12物料衡算
物料衡算概述
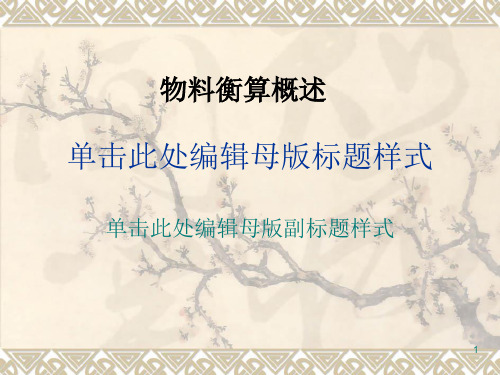
Pharmaceutical Engineering
No Image
4.2.3 衡算范围
在进行物料衡算时,经常会遇到比较复杂的 计算。为计算方便,一般要划定物料衡算范围 。根据衡算目的和对象的不同,衡算范围可以 是一台设备、一套装置、一个工段、一个车 间、一个工厂等。衡算范围一经划定,即可视 为一个独立的体系。凡进入体系的物料均为 输入项,离开体系的物料均为输出项。
对于间歇生产过程和连续生产过程 ,也可以一定质量,如1kg、1000kg(1吨 )或1mol、1kmol的原料或产品为基准进 行物料衡算。
13
Pharmaceutical Engineering
No Image
(3) 衡算基准——单位体积
若所处理的物料为气相,则可以单位体积 的原料或产品为基准进行物料衡算。由于气体 的体积随温度和压力而变化,因此,应将操作状态 下的气体体积全部换算成标准状态下的体积,即 以1m3(标况下)的原料或产品为基准进行物料衡 算。这样既能消除温度和压力变化所带来的影 响,又能方便地将气体体积换算成摩尔数。
(3) 对于有化学反应的体系,应写出化学反 应方程式(包括主、副反应),以确定反应前后 的物料组成及各组分之间的摩尔比。
17
Pharmaceutical Engineering
No Image
4.2.4 衡算方法和步骤
(4) 收集与物料衡算有关的计算数据,包括生产 规模和年生产日;原辅材料、中间体及产品的规格 ;有关的定额和消耗指标,如产品单耗、配料比、 回收率、转化率、选择性、收率等;有关的物理化 学常数,如密度、蒸气压、相平衡常数等。
物料衡算概述
单击此处编辑母版标题样式
单击此处编辑母版副标题样式
物料衡算

3.物料衡算生产过程的总物料衡算3.1.1生产能力年生产商品味精(99%)50000t,折算为100%味精为49500t/a。
日生产商品味精(99%):50000/320=(t/d),折算为100%味精为155t/d。
3.1.2计算指标(以淀粉质为原料)计算指标[10]见表。
表计算指标项目指标淀粉糖化转化率%发酵产酸率(浓度)11%发酵对糖转化率60%培养菌种耗糖为发酵耗糖的%谷氨酸提取收率96%精制收率95%商品淀粉中淀粉含量86%发酵周期(含辅助时间)40h全年工作日320d3.1.3物料衡算(1)1000kg纯淀粉理论上产100%MSG量1000××%×=1153.5kg式中%——谷氨酸对糖的理论转化率——纯味精相对分子质量纯谷氨酸相对分子质量=184147=(2)1000kg纯淀粉实际产100%MSG量1000××%×60%×(100%-%)×96%×95%×=749.6kg (3)1000kg商品淀粉(含量86%的玉米淀粉)产100% MSG量×86%=644.7 kg(4)淀粉单耗①1t100%MSG消耗纯淀粉量1000749.6=t ②1t100%MSG实耗商品淀粉量1000644.7= t/t ③1t100%MSG理论上消耗纯淀粉量10001153.5= t/t④1t100%MSG理论上消耗商品淀粉量0.866986%= t/t (5)总收率可按以下两种方法计算①)749.6)1153.5100%100%64.98% kgkg⨯⨯实际产量(理论产量(==②98.5%60%98.5%96%95%100%64.98%81.7%⨯⨯⨯⨯⨯=(6)淀粉利用率1.008100%65%1.5511⨯=(7)生产过程总损失100%-65%=35%(8)原料及中间品计算①品淀粉或淀粉乳用量:日产100%味精155t,单耗商品淀粉,日耗商品淀粉量155×=d相当日耗100%淀粉:×86%= t/d如使用°Bé,含淀粉30.113g/dL的淀粉乳,日耗量为30%=d(30.113g/dL≈30%)②糖化液量:日产纯糖量×86%××%= t/d只算为30%或34g/dL的糖液30%=; 34= m3③发酵液量:发酵液中纯谷氨酸量×60%×(100%-%)=d折算为谷氨酸11g/dL 的发酵液量11=d×=d 为发酵液相对密度)④提取谷氨酸量:产纯谷氨酸×96%=d折算为90%湿谷氨酸量90%= t/d3.1.4总物料衡算结果总物料衡算结果汇总见表。
化工过程设计 第三章 物料衡算与热量衡算(1)

各流股组份数一览表
HAC 24%
11 循环流 进料 HAC 30% H2O 69.8% H2SO4 0.2% 萃 取 塔 4
流股号 1 2 3
组份数 3 3 3 4 2 2 2 2
1
2
12
3
混合器1
4
5 6 7 8 9 10 11 12
E 7% HAC H2O H2SO4 混合器2
溶 剂 回 收 塔
7(2) E 99% H2O 1%
附加关系式数
自由度
9(4)
(2)溶剂提馏塔及整体的自由度分析
11(2) 循环流
HAC 24%
进料 HAC 30% 1(3) H2O 69.8% H2SO4 0.2% 混合器1 2(3)
萃 取 塔
3(3) 12(2) 溶 剂 回 收 塔 产品流 HAC 99% H2O 1% 产 品 精 馏 塔
独立MB方程数
已知流股变量数 已知其它关系式数 自由度 2、具体MB计算(略)
在开始下一节讲授之前,大家先考虑一个精馏塔的MB问题。 例题:有人提出了一个无反应的单精馏塔流程的方案,试做其MB计算:
100 C3 i-C4 i-C5 C5 kmol/h 0.20 0.30 0.20 0.30
2 1 精 馏 塔 3
MB与HB计算是化工工艺设计中最基本,也是最主要的计算内容。
一、化工流程(过程)中MB、HB、EB三者之间的关系 1、MB与HB之间的关系 MB有可能能单独(不依赖HB而独立)求解; HB一般不能单独求解; (间壁式换热器除外) 当MB不能独立求解时,它就必须与HB联合起来,求解CB。 2、EB与HB之间的关系 流程压力水平不高,而且压力变化也不大,系统能量只考虑其热 焓,而忽略其动能、势能等机械能,在这种情况下:
第三章物料衡算(新)
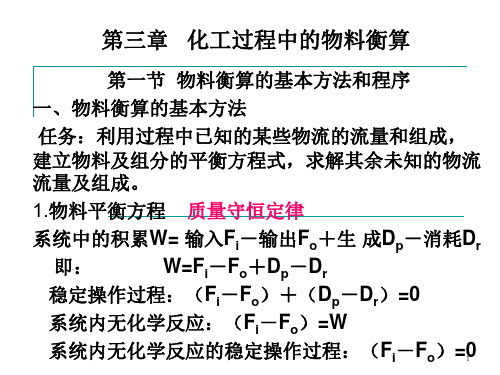
C2H4 + 3 O2
以100kmol进料为基准,用x和y分别代表环氧乙 烷和二氧化碳的生成量,根据题给组成和该系统 的化学反应方程式,可列出下表3-5。
18
表3-5 物料组成
由于反应器出口气体中乙烯和氧的浓度已知, 所以可列出下面两个方程:
解:设 2A+B→2D+E A+D→2C+E C+2B→2F
速率为r1 速率为r2 速率为r3
22
各物质在反应中的变化如表3-4所示 A 进料
/(mol.h-1)
B 100 - r1
C 0
D 0 2r1
E 0 r1
F 0`
200 r2
-2r3
200-2r1-r2 100-r1-2r3
14
有循环物料的反应系统,有两种不同含义的转化 率。一种是新鲜原料通过反应器一次所达到的转 化率,叫单程转化率。这可以理解为以反应器进 口物料为基准的转化率。另一种是新鲜原料进入 反应系统起到离开反应系统止所达到的转化率, 称为全程转化率。显然,全程转化率大于单程转 化率。 (4)收率:转化率是针对反应物而言的,收率则 是针对产物而言的。收率的定义式为:
2.物料衡算基准 选定一个计算基准,并在整个运算中保持一致。 (1)t基准:1d,1h,1s等。 (2)批量基准:每批物料量,Kg/批 。 (3)质量基准:例如取100Kg,一般取某一己知 变量最多或未知变量最少的物流作为基准最为合 适。 (4)体积基准:对气体物料,采用标准体积为基 准,m3,L等。 (5)物质的量基准:有化学反应的取物质的量基 准,mol。
物料衡算

4.2.4 衡算方法和步骤
4
Pharmaceutical Engineering
4.2.1 物料衡算平衡方程式
1.物理过程 根据质量守恒定律, 式中 ——输入体系的总物料量;
G I GO G A
(4-1)
GI ——输出体系的总物料量; GO GA——物料在体系中的总累积量。
பைடு நூலகம்(4-3)
7
Pharmaceutical Engineering
4.2.1 物料衡算平衡方程式
同样,对于稳态过程,组分在体系内没有累 积,则式(4-3)可简化为:
G Ii G Pi GOi G Ri
8
Pharmaceutical Engineering
4.2.2 衡算基准
物料量,不仅总质量平衡,而且对其中的任一组
分或元素也平衡。
6
Pharmaceutical Engineering
4.2.1 物料衡算平衡方程式
2.化学过程 对于有化学反应的体系,式(4-1)和(4-2)仍可 用于体系的总物料衡算或任一元素的物料衡算, 但不能用于组分的物料衡算。
G Ii G Pi GOi G Ri G Ai
13
Pharmaceutical Engineering
4.2.3 衡算范围
在进行物料衡算时 , 经常会遇到比较复杂的
计算。为计算方便 , 一般要划定物料衡算范围。
根据衡算目的和对象的不同 , 衡算范围可以是
一台设备、一套装置、一个工段、一个车间、
一个工厂等。衡算范围一经划定 , 即可视为一
个独立的体系。凡进入体系的物料均为输入
4.1 概述
物料衡算的依据是工艺流程示意图以及为
物料衡算和热量衡算
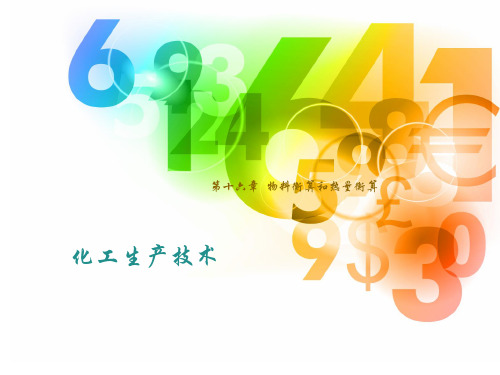
化学反应过程中,物质的量和组分的质量都发生变化,只有 各物料流的质量m守恒(衡算联系物的质量和摩尔数仍守 恒)。
反应过程的物料衡算式
m入 m出
m反 m产
水 %(质量)其它 水 乙苯 (0.0217) 苯乙烯 (0.04) 焦油 (60) ∑
热量衡算是利用能量守恒的原理,通过计算传入和 传出的热量以确定:加热(或冷却)剂用量、设备需要 传递的热量多少等,为工程设计、设备设计提供设 计依据,以保证热量利用方案的合理性,提高热量 的综合利用效果。热量衡算是能量计算的一种,全 面的能量计算应包化算括工。热生产能中、的动能能量和衡电算主能要等是。热量衡
(1) 计算范围 全装置。见图16-5。
(2) 主副反应 反应式见计算过程。甲醇发生五个反应的分 配率为主氧化51.2%,脱氢39.2%,加氢0.6%,深度氧化 0.8%,完全氧化8.2%。
(3) 计算任务 甲醇消耗量,干尾气摩尔组成。
(4) 基准 年工作时为7200 h。以1 h为基准。 8000×1000 kg÷7200 h = 1111.11 kg/h
旁路分流和混合并流都是物理过程。由于没有化学变化,因此可以对总物料及 其中某组分进行衡算。如图16-1所示。
结点A V0=V1+V2 结点B Vl+V3=V4
V2
V3
不合格产品
V0
V1
A
V4 合格产品 B
图 16.1.1 以结点做衡算的示意图
【例16.1.2】 某工厂用烃类气体制合成气生产甲醇。 合化符除H气2成 后 合 装 ,89气的要置以.75体气求,便%量 体 。置 达,为 摩 将换 到气尔 部2脱 工体32组 分艺C1体O成转要m积2后3为化求/减,:气。h小,气送C求2O摩体%去转4尔摩。C化3.O比尔1用气2变为组%此、换C成,变变O反为H换换:H应2:气气52器=4调C各.12和:O%2节为.C48,转。多O.7不62化转少脱%?,
工厂设计-物料衡算
➢ 物料衡算是化工计算的主要内容之一。 ➢ 化工计算包括工艺设计中的物料衡算、能量
衡算、设备选型及计算三部分内容。
➢ 物料衡算是工艺计算的基础,在整个工艺计 算工作中开始的最早,并且是最先完成的项 目。
➢ 当生产方法确定并完成了工艺流程示意图设 计后,即可进行物料衡算。
➢ 由此设计工作由定性分析转入定量计算。
4.2.3 食品机械结构特征代号是表示食品机械的主要工作部件 动作的形式(如冲、印、滚、压等),用汉语拼音第一个大写 字母表示。
4.2.4 食品机械生产能力代号是表示食品机械在单位时间内, 所加工出的产品的实际能力,用阿拉伯数字表示。应以kg/h、 L/h、m/h、m3/h、瓶/h、只/h等为计量单位。
18
■ 物料衡算是设备选型的根据,而设备选型则 要符合工艺的要求。设备选型是保证产品质量 的关键和体现生产水平的标准,又是工艺布置 的基础,并且为动力配电,水、汽用量计算提 供依据。
■设备选型应根据每一个品种单位时间(小时 或分)产量的物料平衡情况和设备生产能力采 确定所需设备的台数。若有几种产品都需要共 同的设备,在不同时间使用时,应按处理量最 大的品种所需要的台数来确定。对生产中的关 键设备,除按实际生产能力所需的台数配备外, 还应考虑有备用设备。后道工序设备的生产能 力要略大于前道工序,以防物料积压。
豆制品 加工机
械
冷饮加 工机械
肉类蛋 品加工
机械
G
糕点(饼干)成型加工机械及包馅、油炸、蒸制等 加工机械和包装机械
T
糖果制品成型加工机械和设备及熬糖、包糖等机械
D
豆类、淀粉类加工机械及其除杂、清洗、破碎等机 械
L
小型汽车水饮料加工设备及冷冻食品等加工机械
物料平衡计算的技巧和步骤
三、物料平衡计算的方法和步骤 (一)水泥厂的物料平衡计算1.烧成车间生产能力和工厂生产能力的计算 (1)年平衡法计算步骤是:按计划任务书对工厂规模(水泥年产量的要求),先计算要求的熟料年产量,然后选择窑型、规格,标定窑的台时产量,选取窑的年利用率,计算窑的台数,最后再核算出烧成系统和工厂的生产能力。
①要求的熟料年产量可按式(3-1)计算: Q y =ped ---100100G y (3-1)式中 Q y ——要求的熟料年产量(t/a );G y ——工厂规模(t/a );d ——水泥重视高的掺入量(%);e ——水泥中混合材的掺入量(%); p ——水泥的生产损失(%),可取为3%~~5%。
当计划书任务书规定的产品品种有两种或两种以上,但所用的熟料相同时,可按下式分别求出每种水泥要求的熟料年产量,然后计算熟料年产量的总和。
Q y1=pe d ---10010011G y1(3-2)Q y2=pe d ---10010022G y2(3-3)Qy=Q y1+Q y2(3-4)式中 Q y1,Q y2——分别表示每种水泥要求的熟料年产量(t/a );G y1,G y2——分别表示每种水泥年产量(t/a ); d 1,d 2——分别表示每种水泥中石膏的渗入量(%); e 1,e 2——分别表示每种水泥中混合材的渗入量(%); Q y ——两种熟料年产量的总和(t/a )。
②窑的台数可按式(3-5)计算:n=1.8760h QQyη (3-5)式中 n ——窑的台数;Q y ——要求的熟料年产量(t/a );Q h.1——所选窑的标定台时产量【t/(台·h)】;η——窑的年利用率,以小数表示。
不同窑的年利用率可参考下列数值:湿法窑0.90,传统干法窑0.85,机立窑0.8~0.85,悬浮预热器窑、预分解窑0.85;8760——全年日历小时数。
算出窑的台数n 等于或略小于整数并取整数值。
例如,n=1.9,取为两台,此时窑的能力稍有富余,这是允许的,也是合理的。
物料衡算
面 粉 875kg 水 315kg 面 粉 350kg
酵 母 25kgkg 接种面团 1372.5kg
水 472.5kg 盐 25kg 油 50kg 切块损 失 52.2kg
可通过工厂实际数 据或实验得来。 注:部分原料工艺 损耗率及原料折用 率见书
糖 62.5kg
二次调粉后面团 2175kg 拌干粉 量 25kg 搓圆后面团 2127.8kg 湿面包坯 2147.8g 成品 1933.02k
损失 214.78k g
P48
三.物料衡算 实例
⒈年产3000T碳酸饮料厂物料衡算
⑴原料成分、产品标准及产品方案 原料成分 产品标准: 产品方案:
序 号 1 2 3 产品名 称 桔汁汽 水 可乐汽 水 小香槟 汽水 年产 量(T) 1400 800 800 一 月 二 月 三 月 四 月 五 月 六 月 七 月 八 月 九 月 十 月 十 一 月 十 二 月
(其中30%—假设稀奶油中F含量)
3)假定脱脂乳中脂肪含量0.05% 4)每吨原料乳可得30%脂肪含量的稀奶油量
1000×3.5%=(1000-X)×0.05%+30%X
X=1000×(3.5-0.05)/(30-0.05)=115kg 5)每吨原料乳可得脱脂乳量
1000×(3.5-0.05)/(30-0.05)=885kg 或1000-115=885kg
3.班产12.5T原汁猪肉罐头工厂
猪肉原料要求 成品标准要求及规格 物料计算过程: (1) 原汁猪肉成品规格397g。 (2) 班成品产量12.5T。 (3) 成品罐数 (4) (5) (6) (7) 需每箱罐数48罐 需纸箱数
=31486.15/48=656(个)
→确定罐型
物料衡算计算公式
物料衡算计算公式
以制叶丝生产线物料衡算为例:
制丝工艺中前后工序之间的流量变化主要是由于水分变化引起,一般采用逐道工序计算的办法。
在计算制丝过程每道工序的在制品加工量(m)时,应根据这道工序加工在制品的实际含水率(h),折算成12%含水率的在制品量(M)。
折算公式为:
m=M(1-12%)/(1-h)
式中:m——某一工序在制品的加工量(kg/h);
M——含水率为12%时的在制品量(kg/h);
h——某一工序加工的在制品含水率(%)。
同样的道理:
计算工序1与工序2之间的变化:
假设工序1在制品加工量M1,含水率H1,工序2在制品加工量M2,含水率H2。
M1已知,则M2的计算公式为:
M2= M1(1- H1)/ (1- H2)
例1:4000kg/h生产线,切片工序在制品加工量为4000kg/h,在制品含水率12%,松散回潮工序在制品加工量为M,含水率为18%,则:M=4000×(1-12%)/(1-18%)=4292kg/h。
例2:4000kg/h生产线,如HT增温工序在制品加工量为4815kg/h,含水率为28%,滚筒干燥后含水率为13%,则滚筒干燥工序在制品加工量M为:
M=4815×(1-28%)/(1-13%)=3984kg/h。
此外,在计算每一工序的在制品加工量时,还要扣去一定的损耗(如扣去筛分掉的碎末等)。
附图:安阳卷烟厂制丝线物料流量衡算图。
- 1、下载文档前请自行甄别文档内容的完整性,平台不提供额外的编辑、内容补充、找答案等附加服务。
- 2、"仅部分预览"的文档,不可在线预览部分如存在完整性等问题,可反馈申请退款(可完整预览的文档不适用该条件!)。
- 3、如文档侵犯您的权益,请联系客服反馈,我们会尽快为您处理(人工客服工作时间:9:00-18:30)。
输入
回收 小计 3077.9 2680.97 3062.5 物料 3062.5 2667.57 3053.3
输
损失
出
小计 未回 收
15.4 3077.9 13.4 2680.97 9.2 3062.5
双2667.57
挤出造粒 3053.3 风送粒料 3038 半成品 粒 3038 粉 2667.57 159.58
=3191.5吨/年
• 自然损耗量占: 3191.5吨×0.1%=3.192吨 • 扫地料占: 3191.5吨×0.4%=12.766吨
• 下脚料占: 3191.5吨×5.5%=175.542吨
• 双螺杆生产线: 年产量为2500吨
• 半成品粉料需要量 :2500吨/0.94=2659.57吨
• 自然损耗量占: 2659.57×0.1%=2.660吨
Hst
ACR
0.8
0.6 3 5 0.5 10 0.03
0.62
0.46 2.31 3.81 0.38 7.7 0.02
6.2
4.6 23.1 38.1 3.8 77 0.2 1000
35.71
26.49 133.03 219.41 21.88 443.43 1.15 5758.87
0.119
0.088 0.443 0.730 0.073 1.477 0.004 19.177
自然损 扫地料 风送 失 0.2 0.3 0.2
合计损 耗率% 总损失 %
0.5
0.3
0.5
0.2
1.5
进入本工序的物料量 =出料量/1-本工序的损失 给双螺杆供料
进入捏合输送的物料量:
2659.57*/(1-0.3%)=2667.57吨
损失量:2667.57-2659.57=8吨
进入筛选输送的物料量:
*
二.物料衡算的方法步骤
1. 画流程示意图
2. 写出主付化学反应式
3. 确定计算任务
4. 收集数据资料
5. 选定计算基准 6. 展开计算 7. 校核与整理计算结果 8. 绘制物料平衡图 *
1.画流程示意图
• 对设备外形、尺寸比例无严格要求
• 无化学变化或相变化、无损耗的设备可 省略不画 • 体现物料的名称、数量、组成及流向
(1) (2) (3) (4) 年工作日 365-11(法定节假日)=354天(8496小时) 设备大修 25天/年=600小时/年 特殊情况停车 11天/年=264小时/年 机头清理 换过滤网 1次/6天 8小时/次 [354天-(25天+11天)]×1次/6天×8小时/次 =424小时(17.7天) (5) 实际开车时间 365-11-25-11-17.7=300.3(天) 或 8760-264-600-264-424=7208(小时) (6) 设备利用系数K K=实际开车时间/年工作时间=7208/8496=0.84
课程结束
2013.01
给单螺杆供料 进入捏合输送的物料量: 3053.3/(1-0.3%)=3062.5吨 损失量: 3062.5-3053.3=9.2吨 进入筛选输送的物料量 3062.5/(1-0.5%)=3077.9吨 损失量: 3077.9-3062.5=15.4吨
混合造粒工段物料平衡表 单位吨
工序
物料 筛选输送 单 3077.9 双 2680.97 捏合输送 单 3062.5
• 反映与计算有关的工艺条件(温度、压力、 流量、配比等) • 标明已知数据和待求的未知数据
2.写出主付化学反应式
有化学反应的塑料成型过程: (1)热固性塑料成型
(2)发泡制品成型
(3)反应挤出
3. 确定计算任务
• 对照示意图和反应式,分析每一步骤,每 一设备中的化学反应和物理变化及对物 料的数量、组成及物料走向所产生的影 响
总5758.87 筛选输送 5730.07 混合输送 3053.3 粉料2659.57 挤出造粒 粒料3038 损失 粒料风送 3031.92 回收159.58 挤出成型 成品5500吨 损失 6.08 损失 损失 28.8 损失 17.2
15.3
自然损耗 5.852 扫地料 26.062 下脚料 319.156 损失 15.956 未回收 143.62
5. 选定计算基准
• 从后往前计算---从年产量出发,计算原料年需要 量、中间产品及三废年生成量 • 从前往后算: (1) 按100公斤出发计算,算出产品量 (2) 与实际产量比较,求出相差倍数
(3) 以上述倍数作为系数求出需要原料量、中间 产物和三废生成量
• 连续化生产: 公斤/小时, 间歇操作:公斤/批 *
4. 收集数据资料
生产过程无特殊现象: 8000∽8400小时/年 停车检修以及出现不合格产品、停车更换过 网时间: 600-800小时/年 每年连续生产时间为 7200小时/年(300天)
4. 收集数据资料
(2) 原料、助剂、中间产物和产品的规格 (3) 有关的物理常数,如密度、相平衡常等
注意资料的可靠性、准确性和数据的 适用范围
• 选定合用的公式 • 分析数据资料,确定已知项和未知项(分 可查到的和需通过计算求出的),弄清计 算任务
4. 收集数据资料
(1) 设计任务数据
① 生产规模--按设计任务书规定,或根据 消耗定额,还应考虑物料在车间的回流 情况 ② 生产时间—确定物料衡算的时间基准, 算出每小时的生产任务,确定设备的 大小
2667.57
3053.3 3038 3197.58
2659.57
3038 3031.92 3197.58
8.0 2667.57
15.3 3053.3 6.08 3038 3197.58 143. 62
粉料 合计
3077.9+ 2680.97
=
5758.87
4.计算物料年需要量、日需要量和每小时需要量
• 扫地料占: 2659.57×0.5%=13.296吨
• 下脚料占:
2659.57×5.4%=143.614吨
• 下脚料回收破碎损耗为5%, 实际可回收量:
(175.542+143.614)×(1-0.05)=303.20吨
• 不可回收部分:
(175.542+143.614)-303.2=15.956吨
2667.57/(1-0.5%)=2680.97吨
损失量:2680.97-2667.57=13.4吨
给单螺杆供料 进入风送的物料量(粒料): (3191.5*-159.58)/(1-0.2%)=3038吨 注:半成品中加入的回收料按进入单螺杆挤出 成型机粒料的5%计: 3191.5×5%=159.58 kg 下脚料未回收部分为: 303.2-159.8=143.4吨 进入挤出造粒的物料量(粉料): 3038/(1-0.5%)=3053.3吨 损失量:3053.3-3038=15.3吨
3.物料衡算
(1) 挤出成型工段物料衡算 (2) 混合造粒工段物料衡算
(1)挤出成型工段物料衡算
挤出成型工段物料损耗表
工 序 百分率% 自然损耗 扫 地 单 0.1 双 0.1 0.4 0.5 下脚料 5.5 5.4 一次成 品 94 94
• 单螺杆生产线: 年产量定为3000吨 • 半成品粒料需求量:3000/0.94
挤出成型工段物料平衡表
工序 物料 量 (吨) 输入物料 量 自然损 耗量 扫地料
单位:吨 下脚料 成品
3.192 12.766 175.542 3000 单 *3191.5 (粒料) 2.660 13.296 143.614 2500 双 *2659.57 (粉料) 5.852 26.062 319.156 5500 合计
原料
名称 PVC CPE 三盐
配方
份数 100 8 2
百分率
% 77 6.2 1.5
每吨产品
消耗定额 770 62 15
5758.87吨
混合粉料
年需要量吨 日需要量吨 小时需要量kg 4434.33 357.05 86.39 14.766 1.189 0.288 615.25 49.54 12.0
Pbst
物料衡算
2013.01
物料衡算
一. 概述 *
二. 物料衡算的方法步骤 * 三. 物料衡算实例 *
一. 概述
• 物料衡算: 设计工作由定性阶段→定量阶段
(1) 在实际生产过程中,物料衡算可以确定生产过 程中的物料比例和物料转变的定量过程,揭示 物料的浪费和生产过程的反常现象,从而帮助 找到改进措施,提高成品率,减少副产品、 杂质和三废排放量,为改进生产提供途径 (2) 设计新车间, 新装置
• 物料平衡—质量守恒定律的具体表现形式
进入的物料量≡排出物量+过程的积累量
或:引入设备的物料量≡操作后产物重量+物料损失
∑F = ∑D + W
F-进料量, D-出料量与损耗量, W-累积量
• 对于稳态连续过程,进料量总和等于出料量与损耗 量总和,即W为零。此时,可变成:
• W=0 ∴ ∑F = ∑D
(2) 混合造粒工段物料衡算
混合造粒工段物料损耗
① 给双螺杆提供粉料 工 序 筛选 自然损失 损耗率% 合计损耗率% 0.2 0.5 输送 扫地料 0.3 0.3 0.3 捏合输送
总损失
0.8
② 给单螺杆提供粒料
工 序 筛选 输送 自然损 失 损耗率 % 0.2 扫地 料 0.3 捏 合 输 送 0.3 挤出 造粒 粒料
4.96
3.67 18.46 30.42 3.04 61.54 0.167 799.047
DOP 石蜡 碳酸钙 碳黑 合计
129.93 100
5. 画物料平衡图
单位吨
碳酸钙 443.43 碳黑 1.15