焊缝X射线检测及其结果的评判方法综述
焊缝X射线检测及其结果的评判方法综述

目前 , 接 已作 为一 种基本 工艺 方法 , 焊 应用 于航 空、 天、 船 、 航 舰 桥梁 、 车辆 、 炉 、 锅 电机 、 电子 、 冶金 、 能 源 、 油化 工 、 山机械 、 石 矿 起重 机械 、 建筑 及 国防等 各个 工 业 部 门… 。 由于 焊 接 过 程 中 各 种参 数 的 影
技术素质和经验差异 以及外界条件的不同而引起的 误 判或 漏 判 , 评判 过程 客观化 、 学化 和规范化 。 使 科
图 1 图 像增 强 实 时成 像检 测 系 统 原 理 图
F g 1 S e c fi a e i t n i e - a e i . k t h o g - e sf r b s d m n i
为 了解 决 上 述 问题 ,0世 纪 9 2 0年 代 末 出 现 了 x射 线 数 字 实 时 成 像 检 测 技 术 ( it aisoy Dga rdocp , il D , 称 为 x 射 线 数 字 照相 ( iil ai rpy R)亦 Dgt d gah , ar o D , R)其工 作原 理 如 图 3所 示 。X 射线 数 字 实 时 成 像 系统 中使 用 的平 板 探 测器 ( lt ae e c r 如 Fa pnl t t ) deo 图 4所示 , 其像 元 尺寸 最 小 可 达 0 17rn 因 而 成 .2 l, n
黑度 分布 是判 断影 像 性 质 的 又一 个 依 据 。另 外 , 缺 陷影像 在 x射线底 片 上 的位 置 , 就是 缺 陷 在 工 件 也 中位 置 的反映 , 这是 判 断 影像 缺 陷性 质 的第 三 个 依
据。
焊接 过程 中产 生 的缺 陷 主要 有 六类 , : 1 熔 即 () 合不 良 : 焊透 、 未 未熔 合 ;2 裂 纹 : 裂 纹 、 裂 纹 ; () 热 冷 ( ) 洞 : 孔 、 孔 ;4) 杂 物 : 渣 、 钨 ; 5 3孔 气 缩 ( 夹 夹 夹 () 成形 不 良: 咬边 、 穿 和焊 瘤 等 ; 6 其 他 缺 陷 。射 烧 ()
焊缝检测总结报告

焊缝检测总结报告引言焊缝检测是在焊接过程中对焊缝的质量进行评估的重要步骤。
通过对焊缝的有效检测,可以确保焊接工艺的合格性,减少焊缝缺陷带来的安全隐患。
本文将对焊缝检测的常用方法和相关技术进行总结,以期提供对焊缝质量检测的全面了解。
焊缝检测方法X射线检测X射线检测是一种常用的焊缝检测方法,通过利用X射线的穿透能力,可以观察焊缝内部的缺陷情况。
这种方法可以检测出焊缝中的气孔、夹渣等缺陷,并能够确定其大小和位置。
X射线检测设备通常由射线发生器和探测器组成,通过对焊缝进行扫描和分析,可以得出检测结果。
然而,由于X射线的辐射性质,操作人员需要具备专业的技术和安全意识。
超声波检测超声波检测是另一种常用的焊缝检测方法。
通过利用超声波在物质中传播的特性,可以观察焊缝内部的缺陷情况。
这种方法可以检测出焊缝中的气孔、夹渣、裂纹等缺陷,并能够确定其大小和位置。
超声波检测设备通常由发射器和接收器组成,通过对焊缝进行扫描和分析,可以得出检测结果。
相比于X射线检测,超声波检测具有非破坏性和无辐射的优势,操作相对较简单。
磁粉检测磁粉检测是一种常用的焊缝检测方法,适用于对表面缺陷进行检测。
通过在焊缝表面施加磁场,再施加磁粉粉末,可以观察焊缝表面的缺陷情况。
磁粉检测可以检测出焊缝表面的裂纹、疲劳损伤等缺陷,并能够确定其大小和位置。
磁粉检测设备通常由磁场产生器和磁粉粉末组成,通过对焊缝表面施加磁场和磁粉粉末,可以得出检测结果。
然而,磁粉检测只能检测表面缺陷,对于焊缝内部的缺陷无法提供有效检测。
焊缝检测技术数字图像处理技术数字图像处理技术在焊缝检测中发挥着重要作用。
通过将焊缝的图像进行数字化处理,可以对焊缝进行精确定位和分析,进而得出检测结果。
数字图像处理技术包括图像增强、边缘检测、图像匹配等方法,能够有效地提高焊缝检测的准确性和可靠性。
机器视觉技术机器视觉技术是一种应用广泛的焊缝检测技术。
通过利用计算机视觉系统,可以对焊缝进行自动检测和分析,实现对焊接过程的自动化控制。
焊缝射线照相底片的评判规律

焊缝射线照相底片的评判规律
一、探伤人员要评片,四项指标放在先*,底片标记齐又正,铅字压缝为废片。
二、评片开始第一件,先找四条熔合线,小口径管照椭圆,根部都在圈里面。
三、气孔形象最明显,中心浓黑边缘浅,夹渣属于非金属,杂乱无章有棱边。
四、咬边成线亦成点,似断似续常相见,这个缺陷最好定,位置就在熔合线。
五、未焊透是大缺陷,典型图象成直线,间隙太小钝边厚,投影部位靠中间。
六、内凹只在仰焊面,间隙太大是关键,内凹未透要分清,内凹透度成弧线。
七、未熔合它斜又扁,常规透照难发现,它的位置有规律,都在坡口与层间。
八、横裂纵裂都危险,横裂多数在表面,纵裂分布范围广,中间稍宽两端尖。
九、还有一种冷裂纹,热影响区常发现,冷裂具有延迟性,焊完两天再拍片。
十、有了裂纹很危险,斩草除根保安全,裂纹不论长和短,全部都是Ⅳ级片。
十一、未熔和也很危险,黑度有深亦有浅,一旦判定就是它,亦是全部Ⅳ级片。
十二、危害缺陷未焊透,Ⅱ级焊缝不能有,管线根据深和长,容器跟着条渣走**。
十三、夹渣评定莫着忙,分清圆形和条状,长宽相比3为界,大于3倍是条状。
十四、气孔危害并不大,标准对它很宽大,长径折点套厚度,中间厚度插入法。
十五、多种缺陷大会合,分门别类先评级,2类相加减去Ⅰ,3类相加减Ⅱ级。
十六、评片要想快又准,下拜焊工当先生,要问诀窍有哪些,焊接工艺和投影。
注:*四项指标系底片的黑度、灵敏度、清晰度、灰雾度必须符合标准的要求。
**指单面焊的管线焊缝和双面焊的容器焊缝内未焊透的判定标准。
射线评片技巧焊缝未熔合射线底片影像特点修订版
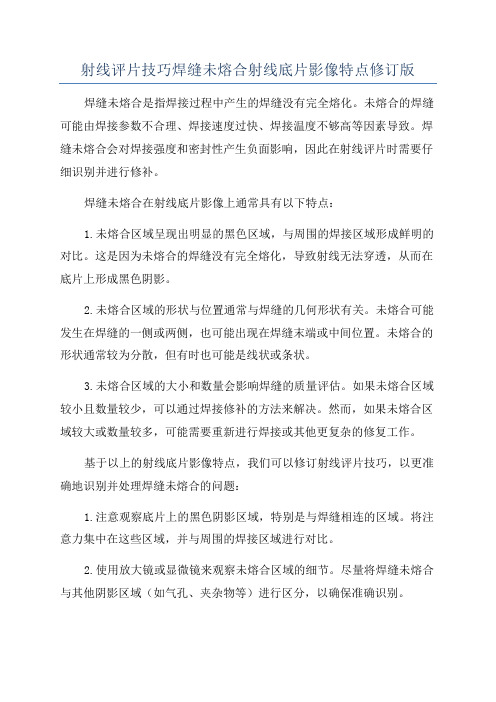
射线评片技巧焊缝未熔合射线底片影像特点修订版焊缝未熔合是指焊接过程中产生的焊缝没有完全熔化。
未熔合的焊缝可能由焊接参数不合理、焊接速度过快、焊接温度不够高等因素导致。
焊缝未熔合会对焊接强度和密封性产生负面影响,因此在射线评片时需要仔细识别并进行修补。
焊缝未熔合在射线底片影像上通常具有以下特点:1.未熔合区域呈现出明显的黑色区域,与周围的焊接区域形成鲜明的对比。
这是因为未熔合的焊缝没有完全熔化,导致射线无法穿透,从而在底片上形成黑色阴影。
2.未熔合区域的形状与位置通常与焊缝的几何形状有关。
未熔合可能发生在焊缝的一侧或两侧,也可能出现在焊缝末端或中间位置。
未熔合的形状通常较为分散,但有时也可能是线状或条状。
3.未熔合区域的大小和数量会影响焊缝的质量评估。
如果未熔合区域较小且数量较少,可以通过焊接修补的方法来解决。
然而,如果未熔合区域较大或数量较多,可能需要重新进行焊接或其他更复杂的修复工作。
基于以上的射线底片影像特点,我们可以修订射线评片技巧,以更准确地识别并处理焊缝未熔合的问题:1.注意观察底片上的黑色阴影区域,特别是与焊缝相连的区域。
将注意力集中在这些区域,并与周围的焊接区域进行对比。
2.使用放大镜或显微镜来观察未熔合区域的细节。
尽量将焊缝未熔合与其他阴影区域(如气孔、夹杂物等)进行区分,以确保准确识别。
3.将未熔合的焊缝区域绘制在焊接图上,以形成焊缝未熔合区域的几何形状。
这有助于评估未熔合的大小和位置,并指导后续修补的方法。
4.根据未熔合的大小和数量,确定相应的修补措施。
对于较小的未熔合区域,可以采用焊接修补的方法。
对于较大或数量较多的未熔合区域,需要重新进行焊接或其他更复杂的修复工作。
总之,射线评片技巧是识别焊缝未熔合问题的重要工具。
通过观察底片上的特点,我们可以准确识别未熔合的区域,并采取相应的修补措施。
修订后的射线评片技巧将使评估焊缝质量变得更准确和可靠。
焊缝射线检测评片技术

焊缝评片的关键技术一:各类型的缺陷产生的原因1:焊接方法的影响2一、外观缺欠1、咬边因焊接造成沿焊趾(或焊根)处出现的低于母材表面的凹陷或沟槽称为咬边。
它是由于焊接过程中,焊件边缘的母材金属被熔化后,未及时得到熔化金属的填充所致。
咬边可出现于焊缝一侧或两侧,可以是连续的或间断的。
(1)危害:咬边将削弱焊接接头的强度,产生应力集中。
在疲劳载荷作用下,使焊接接头的承载能力大大下降。
它往往还是引起裂纹的发源地和断裂失效的原因。
焊接技术条件中一般规定了咬边的容限尺寸。
(2)形成原因:焊接工艺参数不当,操作技术不正确造成。
如焊接电流大,电弧电压高(电弧过长),焊接速度太快。
(3)防止措施:选择适当的焊接电流和焊接速度,采用短弧操作,掌握正确的运条手法和焊条角度,坡口焊缝焊接时,保持合适的焊条离侧壁距离。
2、焊瘤焊接过程中,在焊缝根部背面或焊缝表面,出现熔化金属流淌到焊缝之外未熔化的母材上所形成的金属瘤称为焊瘤。
焊瘤一般是单个的,有时也能形成长条状,在立焊、横焊、仰焊时多出现。
(1)危害:影响焊缝外观,使焊缝几何尺寸不连续,形成应力集中的缺口。
管道内部的焊瘤将影响管内介质的有效流通。
(2)形成原因:操作不当或焊接规范选择不当。
如焊接电流过小,而立焊、横焊、仰焊时电流过大,焊接速度太慢,电弧过长,运条摆动不正确。
(3)防止措施:调整合适的焊接电流和焊接速度,采用短弧操作,掌握正确的运条手法。
3、凹坑焊后在焊缝表面或背面形成低于母材表面的局部低洼缺陷。
未焊满由于填充金属不足,在焊缝表面形成的连续或断续的沟槽。
(1)危害:将会减小焊缝的有效工作截面,降低焊缝的承载能力。
(2)形成原因:焊接电流过大,焊缝间隙太大,填充金属量不足。
(3)防止措施:正确选择焊接电流和焊接速度,控制焊缝装配间隙均匀,适当加快填充金属的添加量。
4、烧穿焊接过程中熔化金属自坡口背面而流出,形成穿孔的缺陷。
常发生于底层焊缝或薄板焊接中。
(1)形成原因:焊接过热,如坡口形状不良,装配间隙太大,焊接电流过大,焊接速度过慢,操作不当,电弧过长且在焊缝处停留时间太长等。
射线评片技巧焊缝未熔合射线底片影像特点
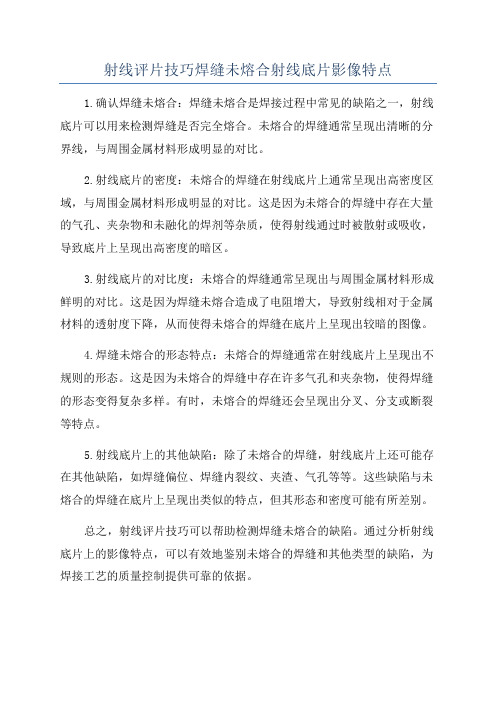
射线评片技巧焊缝未熔合射线底片影像特点
1.确认焊缝未熔合:焊缝未熔合是焊接过程中常见的缺陷之一,射线底片可以用来检测焊缝是否完全熔合。
未熔合的焊缝通常呈现出清晰的分界线,与周围金属材料形成明显的对比。
2.射线底片的密度:未熔合的焊缝在射线底片上通常呈现出高密度区域,与周围金属材料形成明显的对比。
这是因为未熔合的焊缝中存在大量的气孔、夹杂物和未融化的焊剂等杂质,使得射线通过时被散射或吸收,导致底片上呈现出高密度的暗区。
3.射线底片的对比度:未熔合的焊缝通常呈现出与周围金属材料形成鲜明的对比。
这是因为焊缝未熔合造成了电阻增大,导致射线相对于金属材料的透射度下降,从而使得未熔合的焊缝在底片上呈现出较暗的图像。
4.焊缝未熔合的形态特点:未熔合的焊缝通常在射线底片上呈现出不规则的形态。
这是因为未熔合的焊缝中存在许多气孔和夹杂物,使得焊缝的形态变得复杂多样。
有时,未熔合的焊缝还会呈现出分叉、分支或断裂等特点。
5.射线底片上的其他缺陷:除了未熔合的焊缝,射线底片上还可能存在其他缺陷,如焊缝偏位、焊缝内裂纹、夹渣、气孔等等。
这些缺陷与未熔合的焊缝在底片上呈现出类似的特点,但其形态和密度可能有所差别。
总之,射线评片技巧可以帮助检测焊缝未熔合的缺陷。
通过分析射线底片上的影像特点,可以有效地鉴别未熔合的焊缝和其他类型的缺陷,为焊接工艺的质量控制提供可靠的依据。
电子束焊缝X射线检测技术
电子束焊缝X射线检测技术X射线检测是在不改变、不损害材料和零件的状态和使用性能的前提下,判断材料和零件的内部是否存在缺陷的技术。
自1930年X射线检测进入工业应用以来,一直是重要的无损检测方法之一,它不仅可用于金属材料的检验,也可用于非金属材料和复合材料的检验,还可以用于放射性材料的检验,被广泛地应用于航空、航天、船舶、兵器、核工业、电子等各工业领域。
其中应用最广泛的方面是铸件和焊接件的检验。
1.2 X射线检测基本原理当均匀的射线束透照物体时,如果物体局部存在缺陷,它将改变物体对射线的衰减,使得不同部位透射射线的强度不同,导致在胶片上形成影像差异,根据影像判断物体内部的缺陷和物质分布。
原理图见图1。
图1-射线检测原理图1.3问题提出目前国军标和航标中没有针对电子束焊缝的检测要求。
而电子束焊缝射线检测不同于其他焊接形式的焊缝检测,电子束焊缝有着本身特点,如电子束焊缝中易形成小气孔,而电子束焊缝尺寸厚大,如果参数选取不适当,底片对比度降低,容易出现漏检。
电子束焊缝对射线束角度要求也非常高,否则不易检出未熔合、未焊透缺陷。
因此,需要对电子束焊缝X射线检测提出具体要求。
本文根据X射线检测基本原理,电子束焊缝特点,国外相关规范,结合射线照相的影像质量,对设备,工序安排,检测方法,过程控制提出了具体要求。
2 射线照相的影像质量2.1影像质量三个要素对比度、不清晰度,颗粒度是决定射线照片影像质量的3个重要因素。
影像的对比度决定了在透照方向上可识别的细节尺寸。
影像的不清晰度决定了在垂直射线透照方向上可识别的细节尺寸。
影像的颗粒度决定了影响可显示的细节最小尺寸。
3 电子束焊缝X射线检测要求3.1电子束焊接特点和缺陷类型目前,电子束焊接技术得到越来越广泛的推广和应用。
X射线检验是检测电子束焊缝的重要手段之一。
只有掌握电子束焊接特点和电子束焊缝缺陷类型,才能根据这些特点和缺陷类型形成原因、缺陷特征、分布特点,选择正确的检测手段和准确评定。
焊缝X射线检测及其结果的评判方法综述
第!期
周正干, 等: 焊缝 $ 射线检测及其结果的评判方法综述
0’
难以判别的缺陷图像, 作更高级的图像处理, 使缺陷形 状变得醒目, 再供给评定人员作最终评判。这种系统 就是人机对话系统。此为计算机评片的中级阶段, 对 缺陷自动判别系统。 难判缺陷的明朗化较有效。 ( !) 对获取的图像尽可能采用非定量图像处理, 使缺陷位 置和形状突现, 再通过自动判别系统, 对缺陷作定量评 价、 等级分类和合格判定。此为计算机评片的高级阶 段。它是上述 (") ( #) 两系统的综合和发展, 引入了人 工智能等算法。国内沈阳工业大学李德元和徐鲁宁等 人对焊缝 $ 射线底片的自动评判进行了一些深入研 究, 实现了图像的输入和输出、 图像的预处理、 缺陷边 界的提取以及伪彩色处理等基本功能, 并为典型条形 缺陷的区分与识别建立了判据
[&] 焊透缺陷等 。上海理工大学何怡、 杨永才和王海鹏
在国 外, 法 国 LNE 无 损 检 测 技 术 实 验 室 的 4) OC:C?>P 和 5 ) 37Q,+; 等人运用边缘检测和区域检测相 结合的方法, 能够较好地从射线实时成像系统获取的 图像中将焊接区域分离出来, 通过对焊接区域图像的
["0] 分析, 实现对焊接过程的自动控制 ; 印 度 R>/ (:;.+F:,S+>+ 工程学院电气电子工程系的 T:U+;F- 5+9
等人运用数字图像处理技术, 在对 $ 射线底片数字图 像进行预处理的基础上, 提取出焊缝缺陷的若干参数, 采用统计模式识别的方法对缺陷进行分类, 实现了焊
[’] 缝 $ 射线底片的计算机辅助评判 。
[&] 法是 : 将射线底片图像通过底片数字化扫描设备 (或
焊缝探伤检测方法
焊缝探伤检测方法
焊缝探伤检测方法
一、简介
焊缝探伤检测方法是一种采用 X 射线等无损检测技术对焊缝内部探伤缺陷进行检测的方法。
它以 X 射线等有效检测技术为基础,将被检物(焊缝)放置于相应的检测装置中,使电子或 X 射线撞入物体后,使其衰减和散射,利用其吸收率来测量物体内部的缺陷情况。
二、探伤原理
1、X 射线探伤原理
X 射线探伤原理是基于 X 射线撞击物体后,使得物体内部缺陷离子化,从而改变 X 射线的吸收率,从而可以检测出物体内部的缺陷。
2、电子束探伤原理
电子束探伤原理是电子束撞击物体后,由于其能量的传递,使得物体内部缺陷离子化,从而改变 X 射线的吸收率,从而可以检测出物体内部的缺陷。
三、优缺点
1、优点:
(1)无损性检测:X 射线和电子束探伤技术属于无损检测技术,可以精确地检测焊缝内部缺陷,而不会损坏焊缝。
(2)灵敏度高:X 射线和电子束探伤技术具有非常高的灵敏度,可以检测到局部小型缺陷离子化。
2、缺点:
(1)技术复杂:X 射线和电子束探伤技术技术难度较大,除需要专业的设备外,还需要熟练的操作人员。
(2)成本较高:X 射线和电子束探伤技术属于高投入的检测技术,检测成本较高。
小口径管线焊缝X射线检测方法分析及改进
小口径管线焊缝X射线检测方法分析及改进X射线检测方法是焊缝质量无损检测必要的方法之一,工件定位、X射线机的定位、透照方式和射线透照参数的确定,都需要以工件定位来实现X射线检测的功能。
整个定位装置实行一次中心定位,定位装置具有固定性和快捷性,在设计制作过程中对定位的焊接、圆环的形式、工件的定位和滑动结构,必须按照透照方式,对透照参数等提出一定的要求。
标签:X射线;工件定位;透照方式;效果TB随着一体化橇装装置的广泛使用,装置上集成的设备工艺管线也不断变化增大、工艺管线的焊接质量要求越来越严格,检测的规格难易程度也随之增大,出现了透照难度大,检测效率低等弊端。
对于X射线检测方法提出了较高的要求。
1 透照方式根据JB/T4730.2—2005标准,直径小于100mm管线焊口通常采用定向X射线机椭圆成像倾斜透照法,椭圆开口在一倍焊缝宽度。
定向X射线机对焊缝检测工作影响因素有三方面:其一,只能针对焊口单一逐张透照,工作效率慢;其二,定向X射线机透照场太小;其三,费工时,误工期,费人力。
通过上述现象分析,对于影响焊缝检测工作的各个环节因素确定切实可行的保证措施,将定向透照改为周向透照,检测方式由倾斜透照法改为平移透照。
(1)倾斜透照法与平移透照法比较:倾斜透照法是以主射线偏离焊缝一定角度透照的一种方式,见图1,平移透照法射源焦点偏离工件焊缝中心以射线束的边缘部分透照,见图2。
(2)比较结果:平移透照法椭圆成像开口宽度根据公式计算可有效控制;而倾斜透照法只能由操作人员凭经验控制开口宽度;即平移透照法优于倾斜透照法。
根据平移透照开口宽度计算公式:L=(b+q)L1/L2=F-(D+△h)D+△h(b+q)式中:h—焊缝余高;F—焦点至胶片的距离;D—管子外径;b—焊缝宽度;q—椭圆开口宽度。
2 透照范围根据根据JB/T4730.2—2005标准,定向X射线机的原理透照范围只有40°,满足不了实现管线周向透照的目标。
- 1、下载文档前请自行甄别文档内容的完整性,平台不提供额外的编辑、内容补充、找答案等附加服务。
- 2、"仅部分预览"的文档,不可在线预览部分如存在完整性等问题,可反馈申请退款(可完整预览的文档不适用该条件!)。
- 3、如文档侵犯您的权益,请联系客服反馈,我们会尽快为您处理(人工客服工作时间:9:00-18:30)。
焊缝X射线检测及其结果的评判方法综述 周正干, 滕升华, 江 巍, 李和平 (北京航空航天大学机械工程及自动化学院,100083 北京)摘 要:分析了焊缝X射线检测方法的现状,指出了目前存在的主要问题;介绍了焊缝X射线检测结果的人工评定和计算机辅助评定方法,论述了国内外焊缝X射线检测结果计算机辅助识别的研究现状。
研究结果表明,X射线数字实时成像技术是焊缝射线检测的发展方向,焊缝射线数字图像的计算机自动分析与识别技术是射线实时成像技术成功应用的基础。
关键词:无损检测;图像处理;模式识别;焊接中图分类号:TP391.6 文献标识码:A 文章编号:0253-360X(20002)03-85-04周正干0 序 言目前,焊接已作为一种基本工艺方法,应用于航空、航天、舰船、桥梁、车辆、锅炉、电机、电子、冶金、能源、石油化工、矿山机械、起重机械、建筑及国防等各个工业部门[1]。
由于焊接过程中各种参数的影响,焊缝有时不可避免地会出现熔合不良、裂纹、气孔、夹渣、夹钨、未熔合和未焊透等缺陷。
为了保证焊接构件的产品质量,必须对其中的焊缝进行有效的无损检测和评价。
射线检测是常规无损检测的重要方法之一,是保证焊接质量的重要技术,其检测结果将作为焊缝缺陷分析和质量评定的重要判定依据[2]。
对X射线检测结果的评定方法有两种:人工评定和计算机辅助评定。
当人工评定检测结果时,评定人员的工作量大,眼睛易受强光损伤,效率较低,而且缺陷分析受评定人员的技术素质、经验以及外界条件的影响,结果往往会因人而异。
采用计算机对X射线检测结果进行分析和识别,可以大大提高工作效率,有效地克服人工评定中由于评判人员技术素质和经验差异以及外界条件的不同而引起的误判或漏判,使评判过程客观化、科学化和规范化。
1 焊缝X射线的检测方法目前,焊缝X射线检测最常用的方法是胶片照相法。
X射线胶片照相的成像质量较高,能正确提供焊缝缺陷真实情况的可靠信息,但是,它具有操作过程复杂、运行成本高、结果不易保存且查询携带不便等缺点。
随着电子技术及计算机技术的发展,一收稿日期:2001-11-01种新兴的X射线检测技术———基于X射线图像增强器(X ray image intensifier)的实时成像技术(Ra2 dioscopy)应运而生,其工作原理如图1所示,图2是一种典型的图像增强器。
X射线图像增强实时成像检测技术的出现使焊缝X射线检测的效率大大提高。
但是,与胶片照相法相比,由于图像增强实时成像法成像环节较多,信噪比低,图像容易产生畸变,故成像质量相对较低,检测结果的图像对比度和空间分辨率均不是很高。
图1 图像增强实时成像检测系统原理图Fig.1 Sketch of im age2intensifier2b asedradioscopy system为了解决上述问题,20世纪90年代末出现了X 射线数字实时成像检测技术(Digital radioscopy,DR),亦称为X射线数字照相(Digital radiography,DR),其工作原理如图3所示。
X射线数字实时成像系统中使用的平板探测器(Flat panel detector)如图4所示,其像元尺寸最小可达0.127mm,因而成像质量及分辨率明显优于X射线图像增强器系统,几乎可与胶片照相媲美,同时还克服了胶片照相中第23卷 第3期2002年6月焊接学报TRANS ACTI ONS OF THE CHI NA WE LDI NG I NSTIT UTI ONVol.23 No.3June 2002表现出来的缺点。
图2 一种典型的图像增强器系统Fig.2 T ypical image intensifiersystem图3 X 射线数字照相系统原理图Fig.3 Sketch of digital radiographysystem图4 一种典型的X 射线平板探测器系统Fig.4 T ypical X -ray flat panel detector system2 焊缝X 射线底片的评判2.1焊缝X 射线底片的人工评判正确地识别X 射线底片上的影像,判断影像所代表的缺陷性质,评定人员可根据影像的几何形状、黑度分布及位置三方面进行综合考虑,做出判断。
不同性质的缺陷具有不同的几何形状和空间分布特点。
例如,气孔一般成球形,裂纹多为宽度很小、且有变化的缝隙等。
由于X 射线底片上缺陷的影像是缺陷的几何形状按照一定规律在平面上投影形成的图形,因此,影像的几何形状常常是判断缺陷性质的最重要依据。
不同性质的缺陷其内在性质不同:气孔可认为内部含有气体;夹杂物是不同于工件本身材料的物质等。
这种不同性质的缺陷对射线的吸收不同,形成的缺陷影像黑度也就不同,故影像的黑度分布是判断影像性质的又一个依据。
另外,缺陷影像在X 射线底片上的位置,也就是缺陷在工件中位置的反映,这是判断影像缺陷性质的第三个依据。
焊接过程中产生的缺陷主要有六类,即:(1)熔合不良:未焊透、未熔合;(2)裂纹:热裂纹、冷裂纹;(3)孔洞:气孔、缩孔;(4)夹杂物:夹渣、夹钨;(5)成形不良:咬边、烧穿和焊瘤等;(6)其他缺陷。
射线检测主要检测的是前5类,以下是焊接常见缺陷在射线底片上的表现形式[3],评片人员可据此识别之。
未焊透在X 射线底片上一般呈现为笔直的黑线影像,并处于焊缝影像的中心,实际的未焊透缺陷影像还可能是断续的黑线、变宽的黑线条、偏离焊缝中心线的黑线等,或伴随其他形态影像的线状影像。
未熔合在X 射线底片上的形态与射线束的方向有关,一般情况下它呈现为模糊的宽线条状影像,线条沿焊缝方向延伸,位置与未熔合的位置相关,影像的黑度与背景的黑度差较小,有时影像的一侧呈现直边状。
裂纹在X 射线底片上的基本形态呈现为黑线,影像的黑度可能较大,也可能较小,容易与其它缺陷的影像相区别;由于裂纹属于窄缝性缺陷,所以当射线束与它的扩展面成较大角度时,裂纹的影像将变得很模糊,甚至在X 射线底片上不能形成具有一定对比度的裂纹影像,这点需要注意。
气孔在X 射线底片上呈现为黑度大于背景黑度的斑点状影像,黑度一般都较大,影像清晰,影像的形状可能是圆形、椭圆形或长圆形(梨形)。
夹渣在X 射线底片上常见的影像有点状夹渣、密集夹渣和条状夹渣三种形态,其影像的主要特点是形状不规则、边缘不整齐、黑度较大而均匀。
夹钨的影像主要有孤立点状和密集点状两种形态。
咬边在X 射线底片上类似于夹渣,但它一定出现在焊缝区两侧。
烧穿在X 射线底片上呈现为低黑度的圆环或椭圆环及中心高黑度的暗斑形貌。
焊瘤在X 射线底片上呈现为具有圆滑轮廓的较大的低黑度斑点影像,它可能出现在焊缝区内,但经常是出现在焊缝两侧区。
2.2焊缝X 射线底片的计算机辅助评判国内外对于X 射线底片的计算机评判的通用方法是[4]:将射线底片图像通过底片数字化扫描设备(或CC D 摄像机和模数转换器)变成数字图像,然后将其输入计算机,应用适当的图像处理系统,对其进行数据处理———降噪、平滑化、清背景和差分等,再将处理结果用三维图显示或彩色显示,这样无需熟练技术,缺陷形状也很容易识别。
这仅是射线底片计算机评定的初级阶段。
射线底片的全自动评定86 焊 接 学 报第23卷需要多道程序:(1)缺陷检出系统。
其主要目标是对射线底片上的影像进行图像处理,研究图像中缺陷的存在及其位置,并采用适当的图像显示———三维显示或彩色显示。
此为初级水平的自动化。
(2)缺陷辅助判别系统。
对因有噪声存在难以判别的缺陷图像,作更高级的图像处理,使缺陷形状变得醒目,再供给评定人员作最终评判。
这种系统就是人机对话系统。
此为计算机评片的中级阶段,对难判缺陷的明朗化较有效。
(3)缺陷自动判别系统。
对获取的图像尽可能采用非定量图像处理,使缺陷位置和形状突现,再通过自动判别系统,对缺陷作定量评价、等级分类和合格判定。
此为计算机评片的高级阶段。
它是上述(1)(2)两系统的综合和发展,引入了人工智能等算法。
国内沈阳工业大学李德元和徐鲁宁等人对焊缝X射线底片的自动评判进行了一些深入研究,实现了图像的输入和输出、图像的预处理、缺陷边界的提取以及伪彩色处理等基本功能,并为典型条形缺陷的区分与识别建立了判据[5]。
南京气象学院的傅德胜和郑关胜等人也对焊缝X射线底片图像的计算机处理与识别进行了研究,通过选择缺陷的若干模式参数,建立了焊缝缺陷计算机识别模式的基本方法,能比较准确地识别出圆形缺陷、裂纹缺陷、长形夹渣和未焊透缺陷等[6]。
上海理工大学何怡、杨永才和王海鹏等人运用数字图像处理技术,在对X射线底片数字图像进行预处理的基础上,提取出焊缝缺陷的若干参数,采用统计模式识别的方法对缺陷进行分类,实现了焊缝X射线底片的计算机辅助评判[7]。
在国外,日本冈山科技大学的shkia利用模糊推理的方法实现了焊缝X射线底片的计算机自动分析和焊接缺陷的计算机识别,其识别效果达到了专业评片人员的水平[8];德国柏林BAM公司的C.Jacobsen等人利用图像处理和神经网络技术实现了X射线底片中焊缝裂纹缺陷的自动识别[9];阿尔及利亚的Nacereddine Nafa和Drai Redouane等人利用数字图像处理技术实现焊缝边界的轮廓跟踪,利用神经网络技术实现了焊缝缺陷的分类[10];德国汉堡的T.Just和W.Thale等人运用数字图像处理技术,实现了对焊缝X射线底片的自动分析和缺陷识别[11];白俄罗斯飞行器焊接及表面涂层技术研究所的A. E.K apustin和I.I.Bardus ova等人也研究了焊缝底片的计算机辅助识别技术[12]。
另外,法国、乌克兰和英国等都在此领域进行了卓有成效的研究工作,并在1999年柏林召开的“CT在工业中的应用及X射线照相中的图像处理”会议上发表了相关的研究论文[13~15]。
3 焊缝X射线实时成像结果的计算机辅助评定射线实时成像检验技术,是实时地将射线照相的强度分布转换成可见光图像并对检验结果作出评定的技术。
目前用于生产实际的射线实时成像检验系统主要有图像增强实时成像检验系统和数字实时成像检验系统。
图像增强实时成像检验系统的工作原理及设备前已述及。
对于该种实时成像检验系统形成的图像进行自动分析的研究工作,国内已开展了多年,如清华大学的任大海和尤政、天津大学的孙长库和叶声华等人均在此领域进行了多年的研究工作,运用数字图像处理技术和神经网络技术建立了焊缝X射线实时成像自动分析系统,现已应用于实际焊缝检验,取得了良好的效果[16]。
广东粤海钢瓶厂曾祥照、彭志华等同志在此方面亦进行了一些研究工作,他们研制了图像增强实时成像的图像辅助评定软件,用于对焊缝检测图像的辅助评定,使焊缝缺陷评定工作准确性和速度大大提高,评定结果纳入检测数据库管理[17]。