发泡工艺规程要点
发泡生产工艺
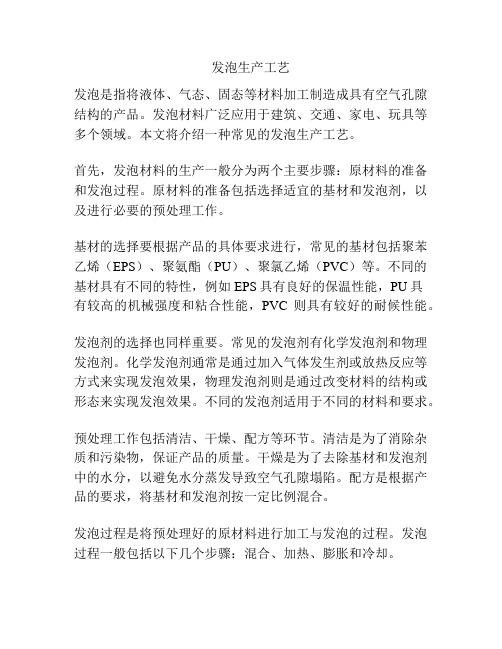
发泡生产工艺发泡是指将液体、气态、固态等材料加工制造成具有空气孔隙结构的产品。
发泡材料广泛应用于建筑、交通、家电、玩具等多个领域。
本文将介绍一种常见的发泡生产工艺。
首先,发泡材料的生产一般分为两个主要步骤:原材料的准备和发泡过程。
原材料的准备包括选择适宜的基材和发泡剂,以及进行必要的预处理工作。
基材的选择要根据产品的具体要求进行,常见的基材包括聚苯乙烯(EPS)、聚氨酯(PU)、聚氯乙烯(PVC)等。
不同的基材具有不同的特性,例如EPS具有良好的保温性能,PU具有较高的机械强度和粘合性能,PVC则具有较好的耐候性能。
发泡剂的选择也同样重要。
常见的发泡剂有化学发泡剂和物理发泡剂。
化学发泡剂通常是通过加入气体发生剂或放热反应等方式来实现发泡效果,物理发泡剂则是通过改变材料的结构或形态来实现发泡效果。
不同的发泡剂适用于不同的材料和要求。
预处理工作包括清洁、干燥、配方等环节。
清洁是为了消除杂质和污染物,保证产品的质量。
干燥是为了去除基材和发泡剂中的水分,以避免水分蒸发导致空气孔隙塌陷。
配方是根据产品的要求,将基材和发泡剂按一定比例混合。
发泡过程是将预处理好的原材料进行加工与发泡的过程。
发泡过程一般包括以下几个步骤:混合、加热、膨胀和冷却。
混合是将配好比例的基材和发泡剂进行充分混合,并加入适量的辅助材料,如增塑剂、阻燃剂等。
混合过程可以通过搅拌或料斗等装置来完成。
加热是将混合好的原材料加热到一定温度,以促进发泡剂的活化和膨胀。
不同的发泡材料有不同的加热温度要求,一般需要在高温下进行加热。
膨胀是指发泡剂受热后产生气体,使材料形成孔隙结构的过程。
发泡剂可通过气化、蒸发或分解等方式释放气体,使材料发生体积膨胀。
冷却是将膨胀好的发泡材料冷却,使其固化并保持其形状。
冷却过程还可以通过控制冷却速度和温度来调节产品的密度和硬度。
以上便是发泡材料生产的常见工艺流程。
不同的发泡材料和产品要求可能还会有一些特殊的工艺步骤。
随着科技的发展和需求的不断增加,发泡材料生产工艺也在不断更新和改进,以提高产品的质量和性能。
发泡操作工艺规范
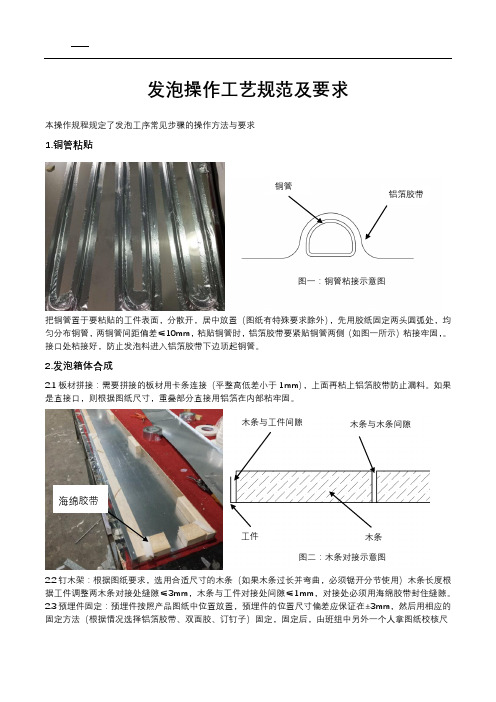
发泡操作工艺规范及要求本操作规程规定了发泡工序常见步骤的操作方法与要求1.铜管粘贴把铜管置于要粘贴的工件表面,分散开,居中放置(图纸有特殊要求除外),先用胶纸固定两头圆弧处,均匀分布铜管,两铜管间距偏差≤10mm ,粘贴铜管时,铝箔胶带要紧贴铜管两侧(如图一所示)粘接牢固,。
接口处粘接好,防止发泡料进入铝箔胶带下边顶起铜管。
2.发泡箱体合成2.1板材拼接:需要拼接的板材用卡条连接(平整高低差小于1mm ),上面再粘上铝箔胶带防止漏料。
如果是直接口,则根据图纸尺寸,重叠部分直接用铝箔在内部粘牢固。
图一:铜管粘接示意图铝箔胶带铜管木条与工件间隙木条与木条间隙海绵胶带工件木条图二:木条对接示意图2.2钉木架:根据图纸要求,选用合适尺寸的木条(如果木条过长并弯曲,必须锯开分节使用)木条长度根据工件调整两木条对接处缝隙≤3mm,木条与工件对接处间隙≤1mm,对接处必须用海绵胶带封住缝隙。
2.3预埋件固定:预埋件按照产品图纸中位置放置,预埋件的位置尺寸偏差应保证在±3mm,然后用相应的固定方法(根据情况选择铝箔胶带、双面胶、订钉子)固定,固定后,由班组中另外一个人拿图纸校核尺寸及件数,防止出现位置不对,漏埋等不良现象。
2.4刷胶:对于不锈钢砂板材质的表面在室温低于20℃时表面必须刷胶,刷胶后放置30min后方可注料。
2.5订钉子:钉子之间的间隙为100mm±10mm,要求:钉子均匀平整。
2.6尺寸校核:工件完全订好后,对照图纸对尺寸校核未注线性公差按照(尺寸1mm∽1500mm 之间为±1mm尺寸1501mm∽4000mm 之间为±2mm)操作,角度未注公差为±1˚。
注:校核尺寸必须量对角。
3.装模(适用于非整体模具)打开模具后,清理干净模具中遗留的发泡料,把工件放入模具中,工件不靠模具侧壁的面要用挡条挡住,模具侧壁工件位置挡板然后用顶杆顶住(挡条和顶杆可用材料为木条、方管、矩形管等),挡条的长度为被挡的“工件面长度-100mm”厚度为“工件发泡层厚度0-1mm”。
发泡工艺规程2007.10
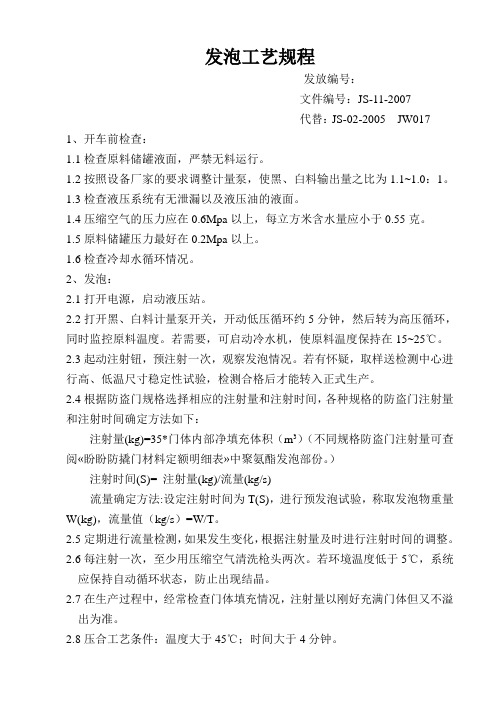
发泡工艺规程发放编号:文件编号:JS-11-2007代替:JS-02-2005 JW0171、开车前检查:1.1检查原料储罐液面,严禁无料运行。
1.2按照设备厂家的要求调整计量泵,使黑、白料输出量之比为1.1~1.0:1。
1.3检查液压系统有无泄漏以及液压油的液面。
1.4压缩空气的压力应在0.6Mpa以上,每立方米含水量应小于0.55克。
1.5原料储罐压力最好在0.2Mpa以上。
1.6检查冷却水循环情况。
2、发泡:2.1打开电源,启动液压站。
2.2打开黑、白料计量泵开关,开动低压循环约5分钟,然后转为高压循环,同时监控原料温度。
若需要,可启动冷水机,使原料温度保持在15~25℃。
2.3起动注射钮,预注射一次,观察发泡情况。
若有怀疑,取样送检测中心进行高、低温尺寸稳定性试验,检测合格后才能转入正式生产。
2.4根据防盗门规格选择相应的注射量和注射时间,各种规格的防盗门注射量和注射时间确定方法如下:注射量(kg)=35*门体内部净填充体积(m3)(不同规格防盗门注射量可查阅«盼盼防撬门材料定额明细表»中聚氨酯发泡部份。
)注射时间(S)= 注射量(kg)/流量(kg/s)流量确定方法:设定注射时间为T(S),进行预发泡试验,称取发泡物重量W(kg),流量值(kg/s)=W/T。
2.5定期进行流量检测,如果发生变化,根据注射量及时进行注射时间的调整。
2.6每注射一次,至少用压缩空气清洗枪头两次。
若环境温度低于5℃,系统应保持自动循环状态,防止出现结晶。
2.7在生产过程中,经常检查门体填充情况,注射量以刚好充满门体但又不溢出为准。
2.8压合工艺条件:温度大于45℃;时间大于4分钟。
3、维修保养3.1每星期清洗过滤器一次。
3.2每半年清洗一次液压油滤网。
3.3压缩空气储罐每天应排污两次以上。
3.4严禁水、汽进入原料系统,料温维持在5℃以上。
3.5检查所有管线及接头,特别是黑白料和液压油胶皮管,如有破损或被重压,应及时更换。
预发泡、发泡工艺规程

质量体系C层次文件版本号:A/0-0 预发泡工艺规程XB/Q-C-01.6-2003-A7.0(一)预发泡操作通用工艺规程1、接通电源,设备电源指示灯亮。
2、通压缩空气,气压值要求不少于0.5MPa。
3、通蒸汽,蒸汽供应压力不少于0.4MPa,并打开其管路排水阀门,排放冷凝水至有大量蒸汽冒出后关闭此阀门。
一般每次生产前开放一次。
4、打开压缩空气排水阀门,排放积水,此阀门一般不关闭。
5、打开蒸汽回路排水阀门,一般不关闭,若冒出蒸汽可关闭少许。
6、打开仓门,清理仓内残留物。
7、启动主轴,关闭仓门。
8、调节蒸汽进汽阀门,控制温度及蒸汽压力,并根据需要设置加热温度为88~100℃。
9、打开加热开关和进气开关,减压开关一般可关闭。
10、加料,每次加可发性聚苯乙烯(EPS)量为1.25~1.35 kg;当温度超过设定值时,指示灯变化,可打开仓门出料,清理仓内和仓门,再关闭仓门继续重复操作。
打开包装的EPS珠粒要求一次性预发完。
11、工作完成后,停止主轴,关闭压缩空气气路、蒸汽气路阀门,关闭电源。
12、预发后的珠粒要在18~25℃、通风良好的环境中贮存8~12小时方可进行发泡。
(二)发泡操作通用工艺规程1、安装模具于发泡机工作台上,深腔模装于上部,浅腔模装于下部。
安装完毕升降工作台合模检查。
2、通压缩空气,压力要求0.5MPa 以上;接通水路蓄满蓄水池。
XB/Q-C-01.9-2003-A8.0 版本号:A/1-0保证供应的蒸汽压力0.4~0.6MPa。
3、工作前排放蒸汽管路的积留水,并打开蒸汽阀门到冒大量蒸汽再都关闭。
4、降下上工作台,使模具间保留3~5mm间隙(若是磨球,则不留间隙)。
5、料枪与模具进料口联接,打开上下进出口,通压缩空气吹吸式充料,充满后关闭料枪气路,用铁杵堵塞进料口。
6、通蒸汽于模腔,微开下出口,关闭上出口,至冒蒸汽止,合模,当蒸汽压力表值为0.1MPa时,关闭下进口;当蒸汽压力表值又为0.1MPa时,关闭蒸汽阀门。
发泡工艺操作规范

发泡工艺操作管理规范目录1、前言 .............................................................................................................................................................................2、适用范围 ..........................................................................3、规范引用文件 ......................................................................4、重要发泡参数定义和反应机理 ........................................................5、各部门职责 ........................................................................6、发泡的采购、入库检验与保存 ........................................................7、发泡来料检验准备工作 ..............................................................8、发泡来料检验和规范 ................................................................9、生产前准备工作 ....................................................................10、发泡过程控制和检验 ...............................................................11、生产加料作业规范 .................................................................12、发泡常见问题解决对策 ..............................................................13、 发泡填充量的计算方法 ............................................................14、发泡原料的保存 ...................................................................15、发泡料的使用注意事项及事故 .......................................................16、发泡工要求和培训工作 .............................................................发泡操作工艺管理标准一、 适用范围本规范规定了发泡(箱体和门体)工艺过程中各相关部门与人员的职责;发泡材料的采购、入库检验与保存规范;发泡工艺标准规范;橱柜发泡质量检查;发泡料使用安全注意事项。
发泡材料生产工艺
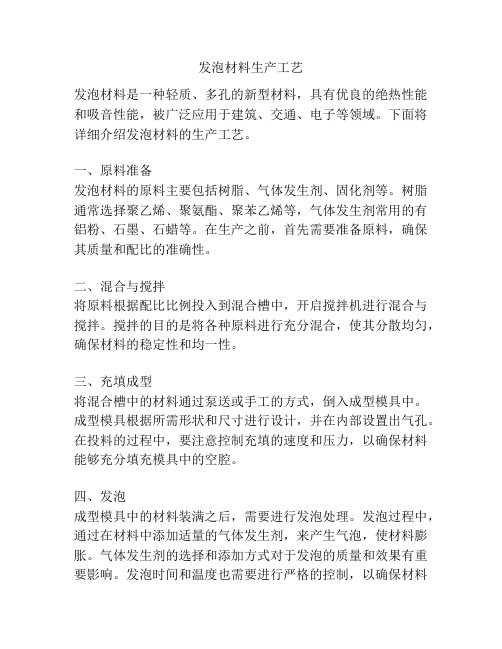
发泡材料生产工艺发泡材料是一种轻质、多孔的新型材料,具有优良的绝热性能和吸音性能,被广泛应用于建筑、交通、电子等领域。
下面将详细介绍发泡材料的生产工艺。
一、原料准备发泡材料的原料主要包括树脂、气体发生剂、固化剂等。
树脂通常选择聚乙烯、聚氨酯、聚苯乙烯等,气体发生剂常用的有铝粉、石墨、石蜡等。
在生产之前,首先需要准备原料,确保其质量和配比的准确性。
二、混合与搅拌将原料根据配比比例投入到混合槽中,开启搅拌机进行混合与搅拌。
搅拌的目的是将各种原料进行充分混合,使其分散均匀,确保材料的稳定性和均一性。
三、充填成型将混合槽中的材料通过泵送或手工的方式,倒入成型模具中。
成型模具根据所需形状和尺寸进行设计,并在内部设置出气孔。
在投料的过程中,要注意控制充填的速度和压力,以确保材料能够充分填充模具中的空腔。
四、发泡成型模具中的材料装满之后,需要进行发泡处理。
发泡过程中,通过在材料中添加适量的气体发生剂,来产生气泡,使材料膨胀。
气体发生剂的选择和添加方式对于发泡的质量和效果有重要影响。
发泡时间和温度也需要进行严格的控制,以确保材料在发泡过程中能够达到理想的体积和孔隙率。
五、固化发泡过程完成后,需要将材料进行固化处理。
固化主要是通过加热或添加固化剂等方式,使材料中的树脂发生交链反应,形成结构稳定的发泡材料。
固化温度和时间的控制对于材料的性能和质量具有重要影响。
固化完成后,材料会变得坚固耐用,能够满足各种使用要求。
六、后处理固化完成后,进行后处理工艺。
包括切割成型、修整边角、去除表面缺陷等。
还可以根据需要进行涂覆、喷漆等处理,以提高产品的外观和使用性能。
综上所述,发泡材料的生产工艺包括原料准备、混合与搅拌、充填成型、发泡、固化和后处理等环节。
这些环节都需要严格控制各项参数,确保材料的质量和性能符合要求。
只有通过科学的生产工艺,才能生产出具有优良性能和稳定质量的发泡材料。
PU发泡操作规程
PU发泡操作规程PU发泡是一种常见的工艺,在建筑、汽车、家具等领域都有广泛的应用。
为了确保PU发泡操作安全、高效、质量稳定,制定一份PU发泡操作规程至关重要。
下面是一份关于PU发泡操作规程的示例,供参考。
一、安全操作规程1.操作人员必须穿戴符合安全标准的工作服、安全帽、防滑鞋等必要的个人防护装备。
2.PU发泡工作区必须保持整洁,无杂物堆积,设有明显的安全警示标识。
3.PU发泡设备必须接受定期维护,确保正常运转,防止因设备故障引发事故。
4.使用PU发泡材料前,必须先了解其特性、储存和操作要求,并遵循供应商提供的使用说明。
5.在操作过程中,禁止吸烟、火源靠近操作区,以免引发火灾或爆炸事故。
6.发生紧急情况时,操作人员必须立即切断PU发泡设备电源,并进行逃生或紧急处理。
二、操作流程1.准备工作:a.清理操作区域,确保无明火和易燃材料。
b.确认PU发泡设备和相关材料齐全,并检查设备和工具是否正常。
c.确定PU发泡材料的用量和施工位置。
2.设备操作:a.开启PU发泡设备电源,调试设备至合适状态。
b.将PU发泡材料装入设备中,根据需要调整出胶量和出胶速度。
c.根据材料特性和工作要求,调整设备温度和压力,并保持恒定。
3.施工操作:a.使用喷枪将PU发泡材料均匀地涂覆在需要发泡的部位上。
b.涂覆完成后,根据需要进行整形和修理,确保表面光滑。
c.考虑发泡材料的膨胀性,合理控制材料用量和施工速度,避免浪费和过量膨胀。
4.清洁和维护:a.施工结束后,立即关闭PU发泡设备电源,仔细清洁设备和喷枪。
b.确保设备干燥,防止材料残留和堵塞。
c.定期对设备进行维护和保养,确保其正常运转。
三、质量控制要求1.PU发泡材料的存储期限和储存条件必须符合供应商要求,避免运用过期或不合格材料。
2.发泡前,必须对施工部位进行适当的准备工作,如清洁、干燥、涂装等,以确保施工效果。
3.严格控制材料用量和施工厚度,避免过量或不足,保证施工质量。
发泡工艺资料
发泡工艺资料目录一、聚氨酯生产原料1、黑料2、白料3、发泡剂二、发泡工艺原理三、环戊烷发泡工艺参数的操纵四、反应速度参数五、聚氨酯泡沫性能要求六、发泡工艺操纵要点七、聚氨酯发泡常见问题及决绝措施环戊烷体系硬质聚氨酯发泡工艺技术一、聚氨酯生产原料聚氨酯生产要紧原料有:黑料、白料、发泡剂。
1、黑料: 黑料的学名为多异氰酸酯,因其是一种黑色粘稠液体,故俗称黑料。
多异氰酸酯的要紧品种有MDI、TDI、PAPI,其中MDI〔二苯基甲烷二异氰酸酯〕用于冰箱聚氨酯泡沫生产。
2、白料:工业生产冰箱聚氨酯泡沫时,通常先将组合聚醚型多元醇、催化剂,泡沫稳固剂进行混合,这种混合物是一种白色粘稠液体,俗称白料。
(1) 组合聚醚型多元醇:冰箱聚氨酯泡沫所使用的多元醇为聚醚型多元醇。
(2) 催化剂:催化剂的要紧作用是加速聚氨酯的形成,缩短固化时刻,提高发泡质量。
(3) 泡沫稳固剂:泡沫稳固剂的要紧作用是乳化系统中的各原料组份,保证体系反应顺利进行;促进气泡的成核作用;提高气泡壁稳固性,使制品泡孔平均细密,具有良好的机械性能。
稳固剂的用量尽管不大,但对泡沫体的泡孔结构、物理性能、制造工艺都有着重大阻碍。
(4) 组合聚醚的性能指标(组合聚醚牌号:HY MA021801)3、发泡剂:在聚氨酯发泡中,发泡剂要紧作用是产动气体,在聚氨酯中形成平均分布的细小气泡。
发泡剂本身不参加多异氰酸酯和组合聚醚之间的化学反应。
利用氟利昂〔如R11、R12〕作发泡剂的发泡工艺称为有氟发泡。
发泡剂不含氟利昂的发泡工艺称为无氟发泡。
如环戊烷发泡。
二、发泡工艺原理通过高压发泡机的注射枪头把黑料和白料与环戊烷的预混物进行混合,并注入箱体或门体的外壳和内胆之间的夹层内。
在一定温度条件下,多异氰酸酯〔中的异氰酸根〔-NCO〕〕与组合聚醚〔中的羟基〔-OH〕〕在催化剂的作用下发生化学反应,生成聚氨酯,同时开释大量热量。
现在预混在组合聚醚的发泡剂〔环戊烷〕不断汽化使聚氨酯膨胀填充壳体和内胆之间的间隙。
发泡操作工艺规范
发泡操作工艺规范及要求本操作规程规定了发泡工序常见步骤的操作方法与要求1.铜管粘贴把铜管置于要粘贴的工件表面,分散开,居中放置(图纸有特殊要求除外),先用胶纸固定两头圆弧处,均匀分布铜管,两铜管间距偏差≤10mm ,粘贴铜管时,铝箔胶带要紧贴铜管两侧(如图一所示)粘接牢固,。
接口处粘接好,防止发泡料进入铝箔胶带下边顶起铜管。
2.发泡箱体合成2.1板材拼接:需要拼接的板材用卡条连接(平整高低差小于1mm ),上面再粘上铝箔胶带防止漏料。
如果是直接口,则根据图纸尺寸,重叠部分直接用铝箔在内部粘牢固。
2.2钉木架:根据图纸要求,选用合适尺寸的木条(如果木条过长并弯曲,必须锯开分节使用)木条长度根据工件调整两木条对接处缝隙≤3mm ,木条与工件对接处间隙≤1mm ,对接处必须用海绵胶带封住缝隙。
2.3预埋件固定:预埋件按照产品图纸中位置放置,预埋件的位置尺寸偏差应保证在±3mm ,然后用相应的固定方法(根据情况选择铝箔胶带、双面胶、订钉子)固定,固定后,由班组中另外一个人拿图纸校核尺图一:铜管粘接示意图铝箔胶带铜管 图二:木条对接示意图木条与工件间隙 木条与木条间隙工件 木条海绵胶带寸及件数,防止出现位置不对,漏埋等不良现象。
2.4刷胶:对于不锈钢砂板材质的表面在室温低于20℃时表面必须刷胶,刷胶后放置30min后方可注料。
2.5订钉子:钉子之间的间隙为100mm±10mm,要求:钉子均匀平整。
2.6尺寸校核:工件完全订好后,对照图纸对尺寸校核未注线性公差按照(尺寸1mm∽1500mm 之间为±1mm尺寸1501mm∽4000mm 之间为±2mm)操作,角度未注公差为±1˚。
注:校核尺寸必须量对角。
3.装模(适用于非整体模具)打开模具后,清理干净模具中遗留的发泡料,把工件放入模具中,工件不靠模具侧壁的面要用挡条挡住,模具侧壁工件位置挡板顶杆图三:平板模与直角模具俯视图然后用顶杆顶住(挡条和顶杆可用材料为木条、方管、矩形管等),挡条的长度为被挡的“工件面长度-100mm”厚度为“工件发泡层厚度0-1mm”。
珍珠棉发泡工艺流程及注意事项详解
珍珠棉发泡工艺流程及注意事项详解下载温馨提示:该文档是我店铺精心编制而成,希望大家下载以后,能够帮助大家解决实际的问题。
文档下载后可定制随意修改,请根据实际需要进行相应的调整和使用,谢谢!并且,本店铺为大家提供各种各样类型的实用资料,如教育随笔、日记赏析、句子摘抄、古诗大全、经典美文、话题作文、工作总结、词语解析、文案摘录、其他资料等等,如想了解不同资料格式和写法,敬请关注!Download tips: This document is carefully compiled by theeditor.I hope that after you download them,they can help yousolve practical problems. The document can be customized andmodified after downloading,please adjust and use it according toactual needs, thank you!In addition, our shop provides you with various types ofpractical materials,such as educational essays, diaryappreciation,sentence excerpts,ancient poems,classic articles,topic composition,work summary,word parsing,copy excerpts,other materials and so on,want to know different data formats andwriting methods,please pay attention!珍珠棉发泡工艺流程及注意事项详解珍珠棉,全称聚乙烯泡沫塑料,因其具有良好的缓冲、抗震、隔热、防潮、抗化学腐蚀等优点,被广泛应用于包装、电子、机械、汽车、家电等多个领域。
- 1、下载文档前请自行甄别文档内容的完整性,平台不提供额外的编辑、内容补充、找答案等附加服务。
- 2、"仅部分预览"的文档,不可在线预览部分如存在完整性等问题,可反馈申请退款(可完整预览的文档不适用该条件!)。
- 3、如文档侵犯您的权益,请联系客服反馈,我们会尽快为您处理(人工客服工作时间:9:00-18:30)。
工艺规程文件编号:HD/GYGC2015-007工艺类别:发泡(通用)编制:校对:审核:批准:生效日期凌海航达航空科技有限公司目录1. 总体要求 (2)2. 目的 (2)3. 适用范围 (2)4. 产品概述 (3)5. 依据 (3)6. 工序级别定义 (3)7. 所用主要设备 (3)8. 工艺流程 (3)9. 检验定义 (3)10. 工作记录 (4)11. 原料特性和配比及验证数据 (4)12. 具体工作要求 (6)13. 聚氨酯发泡作业指导书 (9)14. 工艺重要关联与补充 (13)附录《生产工艺&过程检验卡》(PM-QCP-006-01)——发泡1.总体要求1.1 本工艺的操作者,必须有上岗资格。
执行此工序过程中,操作者,能熟练操作发泡设备,会处理简单的模具问题,熟知发泡原料的配方等发泡基本技能,要密切配合、支持本公司各级检验员的工作,尊重其检验结果,执行质控部对质量问题的纠正、返修裁断。
服从MRB对重大质量问题的审核及处理结果。
1.2 公司内部的生产工序的现场中,该产品/零部件的有效/受控图纸及详实记录的《生产工艺&过程检验卡》(PM-QCP-006-01)、《产品检验记录卡》(PM-QCP-006-03)、《产品终检检验卡》(PM-QCP-006-04)等追溯性文件同时存在,必须做到图、物、卡同步存在或转序。
2. 目的2.1 使生产厂家或本公司生产操作者,在本规程的指导下,正确、高效地生产出合格产品。
2.2 为了实现产品生产过程中的质量控制。
2.3 为了合理利用原辅材料、设备、人员和生产时间。
2.4 为了使公司管理规范化,使生产中的“人、机、料、法、环”得到统筹、合理安排和利用,最大限度地减小内耗、提高效益。
3.适用范围:3.1 桌板类壳体内填充的闭孔硬质发泡。
3.2 扶手胶皮类以金属或塑料为骨架的自结皮发泡。
3.3 非漂浮型的非乘客座椅的椅垫或发泡填充块。
4. 产品综述4.1 无骨架类软或硬质聚氨酯产品。
4.2 内嵌金属或塑料骨架外覆聚氨酯自结皮的产品。
4.3内嵌金属或塑料骨架外覆聚氨酯为填充且外覆真皮为面类产品。
5. 依据《生产任务单》、《检验规程》、受控/有效图纸、经技术确认的样品或等效的技术文件。
6.工序级别定义:6.1 A级:组装类工序。
6.2 B级:零部件或分件生产工序。
7.所用主要设备序号设备名称设备型号设备编号1 发泡加热平台N/A HDSCSB-0512 发泡加热加力平台N/A HDSCSB-0528.工艺流程生产前准备——调A料颜色——加热模具——涂脱模剂——配料——模内加料——发泡开始——取模——室温冷却——整形——转序/包装入库9. 检验定义9.1 自检:由操作者在生产操作过程中自行检验。
9.2 专检:由专职检验员检验即车间检验员、总检检验。
10. 工作记录10.1 直接性记录10.1.1 《领料单》10.1.2 《生产工艺&过程检验卡》(PM-QCP-006-01)10.1.3 《产品检验记录卡》(PM-QCP-006-03)10.1.4 《产品终检检验卡》(PM-QCP-006-04)10.1.5 《入库单》10.1.6 《出库单》10.2 间接性记录10.2.1 《样品样件台账》(PM-ECP-011)10.2.2 《文件收发登记本》(PM-ECP-010-01)10.2.3 《产品报废申请单》(PM-PCP-024-01)10.2.4 《产品报废台账》(PM-PCP-024-02)11. 原料特性和配比及验证数据我公司聚氨酯发泡产品主要原材料是HZD-6802M(中硬度)和HZD-6802L(低硬度)结皮聚氨酯合料的A料和B料。
11.1 物理性质:A料原液:粘度(25℃)1000±200 MPa·sB料原液:粘度(25℃)200±100 MPa·sA料原液比重:(25℃)1.05±0.05g/cm3B料原液比重:(25℃)1.22±0.05g/cm311.2 重量配比:中硬度HZD-6802M 的A料为:(A+C+D):B=[(100+(10~20)+(1~3)]:(40~60)低硬度HZD-6802L 的A料为:(A+C+D):B=[(100+(10~20)+(1~3))]:(40~60)11.3 反应时间(在料温25℃、搅拌转速3000转/分的条件下):CT(乳化时间)HZD-6802M:20-40sec HZD-6802L:20-40sec CT (胶化时间) HZD-6802M:30-60sec HZD-6802L:30-60sec RT(上升停止时间)HZD-6802M:35-70sec HZD-6802L:35-70sec DMT(脱模时间)HZD-6802M:180-360sec HZD-6802L:180-360sec总时间:HZD-6802M:265-530sec HZD-6802L:265-530sec 11.4 发泡性能:11.4.1 HZD-6802M:自由密度:140-200kg/m3测试方法:DIN53420模塑密度:400-500kg/m3测试方法:DIN53420皮层密度:800-900kg/m3测试方法:DIN53479结皮厚度:0.8-2.0mm表面平均硬度:55-75shoreA 测试方法:DIN53505拉伸强度:≥5MPa 测试方法:DIN53571断裂伸长率:≥100% 测试方法:DIN53504撕裂弹度:≥5KN/m 测试方法:DIN5350411.4.2 HZD-6802L:自由密度:80-120kg/m3测试方法:DIN53420模塑密度:200-400kg/m3测试方法:DIN53420皮层密度:600-800kg/m3测试方法:DIN53479结皮厚度:0.8-2.0mm表面平均硬度:40-60shoreA 测试方法:DIN53505拉伸强度:≥3mpa 测试方法:DIN53571断裂伸长率:≥100% 测试方法:DIN53504撕裂弹度:≥3KN/m 测试方法:DIN53504上述数据均来自实验室。
12. 具体工艺要求(见下表)工序工艺质量要求设备/工具检验生产前准备1.按照《生产任务单》、图纸或样品等技术指令,领取模具和原料等生产物资。
N/A 自检、专检2.按图纸或样品等要求,领取所需的预埋件或骨架。
N/A 自检、专检3.按需领取A料. B料. 阻燃剂. 颜色料. 吹色漆. 催化剂.141B氟利昂. 脱模剂。
N/A 自检、专检4.检查模具的完好性,尤其是模具内膜的各部位、活动件及内表面。
N/A 自检、专检5.外观检查骨架等预埋件的完好性,对需要封闭的部位,如滑道内腔、孔、螺纹等,用适当方式封闭好,避免发泡过程中进入原料堵死而后期难以通透。
N/A 自检、专检调A 料颜1.根据图纸或样品或用户要求等技术指令,对A料进行调色。
N/A 自检、专检2.调色的原则是“由浅入深”,即先预调比要求的颜色稍浅的混合色,然后逐渐增加视觉出的欠缺色,慢慢接近要求的最终颜色。
电子称量杯自检、专检3.将每次调色的混合料,无需模具,自然发成小色块。
待其室温风干后,在光线充足的环境下对比,直到合格为止。
电子称量杯自检、专检色 4.在调色过程中,应随记好每次增减基色的量,及最终合格颜色中的各基色量。
电子称量杯自检、专检5.1-4项为自结皮的软质发泡生产过程中的工艺工艺,桌板内填充类的硬质闭孔发泡,不做颜色要求,无需颜色配比。
N/A 自检、专检模具加热1.检查模具加热台的运行状态是否完好。
加热台自检、专检2.打开模具,检查内模表面的完好性,如花纹是否有缺失磨平、骨架挂孔是否完好、模具转轴是否缺失、生锈卡死、是否活动自如、压杆是否有弯曲、缺件现象。
加热台自检、专检3.将检查好的模具,放在加热台上预热。
同时,将预埋骨架准备好。
加热台自检、专检4.将加热台温度设置在45℃±5℃自动控制,但需操作者随时检查验证,发现偏差过大,一定要调整。
加热台自检、专检涂脱模剂1.将预热后的模具打开,放稳。
N/A 自检、专检2. 用毛刷将脱模剂均匀在内模表面上。
注意毛刷的脱毛不能留在模具内模上,要立即清理掉。
N/A自检、专检3. 桌板内填充的硬泡,也可用内模覆塑料薄膜的方式,代替脱模剂的作用,简化脱模工序。
N/A 自检、专检4,脱模剂的使用要适量,应按要求涂抹,如遇到脱模不畅或局部粘模的情况,应适当增加,或加强涂匀。
N/A自检、专检配料1. 根据模具内腔容积所需重量决定配料多少,且单次配料,不可一次配好多个产品的料,造成因固化而浪费原材料。
量筒、量杯自检、专检2. 调好颜色后的A料按如下比例配料:软—《100:40》;中硬—《100:50》;硬—《100:60》。
量筒、量杯自检、专检3. B料(与A料比)100:30。
量筒、量杯自检、专检4. 阻燃剂. 25%~30%量筒、量杯自检、专检5. 催化剂.≈0.04%。
量筒、量杯自检、专检6. 水(根据要求的软硬情况.)≈0.5~1 g 量筒、量杯自检、专检7. 141B 氟利昂:≈0.5~1 g。
量筒、量杯自检、专检8. 用搅拌器搅拌均匀。
量筒、量杯自检、专检固定1. 外观检查骨架的嵌件或铆接的固定件是否完好。
挂孔是否合格。
量筒、量杯自检、专检2. 检查需要密封的部位是否已经封好。
量筒、量杯自检、专检3. 在骨架表面适当涂抹粘接剂的来加强骨架与发泡之量筒、自检、专检骨架间的粘牢度。
量杯4.利用挂点或挂孔,将骨架稳妥地固定在模具内。
量筒、量杯自检、专检5.固定后仔细检查骨架的到位情况。
量筒、量杯自检、专检模内加料1.根据模具内腔容量,往模具内腔装配制好的聚氨酯发泡料,模具必需水平放置(如特殊情况,具体情况具体定)。
加热台自检、专检2.根据模具内腔情况把料装均匀。
可适当用刷子涂抹。
加热台自检、专检3.如发现料不足,应立即补加。
加热台自检、专检发泡1. 立即合好模具,并锁死。
加热台自检、专检2. 水平推入加热板上,加热40~50℃。
加热台自检、专检3.等待加热到达设定的加热时间。
一般设定时间为:500秒±50秒。
加热台自检、专检启模1.加热时间到达后,立即将模具拉出加热区。
加热台自检、专检2.打开模具,放稳上下模。
N/A 自检、专检3.扭开吊架钉,用木质或更软材料做成的辅助工具,轻轻起动工件周边。
N/A 自检、专检4.启出来的工件,应仔细检查一下外观,是否有瑕疵,如有不可修复性瑕疵,应立即用刀具去除发泡外皮,利用其骨架重新发泡。
5.拿出工件后,应对可修复性瑕疵予以补料修复,同时,进行从涂脱模剂开始的下一循环的工序。
N/A 自检、专检室温冷却1. 将取出的工件,平稳地放在开放的工作台上。