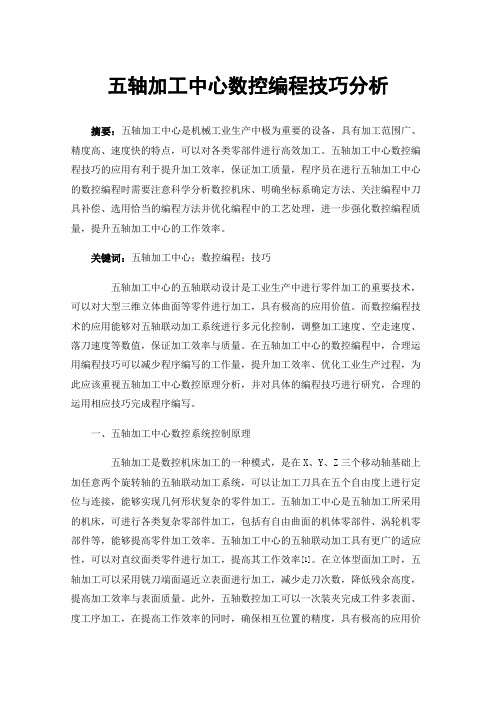
五轴加工中心数控编程技巧分析摘要:五轴加工中心是机械工业生产中极为重要的设备,具有加工范围广、精度高、速度快的特点,可以对各类零部件进行高效加工。
五轴加工中心数控编程技巧的应用有利于提升加工效率,保证加工质量,程序员在进行五轴加工中心的数控编程时需要注意科学分析数控机床、明确坐标系确定方法、关注编程中刀具补偿、选用恰当的编程方法并优化编程中的工艺处理,进一步强化数控编程质量,提升五轴加工中心的工作效率。
关键词:五轴加工中心;数控编程;技巧五轴加工中心的五轴联动设计是工业生产中进行零件加工的重要技术,可以对大型三维立体曲面等零件进行加工,具有极高的应用价值。
而数控编程技术的应用能够对五轴联动加工系统进行多元化控制,调整加工速度、空走速度、落刀速度等数值,保证加工效率与质量。
在五轴加工中心的数控编程中,合理运用编程技巧可以减少程序编写的工作量,提升加工效率、优化工业生产过程,为此应该重视五轴加工中心数控原理分析,并对具体的编程技巧进行研究,合理的运用相应技巧完成程序编写。
一、五轴加工中心数控系统控制原理五轴加工是数控机床加工的一种模式,是在X、Y、Z三个移动轴基础上加任意两个旋转轴的五轴联动加工系统,可以让加工刀具在五个自由度上进行定位与连接,能够实现几何形状复杂的零件加工。
五轴加工中心是五轴加工所采用的机床,可进行各类复杂零部件加工,包括有自由曲面的机体零部件、涡轮机零部件等,能够提高零件加工效率。
五轴加工中心的五轴联动加工具有更广的适应性,可以对直纹面类零件进行加工,提高其工作效率[1]。
在立体型面加工时,五轴加工可以采用铣刀端面逼近立表面进行加工,减少走刀次数,降低残余高度,提高加工效率与表面质量。
此外,五轴数控加工可以一次装夹完成工件多表面、度工序加工,在提高工作效率的同时,确保相互位置的精度,具有极高的应用价值。
五轴加工中心数控系统是运用编程软件完成编程,进而实现数字化控制的过程,通常需要由编程人员与机床操作人员密切配合,保证其程序编写的科学性与准确性。
数控铣床理论题集

数控铳床理论题集一、判断题(是画J,非画x)1.数控机床是为了发展柔性制造系统而研制的。
(X)2.数控技术是一种自动控制技术。
(«)3.数控机床的柔性表现在它的自动化程度很高。
(X)4.数控机床是一种程序控制机床。
(«)5.能进行轮廓控制的数控机床,一般也能进行点位控制和直线控制。
(«)6.加工平面任意直线应采用点位控制数控机床。
(X)7.加工沿着与坐标轴成45o的斜线可采用点位直线控制数控机床。
(«)8.多坐标联动就是将多个坐标轴联系起来,进行运动。
(X)9.联动是数控机床各坐标轴之间的运动联系。
(X)10.四轴控制的数控机床可用来加工圆柱凸轮。
(«)11.加工中心是一种多工序集中的数控机床。
(«)12.加工中心是最早发展的数控机床品种。
(X)13.加工中心是世界上产量最高、应用最广泛的数控机床之一。
(«)14.数控机床以G代码作为数控语言。
(X)15.数控机床上的F、S、T就是切削三要素。
(X)16. G40是数控编程中的刀具左补偿指令。
(X)17.判断刀具左右偏移指令时,必须对着刀具前进方向判断。
(«)18.数控铳床的工作台尺寸越大,其主轴电机功率和进给轴力矩越大。
(«)19. G03X-Y-I-J-K-F-表示在XY平面上顺时针插补。
(X)20.同组模态G代码可以放在一个程序段中,而且与顺序无关。
(X)1、可控轴在三坐标以上的数铳则可进行立体轮廓加工(V )2、对某一数控铳,其G代码和M代码是可以互相转换的(X )3、软驱既可作为数铳的输入设备,也可作为数铳的输出设备(X )4、在CNC机床中,PLC主要用于开关量控制(X )5、CNC闭环系统的特点之一就是调试容易(X )6、数控机床的重复定位精度取决于系统的开关量控制方式(V )7、数控铳床的加工速度由CPU的时钟速度决定(X )8、数控铳床的G00与G01在程序中均可互换(X )9、滚珠丝杆的主要优点是传动效率高(X )10、步进电机不能用于开环控制系统(X )11、加工过程中,不能查阅在CNC中的刀具偏移(X )12、数控系统只能采用DOS操作系统(X )13、数铳急停后应用手动返回参考点(V )14、铰孔可以纠正孔位置精度(X )15、扩孔可以部分地纠正钻孔留下的孔轴线歪斜(V )16、具有成形面的零件,一般在卧式铳床上或在仿型铳床上加工(X )17、铳床夹具常采用定位键来确定夹具与机床之间的相对位置(V )18、相邻两工序的工序尺寸之差叫做工序余量(V )19、对于精度要求较高的工件,在精加工时以采用一次安装为最好(V )20、应该选用前角较小的铳刀来加工硬度低塑性好的材料(X ) 1、数控铳床适合于普通零件的大批量生产(X )2、主程序与子程序的程序段可以互相调用(X )3、每条程序段表示一种操作(V )4、脉冲当量标志着,数控机床位移精度的分辨率(V )5、滚珠丝杠不能自锁(V )6、我国数控机床研制于1958年,由清华大学研制出了最做早样机(V )7、由于光栅易受污染,所以不能用于数控铳床上(X )8、在数铳CRT上,综合显示可以同时显示相对坐标、工件坐标、机床坐标和剩余移动量(V )9、在先进的数控系统中,显示介面可以用WINDOWSNT ( V )10、数控铳床的伺服系统相当于手工操作时人的手(V )11、一般数控铳床的坐标在三维以上,并具有铳刀半径自动补偿功能(V )12、在切削过程中不可以调整数控铳床主轴的转速(X )13、闭环控制的数控铳床比开环控制的数控机床增加了数字转换装置(X )14、孔的圆柱度属于孔的位置精度(X )15、铰孔退刀时,不允许铰刀倒转(V )16、在铳床上可以用键槽圆柱铳刀或立铳刀铳孔(X )17、为了改善低碳钢的切削加工性,在切削前应进行正火处理(V )18、在一个定位基准上同时有两个表面定位称为重复定位(X )19、塑料夹具适于薄壁工件的夹紧(V )20、淬火工序一般安排在精加工之后进行(X )(X ) 1、X6132型卧式万能铳床纵向工作台是在工作台底座的燕尾槽内作直线运动的,燕尾导轨的间隙是由螺母进行调整的。
数控机床原点、参考点、工件零点的区别和联系

数控机床原点、参考点、工件零点的区别和联系
吕宝垒
【期刊名称】《橡塑技术与装备》
【年(卷),期】2024(50)5
【摘要】机床原点和参考点是定义数控机床运动的两个重要的概念,二者既有区别又有联系。
机床原点也就是机床坐标系的零点是数控机床进行位置测量、控制、显示的统一基准。
本文从新的视角定义了数控机床参考点的概念,概述了参考点在数控机床中的作用以及在什么条件下需要重新设定参考点。
结合实际工作中设定数控机床X、Y、Z轴参考点的操作方法,通过总结其内在原理进一步阐明了参考点的特性。
通过设定或建立参考点之后机床的原点才有实际意义,而机床的原点是在机床设计之初就确定的,只有有了机床的原点才能设定参考点的位置,这就是二者之间的区别和联系。
工件零点是工件坐标系的原点,它是在机床坐标系的基础上为方便数控编程而根据工件的特点设定的。
【总页数】5页(P27-31)
【作者】吕宝垒
【作者单位】格劳博机床(中国)有限公司
【正文语种】中文
【中图分类】TQ320.52
【相关文献】
1.找正同轴度法在设定数控机床参考点(或原点)时的应用
2.数控机床工件零点偏置浅析
3.利用数控机床工作台的回转中心设置工件零点的技巧
4.利用数控机床工作台的回转中心设置工件零点的技巧
5.数控机床回转中心巧应用——利用回转中心设置工件零点
因版权原因,仅展示原文概要,查看原文内容请购买。
CNC机床坐标系的确定及工件坐标系
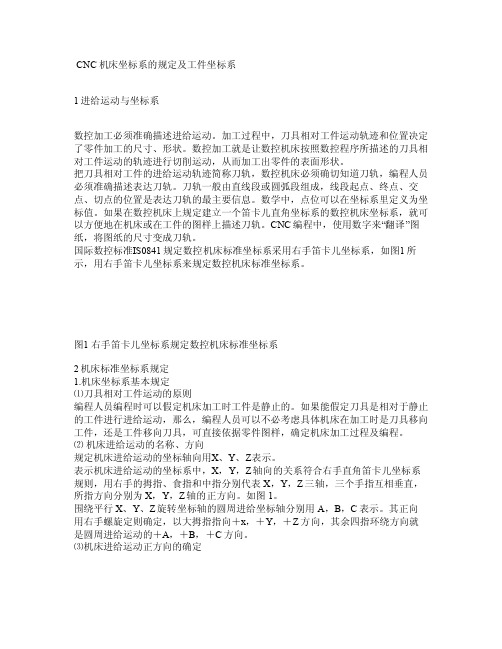
CNC机床坐标系的规定及工件坐标系1进给运动与坐标系数控加工必须准确描述进给运动。
加工过程中,刀具相对工件运动轨迹和位置决定了零件加工的尺寸、形状。
数控加工就是让数控机床按照数控程序所描述的刀具相对工件运动的轨迹进行切削运动,从而加工出零件的表面形状。
把刀具相对工件的进给运动轨迹简称刀轨,数控机床必须确切知道刀轨,编程人员必须准确描述表达刀轨。
刀轨一般由直线段或圆弧段组成,线段起点、终点、交点、切点的位置是表达刀轨的最主要信息。
数学中,点位可以在坐标系里定义为坐标值。
如果在数控机床上规定建立一个笛卡儿直角坐标系的数控机床坐标系,就可以方便地在机床或在工件的图样上描述刀轨。
CNC编程中,使用数字来“翻译”图纸,将图纸的尺寸变成刀轨。
国际数控标准I S0841规定数控机床标准坐标系采用右手笛卡儿坐标系,如图1所示,用右手笛卡儿坐标系来规定数控机床标准坐标系。
图1右手笛卡儿坐标系规定数控机床标准坐标系2机床标准坐标系规定1.机床坐标系基本规定⑴刀具相对工件运动的原则编程人员编程时可以假定机床加工时工件是静止的。
如果能假定刀具是相对于静止的工件进行进给运动,那么,编程人员可以不必考虑具体机床在加工时是刀具移向工件,还是工件移向刀具,可直接依据零件图样,确定机床加工过程及编程。
⑵机床进给运动的名称、方向规定机床进给运动的坐标轴向用X、Y、Z表示。
表示机床进给运动的坐标系中,X,Y,Z轴向的关系符合右手直角笛卡儿坐标系规则,用右手的拇指、食指和中指分别代表X,Y,Z三轴,三个手指互相垂直,所指方向分别为X,Y,Z轴的正方向。
如图1。
围绕平行X、Y、Z旋转坐标轴的圆周进给坐标轴分别用A,B,C表示。
数控机床坐标系和原点概述

工件坐标系的原点即编程零点与零件定位基准

工件坐标系的原点即编程零点与零件定位基准随着现代工业的发展,数控加工技术已经成为了制造业中不可或缺的一部分。
在数控加工中,工件坐标系的原点即编程零点与零件定位基准是一个非常重要的概念。
本文将从以下几个方面对工件坐标系的原点和零件定位基准进行详细的介绍。
一、工件坐标系的原点工件坐标系是指数控机床用来描述零件加工位置和加工轨迹的坐标系。
在数控加工中,工件坐标系的原点是指刀具在加工零件时所处的位置。
在进行数控编程时,需要定义工件坐标系的原点,这个原点通常被称为编程零点。
编程零点的定义对于数控加工来说非常重要,因为它是数控机床进行加工的起点。
在进行数控编程时,需要将零件的设计图纸转化为数控程序,因此必须定义一个原点,以便在程序中进行计算和控制。
此外,在数控加工中,还需要定义一个工件坐标系的坐标轴,以便对零件进行加工。
工件坐标系的原点通常是通过测量零件的尺寸和位置来确定的。
在进行数控加工之前,需要先确定零件的加工位置和加工方向,以便确定编程零点。
在确定编程零点时,需要考虑到零件的尺寸和形状,以及加工工艺和机床的限制条件等因素。
二、零件定位基准零件定位基准是指零件在数控机床上加工时所采用的参考基准。
在进行数控加工时,需要将零件固定在数控机床的工作台上,以便进行加工。
因此,需要在零件和工作台之间建立一个定位基准,以确保零件在加工过程中的位置和方向是正确的。
零件定位基准通常是通过零件的设计图纸来确定的。
在设计零件时,需要考虑到零件的尺寸和形状,以及加工工艺和机床的限制条件等因素,以便确定零件的定位基准。
在进行数控编程时,需要将零件的定位基准转化为数控程序,以便在程序中进行计算和控制。
在进行数控加工时,还需要考虑到零件的加工精度和加工质量等因素。
在确定零件的定位基准时,需要选择一个合适的基准面和基准点,以确保零件在加工过程中的位置和方向是精确和稳定的。
三、工件坐标系的原点与零件定位基准的关系工件坐标系的原点是数控机床进行加工的起点,而零件定位基准是零件在数控机床上加工时所采用的参考基准。
数控机床的坐标系统
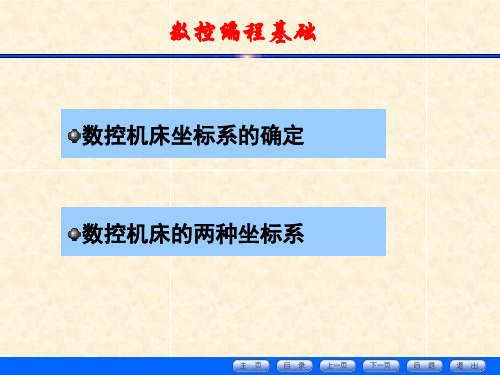
3、编程坐标系(工件坐标系)
又称工件坐标系,是编程时用来定义工 件形状和刀具相对工件运动的坐标系。 工件装夹到机床上时,应使工件坐标系 与机床坐标系的坐标轴方向保持一致。
14
3、工件原点
工件原点(编程原点):由编程人员在工件上根据编程 方便性自行设定的编制加工程序的原点。
15
设置工件原点的一般原则
工件原点与设计基准或装配基准重合,以利于编程。
工件原点尽量选在尺寸精度高、表面粗糙度小的表 面上。
工件原点最好选在工件的对称中心上。
要便于测量和检验。
16
4
坐标轴方向的确定
(1)Z坐标
Z坐标的运动方向是由传递切削动力的主轴所 决定的,即平行于主轴轴线的坐标轴即为Z坐标,Z 坐标的正向为刀具离开工件的方向。
注意:1、当机床有几个 主轴时,选一个与工件装 夹面垂直的主轴为Z坐标。 2、当机床无主轴时,选 与工件装夹面垂直的方向 为Z坐标。(牛头刨床)
思考:立式铣床中钻头钻孔 时为Z轴的哪个方向?卧式 车床Z轴正方向如何确定?
③ 对于没有回转轴或没有回转工件的机床,X轴平行于主要切削方 向,且以该方向为正方向。(牛头刨床)
8
坐标轴方向的确定
(3)Y坐标
在确定X、Z坐标的正方向后,可以用根据X和Z坐标的方向,按照右 手直角坐标系来确定Y坐标的方向。
9
数控机床的两种坐标系
机床坐标系 机床原点
机床零点
编程坐标系 编程原点
10
1、机床原点
机床原点(机械原点):是指机床坐标系的原点,是机床 上的一个固定点.它不仅是在机床上建立工件坐标系的基准 点,而且还是机床调试和加工时的基准点.随着数控机床种类 型号的不同其机床原点也不同,通常车床的机床原点设在卡 盘端面与主轴中心线交点处,而铣床的机床原点则设在机床X、 Y、Z三根轴正方向的运动极限位置.
数控编程坐标系知识

四 机床坐标系与工件坐标系
(1)机床原点
现代数控机床都有一个基准位置,称为机床原点,是机床制造商设置在机床上的 一个物理位置,其作用是使机床与控制系统同步,建立测量机床运动坐标的起始点。
机床坐标系原点是指在机床上设置的一个固定点,即机床原点。它在机床装配、调 试时就已确定下来,是数控机床进行加工运动的基准参考点。一般取在机床运动方向的 最远点。
六 工件的运动
对于移动部分是工件而不是刀具的机床,用带“′”的字母表示工件的正 向运动,如+X′、+Y′、+Z′分别表示工件相对于刀具正向运动的指令,它们 与+X、+Y、+Z表示的运动方向恰好相反。
小结:
机床坐标系是机床上固有的坐标系,是用来确定工件坐标系的基本坐标系, 是确定刀具(刀架)或工件(工作台)位置的参考系。
确定数控机床坐标系时总是假设工件固定,刀具相对工件运动。标准坐 标系采用右手直角笛卡儿定则判断,直线坐标轴X、Y、Z的判定顺序是:先Z 轴,再X轴,最后按右手定则判定Y轴。
机床坐标系原点是指在机床上设置的一个固定点,是数控机床进行加 工运动的基准参考点;机床参考点对机床原点的坐标是已知值,既可根据 机床参考点在机床坐标系中的坐标值间接确定机床原点的位置;编程人员 在编程时设定的坐标系称工件坐标系,工件坐标系坐标轴的确定与机床坐 标系坐标轴方向一致。
尽量选在尺寸精度高,粗糙度低的 工件表面
工件坐标 系原点
最好在工件的对称中心上
要便于测量和检测
机床坐标系与工件坐标系的关系
工件坐标系 原点
机床坐标系 原点
五 附加坐标系
对于直线运动,通常建立的 附加坐标系有:
指定平行于X、Y、Z的坐标轴 可以采用的附加坐标系:第二组U、 V、W坐标,第三组P、Q、R坐标。
- 1、下载文档前请自行甄别文档内容的完整性,平台不提供额外的编辑、内容补充、找答案等附加服务。
- 2、"仅部分预览"的文档,不可在线预览部分如存在完整性等问题,可反馈申请退款(可完整预览的文档不适用该条件!)。
- 3、如文档侵犯您的权益,请联系客服反馈,我们会尽快为您处理(人工客服工作时间:9:00-18:30)。
7. 2 相关知识
• 对机床夹具新的要求。 • (1)能迅速方便地适应新产品的投产,以缩短生产准备
周期,降低生产成本。 • (2)能装夹一组具有相似性特征的工件。 • (3)适用于精密加工的高精度机床夹具。 • (4)适用于各种现代化制造技术的新型机床夹具。 • 因此现代机床夹具的发展方向主要表现为精密化、高效化、
柔性化、标准化4个方面。
下一页 返回
7. 2 相关知识
• 1)精密化
• 随着促进了高精度机床夹球头顶尖加工轴,圆跳动 可小于φ1μm;高精度端齿分度盘的分度精度可达±0.1″;孔系 组合夹具基础板上孔距误差可达几个微米。
不同尺寸,具有完全互换性、高耐磨性、高精度的标准元 件及组合件,按照不同工件的工艺要求,组装成加工所需 要的夹具。
上一页 下一页 返回
7. 2 相关知识
• 专用夹具以设计→制造→使用→报废的单向过程 • 组合夹具为组装→使用→拆散→再组装→使用→再拆散的
循环过程。 • 经生产实践表明,与一次性使用的专用夹具相比,由于它
长时间内,夹具的柔性化将是夹具发展的主要方向。
上一页 下一页 返回
7. 2 相关知识
• 4)标准化 • 夹具的标准化: • 一是零、部件的标准化,以便在各类夹具上通用; • 二是各种夹具结构形式的标准化。 • 专用夹具的标准化、系列化和通用化工作是进一步将夹具
的零部件、组件做成独立的单元,以便简化夹具的设计和 制造工作,并便于组织专业化工厂生产。 • 将夹具的单件生产转变为专业化的批量生产,可大大缩短 产品的生产周期和降低成本,使之适应现代制造业的需要,
是以组装代替设计和制造,具有下列特点: • (1)灵活多变,为零件的加工迅速提供夹具,使生产准
备周期大为缩短。 • 通常一套中等复杂程度的专用夹具,从设计到制造需几个
月,而组装一套同等复杂程度的组合夹具只需几个小时。
上一页 下一页 返回
7. 2 相关知识
• (2)节约大量设计、制造工时及金属材料消耗。 • (3)减少夹具库存面积,改善管理工作。 • (4)组合夹具的不足之处: • 与专用夹具相比,一般显得体积较大、重量较重、刚性也
稍差些。此外,为了适应组装各种不同性质和结构类型的 夹具,须有大量元件的储备。 • 由以上特点可知,组合夹具适合于品种多、数量少、 加工对象经常变换的情况,因此在模具制造中得到广泛应 用。
• 组合夹具的元件精度高、耐磨,并且实现了完全互换,元 件精度一般为IT6~IT7。用组合夹具加工的工件, 一般能稳定在IT8~IT7级精度,经过精确调整可达 IT7级精度。
• 2)高效化
• 高效化夹具主要用来减少工件加工的基本时间和辅助时间,以提高劳 动生产率,减轻工人的劳动强度。常见的高效化夹具有:自动化夹具、 高速化夹具、具有夹紧动力装置的夹具等。
• 为实现机械加工过程的自动化,在生产流水线、自动线上配置随行夹 具;在数控机床、加工中心等柔性制造系统中也需配置高效自动化夹 具,这类夹具常装有自动上、下料机构及独立的自动夹紧单元,大大 提高了工件装夹效率。
也有利于实现机床夹具的计算机辅助设计。
上一页 下一页 返回
7. 2 相关知识
• 7.2.1 组合夹具
• 组合夹具是一种标准化、系列化、通用化程度很高的工艺 装备,目前已形成了一套完整的组合夹具体系,它对保证 产品质量,提高劳动生产率,降低成本,缩短生产周期等 都起着重要的作用。
• 一、组合夹具的工作原理及特点 • 组合夹具是由一套预先制好的各种不同形状、不同规格、
7. 1 任务引入
• 现代生产要求企业所制造的产品品种经常更新换代,以适应市场激烈 的竞争。特别是近年来,数控机床(NC)、柔性制造系统(FM S)、成组技术(GT)、加工中心(MC)等新技术的应用,对机 床夹具提出了新的要求。
• 例如,现在有图7-1所示这组工艺相似的轴,可以用科学的方法把 它们从诸多零件中找出来,然后用一副夹具完成这一组零件的加工。
上一页 下一页 返回
图7.2 盘类零件钻径向分度孔组合夹具
1—基础件; 2—支承板; 3—定位件; 4—导向件; 5—夹紧件; 6—紧固件; 7—其他件; 8—合件
返回
7. 2 相关知识
• 孔系组合夹具主要元件表面为圆柱孔和螺纹孔组成的 坐标孔系,通过定位销和螺栓来实现元件之间的组装和紧 固。孔系组合夹具具有元件刚性好、定位精度和可靠性高、 工艺性好等特点,适用于数控机床。因而自20世纪60 年代以来,随NC、MC的发展,孔系组合夹具得到较快 发展。
上一页 下一页 返回
7. 2 相关知识
• 二、组合夹具系统、系列及元件
• 1.组合夹具系统 • 组合夹具按组装对元件间连接基面的形状,可分为槽系和
孔系两大系统。 • 槽系组合夹具以槽和键相配合的方式来实现元件间的定位。
因元件的位置可沿槽的纵向任意调节,故组装十分灵活, 适用范围广,是最早发展起来的组合夹具系统。
上一页 下一页 返回
7. 2 相关知识
• 3)柔性化 • 机床夹具的柔性化与机床的柔性化相似,它是指机床夹具
通过调整、组合等方式,以适应工艺可变因素的能力。 • 工艺的可变因素主要有: • 生产批量、工序特征、工件的形状和尺寸等。 • 具有柔性化特征的新型夹具种类主要有: • 组合夹具、通用可调夹具、成组夹具、数控夹具等。在较
• 2.组合夹具系列 • 为了适应不同产品加工零件尺寸大小的需要,组合夹具按
其尺寸大小又分为大、中、小型3个系列。槽系各系列主 要参数及适用范围如表7-1所示。
上一页 下一页 返回
表7-1 槽系组合夹具系列及适用范
返回
7. 2 相关知识
• 3.组合夹具元件组成
• 组合夹具的元件,按使用性能分为8大类 • (1)基础件。它是组合夹具中最大的元件,包括各种规
格尺寸的方形、矩形、圆形基础板和基础角铁等。如图7 -2所示的基础件1为矩形基础板做的夹具体。 • (2)支承件。支承件是组合夹具的骨架元件。支承件通 常在组合夹具中起承上启下的作用,即把上面的其他元件 通过支承件与其下面的基础件连成一体,一般各种夹具结 构中都少不了它。