Powder and waterborne coatings 2000–2010
耐高温可焊车间底漆

耐高温可焊车间底漆张双喜【摘要】Energy saving, cost reduction, environmental protection and safety are the important problems for shipbuilding and paint industry. A new weldable and heat resistant shop primer was developed. Through the comparison with conventional shop primer, test this new shop primer showed an excellent heat resistance (up to 1 200 ℃) , less burnt extention and u-nique welding performance which could reduce the re - rust - removing workload and the manufacture. This new shop primer was comparatively simple and convenient to apply and environmentally friendly, as well as harmless to the operator. It will bring a prospective market and vast economic and social efficiency.%节能降本、绿色环保和健康安全是造船业、涂料业面临的大问题.本研究阐述了新一代耐高温可焊性车间底漆的制备过程,并且与传统型、第一代车间底漆之间进行了系统的比较,发现其耐高温,烧延面积小,焊接性能好,大大减少了二次除锈重涂的工作量,在很大程度上降低了制造成本;新一代耐高温车间底漆施工操作简单、方便、环保,并且采用醇类溶剂作为稀释剂,对操作工人身体无毒害,具有广阔的市场前景和很高的经济效益及社会效益.【期刊名称】《涂料工业》【年(卷),期】2013(043)004【总页数】4页(P66-69)【关键词】车间底漆;焊接性;切割性;耐腐蚀性;耐热性;再涂性【作者】张双喜【作者单位】上海胜星树脂涂料有限公司,上海201405【正文语种】中文【中图分类】TQ635.9现代船舶由大型钢板焊接而成。
细滑石粉的分散及其在水性涂料中的应用
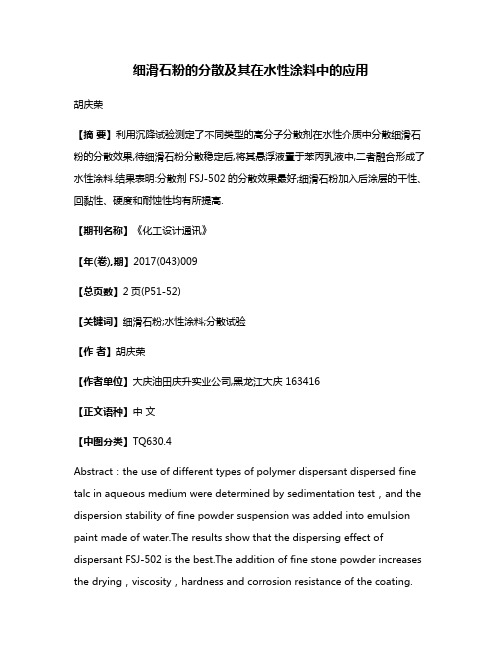
细滑石粉的分散及其在水性涂料中的应用胡庆荣【摘要】利用沉降试验测定了不同类型的高分子分散剂在水性介质中分散细滑石粉的分散效果,待细滑石粉分散稳定后,将其悬浮液置于苯丙乳液中,二者融合形成了水性涂料.结果表明:分散剂FSJ-502的分散效果最好;细滑石粉加入后涂层的干性、回黏性、硬度和耐蚀性均有所提高.【期刊名称】《化工设计通讯》【年(卷),期】2017(043)009【总页数】2页(P51-52)【关键词】细滑石粉;水性涂料;分散试验【作者】胡庆荣【作者单位】大庆油田庆升实业公司,黑龙江大庆 163416【正文语种】中文【中图分类】TQ630.4Abstract:the use of different types of polymer dispersant dispersed fine talc in aqueous medium were determined by sedimentation test,and the dispersion stability of fine powder suspension was added into emulsion paint made of water.The results show that the dispersing effect of dispersant FSJ-502 is the best.The addition of fine stone powder increases the drying,viscosity,hardness and corrosion resistance of the coating.Key words:fine stone powder;waterborne coatings;dispersion test随着经济和技术的进步,细滑石粉被广泛运用于各行各业中,例如涂料、化妆品、塑料及造纸等。
将细滑石粉运用到涂料过程中,能够达到涂料与墙面形成易刷、平整及光泽度好的效果,因此,使用了细滑石粉的涂料,具有良好的耐冲击性、柔韧性,并且其具有硬度高的特点。
高固体份涂料
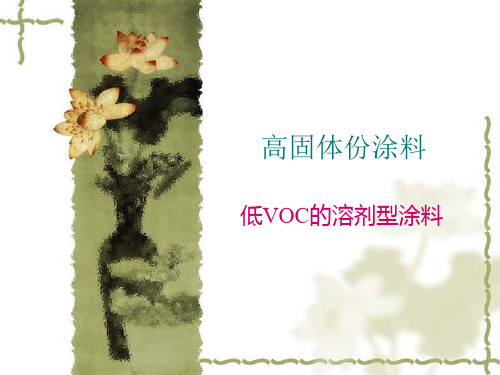
窄分子量分布的丙烯酸树脂的合成
采用夺氢能力较弱的引发剂,如叔戊基过氧化合物;因为引 发剂夺氢能力越小,所得树脂的粘度越低 提高引发剂浓度。引发剂浓度可达4%或更高 较高合成反应温度(超过150℃) 采用链转移剂,如羟基硫醇链转移剂,不仅可以降低丙烯酸 树脂的分子量,还可以提供聚合物端羟基。这些方法都有利 于得到相对窄的分子量分布和低分子量。 新的聚合工艺用于生产低聚物,并不需要较高的引发剂浓度
多异氰酸酯和多元醇的粘度
产品 摩尔质量 粘度 cPs@25℃ 供货形式 中等固含 的多元醇 30000 2000 60%固含 高固含多 元醇 <10000 5000 80%固含 多元醇的粘度远高于多异氰酸酯。 实际上即使是低粘度的多元醇的 其粘度也是多异氰酸酯的数倍。 即使采用粘度仅仅为几厘泊的多 异氰酸酯,对降低涂料粘度的能 力也有限。然而为了满足降低 聚氨酯涂料中,多异氰酸酯占基料 中重量的20~30%,对涂料整体粘 度的影响较小 VOC的挑战,最简单的方法就是 制备更低粘度的固化剂。通过在 生产工艺过程中的改变,就能获 得更低粘度的三聚体和缩二脲。
热喷涂和超临界流体喷涂酸雨对汽车面漆层腐蚀作用的评价方法分散剂表面锚定基团对不同的颜料的锚定性能有机颜料naptholredperylenesquinacridone酞氰绿碳黑anthraquinonediaryides多胺多元醇聚氨酯氢键基团无机颜料eg氧化铁红titanates钛酸酯钛白粉胺羧酸基团磺酸基团磷酸基团离子或酸碱基团颜料类型基团类型锚固机理常用的两类超分散剂图3基于多锚定基团的超分散剂图3基于单锚定基团的超分散剂超分散剂的中聚合物链和锚定基团的链接形式锚定基团在聚合物的末端锚定基团在聚合物的两端bab型嵌段共聚物aba嵌段共聚物无序共聚物梳型共聚物高固体份涂料的活性稀释剂2050交联后低聚物的tg50050000粘度100cpsohnco氨基树脂cooh环氧基氨基树脂硅醇自缩合nh环氧nco官能团类型23官能团度400800窄分布分子量理想范围性能为了提高户外耐候性常加入硅氧烷作为反应性稀释剂可提高汽车清漆的耐酸雨性低分子量的丙烯酸多元醇分子量分布较窄其官能团度较低
水性涂料用流平剂

2 涂膜缺陷的成因
在涂料施工过程中常出现的涂膜缺陷有桔皮 、鱼 眼 、缩孔 、缩边 、贝纳德旋涡 、浮色 、发花等 。与其相关 的影响因素是表面张力 、底材粗糙度 、湿膜厚度 、施工 后涂料触变性 、涂膜的湿边时间和干燥时间等 。
水性涂料通常是非牛顿流体 ,有其特性粘度和触 变性 。由于在涂料施工过程中剪切力变化 ,涂装后涂 料的触变性是影响流平性的重要因素 。自干涂料在 涂装后即达到最低粘度 ,容易流平 ;烤漆在烘烤阶段 达到最低粘度 ,物理干燥过程的溶剂挥发 ,或化学干 燥过程中的交联都会引起粘度的增大 ,并且这种粘度 的增大会超过因温度升高而引起的粘度下降 。因此 ,
另外 ,温度 、浓度 、溶液挥发速度或涂料组分之间 的密度不同都可形成表面张力梯度 ,引起涂膜表面不 平整 。
通常 ,上述这些现象都可借助流平剂来解决 。
4 流平剂的作用
加入流平剂会影响涂膜的外观 、层间附着力和再
涂性 。常规的流平剂有丙烯酸共聚物 、有机硅和氟碳
表面活性剂三类 。以甲基丙烯酸酯作为单体的均聚
不过通常涂膜厚度不能超过涂料的由于底材的粗糙度湿膜厚度涂装后涂料的触变性和涂膜的湿边时间都由涂料体系施工方式和固化条件而定因此只有表面张力这一因素是可通过调整配方来改变的
·环境保护·
水性涂料用流平剂
G. Hobisch ,I. Kriessmann ,W. Staritzbichler (Solutia Austria GmbH) U. Kubillus (Solutia Chemicals ( Thailand) Ltd. )
收稿日期 2002 - 01 - 18 联系人地址 上海市西藏中路 18 号港陆广场 1806 室周小姐 联系电话 (021) 63867500 转 27
翻译14
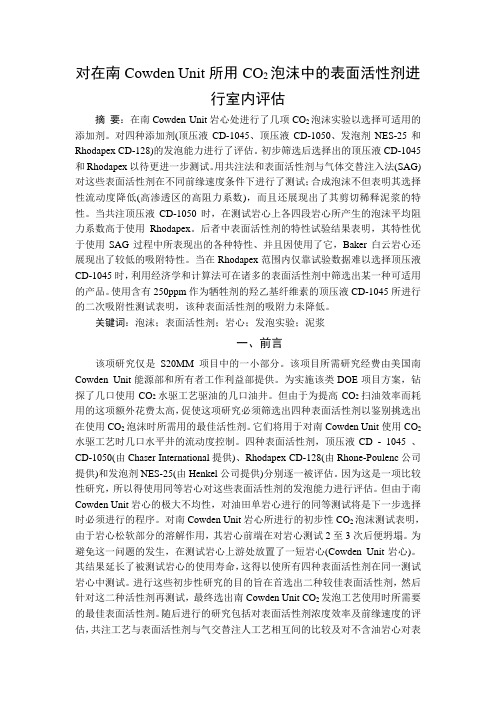
对在南Cowden Unit所用CO2泡沫中的表面活性剂进行室内评估摘要:在南Cowden Unit岩心处进行了几项CO2泡沫实验以选择可适用的添加剂。
对四种添加剂(顶压液CD-1045、顶压液CD-1050、发泡剂NES-25和Rhodapex CD-128)的发泡能力进行了评估。
初步筛选后选择出的顶压液CD-1045和Rhodapex以待更进一步测试。
用共注法和表面活性剂与气体交替注入法(SAG)对这些表面活性剂在不同前缘速度条件下进行了测试;合成泡沫不但表明其选择性流动度降低(高渗透区的高阻力系数),而且还展现出了其剪切稀释泥浆的特性。
当共注顶压液CD-1050时,在测试岩心上各四段岩心所产生的泡沫平均阻力系数高于使用Rhodapex。
后者中表面活性剂的特性试验结果表明,其特性优于使用SAG过程中所表现出的各种特性、并且因使用了它,Baker白云岩心还展现出了较低的吸附特性。
当在Rhodapex范围内仅靠试验数据难以选择顶压液CD-1045时,利用经济学和计算法可在诸多的表面活性剂中筛选出某一种可适用的产品。
使用含有250ppm作为牺牲剂的羟乙基纤维素的顶压液CD-1045所进行的二次吸附性测试表明,该种表面活性剂的吸附力未降低。
关键词:泡沫;表面活性剂;岩心;发泡实验;泥浆一、前言该项研究仅是S20MM项目中的一小部分。
该项目所需研究经费由美国南Cowden Unit能源部和所有者工作利益部提供。
为实施该类DOE项目方案,钻探了几口使用CO2水驱工艺驱油的几口油井。
但由于为提高CO2扫油效率而耗用的这项额外花费太高,促使这项研究必须筛选出四种表面活性剂以鉴别挑选出在使用CO2泡沫时所需用的最佳活性剂。
它们将用于对南Cowden Unit使用CO2水驱工艺时几口水平井的流动度控制。
四种表面活性剂,顶压液CD - 1045 、CD-1050(由Chaser International提供)、Rhodapex CD-128(由Rhone-Poulenc公司提供)和发泡剂NES-25(由Henkel公司提供)分别逐一被评估。
氯化橡胶云铁防锈漆

PracticalCoverage实际涂布率
Allow appropriate loss允许适量损耗
Application Details
施工详述
Mix Radio混合比
One pack单罐装
Method of Application施工方法
Airless Spray无空气喷涂Recommended推荐采用
该涂料为溶剂型涂料,为避免事故或危险发生,应采取最低限度的安全措施如下:
此涂料为易燃物,并含有挥发性易燃溶剂,故必须远离火星和明火。
严禁在作业场所吸烟,并应该采取有效措施,防止火星产生(如采用防爆电器设备,杜绝静电积累,避免金属撞击等)。
施工场所应尽量保持良好通风。为消除使用过程中的爆炸隐患,应保证足够的通风量以维持气体/空气比例不超过最低爆炸极限的10 %,通常每千克溶剂需要200立方米通风量,(与溶剂种类相关)就能维持最低爆炸极限10 %的工作环境。
不限
Storage and
Handling
贮存与管理
Storage贮存Store in cool and dry conditions贮存于阴凉干燥处
Pack size包装规格25Kg in 20 liter container 25公斤装于20公升容器中
Flash Point闪点≥31℃高于23℃
The product is a kind of solvent-based paint. In order to avoid the accident or dangerous occurrence, minimal safety precaution, as follow, should be down.
粉末涂料英语

The investigation of IR, DSC, GPC showed that water resistance, corrosion resistance, stockpiling property and mechanical strength of the lanthanide bakelite modified epoxy powder coating were improved apparently and showed the way was feasible.利用红外、DSC、GPC等测试方法,对粉末涂料进行研究,发现改性后粉末涂料体系耐水性及耐腐蚀性能明显提高,其贮存性能及力学强度也得到了明显改善,说明此方法可行。
收藏指正2.FC-1 CORROSION PROTECTIVE EPOXY POWDER COATINGFC-1防腐型环氧粉末涂料收藏指正3.Performance Research of White Pure Polyester Powder Coatings白色纯聚酯粉末涂料的性能研究收藏指正4.Study on High-adhesive Force Epoxy Powder Coating高附着力环氧粉末涂料的研究收藏指正5.Industrial clients specialized in production of paint and coating ,ink, building materials, adhesive and sealant ,plastics, pharmaceutical goods and pigments can all be benefited from the multinational suppliersnetwork of WWRC.生产油漆、粉末涂料、油墨、建筑材料,粘胶剂及密封剂、塑料、原料等行业的工业用家,均可透过环绮化工搜寻最合适的原料。
IOS-MAT-0066-10

Issued bySignatureAuthorised bySignature Replaces:Björn Johansson and Stellan GrönbergProduct Requirements & Compliance/Product Laws & StandardsPär Stenmark Manager Product Requirements & Compliance/IKEA of SwedenAA-163938-9Surface coatings and coverings – general requirementsContentsThis specification describes IKEA requirements on surface coatings and coverings, solvents and thinners used to treat surfaces before and after coating/covering the products as well as surface cleaning, metal surface treatment and stainless steel surfaces, in respect of chemical content, physical properties, visual qualities, and documentation. The specification is valid for application of surface coatings and coverings (see section 6 Definitions ) to all substrates except the following:•Coating on leather• Printing and coating on textiles• Non-film-forming printing on paper and cardboard other than foil/covering (whereas film-forming printing on paper is included in the IOS-MAT-0066; and printing/coating on foil covering is also included in IOS-MAT 0066, as part of the covering).• Coatings applied to paper during the production process of paper. This coating is considered as part of the paper and included within the scope of IOS-MAT-0010. • Ceramic glazes • Enamel on metal• Inorganic decorations which are fused into/onto glass, enamel, or ceramic glazes• Glue-based filler used for spot application (e.g. white glue with saw dust, or hotmelt glue) • Mirror paint that is in the scope of IOS-MAT-0088• Coatings on zip fasteners that are in the scope of IOS-PRG-0029 • Bed slats coated with glue in the scope of IOS-MAT-0109 • Labels that are in the scope of IOS-PRG-0019• Plastic film applied on paper (this is in the scope of IOS-MAT-0010)About this specificationThis specification addresses IKEA suppliers as well as their surface coating and coveringsuppliers. The purpose of this specification is to describe IKEA requirements concerning surface coatings and coverings in order to:• Minimise harmful effects to environment and health from IKEA articles.• Ensure compliance of IKEA articles with health and environment regulations in all IKEA markets.• Ensure the quality of surfaces on IKEA articles, such as surface resistance, surface appearance, correct colour and gloss, and good workmanship. This document is connected to IOS-TM-0002 Surface resistance – test methods.All references to standards and legislations shall be seen as referring to the latest updated version, unless otherwise stated.Implementation of changesChanges in this specification, version no AA-163938-10, shall be implemented in production at the latest from packaging date stamp 1619 (year 2016 week 19).Products having a packaging date stamp earlier than specified above shall be shipped to IKEA before shipping products compliant with this version of the specification.Signing of the self declaration by the coating/covering supplier means that all their materials delivered after signature date comply with all applicable requirements in IOS-MAT-0066 version 10 (AA-163938-10) – regardless of the specification’s latest implementation date for the IKEA supplier of the changed requirements.Renewal of verification documentationSigning of the self declaration by the coating/covering supplier means that all their materials delivered after signature date comply with all applicable requirements in IOS-MAT-0066 version 10 (AA-163938-10) – regardless of the specification’s latest implementation date stamp for the changed requirements in the IKEA sales article.Changes to regulations and lists referred to in this documentWhen new substances are added to lists of substances (in laws, in standards or by authorities), or classified according to classifications, which are referred to in this specification, the requirements for these substances shall be fulfilled within four months after the substance has been added to the cited list, unless otherwise specified by IKEA.Annual self declarations do not need extra renewal in case new substances are added to the lists of banned substances, unless otherwise stated.Table of contents1Chemical requirements (4)1.1Surface coatings and coverings – requirements for all substrates (4)1.1.1Additional requirements specifically for powder coatings – all substrates (10)1.1.2Additional requirements specifically for UV coatings – all substrates (11)1.2Additional requirements for surface coatings and coverings for solid wood, wood-based materials, and wood-like natural materials (12)1.2.1Additional requirements specifically for UV coatings (14)1.3Additional requirements for surface coatings and treatments for metal substrates (15)1.4Additional requirements for surface coatings for polymeric substrates (16)1.5Additional requirements for surface coatings for glass (16)2Physical properties (16)2.1Surface resistance (16)2.1.1Applicability of surface resistance requirements tables 2.1.A to 2.1.K (16)2.1.2Verifying tests of surface resistance (16)2.1.3Surface resistance requirements (17)2.1.4Scope of surface resistance tables regarding wood-like natural materials (21)2.2Surface coating/covering adhesion (21)2.3Coating blocking and stickiness (21)3Visual requirements (22)3.1Colours (22)3.1.1Colour samples (22)3.1.2Approval of colour and tolerances (22)3.2Gloss (23)3.3Surface appearance and defects in coating film/finish (23)3.4Fingerprints (23)3.5Textured paints (23)4Metal surfaces – coatings and stainless steel (24)4.1Service conditions (24)4.1.1Requirements (25)4.2Corrosion requirements and test methods (26)4.2.1Neutral salt spray test (26)4.2.2Acetic acid salt spray test (26)4.2.3Dip test (26)4.2.4Minimum thickness (28)4.2.5Stainless steel – grinding and polishing requirements (28)4.2.6Use of polishing and finishing compounds (28)4.3Corrosion and coating thickness test frequency (30)5Documentation (30)5.1Verifying tests (30)5.2Sample information (30)5.2.1Test to verify the chemical content (30)5.2.2Test to verify the physical properties (31)5.2.3Test to verify the corrosion on metal surfaces (31)5.3Requirements on test reports and self declarations (31)5.4Safety Data Sheets (SDS) and Technical Data Sheets (TDS) (31)5.5Self declarations (32)5.5.1Inorganic coatings (32)5.5.2Water-based degreasing, iron phosphating and electrolytic zinc plating (32)5.5.3UV coatings (32)5.5.4Solvents used for cleaning (32)5.6Documentation exception (32)5.7Certificate of Compliance of CPSA/CPSIA (33)5.8Warning limits (investigation limits) as a support for compliance (33)6Definitions (34)Appendix A: List of allowed biocides used as preservatives during storage (41)Appendix B: Test methods for surface resistance – deviations and comments (42)Appendix C: Surface coating/covering declaration of chemical substances by surface coating/covering supplier (43)Appendix D: Lead test requirement according to 16 CFR, Part 1303 (USA) (48)Appendix E: Polishing and finishing compounds for metal substrates declaration of chemical substances by polishing and finishing supplier (51)References (53)Summary of Changes in version 10 (55)1Chemical requirementsWhen choosing surface coating and covering materials, and production processes, the aim shall be to select an alternative which minimises any harmful effects to health and environment:•In the raw material•During the production process•During use of the article•When the article becomes wastePrior to packing, the finished surface shall be cured and well ventilated. Requirements on emissions and odour from the final product are stated in IOS-MAT-0010 Chemical compounds and substances.The IKEA supplier is responsible that only surface coating and covering components and systems, which are guaranteed by the coating/covering supplier to fulfil the requirements listed below on content of chemical substances, are used in the production of IKEA products.The IKEA supplier is also responsible to secure that there is no contamination of the surface coating/covering leading to non-compliance with the IKEA chemical requirements in this specification.Note: Solvent for cleaning/degreasing includes solvents used before and after the application ofa surface coating/covering, as well as on surfaces that are not coated/covered.1.1Surface coatings and coverings – requirements for all substrates Table 1.1 Surface coatings and coverings – general requirementsSurface coating/ covering Substance Requirements Test method MinimumDocumentRequirementLiquid coatings •Alkylphenolethoxylates(APEO)•Alkylphenols(AP)•AlkylphenolphosphitesNot allowed to be used.Contamination limit value: 0.10 % in theready-to-use mixture.Extraction(methanol +ammoniumacetate) +HPLC anddetection byMS DADSelfdeclaration(SD)Table 1.1 Surface coatings and coverings – general requirementsSurface coating/ covering Substance Requirements Test method MinimumDocumentRequirementLiquid coatings Biocides of allkindsAddition of biocides used as preservativesfor products during storage (=in-canpreservatives) is only allowed according tothe list of allowed biocides in Appendix A.The concentration of individual biocides, orof mixtures of biocides as parts of aweighted sum (see Appendix A forexplanation), shall not exceed the limits inAppendix A.Addition of biocides used for any otherpurpose is not allowed, unless otherwisestated in the product documentation(Biocides used as film and woodpreservatives are included in IOS-MAT-0098).Addition of biocides is also allowed afterpermission from IKEA. Permission is neededfor all biocides not listed in Appendix A. SeeTable C1 in Appendix C.Apart from the above, biocides used aspreservatives for products during storagebut not in Appendix A and coming fromcoating ingredients that are used at aconcentration of maximum2 % of the final coating component can beused, as long as they are not CMR and theirsum concentration is not above5 ppm (0.0005 %) in the final surfacecoating component.Screeningtest. Differentextraction andanalysismethodsdepending onwhich mate-rials and sub-stances to betested.SDTable 1.1 Surface coatings and coverings – general requirementsSurfacecoating/coveringSubstance Requirements Test method MinimumDocumentRequirement All types ofsurfacecoatings/coverings,thinners,and pre-treatmentCMRsubstancescategory 1Aand 1B andSubstances ofVery HighConcern(SVHC)CMR substances category 1A and 1B andSVHC are not allowed to be used.Contamination limit value: 0.10 %For coatings, this contamination limit valueis valid for each separate coatingcomponent.Some examples of CMR substances that arenot allowed:•N-methyl-2-pyrrolidone (NMP)(CAS no: 872-50-4)•2-ethoxy-ethanol (ethyl glycol) (CASno: 110-80-5)•2-ethoxy ethylacetate (ethyl glycolacetate) (CAS no: 111-15-9)•Dimethylformamide (DMFA, DMFO)(CAS no: 68-12-2)•2-methoxy ethanol (Ethylene glycolmonomethyl ether, EGME) (CAS no:109-86-4)•2-methoxy ethylacetate (methyl glycolacetate EGMEA) (CAS no: 110-49-6)Note: The following CMR substances areallowed to be used in the followingprocesses:•Inorganic nickel compounds and boricacid/borates used in electrochemicalplating baths•Inorganic nickel compounds used whenanodizing•Inorganic cobalt compounds used inbath for post-treatment after electrolyticzinc plating•Formaldehyde – only according tosection 1.2, 1.3 and 1.5.Screeningtest. Differentextraction andanalysismethodsdepending onwhichmaterials andsubstances tobe tested.SDSurfacecoveringsElementalchlorinebleachingPulp that has been bleached with elementalchlorine is not allowed to be used in themanufacturing of supporting paper.-- SDAll types ofsurfacecoatings/covering,thinners,and pre-treatmentFragrances Fragrances, perfumes and masking agentsare not allowed to be used withoutapproval from IKEA.-- SDTable 1.1 Surface coatings and coverings – general requirementsSurface coating/ covering Substance Requirements Test method MinimumDocumentRequirementLiquid coatings, and coverings Organotin(tinorganic)compoundsNo kind of organotin compounds areallowed to be used.Contamination limit value for sum of allorganotin compounds:2.5 mg/kg dry surface material.The limit values refer to the alkyl/aryl tincation without the counter ion.Note: test requirement refers to organotinslisted in the definition of organotincompounds.Exception: In polyurethane coatings onglass, dibutyltin dilaurate (DBTL, CAS no:77-58-7) including monoalkyltin compoundsare allowed to be used as catalyst at amaximum concentration of 0.05% totalorganotin in the ready-to-use mixture.Extraction andGC-MSFor EDcoating: SDand Testreport (TR)For allothers: SDAll types of surface coatings/ coverings Phthalates The following phthalates are not allowed tobe used:•phthalates defined as CMR substancescat 1A or 1B•phthalates that are SVHC•phthalates listed on theState of California“Proposition 65” list•di-n-octyl phthalate, DNOP(CAS no. 117-84-0)Contamination limit value: 500mg/kg forsum of all phthalates. For coatings, thislimit is valid both in the solid content of theready-to-use mixture and in the dry surfacematerial.Note: For information purposes, IKEA willaim to keep an updated list on IKEASupplier Portal of phthalates that areclassified as CMR or SVHC by the EuropeanUnion or that are on the CalifornianProposition 65 list, and thus in the scope ofthis requirement.Extraction andGC-MSSDSurface coatings and coverings PVC (Polyvinylchloride)Not allowed to be used -- SDTable 1.1 Surface coatings and coverings – general requirementsSurface coating/ covering Substance Requirements Test method MinimumDocumentRequirementIsocyanate -containing liquid coatings TDI and HDImonomersMonomer levels of:•TDI (toluene diisocyanate, CAS no:26471-62-5)•HDI (hexamethylene diisocyanate,(CAS no: 822-06-0)In isocyanate-containing liquid coatings andhardeners (prepolymer solution) shall beless than 0.5 % by weight for the sum ofthese diisocyanates monomers in eachcoating component.In 1-component PU systems, the sum ofthese diisocyanates monomers shall be lessthan 0.25 % by weight in the ready-to-usemixture.LC-MS/MS SDOil Waste oil Not allowed to be used -- SD Heavy metal content in coatings and coveringsAll types of surface coatings/ coverings Cadmium (Cd)and itscompoundsNot allowed to be used.Contamination limit value:40 mg Cd/kg dry surface material.Total digestionfollowed byAAS or ICPSDAll types of surface coatings Lead (Pb) andits compoundsNot allowed to be used.Contamination limit value:90 mg Pb/kg dry surface material.Total digestionfollowed byAAS or ICP incompliancewith 16 CFRPart 1303(CPSC – CH-E1003) (USA)SD and TR1for solidfilms infurniturearticles inthe scope of16 CFR, Part1303 (USA),seeAppendix D2, 3SD for allothersurfacecoatings.All types of surface coverings Lead (Pb) andits compoundsNot allowed to be used.Contamination limit value:90 mg Pb/kg dry surface material.Total digestionfollowed byAAS or ICPSDNote: For the purpose of lead testing in accordance with 16 CFR, part 1303, surface coatings applied on coverings are considered as a surface coating, and lead requirements on surface coating as above applies, see Table 1.1. Lead (Pb) and its compounds.1 The TR may be replaced by tests of lead by the coating supplier in coating products that are identical in all material respects to those used in production of the furniture article, see Appendix D. Test reports from these tests of lead in coating products shall be handed over by the coating supplier to the IKEA supplier for registration in the IKEA Connect database, see section 5.2 This requirement is valid regardless of whether a furniture article, as defined in Appendix D, is delivered to the USA or not.3 The content of other heavy metals that are analysed in the same test (on dry surface coating from the final article) shall also be reported in the test report.Table 1.1 Surface coatings and coverings – general requirementsSurface coating/ covering Substance Requirements Test method MinimumDocumentRequirementAll types of surface coatings/ coverings Mercury (Hg)and itscompoundsNot allowed to be used.Contamination limit value:10 mg Hg/kg dry surface material.Total mercurycontent bymicro-wavedigestion andcold vapourAASSDAll types of surface coatings/ coverings Migration ofheavy metalsincluding theircompounds(Sb, As, Ba,Cd, Cr, Pb,Hg, Se)Surface coating films and covering systemson all products shall not exceed limits forheavy metal migration. For limits, see EN71-3:1994/A1:2000.EN 71-3:1994/A1:2000SDSolvent compositionLiquid coatings, pre-treatment, thinners, and solvents for cleaning/ degreasing AromatichydrocarbonsolventsThe content of total aromatic hydrocarbonsolvents shall be less than 1.0 % by weightin the liquid fraction of each surface coatingcomponent.Examples:•Toluene (CAS no: 108-88-3)•Xylene (CAS no (group): 1330-20-7)•Ethylbenzene(CAS no: 100-41-4)•Styrene (CAS no: 100-42-5)•Trimethylbenzenes and higher aromatichydrocarbonsFurthermore, benzene-containing solventsare not allowed to be used. Contaminationlimit value in the solvent: 0.10 % benzene(CAS no: 71-43-2) of each surface coatingcomponent.ISO 11890-2 SDLiquid coatings, pre-treatment, thinners, and solvents for cleaning/ degreasing ChlorinatedhydrocarbonsolventsUse of chlorinated hydrocarbon solvents isnot allowed.Contamination limit value: 0.10 % for thesum of all chlorinated hydrocarbons in theliquid fraction of each surface coatingcomponent.Examples:•Methylene chloride(CAS no: 75-09-2)•Chloroform (CAS no: 67-66-3)•Perchloroethylene(CAS no: 127-18-4)•Trichloroethylene(CAS no: 79-01-6)•1,1,1-trichloroethane(CAS no: 71-55-6)Headspacegas chromato-graphy withelectroncapturedetection(HSGC-ECD)SD1.1.1 Additional requirements specifically for powder coatings – all substratesNote : these requirements are in addition to the requirements in Table 1.1Table 1.1.1 Additional requirements specifically for powder coatings – all substrates Substance RequirementsTest method MinimumDocumentation requirementDi-organotin and tri-organotin compoundsTri-organotins are not allowed to be used. Contamination limit value: 1 mg/kg for sum of tri-organotin compounds in the dry surface material.Di-organotin compounds are allowed to be used, but the sum of di-organotin and tri-organotin compounds shall not be more than 2.5 mg/kg in the dry surface material. Note: All tri-organotin compounds arebanned, and all di-organotins are restricted to the sum limit of 2.5 mg/kg, but the minimum test demand only includes those tri- and di-organotins that are listed in the definition of organotin compounds.The limit values refer to the alkyl/aryl tin cation without the counter ion.Extraction and GC-MSSD and TRTGIC(Triglycidyl isocyanurate)Powder coatings shall not contain any addition of TGIC hardener (CAS no: 2451-62-9). This cross-linking agent is primarily used in polyester-based powder coatings.Contamination limit value 0.10 % by weight in the ready-to-use powder coating.-- SD1.1.2Additional requirements specifically for UV coatings – all substrates Note: these requirements are in addition to the requirements in Table 1.1Table 1.1.2 UV coatings including UV printing inks – general requirements all substratesSubstance Requirements Test method MinimumdocumentationrequirementStenomeric acrylates It is not allowed to use any stenomeric acrylate,including acrylic acid (CAS no: 79-10-7), that isclassified as:Tox. 1-4, STOT SE 1&2, STOT RE 1&2 or Asp.Tox. 1 according to Regulation (EC) No1272/2008 (the CLP regulation) according toeither of the following:•harmonised classification according to AnnexVI in the CLP regulation•the classifications made within the PARADconsortium (see PARAD consortium report onUV/EB acrylates)Contamination limit value: 1.0 % by weight inthe ready-to-use mixture for the sum of suchstenomeric acrylates.Extraction andGC-MSSDToxic coating ingredients Coating ingredients classified as Acute Tox. 1-3,STOT SE 1 or STOT RE 1 according to Regulation(EC) No 1272/2008 are not allowed.Note: Residual substances (technical impurities)classified as toxic are allowed to be found in thecoating ingredients as long as the coatingingredient itself is not classified as toxic.--SDToxic, harmful and corrosive preparations The ready-to-use UV-coating preparation shallnot be classified as Acute Tox. 1-4, STOT SE 1 &2, STOT RE 1 & 2, Asp Tox 1, Skin Corr 1A & 1B,CMR cat. 1A, 1B & 2 or Resp. Sens. cat. 1according to Regulation (EC) No 1272/2008.--SD1.2Additional requirements for surface coatings and coverings for solidwood, wood-based materials, and wood-like natural materialsTable 1.2 Surface coatings and coverings for solid wood, wood-based materials, and wood-like natural materialsSurface coating/ covering Substance Requirements Test method MinimumDocumentationrequirementAll types of surface coatings Formaldehyde Surface coating products shall notcontain formaldehyde, i.e.:•No formaldehyde shall be addedto the surface coating product.•No formaldehyde shall be createdduring storage and curing of thesurface coating.•The formaldehyde contaminationlevel shall be maximum0.5 mg/m2h measured accordingto EN 717-2 (Gas analysismethod) with the finished surfacecoating applied to a glass plate orother inert substrate.The samplingshall reflect arealistic worstcase in com-parison to whenthe productcould reach acustomer (i.e.normal handlingin factory,storage time,packaging andtransport to thenearest desti-nation).SDSurface coverings Formaldehyde Exception from general CMR ban:formaldehyde is allowed to be usedin the following case:•In the production of low-pressurelaminates (LPL), continuous-pressure laminates (CPL), andhigh-pressure laminates (HPL),which are impregnated withmelamine/formaldehyde or urea/formaldehyde resins.•In coatings applied on thecovering as part of itsmanufacture, before the coveringis applied to the substrate.Note: in any case of use offormaldehyde-containing resins,requirements regardingformaldehyde emission stated inother parts of the productdocumentation shall be fulfilled.-- Fordocumentationrequirements,see IOS-MAT-0003.Table 1.2 Surface coatings and coverings for solid wood, wood-based materials, and wood-like natural materialsSurface coating/ covering Substance Requirements Test method MinimumDocumentationrequirementLiquid coatings and thinners OrganicsolventsSurface coatings and thinners shallhave a maximum VOC content of130 g VOC/litre of the ready-to-useproduct.In special cases and after approvalby IKEA, surface coatings andthinners containing organic solventsexceeding 130 g VOC/litre may beused if the process is performedunder conditions with efficient VOCencapsulation and VOC exhaustreduction. The total VOC emissionshall be maximum 15 % of allsolvents used in connection with theapplication of solvent-bornecoatings, including for cleaning ofcoating equipment, as per the massbalance calculation.Note: This requirement does notapply to printing of names or codesfor articles, components or materialswhen that printing has no relevancefor the design of the article.ISO 11890-2ASTM D 2369, incases wherereactive diluentsare presentSDFor special caseswith VOC exhaustreduction, asolventmanagementplan (massbalance)according to EUDirective2010/75/EUAnnex VII part 7shall be carriedout every 12months andconnected inConnect to thearticle (throughappropriatematerial/process/componentcombination).Liquid un-saturated polyester coatings Styrene andvinyl toluenemonomersThe sum of styrene and vinyl toluenemonomers shall be less than 1.0 %by weight in the ready-to-usemixture.-- SDPeroxides Aromatic peroxide hardeners are notallowed to be used.-- SD1.2.1Additional requirements specifically for UV coatingsTable 1.2.1 UV coatings for solid wood, wood-based materials, and wood-like natural materials Substance Requirements Test method MinimumdocumentationrequirementResidual free monomers (stenomeric acrylates) Residual stenomeric acrylic monomers in thefinished cured coating film and the substrateshall be less than 800 mg/m2 extractable.Note: This requirement refers to the finalproduct after curing.In order to fulfil this requirement, key UV-process parameters such as UV-radiation level,UV-lamp distance, applied amount of coating,flow speed etc. shall be fully controlled anddocumented.IOS-TM-0002,section 17SD and TRResidual photo-initiators Roller coated surfaces•Residual concentration of photo-initiators inthe finished cured coating film and thesubstrate shall be less than 2000 mg/m2extractable.Other UV-coated surfaces•No limit (but still test requirement).IOS-TM-0002,section 17SD and TROdour Smell problems caused for example byincorrect curing, or by residues of photo-initiators, their breakdown products and theirimpurities, are not allowed.If any shipment of goods emits an unpleasantor unexpected smell, or deviates from earliershipments or from reference sample in termsof emissions/odour, in a way that is deemedby IKEA to involve a risk of discomfort orhealth effects for customers, this is to beconsidered a valid cause for claim of saidshipment. In case of dispute, evaluation ofodour to bemade by IKEAwith anevaluation groupof at least six persons--1.3Additional requirements for surface coatings and treatments formetal substratesTable 1.3 Surface coatings and treatments for metal substratesSurface coating/ covering Substance Requirements Test method MinimumdocumentationrequirementHot dip galvanizing Cadmium Zinc grades with cadmium content lowerthan 40 mg/kg shall be used.ICP SDChrome plating Hexavalentchrome(Cr-VI)Not allowed to use Cr-VI (chromates,bichromates, or chromic acid) in chromeplating.-- SDChromating, passivation and anodizing Hexavalentchrome(Cr-VI)Not allowed to use Cr-VI (chromates,bichromates, or chromic acid).If Cr-VI is found according to spot testand/or boiling under extractionprocedure (qualitative tests, seeIEC 62321), this indicates that Cr-VI hasbeen used, which is not allowed.IEC 62321 SDAnodizing – correction pens AromatichydrocarbonsolventsException: The 1 % limit for totalaromatic hydrocarbons in the liquidfraction (see Table 1.1) does not applyto correction pens used to touch upanodized surfaces, if used on less than0.2 % of the total anodized surface(yearly average).Note: this exception does not apply tobenzene.--Surface coatings Formaldehyde Exception from general CMR ban:formaldehyde-containing amino resinsare allowed to be used.Note: the formaldehyde-containingresin should be fully cured after thecoating process. Emission limit forformaldehyde from complete productaccording to IOS-MAT-0010 applies.-- SD。