FANUC数控主轴参数应用
fanuc主轴停止减速参数
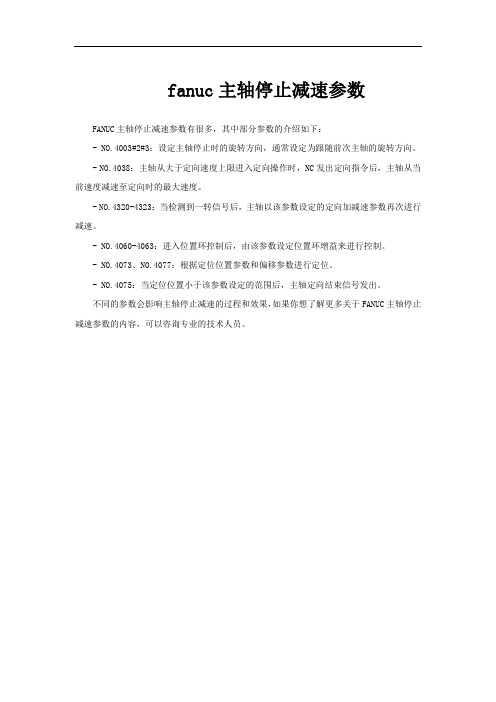
fanuc主轴停止减速参数
FANUC主轴停止减速参数有很多,其中部分参数的介绍如下:
- NO.4003#2#3:设定主轴停止时的旋转方向,通常设定为跟随前次主轴的旋转方向。
- NO.4038:主轴从大于定向速度上限进入定向操作时,NC发出定向指令后,主轴从当前速度减速至定向时的最大速度。
- NO.4320-4323:当检测到一转信号后,主轴以该参数设定的定向加减速参数再次进行减速。
- NO.4060-4063:进入位置环控制后,由该参数设定位置环增益来进行控制。
- NO.4073、NO.4077:根据定位位置参数和偏移参数进行定位。
- NO.4075:当定位位置小于该参数设定的范围后,主轴定向结束信号发出。
不同的参数会影响主轴停止减速的过程和效果,如果你想了解更多关于FANUC主轴停止减速参数的内容,可以咨询专业的技术人员。
13FANUC PMC应用实例—主轴正反转控制
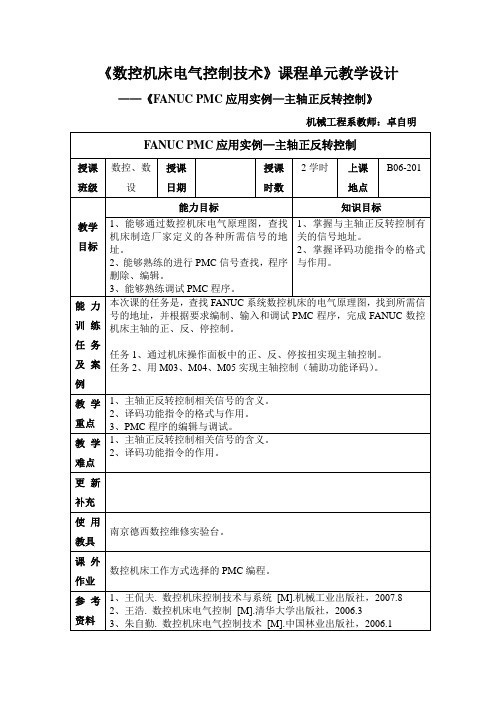
《数控机床电气控制技术》课程单元教学设计——《FANUC PMC应用实例—主轴正反转控制》
机械工程系教师:卓自明
(2)由CNC向PMC发送F选通信号,主要涉及到加工程序中的M、S、T指令。
例如:M03 S500
T0101
M08
注意:主轴停止按扭本身是常闭的,所以我们在编制梯形图时应注意什么呢?
)编制完梯形图后,运行调试
点后退键2次→找到RUN,点RUN运行梯形图→按
运行状态。
PMCLAD理解和调试梯形图。
注意:“机床\面板”钮子开关应该拨到机床侧,这样机床操作面板上的按扭才能起作用。
、教师检查并点评各组完成情况
每组随机抽取一名学生,检查程序编辑与调试运行情况,依此作为该组的整体成
当执行M03时,F7.0为高电平,
(4)编制完梯形图后,进行运行调试
在MDI方式下→输入EOB分号→INSERT→输入
我们以标准机床操作面板为例,信号地址如下:
附:学生任务单姓名:序号:。
fanuc数控系统参数表

fanuc数控系统参数表FANUC系统有很丰富的机床参数,为数控机床的安装调试及日常维护带来了方便条件。
根据多年的实践,对常用的机床参数在维修中的应用做一介绍。
1.手摇脉冲发生器损坏。
一台FANUC 0TD数控车床,手摇脉冲发生器出现故障,使对刀不能进行微调,需要更换或修理故障件。
当时没有合适的备件,可以先将参数900#3置“0”,暂时将手摇脉冲发生器不用,改为用点动按钮单脉冲发生器操作来进行刀具微调工作。
等手摇脉冲发生器修好后再将该参数置“1”。
2.当机床开机后返回参考点时出现超行程报警。
上述机床在返回参考点过程中,出现510或511超程报警,处理方法有两种:(1)若X轴在返回参考点过程中,出现510或是511超程报警,可将参数0700LT1X1数值改为+99999999(或将0704LT1X2数值修改为-99999999)后,再一次返回参考点。
若没有问题,则将参数0700或0704数值改为原来数值。
(2)同时按P和CAN键后开机,即可消除超程报警。
3.一台FANUC 0i数控车床,开机后不久出现ALM701报警。
从维修说明书解释内容为控制部上部的风扇过热,打开机床电气柜,检查风扇电机不动作,检查风扇电源正常,可判定风扇损坏,因一时购买不到同类型风扇,即先将参数RRM8901#0改为“1”先释放ALM701报警,然后在强制冷风冷却,待风扇购到后,再将PRM8901改为“0”。
4.一台FANUC 0M数控系统加工中心,主轴在换刀过程中,当主轴与换刀臂接触的一瞬间,发生接触碰撞异响故障。
分析故障原因是因为主轴定位不准,造成主轴头与换刀臂吻合不好,无疑会引起机械撞击声,两处均有明显的撞伤痕迹。
经查,换刀臂与主轴头均无机械松动,且换刀臂定位动作准确,故采用修改N6577参数值解决,即将原数据1525改为1524后,故障排除。
5.密级型参数0900~0939维修法。
按FANUC 0MC操作说明书的方法进行参数传输时,密级型参数0900~0939必须用MDI方式输入很不方便。
fanuc数控系统常用参数表
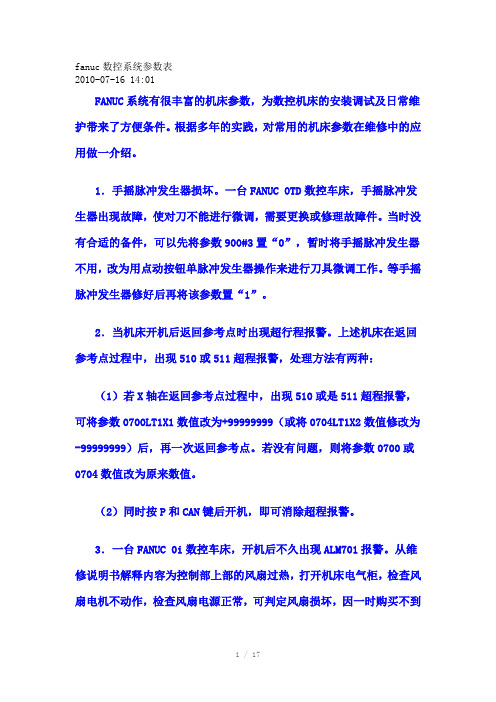
fanuc数控系统参数表2010-07-16 14:01FANUC系统有很丰富的机床参数,为数控机床的安装调试及日常维护带来了方便条件。
根据多年的实践,对常用的机床参数在维修中的应用做一介绍。
1.手摇脉冲发生器损坏。
一台FANUC 0TD数控车床,手摇脉冲发生器出现故障,使对刀不能进行微调,需要更换或修理故障件。
当时没有合适的备件,可以先将参数900#3置“0”,暂时将手摇脉冲发生器不用,改为用点动按钮单脉冲发生器操作来进行刀具微调工作。
等手摇脉冲发生器修好后再将该参数置“1”。
2.当机床开机后返回参考点时出现超行程报警。
上述机床在返回参考点过程中,出现510或511超程报警,处理方法有两种:(1)若X轴在返回参考点过程中,出现510或是511超程报警,可将参数0700LT1X1数值改为+99999999(或将0704LT1X2数值修改为-99999999)后,再一次返回参考点。
若没有问题,则将参数0700或0704数值改为原来数值。
(2)同时按P和CAN键后开机,即可消除超程报警。
3.一台FANUC 0i数控车床,开机后不久出现ALM701报警。
从维修说明书解释内容为控制部上部的风扇过热,打开机床电气柜,检查风扇电机不动作,检查风扇电源正常,可判定风扇损坏,因一时购买不到同类型风扇,即先将参数RRM8901#0改为“1”先释放ALM701报警,然后在强制冷风冷却,待风扇购到后,再将PRM8901改为“0”。
4.一台FANUC 0M数控系统加工中心,主轴在换刀过程中,当主轴与换刀臂接触的一瞬间,发生接触碰撞异响故障。
分析故障原因是因为主轴定位不准,造成主轴头与换刀臂吻合不好,无疑会引起机械撞击声,两处均有明显的撞伤痕迹。
经查,换刀臂与主轴头均无机械松动,且换刀臂定位动作准确,故采用修改N6577参数值解决,即将原数据1525改为1524后,故障排除。
5.密级型参数0900~0939维修法。
按FANUC 0MC操作说明书的方法进行参数传输时,密级型参数0900~0939必须用MDI方式输入很不方便。
发那科车床4002参数说明
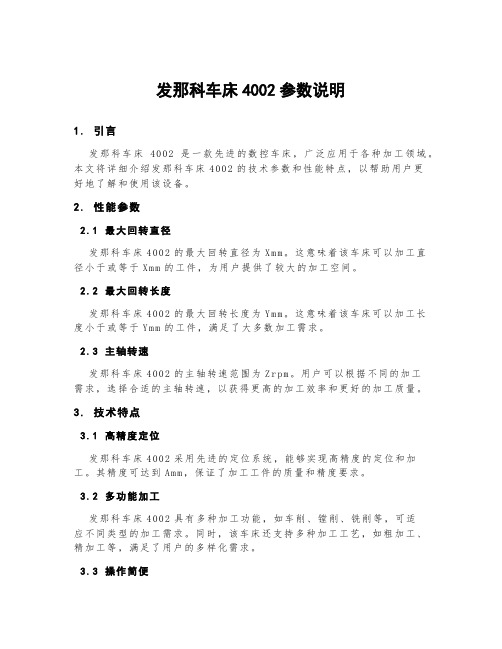
发那科车床4002参数说明1.引言发那科车床4002是一款先进的数控车床,广泛应用于各种加工领域。
本文将详细介绍发那科车床4002的技术参数和性能特点,以帮助用户更好地了解和使用该设备。
2.性能参数2.1最大回转直径发那科车床4002的最大回转直径为X mm。
这意味着该车床可以加工直径小于或等于Xm m的工件,为用户提供了较大的加工空间。
2.2最大回转长度发那科车床4002的最大回转长度为Y mm。
这意味着该车床可以加工长度小于或等于Ym m的工件,满足了大多数加工需求。
2.3主轴转速发那科车床4002的主轴转速范围为Z rpm。
用户可以根据不同的加工需求,选择合适的主轴转速,以获得更高的加工效率和更好的加工质量。
3.技术特点3.1高精度定位发那科车床4002采用先进的定位系统,能够实现高精度的定位和加工。
其精度可达到Am m,保证了加工工件的质量和精度要求。
3.2多功能加工发那科车床4002具有多种加工功能,如车削、镗削、铣削等,可适应不同类型的加工需求。
同时,该车床还支持多种加工工艺,如粗加工、精加工等,满足了用户的多样化需求。
3.3操作简便发那科车床4002采用用户友好的界面设计,使操作变得简单易懂。
操作人员只需要简单的培训即可掌握车床的操作技巧,提高了生产效率和操作的便利性。
3.4高效节能发那科车床4002采用先进的节能技术,减少了对能源的消耗。
该车床在保证加工效率的同时,降低了能源消耗,节约了生产成本,并对环境保护起到了积极的作用。
4.应用领域发那科车床4002广泛应用于各种加工领域,包括但不限于以下几个方面:航空航天-:用于制造飞机零部件、航天器零部件等;汽车制造-:用于制造发动机零部件、车身零部件等;模具加工-:用于制作模具及相关零件,提供高精度的加工服务;通用机械-:用于制造各类机械零部件,满足不同行业的加工需求。
5.结论通过本文的介绍,我们可以看出发那科车床4002具有较高的加工精度和多功能加工能力。
FANUC数控系统主轴参数

FANUC数控系统主轴参数1. 主轴转速(Spindle Speed)主轴转速是指主轴每分钟旋转的圈数,通常以转/分钟(rpm)为单位。
FANUC数控系统通常具有高精度的主轴调速系统,可以根据加工要求调节主轴转速,以满足不同工件材料和加工方式的需求。
2. 主轴加速度(Spindle Acceleration)主轴加速度是指主轴从静止状态加速到设定转速时所需的时间。
在精密加工中,主轴加速度的快慢对加工质量、工件表面质量和主轴寿命都有重要影响。
FANUC数控系统通常具有大范围的主轴加速度调节功能,可以根据不同工艺要求进行调整。
3. 主轴减速度(Spindle Deceleration)主轴减速度是指主轴从设定转速减速到静止状态所需的时间。
主轴减速度的合理设置可以保证主轴停止后位置的精度,减少工件因主轴停转而产生的负面影响。
FANUC数控系统通常具有调整主轴减速度的功能,可以根据工件的要求和机床性能进行调整。
4. 主轴定位精度(Spindle Positioning Accuracy)主轴定位精度是指主轴停止后,在指定位置能够保持的精度。
在高精度加工中,主轴定位精度对工件的加工精度至关重要。
FANUC数控系统通常具有高精度的主轴定位控制系统,可以保证主轴在停止后的位置精度。
5. 主轴控制方式(Spindle Control Mode)主轴控制方式是指主轴的启停和转速控制方式。
FANUC数控系统通常具有多种主轴控制方式,如手动控制、自动控制、远程控制等。
不同的主轴控制方式可以满足不同的加工需求。
6. 主轴力矩(Spindle Torque)主轴力矩是指主轴旋转时所产生的力矩。
主轴力矩的大小决定了机床能够承受的加工负荷,对于大型工件的加工尤为重要。
FANUC数控系统通常可以根据加工要求调整主轴力矩,以适应不同的工作情况。
7. 主轴冷却方式(Spindle Cooling Method)主轴冷却方式是指主轴散热的方式。
FANUC数控系统轴设定参数的调试
0:移动指令按半径规格指令 1:移动指令按直径规格指令
X
半径 Z
直径
学习任务四:参数全清后的恢复
设定正 确否?
学习任务四:参数全清后的恢复
学习任务四:参数全清后的恢复
学习任务四:参数全清后的恢复
学习任务四:参数全清后的恢复
学习任务四:参数全清后的恢复
轴名称设定
参数 1020
X:88 Y:89 Z:90
#2
#1
#0
CTBx CTLx
学习任务四:参数全清后的恢复
参数 1620 各轴快速移动直线型加减速时间常数T或铃型加减速时间常数T1 各轴快速移动加减速时间常数。
设定值:50-200
直线加减速
学习任务四:参数全清后的恢复
参数 1621
各轴快速移动铃型加减速时间常数T2
各轴快速移动铃型加减速时间常数T2。
学习任务四:参数全清后的恢复
学习任务四:参数全清后的恢复
学习任务四:参数全清后的恢复
学习任务四:参数全清后的恢复
学习任务四:参数全清后的恢复
无挡块回零参数设定
1.设置如下参数
1005#1=1:选择返回参考点方式。0:有挡块。1:无挡块 1006#5=0:选择返回参考点方向。0:正方向,1:负方向 1428=1000:每个轴的参考点返回速度 2.将参数1815#5设为1。此时系统会报警“PW0000必需关断电源”,切断NC电
各轴点动进给加减速时间常数 各轴点动进给指数加减速的FL速度
20分钟
学习任务四:参数全清后的恢复
学习任务四:参数全清后的恢复
参数 1825
各轴位置环增益(0.01sec )
• 设定伺服响应,标准值设定为3000。
FANUC数控系统主轴参数的应用(精)
FANUC数控系统主轴参数的应⽤(精)FANUC数控系统主轴参数的应⽤为了满⾜⽤户的切削要求, 充分发挥主轴电动机的切削功率, 主轴速度⼀般被划分成⼏档, 其档位转换靠齿轮变速箱来实现。
以主轴电动机的最⾼限定速度来划分, 主轴的换档存在着两种形式。
⼀种是主轴各个档位的最⾼转速所对应的主轴电动机最⾼速度相同。
例如 XH756 卧式加⼯中⼼。
另⼀种是主轴各个档位的最⾼转速所对应的主轴电动机最⾼限定速度不同。
这种情况主要是在机械设计中由于某些原因⽽作特殊设计时, 需要电⽓进⾏完善。
例如我⼚的XH716⽴式加⼯中⼼。
FANUC-0i 数控系统充分考虑了这两种情况 , 把它们分为齿轮换档⽅式A和B 。
下⾯以XH756 和XH716 为例简要介绍齿轮换档参数的巧妙应⽤。
1 齿轮换档⽅式A如图1 所⽰, 主轴的3 档位所对应的主轴电动机最⾼限定速度是相同的。
例如我⼚的XH756 卧式加⼯中⼼, 主轴低档的齿轮传动⽐为11:108, 中档的齿轮传动⽐为11:36, ⾼档的齿轮传动⽐为11:12; 机械设计要求主轴低档时的转速范围是0-458r/min, 中档的转速范围是459-1375r/min, ⾼档的转速范围是1376-4125r/min, 主轴电动机的最低速度限定为 150r/min。
主轴电动机给定电压为10V 时 , 对应的主轴电动机速度为6000r/min。
通过计算可知各个档位的主轴电动机最⾼转速相同,均为4500r/min。
此时参数应设定如下:参数N0.3736( 主轴速度上限,Vmax=4095×主轴电动机速度上限/指令电压10V 的主轴电动机速度) 设定为4095 × 4500/6000=3071。
参数N0.3735( 主轴速度下限,Vmax=4095×主轴电动机速度下限 / 指令电压为 10V 的主轴电动机速度) 设定为4095 ×150/6000=102。
FANUC常用参数
FANUC常用参数1.报警处理参数(ALM)这些参数用于设置系统报警的处理方式,例如报警终止的条件、报警信息的显示等。
2.坐标系参数(G54~G59)这些参数用于设置工件坐标系的原点和轴向移动的距离。
3.速度参数(F、S、G96~G97)这些参数用于设置切削进给速度、切削用途的材料速度等。
4.转速参数(M3、M4、M5)这些参数用于设置主轴的转速和方向。
5.工具偏移参数(G43、G44、G48)这些参数用于设置和调整工具补偿的位置。
6.急停参数(M0、M1)这些参数用于设置急停的条件和执行急停操作。
7.程序调用参数(M98、M99)这些参数用于调用和执行子程序。
8.伺服参数(SV、SET)这些参数用于设置伺服轴的速度和位置。
9.插补误差参数(G96、G97、G98、G99)这些参数用于设置插补误差补偿的方式和值。
10.自动换刀参数(T、M6)这些参数用于自动换刀操作,设置刀具编号和刀具长度补正值。
11.平台控制参数(G160~G169)这些参数用于配置和控制机床上的附加设备,例如自动上下料机等。
12.快速移动参数(G00)这些参数用于设置快速移动的速度和方式。
13.进给速度参数(G94、G95)这些参数用于设置进给速度单位和进给速度值。
14.反向间隙参数(G41、G42)这些参数用于设置反向间隙的值和位置。
15.加工参数(G01、G02、G03)这些参数用于设置不同的加工方式,例如直线插补、圆弧插补等。
以上是一些常用的FANUC参数示例,不同的机床和加工过程可能会有所差异。
在操作FANUC数控系统时,正确设置和调整这些参数是非常重要的,可以确保机床正常运行,并且获得高质量的加工结果。
FANUC主轴定向的调试步骤,这么详细的教程不多了
FANUC主轴定向的调试步骤,这么详细的教程不多了
主轴定向是使主轴停⽌在某个特定位置的功能,常见的有主轴电机内置传感器定向(要求编码
器有index点)和外置接近开关定向(常⽤在⾮1:1传动时)以及位置编码器定向。
⼀、主轴电机内置传感器定向
参数设置:
定向速度:#3732=4038=200
定向刚性:#4060~4063=1000~3000
其他参数如下表所⽰:
⼆、外置接近开关定向(常⽤于⾮1:1传动时)
参数设置:
定向速度:#3732=4038=50~100(为了稳定的检测⼀转信号,适当降低定向速度)
定向刚性:#4060~4063=1000~3000
具体参数设置如下表:
三、位置编码器定向(⼀般⽤于对主轴位置控制要求较⾼的场合)
参数设置:
旨在共享电⽓知识,提升数控⽔平。
跟随我们的脚步,你就会成为电⽓⾼⼿。
分享、努⼒、感恩。
⼩编都这么努⼒了,你们还有什么理由不拼⼀下。
最后给⼩编点个赞再⾛呗。
- 1、下载文档前请自行甄别文档内容的完整性,平台不提供额外的编辑、内容补充、找答案等附加服务。
- 2、"仅部分预览"的文档,不可在线预览部分如存在完整性等问题,可反馈申请退款(可完整预览的文档不适用该条件!)。
- 3、如文档侵犯您的权益,请联系客服反馈,我们会尽快为您处理(人工客服工作时间:9:00-18:30)。
FANUC数控系统主轴参数的应用
为了满足用户的切削要求, 充分发挥主轴电动机的切削功率, 主轴速度一般被划分成几档, 其档位转换靠齿轮变速箱来实现。
以主轴电动机的最高限定速度来划分, 主轴的换档存在着两种形式。
一种是主轴各个档位的最高转速所对应的主轴电动机最高速度相同。
例如 XH756 卧式加工中心。
另一种是主轴各个档位的最高转速所对应的主轴电动机最高限定速度不同。
这种情况主要是在机械设计中由于某些原因而作特殊设计时, 需要电气进行完善。
例如我厂的XH716 立式加工中心。
FANUC-0i 数控系统充分考虑了这两种情况 , 把它们分为齿轮换档方式A 和B 。
下面以XH756 和XH716 为例简要介绍齿轮换档参数的巧妙应用。
1 齿轮换档方式A
如图1 所示, 主轴的3 档位所对应的主轴电动机最高限定速度是相同的。
例如我厂的XH756 卧式加工中心, 主轴低档的齿轮传动比为11:108, 中档的齿轮传动比为11:36, 高档的齿轮传动比为11:12; 机械设计要求主轴低档时的转速范围是0-458r/min, 中档的转速范围是459-1375r/min, 高档的转速范围是1376-4125r/min, 主轴电动机的最低速度限定为 150r/min。
主轴电动机给定电压为10V 时 , 对应的主轴电动机速度为6000r/min。
通过计算可知各个档位的主轴电动机最高转速相同,均为4500r/min。
此时参数应设定如下:参数N0.3736( 主轴速度上限,Vmax=4095×主轴电动机速度上限/指令电压 10V 的主轴电动机速度) 设定为4095 × 4500/6000=3071。
参数N0.3735( 主轴速度下限,Vmax=4095×主轴电动机速度下限 / 指令电压为 10V 的主轴电动机速度) 设定为4095 ×150/6000=102。
参数N0.3741( 指令电压10V 时对应的主轴速度A, 低档 ) 设定为6000 ×11/108=611。
参数N0.3742( 指令电压10V 时对应的主轴速度B, 中档 ) 设定为6000 ×11/12=1833 。
参数N0.3743( 指令电压10V 时对应的主轴速度C, 高档 ) 设定为6000 ×11/12=5500 。
按照以上参数设定, 该机床速度范围合理覆盖, 并在PMC 程序中自动判别, 合理选择档位。
图1
2 齿轮换档方式 B 如图2 所示, 主轴的
3 个档位所对应的主轴电动机最高限定速度是不同的。
例如主轴低档齿轮传动比为11:108, 主轴中档齿轮传动比为260:1071, 主
轴高档齿轮传动比为169: 238, 而机械设计要求主轴低档的转速范围是0-401r/min, 主轴中挡的转速范围是402-1109r/min, 主轴高档的转速范围是1110-3000r/min。
主轴电动机给定电压为10V 时, 对应的主轴电动机转速为6000r/min, 主轴电动机的速度下限为150r/min。
计算可知, 主轴低档使用的电动机最高转速为401×108/11=3937r/min, 主轴中档使用的电动机最高转速为1109×1071/260=4568r/min, 主轴高档使用的电动机最高转速为4000×238/169=5633r/min,3个档位所对应的主轴电动机最高限定速度各不相同。
此时, 参数N0.3736 设定为4095 ×5633/6000=3844( 以主轴电动机速度最高档位设定, 此例为高档), 参数NO.3735 设定为4095×150/6000=102, 参数NO.3741设定为6000 ×11/108=611, 参数N0.3742 设定为6000× 260/1071=1457, 参数N0.3743 设定为6000×169/238=4260。
仅按以上参数设定后, 主轴实际转速低档将为15 - 573r/min, 中档将为574 - 1367r/min, 高档将为1367 - 4000r/min。
这就不符合机械设计要求, 给自动判别带来困难。
为了弥补这个缺陷, 在齿轮换档方式B中, 可以使用参数NO.3751 和 NO.3752来限制主轴的转速。
参数N0.3751( 主轴从低档切换到中档时切换点的主轴电动机速度,Vmaxl=4095×低档时主轴电动机速度上限 / 指令电压为10V的主轴电动机速度) 设定为4095×3937/6000=2687。
参数N0.3752( 主轴从中档切换到高档时切换点的主轴电动机速度,Vmaxh=4095×高档时主轴电动机速度上限 / 指令电压为10V 的主轴电动机速度) 设定为4095×4568/6000=3118。
此方式参数的设定, 合理解决了各档主轴电动机上限速度不同给自动换档带来的麻烦。
图2
3 结束语
通过以上事例的分析, 我们必须充分结合机械设计特点, 结合PMC 程序的要求, 合理使用数控系统提供的参数功能, 对控制系统的功能做到尽善尽美的应用。