Chemical Pulping
造纸词汇缩写

……………………………………………造纸词汇缩写APP Alkali peroxide pulp 碱性过氧化氢纸浆BCTMP Bleached chemi-thermomechanical pulp 漂白化学热磨机械浆CMP Chemi-mechanical pulp 化学机械浆CTMP Chemi-thermomechanical pulp 化学热磨机械浆DIP Deinked pulp 脱墨废纸浆DKP Deinked kraft pulp 脱墨牛皮废纸浆DLK Double – line clippings 双边切边浆FBB Folding boxboard 折叠纸盒纸板FBK Fully-bleached kraft 全漂牛皮纸浆HW Hardwood 硬木(阔叶木)ISO International Standards Organisation 国际标准组织MF Machine finished 纸机整饰MG Machine glazed 纸机光泽MOW Mixed office waste 混合办公废纸NSSC Neutral sulfite semi-chemical pulping 中性亚硫酸盐半化学制浆OCC Old corrugated containers 旧瓦楞纸箱(旧包装纸箱)OMG Old magazine 旧杂志ONP Old newspaper 旧报纸PE Polyethylene 聚乙烯PGW Pressurized groundwood 压力磨木浆RMP Refiner mechanical pulp 木片磨木桨SBB Solid bleached board 单一漂白木桨纸板SBK Solid bleached Kraft 单一漂白牛皮桨纸板SGW Stone groundwood 磨石磨木桨SUB Solid unbleached board 单一未漂桨纸板SW Softwood 软木(针叶木)TMP Thermomechanical pulp 热磨机械桨UBB Unbleached board 未漂纸板UBK Unbleached kraft 未漂牛皮桨WLC White-line chipboard 漂白挂面粗纸板Sack kraft: 牛皮纸袋纸由硫酸盐桨生产的纸,绝大多数是未漂的,也可用回收的OCC及DLK生产。
造纸工艺四个流程

造纸工艺四个流程The art of papermaking is a captivating journey, transforming humble raw materials into the versatile medium that underpins our communication, creativity, and record-keeping. It's a process that has evolved over centuries, blending ancient techniques with modern innovations. Let's delve into the four fundamental stages of this remarkable transformation. The first stage, pulping, is where the magic begins. Imagine a swirling vortex of fibers, extracted from wood, bamboo, or recycled paper. These fibers, the very essence of paper, are liberated from their rigid structures through mechanical or chemical means. Mechanical pulping, a brute force approach, grinds wood into a fibrous slurry, while chemical pulping employsa more refined approach, dissolving lignin, the glue-like substance that binds wood fibers, leaving behind pure cellulose. The resulting pulp, a milky suspension, holds the promise of countless sheets of paper. Next comes the stage of preparation, where the pulp undergoes a metamorphosis, tailored to its intended purpose. Picture a carefully orchestrated ballet of additives, each playing a crucial role in shaping the final product. Fillers, like clay or calcium carbonate, are introduced to enhance opacity and smoothness. Sizing agents, such as starch or rosin, impart water resistance, preventing ink from feathering and bleeding. Pigments, the artists of the paper world, infuse the pulp with color, transforming it from a blank canvas into a vibrant palette. This meticulous preparation ensures that the paper meets the demands of its intended application, whether it's a delicate watercolor sheet or a sturdy cardboard box. With the pulp primed and ready, the stage is set for the heart of the papermaking process: sheet formation. Imagine a continuous flow of pulp, cascading onto a moving wire mesh, like a waterfall meeting a delicate sieve. As water drains away, the fibers intertwine, forming a fragile web, the nascent sheet of paper. This intricate dance of water and fiber is a marvel of physics and engineering, a testament to human ingenuity. The sheet, still damp and delicate, embarks on a journey through a series of rollers, where it is pressed, smoothed, and compacted, gaining strength and resilience. Finally, the culmination of this transformative journey, the drying stage, imbues the paper with its final character. Imagine a gentle warmth enveloping the moist sheet, coaxing away the remaining moisture. The paper, now acohesive entity, glides through a labyrinth of heated rollers, emerging as a smooth, dry surface, ready to receive the imprint of words, images, and ideas.This final touch, the culmination of meticulous preparation and skillful execution, completes the metamorphosis, transforming a humble slurry of fibers into the versatile medium we know as paper. The four stages of papermaking, pulping, preparation, sheet formation, and drying, are a testament to human ingenuity and our enduring fascination with transforming raw materials into objects of utility and beauty. Each stage, a delicate dance of physics, chemistry, and engineering, contributes to the creation of a material that has shaped civilizations, fueled creativity, and preserved knowledge for millennia. As we hold a sheet of paper, we hold a piece of history, a testament to the enduring power of human innovation.。
化学法制浆流程

化学法制浆流程The chemical pulping process, also known as the Kraft process, is an important method for turning wood into pulp for paper production. This process involves several key steps, including wood preparation, cooking, washing, bleaching, and recovery. 化学制浆工艺也被称为Kraft工艺,是将木材制成纸浆的重要方法。
这个过程包括木材准备、烹饪、洗涤、漂白和回收等几个关键步骤。
One of the first steps in the chemical pulping process is wood preparation, which involves debarking the wood and chipping it into small pieces. These wood chips are then mixed with a mixture of chemicals and water to form what is known as "white liquor." 化学制浆过程中的一个最初步骤是木材的准备,包括去皮和将木材切割成小块。
然后将这些木屑与化学品和水混合在一起,形成所谓的“白液”。
Next, the wood chips are cooked in a large vessel known as a digester. During this process, the white liquor breaks down the lignin in the wood, separating the cellulose fibers and other components to create a slurry of pulp. 接下来,木屑在被称为蒸化器的大容器中进行烹饪。
纸业专业英语词汇翻译(S2)

纸业专业英语词汇翻译(S2)纸业专业英语词汇翻译(S2)纸业专业英语词汇翻译(S2)spark recording paper 电火花记录纸special book paper 盲人书籍纸special impregnating paper 胶膜纸specialty paper 特种纸spinning paper 纸绳纸split color paper 单一颜色纸张sponge paper 海绵状纸spool parchment paper 红羊皮纸spot carbonized paper 局部炭粉涂布纸spot crown paper 饮用麦管用纸square paper 方格纸square rule paper 方格纸stabilization process paper 稳定处理照相纸stabilized paper 调湿纸stained paper 压光机染色的纸张stamp paper 邮票纸stamped paper 印花票用纸standard cover paper 标准封面纸starch paper 淀粉试纸stay paper 箱角补强纸steel engraver's paper 钢凹版印刷纸steel engraving paper 钢凹版印纸刷steel plate paper 板压光泽纸stencil paper 誊写蜡纸stenotype paper 速记打字用纸stereo (type) paper 铅字铸模纸sterilisable paper 杀菌纸sticky fly paper 灭绳纸stratified paper 层压纸straw paper 草浆纸stretchable paper 伸性纸strip chart paper 刻度记录纸带strip film paper 醋酸纤维素涂布感光纸styrene paper 聚苯乙烯合成纸sugar paper 包糖纸sulfate paper 牛皮纸sulfite paper 亚硫酸盐浆袋纸sulphate paper 牛皮纸sulphite paper 亚硫酸盐浆纸supercalendered paper 超级压光处理的纸张supplement paper 增刊用纸;附页用纸surface coated paper 表面涂布纸;表面涂料纸surface sized paper 表面施胶纸surfaced paper 光泽纸surgicak dressubg paper 外科医疗用纸,外科绷带synthetic paper 合成纸synthetic fiber paper 合杨纤维纸salt removal process 碱回收脱盐法sappi process sappi氧气漂白sca-billerud process sca-billerud亚硫酸钠废液回收法self-regulating process 自动调节过程semi-chemical process 半化学浆制造法simon-cusi process simon-cusi蔗渣制浆法sivola process sivola两级蒸煮soda process 烧碱法(制浆),苏打法(制浆)soda-anthraquinone process 蒽醌烧碱法制浆soda-aq process 蒽醌烧碱法制浆solvay process solvay甲醇法制备二氧化氯sonoco sulfite recovery process sonoco(亚硫酸盐废液)铝酸钠回收法sprout-waldron process s.w.冷碱法制浆steam stripping process 汽提法(除臭)stone process 磨石磨木浆法stora process stora两级蒸煮stora-brite process s.b.亚硫酸钠半化学浆的制备sulfate process 硫酸盐法(制浆)sulfite process 亚硫酸盐法(制浆)sulfite recycle process (亚硫酸钠废液)硫化物循环回收法sveen (glue) process 纤维飘浮回收法semichemical pulping 半化学浆法制浆sivola pulping sivola法两级蒸煮soda pulping 烧碱法制浆,苏打法制浆soda additive pulping 带添加剂烧碱法制浆soda-anthraquinone pulping 蒽醌苏打法制浆soda-aq pulping 蒽醌烧碱法制浆soda-oxygen pulping 氧碱法制浆sodium base bisulfite pulping 亚硫酸钠法制浆solvent pulping 溶剂法制浆stora pulping stora两级蒸煮sulfate pulping 硫酸盐法制浆sulfite pulping 亚硫酸盐法制浆sawdust pulp 木屑浆,锯末浆sereened pulp 筛后浆料semi-bleached pulp 半漂浆semi-chemical pulp 半化学浆semi neutral pulp 中性盐半化学浆sheet pulp 浆板shiny pulp 粘状浆short fibered pulp 短纤维浆sisal pulp 波罗麻浆,西沙罗麻浆slime pulp 腐浆slow (draining) pulp 粘状浆slurry pulp 纸浆悬浮液slush pulp 液体浆soda pulp 浇碱法纸浆,苏打浆soda-anthraquinone pulp 蒽醌烧碱法纸浆soda-aq pulp 蒽醌烧碱法纸浆soda-chlorine pulp 碱氯法纸浆soft pulp 软浆softwood pulp 针叶木浆spoelalty pulp 特种浆spinning pulp 人造丝浆steamed pulp 褐色磨木浆strained pulp 筛后浆料straw pulp 草浆strong pulp 高强度纸浆sulfate pulp 硫酸盐浆sulfite pulp 亚硫酸盐浆synthetic pulp 合成浆sabai grass 印度草saccharic acid 糖(二)酸saccharide 糖类saccharification 糖化作用,糖化水解saccharin(e) 糖精saccharinic acid 变糖酸,糖精酸saccharolytic 变糖的saccharose 蔗糖saddle (打浆的)山墙safe load 安全负荷safety belt 安全带safety cock 安全阀safety code 安全规程safety engineering 技术保安safety equipment 安全设备safety factor 安全系数safety measures 安全措施safety paper base stock 安全纸原纸safety regulations 安全规则,安全规章,安全制度safety rules 安全规则safety sereen 防护屏障safety stripe 安全带safety technique 安全技术safety valve 安全阀sal soda 十分(含)碳酸钠sales book manila 帐薄用马尼拉纸salinity 盐浓度,含盐量salle 精选工段,选纸工段sallon-tree (salix) 柳属salt cake 芒硝salt cake makeup 补充芒硝salt cake rotary screen 芒硝回转筛salt wash 盐(水)洗(涤)salt water 盐水salting out tank 脱盐槽saltpeter 硝石,钾硝,硝酸钾salvage 废旧,回收的salvage of waste paper 废纸回收sammeld ruck 套色印刷sample 试样,样品;取样sample card 样本卡片sample card bristol 样本卡纸sample cup 取样量杯sample plot (植林试验)标准地sample preparation 样品制备sample sheet 纸样sampler 取样器sampling cock 取样旋塞,取样阀sampling well 取样井sand bed 砂层;(过滤池)砂床sand blower 喷砂嘴sand cateher 捕砂器sand filter 砂滤器,沙滤池sand jet blower 喷砂嘴sand papering machine 砂纸加工机sand-pine (pinus clausa sargeut.) 沙松separator 捕砂器;捕砂沟separator-stone 磨石separator table 沉砂盘,除砂盘separator trap 沉砂盘,除砂盘separator well (打浆机)除砂沟sanders 砂纸sanitary dishes (卫生)纸盘sanitary napkin 妇女卫生纸sap 汁液;树汁sap peeling 割树汁;割树脂sapling 幼树saponifiable 可皂化的saponification 皂化(作用)saponification number 皂化值saponifier 皂化剂saponify 皂化saponifying agent 皂化剂saponin 皂角甙sapwood 边材sassafra (sassafras) 檫树属sassafras (sassafras officinale nees et eberm.) 美洲檫树satin cap 缎面装饰单面光包装纸satin finish 施釉;光泽装饰satin white 缎白saturate 饱和saturated 饱和的saturated steam 饱和蒸汽saturating felt 油毡纸saturating machine 浸渍性能saturating properties 浸渍性能saturating test 浸渍试验saturation 饱和度saturation bonding 浸渍结合saturation properties 饱和性质saturation value 饱和值saveall 白水回收装置,白水回收机savalla saveall savalla飘浮白水回收装置scraper saveall 刮板式白水回收机sedimentation (type) saveall 沉降式纤维回收机sveen pederson (flotation) saveall s.p.飘浮式纤维回收机saveall box 白水槽saveall pan 白水盘saveall tray 白水盘saw 锯saw blade 锯条,锯片saw-log 制材用原木saw lumber 成材,制材,锯材saw mill 制材厂saw mill refuse 制材厂废屑,制材厂废料saw mill refuse chipper 板皮削片机saw mill residue 制材厂废料,板皮saw mill waste 制材厂废料;废材saw sharpener 圆锯磨刀机saw teeth 锯齿saw wed 锯片sawdust 锯末sawer 锯木工sawing 锯木sawing machine 锯床sawn tree 成材seab (压光)浆块斑点(纸病)sca-billerud process sca-billeruc高温热解法回收scaffold bridge 踏板scalding water 热水,烫水scale 秤;比例尺;刻度;尺度;规模;结垢scale off 片落,鳞落scaling 结垢scan standard 北欧标准,scan标准scanning 扫描scanning beam 扫描射束scanning electronic microscope 扫描电子显微镜scanning period 扫描周期scanning sensor 扫描头,扫描传感器scarification 割树皮scariform perforation plate 梯状多孔板scattering 散射scattering coefficient 散射系数schamotte brick 粘土质耐火砖schedule 程序scheduling 编制程序;编目录scheid tester scheid平滑度测定仪schibbye fractionator schibbye纤维分离器schiff's reagent (检验醛类)schiff试剂schopper folding tester sxhopper耐折度测定仪schopper-riegler beating degree tester 肖伯尔打浆度(测定)仪,s.r.打浆度仪schopper-riegler freeness s.r.游离度schopper-riegler freeness tester s.r.游离度测定仪schopper torsion meter schopper扭力仪schulz stain (鉴定磨木浆用)schuz染色剂schweitzer's reagent schweitzer铜氨溶液试剂sclerenchyma 厚壁组织sclerenchyma fiber 厚壁纤维sclerenchymatous cell 厚壁细胞scleroid cell 厚壁细胞sclerometer 硬度计sclerotic cell 石细胞scoop 勺,提浆勺scoop wheel 提浆翻斗score 划线score bond 记分册用厚纸score break 断痕score cut 纵切score cutter 压切式纵切刀score type slitter 压切式纵切机scoreability 折曲性能scored 折叠的scoreline 折曲线scorer 折叠机;划线机scoring 折曲;折叠;抓痕(纸病)scotch pine (pinus sylvestris l.) 欧洲赤松scotehban 氟碳与铬络合胶(3mco.产品,商业名称)scoot bond 高级证券纸scoot former scott真空圆网成形装置scour 消除;洗刷,洗涤scouring 净化,提纯;冲洗;(毛毯)脱脂scouring water 洗涤水;污水scrap 碎屑,残渣scrap board 钢笔画用纸板scrap iron 废铁scraper 刮板scraper conveyer 刮板运输机scraper drainer 刮板脱水机scraper knife 刮刀scratch 刮痕scratch board 钢笔画用纸板screen 筛;屏障;网状干毯screen analysis 筛分析screen angle (涂布机)网部倾斜度screen classification 筛分析screen cut 筛缝screen cylinder 筛鼓screen fractionation 筛分(作用)screen plate 筛板screen printing 网目印刷screen room 筛选工段screen room foreeman 筛选工长纸业专业英语词汇翻译(S2) 相关内容:。
制浆造纸工艺简述

生物法制浆
以微生物或其制品(酶)对木片进行预处理,然后用机械
法或化学机械法制浆。
生物处理的目的:有选择性地分解(降解)原料中的木 素,尽可能减少碳水化合物的损失。从而降低磨浆能耗, 减轻废水污染,提高纸浆强度。 主要采用:白腐菌、漆酶等(研究阶段)
造纸(papermaking)
造纸就是将制得的纸浆分散开来后获得交织均匀的薄 片。
反应,生成木素磺酸,木素 磺酸与溶液中的盐基结合, 生成木素磺酸盐,从木片中 溶解出来。
化学法制浆中纤维素的分解
1、碳水化合物的降解反应:剥皮反应 ,100°C以上开始;碱性水解, 150°C以上开始
化学法制浆
化学浆的特点:
这种方法制得的纸浆大致保留了纤维的天然长度,
去除了大部分木素,能用来生产强度高、柔软的高档 纸;
施胶(Sizing)
疏水性表面
加填(Fill)
加填 向纸浆中加入适当的无机填料,以改善纸页的光学性能( 不透明)、印刷性能(表面光滑、均匀、吸墨性好),降低 成本,加入量在2—40%。 常用的填料: 滑石粉(成分:MgO 30.6%, SiO2 62%, 白度96.8% 瓷土(成分:Al2O3 39%, SiO2 45%,白度82%) CaCO3 TiO2 BaSO4
蒸煮条件的确定
在100°C以前,蒸煮液浓度有所下降,但木素基本没 有溶出,此阶段碱液向原料内部浸透,主要溶解的物 质是原料的淀粉、果胶、脂肪、树脂及低分子量的半 纤维素。 初始脱木素阶段:100~150°C这一升温阶段,蒸煮 液浓度继续下降,但木素溶出仅26.6%(对原木素) 。 大量脱木素阶段:150~175°C(最高温度),木素 溶出63.2%(对原木素),此时,木片已分散成浆。 残余木素脱除阶段:碱液浓度继续下降,但木素溶出 只有8%(对原木素),这一阶段碳水化合物降解较多 。
简述现代制浆造纸工艺流程
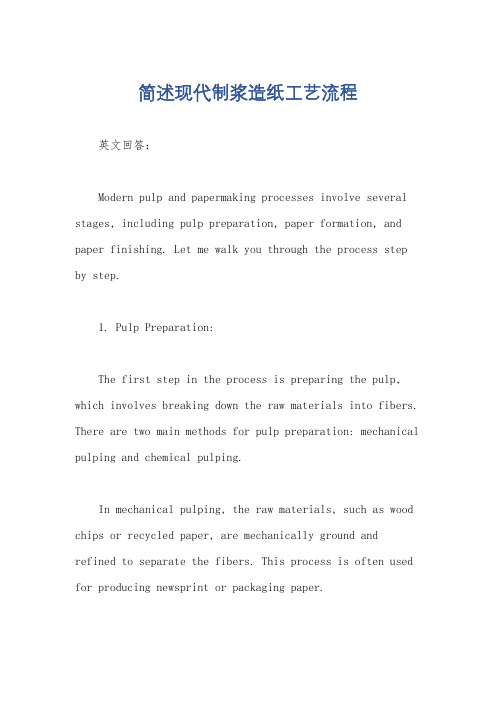
简述现代制浆造纸工艺流程英文回答:Modern pulp and papermaking processes involve several stages, including pulp preparation, paper formation, and paper finishing. Let me walk you through the process step by step.1. Pulp Preparation:The first step in the process is preparing the pulp, which involves breaking down the raw materials into fibers. There are two main methods for pulp preparation: mechanical pulping and chemical pulping.In mechanical pulping, the raw materials, such as wood chips or recycled paper, are mechanically ground and refined to separate the fibers. This process is often used for producing newsprint or packaging paper.Chemical pulping, on the other hand, involves treating the raw materials with chemicals to dissolve the lignin and separate the fibers. There are two common types of chemical pulping: kraft pulping and sulfite pulping. Kraft pulpingis widely used due to its high yield and strong fibers, while sulfite pulping is suitable for producing specialty papers.2. Paper Formation:Once the pulp is prepared, it is ready for paper formation. The pulp is diluted with water and mixed with additives, such as fillers, sizing agents, and dyes, to enhance the paper's properties.The diluted pulp is then fed onto a paper machine, which consists of a headbox, wire section, press section, and drying section. In the headbox, the pulp is evenly distributed onto a moving wire mesh, forming a thin layer of fibers. The water is drained through the wire mesh, leaving behind a wet sheet of paper.Next, the wet sheet passes through the press section, where pressure is applied to remove more water and consolidate the fibers. Finally, the paper enters the drying section, where it is heated and dried using steam-heated cylinders or hot air.3. Paper Finishing:After the paper is dried, it goes through various finishing processes to improve its quality and appearance. These processes include calendering, coating, and cutting.Calendering involves passing the paper through a set of rollers to smoothen the surface and improve its gloss and printability. Coating can be applied to enhance the paper's properties, such as brightness, smoothness, or water resistance. Finally, the paper is cut into sheets or rolls of desired sizes.中文回答:现代制浆造纸工艺流程包括制浆准备、纸张成型和纸张加工等几个阶段。
造纸术英语作文

造纸术英语作文Papermaking is an ancient technique that has played a significant role in the development of human civilization. It involves the transformation of plant fibers into a thin and flexible material used for writing, printing, and packaging. The process of papermaking can be divided into several stages: preparation of the raw materials, pulping, sheet formation, pressing, drying, and finishing.To start with, the raw materials for papermaking are primarily derived from plants. Historically, various plants such as bamboo, mulberry, and hemp were used. Nowadays, the most common source of raw material is wood pulp obtained from trees. The raw materials are first sorted, cleaned, and then reduced to small pieces to facilitate the subsequent pulping process.The pulping process aims to separate the fibers from the raw materials. There are two main methods of pulping: mechanical pulping and chemical pulping. Mechanical pulping involves grinding the raw materials to mechanically separate the fibers. On the other hand, chemical pulping involves treating the raw materials with chemicals todissolve the unwanted components and retain the fibers. The most widely used chemical pulping method is the Kraft process, which utilizes a mixture of sodium hydroxide and sodium sulfide.Once the fibers are separated, they are mixed with water to form a slurry called pulp. The pulp is then poured ontoa wire mesh screen, and the water drains away, leaving behind a thin layer of fibers. This process is known as sheet formation. The fibers in the sheet are then pressedto remove excess water and improve the density of the paper. This is typically done using heavy rollers.After pressing, the paper is dried to remove the remaining water. There are different methods of drying, including air drying, where the paper is left to dry naturally, and machine drying, where heat is applied to speed up the drying process. Once the paper is dry, it undergoes various finishing treatments to improve its quality. These treatments may include sizing, coating, calendering, and cutting.Papermaking has had a profound impact on human civilization. It has allowed for the dissemination ofknowledge through the production of books, newspapers, and other printed materials. It has also played a crucial rolein the development of bureaucracy, enabling the recording and storage of information. Additionally, paper has been used for packaging, packaging materials, and various other applications.造纸术是一种古老的技术,在人类文明的发展中起着重要作用。
造纸术工艺流程英文英语
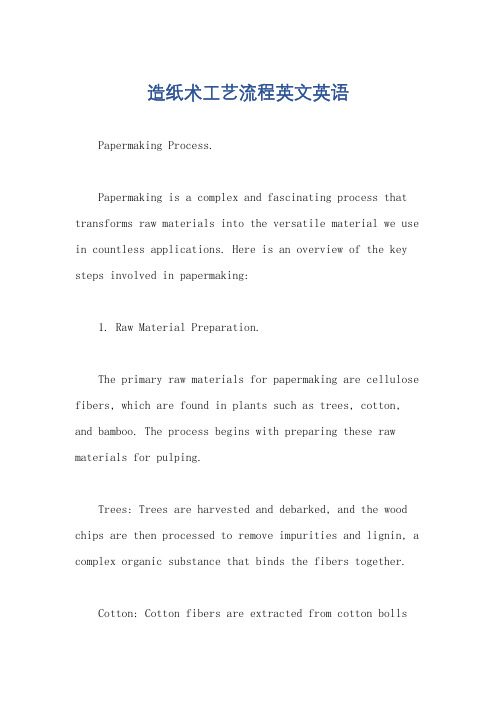
造纸术工艺流程英文英语Papermaking Process.Papermaking is a complex and fascinating process that transforms raw materials into the versatile material we use in countless applications. Here is an overview of the key steps involved in papermaking:1. Raw Material Preparation.The primary raw materials for papermaking are cellulose fibers, which are found in plants such as trees, cotton, and bamboo. The process begins with preparing these raw materials for pulping.Trees: Trees are harvested and debarked, and the wood chips are then processed to remove impurities and lignin, a complex organic substance that binds the fibers together.Cotton: Cotton fibers are extracted from cotton bollsthrough a process known as ginning. The fibers are then cleaned and processed to remove impurities.Bamboo: Bamboo culms are harvested, chopped, and pulped to extract the cellulose fibers.2. Pulping.Pulping involves breaking down the raw materials into individual cellulose fibers. There are two primary pulping methods:Mechanical Pulping: This method uses mechanical force to grind or crush the raw materials into fibers. Mechanical pulps are typically used to produce lower-grade papers with a higher proportion of short fibers.Chemical Pulping: This method uses chemical solutions to dissolve lignin and other non-cellulose components, leaving behind pure cellulose fibers. Chemical pulps are used to produce higher-grade papers with a higher proportion of long fibers.3. Screening and Cleaning.After pulping, the pulp is screened and cleaned to remove any remaining impurities, such as bark, knots, and dirt. This step ensures a clean and consistent pulp for the next stage.4. Bleaching.Bleaching is an optional step that involves treating the pulp with chemicals to remove color and impurities. Bleaching produces a brighter and whiter pulp, which is essential for certain types of papers, such as printing and writing papers.5. Stock Preparation.Stock preparation involves preparing the pulp for sheet formation. Additives, such as sizing agents, fillers, and dyes, may be added to the pulp at this stage to enhance the properties of the paper.6. Sheet Formation.Sheet formation is the process of forming the wet paper sheet. The pulp is diluted with water and fed onto a wire mesh conveyor belt called a Fourdrinier machine. As the water drains through the mesh, the cellulose fibers intertwine and form a continuous sheet.7. Pressing.The wet paper sheet is then pressed between rollers to remove excess water and compact the fibers. Pressing increases the paper's strength and density.8. Drying.The paper sheet is passed through a series of heated rollers to remove the remaining moisture. Drying is a critical step that determines the paper's final properties, such as moisture content, strength, and smoothness.9. Finishing.After drying, the paper may undergo additionalfinishing processes, such as:Coating: A thin layer of coating may be applied to the paper表面 to enhance its smoothness, gloss, and printability.Calendering: The paper is passed through heated rollers to smooth the surface and improve its appearance.10. Cutting and Packaging.The finished paper is cut into sheets or rolls and packaged for distribution.Environmental Considerations.Papermaking has environmental implications due to the use of resources such as trees and water. Sustainable forestry practices and responsible water management areessential to minimize the environmental impact. Additionally, recycling paper significantly reduces the demand for virgin raw materials and helps conserve resources.。
- 1、下载文档前请自行甄别文档内容的完整性,平台不提供额外的编辑、内容补充、找答案等附加服务。
- 2、"仅部分预览"的文档,不可在线预览部分如存在完整性等问题,可反馈申请退款(可完整预览的文档不适用该条件!)。
- 3、如文档侵犯您的权益,请联系客服反馈,我们会尽快为您处理(人工客服工作时间:9:00-18:30)。
Advantages of sulfite pulping
Produce bright pulp which is easy to bleach to full brightness Produce higher yield of bleached pulp The pulp is relatively easy to refine (beat) for papermaking application
(2)More soluble bases, i.e. magnesium, sodium and ammonium, are used in sulfite pulping. By utilizing proper conditions, it is now possible to pulp wood species which are unsuitable for classic calcium acid sulfite pulping. Recovery of cooking chemicals from the calcium base system has never been practiced. There are still some technical and economic problems in recovery of cooking chemicals from Mg base and Na base.
(b)Cleavage of β-aryl ether bonds in phenolic lignin units -In kraft pulping, hydrosulfide ions are sufficiently nucleophilic to cause a cleavage -In soda pulping, alkali-stable structures are formed,e.g.the formation of β-formaldehyde elimination and proton elimination, without the cleavage at the β-C atom. -The quinone methide intermediate reacts more rapidly with SH-、S2- than with OH-,which explains the more rapid and extensive degradation of lignin by kraft pulping liquor than by soda liquor.
(C)Cleavage of β-aryl ether bonds in nonphenolic units much more slow and in the case of :
-Having α-hydroxyl group to form epoxide intermediate between Cα-Cβ -Having α-carbonyl group to form episulfide intermediate between Cβ-Cr
Disadvantages of sulfite pulping
Limited variety of species, especially for acid sulfite pulping Relatively low pulp strength Relatively sensitive to bark Some technical and economic problems in chemical recovery
4 Development Trends in Chemical Pulping
(1)Kraft process is the dominant process of chemical pulping In north America, chemical pulping accounts for 70% of the total production, of which 90% is produced by kraft process.
Cleavage of linkages of lignin structural units
(a) Cleavage of α-aryl ether and α-alkyl ether bonds in phenolic lignin unit—— very easy The cleavage leads to the formation of a quinone methide structure But α-aryl ether and α-alkyl ether bonds in nonphenolic lignin units are stable
5.Chemical Reactions during Alkaline Cooking
(1)Reactions of lignin in alkaline pulping The reactions of lignin during alkaline pulping are complex. Hydroxyl ions, acting as nucleophilic agents, bring about the cleavage of certain types of ether linkages in alkaline pulping. In kraft cookng ,the combination of hydrosulfide and sulfide ions present is less alkaline but more strongly nucleophilic than hydroxyl ions alone.
Advantages of Kraft pulping
All wood and non-wood species can belatively insensitive to bark Cooking times are relatively short Problems with pitch in the pulp are relatively small The pulp is much stronger Regeneration of chemicals and energy is efficient Side-products such as turpentine and tall-oil are valuable
Chemical Pulping
ZHAN Huaiyu
1.The Objective of Chemical Pulping
The objective of chemical pulping is to degrade and dissolve away the lignin and leave behind most of the cellulose and hemicellulose in the form of intact fibers. The raw materials are cooked with the appropriate chemicals in an aqueous solution at elevated temperature and pressure. Two principal methods: Alkaline pulping Sulfite pulping
(d)Cleavage of C-C bonds leading to a reduction or total elimination of side-chain -Cleavage of Cβ-Cγ -Cleavage of Cα-Cβ -Cleavage of Cα-Aγ
Displacement batch processes -Rapid Displacement Heating (RDH) -SuperBatch Cooking (SB) -White Liquor Impregnation (WLI) Principles of Extended Delignification Modified Cooking -Even alkali concentration profile during the whole cooking process -High HS-、S2- concentration at the stage of bulk delignification -As low as possible of solid content in the black liquor,especially at the late stage of cooking -As low as possible of the maximum temperature
2.Alkaline Pulping
(1) Soda or Soda-AQ pulping Chemicals: NaOH+Na2CO3 (small amount) AQ Suitability:hardwood, non-wood fibers (2) Kraft pulping (Sulfate pulping) Chemicals:NaOH+Na2S Suitability:softwood, hardwood,non-wood fibers “Kraft” is the Germanic word for strong. The fact that Na2SO4 is commonly used as a makeup chemical is the reason that the Kraft process is sometimes called the “sulfate process”.
(3)High efficient,low energy consumption modified kraft pulping processes are developed and practiced