加工中心加工工艺
加工中心加工工艺

第8章 加工中心加工工艺
8.1 概述 8.2 加工中心加工工艺的制订 8.3 典型零件的加工中心加工工艺 习题
第8章 加工中心加工工艺
8.1 概 述
8.1.1 加工中心的工艺特点
(1) 加工精度高。
(2) 表面质量好。 (3) 质量稳定。 (4) 生产效率高。 (5) 具有较强的故障自诊断功能。
是下道工序的定位基准,所以待各加工工序的定位基准确定之
后, 即可从最终精加工工序向前逐级倒推出整个工序的大致 顺序。
第8章 加工中心加工工艺 (3) 确定加工中心的加工顺序时,还先要明确零件是否要 进行加工前的预加工。预加工常由普通机床完成。若毛坯精度 较高,定位也较可靠,或加工余量充分且均匀,则可不必进行
第8章 加工中心加工工艺
图8-5 支架
第8章 加工中心加工工艺 4. 模具 常见的模具有锻压模具、铸造模具、注塑模具及橡胶模 具等。图 8-6 所示为连杆锻压模具。 这类零件的型面大多由 三维曲面构成,采用加工中心加工这类成型模具,由于工序 高度集中,因而基本上能在一次安装中采用多坐标联动完成 动模、静模等关键件的全部精加工,尺寸累积误差及修配工 作量小。
第8章 加工中心加工工艺 (5) 对于螺纹孔,要根据其孔径的大小选择不同的加 工方式。直径在M6~M20 mm之间的螺纹孔,一般在加工中心
上用攻螺纹的方法加工;直径在M6 mm以下的螺纹,则只在加
工中心上加工出底孔,然后通过其它手段攻螺纹;直径在M20 mm以上的螺纹,一般采用镗刀镗削而成。
第8章 加工中心加工工艺 8.2.3 加工阶段的划分
(6) 软件适应性强。
第8章 加工中心加工工艺 8.1.2 加工中心加工的对象 1. 箱体类零件
数铣及加工中心加工工艺

5
5
数控铣及加工中心加工工艺
工作范围
纵向长度:
X
400 mm
高
横向长度:
Y
450 mm
速
垂直高度:
加
工作主轴
30'000 min-1
数 控
工
中 心
工作主轴
42'000 min-1
铣
主
、
要
工作主轴
60'000 min-1
Z
350 mm
S6
12.5 kW
S1
10.0 kW
S6
13.0 kW
S1
10.0 kW
的
工步2:粗精铣表面2型面;
制
工步3:精铣表面1型面。
定
18
数控铣床及加工中心加工工艺
常用对刀方式
对刀是确定工件在机床上的位置, 也即是确定工件坐标系与机床坐
数
Y
控
铣
X
及
加
标系的相互位置关系。对刀过程 一般是从各坐标方向分别进行, 它可理解为通过找正刀具与一个 在工件坐标系中有确定位置的点 (即对刀点)来实现。
工
求达到的精度及表面粗糙度相适应。
中
在数控镗铣床及加工中心上可铣削平面、平面轮廓及曲面。
心
孔加工的方法有钻削、扩削、铰削、铣削和镗削等;
加 工
螺纹的加工可采用攻螺纹、铣螺纹等方法。
工
艺
的
制
定
23
数控铣及加工中心加工工艺
平面轮廓加工
数
刀具的选择
控
铣
、
加 工 中
铣削平面类零件周边轮廓一般采用立铣刀。刀具的尺寸应满足: 刀具半径R小于朝轮廓内侧弯曲的最小曲率半径ρmin, 一般 可取R=(0.8~0.9) ρmin;
加工中心工艺介绍

数控加工工艺及刀具
3
2018年2月5日星期一
1.1 加工中心的分类
主轴位置 立式 卧式 立卧转换
数控加工工艺及刀具
4
2018年2月5日星期一
数控加工工艺及刀具
5
2018年2月5日星期一
数控加工工艺及刀具
6
2018年2月5日星期一
数控加工工艺及刀具
7
2018年2月5日星期一
数控加工工艺及刀具
加工中心工艺介绍
内容
1 加工中心的主要特点及功能 2 加工中心的刀具、夹具及加工工艺 3 典型零件加工工艺分析
数控加工工艺及刀具
2
2018年2月5日星期一
1 加工中心的主要特点及功能
加工中心(Machining Center,简称MC)是一种具 有复合加工功能的数控机床,是集铣削、钻削、铰 削、镗削、攻螺纹于一体的多功能机械加工设备。 加工中心最初是从数控铣床发展而来的,与铣床的 最大区别是加工中心是带有到库和自动换刀装置的 数控机床,又称为自动换刀数控机床或多工序数控 机床。
加工中心的刀库种类及换刀形式
刀库种类 直线刀库 圆盘刀库 链式刀库 其他刀库
数控加工工艺及刀具
13
2018年2月5日星期一
数控加工工艺及刀具
14
2018年2月5日星期一
1.3 加工中心的特点
特点
加工精度高
精度稳定
表面质量好
加工效率高
数控加工工艺及刀具
15
2018年2月5日星期一
28
2018年2月5日星期一
2.3 加工中心加工工艺
(1)零件的工艺分析 包括零件图的完整性、正确性和技术要求,分析零件的 结构工艺性和定位基准等
加工中心及加工工艺教材

7.3.2 加工中心加工零件的工艺 分析
1.结构工艺性 (1)加工量要小,以便减少切削加工时间,降低成本。 (2)零件上孔和螺纹的尺寸规格尽可能少,减少钻头、 铰刀及丝锥等刀具的数量,防止刀库容量不足。 (3)零件尺寸尽量标准化,以便采用标准刀具。 (4)零件加工表面应具有加工的方便性和可能性。 (5)零件结构应具有足够的刚性,以减少夹紧变形和 切削变形。
二、加工中心刀具的装夹
1.加工中心刀具定位长度的确定 确定刀具定位长度的原则是:在满足零件加 工要求的前提下,尽量减小刀具长度,以 提高刀具系统的刚性。
二、加工中心刀具的装夹
2.钻头的装夹 过渡套有莫氏1号、2号、3号、4号。
二、加工中心刀具的装夹
3.刀柄 加工中心刀柄是机床主轴与刀具之间的连接工具,是加工中 心必备的辅具。它除了能够准确地安装各种刀具外,还应 满足在机床上的自动松开和拉紧定位、刀库中的储存和识 别以及机械手的夹持和搬运等需要。
一、数控加工中心常用的刀具
2.扩孔刀具及使用特点
一、数控加工中心常用的刀具
3.镗孔刀具结构及特点 (1)单刃镗刀, (2)双刃镗刀, (3)微调镗刀
一、数控加工中心常用的刀具
4.铰孔刀具结构及特点 标准铰刀和浮动铰刀
一、数控加工中心常用的刀具
5.丝锥
一、数控加工中心常用的刀具
6.孔加工复合刀具
加工中心及加工工艺
7.1加工中心工艺特点及其加工对象
7.1.1 工艺特点 (1)加工精度和质量高。 (2)生产效率高。 (3)生产效益好。 (4)简化了生产调度和管理。
7.1.2 加工中心的主要加工对象
1.既有平面又有孔系的零件 (1)箱体类。(2)盘、套、板类零件。
7.1.2 加工中心的主要加工对象
加工中心工艺流程
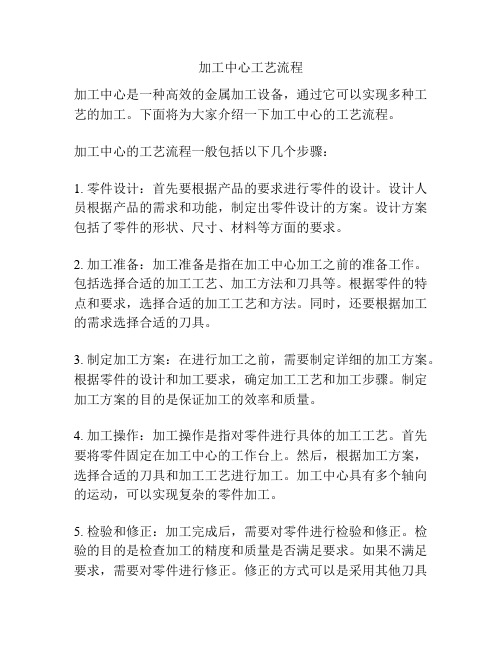
加工中心工艺流程加工中心是一种高效的金属加工设备,通过它可以实现多种工艺的加工。
下面将为大家介绍一下加工中心的工艺流程。
加工中心的工艺流程一般包括以下几个步骤:1. 零件设计:首先要根据产品的要求进行零件的设计。
设计人员根据产品的需求和功能,制定出零件设计的方案。
设计方案包括了零件的形状、尺寸、材料等方面的要求。
2. 加工准备:加工准备是指在加工中心加工之前的准备工作。
包括选择合适的加工工艺、加工方法和刀具等。
根据零件的特点和要求,选择合适的加工工艺和方法。
同时,还要根据加工的需求选择合适的刀具。
3. 制定加工方案:在进行加工之前,需要制定详细的加工方案。
根据零件的设计和加工要求,确定加工工艺和加工步骤。
制定加工方案的目的是保证加工的效率和质量。
4. 加工操作:加工操作是指对零件进行具体的加工工艺。
首先要将零件固定在加工中心的工作台上。
然后,根据加工方案,选择合适的刀具和加工工艺进行加工。
加工中心具有多个轴向的运动,可以实现复杂的零件加工。
5. 检验和修正:加工完成后,需要对零件进行检验和修正。
检验的目的是检查加工的精度和质量是否满足要求。
如果不满足要求,需要对零件进行修正。
修正的方式可以是采用其他刀具或调整工艺等方式。
6. 表面处理:加工完成后,可以对零件进行表面处理。
表面处理可以提高零件的美观程度和耐腐蚀能力。
常见的表面处理方式有喷涂、电镀、打磨等。
7. 成品包装:最后,将加工完成的零件进行包装。
包装的目的是保护零件,防止受到损坏。
根据零件的特点和用途,选择合适的包装方式。
以上就是加工中心的工艺流程。
通过加工中心的高效加工能力,可以满足各种零件加工的需求。
加工中心的应用范围广泛,常见于汽车、航空、船舶等行业。
随着科技的不断发展,加工中心的加工精度和效率也在不断提高,为各种行业的生产提供了有力的支持。
加工中心上加工零件的工艺和要求
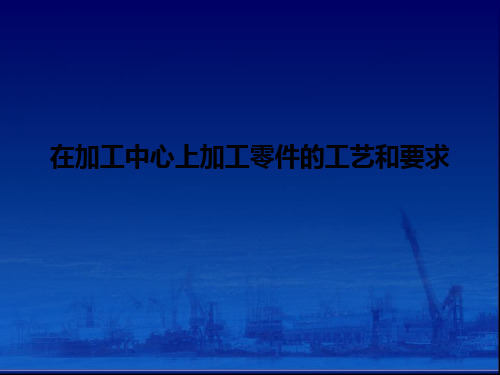
加工中心加工内容的选择
• 选定适合加工中心加工的零件之后,需要进一步选择确定适合加工中 心加工的零件表面。通常选择下列表面: • ①尺寸精度要求较高的表面。 • ②相互位置精度要求较高的表面。 • ③丌便于普通机床加工的复杂曲线、曲面。 • ④能够集中加工的表面。
加工零件的结构工艺性分析
• 从机械加工的角度考虑,在加工中心上加工的零件,其结构工艺性应 具备以下几点要求 : • ①零件的切削加工量要小,以便减少加工中心的切削加工时间,降 低零件的加工成本。 • ②零件上光孔和螺纹的尺寸规格尽可能少,减少加工时钻头、铰刀 及丝锥等刀具的数量,以防刀库容量丌够。 • ③零件尺寸规格尽量标准化,以便采用标准刀具。 • ④零件加工表面应具有加工的方便性和可能性。 • ⑤零件结构应具有足够的刚性,以减少夹紧变形和切削变形。
在加工中心上加工零件的工艺和要求
立式加工中心
• 加工范围广泛,可完成铣、镗、钻、绞、攻丝等加工、若选用数控转 台,可扩大为四轴控制实现多轴加工、大件采用稠筋封闭式框架结构、 刚性高、抗震性好、五大件由进口五面体加工中心加工,切削应力小, 热变形少 、大部分配套件(包括电器元件)采用进口或合资品牌,整 机可靠性高
加工路线的确定
• 加工中心上刀具的进给路线包括孔加工进给路线和铣削加工进给路线。 • 孔加工时,一般是先将刀具在xy平面内快速定位到孔中心线的位置上, 然后再沿z向(轴向)运动进行加工。
由于5. 6孔不1.2.3.4孔在Y向的定位方向相反,y向反向 间隙会使误差增加,从而影响5.6孔不其它孔的位置精度。按 图c所示路线,可避克反向间隙的引入。
• 五轴联动加工中心立式系列具有X﹑Y﹑Z三个直线运动的数控坐标轴 和二个旋转运动的数控坐标轴, 可实现五轴联动。各坐标轴可自动定 位,工件在一次装夹后,可自动完成铣﹑钻﹑镗﹑铰和攻丝等多种工序 的加工。适用于蜗轮、叶片、复杂模具和空间凸轮等具有复杂曲面的 零件加工,已在军工、航空、航天、发电和造船等机械加工行业中获 得了广泛应用。
加工中心加工工艺规范范文

加工中心加工工艺规范一、龙门加工中心加工工艺规范操作者必须接受有关龙门加工中心的理论和实践的培训,并且通过考核获得上岗证,才能具备操作龙门加工中心加工的资格。
1、加工前准备1.操作者必须根据机床使用说明书熟悉机床的性能,加工范围和精度,并且熟悉机床及其数控装置和计算机各部分的作用及其操作方法。
2.检查各开头、旋钮和手柄是否在正确位置。
2、加工要求1.进行首件加工前,必须经过程序检查、轨迹检查、单程序段试切及工件检查等步骤。
2.加工时,必须正确输入程序,不得擅自更改别人的程序。
3.加工过程中,操作者必须监视显示装置,发现报警信号时,应及时停机排除故障。
4.加工中不得任意打开控制系统及计算机柜。
5.本工序是关键加工工序,所加工的工件经自检合格后,必须送检验员专检。
3、刀具与工件装夹1.刀具安装应注意刀具使用顺序,刀具安放位置须与程序要求顺序和位置一致。
2.工件装夹应牢固可靠,注意避免在工作中刀具与工件、刀具与刀具发生干涉。
4、加工参数设定1.主轴转速定义:N=1000*V/3.14*D N--主轴转速(rpm/min) V--加工速度(m/min) D--刀具直径(mm),加工速度在刀具资料中查出2.进给速度设定:F=N*M*F’ F-进给速度(mm/min),N-主轴转速(rpm/min),M-刀具刃数值,F’-刀具加工量(mm/刃口)5、工件碰数对一件装夹好的工件,可以利用碰数头对其进行碰数定工件的加工零件,步骤如下:(机械式碰数头应在旋转状态下,转数450-600rpm/min)1.手动移动工作台X轴,使碰数头碰工件的一侧面,当碰数头刚碰到工件,红灯发亮,这时就设定这点相对座标值为零。
2.手动移动工作台X轴,使碰数头碰工件的另一侧面,当碰数头刚碰到工件,记下这时的相对座标值。
3.把这时的相对座标值除以2,所得数值就是工件X轴上的中间值。
4.再移动工作台到X轴上的中间数值,把这点的X轴的相对座标值设定为零,这一点就是工件X轴上的零位。
数控加工中心加工工艺范文
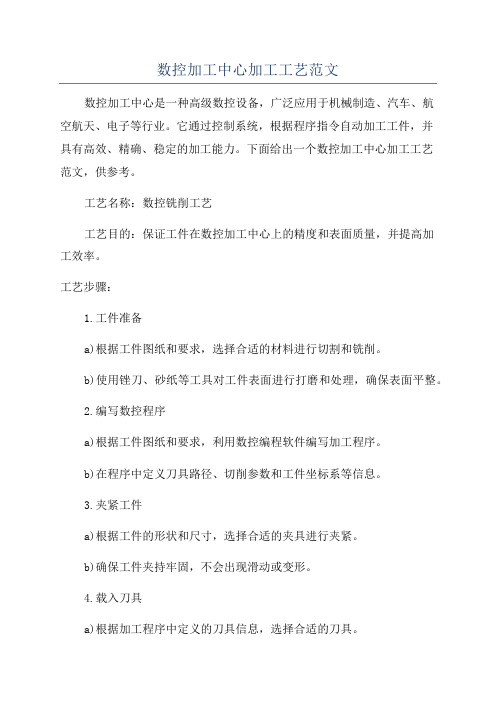
数控加工中心加工工艺范文数控加工中心是一种高级数控设备,广泛应用于机械制造、汽车、航空航天、电子等行业。
它通过控制系统,根据程序指令自动加工工件,并具有高效、精确、稳定的加工能力。
下面给出一个数控加工中心加工工艺范文,供参考。
工艺名称:数控铣削工艺工艺目的:保证工件在数控加工中心上的精度和表面质量,并提高加工效率。
工艺步骤:1.工件准备a)根据工件图纸和要求,选择合适的材料进行切割和铣削。
b)使用锉刀、砂纸等工具对工件表面进行打磨和处理,确保表面平整。
2.编写数控程序a)根据工件图纸和要求,利用数控编程软件编写加工程序。
b)在程序中定义刀具路径、切削参数和工件坐标系等信息。
3.夹紧工件a)根据工件的形状和尺寸,选择合适的夹具进行夹紧。
b)确保工件夹持牢固,不会出现滑动或变形。
4.载入刀具a)根据加工程序中定义的刀具信息,选择合适的刀具。
b)使用专门的刀具装夹设备将刀具装入数控加工中心的刀库中。
5.调整加工参数a)根据工件的材料和要求,设置合适的切削速度、进给速度和切削深度等参数。
b)根据加工过程中的实际情况,适时调整参数,以获得最佳的加工效果。
6.开始加工a)在数控加工中心的控制面板上输入加工程序。
b)启动加工过程,观察加工状态,确保加工过程中的稳定性和精确性。
7.监控加工过程a)在加工过程中,根据需要,定期监控加工状态,避免出现机械故障或工艺偏差。
b)根据机床的操作手册,操作数控加工中心上的监控系统和装置,保证加工过程的安全和稳定。
8.完成加工a)加工完成后,检查工件的尺寸、形状和表面质量,确保达到图纸要求。
b)清洁工作台和加工设备,将刀具归位,并妥善保管。
9.记录数据a)记录加工过程中的有关数据,如加工时间、加工参数、加工效果等。
b)分析数据,总结经验,为以后的加工提供参考和改进。
以上是数控加工中心加工工艺的基本步骤,具体的加工工艺步骤和要求可能因工件的形状、材料和要求不同而有所差异。
在实际应用中,还需要根据具体情况进行调整和改进,并结合数控加工中心的特点和优势,尽可能提高加工效率和加工质量。
- 1、下载文档前请自行甄别文档内容的完整性,平台不提供额外的编辑、内容补充、找答案等附加服务。
- 2、"仅部分预览"的文档,不可在线预览部分如存在完整性等问题,可反馈申请退款(可完整预览的文档不适用该条件!)。
- 3、如文档侵犯您的权益,请联系客服反馈,我们会尽快为您处理(人工客服工作时间:9:00-18:30)。
(5)加工路线的确定 ① 孔加工进给路线的确定 xoy平面内快速定位至孔中心线,应考虑: •定位快,空行程短;
•定位准,防止进给丝杠反向间隙影响;
•定位快、准不能兼顾时,若最短进给路 线能保证定位精度则取最短路线;反之, 取保证定位准确的路线。
7.2.2 加工中心加工零件的工艺性分析 (1)零件的结构工艺性分析
①零件的切削加工量要小。 ②光孔和螺纹的尺寸规格尽可能少。
③尺寸规格尽量标准化,以便采用标准 刀具。
④零件加工面应具有加工的方便性和可 能性。
⑤零件结构具有足够的刚性,减少装夹、 切削变形。
零件的结构工艺性实例
(2)定位基准的选择 ①尽量选择零件设计基准为定位基准。
(3)刀柄
模块式刀柄
整体式刀柄
(4)刀具尺寸的确定
直径尺寸——孔加工刀具根据孔径确 定,面铣刀与立铣刀直径选择参考铣 削加工。
长度尺寸——满足加工要求前提下, 尽可能减小刀具长度,提高刚度。
7.2.5 刀具预调与换刀点
(1)刀具预调
确定各工序所用刀具在刀柄上装 夹好后的轴向尺寸和径向尺寸,供加 工时使用。一般采用机外对刀仪进行 预调。
c. 铣削轮廓及通槽时,铣刀应有一段切 出距离Z0,可直接快速移动到距工件表 面Z0处。
7.2.4.2 刀具的选择
( 1)对刀具的要求 刀具能够承受高速切削和强力切削,
性能要稳定,一般选用硬质合金、CBN、 金刚石刀具。
( 2)刀具的种类 除铣刀以外,加工中心使用比较多的是
孔加工刀具,包括加工各种大小孔径的麻 花钻、扩孔钻、锪孔钻、铰刀、镗刀、丝 锥以及螺纹铣刀等。
(3)加工工序的划分
工序集中原则:考虑加工精度及效率。
(4)加工顺序的安排
a.尺寸精度——同一加工表面按粗加 工、半精加工、精加工顺序进行;位置 精度——所有加工面先粗加工、然后半 精加工、精加工分开进行。
b.先面后孔
c.相同工位集中加工,应尽量按就近位置 加工,缩短刀具移动距离和空行程时间。
d.工作台回转时间小于换刀时间时,可 采用刀具集中工序。
第7章 加工中心加工工艺
一、学习目标
•了解加工中心的主要加工对象、加工 工艺特点。 •掌握加工中心加工零件工艺性分析的 主要内容与方法。 •掌握加工中心加工工艺路线拟定的内 容及方法。 •能够独立完成一般零件的加工中心加 工工序设计。
二、教学重点
•加工中心的工艺特点及主要加工对象 (7.1) •加工中心工艺路线的拟定 (7.2.3) •加工中心加工工序设计 (7.2.4)
Z向进给分为快速移动进给和工作进给:
加工通孔时,应使刀具伸出一定的切出距离
② 铣削加工进给路线的确定
包括切削进给和Z向进给。切削进 给路线选择参考铣削加工,Z向进给路 线选择方法如下:
a. 铣削开口不通槽时, 铣刀在z向可直接快 速移动到位,不需 工作进给;
铣削封闭槽(如键槽)时,铣刀需 要有一切入距离Za,先快速移动到R平 面,然后以工作进给速度进给至铣削深 度H。
50
5 T05 8铰刀
1
50
6 T06 10铰刀
1
50
7 T07 10高速钢立铣刀 1
50
编制(×5×)×切审削核 用×量××的批选准 择×××
座盒
零件图 号
加工表面
铣上下表面
钻中心孔 钻8H9孔和工艺孔底孔 2-10H9孔底孔 铰8H9孔和工艺孔 铰2-10H9孔 铣削矩形槽、外形
年月日 共 页
备注
三、教学难点
•典型零件的加工中心加工工艺分析 (7.3)
四、考核点 1、定位基准的选择。 2、加工顺序的安排。 3、夹具选择原则。 4、刀具预调。
第七章主要内容讲解
7.2 加工中心加工工艺分析 7.2.1 加工中心加工内容的选择 ① 尺寸精度要求较高的表面。 ② 相互位置精度要求较高的表面。 ③ 不便于普通机床加工的复杂曲面。 ④ 能够集中加工的表面。
T01 125 200 100
②一次装夹完成全部关键部位加工。
③完成尽可能多的加工内容。
④定位基准与设计基准难以重合时,通过 尺寸链计算,严格控制定位基准与设计基 准间联系尺寸的公差范围,确保加工精度
7.2.3 加工中心加工工艺路线的拟订
(1)加工方法的选择 根据零件的表面特征、精度及表面粗糙
度等要求选择相应的加工方法。
平面、平面轮廓及曲面——铣削方式加工,粗 铣IT12~14,Ra12.5~50;精铣IT7~9级, Ra1.6~3.2
r=1mm 第页
(6)填写数控加工工序卡片
座盒零件数控加工工序卡片
单位名称
产品名称或代号
零件名称 座盒
零件图号
Hale Waihona Puke 工序号程序编号夹具名称
使用设备
车间
螺旋压板
TH5660A 数控中心
工步号
工步内容
刀 刀具 主轴 进给 背/侧吃 具 规格 转速 速度 刀量 备注 号 /mm rpm mm/min /mm
1 粗铣上表面
刀具测量直径
获得刀具尺寸的方法: 使用测量装置(如刀具预调仪)
采用机床本身进行测量,存在问题:
•机上调整刀具浪费时间。 •非常困难。 •操作者没有机会和条件详细检查切 削刀具的微观状况。
7.3 典型零件加工中心加工工艺分析
7.3.1 箱体类零件加工中心加工工艺分析
图示零件材料YL12,毛坯尺寸长 宽高19011035,采用TH5660A立式 加工中心加工,单件生产,其加工工艺 分析如下。
(1)零件图工艺分析
(2)确定装夹方案 工艺凸台及工艺孔
(3)确定加工顺序及走刀路线
反面加工
正面加工
(4)刀具的选择
产品名称或代号
零件名称
序号 刀具号 刀具规格名称 数量 刀长mm
1 T01 125可转位面铣
1
刀
2 T02 4中心钻
1
3 T03 7.8钻头
1
50
4 T04 9.8mm钻头
1
孔加工——钻、扩、铰、镗、圆弧插补铣削。
螺纹孔加工——攻丝(M6~M20)、手动攻丝 (M6以下)、镗削( 大于M20)
(2)加工阶段的划分
a.加工中心只完成精加工,不必划分加工阶段
b.零件主要表面在上加工中心前,未经粗加工, 则应分粗加工、精加工两个阶段进行;
c.单件小批生产、新产品试制且精度不高、毛 坯加工余量小时,粗加工、精加工可合并进 行,但应分两道工序并采用相应的夹紧力。