炼焦新技术
炼焦新技术
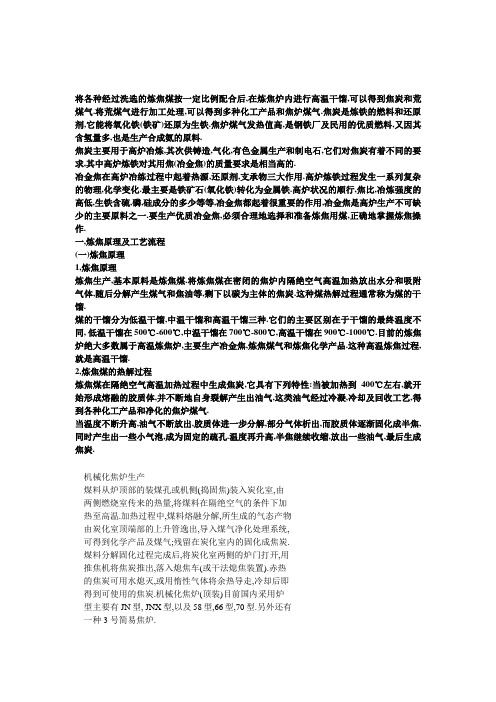
将各种经过洗选的炼焦煤按一定比例配合后,在炼焦炉内进行高温干馏,可以得到焦炭和荒煤气.将荒煤气进行加工处理,可以得到多种化工产品和焦炉煤气.焦炭是炼铁的燃料和还原剂,它能将氧化铁(铁矿)还原为生铁.焦炉煤气发热值高,是钢铁厂及民用的优质燃料,又因其含氢量多,也是生产合成氨的原料.焦炭主要用于高炉冶炼,其次供铸造,气化,有色金属生产和制电石,它们对焦炭有着不同的要求,其中高炉炼铁对其用焦(冶金焦)的质量要求是相当高的.冶金焦在高炉冶练过程中起着热源,还原剂,支承物三大作用.高炉炼铁过程发生一系列复杂的物理,化学变化.最主要是铁矿石(氧化铁)转化为金属铁.高炉状况的顺行,焦比,冶炼强度的高低,生铁含硫,磷,硅成分的多少等等,冶金焦都起着很重要的作用,冶金焦是高炉生产不可缺少的主要原料之一.要生产优质冶金焦,必须合理地选择和准备炼焦用煤,正确地掌握炼焦操作.一,炼焦原理及工艺流程(一)炼焦原理1,炼焦原理炼焦生产,基本原料是炼焦煤.将炼焦煤在密闭的焦炉内隔绝空气高温加热放出水分和吸附气体,随后分解产生煤气和焦油等,剩下以碳为主体的焦炭.这种煤热解过程通常称为煤的干馏.煤的干馏分为低温干馏,中温干馏和高温干馏三种.它们的主要区别在于干馏的最终温度不同, 低温干馏在500℃-600℃,中温干馏在700℃-800℃,高温干馏在900℃-1000℃.目前的炼焦炉绝大多数属于高温炼焦炉,主要生产冶金焦,炼焦煤气和炼焦化学产品.这种高温炼焦过程,就是高温干馏.2,炼焦煤的热解过程炼焦煤在隔绝空气高温加热过程中生成焦炭,它具有下列特性:当被加热到400℃左右,就开始形成熔融的胶质体,并不断地自身裂解产生出油气,这类油气经过冷凝,冷却及回收工艺,得到各种化工产品和净化的焦炉煤气.当温度不断升高,油气不断放出,胶质体进一步分解,部分气体析出,而胶质体逐渐固化成半焦,同时产生出一些小气泡,成为固定的疏孔.温度再升高,半焦继续收缩,放出一些油气,最后生成焦炭.。
浅析炼焦化工工艺流程及新工艺应用

浅析炼焦化工工艺流程及新工艺应用在我国经济日益发展的当下,资源稀缺问题仍然存在。
在人民的生产生活中,煤炭依然发挥着不可替代的作用。
煤炭作为一种稀缺性大且开采难度高的资源,其重要性主要体现在制造生产过程中。
煤炭的制作需经过较为严格的炼焦工艺,但此时得到的物质并不纯粹,资源浪费现象仍然存在。
为了实现煤炭资源的有效制作和利用,本文对于炼焦工艺做出详细研究,从工艺流程、新工艺应用等方面展开分析,以期推动该技术的推广应用。
标签:炼焦;化工工艺;流程;应用资源稀缺问题是当前世界各国面临的共同问题。
从经济学角度讲,资源的数量是固定的,而人的欲望是无穷的,我们不能够左右人的想法,却能够促进资源被有效开采和利用。
煤炭资源的开采本就不易,现在的技术水平还不能够保证资源被百分之百采用。
因此,在炼焦化工工艺中,技术人员应该严格监督化工的流程步骤,并适时采用新的工艺技术。
从炼焦工艺出发,本文对炼焦工艺、流程步骤以及新工艺的运用部署展开分析,希望能够为广大炼焦工作者提供有效帮助。
1炼焦化工的内容在煤炭生产过程中,炼焦阶段的要求较为严格。
普遍的炼焦化工工艺:首先炼焦化工工艺必须保持无氧,因此需要较高的温度,以1500℃为基本,对炼焦材料进行加工,然后对材料展开干馏措施,得到煤气和焦炭。
对于得到的煤气和焦炭,还需经过热分解环节得到相关的化学产品。
在高温炼焦过程中,气孔凭借自身的强度可以帮助加热炉起到支撑作用,这在炼铁工艺中更为明显。
炼焦工艺的资源浪费性较高,所产生的副产品也较高;面对炼焦工艺,胶质单体仍然是一大难题,由于其本身的粘附性以及挥发性较强,在生产中会受到膨胀压力致使体积变大,在一定程度上提高了炼焦工艺的难度[1]。
2炼焦的原理以及工艺流程2.1炼焦工艺的原理炼焦工艺是获得煤炭资源的主要手段在对炼焦煤进行高温加热之前,要保证炼焦煤处于一个密闭空间内,并且这一密闭空间内不存在空气。
高温加热炼焦煤会吸附附近的气体,产生一定的水分并且释放出热量,通过物理和化学反应产生焦油和煤气,形成固体焦炭,上述该过程属于干馏,通过温度高低不同其有低温、中温和高温三种类型,而多数煤炭企业主要运用的是高温干馏。
炼焦方法

炼焦方法捣固炼焦介绍:一.捣固炼焦的价值与意义捣固炼焦技术是一种可根据焦炭的不同用途,配入较多的高挥发分煤及弱粘结性煤,在装煤推焦车的煤箱内用捣固机将已配合好的煤捣实后,从焦炉机侧推入炭化室内进行高温干馏的炼焦技术。
捣固炼焦是炼焦一项新技术。
其优势明显:技术捣固炼焦技术可多用弱粘结性煤,少用强粘结性煤,增大了炼焦煤料的可选范围,降低炼焦成本、改善焦炭质量,捣固炼焦工艺以其显著的经济技术优势,在国内得到迅猛发展。
捣固炼焦技术对我国焦化广大工作者来说,是一个新的课题,有待探索研究,在实践的过程中不断丰富捣固炼焦技术理论,以指导我国捣固炼焦技术的应用和发展。
捣固炼焦工艺是在炼焦炉外采用捣固设备, 将炼焦配合煤按炭化室的大小, 捣打成略小于炭化室的煤饼, 将煤饼从炭化室的侧面推入炭化室进行高温干馏。
成熟的焦炭由捣固推焦机从炭化室内推出,经拦焦车、熄焦车将其送至熄焦塔, 以水熄灭后再放到凉焦台, 由胶带运输经筛焦分成不同粒级的商品焦炭经研究发现:在相同配煤比之下,捣鼓炼焦大幅度提高了焦炭的冷态强度。
捣鼓可以改善焦炭气孔结构,提高焦炭反应强度。
捣固炼焦是用机械力将煤料的粒子压紧,因压紧而导致:①增加煤料堆密度;②因粒子的压紧而使胶质体填充的空隙减少,而相对扩展了粘结范围;③由于堆密度的增加单位体积内析出的煤气量增加,而提高了膨胀压力。
这些因素导致了焦炭多孔体的气孔壁增厚,气孔率降低且趋向均匀,因而M40、M10都有所改善,CRI和CSR也略有改善。
二.我国捣固炼焦的发展现状与发张趋势现状:捣固炼焦技术在我国炼焦生产中已占重要地位,目前,我国捣固炼焦炉分布在陕西、河北、山东等十三个省份,共有捣固炼焦企业81家,捣固焦炉168座,产能已达5035万吨,占焦炭产能的16.07%。
在现生产的捣固焦炉中,以炭化室高4.3米,炭化室宽500mm的焦炉为主,其次是炭化室高3.2米和炭化室高3.8米的焦炉;我国捣固炼焦炉平均炉龄较短,绝大部分焦炉炉龄在五年之内。
中国大型焦炉炼焦工艺技术优化与改进

我国大型焦炉炼焦工艺技术优化与改进一、引言我国作为世界上最大的焦煤生产和消费国,焦炉炼焦工艺技术一直是焦化企业关注的焦点。
随着煤炭产业结构调整和技术进步,炼焦工艺技术的优化与改进变得尤为重要。
本文将对我国大型焦炉炼焦工艺技术的优化与改进进行深入探讨。
二、我国大型焦炉炼焦工艺技术现状1. 炼焦工艺技术概述我国大型焦炉炼焦工艺技术主要包括焦炭生产的原料选择、炉前处理、煤气利用和焦炉运行等环节。
目前,我国大部分焦化企业依然采用传统的炼焦工艺技术,存在能耗高、环境污染严重等问题。
2. 技术优化的迫切性随着国家对环境保护和能源节约的要求日益提高,炼焦企业迫切需要进行工艺技术的优化与改进,提高炼焦效率、减少能耗和污染排放。
三、技术优化与改进的途径1. 原料选择的优化优化煤炭、焦煤和炼焦助剂的选择,提高炼焦质量和产量,减少炼焦过程中的能耗。
2. 高效环保设备的引入引入先进的高效环保设备,如干熄焦技术、煤气余热利用技术等,降低炼焦过程中的二氧化硫和氮氧化物排放,实现清洁生产。
3. 先进控制技术的应用应用先进的控制技术,进行炼焦过程的自动化和智能化控制,提高设备运行稳定性和生产效率。
4. 节能减排技术的推广推广节能减排技术,如余热发电技术、焦炉废气治理技术等,实现能源的最大化利用和环境污染的最小化排放。
四、技术优化与改进的效果通过对我国大型焦炉炼焦工艺技术的优化与改进,可以实现以下效果:1. 提高焦炭的质量和产量,降低炼焦能耗。
2. 减少炼焦过程的环境污染排放,改善周边环境质量。
3. 提升焦炉设备的稳定性和运行效率,降低生产成本。
4. 实现清洁生产,符合国家的环保政策和节能减排要求。
五、结语我国大型焦炉炼焦工艺技术的优化与改进是一个复杂系统工程,需要从原料选择、环保设备引入、控制技术应用和节能减排技术推广等多个方面进行全面优化。
只有不断地改进和完善炼焦工艺技术,才能实现焦炭生产的可持续发展。
希望随着技术的不断进步,我国大型焦炉炼焦工艺技术能够实现更加环保、高效和可持续的发展。
炼焦新技术

炼焦新技术作者:苏晓晓化工08-1班19号摘要:在使用常规焦炉炉型的情况下,提高焦炭质量主要集中在对炼焦原料煤的预处理,改善焦炉的加热制度和对焦炭进行后序处理3个方面,本文列举了以上方面的几项新技术。
关键词:原煤预处理改善加热后序处理1 原料煤的预处理技术1.1捣固炼焦技术捣固炼焦,一般是用高挥发份弱粘结性或中等粘结性煤作为炼焦的主要配煤组份,将煤料粉碎至一定细度后,用机械捣固成煤饼,送入焦炉炭化室内炼焦。
装炉煤料捣固成煤饼后.从焦炉的机侧装入炭化室,其密度可以提高到950kg/ms一1 150kg/m3,质量增加27%,炼出的焦炭比顶装煤焦炉生产的焦炭抗碎强提高1%一6%,耐磨强度肘10改善2%一4%,反应后强度C凇提高1%一6%,在相同焦炭质量下,可多用20%一25%的高挥发分弱黏结性煤.使入炉煤料中高挥发分弱黏结性煤的配入量高达70%~80%。
1.2配型煤炼焦技术配型煤炼焦,就是将炼焦原料煤中的一部分压块成型,再与其它的粉煤混合,人炉炼焦。
在配煤比相同的条件下。
配型煤炼焦生产的焦炭与常规粉煤炼焦生产的焦炭比较提高2%一3%,变化不大或稍有改善,JIS转鼓试验指标提高1%-3%,CRI降低5%一8%,CSR提高5%一12%。
焦炭筛分组成有所改善。
大于80ram级产率有所下降,80ram~25ram级显著增加(一般可增加5%。
10%),小于25ram级变化不大.因而提高了焦炭粒度的均匀系数。
1.3煤调湿技术(CMc)“煤调湿”是“装炉煤水分控制工艺”的简称,是将炼焦煤料在装炉前去除一部分水份,保持装炉煤水分稳定在6%左右,然后装炉炼焦。
煤调湿不同于煤预热和煤干燥:煤预热是将入炉煤在装炉前用气体热载体或固体热载体快速加热到热分解开始前温度(150℃~250℃),此时煤的水分为零,然后再装炉炼焦;而煤干燥没有严格的水分控制措施,干燥后的水分随来煤水分的变化而改变;煤调湿有严格的水分控制措施,能确保人炉煤水分恒定。
最新炼焦煤配煤技术

研究认为,废塑料与煤共焦化技术可行。该所曾对几 种沥青与重庆焦化渣用Corbett法进行了组成分析,研究 表明,减压渣油和丙烷脱沥青饱和烃含量较高,沥青质很 少,作为改质剂性能较差。热裂化渣油和乙烯焦油含有相 当高的芳烃与沥青,QI少,因此作为改质剂性能较好。煤 焦油沥青具有较高的芳香性能,因此溶剂性能较好,但QI 含量高,对焦油过程中间相发展不利。
在炼焦技术上、大多数炼焦用的单独焦煤都不能练出 符合高炉对焦炭强度和质量要求的焦炭,而粘结性较好的 主焦煤即使能单独练出强度合格的焦炭,但是由于在炼焦 过程中药产生较强的膨胀压力,而影响焦炉的寿命或造成 难推焦等问题,而肥煤虽有较强的粘结性,单单独炼焦时 、练成的焦炭易形成部分的蜂窝焦而影响焦炭的强度,因 此
目前,我国炼焦配煤中高挥发分煤的用量一般较高, 有的焦化厂配合煤可燃基挥发分已达到 34%。一般大、 中高炉用焦的配合煤的可燃基挥发分则在28%-32% 之间 。
在炼焦的生产上都不能用单种煤炼焦,而是将几种类别的 炼焦配合使用,发挥各类煤在炼焦时的特点、扬长避短、 优势互补、从而以经济合理的配煤方案练出质量符合的焦 炭。
中国炼焦用煤的焦煤、肥煤虽然粘结性结焦性较好, 但是这两类煤质中国一般都属于较难洗选的煤、洗精煤的 灰分高、硫高、使用其用量受到一定的限制,而中国所产 的气煤和弱粘煤在炼焦中虽然粘结性较差,但它们已选, 灰低、硫低,其资源又丰富,储存量大,产量高、煤价相 对较低,因而在炼焦煤中,在一定的比例的焦煤和肥煤基 础上配入适量的气煤和弱粘煤,因其挥发分高、收缩度大 ,便于推焦,而煤气焦化产品回收也多。
(1)配合煤的灰分
煤中灰分在炼焦后全部残留于焦炭中,灰分是焦炭中
的有害杂质,焦炭的灰分愈高,炼铁时焦炭及石灰石消耗 量就增多,高炉的生产能力就要降低,同时灰分中的大颗 粒在焦炭中形成裂纹中心,使焦炭的抗碎强度降低,也使 焦炭的耐磨性变坏。所以配合煤的灰分应控制在一定范围 之内。假设配合煤的结焦率为 75%,而要求焦炭的灰分 等于或小于12.5% ,则配煤的灰分就不能大于 9.4%。配 合煤的灰分是根据各单种煤的灰分按加权平均计算的。如 果在配合煤中使用了一两种灰分较高的精煤,则其余成分 必须选配较低灰分的单种煤,才能保证焦炭的灰分符合要 求。
炼焦新工艺简介

第三章
工艺一班:小
炼焦新工艺简介
• 配煤的预处理技术 • 型焦
配煤的预处理技术
一、配煤掺油
配煤掺油后,煤粒吸附了碳氢化合物分子,在表 面形成了单分子层薄膜,产生油润作用,减小了煤 表面水分造成的颗粒间的附着力,使煤的流动性提 高,堆密度增大。由于煤的堆密度的提高,使得全 焦率增加5.8%,冶金全焦产量提高6%,焦炭耐磨 强度也有所改变。
二、捣固炼焦
1、方法原理:将配煤在,即捣固炼焦。一般炼焦的堆密度由散装 煤的0.72t/m*3提高到0.95-1.15t/m*3,使煤粒之间的接触紧密,在 结焦过程中胶质体充满程度大,并减小气体的析出速度,从而得 到的焦炭结构致密。
2、效果:采用捣固炼焦,可扩大气煤用量,改善焦炭质量。
1、预热煤炼焦 煤预热炼焦时,预热温度对煤的堆密度、煤质 氧化和焦炭质量都有影响。德国的普雷卡邦法预热煤炼焦工艺 流程见下图,热烟气和惰性气体相混,以调节温度并首先进入 预热管来预热煤,由预热管出来的热气体再去干燥管。
此法完全利用逆流操作原理,其优点如下:
1、改善焦炭质量并增加气煤用量 预热煤炼焦所得的焦炭, 与同一煤料的湿煤炼焦所得的焦炭相比,有真密度大、气孔 率小、耐磨强度高、反应性低、反应后强度大和平均粒度大 等特点。
(2)工艺 气体热载体工艺 以热废气作为快速加热的载体,使煤粉 快速加热,并热压成型煤。如下图:
固体热载体工艺 以高温无烟煤粉、矿粉和焦粉作为 载体和配料,在预热至200-250度的烟煤混合的同时, 实现快速加热。一般此工艺由四部分组成:在炉中进行 固体载体加热;进行烟煤预热;混合、维温和热压成型; 在炭化炉中进行型煤炭化焙烧。四部分相对独立,易于 控制和操作。但此工艺维温时间较短废热利用不好和所 用煤种较窄等问题。
炼焦新工艺的国内外发展现状
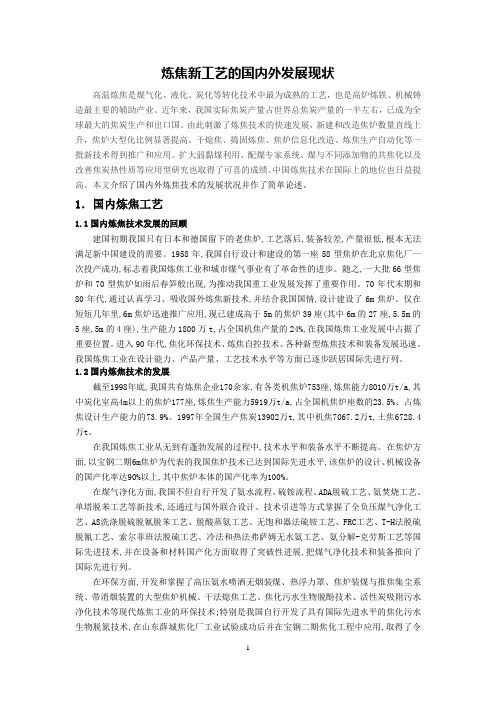
炼焦新工艺的国内外发展现状高温炼焦是煤气化、液化、炭化等转化技术中最为成熟的工艺,也是高炉炼铁、机械铸造最主要的辅助产业。
近年来,我国实际焦炭产量占世界总焦炭产量的一半左右,已成为全球最大的焦炭生产和出口国。
由此刺激了炼焦技术的快速发展,新建和改造焦炉数量直线上升,焦炉大型化比例显著提高。
干熄焦、捣固炼焦、焦炉信息化改造、炼焦生产自动化等一批新技术得到推广和应用。
扩大弱黏煤利用、配煤专家系统、煤与不同添加物的共焦化以及改善焦炭热性质等应用型研究也取得了可喜的成绩。
中国炼焦技术在国际上的地位也日益提高。
本文介绍了国内外炼焦技术的发展状况并作了简单论述。
1.国内炼焦工艺1.1国内炼焦技术发展的回顾建国初期我国只有日本和德国留下的老焦炉,工艺落后,装备较差,产量很低,根本无法满足新中国建设的需要。
1958年,我国自行设计和建设的第一座58型焦炉在北京焦化厂一次投产成功,标志着我国炼焦工业和城市煤气事业有了革命性的进步。
随之,一大批66型焦炉和70型焦炉如雨后春笋般出现,为推动我国重工业发展发挥了重要作用。
70年代末期和80年代,通过认真学习、吸收国外炼焦新技术,并结合我国国情,设计建设了6m焦炉。
仅在短短几年里,6m焦炉迅速推广应用,现已建成高于5m的焦炉39座(其中6m的27座,5.5m的5座,5m的4座),生产能力1800万t,占全国机焦产量的24%,在我国炼焦工业发展中占据了重要位置。
进入90年代,焦化环保技术、炼焦自控技术、各种新型炼焦技术和装备发展迅速。
我国炼焦工业在设计能力、产品产量、工艺技术水平等方面已逐步跃居国际先进行列。
1.2国内炼焦技术的发展截至1998年底,我国共有炼焦企业170余家,有各类机焦炉753座,炼焦能力8010万t/a,其中炭化室高4m以上的焦炉177座,炼焦生产能力5919万t/a,占全国机焦炉座数的23.5%、占炼焦设计生产能力的73.9%。
1997年全国生产焦炭13902万t,其中机焦7067.2万t,土焦6728.4万t。
- 1、下载文档前请自行甄别文档内容的完整性,平台不提供额外的编辑、内容补充、找答案等附加服务。
- 2、"仅部分预览"的文档,不可在线预览部分如存在完整性等问题,可反馈申请退款(可完整预览的文档不适用该条件!)。
- 3、如文档侵犯您的权益,请联系客服反馈,我们会尽快为您处理(人工客服工作时间:9:00-18:30)。
炼焦新技术—煤调湿技术我国现有焦炉生产能力较大,占世界第一位,炼焦煤水分偏高,而且优质炼焦煤日益短缺,围绕现有焦炉和炼焦生产工艺,开发提高焦炭质量和利用炼焦余热的新工艺、新技术是适应企业发展,提高企业经济效益的有效途径。
煤调湿技术可降低入炉煤水分,降低炼焦耗热量,增加入炉煤堆密度,提高焦炭质量。
近几年来,煤调湿技术在国内外炼焦行业异军突起,得到了广泛的应用,究其原因是煤调湿技术具有其独特的优越性:可使焦炭和化工产品增产11%,提高经济效益;焦炉加热用燃料降低,减少耗热量;焦炭质量得到提高;充分利用了焦炉余热,取得了明显的经济和社会效益。
一、煤调湿(Coal Moisture Control ,简称“ CMC ”)技术简述煤调湿技术是通过直接或间接加热来降低并稳定控制入炉煤的水分,该技术不追求最大限度地去除入炉煤的水分,而只把水分稳定在相对低的水平,既可达到增加效益的目的,又不因水分过低而引起焦炉和回收系统操作的困难,使入炉煤密度增大、焦炭及化工产品增产、焦炉加热用煤气量减少、焦炭质量提高和焦炉操作稳定等效果。
二、煤调湿的基本原理利用外界热能将入炉煤在焦炉外干燥,控制入炉煤的水分,从而控制炼焦耗热量、改善焦炉操作、提高焦炭产量或扩大弱粘结性煤的用量。
三、工艺流程及发展煤调湿技术通过直接或间接加热来降低并稳定控制入炉煤水分,并不追求最大限度地去除入炉煤气的水分,而只是把水分稳定在相对较低的水平,就可以达到增加效益的目的,又不会因水分过低而引起焦炉和回收系统操作困难。
煤调湿技术于20世纪80年代初在日本开始应用,历经了3 种工艺技术的变革:第一代是热媒油干燥方式;第二代是蒸汽干燥方式;第三代是最新一代的流化床装置,设有热风炉,采用焦炉烟道废气或焦炉煤气对其进行加热的干燥方式。
1、第一代煤调湿技术第一代CMC是热煤油干燥方式,其工艺见下图。
热媒油式煤调湿工艺流程图利用热油回收焦炉上升管煤气显热和焦炉烟道气的余热,温度升高到195℃的热油通过干燥机将常温的煤预热到80℃,煤的水分由9%左右降到5.7%,调湿后的煤在运输过程中水分还将降低0.7%,装入煤水分保持在5%±0.7%。
2、第二代煤调湿技术第二代CMC是蒸汽干燥方式。
利用干熄焦蒸汽发电后的低压蒸汽或其它低压蒸汽作为热源,在多管回转式干燥机中,蒸汽对煤料间接加热干燥。
其基本的工艺流程见下图,来自原料煤工序的湿煤经过进料螺旋输送机进入多管回转式干燥机,在干燥机体内,煤料与逆流运行的1.3MPa 饱和蒸汽环管充分接触,并进行热量交换。
煤料从干燥机入口向出口方向移动,当物料到达干燥机出口时水分降至6.5%,经出料口排出,与收尘器分离下来的粉尘混合后一起送至煤塔。
从入口处进入的220℃烟道气作为携湿气在携湿的同时利用自身热量也给物料提供部分热量进行调湿。
携湿后的烟道气由多管回转式干燥机的集尘罩顶部排出,排出的烟道气及夹带煤粉尘被引风机抽吸到布袋除尘器内进行气固分离。
气固分离净化后的烟道气经引风机引至安全地点排放。
调湿煤经输送、调湿等过程以后,采取了必要的除尘措施,防止粉尘飞扬。
在输送过程中,带式输送机设防尘机罩进行全封闭,头部落料点处设收尘设施。
1 螺旋进料机;2 环管分体式蒸汽回转干燥机;3 布袋除尘器;4 干燥引风机;5 出料螺旋输送机;6 皮带输送机环管分体式蒸汽回转煤调湿工艺流程图多管回转式干燥机是在普通回转圆筒干燥机内部安置了蒸汽加热管,加热管贯穿整个干燥机,以同心圆方式排成1-3 圈,干燥所需热量由蒸汽加热管提供,是间接连续干燥机。
加热管随筒体转动,进入干燥机的物料在转筒内受到加热管的升举和搅拌作用,被加热管提供的热量干燥,再借助于干燥机的倾斜度从加热口向出料口移动,从出料口排出。
物料中汽化的二次蒸汽从排气口进入尾气处理系统,除去粉尘后放空;对易燃易爆易氧化工况,还可采用惰性气体闭路循环,多管回转式干燥机传热面积大,热效率高,因此适用于处理量大、连续干燥的物料。
多管回转式干燥机内部的换热管组件为特制部件,采用直管与环管相结合,与采用直管固定换热管的蒸汽回转干燥机相比,增大了相同空间内的换热面积,保证了蒸汽与物料之间的充分热量交换,提高了干燥机的调湿效率。
每一组换热管组件均可单独从进料端抽出,可以及时实现换热管的更换和维护。
环管分体蒸汽回转干燥机的主要特点有:(1)、传热面积大,热效率高,热效率高达80%~90%;(2)、填充率高、处理能力大,适用于连续操作;(3)、干燥温度低,操作简单,使用方便;(4)、气体仅作为带走挥发组分的携带气,气体用量小,粉尘回收设备简单;(5)、密闭性能好,非常适用于易燃易爆易氧化的工况;(6)、使用方便,易于检修,结构简单,加工成本低。
3、第三代煤调湿技术第三代是最新一代的流化床装置。
在对前二代CMC技术实践和总结的基础上,新日铁开发投产了第三代也是最新一代的流化床CMC装置,取得了显著降低炼焦耗热量、提高焦炉生产能力和改善焦炭质量的效果,其工艺见下图。
流化床式煤调湿工艺流程图水分为10%-11%的煤料由湿煤料仓送往2个室组成的流化床干燥机,从分布板进入的热风直接与煤料接触,对煤料进行加热干燥,使煤料水分降至6.6%。
第三代CMC干燥用热源是由抽风机抽吸的焦炉烟道废气,其温度为180-230℃。
本装置还设有热风炉,当煤料水分过高或焦炉烟道废气量不足或烟道废气温度过低时,可将抽吸的烟道废气先送入热风炉,用焦炉煤气点火,使高炉煤气燃烧,提高烟道废气的温度。
入炉煤料含水量设定为6.0%是为了防止调湿后煤料产生过多的粉尘。
将CMC出口煤含水量设定略高于6.0%,是因为从CMC出口到焦炉的运输过程中会蒸发一部分水分。
流化床干燥机内的分布板是特殊钢材制作的筛板,干燥机的其他部分均可用普通碳钢材制作。
在CMC的几个部位上设置有氧监测仪,自动报警,防止发生爆炸等不安全事故。
经过多年的生产实践,第三代 CMC 技术的效果是:采用 CMC 技术后,煤料含水量每降低 1%,炼焦耗热量就降低约50.0MJ/t(干煤)。
当煤料水分从 10%下降至 6%时,炼焦耗热量相当于节省了200MJ/t。
由于装炉煤水分的降低,使装炉煤堆密度提高,干馏时间缩短,因此,焦炉生产能力可以提高约 4~10%。
改善焦炭质量,其 DI 值可提高 1~1.5 个百分点。
煤料水分的降低可减少 1/3 的剩余氨水量,相应减少剩余氨水蒸氨用蒸汽 1/3。
同时也减轻了废水处理装置的生产负荷。
节能的社会效益是减少温室效应,平均每吨入炉煤可减少约35.8kg 的CO2排放量。
因煤料水分稳定在 6%的水平上,使得煤料的堆密度和干馏速度稳定,有益于改善高炉的操作状态,有利于高炉的降耗高产。
煤料水分的稳定可保持焦炉操作的稳定,延长焦炉寿命。
采用流化床 CMC 所带来的问题是:煤料水分的降低,使炭化室荒煤气中的夹带物增加,使粗焦油中的渣量增加 2~3 倍,为此,设置了三相超级离心机,保证了焦油质量。
炭化室炉墙和上升管结石墨有所增加,为此,设置了除石墨设施,有效地清除了石墨,保证了正常生产。
调湿后煤料用皮带输送机送至煤塔过程中散发的粉尘量较湿煤增加了1.5 倍。
四、技术适用条件煤调湿技术是煤预热技术发展而来的。
与第一代和第二代CMC相比,第三代流化床CMC 技术工艺流程短,设备少且结构简单,具有投资省、操作成本低、便于检修、占地面积小及节能减排效果明显等优点。
根据煤调湿技术项目投资经济效益分析得知,只有炼焦煤水分含量超过9.5%的焦化企业,煤调湿技术投资内部收益率才能超过8%社会投资收益率,建设煤调湿装置才是经济的。
为此,从投资回报率角度看,我国南方、沿海及东北地区比较适合建设煤调湿装置。
三种煤调湿技术的适用范围下:导热油煤调湿技术操作环节多、投资高。
因此,现有导热油煤调湿技术需经改进后,才可以在独立焦化企业推广。
蒸汽煤调湿技术不节能还耗能,不能作为节能技术大力推广。
可以用于有富余低压蒸汽的钢铁联合企业。
烟道气煤调湿技术(第三代煤调湿技术)已经成熟,是比较理想的节能环保技术,符合国家节能方针政策。
五、CMC技术的优点及节能减排效果随着国内炼焦行业的快速发展,主炼焦煤即焦煤越来越紧张,因此增大弱粘结煤的配比势在必行。
而CMC技术从工艺以及实际操作经验上,可以解决此问题。
CMC具有以下主要优点:(1)、入炉煤堆密度增加据计算,每降低1%的水分,堆密度相应增加1.0%~1.5%,从而达到在炭化室有效容积不变的情况下,可以多装煤,从而达到增产的效果。
按水分降低4%计,可增产4~6%。
(2)、焦炉结焦时间缩短每降低1%的水分可以缩短结焦时间为0.5~1.0%,据此可以增加每天的出焦孔数。
因此也能增加焦炭产量。
(3)、每降低1%的水分,焦炭强度可以增加到0.15~0.2%,在保持原来的焦炭强度条件下,可以增加弱粘结煤的配煤比例。
一般情况下,可以增加5~8%的弱粘煤,具体数值要根据生产过程中对煤种进行试验确定。
(4)、由于入炉煤水分的降低,可以降低炼焦耗热量,每降低1%的水分可以节省41.8~83.6MJ∕t 煤的能源。
(5)、由于入炉煤总水分的降低,剩余氨水量降低,可以减少焦化污水的处理量。
节能减排效果(1)、改善炼焦煤的粒度组成,各粒级煤质变化趋于均匀;(2)、装炉煤堆积密度提高约5%,提高焦炉生产能力4%~10%;(3)、提高焦炭强度:M40提高1%~2.5%,M10改善0.5%~1.5%;(4)、焦炭反应性降低0.5%~2.5%,反应后强度提高0.2%~2.5%;(5)、降低炼焦耗热量约5%;节约焦炉加热煤气,装炉煤含水量每下降1个百分点,炼焦耗热量可降低45~60MJ/t。
当装炉煤含水量下降4个百分点时,可节省炼焦耗热量180~240MJ/t,相当于节约焦炉加热煤气 (混合煤气热值4000kJ/m3)45~60m3/t,折合标煤6.1~8.2kg/t。
(6)、减少废水排放,可减排蒸氨废水30~40kg/t,节约蒸氨用蒸汽6~8kg/t。
(7)、提高高炉生产能力1%~2%。
六、技术推广应用情况由于煤调湿技术显著的节能效果,近二十年来,日本先后开发了三代煤调湿技术,煤调湿技术在日本得到普遍的应用和推广。
各厂煤调湿装置基本都是将装炉煤水分由9%降到5%~6%。
截至2009年12月,日本共有15家焦化厂,47组(座)焦炉,其中有33组(座)焦炉配置煤调湿装置,占炉组(座)总数的70.2%,其中流化床4套,间接加热回转式10套。
1983年9月,第一代导热油煤调湿装置在日本大分厂建成投产。
日本新能源产业技术开发机构(简称NEDO)于1993~1996 年在我国重庆钢铁(集团)公司实施的―煤炭调湿设备示范事业‖就是第一代煤调湿技术。
处理能力140t/h,干燥器入口煤的水分11.0%,干燥器出口煤的水分6.5%,此套系统经调试后,由于多种原因没有顺利运行,现已闲置荒废。