汽车冲压新技术详解
汽车车身的冲压成形技术分析

汽车车身的冲压成形技术分析随着汽车工业的发展,汽车车身的制造技术也在不断地进步和完善。
冲压成形技术作为汽车车身制造的重要工艺,具有高效、成本低、适用范围广等优点,受到了广泛的应用。
本文将对汽车车身的冲压成形技术进行分析,并探讨其发展趋势。
一、冲压成形技术的基本原理冲压成形技术是利用模具将金属板材进行加工成所需形状的工艺。
其基本原理是将金属板材放置于冲床上,通过冲头对金属板材进行冲击或拉伸,使得金属板材形成所需的形状和尺寸。
冲压成形技术可分为冲切、拉伸和弯曲等多种方式,可以满足不同形状和结构的要求。
二、汽车车身的冲压成形工艺汽车车身是由多个金属板件焊接组合而成,其制造过程中涉及到大量的冲压成形工艺。
汽车车身的冲压成形工艺主要包括车身外板、车身内板和横梁等部件的制造。
车身外板通常采用单一的冲压成形工艺,而车身内板和横梁则需要经过多次复杂的冲压成形工艺。
汽车车身冲压成形工艺具有高精度、高效率、结构复杂等特点,需要具备高水平的设备和工艺技术支持。
1. 自动化程度提高随着科技的进步,汽车车身冲压成形技术将朝着自动化程度更高的方向发展。
传统的汽车车身冲压成形过程中需要大量的人工操作,而自动化设备能够更快、更精准地完成生产任务,提高生产效率的同时降低生产成本。
2. 精度和表面质量要求提高随着汽车工业对产品质量要求的提高,汽车车身冲压件的精度和表面质量也将成为发展的重点。
未来的汽车车身冲压成形技术将会更加注重产品的表面质量和尺寸精度,以满足汽车外观的要求。
3. 智能化制造技术的应用智能化制造技术将成为汽车车身冲压成形技术的发展趋势之一。
通过引入先进的传感技术、控制技术和数据分析技术,实现对整个生产过程的实时监控和智能化调控,提高了生产线的柔性和智能化程度。
4. 环保要求的提高随着环保意识的增强,汽车车身冲压成形技术将更加注重节能和减排。
未来的汽车车身冲压成形技术将会更多地采用高效节能的设备和工艺,并注重废料的再利用和资源的循环利用,以降低对环境的影响。
汽车车身的冲压成形技术分析

汽车车身的冲压成形技术分析汽车车身是汽车的重要组成部分,其外形设计和制造工艺直接影响着汽车的外观、性能和安全性。
而汽车车身的冲压成形技术是目前最常用的车身制造技术之一,本文将对汽车车身的冲压成形技术进行深入分析。
一、冲压成形技术概述冲压成形技术是利用冲压设备和模具将金属板料加工成所需形状的一种制造方法,其特点是高效、精度高、成本低。
冲压成形技术在汽车制造领域得到了广泛应用,尤其是汽车车身的制造中,冲压成形技术的作用尤为突出。
二、冲压成形技术在汽车车身制造中的应用1.冲压成形工艺汽车车身的冲压成形工艺主要包括下料、模具设计、冲床冲压、清洗、组装等环节。
首先是通过下料设备将金属板料剪切成所需大小。
然后根据车身的设计要求设计并制造冲压模具。
接着使用冲床对金属板料进行冲压成形,通过模具的设计和冲床的运行,将金属板料冲压成车身需要的各种零部件。
最后对冲压成形后的零部件进行清洗、去毛刺等处理,然后进行组装,形成完整的车身结构。
2.冲压成形技术的优势冲压成形技术在汽车车身制造中具有高效、精度高、生产成本低等优势。
冲压成形可以使金属板料在较短的时间内完成成形,提高了生产效率。
由于模具的精密设计和冲床的高速运动,可以实现对车身零部件的高精度冲压,保证其尺寸和形状的准确度。
由于冲压成形生产线的自动化程度较高,相对于传统的手工制造工艺,冲压成形技术降低了人工成本,使得汽车的生产成本得到了有效控制。
1.高强度材料的应用随着汽车安全性能的不断提高,对车身材料的要求也越来越高。
传统的冷轧钢板在一定程度上已经无法满足汽车车身材料的需求。
高强度材料如高强度钢、铝合金等开始在汽车车身制造中得到应用。
这些新材料的应用对冲压成形技术提出了更高的要求,需要冲压设备和模具能够更好地处理这些高强度材料,以保证车身零部件的成形质量。
2.多工位冲压设备的应用为了提高生产效率和节约生产成本,汽车车身制造中开始使用多工位冲压设备。
多工位冲压设备可以在一次加工中完成多道工序,实现一次性成形多个零部件,提高了生产效率和降低了生产成本。
汽车车身冲压的新技术和发展的趋势
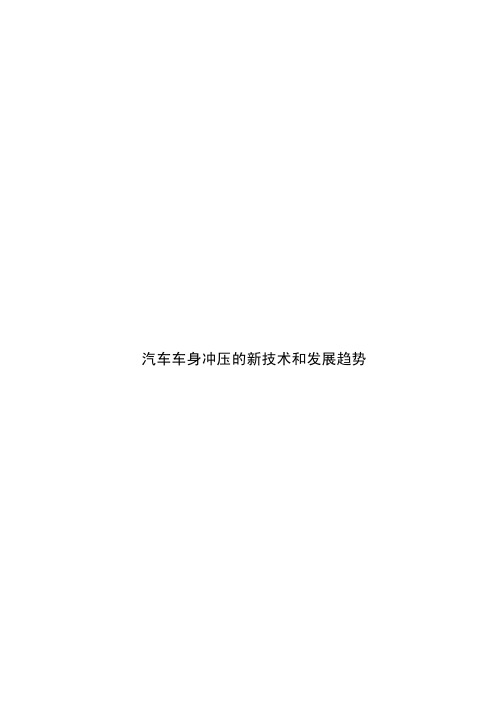
汽车车身冲压的新技术和发展趋势汽车车身冲压的新技术和发展趋势姓名:班级:学号:汽车车身冲压的新技术和发展趋势冲压成型工艺是一种先进的金属加工工艺方法,它是建立在金属塑性变形的基础上,在常温条件下利用模具和冲压设备对板料施加压力,使板料产生塑性变形或分离,从而获得具有一定形状、尺寸和性能的零件。
冲压工艺生产效率高、操作简便、便于实现机械化与自动化、尺寸一致性好、原材料消耗低等优点,所以汽车上的许多结构件广泛采用冲压件。
冲压成型工艺在汽车车身制造工艺中占有重要的地位,特别是汽车车身的大型覆盖件,因大多形状复杂,结构尺寸大,有的还是空间曲面,并且表面质量要求高,所以用冲压加工方法来制作这些零件是用其他加工方法所不能比拟的。
载重货车的驾驶室、车前钣金件、货箱板以及轿车的各种车身覆盖件和客车的各种骨架等,几乎全都是用冲压加工方法制作的。
冲压工艺不仅可以提高生产效率,还可以降低生产成本,使汽车工业得以迅速发展。
现代汽车工业具有生产规模化、车型批量小、品种变化快、多车型共线生产的特点,车身覆盖件也随之呈现大型化、一体化的特征,这些趋势要求冲压技术与设备不断向柔性化和自动化方向发展,高柔性、高效率的自动化冲压设备正在逐步取代传统的刚性生产线,成为世界冲压生产的主流。
冲压设备长期以来,传统冲压设备因其稳定的生产条件保证了冲压件的质量,模具的使用也相对持久,但是缺乏灵活性是这一生产方式的明显缺陷。
集成化控制技术在压力机上的应用给冲压生产带来了更多的灵活性,大型多工位压力机、柔性冲压自动线等设备正在改写冲压生产的历史。
1.集成化控制为适应柔性化的生产要求,压力机的所有控制功能应做到集成化,从而实现全套模具的菜单化管理,主要包括滑块行程调整、平衡器气压的调整、气垫行程调整以及自动化控制系统等各个环节的参数设定。
具有现场通信网络、现场设备互联、互动操作性、分散功能模块、开放式功能的现场总线技术是压力机控制技术的发展方向,对实现自动化具有明显推动作用。
大众冲压工艺(3篇)

第1篇一、引言冲压工艺是一种重要的金属加工方法,广泛应用于汽车、家电、航空航天、电子通讯等领域。
随着工业技术的发展,冲压工艺在材料、设备、技术等方面都取得了显著的进步。
本文将对大众冲压工艺进行技术解析,并探讨其在不同领域的应用。
二、大众冲压工艺技术解析1. 冲压工艺原理冲压工艺是指利用冲压机械对金属板材进行塑性变形,使其成为所需形状和尺寸的零件或产品的加工方法。
冲压工艺主要包括以下步骤:(1)放料:将金属板材放置在冲压机械的工作台上。
(2)定位:将板材定位在冲压机械的模具上。
(3)剪切:利用剪切力将板材切割成所需尺寸。
(4)成形:利用模具对板材进行塑性变形,形成所需形状和尺寸的零件。
(5)取件:将成形后的零件从模具中取出。
2. 冲压工艺分类根据冲压工艺的特点,可以分为以下几种类型:(1)冷冲压:在室温下对金属板材进行冲压加工。
(2)热冲压:在高温下对金属板材进行冲压加工。
(3)深冲压:板材厚度较大,成形后零件深度较深的冲压工艺。
(4)浅冲压:板材厚度较小,成形后零件深度较浅的冲压工艺。
3. 冲压工艺特点(1)生产效率高:冲压工艺可以实现大批量生产,提高生产效率。
(2)精度高:冲压工艺可以精确控制零件的尺寸和形状。
(3)材料利用率高:冲压工艺可以充分利用材料,减少浪费。
(4)成本低:冲压工艺设备投资较小,运行成本低。
三、大众冲压工艺在各个领域的应用1. 汽车行业在汽车行业中,冲压工艺主要用于车身及零部件的制造。
如发动机罩、车门、行李箱盖、车架等。
冲压工艺在汽车制造中的应用具有以下优势:(1)提高车身强度和刚度。
(2)降低车身重量,提高燃油效率。
(3)提高车身美观性。
2. 家电行业在家电行业中,冲压工艺主要用于制造家电产品的外壳、支架等。
如洗衣机、冰箱、空调等。
冲压工艺在家电制造中的应用具有以下优势:(1)提高家电产品的美观性和耐用性。
(2)降低成本,提高生产效率。
(3)适应各种形状和尺寸的家电产品。
轿车冲压简介课件

02
01
修边
翻边
整形、压印和刻字
检验和入库ຫໍສະໝຸດ 010203
04
去除多余的边缘或材料,使零件符合设计要求。
将零件的边缘或孔口加工成所需形状。
根据需要进一步调整和加工零件。
对成品进行质量检查,合格后进行包装入库。
环境控制
保持生产环境的清洁和干燥,避免零件受到污染或生锈。
工艺参数控制
合理设置和调整工艺参数,如压力、速度和行程等,以保证零件质量。
其他材料
04
CHAPTER
轿车冲压技术的新发展
自动化冲压技术是指通过自动化设备实现冲压过程的自动化,减少人工干预,提高生产效率。
自动化冲压技术可以降低生产成本,提高产品质量,减少生产过程中的安全隐患。
自动化冲压技术需要高精度的模具和设备,同时需要专业的技术人员进行维护和调试。
快速冲压技术是指通过高速冲压设备和工艺,实现快速制造冲压零件。
02
CHAPTER
轿车冲压工艺流程
按工艺特点分类:单冲模冲压、级进模冲压和复合模冲压。
按材料变形方式分类:分离工序和成形工序。
按模具结构形式分类:单工序模、复合模和连续模。
根据产品要求选择合适的板材,并进行剪裁。
备料
落料
拉延
使用冲压设备将剪裁好的板材加工成所需形状的毛坯。
通过模具将毛坯加工成三维形状的零件。
详细描述
安全性原则
模具设计应注重降低制造成本,提高经济效益。
经济性原则
钢材是冲压模具制造的主要材料,其硬度、耐磨性和韧性等性能对模具使用寿命和冲压件质量有重要影响。
钢材
硬质合金具有高硬度、高耐磨性和良好的耐热性等特点,适用于高精度、高效率的冲压模具制造。
汽车冲压模具的技术分析
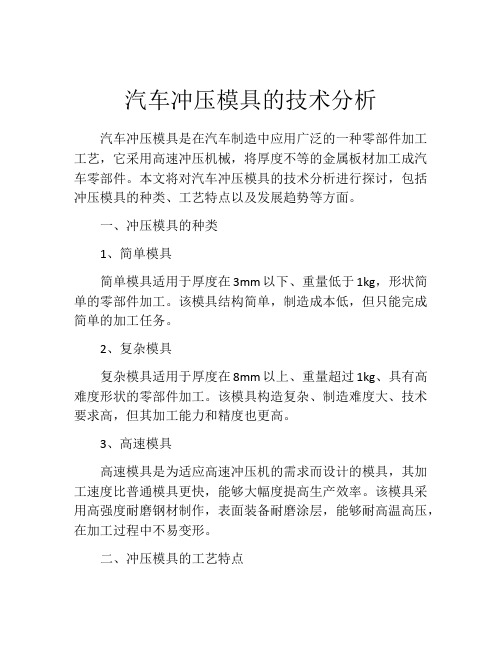
汽车冲压模具的技术分析汽车冲压模具是在汽车制造中应用广泛的一种零部件加工工艺,它采用高速冲压机械,将厚度不等的金属板材加工成汽车零部件。
本文将对汽车冲压模具的技术分析进行探讨,包括冲压模具的种类、工艺特点以及发展趋势等方面。
一、冲压模具的种类1、简单模具简单模具适用于厚度在3mm以下、重量低于1kg,形状简单的零部件加工。
该模具结构简单,制造成本低,但只能完成简单的加工任务。
2、复杂模具复杂模具适用于厚度在8mm以上、重量超过1kg、具有高难度形状的零部件加工。
该模具构造复杂、制造难度大、技术要求高,但其加工能力和精度也更高。
3、高速模具高速模具是为适应高速冲压机的需求而设计的模具,其加工速度比普通模具更快,能够大幅度提高生产效率。
该模具采用高强度耐磨钢材制作,表面装备耐磨涂层,能够耐高温高压,在加工过程中不易变形。
二、冲压模具的工艺特点1、高精度汽车零部件通常要求高精度,要求冲压模具能够准确地切割和成型材料。
因此,模具的设计和制造需要考虑工艺流程、材料特性和产品质量要求等因素。
目前,采用CAD/CAM设计和制造技术的冲压模具的精度能够达到微米级别。
2、高效率高效率是汽车冲压模具的又一重要特征。
随着汽车工业的发展,节约时间成了工业生产的一个绝对要素,冲压模具须有着一定的加工速度和生产率。
为了提高加工效率和生产率,采用高速冲压机和高速钢材制造模具是目前常用的方法。
3、高坚固性冲压模具的坚固性和刚度是关系到加工质量和寿命的重要组成部分。
汽车模具在工作过程中所承受的高压和高速冲击力是巨大的,因此要求模具所使用的钢材具有足够的抗压性和耐磨性。
4、低成本冲压模具的制造成本直接关系到企业的生存和竞争力。
因此,为了降低制造成本,应尽量采用先进的CAD/CAM技术,大幅度减少模具的设计和制造周期,应用先进的模具制造技术,提高模具加工的收益率。
三、冲压模具的发展趋势1、高速为了应对市场竞争,汽车工业需要提高生产效率和质量,而高速化是势必趋势。
汽车冲压新技术与传统冲压技术的研究分析
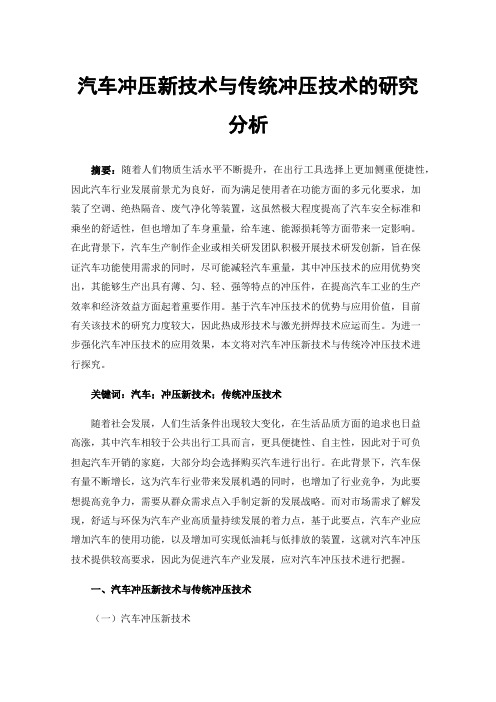
汽车冲压新技术与传统冲压技术的研究分析摘要:随着人们物质生活水平不断提升,在出行工具选择上更加侧重便捷性,因此汽车行业发展前景尤为良好,而为满足使用者在功能方面的多元化要求,加装了空调、绝热隔音、废气净化等装置,这虽然极大程度提高了汽车安全标准和乘坐的舒适性,但也增加了车身重量,给车速、能源损耗等方面带来一定影响。
在此背景下,汽车生产制作企业或相关研发团队积极开展技术研发创新,旨在保证汽车功能使用需求的同时,尽可能减轻汽车重量,其中冲压技术的应用优势突出,其能够生产出具有薄、匀、轻、强等特点的冲压件,在提高汽车工业的生产效率和经济效益方面起着重要作用。
基于汽车冲压技术的优势与应用价值,目前有关该技术的研究力度较大,因此热成形技术与激光拼焊技术应运而生。
为进一步强化汽车冲压技术的应用效果,本文将对汽车冲压新技术与传统冷冲压技术进行探究。
关键词:汽车;冲压新技术;传统冲压技术随着社会发展,人们生活条件出现较大变化,在生活品质方面的追求也日益高涨,其中汽车相较于公共出行工具而言,更具便捷性、自主性,因此对于可负担起汽车开销的家庭,大部分均会选择购买汽车进行出行。
在此背景下,汽车保有量不断增长,这为汽车行业带来发展机遇的同时,也增加了行业竞争,为此要想提高竞争力,需要从群众需求点入手制定新的发展战略。
而对市场需求了解发现,舒适与环保为汽车产业高质量持续发展的着力点,基于此要点,汽车产业应增加汽车的使用功能,以及增加可实现低油耗与低排放的装置,这就对汽车冲压技术提供较高要求,因此为促进汽车产业发展,应对汽车冲压技术进行把握。
一、汽车冲压新技术与传统冲压技术(一)汽车冲压新技术1、热成形技术主要加工对象为特殊的热成形钢,工作原理是对其进行加热,使其奥氏体化后送入模具内进行冲压成形。
通过热成形技术能够将特殊的热成形钢由奥氏体转变为马氏体,使其强度发生较大优化,通常可提高至1500-2000MPa,能够进一步加强车身的抗击能力,提高车辆的安全性[1]。
汽车制造工艺4冲压工艺全解

汽车制造工艺4冲压工艺全解汽车制造工艺 4:冲压工艺全解在汽车制造的庞大体系中,冲压工艺无疑是一道关键且基础的工序。
它就像是一位神奇的雕塑家,将一块块平凡的金属板材塑造成为汽车车身的各个零部件,赋予了汽车独特的形态和坚固的结构。
冲压工艺的原理其实并不复杂。
简单来说,就是通过压力机和模具对板材施加外力,使其发生塑性变形或分离,从而获得我们所需的形状和尺寸的零件。
这个过程就好比我们用擀面杖擀饺子皮,只不过冲压工艺的“擀面杖”和“面板”要强大得多。
冲压工艺所使用的设备主要是压力机。
压力机的种类繁多,常见的有机械压力机和液压压力机。
机械压力机依靠机械传动来提供压力,动作迅速,生产效率高;而液压压力机则通过液压系统产生压力,压力大小和行程可以更加精确地控制。
在冲压过程中,模具的作用至关重要。
模具就像是一个定制的模板,决定了零件的形状和尺寸。
一套优质的模具不仅能够保证零件的精度和质量,还能提高生产效率,降低成本。
模具的设计和制造需要经过严格的计算和精密的加工,以确保其能够承受巨大的压力和频繁的使用。
冲压工艺的流程通常包括以下几个步骤:首先是板材的准备,要选择合适的材质、厚度和尺寸的板材;然后将板材送入压力机,通过模具进行冲压;冲压完成后,需要对零件进行切边、冲孔等后续处理,以去除多余的部分,使零件更加规整;最后,对零件进行检验,确保其符合质量要求。
冲压工艺的优点非常显著。
它能够实现大规模生产,生产效率高,成本相对较低。
而且,冲压出来的零件具有较高的精度和一致性,能够很好地满足汽车制造对于零部件质量的严格要求。
此外,冲压工艺还可以制造出形状复杂、强度高的零件,为汽车的设计提供了更多的可能性。
然而,冲压工艺也并非完美无缺。
在冲压过程中,由于板材的塑性变形,可能会导致材料的性能发生变化,比如强度和韧性的降低。
同时,模具的制造和维护成本较高,需要投入大量的资金和技术。
而且,如果设计不合理或者操作不当,还可能会出现零件的破裂、起皱等质量问题。
- 1、下载文档前请自行甄别文档内容的完整性,平台不提供额外的编辑、内容补充、找答案等附加服务。
- 2、"仅部分预览"的文档,不可在线预览部分如存在完整性等问题,可反馈申请退款(可完整预览的文档不适用该条件!)。
- 3、如文档侵犯您的权益,请联系客服反馈,我们会尽快为您处理(人工客服工作时间:9:00-18:30)。
文献综述
汽车车身冲压成形技术是汽车制造技术的 重要组成部分,以致有些国际同行认为汽 车技术的竞争实质上是冲压成形技术及其 相应的焊装技术的竞争。虽然上述观点不 一定准确,但说明冲压成形技术在汽车制 造中的重要地位。
众所周知,汽车车身的金属件几乎 100%为冲压件,而且汽车车身的更新 换代远比底盘和发动机的更新换代快。 这就决定了冲压成形技术在汽车产品的 开发中不仅影响制造周期,还直接影响 成本和产品品质,因而影响产品的综合 竞争力。
新马自达2的车身结构中使用了440, 590,780和980Mpa级别的高强度钢
板和超高强度
2. 高强度钢板在车体框架上的应用
随着正面撞击、侧面撞击的撞击安全性标 准的提高,结构件、加强件等主要使用 590MPa级高强度钢板,也有厂家使用 780MPa级、980MPa级高强度钢板。
前防撞梁外板
TRIP钢
包括热轧、冷轧、电镀和热镀锌产品。 主要组织:铁素体、贝氏体和残余奥氏体, 其中残余奥氏体的含量在5%~15%,强 度:600~800MPa。 主要成分:C、Si和Mn,其中Si的主要作 用是抑制贝氏体转变时渗碳体的析出, 但对于钢板表面质量不利。
Octavia明锐全车大量采用了激光拼焊
尽管拼焊材料在使用初期以提高材料利 用率为目的,仅用于小型部件上,但最 近已将拼焊材料扩大应用于车身侧板和 车箱底板等大型部件。
拼焊板主要采用400~590MPa级高强度 钢板,也有使用780MPa级和980MPa 级高强度钢板的情况。
3. 高强度钢板在汽车底盘上的应用
一般用于需高强度、高抗碰撞吸收能且 也有一定成形要求的汽车零件,如车轮、 保险杠、悬挂系统及其加强件等。
DP钢板优点
①屈服点低,抗拉强度高,屈强比低; ②无屈服点伸长或是屈服伸长,应力应 变曲线平滑; ③伸长率高; ④初始加工硬化率高,加工强化性能好; ⑤抗疲劳性能好。所以DP钢特别适合冲 压翻边性能良好的部件,一直被汽车界 所关注,有可能成为汽车首选的冷轧高 强度钢板。
08年,在继具备自主知识产权的“轻量 化半挂车”推向市场后,再度推出高强 度钢“轻量化散装水泥罐车”。“5.12” 灾后重建,四川水泥需求量陡增至3.7亿 吨,需新增车辆约4000台(每台1年运 能2.5万吨,3年运完),针对这一市场 需求,专汽公司在经过充分的市场论证 后,提出了散装水泥罐车研发思路,得 到有限公司的大力支持。
高强度钢板可以减轻零件质量,提高 整车碰撞的安全性,提高零件的外观质 量和抗凹性,因此近年来在车身生产中 得到了越来越多的应用。
1.高强度钢在汽车面板上的应用
车顶、车门、等部件要求具有变形刚度 和抗凹陷性,主要使用抗拉强度为340~ 390MPa的烘烤硬化钢板(BH钢板)。 BH钢板的屈服强度在烘烤涂漆时升高, 可在不损失成形性的前提下,提高抗凹 陷性,减薄钢板。现在,有的车型已使 用440MPa级BH型高强度钢板。
汽车冲压新技术
报告内容
第一节 冲压原材料研究的最新进展 (高强度钢和超高强度钢板以及轻质 金属材料等的使用)
第二节 冲压技术发展的新动向(内高 压成形技术与热冲压成形等)
第三节 模具的发展新动向(产品专业化、 制造数字化与模具设计的专门化)
第四节 冲压设备的发展新动向(大型多 工位压力机与柔性生产化)
第一节 冲压原材料研究的最新进展
新型冲压用板材包括: 高强度钢板; 耐腐蚀钢板; 双相钢板; 涂层板及复合板材。
高强度钢板
定义:指对普通钢板加以强化处理而得 到的钢板。 强化原理:固溶强化、析出强化、细晶 强化、组织强化(相变强化及复合组织 强化)、时效强化及加工强化等。其中, 前5种是通过添加合金成分和热处理工 艺来控制板材性质的。
应用部位:卡车的底盘部分,也用于大客 车的车轮,轮毂等部件 屈服强度:350MPa到550MPa之间 组织结构:具有铁素体加少量珠光体组织。
最近,开发出690MPa级卡车大梁用钢, 它利用了在由热带轧机直接轧出的贝氏 体钢中所有的强化机理。
DP钢板
主要组织:铁素体和马氏体,其中马氏 体的含量在5%~20%。 强度:500~1200MPa。 特征:DP钢具有低屈强比、高的加工硬 化指数、高烘烤硬化性能、没有屈服延 伸和室温时效等特点.
目前,该车已完成设计进入试制阶段, 预计11月底下线试运行。
该车采用高强度钢制作,设计容积 39.8m3,载重50吨,与相同载重的普 通车型比较,自重轻1吨左右,能够与所 有品牌重型卡车底盘匹配,计重收费优 势凸现。预测市场前景看好,将提升公 司市场竞争力。
4. 常用钢种简介
热轧低合金高强度钢(HSLห้องสมุดไป่ตู้)薄钢板
高强度钢板的高强度涵义
a. 屈服强度、抗拉强度高,在2703l0MPa范围之内。用于汽车零件的高 强度钢板,其抗拉强度可以达到600800MPa,而相应的普通冷轧软钢板的 抗拉强度只有300MPa; b.高强度钢板的应用,能减轻冲压件的 重量,节省能源和降低冲压产品成本。
在日本,抗拉强度不小于490MPa的 热轧带钢和抗拉强度不小于340MPa的 冷轧钢带被称为高强度钢。
用材已从传统的440MPa级热轧板发展 到780MPa,最大减重达30%。近年来, 高强度钢板在底盘上的使用比例正在急 剧增加。今后,高强度钢板的使用比例 及更高强度钢板的应用有望进一步提高。
采用高强钢制造的汽车底盘
举例:同升专用汽车公司
为了从根本上摆脱对底盘厂商的过度依 附,最终达到底盘厂商对自己的依附, 依托有限公司,将铁路货车新材料、新 工艺等专有技术平移到专用汽车产品上, 努力走自主创新的道路。
有些厂家甚至采用将390MPa、 440MPa级高强度钢板冲压成形后,对 强化部分进行高频加热和淬火,以使部 件局部抗拉强度达到1200MPa,并在冲 压加热钢板的同时进行冷却,以使部件 整体抗拉强度达到1470MPa的方法。
欧洲流行的高强钢U形车厢结构
此外,还有采用激光拼焊方法,将不同 厚度、不同材质钢板拼合起来,使材料 配置适用于所要求材质和使用部位。