精实生产零PPM不良的品质管理零PPM不良防错实例
精益生产方式中的零缺陷品质管理方法.

精益生产方式中的零缺陷品质管理方法质量是企业的生命,这一命题被许多优秀的企业奉为金科玉律,这些企业也因为信奉质量哲学,成为了举世瞩目世界级跨国公司。
这些公司包括发明6σ管理系统的摩托罗拉,将6σ管理系统发展到登峰造极的通用电气公司,他们在全力提高产品品质的同时,也因此获得了丰厚的利润回报,通过提高质量,不仅获得了顾客满意度,同时节省了巨额的质量成本。
我们可以坚定的宣告,质量的提高与成本的降低并行不悖,追求零缺陷就是追求最最大限度的成本降低。
条条大路通罗马,追求零缺陷的道路也同样不止一条,就在欧美企业对6σ管理系统顶礼膜拜时,借助于东西方文化的差异,在东方,在日本,在丰田,逐步形成了另外一套零缺陷的品质管理方法,并取得了骄人的业绩。
据2000年的统计,每百辆日本汽车的缺陷数为9个,每百辆德国汽车的缺陷数为11个,每百辆的美国汽车的缺陷数为14个。
可以用事实证明,诞生于日本丰田的精益生产方式,是与6σ管理系统并驾齐驱的国际顶级品质管理系统,目前全球最优秀的制造型企业将6σ管理系统与精益管理(Lean相结合,并以实施Leanσ为荣。
精益生产管理是从消除制造过程中的浪费为主要出发点,在制造过程中,共有7大浪费,其中之一就是制造不良的浪费,为了消除这一浪费,“自働化”,成为精益生产的两大支柱之一。
可以说,追求零缺陷的品质管理,是精益生产系统顺利运行的基础。
质量管理的方法是与生产管理的方法同步提高的,在制造业处于作坊式的时期,质量的保证主要依赖于制造者的个人技能,当时并没有专职检查人员的出现;当生产管理进入到大批量生产的年代后,专职检验员的出现,采用适当的抽检比例,判断整批产品的质量符合性成为质量保证的主流,进而发展到采用统计过程控制的方法,追求用尽可能少的样本,通过控制影响产品质量的诸要素来保证产品的质量。
尽管如此,采用统计过程控制的方法并不能保证零缺陷,尽管品质的不合格率已采用PPM的方法进行统计,但是,对于顾客来说,购买到一件不合格品,就足以放弃对企业的信心,从而让企业失掉顾客的忠诚度。
经典精益生产改善案例

经典精益生产改善案例精益生产说起来容易,做起来难。
精益之行还需要在精益思想、原则和准则的指导下学习和实践一些有用的工具和方法,比如工业工程(IE)、价值流图分析、柔性生产线建立、缩短作业转换时间、拉动式连续“一个流”生产、5S、QC工具、统计质量控制、防呆错技术、TPM等等。
01. 自动化与防呆防错,一个小改善的大效果零缺陷最大的窍门:通过发掘人的智慧,找到“傻瓜”都能做对的办法,减少品质对人的依赖。
1 . 有一家电子生产型企业,他们在组装设备时由于需要装配的螺丝数量多,操作工经常会有遗忘,导致不良。
后来,公司就从精益生产的角度进行考虑,降低人的因素。
他们专门设计了一种机械手,机械手末端有磁铁。
如果这个部位需要装5颗螺丝,机械手就自动抓起5颗螺丝,如果需要装16颗螺丝,机械手就自动抓起16颗螺丝。
操作工只要看下机械手上有没有剩余的螺丝就可以了。
这样就减少了品质不良的发生。
2 . 还有一家生产复印机的工厂,他们的复印机里面有一个小风扇,这个小风扇非常重要,一旦装反了,就会导致机械损坏。
但由于是流水线作业,操作工在装配时,由于疲劳、遗忘等多种原因,可能会出错。
主管就要求操作工装好后要进行检查,用手摸一下,试下风向。
但是每天生产数千台复印机,操作工人可能就会产生错觉,有风?没风?还是会产生装反的现象。
后来,就通过发掘员工潜能,在复印机旁边装一个小风车,如果装配正确就会有风,风车会转,因此只要风车会转,装配就是完好的,否则,就是错误的。
这样这家公司复印机的合格率就大大提高了。
02. 标准化与简单化改善前:出库部分拣集包组班组长日常管理无标准化的管理规范,班组长日常管理的关键管控点存在管控疏漏的情况,不利于班组成长。
改善后:建立规范的班组长时段化管控标准,将日常管理事务标准化,确保管理受控,同时提升班组长的管理能力。
03. 如何强化管理,目视化的改善某企业有一个开放式的大办公室,有200人在一起办公。
由于管理不到位,经常发生办公室的灯、空调没有关的现象。
精实生产零PPM不良的品质管理-品质保证观念的误解

UP
2
2.3 誤解三:通過抽樣檢查,就表示品質沒有問題了
良品
從一批貨中抽取一小部 分的物品,加以檢查,判定 不良的數量是否超過一規定 數量,來做為該批貨是否允 收的依據。 此檢驗手法只保證不良 率不會超過允收標準,並不 能保證物品皆為”良品”。 不良品
良品
3
2.4 誤解四:抽樣檢查是最經濟又能保證品質的方法
五 現 法
6
地 圖 法
五 問 法
比 較 法
放 大 法
解 剖 法
潛 水 法
2.7 誤解七:有了標準程序書,品質就有保障了
自從ISO要求產品品質管理體系,要符合一定的程序作法,並且要通過認證的 要求,許多公司也就努力導入這些程序作法,來表示品質保證的水準獲得認可。 其中最常看到的文書作業,就是”標準程序書”的制定。但常常流於形式, 而失去了意義。故現場的管理要能做到”透明化”及”目視化”。
市場競爭是多元化:
要比競爭對手做得
品 質
交 期
價 格
更
1
好
更
快
更
低
2.2 誤解二:加強檢查,可以確保品質
就保障客戶對品質的要求,以檢查的方式,當然有一定程度的幫助, 但是並不是最好的方式。而且,以人工檢查的方式,並不能百分之百防止不 良品流出公司,到客戶手中。 品質保證最好的策略,就是朝提升製程能力努力,達成”品質是製造出 來”的境界。真的沒辦法要做檢查的話,也要朝”自働檢查”的方向努力。
管制圖在一般工廠常有的現象有: 1) 管制圖繪了規格界線,卻沒有繪出管制界線 → 即認為製程穩定,無異常,不 知該採取哪些矯正措施。 2) 管制圖上出現了異常點,沒有採取任何矯正行動或是只採取補救行動,造成一 段時間後,異常點又再次發生,治標不治本。 3) 管制圖上資料量測精度不夠,造成資料波動起伏太大,無法偵測潛在問題的能 力。 *管制圖上的變化只為提供警訊,需要去找出真因,採取對策,才能使品質穩定。
精实生产零PPM不良的品质管理

疏失錯誤的真因
20% 技術能力不足造成 忘記了
不良
人為錯誤造成 做錯了 作業指示不完整 80% 指示方法欠週詳 3S不徹底 管理面不佳造成 作業方法不理想 製程能力不足 生產線布置不妥
人為疏失的類別
1.明知故犯型:不遵守規範,自行其事為傲。 2.認知錯誤型:彼此間認知有差別。 3.漫不經心型:注意力不集中或不用心理解。 4.混淆不清型:物件無法清晰分辨。 5.半生不熟型:工作技巧尚未熟練。 6.藝高膽大型:不依標準程序作業,而依其習慣工作。 7.無知犯錯型:缺乏訓練、缺乏知識而任意工作。 8.反應遲鈍型:反應太慢,無法立即接續工作。 9.指示不全型:指示的工作方法或程序不齊全與不週到。 10.意料之外型:遭遇意外狀況而驚慌失措,產生錯誤動作。
遵守作業標準與標準作業
作業標準 與 標準作業 是不同的
作業標準
規範個別工序之標準程序 規範人員、動線、機器佈置、 在製品數量的最佳組合之標準狀態 要依據目標的”產距時間”生產 不是某一工序過快或過慢生產 會造成生產條件一致性的變異
標準作業
產生不良的潛在因素
落實自主保全與預防保全
機器的保全之目的 減少機器故障時間 保持製程能力保障品質
發生防止: 1.排除化:根本上不使發生不良品。 2.代替化:利用自動元件設計機構防止人為疏失。 3.容易化:容易區別各物件,減少失誤。 波及防止: 4.異常檢出:發生異常時,機器設備與作業人員能立即知道並排除。 5.緩和影響:透過機器設備的機能連鎖或安全的連鎖機能使不良品數 量與嚴重程度能降到最低。
一般的保全二大領域
自主保全
由操作機器的作業人員自己做保全 日常點檢清掃 提早發覺異常跡象
預防保全
由操作機器的作業人員自己做保全 日常點檢清掃 提早發覺異常跡象
品质管理——三的原则
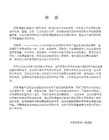
根据异常停机的原则,操作者自己检查发现不良时,要立即停机(线),并使用异常报警装置( ANDON ),呼叫支援者进行处理。使得不合格品绝对不可流到下一道工序。如果条件可行时应该在设备上建立 100% 的自动检查装置,代替操作者完成全数检查。在当今先进的科学技术发展水平,制作异常停止的自働化系统不是十分困难的事情,是完全可以做到的。
作为操作者一旦发现不良品,必须及时停机(线),将不良品在本工序截下,并且在本工序内完成处置和再发防止对策的建立。
3 .不接受不良品
后工序人员一旦发现不良,将立即在本工序实施停机(线),通知前工序。前工序人员需要马上停止加工,追查原因,采取对策。
基于以上现场品质控制的原则,精益生产管理确立了实现“零不良”的 11 个基本原则:
“三不放过原则”:异常原因不清不放过、责任不清不放过、预防措施不到位不放过;
精益生产塑造精益品质
精益生产管理对品质的认识可以归纳为一个核心,就是追求零 PPM (百万分之一) , 追求客户的 100% 的满足。以往谈到精益生产管理时往往偏重于介绍精益生产中对生产平准化、物流、看板、标准作业、 U 型生产线场地布局、多能工训练等方面的内容。但是实施精益生产的一个基本的前提是不能以牺牲安全和品质为代价去提升生产业绩。因此实施精益生产的核心前提必须保证提供客户满意的产品品质和追求零 PPM (百万分之),在整个组织,特别是告诫生产现场人员,如果出现百万分之一的不良意味着送到客户的手中就会带来 100% 的不良。
1 .全数检查的原则:所有零件所有工序无论采取什么形式都必须由操作着实施全数检查。精益生产认为抽样检验等于不检验,必须实施 100% 检验。这不是统计过程控制( SPC )的倒退,而是借助于统计过程控制的原理在工序(程)内检查的原则:品质是制造出来的,如果安排另外的检查人
精益生产-防错措施

重复的动作
定 义: 错 误
Mass
Lean Culture
程中有任 完 成 的制 当一个已 或缺 少 时 件 不 符合 何必要条
不良和错误是不相同的
不良 是 结果 不良 是 结果 错误 导致不良 错误 导致不良
Mass
Lean Culture
因 错误
果 不良
不良 与 错误
生产流程
Mass
Lean Culture
应用范围:
•防错措施适用于每一工作区域 •避免人员受伤 •提升工作的安全 •防止不良品产生 •避免机器损坏
Mass
Lean Culture
Mass
Lean Culture
防错法之理由
• 预防错误或预防错误造成不良 • 察觉不良然后实时停止,避免其它 不良流出工作站
Mass
Lean Culture
警告异常 建立标准的规范
Mass
Lean Culture
不良和错误的日常实例
Defect - Result
不良 – 果
Error - Cause
错 误 – 因
Burnt toast
烤焦的土司 空白页
Timer 定时器设定不当 improperly set Original placed 原稿放置不当 incorrectly Stamp out of 打印机墨水用完 ink
防错法制衡不良
Mass
Lean Culture
• 您在执行防错法之前需要完全了解错误与不良 之不同之界定
• 错误之发生是因设计或制造之工程与规格之间 变异。例如错误产生是因为作业未依照制程标 准及质量系统规范作业造成,错误可能因机器 或作业人员发生在制造过程中。
零PPM不良的品质管理

02
零ppm不良的目标与意义
ppm的涵义
ppm在品质管理中是一个常用的指 标,表示每百万单位中不良品的数量 。ppm值越低,表示产品的不良率 越低,品质越稳定。
ppm不仅用于衡量产品本身的品质, 还反映了生产过程中的控制和品质管 理水平。
详细描述
全面质量管理强调预防为主,强调持续改进,注重全员参与 和过程控制。它通过制定和实施质量方针和质量目标,以及 建立有效的质量管理体系,确保产品和服务的质量符合顾客 要求,并不断提高组织的竞争力和绩效。
品质保证(QA)
总结词
品质保证是一种管理手段,旨在通过一系列的检验、测试和评估活动,确保产品和服务的质量符合规定的要求。
零ppm不良的目标
零ppm不良的目标意味着在生产过程中追求完美,力求将不良率降至最低,甚至 达到零不良。
这一目标的实现需要从原材料、生产过程、检测环节等多方面进行严格控制和管 理。
ቤተ መጻሕፍቲ ባይዱ
零ppm不良的意义
提高产品质量
零ppm不良有助于提高产品的整体 质量,满足客户对产品品质的高要求。
增强企业竞争力
高品质的产品能够提升企业的市场竞 争力,赢得客户的信任和忠诚度。
详细描述
品质控制的核心是过程控制和数据分析,通过运用各种统计方法和工具,对生产过程中的关键工序进 行监控和调整,确保产品的质量和性能稳定。同时,品质控制还包括对生产过程中出现的不合格品的 处理和纠正措施的制定和实施。
预防性品质管理
总结词
预防性品质管理是一种管理理念,旨在 通过识别和消除潜在的质量问题,预防 不良品的产生,从而降低质量成本和提 高产品质量。
如何做到品质零PPM(百万分之一)缺陷率?实例理论讲解

如何做到品质零PPM(百万分之一)缺陷率?实例理论讲解导读提起精益生产管理,人们或许有些陌生,何为精益生产管理?精益生产管理就是对品质追求零PPM(百万分之一)的缺陷率,追求客户100%的满意。
那么如何做到?小编从实例出发,为大家分析。
某企业的生产车间接到任务,要生产一组产品,需要经过铣、钻、磨、装配和打包等多道工序,每周生产3200件。
所有这些产品的加工过程相似,需要的工人相同。
该企业每周工作5天,每天工作8小时。
生产指定产品每道工序的单位加工时间。
该生产单元按照工艺专业化布置。
尽管这些产品具有一定的相似性,不需要大量的生产准备时间,但是因为加工次序和优先级别不同,使生产很难达到应有的顺畅程度,生产拖拖沓沓,有时还需要推迟交货时间,经常需要工人加班加点才能完成生产任务,不但使生产成本提高,并且顾客对推迟交货的意见很大。
这家企业决定对该生产单元进行精益化改造,以彻底改变目前生产拖沓、效率低下的状况。
经过大量调查,发现铁、钻、磨床尚有剩余生产能力,因此在不影响车间内其他产品生产的条件下,可以对这些设备进行适当调整,安排到一个生产单元内。
此外,所有的装配线和包装依靠手工完成,只需要提供一些台子和某些工具就可以完成。
计算单件产品生产时间(Takt Time),取两个工作台,尚有生产能力剩余,产品加工包括铣、钻、磨三道工序。
因为这几道工序的加工时间有长有短,为了保证按照连续流程生产,必须平衡各道工序的劳动利用程度,提高劳动生产率,因而可以在生产车间内设置一个微型加工单元,把铣、钻、磨这三道工序有机地组合起来,并且只要一个工人就可以独立完成这三项操作。
完成铣、钻、磨这三道工序所需的加工时间为170s。
因此,每小时可以完成21.2单位的产品,并且只需4个工作台。
计算过单件产品生产时间和完成指定生产任务所需的工作台后,便可以开始规划精益生产单元的布置。
在实际设计生产精益生产单元时,可以考虑设置两个铣、钻、磨加工区,每个加工区由两个工作台组成,每个工作台配备一名工人。
- 1、下载文档前请自行甄别文档内容的完整性,平台不提供额外的编辑、内容补充、找答案等附加服务。
- 2、"仅部分预览"的文档,不可在线预览部分如存在完整性等问题,可反馈申请退款(可完整预览的文档不适用该条件!)。
- 3、如文档侵犯您的权益,请联系客服反馈,我们会尽快为您处理(人工客服工作时间:9:00-18:30)。
減少不良的改善過程
步驟一 步驟二 步驟三 主題選定 目標設定 現況調查
‧確定主題名稱,改善範圍
‧上級方針‧客戶要求‧競爭對手‧自我挑戰
‧掌握五現原則
不良模式帕拉圖 選定A類為改善對象
A類項目再細分底層項目
步驟四 步驟五 步驟六 步驟七 步驟八
真因造查 對策試行 效果確認 標準維持 水平展開
‧尋找真因七手法 ‧穩定製程三要領‧防錯法十大原理 ‧管理面配套措施 ‧推移圖‧改善成果表 ‧作業重點書‧人為疏失表 ‧目視管理板‧每日一課 ‧推廣計畫
防錯實例
防錯實例
謝謝各位!ຫໍສະໝຸດ