MSA计算
数型MSA方法介绍

数型MSA方法介绍(第三版)Part I: 总则1. 概述评价人在重复检测合格与不合格零件时的有效性或能力。
评价人拒收合格零件或接受不合格零件的风险有多大。
当评估再现性时,可以比较不同评价人的有效性。
2.概念A. 有效性(E)准确检测合格与不合格零件的能力它介于0到1之间,1是最完美的。
计算公式如下:E=正确识别的零件数/正确数量的总机会数正确数量的总机会数=零件数和每个零件被测次数的乘积。
例如:10个零件各测3次,则正确数量的总机会数将为3x10=30B. 漏报概率(Probability of a Miss)Pmiss指接收不合格零件的机会——非常严重的错误。
计算公式:Pmiss=漏报数量/不合格零件机会总数不合格零件机会总数=研究中所用的不合格零件与每个零件被测次数的乘积。
例如:5个不合格零件各测3次,则不合格零件机会总数将为3x5=15C.误报概率Pfa (Probability of a false alarm)指拒收合格零件的机会——造成不必要的返工和重检若Pfa过大,大量的成本将浪费于返工和重检。
Pfa=误报数量/合格零件机会总数合格零件机会总数=所用的合格零件与每个零件被测次数的乘积。
例如:6个合格零件各测3次,则合格零件机会总数将为3x 6=18D. 偏倚是Pmiss和Pfa的函数B >= 0B=Pfa/PmissB<1 偏倚倾向于接受零件(Pfa < Pmiss)B=1 无偏倚(Pfa = Pmiss)B>1 偏倚倾向于拒收零件(Pfa > Pmiss)3.具体收集数据的方法从过程中抽取50个零件样本,以获得覆盖过程范围的零件。
真值已知3名评价人,每人对每个零件测3次接受(合格) ——1 拒绝(不合格) —— 0经验:特别选择—并非随机选择能判别合格或不合格的零件。
所选零件数参见下表:——选1/3合格,1/3不合格,1/3边缘产品(marginal)边缘产品:又可细分为,合格边缘和不合格边缘产品。
【精品文档】msa计算范例-范文word版 (7页)
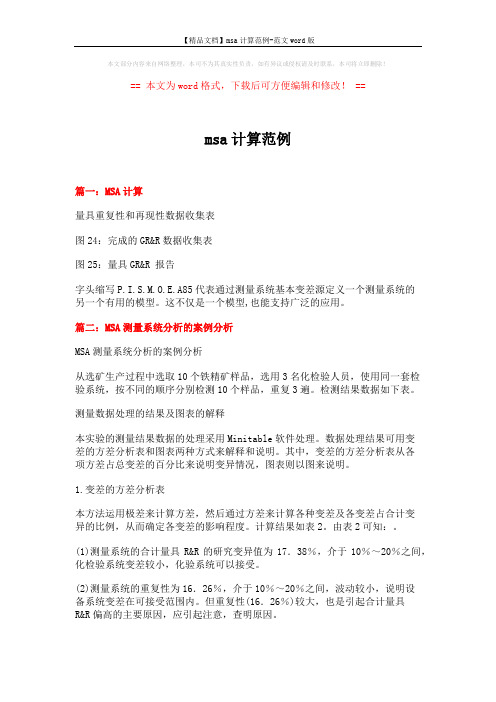
本文部分内容来自网络整理,本司不为其真实性负责,如有异议或侵权请及时联系,本司将立即删除!== 本文为word格式,下载后可方便编辑和修改! ==msa计算范例篇一:MSA计算量具重复性和再现性数据收集表图24:完成的GR&R数据收集表图25:量具GR&R 报告字头缩写P.I.S.M.O.E.A85代表通过测量系统基本变差源定义一个测量系统的另一个有用的模型。
这不仅是一个模型,也能支持广泛的应用。
篇二:MSA测量系统分析的案例分析MSA测量系统分析的案例分析从选矿生产过程中选取10个铁精矿样品,选用3名化检验人员,使用同一套检验系统,按不同的顺序分别检测10个样品,重复3遍。
检测结果数据如下表。
测量数据处理的结果及图表的解释本实验的测量结果数据的处理采用Minitable软件处理。
数据处理结果可用变差的方差分析表和图表两种方式来解释和说明。
其中,变差的方差分析表从各项方差占总变差的百分比来说明变异情况,图表则以图来说明。
1.变差的方差分析表本方法运用极差来计算方差,然后通过方差来计算各种变差及各变差占合计变异的比例,从而确定各变差的影响程度。
计算结果如表2。
由表2可知:。
(1)测量系统的合计量具R&R的研究变异值为17.38%,介于10%~20%之间,化检验系统变差较小,化验系统可以接受。
(2)测量系统的重复性为16.26%,介于10%~20%之间,波动较小,说明设备系统变差在可接受范围内。
但重复性(16.26%)较大,也是引起合计量具R&R偏高的主要原因,应引起注意,查明原因。
(3)测量系统的再现性和检验人员的变异都为6.15%,小于10%,说明检验人员间的变差波动很小。
化检验人员操作一致性较好。
(4)样品间的变异值为98.48%,变异显著,检验系统明显表示出样品间的品质差异。
(5)区别分类数(ndc)为7,大于5。
因此,化验系统能够满足测量的需要。
2.图表结果图表以较直观的方式来说明检验情况,并可以看出较细微的差异:(1)各变异分量各变异分量情况由图1显示,从图1可以看出样品间的变异是变异的主要来源,系统能够区分试样品位的变化。
MSA计算公式范文

MSA计算公式范文
MSA(Mean Shift Algorithm)是一种无参数的非监督学习算法,用
于对数据进行聚类。
该算法采用核密度估计的方法,通过不断移动数据点
的位置来寻找数据点密度最大的位置,最终将密度相近的数据点聚集在一起。
MSA的计算公式可以分为两个部分:核密度估计和均值漂移。
下面将
详细介绍这两个部分的计算公式。
1.核密度估计
核密度估计用于估计数据点周围的密度。
常用的核函数有高斯核函数、Epanechnikov核函数等。
核密度估计的计算公式如下:
其中,x是待估计密度的点,xi是数据点集中的其中一个点,K是核
函数,h是带宽参数,·,表示绝对值。
2.均值漂移
均值漂移是通过迭代计算来不断移动数据点的位置,直到达到最大密
度位置为止。
每次迭代时,计算数据点在核密度估计函数上的梯度,然后
根据梯度方向移动数据点。
均值漂移的计算公式如下:
其中,x表示当前数据点,qi表示移动后的数据点,N(x)表示以x为
中心,半径为h的所有数据点。
在每次迭代中,移动数据点的位置可以通过以下公式计算:
其中,x表示当前数据点,q(x)表示数据点在当前位置的均值漂移位置,n表示数据点的个数。
通过不断迭代计算,均值漂移算法会将密度相近的数据点聚集在一起。
总结起来,MSA的计算公式包括核密度估计和均值漂移两个部分,前
者用于估计数据点的密度,后者用于不断移动数据点的位置,直到达到最
大密度位置。
这种迭代的方式能够有效地将密度相近的数据点聚集在一起,实现聚类效果。
MSA计算公式.pdf

#DIV/0!
15
极差Rc 0.00 0.00
0.00
0.00 0.00 0.00 0.00 0.00 0.00 0.00
Rc
0.0000
16
零件均值 X 0.000 0.000 0.000 0.000 0.000 0.000 0.000 0.000 0.000 0.000
X
0.0000
Rp XMax - XMin 0.0000
再现性-评价人变差(AV)
重复性和再现性 (GRR 或 R&R)零件变差 零件数量 2
3
AV
[ XDIFF
K
2
2
EV2
/nr]
R& R
EV2 AV 2
#DIV/0! PV=RP×K3
K3
0.7071 0.5231
评价人数 K2
#DIV/0!
0.0000
2
0.7071 0.0000 总变差(TV)
#DIV/0!
分级数
这个分级数就是覆盖预期的产品变差所用不重叠的97%置信区间的数量
ndc=1.41(PV/R&R)
#DIV/0!
ndc取整,且应该大于等于5
控制限计算
极差上限
UCLR= R*D4
2次测量时D4=3.27;3次测量时D4=2.58
极差下限
UCLR= R*D3
试验少于7次时,D3=0,下控制限为0
7 0.19 0.19 0.19 0.189 0.00 0.19 0.19 0.19 0.190 0.00 0.19 0.19 0.19 0.190 0.00 0.190
05
极差 Ra 0.00 0.00
0.00
MSA计算说明

量具重复性与再现性说明
一、重复性:
重复性又称量具变异,是指用同一种量具,同一位作业者,多次测量相同
零件之指定特性时所得之变异。
⒈EV
:重复性。
⒉R :所有作业者执行多次量测之变异平均值。
⒊K 1:重复性系数,与量测次数有关。
⒋TV :全变异。
⒌R &R :重复性与再现性变异。
⒍PV :零件变异。
二、再现性:
再现性又称作业者变异,是指不同作业者以相同量具量测相同零件之特性时,量测平均值之变异。
⒈AV :再现性。
⒉X DIFF :不同作业者所量测之平均值之最大值与最小值之变异。
⒊K 2:再现性系数,与作业人数有关。
⒋TV :全变异。
⒌n :被量测零件数目。
⒍r :每位作业者量测次数。
一、重复性>再现性:⒈量测仪器需加以保养。
⒉产品之变异出现异常。
⒊量具之夹紧或定位不一致。
二、再现性>重复性:⒈量具之校正未落实。
⒉作业者对量具使用不熟。
⒊可能需要辅助仪器协助作业者使用。
MSA计算公式范文
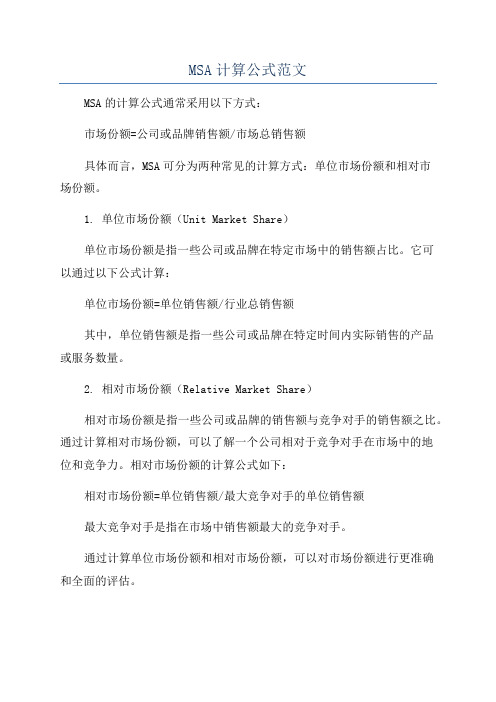
MSA计算公式范文MSA的计算公式通常采用以下方式:市场份额=公司或品牌销售额/市场总销售额具体而言,MSA可分为两种常见的计算方式:单位市场份额和相对市场份额。
1. 单位市场份额(Unit Market Share)单位市场份额是指一些公司或品牌在特定市场中的销售额占比。
它可以通过以下公式计算:单位市场份额=单位销售额/行业总销售额其中,单位销售额是指一些公司或品牌在特定时间内实际销售的产品或服务数量。
2. 相对市场份额(Relative Market Share)相对市场份额是指一些公司或品牌的销售额与竞争对手的销售额之比。
通过计算相对市场份额,可以了解一个公司相对于竞争对手在市场中的地位和竞争力。
相对市场份额的计算公式如下:相对市场份额=单位销售额/最大竞争对手的单位销售额最大竞争对手是指在市场中销售额最大的竞争对手。
通过计算单位市场份额和相对市场份额,可以对市场份额进行更准确和全面的评估。
除了以上两种常见的计算方式,还有其他一些与MSA相关的公式,例如市场覆盖率(Market Coverage)和增长率(Growth Rate)等。
市场覆盖率是指一些公司或品牌的销售额占整个市场总销售额的百分比。
市场覆盖率=单位销售额/行业总销售额增长率是指一些公司或品牌在特定时间内销售额的增长情况。
增长率=(当前销售额-前期销售额)/前期销售额×100通过计算增长率,可以了解一个公司或品牌的销售额增长速度。
MSA的计算公式可以帮助企业评估自身在市场中的地位和竞争力,并与竞争对手进行比较。
通过分析市场份额,企业可以制定更有效的市场战略,提高销售额和市场占有率。
然而,需要注意的是,MSA只是估算市场份额的一种方式,对于具体的市场状况和竞争环境,还需要进行深入的市场调研和分析。
MSA_计算公式

MSA_计算公式MSA(Mean Shift Algorithm)是一种非参数的聚类算法,主要用于数据点的聚类和密度估计。
它的计算公式是基于核密度估计和梯度上升的思想,通过迭代寻找数据点的局部最大密度区域,从而得到聚类结果。
1.数据点密度估计:对于给定的数据集,首先需要进行数据点的密度估计。
常用的方法是使用高斯核函数,计算每个数据点与其邻域内其他数据点的距离,并将距离作为权重计算密度。
具体公式如下:\[k(x_i, x_j) = \exp \left( -\frac{{\,x_i - x_j\,^2}}{{2h^2}} \right)\]其中,\(x_i\)和\(x_j\)是数据集中的两个数据点,\(h\)是高斯核函数的带宽。
2.梯度上升迭代:在数据点的密度估计完成后,需要进行梯度上升的迭代过程,找到局部最大密度区域。
具体公式如下:\[m(x) = \frac{\sum_{i=1}^{n} k(x, x_i) \cdotx_i}{\sum_{i=1}^{n} k(x, x_i)} - x\]其中,\(m(x)\)表示数据点\(x\)的梯度向量,\(k(x,x_i)\)表示数据点\(x\)与数据点\(x_i\)之间的权重,\(n\)表示数据集中的数据点数量。
3.密度最大化:通过迭代计算梯度向量,将数据点移动到局部最大密度区域。
具体公式如下:\[x_{t+1}=m(x_t)+x_t\]其中,\(x_{t+1}\)表示迭代后的数据点位置,\(x_t\)表示迭代前的数据点位置。
4.聚类结果:在迭代过程中,如果两个数据点的位置足够接近,则认为它们属于同一个聚类。
可以使用距离阈值来判断两个数据点是否属于同一个聚类。
MSA算法的优点是不需要预先指定聚类数量,且对于数据集的分布形状没有假设。
但是,该算法的计算复杂度较高,对数据点的数量和维度敏感。
因此,在实际应用中需要考虑算法的效率和可扩展性。
总结起来,MSA算法的计算公式主要包括数据点密度估计、梯度上升迭代、密度最大化和聚类结果。
MSA重复性再现性讲解及分析公式

分析方法
预实施 1、分析员要事先对所有零件进行编号并标识测量 点,对于给定特征有多个测量点时,为避免零件 内部偏差的影响,要确定其中一个作为测量点。 2、所选用的检查员一定是在测量仪器(设备) 使用方面经过培训的熟练的人员。 3、如果可能的话,每次试验前应对测量仪器 (设备)进行校准。
分析方法
4.97 4.98 0.03 5.05 5.04 5.03 0.02 4.98 5.02 4.99 0.04 4.98 4.97 4.96 0.02 5.01
4.97 4.98 0.03 4.97 4.98 5.01 0.04 4.97
5.04 5.05 0.02 5.02 5.03 5.04 0.02 4.96
XC3 XC31
XC22 XC23
XC32 XC33
XC24
XC34
XC25
XC35
XC26
XC36
XC27
XC37
XC28
XC38
XC29
XC39
XC2A
XC3A
XCbar
RC RC1 RC2 RC3
RC4
RC5 RC6 RC7 RC8 RC9 RCA RCbar
分析方法
计算公式 XAbar=(XA11+ XA12 +…+ XA3A)/30 XBbar=(XB11+ XB12 +…+ XB3A)/30 XCbar=(XC11+ XC12 +…+ XC3A)/30 Xbardiff=MAX(XAbar, XBbar, XCbar )-MIN (XAbar, XBbar, XCbar ) RAbar=(RA1 + RA2 + …+RAA )/10 RBbar=(RB1 + RB2 + …+RBB )/10 RCbar=(RC1 + RC2 + …+RCC )/10 Rbar=(RAbar + RBbar + RCbar ) /3
- 1、下载文档前请自行甄别文档内容的完整性,平台不提供额外的编辑、内容补充、找答案等附加服务。
- 2、"仅部分预览"的文档,不可在线预览部分如存在完整性等问题,可反馈申请退款(可完整预览的文档不适用该条件!)。
- 3、如文档侵犯您的权益,请联系客服反馈,我们会尽快为您处理(人工客服工作时间:9:00-18:30)。
%EV = 100[EV/TV] = 100[ =
17.62
0.20188 1.14610
/
]
%
再现性—设备变差(AV)
AV
= √(XDIFF×K2) 2 -(EV2/(nr) ) = √(0.4446×0.523) 2-(0.201882/(10×3) ) =
0.22963 r = 实验次数 评价人 K2 2 0.7071 3 0.5231
%GRR
= 100[GRR/TV] = 100[ =
26.68
0.30575 1.14610
/
]
%
零件变差(PV) PV = RP ×K3 1.10456 = 1.10456 =
×
4 5 6 7
%PV
= 100[PV/TV] = 100[ =
96.38
1.1045 1.14610
/
]
%
PV
总变差(TV) TV
0.880 0.42 1.099
0.150 0.09 0.367
-1.327 0.39 -1.064
-0.483 0.38 -0.186
0.080 0.20 0.454
-0.503 0.10 -0.342
1.697 0.42 1.940
-1.807 0.67 -1.571
X= ([R a= 0.184] + [R b=0.513] + [ R c=0.328 ]) / [#评价人个数= 3] = [MaxX =0.1903] - [MinX= -0.2543] = XDIFF = 0.446 • [R=0.3417]*[D4 =2.5 8 ]= UCLR = 0.8816 •
量具重复性和再现性数据收集表
评价人/试验# 1 A 2 3 均值 极差 B 2 3 均值 极差 C 2 3 1 0.04 -0.11 -0.15 -1.38 -1.13 -0.96 0.88 1.09 0.67 0.14 0.20 0.11 -1.46 -1.07 -1.45 1 0.08 0.25 0.07 -0.47 -1.22 -0.68 1.19 0.94 1.34 0.01 1.03 0.2 -0.56 -1.20 -1.28 1 0.29 0.41 0.64 2 -0.56 -0.68 -0.58 3 1.34 1.17 1.27 4 0.47 0.5 0.64 5 -0.8 -0.92 -0.84
图 24:完成的 GR&R 数据收集表
评价人/试验# 1 A 1 2 3 均值 极差 B 2 3 均值 极差 C 1 2 3 均值 极差 零件均值 1 0.29 0.41 0.64 0.447 0.35 0.08 0.25 0.07 0.133 0.18 0.04 -0.11 -0.15 2 -0.56 -0.68 -0.58 -0.607 0.12 -0.47 -1.22 -0.68 -0.790 0.75 -1.38 -1.13 -0.96 3 1.34 1.17 1.27 1.260 0.17 1.19 0.94 1.34 1.157 0.40 0.88 1.09 0.67 4 0.47 0.5 0.64 0.537 0.17 0.01 1.03 0.2 0.413 1.02 0.14 0.20 0.11 5 -0.8 -0.92 -0.84 -0.853 0.12 -0.56 -1.20 -1.28 -1.013 0.72 -1.46 -1.07 -1.45 零件 6 0.02 -0.11 -0.21 -0.100 0.23 -0.2 0.22 0.06 0.027 0.42 -0.29 -0.67 -1.49 7 0.59 0.75 0.66 0.667 0.16 0.47 0.55 0.83 0.617 0.36 0.02 0.01 0.21 8 -0.31 -0.20 -0.17 -0.227 0.14 -0.63 0.08 -0.34 -0.297 0.71 -0.46 -0.56 -0.49 9 2.26 1.99 2.01 2.087 0.27 1.80 2.12 2.19 2.037 0.39 1.77 1.45 1.87 10 -1.36 -1.25 -1.31 -1.307 0.11 -1.68 -1.62 -1.50 -1.600 0.18 -1.49 -1.77 -2.16
岗位培训、口述、作业指导书、控制计划、检验计划、 如何做
标准操作程序 (S.O.P) , 通常口头, 文件化 S.O.P 、 DCC
= √GRR 2 + PV 2 =√(0.30575 +1.10456 ) =
1.14610
2 2
8 9 10
ndc
= 1.41( =
= 1.41(
1.10456 0.30575
/GRR) /
5.094---5
)
表中所有的有关理论和常数的资料参见 MSA 参考手册第三版
字头缩写 P.I.S.M.O.E.A85 代表通过测量系统基本变差源定义一个测量系统的另 一个有用的模型。这不仅是一个模型,也能支持广泛的应用。 误差源 P I S M O E A 零件 仪器 标准 方法 操作者 环境 假设 别名或分量 生产件、样本、被测体、测试单元(UUT) ,人工制 品、检查标准 量具、M&TE 单元、主量具、测量机器、试验台 刻度、基准、人工制品、检查标准、固有的标准、一 致意见、标准基准材料(SRM) 、等级、接受准则 试验程序、零件程序 评价人、校准或试验技师、评估人、检查员 动力、电磁干扰(EMI) 、噪声、时间、空气 统计的、操作的、校准、常数、手册值、热稳定、弹 性模数、科学定律 *实际或物理真值未知 误差源 P I S M O E A 目的 典型生产,汽车 MSA 随机生产件,整个过程范围 单一型生产量具 比例、主标准或分级;符合“ 10 比 1”法则 也可以文件化;控制计划 (2-3)典型的,经过培训过的、 通常操作人员 稳定生产和操作条件 统计的、经常忽略 过程控制(SPC) 自动在线或试验台 检查标准、人工样品 DCC CMM、试验台 比例和几何、参考试 验标准 程序或自动试验循环 严格试验的操作者、 专业培训和技能 经常控制 统计的、具体应用 产品控制, 100%检验 校准 测体 主量个和设备 标准样品、基准、固有 的或一致的、人工样品 文件化的、正式校准程 序 合格技师、ISO17025 内 行证据 控制限、优化的,一个 主要误差源 不能假设的,一种主要 误差源 产品控制,校准公差 生产单元、 试验样本、 量具、UUT、试样、被 准则、常数或可靠测量 的假设 谁来做 温度、湿度、浓度、现场清洁、照明、位置、振动、 测量条件、噪声 比较方法 作为真值接受的已知 值、基准值或接受准则 因子或参数 未知
零件 6 0.02 -0.11 -0.21 7 0.59 0.75 0.66 8 -0.31 -0.20 -0.17 9 2.26 1.99 2.01 10 -1.36 -1.25 -1.31
平均值
X a= R a=
-0.2 0.22 0.06 0.47 0.55 0.83 -0.63 0.08 -0.34 1.80 2.12 2.19 -1.68 -1.62 -1.50
当试验次数为 2 次时 D4=3.27, 3 次时 D4=2.58。 UCLR 表示 R 的界限。圈出那些超出界限的值,了解原因并纠正。 用原来相同的评价人和仪器对同一个零件重复原来的测量,, 或剔除这些值并由其余观测值再次平均并计算 R 和 UCLR 值。
图 25:量具 GR&R 报告 量具重复性和再现性报告
平均值 0.1 0.1 0.2 X a= R a= 0.19 0.1 0.0 0.1 0.0 X b= R b= 0.06 0.5 -0.2 -0.2 -0.2 X c = -0.25 R c= 0.3 Rp= 0.00 3.5 R= 0.34
0.073 0.19 0.169
-1.157 0.42 -0.851
]) / [评价人 = ] =
R=
X DIFE = [MaxX = *UCLR =[R= *UCLR =[R=
]×[D4 = ]×[D4 =
*2 次试验 D4=3.27,3 次试验 D4=2.58。UCLR 代表了单个极差的控制限。将那些超出控制
限的点圈出,识别原因并纠正。使用与开始时相同的评价人及单位重复这些读数,或除去 某些值并从保留的观察值重新获得平均值,重新计算极差 R。
零件号和名称: 特性: 规范: 量具名称: 量具号: 量具类型: 日期: 完成人:
R = 0.3417
X DIFF =0.4446
R P = 3.511
% 总变差 (TV)
测量单元分析 重复性—设备变差(EV)
EV
= R × K1 = =
0.3417 × 0.20188
0.5ห้องสมุดไป่ตู้08
试验 K1 2 0.8862 3 0.5908
X b= R b=
-0.29 -0.67 -1.49 0.02 0.01 0.21 -0.46 -0.56 -0.49 1.77 1.45 1.87 -1.49 -1.77 -2.16
均值 极差 零件均值 X=
X c= R c= R p=
R= ([R a=
] + [R b= ]
—
] + [ R c= [MinX = ]= ]= ]=
%AV
= 100[AV/TV] = 100[ =
20.04
0.22963 1.14610
/
]
%
n = 零件数
重复性和再现性(GRR) GRR
= √ EV 2 + AV 2 =√(0.20188 +0.22963 ) =
0.30575
2 2
零件 2 3
K3 0.7071 0.5231 0.4467 0.4030 0.3742 0.3534 0.3375 0.3249 0.3146