粗糙度轮廓仪检验记录表
粗糙度轮廓仪日常保养点检记录表
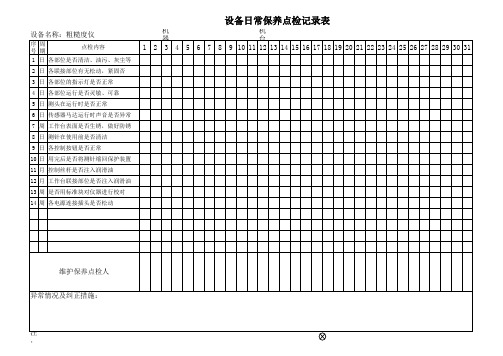
维护保养点检人 异常情况及纠正措施:
注 :
设备名称:粗糙度仪
序周 号期
点检内容
1 日 各部位是否清洁、油污、灰尘等
2 日 各联接部位有无松动,紧固否
3 日 各部位的指示灯是否正常
4 日 各部位运行是否灵敏、可靠
5 日 测头在运行时是否正常
6 日 传感器马达运行时声音是否异常
7 周 工作台表面是否生锈,做好防锈
8 日 测针在使用前是否清洁
9 日 各控制按钮是否正常
10 日 用完后是否将测针缩回保装置
11 月 控制丝杆是否注入润滑油
12 月 工作台联接部位是否注入润滑油
13 周 是否用标准块对仪器进行校对
14 周 各电源连接插头是否松动
设备日常保养点检记录表
机
机
器
台
1 2 3 4 5 6 7 8 9 10 11 12 13 14 15 16 17 18 19 20 21 22 23 24 25 26 27 28 29 30 31
粗糙度检测方法及评定【干货技巧】
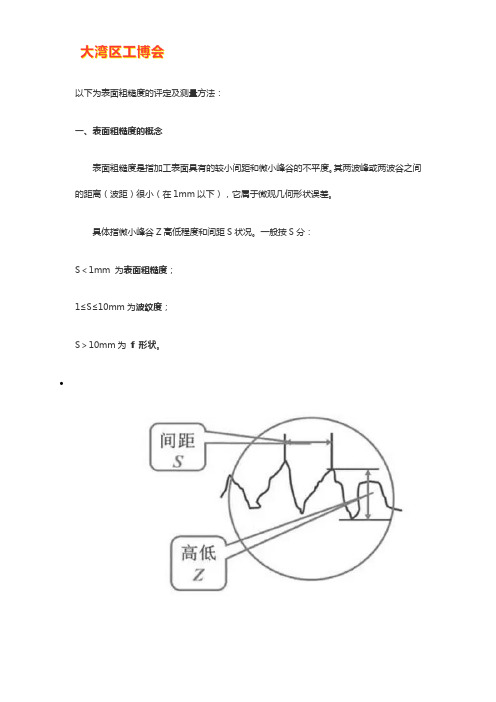
以下为表面粗糙度的评定及测量方法:一、表面粗糙度的概念表面粗糙度是指加工表面具有的较小间距和微小峰谷的不平度。
其两波峰或两波谷之间的距离(波距)很小(在1mm以下),它属于微观几何形状误差。
具体指微小峰谷Z高低程度和间距S状况。
一般按S分:S<1mm 为表面粗糙度;1≤S≤10mm为波纹度;S>10mm为f 形状。
•二、VDI3400、Ra、Rmax对照表国家标准规定常用三个指标来评定表面粗糙度(单位为μm):轮廓的平均算术偏差Ra、不平度平均高度Rz和最大高度Ry。
在实际生产中多用Ra指标。
轮廓的最大微观高度偏差Ry在日本等国常用Rmax符号来表示,欧美常用VDI指标。
下面为VDI3400、Ra、Rmax 对照表。
三、表面粗糙度形成因素表面粗糙度一般是由所采用的加工方法和其他因素所形成的,例如加工过程中刀具与零件表面间的摩擦、切屑分离时表面层金属的塑性变形以及工艺系统中的高频振动、电加工的放电凹坑等。
由于加工方法和工件材料的不同,被加工表面留下痕迹的深浅、疏密、形状和纹理都有差别。
四、表面粗糙度对零件的影响主要表现影响耐磨性。
表面越粗糙,配合表面间的有效接触面积越小,压强越大,摩擦阻力越大,磨损就越快。
影响配合的稳定性。
对间隙配合来说,表面越粗糙,就越易磨损,使工作过程中间隙逐渐增大;对过盈配合来说,由于装配时将微观凸峰挤平,减小了实际有效过盈,降低了连接强度。
影响疲劳强度。
粗糙零件的表面存在较大的波谷,它们像尖角缺口和裂纹一样,对应力集中很敏感,从而影响零件的疲劳强度。
影响耐腐蚀性。
粗糙的零件表面,易使腐蚀性气体或液体通过表面的微观凹谷渗入到金属内层,造成表面腐蚀。
影响密封性。
粗糙的表面之间无法严密地贴合,气体或液体通过接触面间的缝隙渗漏。
影响接触刚度。
接触刚度是零件结合面在外力作用下,抵抗接触变形的能力。
机器的刚度在很大程度上取决于各零件之间的接触刚度。
影响测量精度。
零件被测表面和测量工具测量面的表面粗糙度都会直接影响测量的精度,尤其是在精密测量时。
表面粗糙度的检测
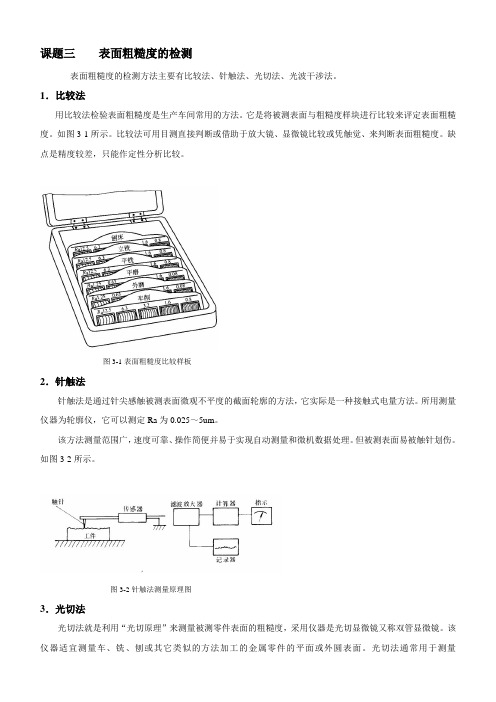
课题三表面粗糙度的检测表面粗糙度的检测方法主要有比较法、针触法、光切法、光波干涉法。
1.比较法用比较法检验表面粗糙度是生产车间常用的方法。
它是将被测表面与粗糙度样块进行比较来评定表面粗糙度。
如图3-1所示。
比较法可用目测直接判断或借助于放大镜、显微镜比较或凭触觉、来判断表面粗糙度。
缺点是精度较差,只能作定性分析比较。
图3-1表面粗糙度比较样板2.针触法针触法是通过针尖感触被测表面微观不平度的截面轮廓的方法,它实际是一种接触式电量方法。
所用测量仪器为轮廓仪,它可以测定Ra为0.025~5um。
该方法测量范围广,速度可靠、操作简便并易于实现自动测量和微机数据处理。
但被测表面易被触针划伤。
如图3-2所示。
图3-2针触法测量原理图3.光切法光切法就是利用“光切原理”来测量被测零件表面的粗糙度,采用仪器是光切显微镜又称双管显微镜。
该仪器适宜测量车、铣、刨或其它类似的方法加工的金属零件的平面或外圆表面。
光切法通常用于测量Ra=0.5~80µm的表面。
4.光波干涉法干涉显微镜是利用光波干涉原理测量表面粗糙度。
干涉显微镜测量的范围一般为0.03~1µm。
也可作Rz、Ry参数评定。
本课题结合课堂讲授的典型零件的标注,分析并检测表面粗糙度,根据国家标准评定表面粗糙度。
选用方法为光切法和光波干涉法。
实验3-1 用光切显微镜检测表面粗糙度一、实验目的1.了解用光切显微镜测量表面粗糙度的原理和方法2.正确理解表面粗糙度的评定参数,加深对微观不平度十点高度Rz的理解二、测量原理及仪器说明双管显微镜又撑光切显微镜,它是利用被测表面能反射光的特性,根据“光切法原理”制成的光学仪器,R=0.8-80um的表面粗糙度。
其测量范围取决于选用的物镜的放大倍数,一般用于测量Z图3-3光切显微镜1—底座;2—立柱;3—升降螺母;4—微调手轮;5—支臂;6—支臂锁紧螺钉;7—工作台;8—物镜组;9—物镜锁紧机构;10—遮光板手轮;11—壳体;12—目镜测微器;13—目镜仪器外型如图3-3所示,它由底座6,支柱5,横臂2,测微目镜13,可换物镜8及工作台7等部分组成。
粗糙度轮廓仪测量误差分析
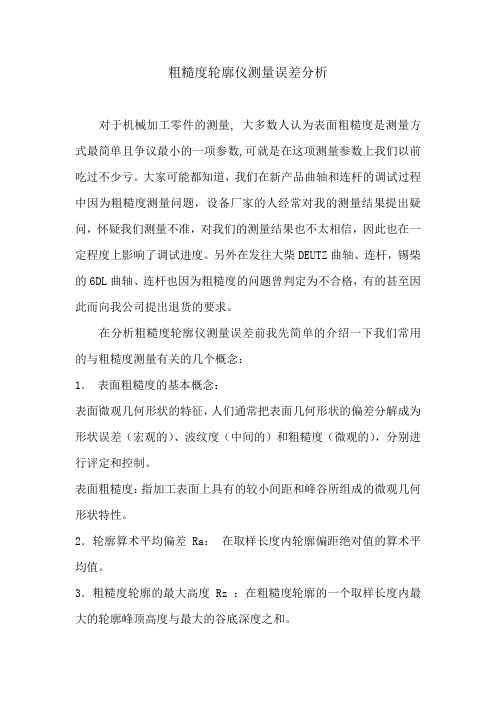
粗糙度轮廓仪测量误差分析对于机械加工零件的测量, 大多数人认为表面粗糙度是测量方式最简单且争议最小的一项参数,可就是在这项测量参数上我们以前吃过不少亏。
大家可能都知道,我们在新产品曲轴和连杆的调试过程中因为粗糙度测量问题,设备厂家的人经常对我的测量结果提出疑问,怀疑我们测量不准,对我们的测量结果也不太相信,因此也在一定程度上影响了调试进度。
另外在发往大柴DEUTZ曲轴、连杆,锡柴的6DL曲轴、连杆也因为粗糙度的问题曾判定为不合格,有的甚至因此而向我公司提出退货的要求。
在分析粗糙度轮廓仪测量误差前我先简单的介绍一下我们常用的与粗糙度测量有关的几个概念:1.表面粗糙度的基本概念:表面微观几何形状的特征,人们通常把表面几何形状的偏差分解成为形状误差(宏观的)、波纹度(中间的)和粗糙度(微观的),分别进行评定和控制。
表面粗糙度:指加工表面上具有的较小间距和峰谷所组成的微观几何形状特性。
2.轮廓算术平均偏差Ra:在取样长度内轮廓偏距绝对值的算术平均值。
3.粗糙度轮廓的最大高度 Rz :在粗糙度轮廓的一个取样长度内最大的轮廓峰顶高度与最大的谷底深度之和。
5.粗糙度的测量方法:粗糙度的测量方法通常有:比较法、印模法、光切法、干涉法和针描法等。
表面粗糙度测量方法中应用最广的是针描法。
它具有性能稳定,测量迅速,数字显示,放大倍数高,使用方便等优点,因此在计量室和生产现场都获得广泛应用,现在我公司及大柴、锡柴使用的粗糙度轮廓仪的原理就是这种方法。
下面我从针描法测量的机械原理和人员操作上简单分析粗糙度轮廓仪测量时产生的误差:一、测量方向的不同将引起不同的测量结果:粗糙度测量时应垂直于加工痕迹的的方向上进行。
不能确定加工痕迹的和非切削加工表面,应在几个不同的方向上进行测量,取恰当的值作为测量结果。
图1:对于测量方向与加工方向结果见图:a)表示测量方向的示意图 b)不同测量方向的轮廓形状二、不应在有表面缺陷的位置测量粗糙度:在表面粗糙度评定中不应把表面缺陷,如气孔、划痕、沟槽等包含进行去,也不应作为表面粗糙度合格与否的指标。
轮廓度仪日常点检保养记录表

1 校准标签在有效期之内
工作环境符合要求
2 温度20±5℃
湿度40%-70%RH
每
个
3
大理石工作台完好、清 洁、无杂物
工 作
4 导轨清洁无异物
日
5 开机正常无异响
6 打印输出正常
7 测量块校正正常
每 月
8 清洁导轨并润滑
半 年
点检保养人员
异常状况及处理措施
备注:设备正常打“√ ”,设备异常打“×”。保养异常及设备缺陷记录到异常状况及处理措施上,并及时通知检修班长及设备部或厂家进行维修, 严禁操作人员对设备及线路进行拆卸。
保养异常及设备缺陷记录到异常状况及处理措施上并及时通知检修班长及设备部或厂家进行维修严禁操作人员对设备及线路进行拆卸
设备日常点检保养记录表
设备名称:轮廓度仪
设备型号:
编号:
车间主任:
20 年 月
序 号项目要求频 次123
4
5
6
7
8
9 10 11 12 13 14 15 16 17 18 19 20 21 22 23 24 25 26 27 28 29 30 31
轮廓仪操作指导书
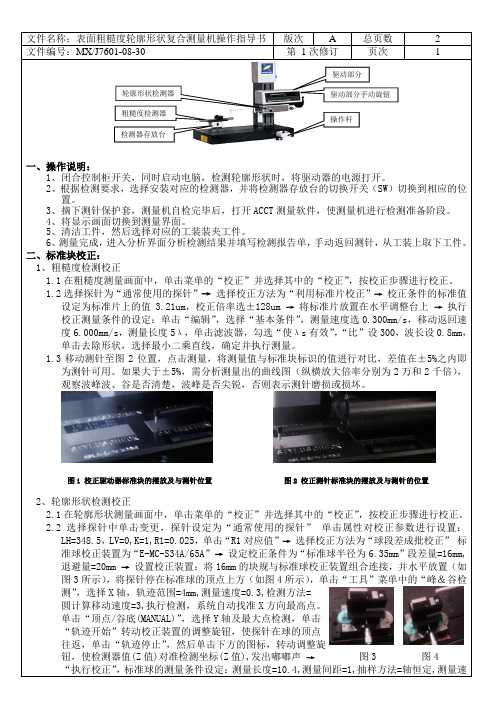
文件名称:表面粗糙度轮廓形状复合测量机操作指导书 版次 A 总页数 2 文件编号:MX/J7601-08-30 第 1次修订 页次 1一、操作说明:1、闭合控制柜开关,同时启动电脑,检测轮廓形状时,将驱动器的电源打开。
2、根据检测要求,选择安装对应的检测器,并将检测器存放台的切换开关(SW )切换到相应的位置。
3、摘下测针保护套,测量机自检完毕后,打开ACCT 测量软件,使测量机进行检测准备阶段。
4、将显示画面切换到测量界面。
5、清洁工件,然后选择对应的工装装夹工件。
6、测量完成,进入分析界面分析检测结果并填写检测报告单,手动返回测针,从工装上取下工件。
二、标准块校正: 1、粗糙度检测校正1.1在粗糙度测量画面中,单击菜单的“校正”并选择其中的“校正”,按校正步骤进行校正。
1.2选择探针为“通常使用的探针”→ 选择校正方法为“利用标准片校正”→ 校正条件的标准值设定为标准片上的值3.21um ,校正倍率选±128um → 将标准片放置在水平调整台上 → 执行校正测量条件的设定:单击“编辑”,选择“基本条件”,测量速度选0.300mm/s ,移动返回速度6.000mm/s ,测量长度5λ,单击滤波器,勾选“使λs 有效”,“比”设300,波长设0.8mm ,单击去除形状,选择最小二乘直线,确定并执行测量。
1.3移动测针至图2位置,点击测量,将测量值与标准块标识的值进行对比,差值在±5%之内即为测针可用。
如果大于±5%,需分析测量出的曲线图(纵横放大倍率分别为2万和2千倍),观察波峰波、谷是否清楚,波峰是否尖锐,否则表示测针磨损或损坏。
图1 校正驱动器标准块的摆放及与测针位置 图2 校正测针标准块的摆放及与测针的位置2、轮廓形状检测校正2.1在轮廓形状测量画面中,单击菜单的“校正”并选择其中的“校正”,按校正步骤进行校正。
2.2选择探针中单击变更,探针设定为“通常使用的探针” 单击属性对校正参数进行设置:LH=348.5,LV=0,K=1,R1=0.025,单击“R1对应值”→ 选择校正方法为“球段差成批校正” 标准球校正装置为“E-MC-S34A/65A ”→ 设定校正条件为“标准球半径为6.35mm ”段差量=16mm,退避量=20mm → 设置校正装置:将16mm 的块规与标准球校正装置组合连接,并水平放置(如图3所示),将探针停在标准球的顶点上方(如图4所示),单击“工具”菜单中的“峰&谷检测”,选择X 轴,轨迹范围=4mm,测量速度=0.3,检测方法= 圆计算移动速度=3,执行检测,系统自动找准X 方向最高点。
外观质量现场检测记录表
1备注:一级(合格率100%)100%^标准分,二级(合格率90%〜99.9%)90%^标准分,三级(合格率70%〜89.9%)70%^标准分,四级(合格率小于70%)得分为0。
渠道建筑物外观质量现场检测记录表(节制、分水、退水闸)备注:一级(合格率100%)得分为100%^标准分,二级(合格率90%〜99.9%)得分为90%^标准分,三级(合格率70%〜89.9%)得分为70%^标准分,四级(合格率小于70%)得分为0。
渠道建筑物外观质量现场检测记录表(节制、分水、退水闸续1)备注:一级(合格率100%)100%^标准分,二级(合格率90%〜99.9%)90%^标准分,三级(合格率70%〜89.9%)70%^标准分,四级(合格率小于70%)得分为0。
测量:记录:见证:昌吉州x干渠近期x检测记录表(混凝土交通桥)备注:一级(合格率100%)得分为100%^标准分,二级(合格率90%〜99.9%)得分为90%^标准分,三级(合格率70%〜89.9%)得分为70%^标准分,四级(合格率小于70%)得分为0。
测量:记录:见证:昌吉州xxxxx干渠近xxxx工程单位工程验收渠道建筑物外观质量现场检测记录表(混凝土交通桥续1)备注:一级(合格率100%)得分为100%^标准分,二级(合格率90%〜99.9%)得分为90%^标准分,三级(合格率70%〜89.9%)得分为70%^标准分,四级(合格率小于70%)得分为0。
测量:记录:见证100%100%^90%〜99.9%90%^70%〜89.9%70%^小于70%)得分为0。
测量:记录:见证:备注:一级(合格率100%)得分为100%^标准分,二级(合格率90%〜99.9%)得分为90%^标准分,三级(合格率70%〜89.9%)得分为70%^标准分,四级(合格率小于70%)得分为0。
测量:记录:见证9备注:一级(合格率100%)得分为100%^标准分,二级(合格率90%〜99.9%)得分为90%^标准分,三级(合格率70%〜89.9%)得分为70%^标准分,四级(合格率小于70%)得分为0。
粗糙度轮廓仪介绍
粗糙度轮廓仪介绍
粗糙度轮廓仪介绍
功能
可测量各种精密机械零件的素线形状,直线度、角度、凸度、对数曲线、槽深、槽宽等参数。
适用范围
本系列仪器广泛应用于机械加工、电机、汽配、摩配、精密五金、精密工具、刀具、模具、光学元件等行业。
适用于科研院所、大专院校、计量机构和企业计量室、车间。
可测轴承、滚针、滚子、电机轴、曲轴、圆柱销、活塞销、活塞、气门、阀门、齿轮、油泵油嘴、液压件、气动件、纺机配件等。
主要参数
导轨直线性系统精度:<0.2μm / 60 mm
测量长度:<100mm
Y 量程:4mm
电感传感器:1 / 4096
光栅尺:X向分辨率1μm,全长误差±1.5μm
可测零件直径:内圈 <300 mm,外圈可较大
气源压力:ㄒ0.45Mpa
环境要求:温度:10~30℃;相对湿度:<85%
功率需求:约400W;交流220V±10%,50Hz。
福达模具NC加工检查表
工序名称零件名称类别序号动静检查方法自检检查确认外观0※目视1※机床拉表2※粗糙度样块3※目视4※粗糙度样块/直尺5※直尺6※粗糙度样块/直尺/卡尺7※粗糙度样块/目视8※粗糙度样块/直尺9※机床拉表10※粗糙度样块11※机床检测12※※机床检测/粗糙度样块13※机床检测14※※机床检测/粗糙度样块15※粗糙度样块/目视16※目视/直尺17※直尺18※目视/直尺日期平整、宽度5-15mm.压边圈底面二级顶杆安位置按图纸尺寸点窝。
压边圈底面导板安装面长度、宽度符合图纸要求。
垂直度0.02≤100mm、平行度 0.02≤100mm、标注。
粗糙度=倒角=R10。
图纸尺寸、间隙0-0.05mm、标注。
垂直度0.02≤100mm、平行度 0.02≤100mm、标注。
粗糙度=压边圈侧基准面粗糙度= ,美观。
砸数清晰、整齐、准确。
压边圈内导滑面精度压边圈底面脐子粗糙度粗糙度= 。
上、下模底面键槽图纸尺寸、间隙0.05-0.1mm、标注上、下模压板感知面粗糙度= ,/符合图纸要求。
压边圈底面脐子平面度自然状态下≤0.05mm/㎡。
粗糙度= ,/符合图纸要求。
上、下模压板槽、压板面粗糙度= ,/符合图纸要求。
上、下模底面上的安装面粗糙度= /符合图纸要求。
如无公差标注,按尺寸加大0.1mm要求。
上、下模侧基准面粗糙度= 、美观。
砸数清晰、整齐、准确。
加工件外表卫生是否加工。
粗糙度= 。
自然状态下≤0.05mm/㎡。
铁屑、油泥、灰尘等。
检查项目检查要领福达模具NC加工检查表项目名称操作者本厂制号拉延类底面部分压边圈底面导板安装面精度压边圈底面导板安装面尺寸压边圈底面导板安装托台上、下模底面平面度上、下模底面粗糙度下模机床定位压边圈内导滑面尺寸1※粗糙度样块/目视2※卡尺3※目视4※目视5※※粗糙度样块/机床检测6※※粗糙度样块/机床检测7※※粗糙度样块/机床检测8※粗糙度样块9※※粗糙度样块/机床检测10※※粗糙度样块/机床检测11※粗糙度样块/手感12※粗糙度样块13※厚薄规/角尺14※粗糙度样块15※目视16※目视17※内径百分表粗糙度样块18※直尺/卡尺/深度尺19※内径百分表粗糙度样块20※目视/卡尺/卡钳21※直尺/卡尺/深度尺22※机床检测23※※机床检测/粗糙度样块24※机床检测25※※机床检测/粗糙度样块拉延类正面部分图纸尺寸、间隙0-0.05mm、标注。
检验记录表单的数据填写规范要求
检验记录数据的填写规范要求为规范公司内标准,特地对检验数据记录表单进行规范,要求如下:一、机械检验1、隔爆面粗糙度检验量具:粗糙度比对卡数据填写:Rax.x,实测值,如Ra6.3。
2、结合面宽度检验量具:游标卡尺数据填写:00.00,实测最短值,列如21.32。
3、火焰通路宽度检验量具:游标卡尺数据填写:00.00,实测最短值,列如21.32。
4、隔爆间隙检验量具:塞尺数据填写:00.00,实测最大值,列如0.21。
5、隔爆面平面度检验量具:刀口尺、铸铁平台、塞尺数据填写:00.00,实测最大值,列如0.05。
(注意:正常机床加工在0.03-0.07之间)6、结合面长度检验量具:游标卡尺数据填写:00.00,实测值,列如21.32。
7、隔爆孔检验量具:内径百分表数据填写:Φ15,实测值为实测范围尺寸。
如Φ15(0-+0.04)8、轴检验量具:外径千分尺9、数据填写:Φ15(0-0.000),实测值为实测范围尺寸。
如Φ15(0-+0.04)10、密封圈的外径、内径、厚度等测量量具使用游标卡尺。
11、检验中使用到卷尺测量的(变压器外壳、铁芯等大件),实际测值均确到1mm。
二、电气检验电气检验所使用的仪器仪表检验所测得的数据为所显示的全数值,如用万用表测量直流电压,表显示23.348,则记录23.348V。
三、检验员要求:1、检验产品前必须准备所对应的检验规程及检验表单,需熟悉并理解检验规程内容,按照检验规程准备检验量具,检验完成后填写表单时必须按照检验规程中规定填写。
量具量程达不到检验表单中要求精度的,按量具的实际精度填写数值,并汇报。
所有检验测试数据必须是实测值,要求需填写的表单,必须及时递交。