电动阀门执行器出口英文使用说明书
电动阀门电动驱动器说明书
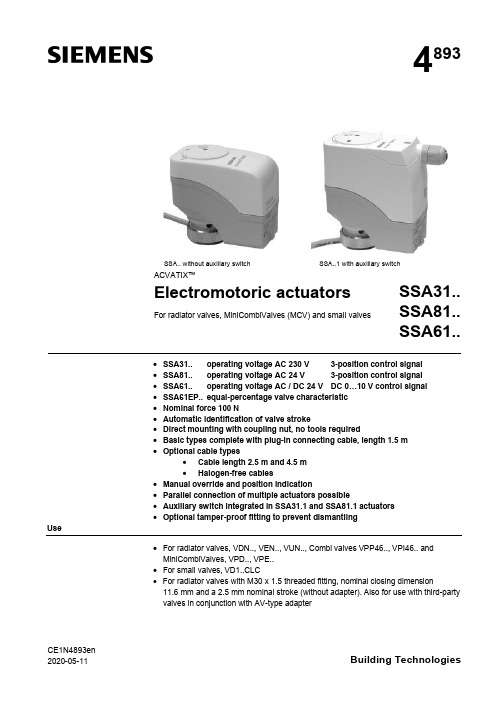
CE1N4893en 2020-05-11Building Technologies4893SSA.. without auxiliary switch SSA..1 with auxiliary switchACVATIX™Electromotoric actuatorsFor radiator valves, MiniCombiValves (MCV) and small valvesSSA31..SSA81..SSA61..·SSA31.. operating voltage AC 230 V 3-position control signal ·SSA81.. operating voltage AC 24 V 3-position control signal ·SSA61.. operating voltage AC / DC 24 V DC 0…10 V control signal ·SSA61EP.. equal-percentage valve characteristic ·Nominal force 100 N·Automatic identification of valve stroke·Direct mounting with coupling nut, no tools required·Basic types complete with plug-in connecting cable, length 1.5 m ·Optional cable types·Cable length 2.5 m and 4.5 m ·Halogen-free cables·Manual override and position indication·Parallel connection of multiple actuators possible·Auxiliary switch integrated in SSA31.1 and SSA81.1 actuators ·Optional tamper-proof fitting to prevent dismantlingUse·For radiator valves, VDN.., VEN.., VUN.., Combi valves VPP46.., VPI46.. and MiniCombiValves, VPD.., VPE..·For small valves, VD1..CLC· For radiator valves with M30 x 1.5 threaded fitting, nominal closing dimension11.6 mm and a 2.5 mm nominal stroke (without adapter). Also for use with third-party valves in conjunction with AV-type adapter2/10SiemensCE1N4893enSmart InfrastructureBuilding Technologies2020-05-11· For modulating or 3-position control in heating systems, chilled ceilings and terminal units.Type summaryTypereference Operating voltage Run time at 50 HzControl signalConnecting cableAuxiliary switchSSA31AC 230 V150 s3-position1.5 m SSA31/001)no cable SSA31.1 1.5 m YesSSA81AC 24 V1.5 m SSA81/001)no cable SSA81.1 1.5 m YesSSA61AC / DC 24 V 34 s DC 0...10 V1.5 m SSA61/001)no cable SSA61EP 2) 1.5 m SSA61EP/002)no cable1)For available cable lengths or terminal block connectors refer to "Accessories", page 42)With equal-percentage valve characteristicTypereference DescriptionOperating voltage Control signalASY3L25Connecting cable 2.5 mAC 230 V3-positionASY3L45Connecting cable 4.5 m ASY8L25Connecting cable 2.5 m AC 24 V ASY8L45Connecting cable 4.5 mASY8L45HF Connecting cable 4.5 m, halogen-free, VDE 0207-24ASY6L25Connecting cable 2.5 m AC / DC 24 V DC 0...10 V ASY6L45Connecting cable 4.5 m ASY6L45HF Connecting cable 4.5 m, halogen-free, VDE 0207-24ASY98Retaining screw for terminal block connectors. Included in ASY99 and ASY100.ASY99Terminal block connector for 3-position actuators SSA81../00ASY100Terminal block connector for DC 0…10 V modulating actuators SSA61/00AL40Tamper-proof fitting to prevent dismantling of actuators Adapter typefor third-party valves Adapter type for third-party valves AV51Beulco old (M30x1.0)AV56Giacomini AV522)Comap AV57Herz AV53Danfoss RA-N (RA2000)AV58Oventrop old (M30x1.0), till 2002AV54Danfoss RAVL AV592)Vaillant AV55Danfoss RAV AV60TA, till 20021)AV61Markaryd (MMA)1) No adapter required for type TBV-C 2)While stocks lastOrdering Type Stock no.DescriptionQuantity SSA81/00SSA81/00Electromotoric actuator 2ASY8L45ASY8L45Connecting cable2Actuators, valves and accessories are packed separately. Items are suppliedindividually packed.Overview tables, see page 9.AccessoriesExample:DeliveryRev.-No.3/10SiemensCE1N4893en Smart Infrastructure2020-05-11Equipment combinationsk vs = nominal flow rate of cold water (5...30 °C) through the fully open valve (H 100)at a differential pressure of 100 kPa (1 bar)V & = Nominal volume flow at 0.5 mm strokeTo ensure trouble-free operation of third-party valves with the SSA.. actuator, the valves must satisfy the following requirements:·Threaded connections with coupling nut M30 x 1.5·Nominal force F £ 100 N ·Dimension x x > 9.0 mm ·Dimension y y £ 14.5 mmFunction / mechanical designWhen the actuator is driven by DC 0…10 V control voltage or by a 3-position signal, it produces a stroke which is transmitted to the valve stem.The description of operation in this document applies to the valve versions which are fully open when de-energized (NO).·Voltage at Y1:Stem retracts Valve opens ·Voltage at Y2:Stem extends Valve closes ·No voltage at Y1 and Y2:Actuator maintains its current position· The valve opens / closes in proportion to the control signal at Y.· At DC 0 V, the valve is fully closed (A à AB).· When power supply is removed, the actuator maintains its current position.1)Actuator is calibrated to 2.5 mm stroke of VPI46.15.L06S t r o k e 2,5 m m ((c a l i b r a t e d )1)22.51.510.500246810control signal Y [V]Type reference Valve type k vs [m 3/h]V&[l/h]PN class Data sheet VDN.., VEN.., VUN..Radiator valves 0.09…1.41PN 10N2105, N2106VPD.., VPE..MCV radiator valves 25…483N2185VD1..CLC Small valves 0.25…2.60N2103VPP46.., bi valves 30…4001PN 25N4855For other radiator valves with type AV.. adapters refer to "Type summary / accessories"Radiator valves (M30 x 1.5) from other manufacturers, without adapter:· Heimeier · Crane D981..· TA-Type TBV-C · Oventrop M30 x 1.5 (from 2001)· MNG · Junkers · Honeywell-Braukmann · Cazzaniga · Beulco (new)Valves from othermanufacturers3-position control signalSSA31.. / SSA81..DC 0...10 V control signalSSA61, SSA61/004/10SiemensCE1N4893enSmart InfrastructureBuilding Technologies2020-05-11Combi valves VPI46../VPP46.. in combination with SSA61EP.. have an equal-percentage characteristics.· The valve opens / closes in equal percentage ratio to the control signal at Y.· At DC 0 V, the valve is fully closed (A à AB).· When power supply is removed, the actuator maintains its current position.1)Actuator is calibrated to 2.5 mm stroke of VPI46.15L06S t r o k e 2,5 m m (c a l i b r a t e d )1)2.42.51.510.500246810control signal Y [V]·Plastic housing·Locking-proof, maintenance-free gear train·Manual override with hexagonal socket wrench 3 mm ·Reduced power consumption in the holding positions·Load-dependent switch-off in the event of overload and in stroke end positions·Parallel operation of 6 SSA31.., 24 SSA81.. and 10 SSA61..possible, provided the controllers’ output is sufficient ·Terminal block connectors for customer made cables available (only for use with AC 24 V and AC / DC 24 V actuators)·Connecting cables with AC 24 V and AC 230 V connectors cannot be mixed up·Halogen-free cables availableAccessoriesAdapter types AV51 to AV61 are available for mounting the SSA.. actuators on third-party radiator valves as shown under "Type summary/accessories", page 2.1xtighten gentlyType ASY98 to secure the cable connector. Included in ASY99 and ASY100.The cable connector snaps into position,but can be additionally secured with the retaining screw.DC 0...10 V control signal SSA61EP,SSA61EP/00Features and advantagesAdapter type AV.. for third-party valves Tamper-proof fitting AL40Retaining screw ASY985/10SiemensCE1N4893en Smart Infrastructure2020-05-11For special cable lengths of the AC / DC 24 V actuators.·Type ASY99 for 3-position actuators SSA81../00·Type ASY100 for DC 0…10 V modulating actuators SSA61/00The terminal block connectors are supplied complete with mounting instructions (74 319 0385 0).Notes The actuators must be electrically connected in accordance with local regulations (refer to "Connection diagrams", page 9).Regulations and requirements to ensure the safety of people and property must be observed at all times!The permissible temperatures (refer to "Technical data", page 7) must be observed.The connecting cable of the actuator may come into contact with the hot valve body,provided the temperature of the valve body does not exceed 80 °C.Actuator types SSA 31.1 and SSA81.1 have a built-in auxiliary switch. The switch cannot be fitted in other actuators later.Mounting instructions (Ref. 74 319 0497 0) are enclosed in the product packaging.The actuator and valve are assembled with the coupling nut; no tools or adjustments are required.The actuator must be fitted in position 1 with the power disconnected (refer also to "Manual override", page 6):·Position the actuator and tighten the coupling nut manually ·Do not use any tools such as wrenches·Avoid lateral pressure or (cable) tension on the mounted actuator!In the case of actuators without a connecting cable (SSA../00), the separately orderedCrimp ferrule on stripped wire of connecting cable.When commissioning, check the wiring and the functioning of the actuator and auxiliary switch, if fitted.·Actuator stem extends (from position 1 to 0): Valve closes ·Actuator stem retracts (from position 0 to 1): Valve opens During commissioning and whenever the operating voltage is switched on,the SSA61.. runs a self-calibration routine. (Valve stroke 0® Max.stroke ® Setpoint).Never intervene manually in this process.ON0 %EngineeringMountingOrientationInstallationCommissioningTerminal block connectors ASY99ASY1006/10SiemensCE1N4893enSmart InfrastructureBuilding Technologies2020-05-11The second or third attempt at calibration occurs automatically after an 8-minute delay.After three failed calibration attempts the actuator stem remains in the extended position and the radiator valves are closed.For valves with strokes < 1.5 mm, the actuator/valve combination locks after three failed calibration attempts.The new Siemens type VDN.., VEN.. and VUN.. radiator valves have in all 1.5 mm stroke.A 3 mm hexagonal socket wrench can be used to move the actuator to any position.However, if a control signal from the controller is present, then this takes priority in determining the position.To retain the manually set position, unplug the connecting cable or switch off the operating voltage and the control signal.2.5 mm stroke5.5 mm strokeThe actuators are maintenance-free.When carrying out service work on the plant, following must be noted:·Turn power off (e.g. remove the plug)·If necessary, disconnect electrical connections from the terminals·The actuator must be commissioned only with a correctly mounted valve in place!SSA.. actuators cannot be repaired; the complete unit must be replaced.DisposalWarrantyThe technical data given for these applications is valid only when the actuators are used with the Siemens valves listed under "Equipment combinations", page 2.The use of the SSA.. actuators in conjunction with third-party valves invalidates any warranty offered by Siemens Building Technologies / HVAC Products.Note: Correctcalibration is only possible ·with valve·stroke > 1.5 mmOperationNoteManual overrideMaintenance!Repair7/10SiemensCE1N4893en Smart Infrastructure2020-05-11Technical dataPower supplyControlFunctional dataElectrical connectionsNorms and directivesDimensions /weight Housing colors 1)Provided the controller output is sufficient2)The documents can be downloaded from /bt/download8/10SiemensCE1N4893enSmart InfrastructureBuilding Technologies2020-05-11General ambient conditionsOperation EN 60721-3-3Transport EN 60721-3-2Storage EN 60721-3-1Environmental conditions Class 3K3Class 2K3Class 1K3Temperature +1...+50 °C –25...+70 °C –5...+50 °C Humidity 5...85 % r.h.< 95 % r.h. 5...95 % r.h.Connecting cableConnection terminalsY2Y1G4864Z 15Control signal CLOSE Control signal OPENSystem potential AC 24 VG0Y G4864Z 16System neutralControl signal DC 0...10 V System potential AC/DC 24 VFactory setting: 50 %0...50 % Q11® Q1250...100 % Q11® Q14The switching point can be adjusted by turning the switching cam with a screwdriver (see Mounting Instructions).Recommended connecting cable: H03VV-F, 2x0.5…0.75 mm 2.ASY3L.. with SSA31..ASY8L.. with SSA81..ASY6L.. with SSA61..ASY99for SSA81..ASY100for SSA61..Terminals for auxiliary switchesSSA31.1, SSA81.19/10SiemensCE1N4893en Smart Infrastructure2020-05-11Connection diagramsN Controller Y ActuatorL System potential AC 230 V NSystem neutralY1, Y2Control signal OPEN, CLOSE Q1, Q2Controller contactsN Controller YActuatorSP, G System potential AC 24 V SN, G0System neutralY1, Y2Control signal OPEN, CLOSE Q1, Q2 Controller contactsN Controller YActuatorSP, G System potential AC 24 V SN, G0System neutral Y Control signalSSA31..SSA81..SSA61..10/10SiemensCE1N4893enSmart InfrastructureBuilding Technologies2020-05-11DimensionsDimensions in mm8377484893M 0172.59M30 x 1,54893M 0298.5834889.5M30 x 1,59Revision numbersType reference Valid from Rev.-No.Type reference Valid from Rev.-No.SSA31K SSA61K SSA31/00K SSA61/00KSSA31.1K SSA81K SSA81/00K SSA81.1KActuator without auxiliary switch SSA31..SSA81..SSA61..Actuator with auxiliary switch SSA31.1..SSA81.1..Issued bySiemens Switzerland LtdBuilding Technologies Division International Headquarters Theilerstrasse 1a 6301 Zug SwitzerlandTel. +41 41-724 24 24/buildingtechnologies © Siemens Switzerland Ltd, 2005Technical specifications and availability subject to change without notice.。
KFD阀门控制箱中英文说明书

额定电流(安培)调节型适用电装型号Ⅲ配型、型Ⅳ配型结构形式:、抽屉式、小型R ated current (am pere)T A djusting typeZ W Q W JQ A pplicable type of electric fitting: for ZW type and Q W type.C X G Structure from : C draw er type, X sm all C ontrol cabinet of electric valve cabinetⅢⅣ抽屉式、挂壁式、、、阀门电动装置控制箱for JQ type draw er type, G wall type K F D —— 普 通 型 KFD 系 列 Common type KFD series一、概 述 Brief introduction该系列电动阀门控制箱,是与我厂生产的ZW 型、JQ 型及QW 型阀门电动装置配套使用的电控箱,用于控制阀门的开启和关闭,可用于现场单独控制或远方集中控制。
KFD 型电控箱有抽屉式和挂壁式两种结构。
This series of control cabinet of electric valve is the one to be used together with ZW type, JQ type and QW type electric valve actuator produced by our company and to control the opening and closing of valve. It can be used in site individual control or long-distance centralized control.KFD type electric control cabinet has two kinds of structure: drawer type and wall type. Designation型号表示方法 Designation二、技术数据 T echnical data1、电源:380V 50Hz 三相四线制(特殊要求,另见)2、工作环境:(1)环境温度:—20℃~+60℃ (2)相对湿度:≤85%(20℃时)(3)周围不含强腐蚀性、易燃易爆介质及导电尘埃。
电动蝶阀使用说明书中英文

电动蝶阀使用说明书中英文电动蝶阀Electric Butterfly Valve使用说明书Operation Manual一、用途Ⅰ.Application本系列蝶阀适用于冶金、矿山、建材、石化、造纸、纺织等行业的工业管道中。
它对气体半流体等管道中的介质按不同的信号,改变其流量的大小,从而达到自动调整风量,实现自动控制。
体阀采用优质钢板焊接结构,具有传动轻巧灵活,密封性能好,开闭时间短,切断速度快,能可靠的杜绝事故的发生。
This series butterfly valve is suitable to use in the industry pipe of metallurgical, ore building material. Paper textile and so on, Accord to the different signal in the pipes of the gas half fluid medium. Change the flow volume, and adjust the fan volume automatically. It can realize automatic control. The valve is used good welding structure. It is characterized by light, nimble good sealing, short open time, fast speed broken and dependable.二、结构及工作原理Ⅱ.The structure and Working principle1、电动蝶阀由电动执行机构和蝶阀组成,有关电动执行机构作用原理,使用维护等参阅电动执行机构说明书。
1、The electric butterfly valve is composed of electric execute structure and butter fly valve. The relative electric execute. Working principle and main is refer to the operation manual of electric executor.2、电动蝶阀按作业方式可分为电开式和电关式两种。
AUMA说明书中英文对照文稿

AUMA说明书中英文对照文稿操作说明手册的封面内容翻译(中英文对照):Multi-turn actuators万向驱动装置SA07.1-SA48.1 (产品型号)SAR 07.1-SAR 30.1 (产品型号)AUMA NORM (AUMA是这个阀门生产厂的品牌名称)AUMA标准Operation instructions (操作手册)目录内容:Scope of these instructions:本手册内容介绍的范围包括:These instructions are valid for multi-turn actuators for Open-close duty, SA 07.1-SA 48.1 ,and multi-turn actuators for modulating duty, SA07.1-SA 30.1.本手册的说明适应型号为SA 07.1-SA 48.1、具有开启-关闭功能系列的万向驱动装置和型号为SA07.1-SA 30.1、具有调节功能系列的万向驱动装置有效。
These operations instructions are only valid for “clockwise closing”, i.e. driven shaft turns clockwise to close the valve.这些操作说明只对"顺时针关闭"有效,即:驱动轴顺时针转动关闭阀门。
.Safety instructions (安全说明 )1.1 Range of application (应用的范围) AUMQ multi-turn actuators are designed for the operation of industrial valves, e.g, globe valves, butterfly valves and ball valves. For other applications, please consult us. AUMA is not liable for any applications. Such risk lies entirely with the user. AUMQ万向驱动装置是为工业用阀所设计的,例如:工业生产常用球瓣阀,蝶阀和球阀。
多turn电动阀门控制器用户操作手册说明书

HT ANTI-CONDENSATION HEATER
IP3 VALVE MIDDLE TRAVEL POSITION SWITCH(No 3)
3 22
45Leabharlann 10232 14 36 07 13 35
BLK BLINKER SWITCH POT POTENTIOMETER (VALVE POSITION SIGNAL) CPT CURRENT POSITION TRANSMITTER
MADE BY 10/03/2020 JB WD CK-CKR STD., MSM-CCW, 3PH,
CHECKED 10/03/2020 JP
NOCPT, HT115, LIM, TOR, IMP
APPROVED 10/03/2020 JP
range
FORMAT
DRAWING Nº
A4 N00300AX - 2
BLK 24-25
BLK 24-25
BE CONNECTED THROUGH BOTH CIRCUITS. STANDARD 250AVC/5A, 24VDC 0,25A. GOLD CONTACT SWITCHE (LOW ENERG. CIRCUITS) UNDER REQUEST
5
6
7
8
CK-WD
1
2
3
4
5
6
7
E D C
S1 POWER
U V W N PE
F1 F2 F3
KM2
L1 L2 L3
III ELECTRIC ACTUATOR M1
(centork supply)
V (250 VAC max allowable voltage) 0
Rain Bird 6100 Series 电子阀门控制器说明书
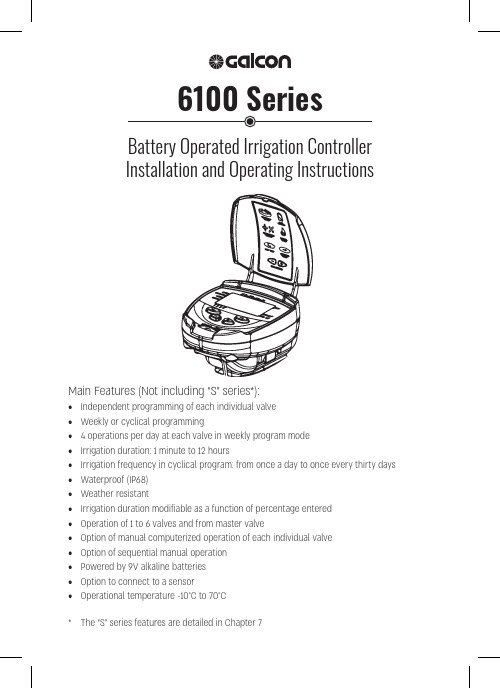
appropriate batteries to the controller.shown, tap scan for timers.Please Note!The pairing code will appear on the irrigationcontroller screen for about 10 seconds only * Enable location on your smartphone232. Manual-Mechanical OperationThe irrigation valve can be opened regardless of the controller’s operation. This mode is useful when immediate irrigation is required, and the controller is not assembled yet. The operating lever is below the solenoid.The lever has 3 positions:AUTO – Mid positionCLOSE - Rotating clockwiseOPEN - Rotating counter clockwiseNOTE: In normal working conditions,the lever should be in the middle, inAUTO position.4so, otherwise the battery cover pins might break!CLOSE3.2Place the base of the controller (1) on the solenoid (2). Position theThe controller makes a soft click sound when properly connected to the base.312the controller, according to the valve numberLabeled cables (1) emerge from the controller. The end of each cable is protected by a cover that must be removed prior to connecting the cable.NOTE: The controller and its cables are waterproof. In order topreserve the waterproof characteristics it is important not to expose the wires that are not being used.To preserve watertightness the following instructions need to be followed:• Connect the cables to the valves (3) using the special waterproof connectors (2) supplied with the product. See illustration.Cut the cover of the cable coming out of the controller (1) near the end of the cable and expose the cable leads from the outer black insulating sleeve only. The solenoid cables have three wires: white, red and black. Do not expose the three wires from their colored insulationConnect the wires to the waterproof connector (2).SET PLUS MINUS ENTERPress “Enter”several times until the“Clock” appears.. The hour digits blink.Press “Plus” and “Minus” buttonssimultaneously. The clock reading time display format at any step in the programming process.several times until the“Clock” appears.will cause theminute digit to flash. Set the desired duration of.. A blinking arrow appears at the top of the display. Place the arrow in front of the current day of the week using the “Plus” or “Minus” buttons.If the most recent data item stops blinking before you finish programming it, press “Set” to continue the programming process.Switching Between AM/PM and 24 Hour Time FormatPress Enter until. A blinking arrow will appearat the bottom of the display.and .Press Enter to proceed to the nextuntil “Duration”Press “Set”or “Minus” buttons. Press “Set” again - the minute digits blink. Set the desired number of minutes by pressing “Plus”buttons.Press “Enter” to proceed to the next step.until “Days” appears.Press “Set” . A blinking arrow appears at the top of the display, under Selecting/adding irrigation days: Press “Plus”you want to cancel. Click Setonce or twice. Clickstart time that was entered will appear on the display.. The displayed item (or the last start time entered) will Set the desired start time( note the AM and PM terms) bypressing “Plus” or “Minus”actions 2-3 for programing II-III-IV ifrequired.To cancel a specific start time, select it bypressing “Enter”. The hour digits will blink. Press “Plus” or “Minus” until the word To program another valve, select it and repeat the above steps, starting Example: Programming a Weekly Irrigation ProgramSuppose you want to program the irrigation controller so that it irrigates threetimes a day. In the 24-hour format: 08:00, 13:00 and 19:00, for two and a half To switch to 24-hour format, see Section 4.3 (If you are using the DC-1 irrigationPress Enter until. A flashing arrow will appear at the bottom of the display.or to move the arrow to the valve number you want to Press ENTER until the icon. The hour digit will flash. Press or until the number 2 will be displayed.. The minute digit will flash. Press ornumber 30 will appear in units of minutes.Press Enter . The days icon. A flashing arrow will appear at the top of the display, below Monday. Press Set until the flashing arrow appears below Tuesday, and then click on the plus symbol . The arrow below Tuesday will stop flashing and move to the right, to Wednesday. Press twice to move the arrow to Friday, and then click Plus . Press Enter ; the start time STARTI will be displayed. Click Set. The hours digit will flash.or minus sign. Repeat this step to set the second start time (2) STARTII to 13:00, Press Enter for the fourth start time (4) START IV will be displayed.and the hours digit will flash.Press the plus or minus sign until OFF is displayed. The fourth valve opening is now canceled.once, for the duration and the time set.Note: The duration is determined according to Section 4.41. Press ENTER until appears.2. Press Set several times (for all days ofthe week) until the icon appears andthe word ONCE blinks in the display.In this operation we program the controller to operate the irrigation system once for a fixed number of days, for the time allotted to irrigation.Note: The duration of the valve opening is determined according to Section 4.4.1. Press Enter until the iconappears.repeatedly (for all days ofthe week) until the periodic symbolappears, and the word Once will flash onor. The display will show the number ofdays between irrigations (irrigation cycle). For example, if you set 2 days, irrigation will take place every two days for the determined time.until STARTI appears.opening time.. The time display will flash.Set the desired opening time using). Pay attention to the AM and PM terms.Press Set until the number to the rightof the start hour flashes (the number abovethe word “days”).Set the number of days until the opening of the valve with or .Note: Opening of 2, 3 and 4 are canceled in this program.5.4 Example of Defining a Periodic Irrigation Program Suppose you want to program the irrigation controller to open the valve at Determine the duration of irrigation in accordance with Section 4.4: defining the duration of the irrigation. Press Enter until the iconand set the duration of the irrigation by pressing or .irrigation duration. Note that the originally defined programcontinues to run according to thedetermined times.For setting-up times:1. Press Enter until the valve iconSection 5.3 Valve Selection Press Enteruntil the ‘Manualuntilappears, and press in the display. The Press Enter until the days icon several times (for all days of the week) until the word Once flashes on the display.While the display is blinking, press or the display, which is the frequency of the irrigation.Press Enter . The display will show .STARTI.. The hours display will flash.Set the start times and minutes, by pressing or Section 4.6.5.6It is possible to operate all the valves sequentially, one after the other.until the clock iconfor 5 seconds. Valve No. 1 will open and operate for the duration of thecloses the current valveThe shutdown operation prevents irrigation in all valves.until the clock icon(more than 5 seconds.)(no irrigation) will bedisplayed flashing in front of the captionTo return control to the controller, pressuntil the clock icon appears,continuously until the icon disappears. Downtime may be carried out while the valve is turned on.In downtime mode, if you accidentally try to turn on a valve manually or if it reached its time to open, the word ‘rain’ will appear and the valve willAddition and Reduction in PercentagesIt is possible to add or reduce the duration of irrigation in all tapsPress Enterand together. The display will, 00 will flash. By means ofwill add or subtract the percentageas required (in steps of 10%). If you added oror -% on the main screen.Note: It is not possible to change a percentage to a single valve. 6. Additional ViewsThis section is not intended for DC-1 and DC-2 models. When two valves are On and a third valve is scheduled to open, this valve will switch to Waiting.When the batteries are low, a blinking battery icon will appear on the controller.6.3When the batteries are low and are not replaced in time, the battery icon possible and reprogram the controller.6.4valve.Note: To resume the valve operation, set the duration asThe controller can be stopped by connecting it to a sensor. ForAll types of dry-contact N.C.sensors can be used. The sensor connection is performed as described in Section 3.4 – Wiring the controller to a two-wireAs long as the sensor does not close the circuit (that is, a defined prevention condition has been identified), the icon appears on the display. In this setting, valves will not be irrigating. S OFF will appear in the display in manual mode. This means that the sensor is activated, and is currentlyirrigation program will be carried out (see Section 6.2).until the “Open Window”appears. The screen will showthe word OFF or the last entered window opening time.. The word OFF will flash onthe display.Set the desired window opening time using either or (note the AM and PM terms).until the “Close Window” icon appears. The screen will display 12:00 AM or the lastoruntil the iconappears next to “Open Window”. The opening time will flashor until OFF appears nextto the window icon.Select the valve you want to associate to the sensor., until the icon appears next to the sensor you wantto turn on the sensor in the valve irrigation program. The word appears onthe display. In this situation, the valve associated or , program any time after the current time, for example 09:30 AM. This time will be the first opening of the current day. Starting10. In any case, Galcon’s liability in connection with the products and/or according to this Warranty Certificate, including (but without detracting from the aforesaid) in connection with and/or as a result of the product (or part thereof) and/or use of the product, will be limited (cumulative and in relation to all damages, claims and/ or causes of action) for the consideration that Galcon actually received from the customer in respect of the product(s). The above limitation on Galcon’s liability will apply whether Galcon’s liability is based on contractual and/or tort cause and/or absolute liability and/or any other cause of any kind.11. Galcon’s warranty under this Warranty Certificate and the remedies set forth above in relation to Galcon’s warranty, constitute the sole and exclusive terms and conditions in relation to Galcon’s warranty, any instruction, other document and/or obligation, and including any other warranty, shall not be valid; remedies and other conditions, whether given verbally or in writing, and/or given explicitly or implicitly for a specific purpose and/or liability against hidden defects. Galcon will not be liable under any statutory liability (express or implied), including and without detracting from the generality of the aforesaid, liability regarding marketability and/or suitability for a specific purpose and/or liability against hidden defects.12. The customer is solely responsible for the choice of the product, and for the manner in which the product(s) are used and adapted to his needs.13. The provisions of this warranty certificate shall apply, and shall be construed, in accordance with the laws of the State of Israel only, and no other law shall apply. Any dispute regarding the use of the product and/or this Warranty Certificate, its execution or infringement, will be heard only before the competent courts in the city of Tel Aviv, and no other court will have jurisdiction to hear it.NOTE: This equipment has been tested and found to comply with the limits for a Class B digital device, pursuant to part 15 of the FCC Rules. These limits are designed to provide reasonable protection against harmful interference in a residential installation. This equipment generates uses and can radiate radio frequency energy and, if not installed and used in accordance with the instructions, may cause harmful interference to radio communications. However, there is no guarantee that interference will not occur in a particular installation. If this equipment does cause harmful interference to radio or television reception, which can be determined by turning the equipment off and on, the user is encouraged to try to correct the interference by one or more of the following measures:• Reorient or relocate the receiving antenna.• Increase the separation between the equipment and receiver.• Connect the equipment into an outlet on a circuit different from that to which the receiver is connected.• Consult the dealer or an experienced radio/TV technician for help. Changes or modifications to this equipment not expressly approved by the party responsible for compliance (Galcon Bakarim Agricultural Cooperative Society, Ltd.) could void the user’s authority to operate the equipment.Mechanical Eng. Ben EmerguiPhone +972-52-3753938。
Parker Autoclave Engineers FRC电动阀门操纵机说明说明书

Principle of Operation:The need to remotely control process flow electrically using high pressure multi-turn needle valves has long been sought.Pneumatic control of this type is an engineering challenge and cost prohibitive. Parker Autoclave Engineers solves these issues with our FRC line of electric actuators. When mated to our Regulating Stem Needle Valves and sent a 4-20mA signal, this actuated valve system provides precise control when needed and even provides enough torque to close the valve when not needed. This valve/actuator combination is capable of controlling Liquid or Gas flows.The FRC Electric Actuator uses a 4-20mA input signal to turn the valve a programed amount of turns from fully closed to fully open (typically 5 turns) while also providing a position feedback using an independent 4-20mA signal. It is also capable ofclosing the valve completely when a 4mA signal is received. Should power be lost, the valve will freeze and “remember” it’s last position and will not need to be re-zeroed. The FRC actuator is designed to work with a number of Parker Autoclave Engineers Needle Valves from 1/8" to 3/4" tube sizes and up to 60,000 psi (4140 bar) using the Regulating Stem option - see individual valve brochures for Cv and Flow Curves.Features:• Designed for Multi-turn Needle Valves, tubing/pipe sizes 1/8" to 3/4"• Precise, accurate control using Regulating Stem option.• Operational Temperature Range: -40° to 160°F (-40° to 70°C) - Valve temperature not to exceed 600°F • Closing Torque capable of up to 60,000 psi (4140 bar) operation• Weatherproof or Explosionproof (CSA approved Cls 1, Div 1 Grps B, C & D)• Maximum Rotation Speed: FRC1 = 4 sec/turn, FRC2 = 15 sec/turn (5 turn open/close)• Weatherproof Enclosure is supplied with TURCK 5 position cable connector and 20’ of cableNeedle Valve ActuatorsModel FRC - Electric, 24 VDCFlow Regulating Control/Shutoff10V2, SW, SM, VM SeriesNeedle Valves to 60,000 psi (4140 bar)2Needle Valve Actuator: Model FRC - Electric Flow Regulating Control/Shutoff 02-9336BE 0523Specifications and Ordering Guide:Electric ActuatorElectrical Specifications:• Electrical Input: 24VDC only, 72 Watt maximum • Control Input: 4-20mA• Position Feedback: Independent 4-20mA • Position Detection: Hall Sensors • Motor: BLDC brushless DC motorMechanical Specifications:• Standard Enclosure - EPD Coated NEMA 4/IP65 Equivalent • Optional Anodized Aluminum Explosion-Proof Enclosure, Nema 8/IP67, CSA Approved for Class 1, Division 1, Groups B, C, D / T6 Areas (*Group B is suitable for Hydrogen)• 500+ Positions per turn (+/- 0.25° Position Accuracy), 3243 Actuator Positions over Full Span• Maximum Rotation Speed: #1 Actuator = 4 sec/turn (5 turn open/close), #2 Actuator (high torque) = 15 sec/turn (5 turn open/close)• Actuator Operating Temperature -40°(-40°C) to160°F(70°C), Valve Temperature not to exceed 600°F • Actuator life Expectancy: 250,000 cycles • Gears and Bearings are Lifetime Lubricated• 20 ft. cable included with 6 pin/5 wire connector (FRC1 and FRC2 Weatherproof version only)• Wiring Terminal, Maximum Wire Size: 18 Gauge (To Terminate larger gauge wire, see Option Code XPFL below)Position on Powerloss:• Remembers Last Position•Reseats Valve if Current is Between 3.0 and 4.16mAOrdering Guide:(reference individual Valve Series brochure for exact valve detail)20SM9882-FRC2XTG = 20SM Series Needle Valve, 20,000 psi MAWP , 9/16” MP Cone and Thread, 2-way Angle/Replaceable Seat Valve, Flow Regulating On/Off Explosion Proof Actuator/High Torque, PTFE Glass packing to 600°F max.Note: Actuators can be rotated to any one of four compass locations. (requires zeroing function (re-seating).Dimensional Information:3 Needle Valve Actuator: Model FRC - Electric Flow Regulating Control/Shutoff 02-9336BE 0523Dimensional Information:4Needle Valve Actuator: Model FRC - Electric Flow Regulating Control/Shutoff 02-9336BE 0523Dimensional Information:5 Needle Valve Actuator: Model FRC - Electric Flow Regulating Control/Shutoff 02-9336BE 0523Dimensional Information:1/2" NPT (Nipple)6Needle Valve Actuator: Model FRC - Electric Flow Regulating Control/Shutoff 02-9336BE 0523Parker’s Motion & Control TechnologiesAt Parker, we’re guided by a relentless drive to help our customers become more productive and achieve higher levels of profitability by engineeringthe best systems for their requirements. It means looking at customer applications from many angles to find new ways to create value. Whateverthe motion and control technology need, Parker has the experience, breadth of product and global reach to consistently deliver. No company knows more about motion and control technology than Parker. For further information call 1-800-C-Parker.7Needle Valve Actuator: Model FRC - Electric Flow Regulating Control/Shutoff 02-9336BE 0523! CAUTION !Do not mix or interchange component parts or tubing with those of other manufacturers. Doing so is unsafe and will void warranty.Parker Autoclave Engineers Valves, Fittings, and Tools are not designed to interface with common commercial instrument tubing and are designed to only connect with tubing manufactured toParker Autoclave Engineers AES specifications. Failure to do so is unsafe and will void warranty.Offer of SaleThe items described in this document are available for sale by Parker Hannifin Corporation, its subsidiaries or its authorized distributors. Any sale contract entered by Parker will begoverned by the provisions stated in Parker's standard terms and conditions of sale (copy available upon request).©2023 Parker Hannifin Corporation | Autoclave Engineers is a registered trademark of the Parker Hannifin Corporation Literature #: 02-9336BE May 2023ISO-9001 CertifiedInstrumentation Products Division Autoclave Engineers Operation 8325 Hessinger Drive Erie, PA 16509-4679Tel: 814 860 5700Fax: 814 860 5811/ipdInstrumentation Products Division Division Headquarters 1005 A Cleaner WayHuntsville, AL 35805 USA Tel: 256 881 2040Fax: 256 881 5072WARNINGFAILURE, IMPROPER SELECTION OR IMPROPER USE OF THE PRODUCTS AND/OR SYSTEMS DESCRIBED HEREIN OR RELATED ITEMS CAN CAUSE DEATH,PERSONAL INJURY AND PROPERTY DAMAGE.This document and other information from Parker Hannifin Corporation, its subsidiaries and authorized distributors provide product and/or system options for further investigation by users having technical expertise. It is important that you analyze all aspects of your application and review the information concerning the product or system in the current product catalog. Due to the variety of operating conditions and applications for these products or systems, the user, through its own analysis and testing, is solely responsible for making the final selection of the products and systems and assuring that all performance, safety and warning requirements of the application are met. The prod-ucts described herein, including without limitation, product features, specifications, designs, availability and pricing, are subject to change by Parker Hannifin Corporation and its subsidiaries at any time without notice.Needle Valve Actuator: Model FRC - Electric Flow Regulating Control/Shutoff 02-9336BE 0523Parker WorldwideNorth AmericaUSA – Corporate, Cleveland, OH Tel: +1 256 896 3000USA – IPD, Huntsville, AL Tel: +1 256 881 2040*****************USA – IPD, (Autoclave), Erie, PA Tel: +1 814 860 5700*******************CA – Canada, Grimsby, Ontario Tel +1 905-945-2274*********************South AmericaAR – Argentina, Buenos Aires Tel: +54 3327 44 4129 ******************BR – Brazil, Diadema, SP Diadema, SPTel: +55 11 4360 6700******************CL – Chile, Santiago Tel: +56 (0) 2 2303 9640******************MX – Mexico, Toluca Tel: +52 722 275 4200*******************Asia PacificAU – Australia, Dandenong Tel: +61 (0)2 9842 5150******************************CN – China, Shanghai Tel: +86 21 2899 5000*****************************HK – Hong Kong Tel: +852 2428 8008IN – India, MumbaiTel: +91 22 6513 7081-85ID – Indonesia, Tangerang Tel: +62 2977 7900********************JP – Japan, Tokyo Tel: +(81) 3 6365 4020******************KR – South Korea, Seoul Tel: +82 2 559 0400*******************MY – Malaysia, Selangor Tel: +603 784 90 800*******************SG – Singapore,Tel: +65 6887 6300*******************TH – Thailand, Bangkok Tel: +66 2 186 7000*********************TW – Taiwan, Taipei Tel: +886 2 2298 8987*************************VN – Vietnam, Hochi Minh City Tel: +848 382 508 56**********************Europe, Middle East, AfricaAE – UAE, Dubai Tel: +971 4 812 7100********************AT – Austria, Wiener Neustadt Tel: +43 (0)2622 23501-0*************************AT – Eastern Europe, Wiener Neustadt Tel: +43 (0)2622 23501 900****************************AZ – Azerbaijan, Baku Tel: +994 50 2233 458****************************BE/LU – Belgium, Nivelles Tel: +32 (0)67 280 900*************************BG – Bulgaria, Sofia Tel: +359 2 980 1344**************************BY – Belarus, Minsk Tel: +48 (0)22 573 24 00*************************CH – Switzerland, Etoy Tel: +41 (0) 21 821 87 00*****************************CZ – Czech Republic, Klecany Tel: +420 284 083 111*******************************DE – Germany, Kaarst Tel: +49 (0)2131 4016 0*************************DK – Denmark, Ballerup Tel: +45 43 56 04 00*************************ES – Spain, Madrid Tel: +34 902 33 00 01***********************FI – Finland, VantaaTel: +358 (0)20 753 2500*************************FR – France, Contamine s/Arve Tel: +33 (0)4 50 25 80 25************************GR – Greece, Athens Tel: +30 210 933 6450************************HU – Hungary, Budapest Tel: +36 223 885 470*************************IE – Ireland, DublinTel: +353 (0)1 466 6370*************************IT – Italy, Corsico (Ml)Tel: +39 02 45 19 21***********************KZ – Kazakhstan, Almaty Tel: +7 7273 561 000****************************NL – The Netherlands, Oldenzaal Tel: +31 (0)541 585 000********************NO – Norway, Stavanger Tel: +47 66 75 34 00************************PL – Poland, Warsaw Tel: +48 (0)22 573 24 00************************PT – Portugal, Leca da Palmeira Tel: +351 22 999 7360**************************RO – Romania, Bucharest Tel: +40 21 252 1382*************************RU – Russia, Moscow Tel: +7 495 645-2156************************SE – Sweden, Spånga Tel: +46 (0)8 59 79 50 00************************SK – Slovakia, Banská Bystrica Tel: +421 484 162 252**************************SL – Slovenia, Novo Mesto Tel: +386 7 337 6650**************************TR – Turkey, Istanbul Tel: +90 216 4997081************************UA – Ukraine, KievTel: +48 (0)22 573 24 00*************************UK – United Kingdom, Warwick Tel: +44 (0)1926 317 878********************ZA – South Africa, Kempton Park Tel: +27 (0)11 961 0700*****************************。
电动蝶阀使用说明书(中英文)

电动蝶阀使用说明书(中英文)电动蝶阀Electric Butterfly Valve使用说明书Operation Manual一、用途Ⅰ.Application本系列蝶阀适用于冶金、矿山、建材、石化、造纸、纺织等行业的工业管道中。
它对气体半流体等管道中的介质按不同的信号,改变其流量的大小,从而达到自动调整风量,实现自动控制。
体阀采用优质钢板焊接结构,具有传动轻巧灵活,密封性能好,开闭时间短,切断速度快,能可靠的杜绝事故的发生。
This series butterfly valve is suitable to use in the industry pipe of metallurgical, ore building material. Paper textile and so on, Accord to the different signal in the pipes of the gas half fluid medium. Change the flow volume, and adjust the fan volume automatically. It can realize automatic control. The valve is used good welding structure. It is characterized by light, nimble good sealing, short open time, fast speed broken and dependable.二、结构及工作原理Ⅱ.The structure and Working principle1、电动蝶阀由电动执行机构和蝶阀组成,有关电动执行机构作用原理,使用维护等参阅电动执行机构说明书。
1、The electric butterfly valve is composed of electric executestructure and butter fly valve. The relative electric execute. Working principle and main is refer to the operation manual of electric executor.2、电动蝶阀按作业方式可分为电开式和电关式两种。
- 1、下载文档前请自行甄别文档内容的完整性,平台不提供额外的编辑、内容补充、找答案等附加服务。
- 2、"仅部分预览"的文档,不可在线预览部分如存在完整性等问题,可反馈申请退款(可完整预览的文档不适用该条件!)。
- 3、如文档侵犯您的权益,请联系客服反馈,我们会尽快为您处理(人工客服工作时间:9:00-18:30)。
Non-Invasive Electric Actuator Electronic control module debugginginstructionsVersion V201SummaryThis component can receive the DCS system on-off signals (passive dry contact of active, active 24 v, 220 v, keep running can switch) or analog signals (DC4-20 ma, 0 to 10 v, etc.), direct drive electric actuators switch action or adjust the action. Output DC4-20 ma feedback current and contact/remote control state instructions. The component integration the servo control unit, solid-state drive unit, liquid crystal display unit, knobs and other ancillary units and aluminum shell assembly operation.The product operates as a fool camera is simple, like intelligent perfect protection function.2Operating Instructions2.1Knob Operating InstructionsThe red knob is the mode button, can be switched between Local/Stop/Remote. Or in a set state, to save the menu contents (from the stop bit screwed to the site) or to exit the menu(from the stop bit screwed into the remote).Black knob for the operating button can be opened or closed operation at the local.Or to plus or minus in the set state.With button operation, short time effect for the inching mode. When the operation button is effective for more than 3 seconds, in the lower right corner of the LCD, the bc is displayed automatically entered into the hold mode. When actuator movement, click the action button reverse rotation or spin mode button to Stop, the actuator Array stops.2.2 setting tool description (setting tool are optional, needto please when ordering special instructions)"Up" button = Open calibration key, "Down" button = close calibrationkey, "Enter" button = Confirm key or Save key"Stop" button = stop key, "Open" button = open key, "Close" button =close key.When mode button at Local location, press "Open" button to performopen, press "Close" button to perform off. In the action, press the"Stop" button to stop the move, short press "Close" to stop the openingprocess, short press "Open" to stop the closing process.In local mode, even by three "Up" key to enter the open position calibration status, "Open", "Close" and "Stop" keys to control the electric actuator to open, close and stop, "Enter" key to save the trip, "Stop "key is used to return.In local mode, even by three "Down" key to enter the closed position calibration status, like the rest of the operation as above.3Signal query (LCD lower left corner for a signal check area) 3.1 Remote control signal inquiryWhen the mode button is screwed into the Remote, the remote control signal received is displayed in the lower-left corner of the LCD. Switch type: show OP represents a open signal, show CL represents a close signal, show BC represents a keep signal (multi state of coexistence of alternate display). Regulating type: to display the received control current value or voltage value.3.2 Valve position signal queryWhen the mode button is screwed onto the Local, the LCD shows the valve position signal in lower left corner. When using a potentiometer, show the percentage of resistance (d01 ~ d99); When using 12 encoder, shows the percentage of the encoder (b01 ~ b99); When using 18 encoder, display micrometer ratio of the encoder (001 to 999).4 4 Stroke calibrations4.1 Calibration for close limit:The mode button at the Stop position, the rotary operation knob to the Close position for about 3 seconds, until the letter L is flashing of the LCD to release operation button, then the mode button to the Local position, now letter L no longer flashes and the system into the closed position calibration status. The actuator can open or close by the operating button. When the actuator operates to the closed position, then the mode button to spin the Stop position, and back to the Local position, at this time the red LED flashing two times said the closed position calibration is completed. If the mode button is screwed to the Remote position from Stop position, that exit travel calibration.4.2 Calibration for open limitThe mode button at the Stop position, the rotary operation knob to the Open position for about 3 seconds, until the letter H is flashing of the LCD to release operation button, then the mode button to the Local position, now letter H no longer flashes and the system into the open position calibration status. The actuator can open or close by the operatingmode button to spin the Stop position, and back to the Local position, at this time the green LED flashing two times said the open limit position calibration is completed. If the mode button is screwed to the Remote position from Stop position, that exit travel calibration.Note: When you save a stroke, display Fu or Fn characters on the LCD, please re-adjust potentiometer or rotary encoder range, and recalibrate the trip.5Feedback current trimming5.1 Feedback current 4mA trimmingThe mode button at the Stop position, the rotary operation knob to the Open position for about 10 seconds, until the letter LF is flashing of the LCD to release operation button, then the mode button to the Local position and back to the Stop position, and the system into the 4mA current trimming status. At this point,the size of the output current can be adjusted by the operating button. When adjusting the output current reaches 4mA, then mode button to spin the Local position, this time the red LED flashes three times, said 4mA output current trim is complete. If the mode button to Stop position from Remote position, which exit status of the output current trim.5.2 Feedback current 20mA trimmingThe mode button at the Stop position, the rotary operation knob to the Open position for about 10 seconds, until the letter HF is flashing of the LCD to release operation button, then the mode button to the Local position and back to the Stop position, and the system into the 20mA current trimming status. At this point,the size of the output current can be adjusted by the operating button. When adjusting the output current reaches 4mA, then mode button to spin the Local position, this time the green LED flashes three times, said 20mA output current trim is complete. If the mode button to Stop position from Remote position, which exit status of the output current trim.6About dead zoneThe dead zone to adapt automatically, without setting can ensure that in any conditions without oscillation, and the positioning precision is higher.7Alarm description (error code displayed on the LCD in the lower right corner) FaultcodeFault informationFA Actuator running direction errorFu V alve position potentiometer or encoder Angle is too largeFn V alve position potentiometer or encoder Angle is too smallFP Power phaseFF Broken valve position potentiometer, rotary to blind or pick the wrong line, or encoder failure.FC Over closed torqueFO Over open torqueFH Remote control signals to open and close signals exist (only on-off type)FS Control current signal is lost (only positioning)Fb Current control signal calibration error(only positioning)Fd Stall or other causes the valve position does not changeFL Limit contact line or torque contact line reversedFE The motor is too hot or the torque public terminal is openNOTE: The green LED is the open limit position light on the screen, the red LED is closed position light on the screen.8Advanced SettingsNOTE: All the Advanced Settings can be set after the mode button in the "Local" position. Advanced settings must open the electrical box cover and you can operate. The Close Key and Open Key mentioned below are in the electronic control board.8.1 Action when the control current loss:(Only positioning type, default: Remain in Situ)8.1.1 To press the “Close Key” and power up for 3 seconds until the red LED on the board is lit. And you release the key, then the red LED flashes three times; the “FullClose” setup is completed.8.1.2 To press the “Open Key” and power up for 3 seconds until the green LED on the board is lit. And you release the key, then the green LED flashes three times; the “Full Open” setup is completed.8.1.3 Simultaneously press two keys and power up for 3 seconds until the green and red LEDs on the board are lit. And you release the two keys simultaneously, then the two LEDs flashes three times; the “Remain in Situ” setup is completed.8.2 Control current calibration:(Only positioning type)8.2.1 To send 4mA control current to the module from the outside, press the “Close Key” and power up for 10 seconds until the red LED on the board is lighted second times. And you release the key, then the red LED flashes three times; and the4mA calibration is completed.8.2.2 To send 20mA control current to the module from the outside, press the “Open Key” and power up for 10 seconds until the green LED on the board is lighted second times. And you release the key, then the green LED flashes three times; and the20mA calibration is completed.8.3 Polarity for the control current:(Only positioning type)20mA = Full Open /4mA = Full Open (default:20mA = Full Open) Simultaneously press “Open Key” and “Close Key” and then power up for 10 seconds. To release the key after the red LED and green LED second lights up. Short press “Open Key” or “Close Key” to alternately lit red LED or green LED. The red LED light represents “20mA = Full Open”, the green LED light represents “4mA = Full Open”. Simultaneously press “Open Key” and “Close Key” for 3 seconds. To release two keys after the two LEDs lights up. Then corresponding LED flashes three times, the polarity for the control current setup is complete.8.4 Two-Wire Control:(Only on-off type)Disable or Open First or Close First (default: Disable)8.4.1Close FirstYou press “Close Key” and then power up for 10 seconds. The key is released after the red LED second light up. And the red LED flashes three times, this setup is complete. This Close First refers to the actuator close operation when voltages signal on the “Remote Close” terminal of the actuator. But no voltage signal, actuators open operation. When wiring, “Remote Open” terminal connected to 24V +.8.4.2Open FirstYou press the “Open Key” and then power up for 10 seconds. The key is released after the green LED second light up. And the green LED flashes three times, this setup is complete.This Open First refers to the actuator open operation when voltages signal on the “Remote Open” terminal of the actuator. But no voltage signal, actuators close operation. When wiring, “Remote Close” terminal connected to 24V +.8.4.3 DisableYou press the two keys simultaneously and then power up for 10 seconds. The key is released after the two LEDs second lights up. Then the two LEDs flashes three times, this setup is complete.8.5 Close direction:Clockwise /Anti-clockwise (default:Clockwise)You press the “Open Key” and “Close Key” simultaneously and then power up for 20 seconds. The keys are released after the red LED and green LED third lights up. Short press “Open Key” or “Close Key” to alternately lit red LED or green LED. Red LED light represents “Clockwise”, green LED light represents “Anti-clockwise”. You press the two keys simultaneously for 3 seconds. The keys is released after the two LEDs light up. Then corresponding LED flashes three times, the Close direction setup is complete.9Common problems to deal withPower LED is not lit or digital display does not show 1. Power is not actually access. 2. voltage is too low 3. Wiring fault. 4. Module badLEDs and digital display abnormal 1. See fault code.2. Query information.3. Replace the moduleAfter power on ,actuator can be not control in the LOCAL and REMOTE mode 1. Wiring fault or loose wiring. 2. Fault Protection.3. Motor bad or stuck.4. Bad start capacitor.5. module badLOCAL mode work is normal but the REMOTE mode can't control 1. No signal or junction anti- , 2. Bad or no knob plate in Remote3. Positive / reaction set wrong.4. Module badREMOTE mode work is normal but the LOCAL mode can't control 1. Not in LOCAL mode. 2. Knobs board bad or not at the scene mode. 3. Operation button is not properly screwed in placeActuator can open but not close or can close but not open 1. Torque wiring fault or loose wiring. 2. to limit position or over torque3. Motor bad or stall or wiring fault.4. Module badThe action immediately after power on 1. Wiring fault. 2. control signal is present3. Implementation the action when the control current loss4. Set the wrong.5. module badThe middle position can move but to the limit position does not move 1. Reverse limit switch line. 2. Motor bad or loose wiring 3. Module badThe direction of movement is the anti 1. Motor lines reversed. 2. Anti valve calibration.3. Signal Reverse4. Polarity for the control current or closing direction set wrong.No output current or sometimes no 1. The output wiring fault or bad. 2. Module bad 3. potentiometer wiring fault or loose wiringFeedback current is larger or smaller or unchanged 1.Potentiometer failure. 2. Calibration error.3. module bad4. potentiometer meshing with drive gear not wellNote: Please strictly in accordance with the wiring diagram electrical wiring connection.Like has the change, without notice。