生产线效率提升持续改善收益计算
效率计算
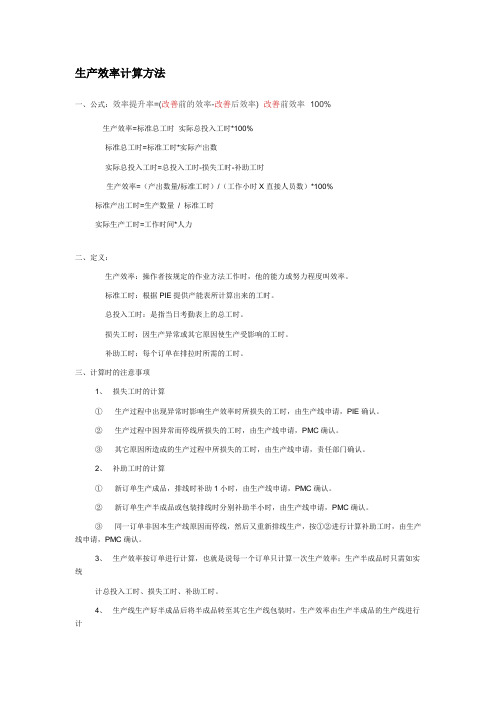
生产效率计算方法一、公式:效率提升率=(改善前的效率-改善后效率)÷改善前效率×100%生产效率=标准总工时÷实际总投入工时*100%标准总工时=标准工时*实际产出数实际总投入工时=总投入工时-损失工时-补助工时生产效率=(产出数量/标准工时)/(工作小时X直接人员数)*100%标准产出工时=生产数量/ 标准工时实际生产工时=工作时间*人力二、定义:生产效率:操作者按规定的作业方法工作时,他的能力或努力程度叫效率。
标准工时:根据PIE提供产能表所计算出来的工时。
总投入工时:是指当日考勤表上的总工时。
损失工时:因生产异常或其它原因使生产受影响的工时。
补助工时:每个订单在排拉时所需的工时。
三、计算时的注意事项1、损失工时的计算①生产过程中出现异常时影响生产效率时所损失的工时,由生产线申请,PIE确认。
②生产过程中因异常而停线所损失的工时,由生产线申请,PMC确认。
③其它原因所造成的生产过程中所损失的工时,由生产线申请,责任部门确认。
2、补助工时的计算①新订单生产成品,排线时补助1小时,由生产线申请,PMC确认。
②新订单生产半成品或包装排线时分别补助半小时,由生产线申请,PMC确认。
③同一订单非因本生产线原因而停线,然后又重新排线生产,按①②进行计算补助工时,由生产线申请,PMC确认。
3、生产效率按订单进行计算,也就是说每一个订单只计算一次生产效率;生产半成品时只需如实统计总投入工时、损失工时、补助工时。
4、生产线生产好半成品后将半成品转至其它生产线包装时,生产效率由生产半成品的生产线进行计算,负责包装的生产线提供包装时所用的总投入工时、损失工时、补助工时。
5、生产好的成品因本生产线作业不良而造成重工的,重工时所用到的工时将计算到生产该成品的实际投入总工时内进行计算生产效率,由生产该成品的线别承担工时。
6、计算损失工时和补助工时时由生产线填写<组装课损失/补助工时申请书>,按计算时注意事项的第1、2项规定进行计算与确认。
生产线效率分析与生产计划改进

生产线效率分析与生产计划改进随着工业发展的加速,现代企业对于生产线效率的追求变得日益重要。
高效的生产线不仅能够提高企业的盈利能力,还可以提升产品质量和客户满意度。
本文将针对生产线效率进行详细分析,并提出相关的生产计划改进措施。
一、生产线效率分析1. 效率计算方法生产线效率通常使用OEE(Overall Equipment Efficiency)指标进行量化测算。
OEE综合了设备利用率、生产质量和生产能力等因素,可以全面评估生产线的运行状况。
OEE的计算公式为:OEE = 设备利用率 ×制造效率 ×生产质量。
2. 设备利用率设备利用率是衡量生产线利用设备的程度,常用公式为:设备利用率 = 实际运行时间 / 理论运行时间。
通过提高设备利用率,可以减少生产线的停机时间和故障率,进而提高生产效率。
3. 制造效率制造效率表示在生产过程中,实际生产数量与理论生产数量之间的比率。
制造效率可以通过以下公式来计算:制造效率 = 实际生产数量 / 理论生产数量。
通过改进生产工艺和流程,降低废品率以及减少生产线中的不必要等待时间,可以提高制造效率。
4. 生产质量生产质量是衡量生产线面向市场交付的产品质量的指标。
生产质量可以通过以下公式计算:生产质量 = 合格产品数量 / 总生产数量。
通过加强质量控制、提高生产员工的技能水平,可以提高生产质量,减少不良产品的产生。
二、生产计划改进措施1. 资源优化分配合理的资源分配是提高生产线效率的关键。
通过对生产任务进行全面分析和评估,合理安排人力、设备和原材料,可以确保生产线运行平稳,避免资源的浪费和过度使用。
2. 智能化技术应用现代技术的应用可以大大提升生产线效率。
例如,通过设备自动化和物联网技术的应用,可以实现设备的智能监控和远程控制,减少人工的干预,提高生产线的自动化程度和生产效率。
3. 优化物料管理物料管理对于生产线的运作至关重要。
通过建立合理的物料供应链和采用合适的物料管理方法,如先进的ERP系统,可以降低物料的缺失率和库存成本,提高生产线的运行效率。
改善后产能提升20%,收益一般怎么算合适?【精益通】
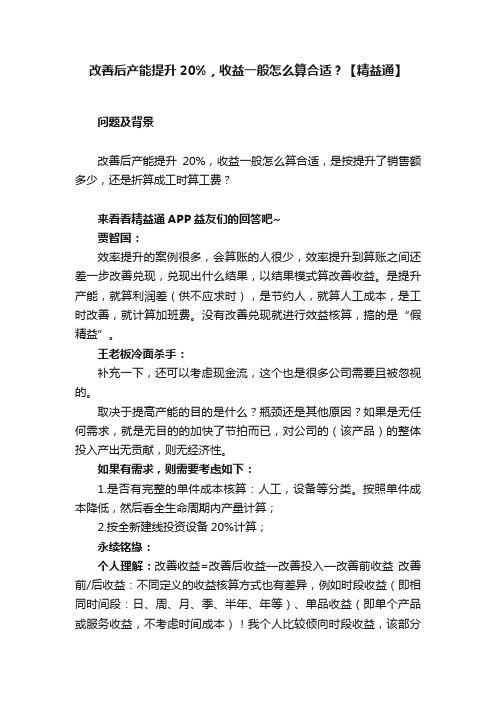
改善后产能提升20%,收益一般怎么算合适?【精益通】问题及背景改善后产能提升20%,收益一般怎么算合适,是按提升了销售额多少,还是折算成工时算工费?来看看精益通APP益友们的回答吧~贾智国:效率提升的案例很多,会算账的人很少,效率提升到算账之间还差一步改善兑现,兑现出什么结果,以结果模式算改善收益。
是提升产能,就算利润差(供不应求时),是节约人,就算人工成本,是工时改善,就计算加班费。
没有改善兑现就进行效益核算,搞的是“假精益”。
王老板冷面杀手:补充一下,还可以考虑现金流,这个也是很多公司需要且被忽视的。
取决于提高产能的目的是什么?瓶颈还是其他原因?如果是无任何需求,就是无目的的加快了节拍而已,对公司的(该产品)的整体投入产出无贡献,则无经济性。
如果有需求,则需要考虑如下:1.是否有完整的单件成本核算:人工,设备等分类。
按照单件成本降低,然后看全生命周期内产量计算;2.按全新建线投资设备20%计算;永续铭缘:个人理解:改善收益=改善后收益—改善投入—改善前收益改善前/后收益:不同定义的收益核算方式也有差异,例如时段收益(即相同时间段:日、周、月、季、半年、年等)、单品收益(即单个产品或服务收益,不考虑时间成本)!我个人比较倾向时段收益,该部分核算为:收益=销售收入—投入(管理+原材料+人工+水电+场地+厂房折旧+设备折旧+加工辅材费用+广宣攻关等费用)!公式内涉及内容均以一个时间段为节点核算!改善投入=改善所有投入(含人工+调试+新投设备/厂房折旧等)需要注意:1、涉及折旧/租赁等如定义不清晰往往操作空间很大;2、另外改善前后都有产品合格率也要考虑;3、增效后看不见的消耗(如人员负荷度提高了费用是否会增加,且增加趋势不成比例;水电消耗等);4、该核算方式不适用于财务报表!5、容易漏掉“改善前收益”!BlueSea:效率改善的对象是人的还是设备的work center需要明确,相应的财务有该工作中心的工费率,节省的时间*工费率就是节省的钱,不过还要看这个改善适用的范围,如果只针对某款产品的话,那总得节省金额要看forecast的量。
产线效率计算及提升基础知识概要

产线效率计算及提升基础知识概要产线效率是指在一定时间内产线所能生产的产品数量与理论最大产能的比例。
提升产线效率是企业提高生产能力、提高产品质量和降低生产成本的关键。
生产能力是指在一定时间内产线能够生产的产品数量。
一般来说,生产能力可以通过以下公式计算:生产能力=单位时间内产品数量生产效率是指在一定时间内产线实际生产的产品数量与生产能力的比例。
生产效率可以通过以下公式计算:生产效率=实际生产数量/生产能力*100%提升产线效率的关键在于优化生产过程,减少生产中的浪费和资源的浪费。
常见的提升产线效率的方法包括以下几个方面:1.优化生产流程:通过分析生产流程,找出瓶颈和不必要的环节,通过改进和简化流程来提高效率。
例如,可以采用就近生产和物料配送方式、合理安排生产顺序等。
2.优化人员配置:科学合理地配置人员,充分利用人员的技能和经验,避免产生人员闲置和过多的劳动力分配问题。
3.自动化和机械化设备:引进高效的机械设备和自动化技术,减少人工干预,提高生产效率和质量。
自动化设备可以实现生产自动化、无人化,减少生产误差和次品率。
4.建立标准化和培训制度:制定生产标准和操作流程,确保生产过程的规范化和标准化。
同时对员工进行培训,提高员工的技能和操作水平,减少生产中的误操作和浪费。
5.持续改进和创新:通过持续改进和创新,不断提高生产效率和质量。
可以采用精益生产和六西格玛等方法,优化生产流程,减少浪费和缺陷。
6.管理和监控:建立有效的管理和监控制度,及时发现和解决问题,避免生产中的延误和故障。
可以采用生产管理软件、仪表盘系统等工具,对生产过程进行实时监控和数据分析。
综上所述,提升产线效率涉及多个方面的技术和管理措施,需要结合企业自身的实际情况制定具体的提升计划和实施方案。
只有持续不断地进行优化和改进,企业才能在激烈的市场竞争中保持竞争力。
生力、生效率及平衡的算方法

生产力、生产效率及线平衡的计算方法一、产效率的计算公式:实际产量*标准工时生产效率 =直接人力*上班工时+加班工时-异常工时1、实际产量:以产出机器台数为准2、加班工时:实际加班的直接人力×加班时间3、异常工时:本部门以外造成停线或挡产的工时4、标准工时:以IE发布标准工时为准二、生产力的计算公式:实际产量*标准工时生产力 =直接人力*上班工时+加班工时1、实际产量:以产出机器台数为准2、加班工时:实际加班的直接人力×加班时间3、标准工时:以IE发布标准工时为准三、生产线平衡:一个产品,少则两三个制程,多几十个,而每个工程又是由多个作业要素所组成,我们常见在生产工厂里,制造部门依物料的加工流程分为一、二、三课,而每课内又由许多的个别工序所组成,所以又把它连合成一条条的生产线。
我们这里所谈的生产线平衡法,广义的来说也应该含盖课与课之间的平衡。
而所谓的生产线平衡就是指工程流动间或工序流动间负荷之差距最小流动顺畅,减少因时间差所造成之等待或滞留现象。
四、生产线平衡表示法五、现状生产线平衡分析对生产中的生产线进行分析时,依下述步骤进行:1.对生产线的各工程顺序(作业单位)予订定,并填入生产流动平衡表内。
2.测算各工序实质作业时间以DM(Decimal Minute)为单位记入平稳表内(1人实质时间栏)注:1DM=0.01分 =0.6秒3.清点各工序作业人数,并记入人员栏内。
4. 1人实质作业时间÷人数分配,记入时间栏。
5.此分配时间划出柱状图或曲线图。
6.在分配的实质时间最高的这一工序顶点横向划一条点线。
7.计算不平衡损失上面斜线部分的总合即为为平衡损失的总合T(Lose)=∑|Tm-Ti|不平衡损失=(最高的DM×合计人数)-(各工序时间的合计)如上图=(21×19)-320=798、生产线平衡率各工序实质时间(1人) 320生产线平衡率= —————————— = ——— =80.2%最高的DM×合计人数 21×199、生产线不平衡损失率=1-生产线平衡率=1-80.2%=19.8%如使用输送带之传送,则应计算输送带的流动速度(M/时间单位)称为节拍时间,符号TC。
产线效率计算及提升基础知识

C17,R29,C 0,R4,U5,U1 11,Q6,Q8,C 4,C40,C20,
27,C21 ,R30
8,ZD3 J10,C36
插 C23,C12,C 22,Q7,C37, C30,D17
插 L1,D&E,C1 5,C16,Q9,C 64,+5Vsb 線
插 D16,VR3,D 20,D21,L9; BD1,L8
生产力之计算
生产力:产出工时 / 投入工时
产出工时:单位时间内良品的产出(获得)总工时 =线标准工时×工作站数×良品数(单位时间内,例
如8小时) 投入工时:单位时间内投入的总人工小时或机
器小时
生产效率:产出工时 / (投入工时 – 转嫁工时)
生产力之计算
损失工时 : 转嫁工时 + 非转嫁工时
转嫁工时 : 非部门内造成的损失
(3 * 4)
新线平衡率%
=
1 – 17%
=17% = 83%
线平衡率之提升% = (83% - 67%) / 67% = 24%
生产线平衡之实例说明(8)
•计算分割后的生产线之:
3+2+3+2
3.生产线工作站数之最小值(Nmin)=Min integer n│n≧
=3
3
4.生产线工作站数之可行最小值(Nfes)= number of k │P>(3/2) = 4
生产线平衡之衡量工具(2)
二、线平衡率% ( =1 - 平衡滞延率)
n
Σ ( C – Pk ) 1 - k=1
N*C
X 100%
n
Σ Pk
=
k=1
X 100%
N*C
生产线平衡之衡量工具(3)
生产现场管理常用分析公式
生产现场管理常用分析公式生产现场管理常用分析公式2012-11-07 13:35:25| 分类:生产现场管理 |字号订阅1、效率的计算方法:1)效率=实际值/基准值*100%2)作业效率=产能*标准工时÷投入工时*100%=实际产能÷标准产能*100%=标准作业时间÷实际作业时间*100%1)运转率=净运转时间÷运转可能的时间*100%2)故障率=故障次数÷运转总时间*100%3)线平衡效率=工序时间总和÷(最长工序时间*人员数)*100% 4)不良率=不良个数÷生产个数*100%5)损失率=(1-线平衡效率)*100%2、标准工时计算方法:1)基准周期时间(C/T)=(实测平均数)*(1+评比%)=正常作业时间。
2)标准产能=投入时间*投入人数=标准时间*标准人数3)瓶颈工时(L/T)=(C/T)max4)标准时间=C/T*(1+宽放率)5)标准时间=正常作业时间+宽放时间*100%=观测时间*评价系数*(1+宽放率)*100%6)标准总工时(S/T)=(C/T)max*标准人数*(1+宽放率)注:当投入人数=标准人数,标准产能=投入时间/标准时间,则实际计算公式:标准产能=3600/标准瓶颈工时。
3、直通率计算公式1)产品直通率=【进入过程件数-(返工+返修数+退货数)】/过程件数*100%2)直通率=(直通合格数/投入总数)*100%4、设备稼动率计算公式1)稼动率=(作业时间-流失时间)/作业时间,或,稼动率=稼动时间/总工时2)时间稼动率=稼动时间/负荷时间3)速度稼动率=基准周期时间/实际周期时间4)实质稼动率=生产量×实际周期时间/稼动时间5)性能稼动率=速度稼动率×实质稼动率6)良品率=(投料数-废品数)/投料数7)废品数=启动废品+过程废品+返修品+试验品8)设备综合效率(综合稼动率)=时间稼动率×性能稼动率×良品率。
生产线平衡计算
生产线平衡计算
生产线平衡计算是指在生产流程中,通过对各个工序的时间和人员进行合理分配,使得整个生产线的效率最大化,从而实现生产过程的稳定性和高效性。
下面介绍一些常用的生产线平衡计算方法:
1. Takt Time:指一个生产周期内需要生产完成的数量和时间的比率,即制造一个产品所需的时间。
Takt Time可以帮助确定生产线的节拍,以确保生产线在给定时间内生产足够的产品。
2. 工位平衡:将某个生产流程分成多个步骤(工位),并按照相同的时间分配到每个工位上,确保各个工位的工作量相等,避免出现瓶颈和浪费。
3. 数据收集:通过收集生产线上每个工序的时间数据以及操作员信息,分析每个工序的效率和人力利用率,并针对不足之处进行改进。
4. 标准化工作:建立标准化工作程序,包括操作规程、物料配送、设备调整等,以便提高生产效率和质量。
5. 连续改进:持续监控生产线效率和质量,发现问题并解决它们,以实现生产线的不断优化和改进。
需要注意的是,生产线平衡计算并不是一成不变的,它需要根据实际情况进行灵活调整和优化。
产线效率计算及提升基础知识
产线效率计算及提升基础知识引言:在现代制造业中,产线效率是一个关键的指标。
产线效率的高低直接影响着企业的生产能力和竞争力。
提升产线效率可以降低生产成本,提高产品质量和交付速度。
本文将介绍产线效率的计算方法和提升的基础知识,旨在帮助企业优化生产流程,提高产线效率。
一、产线效率计算方法产线效率可以用不同的指标进行衡量,下面介绍常用的两种计算方法。
1. OEE(Overall Equipment Effectiveness,总设备效率)OEE是一个衡量设备效率的指标,它将设备的运行时间、性能效率和质量损失综合考虑。
OEE的计算公式为:OEE=设备运行时间×性能效率×良品率设备运行时间=总停机时间/总时间性能效率=实际产量/理论产量良品率=良品数量/总产量通过计算OEE,可以知道设备的工作时间利用率、性能效率和质量损失情况,从而找出产线效率的薄弱环节,并采取相应的措施进行改善。
2. Takt时间(Takt Time)Takt时间是指单位时间内完成一个产品的节拍时间,即生产一个产品的平均时间。
Takt时间的计算公式为:Takt时间 = 计划生产时间 / 需求量通过计算Takt时间,可以根据市场需求和生产能力确定产品的生产周期,并对生产线进行合理的规划和调度。
二、产线效率提升的基础知识1.合理的生产布局合理的生产布局可以减少物料和产品的运输时间,节约生产成本,提高生产效率。
生产布局应该考虑到生产流程的顺序和物料的流动路径,以实现最小化的物料和人员移动。
2.汇总和分析数据汇总和分析数据可以帮助企业了解生产过程中的问题和瓶颈,并采取相应的措施进行改善。
通过数据分析,可以找出影响产线效率的关键环节,并针对性地进行改进。
3.标准化操作通过建立标准操作程序和培训员工,可以确保生产中的每一步都按照最佳实践进行。
标准化操作可以减少错误和浪费,提高生产效率和产品质量。
4.持续改进持续改进是提高产线效率的关键。
改善收益金额计算公式
以上计算方法外也可用其它公式,只要是客观的效果金额即可.
效果节省及投入成本计算方法:
项目
计 算 公 式(以月度为周期计算)
生产效率提升
S/T缩短:(缩短前标准-缩短后标准)×月生产量×小时工资(14元)
换模时间缩短:(改善前换模时间-改善后换模时间)×月换模次数×小时工资
流失时间减少:(改善前流失时间-改善后流失时间)×月工作天数×小时工资
品质
向上
节俭材料费:(改善前资材用量-改善后资材用量)×资材单价×月替效果除外.
其他
在工减少:(改善前月在工量-改善后月在工量)×在工单价×金融利息
在库减少:(改善前月在库量-改善后月在库量)×在库单价×金融利息
生产量增加:(改善后月生产能力-改善前月生产能力)×单位利润
备注
小时工资:对应岗位员工小时工资¥(各分公司制定本单位统一指导标准)
节俭修理工数:(改善前返修率-改善后返修率)×月生产量×单位修理工时×小时工资
工程不良率:(改善前废弃率-改善后废弃率)×产品单价×月生产量
客户不良:(改善前月索赔费-改善后月索赔费)
人员节俭
少人化节俭:(改善前人数-改善后人数)×年均人工资(8万元)
设备工具改善
设备生产性向上:(改善后设备综合效率-改善前设备综合效率)×设备购入价格/设备折旧年限
C/O缩短:(缩短前C/O-缩短后C/O)/缩短前C/O×设备购入价格/设备折旧年限
流失减少:(改善前流失率-改善后流失率)×设备购入价格/设备折旧年限
节俭原价
单价下引:(改善前单价-改善后单价)×月生产量[使用量]
节俭使用量:(改善前月使用量-改善后月使用量)×单价
代替效果:(代替前单价-代替后单价)×月使用量
- 1、下载文档前请自行甄别文档内容的完整性,平台不提供额外的编辑、内容补充、找答案等附加服务。
- 2、"仅部分预览"的文档,不可在线预览部分如存在完整性等问题,可反馈申请退款(可完整预览的文档不适用该条件!)。
- 3、如文档侵犯您的权益,请联系客服反馈,我们会尽快为您处理(人工客服工作时间:9:00-18:30)。
22.8.653 22.8.691 22.9.601 22.8.599
14W 6400 8480
6 18.00 2.52
APR
15W 1 5400 6 7040 9
5 18.00 1 2.56 2
2012年该生产线产量310263套,则计算收益如下:
收益=
(
310263 2.53
310263 2.82
2.43 2.52 2.58 2.48 2.63 2.61 2.61 2.59 2.52 2.56 2
通过改善,2012年10~12月平均出产量/小时/人”为2.82:
35W 720 000 3 0.40 .74
36W 8047 7920
6 21.18 2.88
SEP
37W 7410 7200
5 21.46 2.88
谢谢!
生产线效率提升持续改善收益计算
持续改善办公室 2013年
内容
目前效率提升方面的收益计算公式有如下3种:
1、效率提升收益=减员数×年人工成本值-同产量新增工时成本-其它新增成本 2、效率提升收益=同等效果项目对象减少的工时×工时成本-其它新增成本 3、效率提升收益=(成品销量-极限产能实际值×(1+设备新增率))×单位边 际贡献-新增成本
57706400 77200600
45
56
1188..0000 1188..0000
22..4734 22..5727
487WW 75887613 16080780
75 1188..1044 22..5884
498WW 65741939 77711600
65 1188..0670 22..8498
MARDEC
)*
34 =428782.7元
6
注意事项
• 涉及效率提升,一定要提交标准工时表。 • 若该生产线申报改善收益,一定要有改善内容,
采取了改善措施,否则只能报纯降本项目。 • 若该条生产线在之前已计算过减人或其他的收益
的,需要将这部分金额扣除。 • 效率提升收益为一年结一次,一般原则上是当年1
季度结上一年度的收益。
0
4198 5435 7871 5499 8013 6200 7891 6773 6400 5400 6
0
5760 7200 10080 7160 10080 7920 10080 8640 8480 7040 9
0
4
5
7
5
7
6
7
6
6
5
18.00 18.00 18.14 18.60 18.14 18.00 18.00 18.13 18.00 1
38W 39W 410WW 718周5实际2产90量7 53710473 工78作60时间3(4M9IN0) 73685000
6周工作天5 数 64 19.6周7平均18人.0数0 1188..0000 出2.产79量/小2时.7/8人 22..4796
JOACNT
421WW 432WW
66986178 55895127
2
内容
公式使用规则:
YES
其他方式计算
效率提升
生产线是否多品种大批量, 无法实现工时精确分解。
(如涂装线)
NO
能否采用公式3
NO
采用 公式2或公式1计算
YES
NO
是否
24小时生产
YES
NO
用公式3能否
计算出收益
YES
得出收益
3
内容
公式2使用说明:
工时成本,即68000/250/8=34元/小时。
4190WW 5101WW 5112WW 5123WW
68205103 66529000 67485991 76579763
713010080 77691200 714020080 88664400
67
76
67
66
1188.0.104 1188.0.000 1188.0.000 1188.2.153
JAN
1W 2W 3W 4W
周实际产量 5707 6967 5852
0
工作时间(MIN) 7650 9320 7940
0
周工作天数 6
7
6
0
周平均人数 18.00 18.00 18.00
出产量/小时/人 2.49 2.49 2.46
FEB
MAR
APR
5W 6W 7W 8W
9W 10W 11W 12W 13W 14W 15W 1
效率提升收益=同等效果项目对象减少的工时×工时成本-其它新增成本
“同等效果项目对象减少的工时”=
(
当年度产量 上一年度收益结算时的“出产量/小时/人”
当年度产量 当年改善后3个月平均“出产量/小时/人”
)
注:“出产量/小时/人”引用生产线效率提升表中的“出产量/小时/人”。 若以当年度改善后3个月计算收益结题,则产量以月度滚动计划为准。 2012年度改善前的数据引用2012年1季度平均数据。
4
内容
公式3使用说明:
成品销量,即改善后月度滚动计划。 效率提升收益=(成品销量-极限产能实际值×(1+设备新增率))×单位边际贡献-新增成本
极限产能实际值=改善前3个月平均“当天实际产量”×365
注: “当天实际产量”引用生产线效率提升表中的“当天实际产量”。
5
案例
某生产线效率情况 2012年1~3月平均“出产量/小时/人”为2.53:
97322000 76964800
75
66
1280..0700 1188..0807
22..4794 22..4862
43WW 31008 37010
06 18.00 2.79
454WW 67049 81020
06 18.00 2.77
FEB NOV
465WW 476WW
45179987 55483750