车削中零件表面粗糙度控制方法探讨
细长轴车削加工问题浅析

细长轴车削加工问题浅析细长轴件是一种常见的机械零件,如车床主轴、机床导轨等。
其加工过程中需要采用车削加工工艺,但由于其特殊的几何形状,加工过程中容易出现一些问题。
本文将对细长轴件车削加工中出现的问题进行分析和解决方法的探讨。
一、加工难度高细长轴件加工时,由于长度比较长,容易出现加工过程中的“弯曲”现象,这会导致加工难度增加。
因此,为了确保加工质量,需要在加工过程中采用一些措施,比如采用精确的机床、加压滚轮等来防止弯曲。
二、加工质量不稳定由于加工过程中存在弯曲的现象,轴件的加工质量很容易受到影响,导致加工质量不稳定。
为了避免这种情况的发生,关键是要选择适合的机床、工艺和切削参数,控制车刀切削速度,保证切削力和切削热量在可控的范围内,从而实现加工质量的稳定。
三、加工表面粗糙度高细长轴件加工表面粗糙度高是常见的现象,主要是由于车削过程中产生的振动和切削力导致的。
为了避免这种现象的发生,需要优化加工工艺、选择合适的刀具和刀柄,选用合适的车削速度和加工深度等。
同时,还可以采用降低切削液粘度、提高切削液流量等方法来降低表面粗糙度。
四、刀具寿命短由于细长轴件的加工过程存在较大的切削力和振动,因此容易导致刀具磨损严重和寿命短。
为了延长刀具的寿命,可以采用选择合适的刀具材料和刀具形状,选用合适的切削参数和刀具覆盖率,采用精确的刀具刃磨工艺等方法。
总之,细长轴件的加工过程中会出现很多问题,但只要合理选择机床、优化加工工艺、严格控制加工质量,就能够保证加工效率和加工质量的稳定。
在实际加工过程中,应根据不同的加工要求和加工对象采用合适的加工工艺和切削参数,以提高加工效率和加工质量。
研磨表面粗糙度值高的解决方法
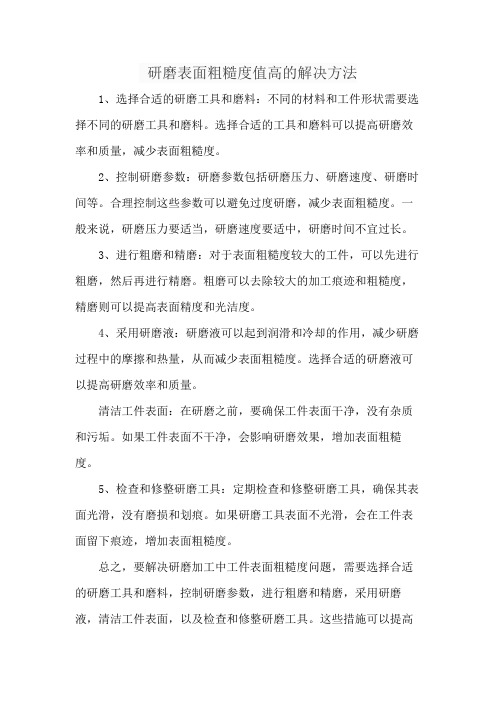
研磨表面粗糙度值高的解决方法
1、选择合适的研磨工具和磨料:不同的材料和工件形状需要选择不同的研磨工具和磨料。
选择合适的工具和磨料可以提高研磨效率和质量,减少表面粗糙度。
2、控制研磨参数:研磨参数包括研磨压力、研磨速度、研磨时间等。
合理控制这些参数可以避免过度研磨,减少表面粗糙度。
一般来说,研磨压力要适当,研磨速度要适中,研磨时间不宜过长。
3、进行粗磨和精磨:对于表面粗糙度较大的工件,可以先进行粗磨,然后再进行精磨。
粗磨可以去除较大的加工痕迹和粗糙度,精磨则可以提高表面精度和光洁度。
4、采用研磨液:研磨液可以起到润滑和冷却的作用,减少研磨过程中的摩擦和热量,从而减少表面粗糙度。
选择合适的研磨液可以提高研磨效率和质量。
清洁工件表面:在研磨之前,要确保工件表面干净,没有杂质和污垢。
如果工件表面不干净,会影响研磨效果,增加表面粗糙度。
5、检查和修整研磨工具:定期检查和修整研磨工具,确保其表面光滑,没有磨损和划痕。
如果研磨工具表面不光滑,会在工件表面留下痕迹,增加表面粗糙度。
总之,要解决研磨加工中工件表面粗糙度问题,需要选择合适的研磨工具和磨料,控制研磨参数,进行粗磨和精磨,采用研磨液,清洁工件表面,以及检查和修整研磨工具。
这些措施可以提高
研磨效率和质量,减少表面粗糙度。
UG编程在车削表面粗糙度控制中的技巧和注意事项
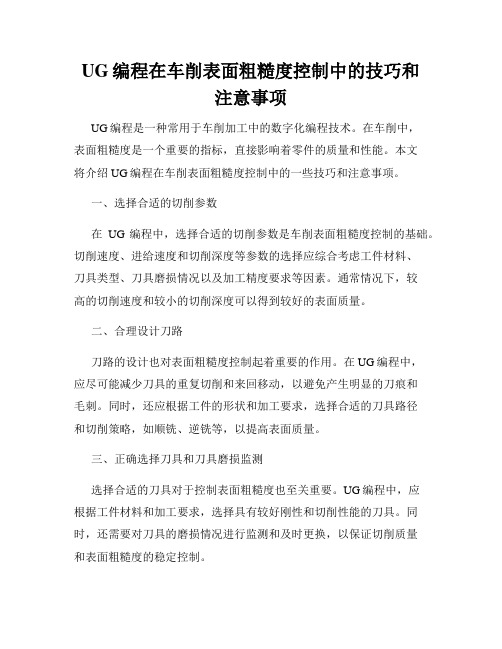
UG编程在车削表面粗糙度控制中的技巧和注意事项UG编程是一种常用于车削加工中的数字化编程技术。
在车削中,表面粗糙度是一个重要的指标,直接影响着零件的质量和性能。
本文将介绍UG编程在车削表面粗糙度控制中的一些技巧和注意事项。
一、选择合适的切削参数在UG编程中,选择合适的切削参数是车削表面粗糙度控制的基础。
切削速度、进给速度和切削深度等参数的选择应综合考虑工件材料、刀具类型、刀具磨损情况以及加工精度要求等因素。
通常情况下,较高的切削速度和较小的切削深度可以得到较好的表面质量。
二、合理设计刀路刀路的设计也对表面粗糙度控制起着重要的作用。
在UG编程中,应尽可能减少刀具的重复切削和来回移动,以避免产生明显的刀痕和毛刺。
同时,还应根据工件的形状和加工要求,选择合适的刀具路径和切削策略,如顺铣、逆铣等,以提高表面质量。
三、正确选择刀具和刀具磨损监测选择合适的刀具对于控制表面粗糙度也至关重要。
UG编程中,应根据工件材料和加工要求,选择具有较好刚性和切削性能的刀具。
同时,还需要对刀具的磨损情况进行监测和及时更换,以保证切削质量和表面粗糙度的稳定控制。
四、采用优化的冷却润滑方式冷却润滑方式也会对车削表面粗糙度产生重要影响。
UG编程中,可以通过合理设置冷却液的喷射方式和喷射位置,以及控制冷却液的流量和温度等因素来优化冷却润滑效果。
良好的冷却润滑可以有效降低切削温度,减少切削力和摩擦,提高表面质量。
五、精确控制加工精度在UG编程中,加工精度的控制也是实现表面粗糙度控制的关键。
应合理设置数控系统的参数,提高数控机床的定位精度和重复定位精度。
同时,还应根据工件的实际尺寸和加工要求,对加工工序进行适当的补偿和调整,以提高表面质量和精度。
六、充分利用UG编程的功能和优势UG编程作为先进的数字化编程技术,具有丰富的功能和优势,可以在车削表面粗糙度控制中充分发挥作用。
在编程过程中,可以合理利用UG软件的各种工具,如模拟仿真、插件功能等,对刀具路径和切削策略进行优化和调整,进一步提高表面质量和精度。
微小型零件车铣加工表面粗糙度单因素试验研究

为优化切削参数和提高加工质量提供技术保2车铣加工基本原理车铣加工实质上是通过铣削达到常规的车削目的使工件在形状精度位置精度已加工表面完整性等多方面达到使用要求的一种先进切削加工方法
维普资讯
20 0 7年 8月
广 西 轻 工 业
G A G I O R A FLG TID SR U N X U N LO IH U T Y J N 机 械 与 电 气
速 的 变化 对粗 糙 度 值 的 影 响程 度 刚好 相 反 。
【 关键词 】 微小 型零件; 铣加工; 参数; 车 切削 表面粗 糙度; 素试验 单因 【 中图分类号 】T 1 563 G 1. 【 文献标识码 】A 【 文章编号 】1 0 — 6 32 0 )8 0 4 — 2 0 3 2 7 ( 70 — 0 2 0 0
镰 刀蕨 方 向
图 1 正 交车 铣 加 工 原 理
图 3 工件 转 速 与表 面 粗糙 度 的 关 系曲 线
【 作者 简介 】 刘克非(9 5 )男, 16 一 , 湖北荆州人, 副教授 , 主要从事微小型零件的加工及装配技术研究。 【 金项 目 】 基 湖北省教育厅重点科研资助项目( 2 0 20 3 D 0750)
试验参数选用如下 :
工 件 转 速 :0 r n 1 0/ ; mi 铣 刀 转 速 :2 0 r n 1 0 0/ ; mi 轴 向进 给 速 度 为 :.1 00 mm; 切 削 深 度 :.0 — .3 O0 5 01 mm 试 验 结果 如 图 6 。 示
车削橡胶表面粗糙度ra0.8的工艺_解释说明
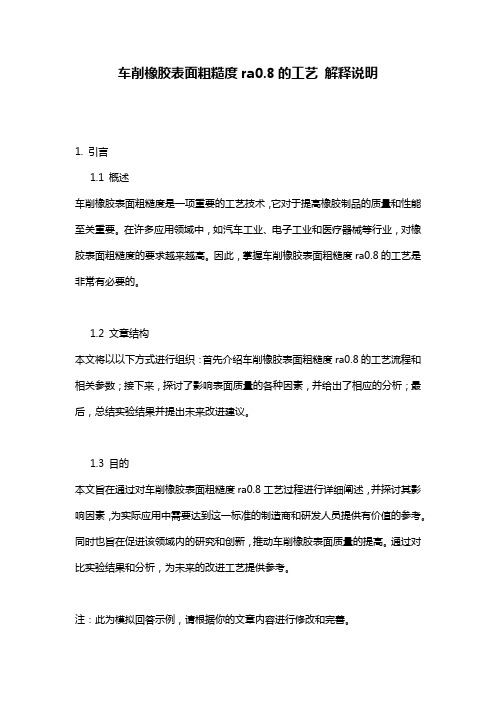
车削橡胶表面粗糙度ra0.8的工艺解释说明1. 引言1.1 概述车削橡胶表面粗糙度是一项重要的工艺技术,它对于提高橡胶制品的质量和性能至关重要。
在许多应用领域中,如汽车工业、电子工业和医疗器械等行业,对橡胶表面粗糙度的要求越来越高。
因此,掌握车削橡胶表面粗糙度ra0.8的工艺是非常有必要的。
1.2 文章结构本文将以以下方式进行组织:首先介绍车削橡胶表面粗糙度ra0.8的工艺流程和相关参数;接下来,探讨了影响表面质量的各种因素,并给出了相应的分析;最后,总结实验结果并提出未来改进建议。
1.3 目的本文旨在通过对车削橡胶表面粗糙度ra0.8工艺过程进行详细阐述,并探讨其影响因素,为实际应用中需要达到这一标准的制造商和研发人员提供有价值的参考。
同时也旨在促进该领域内的研究和创新,推动车削橡胶表面质量的提高。
通过对比实验结果和分析,为未来的改进工艺提供参考。
注:此为模拟回答示例,请根据你的文章内容进行修改和完善。
2. 车削橡胶表面粗糙度ra0.8的工艺2.1 工艺介绍车削橡胶表面粗糙度ra0.8的工艺是一种用于加工橡胶材料的方法,旨在获得满足特定要求的表面粗糙度。
橡胶材料常用于制造密封件、软管和弹性零部件等,其表面质量对于产品性能至关重要。
通过合理的工艺参数控制和优化方法,可以实现车削橡胶表面平整度和精度要求。
2.2 工艺参数控制实现车削橡胶表面粗糙度ra0.8需要对以下工艺参数进行控制:a) 切削速度:切削速度是指车刀在单位时间内切削点周围移动的线速度。
适当提高切削速度有助于减少切屑与被加工表面的接触时间,从而降低加工过程中的热积聚和振动,进而改善表面质量。
b) 进给速度:进给速度是指车刀在单位时间内沿轴向方向从外到内移动的速率。
适当调整进给速度可以控制切削层厚度和切削力,有效降低交变应力带来的表面痕迹,并减少成形副产品的生成。
c) 刀具选择:选择合适的车刀类型、形状和材料对于获得期望的表面粗糙度至关重要。
减小工件表面粗糙度的方法

减小工件表面粗糙度的方法引言工件表面粗糙度是指表面的几何形状与理想平坦表面之间的差异程度。
表面粗糙度对于许多工件的性能和功能起着重要的影响。
较小的表面粗糙度可以提高工件的光洁度、耐磨性和材料的强度。
本文将探讨一些减小工件表面粗糙度的方法。
表面加工方法机械加工1.车削–通过在旋转工件上切削材料来改善表面粗糙度。
–选择适当的切削速度、进给量和刀具形状可以获得更好的表面质量。
2.磨削–利用砂轮在工件表面切削和磨砂以减小表面粗糙度。
–使用不同颗粒大小和材料的砂轮可实现不同的表面光洁度。
化学方法1.电解抛光–通过电解作用将工件表面的材料溶解以减小表面粗糙度。
–控制电解液成分、温度和电流密度可获得所需的表面质量。
2.化学抛光–使用酸、碱等化学溶液对工件表面进行处理以改善表面光洁度。
–选择合适的溶液浓度和处理时间,避免过度腐蚀。
物理方法1.喷砂–利用高速流动的砂粒对工件表面进行冲击,去除表面的杂质和粗糙度。
–调节喷砂压力、砂粒种类和喷砂时间可控制表面质量。
2.光束照射–使用激光或电子束对工件表面进行照射,使其熔化和重新凝固以减小表面粗糙度。
–控制照射能量和速度可实现所需的表面质量。
表面处理技术酸洗1.酸洗方法–将工件浸泡在浓度适中的酸溶液中,去除表面的氧化层和锈蚀物。
–常用的酸洗方法包括浸泡法、喷淋法和刷洗法。
2.注意事项–控制酸洗时间,避免过度腐蚀工件表面。
–对不同材料应选择合适的酸洗液和浓度。
表面涂层1.喷涂–使用喷枪将涂料均匀地喷在工件表面上,形成一层保护性涂层。
–选择合适的涂料类型和喷涂工艺可改变表面粗糙度。
2.电镀–在工件表面通过电解沉积金属等材料以形成一层金属涂层。
–控制电镀时间和电流密度可获得所需的表面质量。
表面打磨1.机械打磨–使用砂纸、抛光布等工具对工件表面进行打磨以改善表面光洁度。
–选择合适的打磨材料和方法可实现不同的表面质量。
2.化学打磨–使用强酸或碱溶液对工件表面进行处理以降低表面粗糙度。
车削过程中工件表面粗糙度值的控制
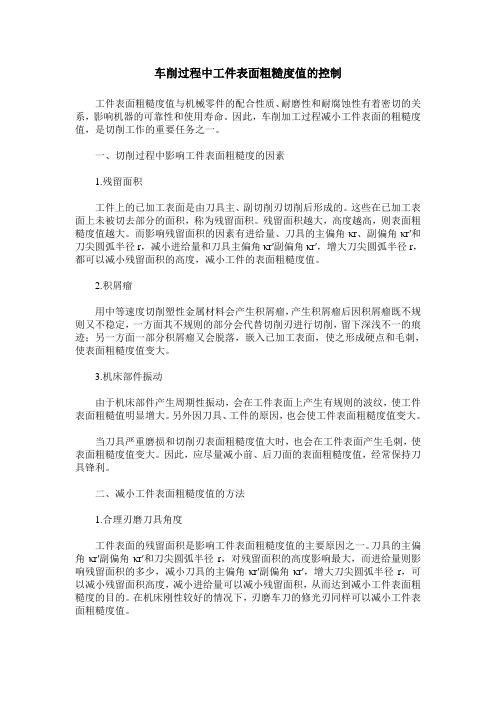
车削过程中工件表面粗糙度值的控制工件表面粗糙度值与机械零件的配合性质、耐磨性和耐腐蚀性有着密切的关系,影响机器的可靠性和使用寿命。
因此,车削加工过程减小工件表面的粗糙度值,是切削工作的重要任务之一。
一、切削过程中影响工件表面粗糙度的因素1.残留面积工件上的已加工表面是由刀具主、副切削刃切削后形成的。
这些在已加工表面上未被切去部分的面积,称为残留面积。
残留面积越大,高度越高,则表面粗糙度值越大。
而影响残留面积的因素有进给量、刀具的主偏角κr、副偏角κr′和刀尖圆弧半径r,减小进给量和刀具主偏角κr′副偏角κr′,增大刀尖圆弧半径r,都可以减小残留面积的高度,减小工件的表面粗糙度值。
2.积屑瘤用中等速度切削塑性金属材料会产生积屑瘤,产生积屑瘤后因积屑瘤既不规则又不稳定,一方面其不规则的部分会代替切削刃进行切削,留下深浅不一的痕迹;另一方面一部分积屑瘤又会脱落,嵌入已加工表面,使之形成硬点和毛刺,使表面粗糙度值变大。
3.机床部件振动由于机床部件产生周期性振动,会在工件表面上产生有规则的波纹,使工件表面粗糙值明显增大。
另外因刀具、工件的原因,也会使工件表面粗糙度值变大。
当刀具严重磨损和切削刃表面粗糙度值大时,也会在工件表面产生毛刺,使表面粗糙度值变大。
因此,应尽量减小前、后刀面的表面粗糙度值,经常保持刀具锋利。
二、减小工件表面粗糙度值的方法1.合理刃磨刀具角度工件表面的残留面积是影响工件表面粗糙度值的主要原因之一。
刀具的主偏角κr′副偏角κr′和刀尖圆弧半径r,对残留面积的高度影响最大,而进给量则影响残留面积的多少,减小刀具的主偏角κr′副偏角κr′,增大刀尖圆弧半径r,可以减小残留面积高度,减小进给量可以减小残留面积,从而达到减小工件表面粗糙度的目的。
在机床刚性较好的情况下,刃磨车刀的修光刃同样可以减小工件表面粗糙度值。
刀具前角的大小直接影响切削刃的锋利程度,影响切削力的大小与切削变形的大小,增大前角可使切削刃锋利,切削力减小,切削变形减小。
表面粗糙度加工方式
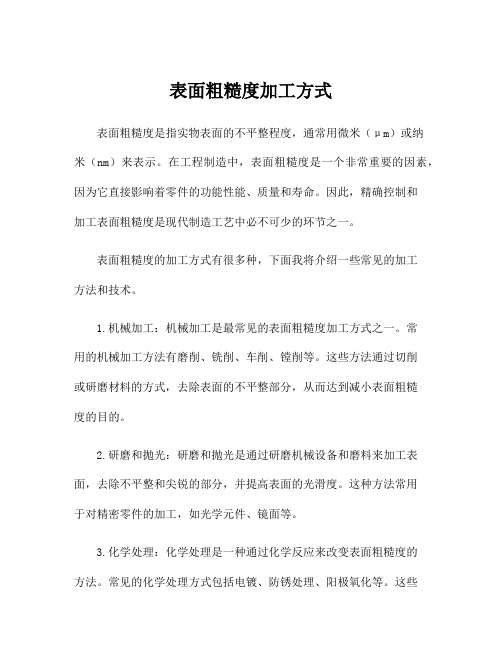
表面粗糙度加工方式表面粗糙度是指实物表面的不平整程度,通常用微米(μm)或纳米(nm)来表示。
在工程制造中,表面粗糙度是一个非常重要的因素,因为它直接影响着零件的功能性能、质量和寿命。
因此,精确控制和加工表面粗糙度是现代制造工艺中必不可少的环节之一。
表面粗糙度的加工方式有很多种,下面我将介绍一些常见的加工方法和技术。
1.机械加工:机械加工是最常见的表面粗糙度加工方式之一。
常用的机械加工方法有磨削、铣削、车削、镗削等。
这些方法通过切削或研磨材料的方式,去除表面的不平整部分,从而达到减小表面粗糙度的目的。
2.研磨和抛光:研磨和抛光是通过研磨机械设备和磨料来加工表面,去除不平整和尖锐的部分,并提高表面的光滑度。
这种方法常用于对精密零件的加工,如光学元件、镜面等。
3.化学处理:化学处理是一种通过化学反应来改变表面粗糙度的方法。
常见的化学处理方式包括电镀、防锈处理、阳极氧化等。
这些处理方式可以在表面形成一层保护膜或改变表面的化学性质,从而改善表面光洁度和耐腐蚀性能。
4.热处理:热处理是一种通过加热和冷却的方式来改变材料的组织结构和性能的方法。
在热处理过程中,材料的表面粗糙度也会发生改变。
例如,淬火和回火可以使材料表面形成硬度高、抗磨损性能更好的层。
5.表面喷涂:表面喷涂是一种通过将涂层喷射到工件表面,从而改变其表面粗糙度和性能的方法。
常用的喷涂方式包括喷漆、喷粉末、喷涂液等。
这些涂层可以增加表面的光滑度、硬度和耐腐蚀性能。
6.激光加工:激光加工是一种非接触式加工方式,可以对材料进行高精度的加工。
激光可以通过高能量的热、蒸发和熔化的方式,去除表面的不平整部分,从而改善表面的粗糙度。
以上是一些常见的表面粗糙度加工方式,每种方式都有其适用的场合和限制。
在实际应用中,需要根据具体材料和要求选择合适的加工方式。
同时,加工后的表面粗糙度应该符合相关标准和要求,以确保零件的质量和性能。
除了加工方式之外,还可以通过优化工艺参数、采用更高精度的加工设备、改进材料和润滑剂等措施来减小表面粗糙度。
- 1、下载文档前请自行甄别文档内容的完整性,平台不提供额外的编辑、内容补充、找答案等附加服务。
- 2、"仅部分预览"的文档,不可在线预览部分如存在完整性等问题,可反馈申请退款(可完整预览的文档不适用该条件!)。
- 3、如文档侵犯您的权益,请联系客服反馈,我们会尽快为您处理(人工客服工作时间:9:00-18:30)。
削加工 中不断追求的 目标之一 。下面对表面粗糙度
等方面进行分析和探讨 。
验 ,从 以下 几方 面 对 车削 加 工 中如 何 控制 表 面粗 糙 度值 进 行探讨 。
2 . 1 磨 损 斑点闺
1 表面粗糙度对零件性能造成 的影响【 1 ]
( 1 )耐磨性 :耐磨性 就 是零 件 抵抗 磨 损 的性 能 。
旋转精度 、 刚度 、 抗振性 和减 小热变形影响 ; 同时调
使 间隙小于 0 . 0 4 m m, 并保证床 时产生 的一种很严重的表面缺陷 ,可使工件粗糙度 整好车床床鞍间隙 , 增大 2 — 4级左 右 。车削 时 车刀 要保 持锋 利 , 可 大大 减 鞍移动平稳 、 轻便 ; 调整好 中滑板丝杠和螺母 间隙 ,
利用切削速度来控制积屑瘤 。 如用高速钢刀车 , 尽 可能要小于 5 m / a r i n , 采用低速车并浇注充足切削液 , ( 2 )刀具 : 刀具参数根据 实际合理选择 , 经常保 持切 削刃光洁 、 锋利 , 增加车刀安装 刚度 , 避免 车刀
尤 其是 内孔 车 刀安 装更 要 注意 。 若用硬质合金刀车应提高 ,避开最易产生积屑瘤 弯 曲和 振动 , ( 3 ) 机床 : 调整车床主轴轴承间隙 , 提高主轴 的 的中速区域 , 尽量采用 7 0 m / a r i n以上速度。 ( 2 )鳞 刺 : 鳞 刺 是 在低 速 、 小 前 角 切 削 塑性 金 属
E q u i p me n t Ma n u f a c t u r i n g T e c h n o l o g y No . 8 , 2 0 1 5
车削 中零件 表面粗糙 度控 制方法探讨
董 传 峰
( 山东冶金技师学院 山东 济南 2 5 0 1 0 9 )
摘 要: 机械 零件的破 坏 , 往往是从表 面层 开始的。产品的性能 , 尤其是 它的可靠性和耐久性 , 在很 大程度上取 决于零 件
寿命 。如何减小粗糙度值 , 从而提高表面质量也是切
零 件 类 型 虽然 多 种 多样 , 无论 轴 类 还 是套 类 , 无 对零件使用性能 的影响 ,影响零件表面粗糙度的 因 论薄壁还是细长类零件 ,在车削时粗糙度控制方法 素 ,以及在车削生产 中如何控制零件的表面粗糙度 都是 相 似 的 ,下 面 结合 笔 者 多年 机 械 加工 和教 学 经
中图分类号 : T G5 1 文献标识码 : B 文章编号 : 1 6 7 2 — 5 4 5 X ( 2 0 1 5) 0 8 — 0 21 4 - 0 2
在 车 削加 工 中 ,由 于各 种原 因使 得 加 工后 的零
( 3 )耐腐 蚀性 :实 践 表 明零件 表 面过 于 粗糙 , 轮
当车刀达 到磨 钝标 准 以后继 续使 用 , 这 时会 产生
噪音和加剧振动 , 增 大了刀具和工件的摩擦 , 会在零
当零件表面过于粗糙时 , 则会使摩擦 系数增大 , 加剧 件 上 留下 挤 亮 的斑 纹 , 增 大 了粗 糙 度 , 车 削 时 一定 要 了零件 的磨损 , 太光滑反而造成润滑油不易储存 , 润 使 车刀保 持锋 利状 态是第 一位 的 , 钝 了应 及 时刃磨 。 滑不充分 , 同样都会降低零件寿命 , 要根据实际确定 2 . 2 积 屑瘤 刺痕 、 鳞 刺及切 屑 拉毛 [ 2 1
如 何评 定 一 个零 件 的表 面 粗糙 程 度 ,我们 通 常 合 性质 。
采用 R轮廓参数 , 其中算术平均偏差 R a 和轮廓最大
描 述 工 件 表 面上 微小 的间距 和微 小 的 峰谷 所 形 成 的 微 观 几 何不 平 度 ,能体 现 工件 表 面 微 观几 何 形 状 的
粗 糙程 度 。 ( 1 )积 屑瘤 刺痕 : 当用 中等速 度 切 削塑性 金 属 产
( 2 ) 疲劳强度: 零件有时会在毫无征兆的情况下 生积屑瘤后 ,有一少部分脱落的积屑瘤会嵌入到零 突然 破 坏 掉 ,这 是 由于受 交 变载 荷 冲击 引起 应 力 集 件 已加 工 面 , 形 成一 些 密 密麻 麻 的 硬点 和 毛 刺 , 加 大 中, 产生疲劳裂纹 , 降低 了零件的疲劳强度。
件 表 面 与理 想 表 面不 一 致 ,总 会存 在 许 多 高低 不平 廓 凹谷极易存储腐蚀性物质 , 抗蚀性就会越差 。
的微小峰谷 ,这些微观几何形状误差就是通常意义
上 的表 面粗 糙度 。
( 4 ) 配合性质 : 表面粗糙度会使相互配合的零件 之 间间隙增大或过盈减小 ,从而影 响配合精度和配
( 5 ) 接触刚度 : 如果零件表 面过于粗糙 , 会使零
响 到机器 的工 作精 度 和造 成工 艺系 统 的振动 。
高度 R z 又是最常用的两个高度参数 。表面粗糙度是 件 的接触表面实际面积减小 , 接触刚度降低 , 从而影
质量 , 对零件的耐磨性 、 耐腐蚀性 、 疲 劳强度、 配合性 2 车削. 中影 响工件表面粗糙 度的 因素及控 制 质 以及力学性能都有很大影响 ,甚至直接影响零件 方 法
表面层的加工质量 。 表面粗糙 度是衡量 已加工表面质量比较直观 , 也是最常采 用的一项指标 。 在机械加工尤其是车削 中
如 何 控 制 零 件 粗糙 度 , 加 工 出 高质 量 的零 件 , 也 是 各 类技 术人 员要 解 决 的 首要 问题 。
关键词 : 车削; 表面粗糙 度 ; 控制 ; 方法
收稿 E t 期: 2 0 1 5 — 0 5 — 0 6
粗糙 度 。积屑瘤 对 切削 速度 是 比较敏 感 的 , 在 车 削时
作者简 介: 董传峰( 1 9 8 1 一 ) , 男, 山东省济南市人 , 本科 , 助理讲师。研究方向 : 机 电一体化 。
21 4
《 装备制造技术) ) 2 0 1 5 年第 8 期