第二章 常用合金铸件的生产PPT课件
第二章常用合金铸件的生产

各种管件
第二章常用合金铸件的生产
螺丝扳手、减速器壳、转向节壳、制动器、曲 轴、凸轮轴、连杆、万向接头
第二章常用合金铸件的生产
三、球墨铸铁 向出炉的铁水中加入球化剂和孕育剂而得到的
球状石墨铸铁。 1.球墨铸铁的组织和性能 强度和韧性高; 可热处理(退火、正火、调质、高频淬火、等
河南巩县铁生沟西汉铁镢
西汉铁镢金相照片
第二章常用合金铸件的生产
柴油机汽油机曲轴 磨床铣床车床的主轴
第二章常用合金铸件的生产
阀门
第二章常用合金铸件的生产
汽车拖拉机传动齿轮
第二章常用合金铸件的生产
球墨铸铁的牌号:QT+两组数字
表2-5 球墨铸铁的主要牌号、力学性能和用途举例
第二章常用合金铸件的生产
-
图 2 15 黑 心 可 锻 铸 铁
第二章常用合金铸件的生产
应用:可锻铸铁通常用于制造形状复杂、 承受冲击载荷的薄壁小件。这些小件若用一 般铸钢制造困难较大;若用球墨铸铁,质量 上又难保证。
工艺:缓慢加热到920~980℃的高温, 保温10~20h。石墨化退火的总周期一般为 40~70h。可锻铸铁的生产过程复杂,退火周 期长,能源耗费大,铸件的成本较高。
第二章常用合金铸件的生产
二、可锻铸铁
可锻铸铁又称玛铁(钢)。它是将 白口铸铁经石墨化退火而成的一种铸铁。 抗拉强度得到显著提高,且有着相当高 的塑性与韧性(但不可锻)。 种类:黑心可锻铸铁(铁素体基体, KTH,强度、硬度较珠光体可锻铸铁 低。 )
珠光体可锻铸铁
白心可锻铸铁
第二章常用合金铸件的生产
第二章常用合金铸件的生产
(2)冷却速度 冷却速度越慢,石墨析出越多、越 粗大;反之,石墨的析出受到抑制。 影响冷却速度的因素:铸型材料、 铸件的壁厚。
金属工艺学2
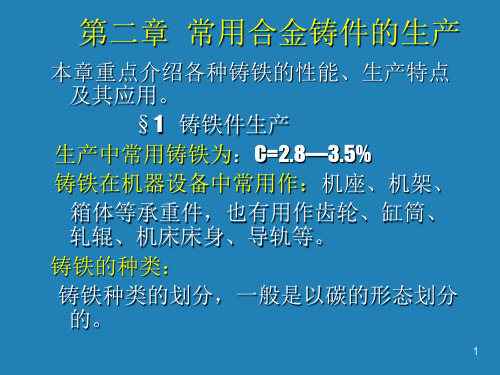
§2 铸钢件生产 铸钢件的生产比铸铁生产要求更严格, 这是因为铸钢的铸造工艺性较差,热裂、冷 裂倾向大且成分要求严格。
一. 铸钢的类别和性能 类别:铸造碳素钢和铸造合金钢。
铸钢不仅强度高,并有优良的塑性和韧性, 因此适于制造形状复杂、强度和韧性要求都高 的零件。
14
性能:
从表中的数值可见:铸钢的综
抗拉强度一般为400~600Mpa,最高可
达900Mpa;伸长率一般为2℅~10℅,最高可达
18℅
9
球墨铸铁兼有接近灰铸铁的优良铸造性能。
QT400 – 18
QT表示球铁
后面两组数字的含义与可锻铸铁相同
10
取代部分可锻铸铁、铸钢件,也取代部 分负荷较重但受冲击不大的铸钢件。 2. 生产特点:
与铸造灰口铁相比有如下特点。
RuT-400
RuT表示蠕墨铸铁
抗拉强度大于400松倾向比 球墨铸铁小,铸造工艺简便。
2. 应用 力学性能高,导热性和耐热性优良,可制造大型 柴油机气缸盖、制动盖、钢锭模、金属型等。
断面敏感性小,铸造性能好,可用于制造形状 复杂的大铸件,如重型机床和大型柴油机机体。
铸钢件的热处理----铸造后都应按工艺要求进行 热处理。常见的热处理为退火和回火。 标注代号: ZG19Mn12Si7 ( zh . H ) 回火代号 铸钢牌号 正火代号
18
§3 铜、铝合金铸件生产 一 . 铸造铜合金 1. 铸造铜合金的种类及应用:
黄铜
以锌为主加元素的铜合金(硅、锰、铝、铅 ),随锌含量增加,强度和塑性显著提高,大 于47℅后显著降低
900---980℃
P
770℃
F
650℃
8
三 . 球墨铸铁
常用铸造合金及其熔炼(精选优秀)PPT
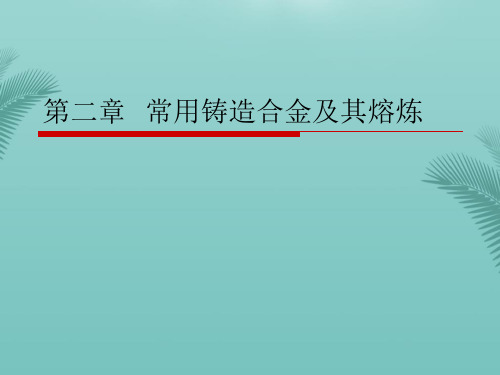
珠光体球墨铸铁和45号锻钢的力学性能比较
性能 抗拉强度b/MPa 屈服强度0.2/MPa 屈强比0.2/b
伸长率δ(%) 疲劳强度
45号锻钢(正火) 珠光体球墨铸铁(正火)
690
815
410
640
0.59
0.785
26
3
150
155
(有缺口试样)-1/MPa
硬 度/HBS
目的:改善切削性能。
3)表面淬火
提高某些铸件的表面硬度; 中、高频感应加热、火焰加热。
例如,机床导轨用高(中)频 淬火时,表面基体淬硬层深度 约为1.1~2.5(3~4)mm,硬 度HRC50。
5、灰口铸铁的应用
机床床身、底座、电器壳体、缸 体、泵体、盖、手轮等受力不大、 耐磨、减震零件。 变速箱体
缺陷:球墨铸铁件容易出现皮下气孔 ZG230-450齿圈的铸造工艺方案:
高生产率、低成本地熔炼出预定成分和温度的铁液。
硅为主要元素的多元合金。 目的:改善切削性能。
如汽车、拖拉机底盘零件,阀体和阀盖,机油泵齿轮; 蠕化处理:是将蠕化剂放入经过预热的堤坝或铁液包内的一侧,从另一侧冲入铁液,利用高温铁液将蠕化剂熔化的过程。
3、影响性能的因素 :
控制铸铁的组织和性能,必须控制铸 铁的石墨化程度。
主要影响因素:化学成分和冷却速度。
(1)化学成分
碳和硅:碳和硅是铸铁中最主要的元 素,对铸铁的组织和性能起着决定性的 影响。
碳是形成石墨和促进石墨化的元素。 硅是强烈促进石墨化的元素。 硫严重阻碍石墨化的元素。 锰能抵消硫的有害作用,故属于有
益元素。但过多则阻碍石墨化。 铸铁中锰的含量一般为0.6%~1.2%。 磷的影响不显著。
常用合金铸件的生产课件

常用合金铸件的生产课件1. 引言本课件主要介绍常用合金铸件的生产过程,包括铸造工艺、模具设计、合金材料选择、铸造过程控制等方面内容。
通过学习本课件,您将了解到合金铸件的生产过程以及如何进行有效的控制和优化。
2. 铸造工艺铸造是制造合金铸件的常用工艺之一,主要包括砂型铸造、金属型铸造和压铸等。
下面我们将对这几种常用的铸造工艺进行介绍。
2.1 砂型铸造砂型铸造是一种常用的铸造工艺,它使用砂型作为铸件的模具。
砂型铸造可以用于生产各种形状和大小的铸件,成本较低且适用于小批量生产。
砂型铸造的主要步骤包括模具设计、模具制造、砂型制备、浇注、冷却、清理等。
2.2 金属型铸造金属型铸造是使用金属模具进行铸造的工艺,主要适用于中小型铸件的生产。
相比于砂型铸造,金属型铸造的成本较高,但能够获得更高的精度和表面质量。
金属型铸造的主要步骤包括模具设计和制造、熔炼铸造金属、填充模腔、冷却、脱模等。
2.3 压铸压铸是一种高效的铸造工艺,通过将熔融金属注入压铸机中,利用高压和快速冷却来形成铸件。
压铸可以实现高生产效率和精确度,适用于大批量生产。
压铸的主要步骤包括模具设计和制造、熔炼金属、注射填充、压力维持、冷却脱模等。
3. 模具设计模具设计是铸件生产过程中的重要环节,它直接影响到铸件的质量和成本。
好的模具设计能够提高铸件的精度和表面质量,减少材料使用,降低生产成本。
以下是模具设计的一些关键点。
3.1 模具结构设计模具结构设计应考虑到铸件的形状、尺寸和特殊要求等因素。
合理的模具结构能够方便铸件的填充和冷却,提高铸件质量。
3.2 模具材料选择模具材料应具有高热传导性、良好的耐磨性和耐热性。
常用的模具材料有铸铁、钢等。
3.3 模具制造工艺模具制造工艺包括模具加工、热处理、组装等步骤。
模具加工的精度和质量直接决定了铸件的精度和表面质量。
4. 合金材料选择合金材料的选择在铸件生产过程中起着关键作用。
不同的合金具有不同的性能和应用范围,合适的合金选择可以提高铸件的强度、抗腐蚀性和耐磨性。
(精选)常用合金铸件的生产
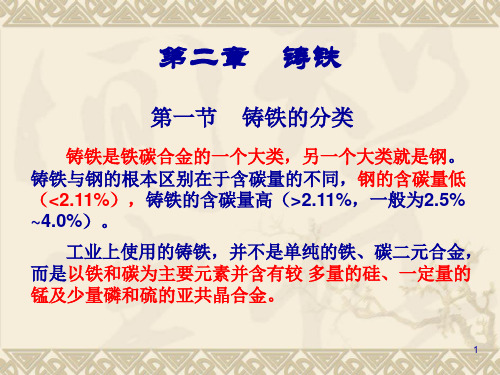
HT250 细珠光体 HT300 细珠光体 HT350 细珠光体
较细片状 薄壁缸体、缸盖、机床立柱、横梁、床身、箱体、活塞等
细小片状 细小片状
机床导轨,受力较大的床身、立柱,液压阀体,大型发动机 缸体、缸盖,蜗轮,泵壳等
机床导轨、工作台,水泵缸体、阀体、凸轮,大型发动机缸 体、缸盖、衬套,需要表面淬火的铸铁件等
6.缺口敏感性小,石墨已在金属基体上形成大量的缺 口,故外来缺口影响甚微。
6
二、灰铸铁的组织
灰铸铁按基体组织可分为铁素体灰铸铁、铁素体+珠 光体灰铸铁、珠光体灰铸铁三种。
1.铁素体基体灰铸铁 铁素体基体的灰铸铁的石墨 片粗大、量多,几乎所有的碳都 转变成了石墨,石墨片对基体的 割裂作用大,故力学性能差,应 用较少。
按铸铁中碳的存在形态(反映在截面颜色),可将 铸铁分为灰口铸铁、白口铸铁、麻口铸铁三类。
2
铸铁
灰口铸铁:大量的碳以游离态(石墨)存在,断口 呈灰黑色,应用最广。
白口铸铁:大量的碳以化合态(Fe3C)存在,断口 呈银白色,既硬又脆,难以进行机械加 工,很少用于制造零件。
麻口铸铁:大部分碳化合态存在,少量以石墨形态 存在,断口为银白色基体散布着一些黑 点,既硬又脆,难以加工,极少用。
7
2.铁素体+珠光体基体灰铸铁 珠光体与铁素体混合基体上分 布着较粗大的石墨,故强度较低, 铸造性能、切削性能、减振性优于 珠光体基体灰铸铁,适用于一般机 件,如齿轮箱等,是应用最广的灰 铸铁。
3.珠光体基体灰铸铁
珠光体基体上分布着均匀、细小的石墨片,对基体 的割裂作用较轻,故强度、硬度较高,多用于重要机件, 如床身等。
9
四、灰铸铁的牌号和应用
与钢不同,灰铸铁的牌号不能用化学成分表示,而 是用力学性能来表示。
《铸件生产》课件

通过分析质量问题的根本原因,采取有效 的预防措施,避免类似问题的再次发生。
对不合格品进行标识、隔离,并采取返工 、降级、报废等处置措施。
质量信息反馈
质量事故处理
及时收集和分析质量信息,向相关部门和 人员反馈,促进质量持续改进。
对于重大质量事故,应按照相关规定进行 调查和处理,追究责任并采取纠正措施。
详细描述
熔炼设备主要包括电弧炉、感应炉、冲天炉等,它们能够将各种金属材料如铁、 铜、铝等熔化为液态,以便进行铸造。熔炼设备在铸造生产中起着至关重要的作 用,其性能和操作方式直接影响着熔融金属的质量和铸造产品的质量。
造型设备
总结词
造型设备是铸造生产中的重要环节,用于制作铸型和芯型,以形成铸件的外形 和内部结构。
优化铸造工艺
通过改进铸造工艺参数和流程,减少生产时间和 成本,提高生产效率。
信息化管理
利用信息化技术实现生产过程的实时监控和数据 化管理,提高生产协同和管理效率。
ABCD
引入自动化设备
采用自动化设备替代传统手工操作,实现快速、 高效的生产。
人才培养与引进
加强铸造技术人才的培养和引进,提高企业整体 技术水平和创新能力。
和可靠性。
材料选择与成本控制
根据产品要求选择合适的材料,既要满足使用性 能要求,又要考虑成本因素。
材料成本占铸件生产总成本的比重较大,因此合 理选择材料能够有效降低生产成本。
考虑材料的加工性能和回收再利用性,以提高生 产效率和降低能耗。
03
铸件生产设备
熔炼设备
总结词
熔炼设备是铸造生产中的重要组成部分,用于将金属材料熔化为液态,为后续的 铸造过程提供所需的熔融金属。
案例二
案例三
金属工艺学铸造第二章

4.牌号 4.牌号 :
KTH数字1 数字 数字2 KTH数字1—数字2 数字
KT:表示可锻铸铁, KT:表示可锻铸铁, H:表示黑心 Z:表示珠光体 数字1 数字2 数字1:表示最低抗拉强度 数字2 :表示最低伸长率
5.生产方式:先铸出白口坯件——清理坯件 清理坯件——石墨化退火 5.生产方式:先铸出白口坯件 生产方式 清理坯件 石墨化退火
(一)灰铸铁(灰口铸铁) 灰铸铁(灰口铸铁) 灰铸铁是指具有片状石墨的铸铁 • 应用最广,占铸铁总产量80%以上。 应用最广,占铸铁总产量80%以上。 80%以上 • 灰铸铁的组织: 灰铸铁的组织: 片状石墨+ 片状石墨+金属基体 • 几点注意: 几点注意: 铸铁含碳量; 铸铁含碳量; 状态图上的位置; 状态图上的位置; 铸铁的常温组织。 铸铁的常温组织。
(二)可锻铸铁 (玛铁、玛钢) 玛铁、玛钢)
由白口铸铁经石墨化退火而成的一种铸铁 1.组织 团絮状石墨+ 组织: 1.组织:团絮状石墨+金属基体 2.机械性能 石墨割裂作用减小,抗拉强度显著提高。 机械性能: 2.机械性能:石墨割裂作用减小,抗拉强度显著提高。 σb=300~400 MPa,最高可达700 MPa。 =300~ MPa,最高可达 最高可达700 MPa。 但不能用于锻造。 (δ≤12%,aK≤30 J/cm2,)但不能用于锻造。 ≤12%,a 3.分类 分类: 3.分类:
(四)蠕墨铸铁 1.组织:蠕虫状石墨+ 1.组织:蠕虫状石墨+金属基体 组织 2.蠕墨铸铁的性能 2.蠕墨铸铁的性能 • 力学性能介于基体相同的灰铸铁和球墨铸铁之间; 力学性能介于基体相同的灰铸铁和球墨铸铁之间; b=360~ 优于灰铸铁, 抗拉强度 σb=360~440MPa, 优于灰铸铁,塑性和 b=360 韧性δ=1.5% 4.5%) =1.5%~ 韧性δ=1.5%~4.5%) =1.5% • • • • • 强度和韧性不如球铁; 强度和韧性不如球铁; 铸造性能接近灰铸铁;缩孔、缩松倾向比球墨铸铁小, 铸造性能接近灰铸铁;缩孔、缩松倾向比球墨铸铁小,故 铸造工艺较简便; 铸造工艺较简便; 耐磨性优于孕育铸铁及高磷耐磨铸铁; 耐磨性优于孕育铸铁及高磷耐磨铸铁; 导热性优于球铁,抗氧化性较其它铸铁均高; 导热性优于球铁,抗氧化性较其它铸铁均高; 断面敏感性较灰铸铁小,厚大截面上的性能较为均匀。 断面敏感性较灰铸铁小,厚大截面上的性能较为均匀。
- 1、下载文档前请自行甄别文档内容的完整性,平台不提供额外的编辑、内容补充、找答案等附加服务。
- 2、"仅部分预览"的文档,不可在线预览部分如存在完整性等问题,可反馈申请退款(可完整预览的文档不适用该条件!)。
- 3、如文档侵犯您的权益,请联系客服反馈,我们会尽快为您处理(人工客服工作时间:9:00-18:30)。
• 三、可锻铸铁 • 可锻铸铁是将白口铸铁坯件经长时间高温退火而得到的
一种具有较高塑性和韧性的铸铁。 • 1.白口铸件的生产 • 为了获得合格的可锻铸铁件,关键是必须保证浇铸出的
铸件坯料组织全部是白口,否则,即使铸件组织中有少量 的片状石墨,也会影响退火后可锻铸铁件的组织和性能。 为此,出炉的铁水必须具备低碳、低硅、低硫和低磷。例 如,KTH350—10的化学成分为Wc=2.4%—2.8%,Wsi= 0.9%—1.4%,Ws<0.18%,Wp<Z0.2%。 • 用来制造可锻铸铁的白口铸件,熔点高、结晶间隔大,且 凝固收缩率高,铸件易产生浇不足、冷隔、缩孔、缩松、 裂纹等缺陷。 • 可锻铸铁只适用于生产薄壁小件。壁厚不超过25mm,否 则铸造时难以获得白口铸铁组织。另外铸件太厚时,使退 火时间过长。
• 普通灰铸铁的主要缺点是壁厚敏感性较大(表6— 1),铸件壁愈大时,石墨片愈粗大,强度愈低。 当截面增加到1OOmm时,强度可下降50%左右。 故普通灰铸铁不宜制造壁厚较大的铸件,仅适用 于制造受力较小、形状复杂的中小型铸件。
• 2.孕育铸铁
• 为了进一步提高灰铸铁的力学性能,在生产上常采用孕育 处理(也称变质处理)。其方法是:浇注前,往铁水中加入 一定量的孕育剂(硅铁或硅钙合金)造成人为晶核,以改变 铁水的结晶条件,使其获得细晶粒的珠光体基体组织和均 匀细小片状的石墨。这种方法处理后的铸铁叫“孕育铸铁” 或“变质铸铁”,也称高强度铸铁。
第二章 常用合金铸件的生产
•
第一节 铸铁件的生产
• 一、灰铸铁
• 按照铁水处理方法的不同,灰铸铁可分为普通灰 铸铁和孕育铸铁两大类。
• 1.普通灰铸铁
• 指出炉铁水不经任何处理而制成的铸铁,如 HTl00和HT150均属这类铸铁。普通灰铸铁也称 低强度灰铸铁,其碳、硅含量较高(3.0%~3.7%C, 1.8%~2.4%Si)。
• 孕育铸铁适用于静载荷下要求较高强度、高耐磨 性或高气密性的铸件,特别是厚大铸件,如机床 床身、发动机气缸体等。
• 3.灰铸铁的铸造工艺特点
• 灰铸铁通常是在冲天炉内熔炼,且大多不 需进行炉前处理直接浇注即可。灰铸铁的 铸造性能优良,便于制出薄而复杂的铸件, 一般也不需设置冒口和冷铁,使铸造工艺 简化。
• 2.白口铸铁件的石墨化退火
• 石墨化退火是制造可锻铁的主要过程,图6-5为黑心可 锻铸铁的退火工艺曲线。其方法是将清理后的白口坯料叠 放在退火箱中,将箱盖用泥封好后送入退火箱中,缓慢加 热到900-980℃,保温15h左右,使渗碳体分解为奥氏体 加团絮状石墨。然后缓慢冷却,随温度的降低,过饱和的 碳自奥氏体内逐渐析出,团絮状石墨不断长大。当温度降 到共析转变温度范围(750~720℃)并以缓慢速度(3-5℃/ h)冷却时,奥氏体直接转化为铁素体和石墨,最 终获得铁 素体的黑心可锻铸铁。如果在通过共析转变时冷却速度较 快,则奥氏体转变为珠光体和石墨,最终获得珠光体可锻 铸铁。
• 4.球墨铸铁的铸造工艺特点 • 球墨铸铁的凝固过程、铸造性能和灰铸铁有明显的不同,
因而铸造工艺也不同。 • (1)流动性比灰铸铁差。因为球化和孕育处理,使铁水温度
大大下降。因此,球墨铸铁需要较高的浇注温度和较大的 浇口尺寸。 • (2)收缩较灰铸铁大。其主要原因是:球铁为糊状凝固特征, 球铁含碳量高,近共晶成分,凝固收缩率低,但缩孔、缩 松倾向较大。球铁在浇注后的一个时期内,截面上存在相 当宽的液固共存的同时凝固区,凝固后的外壳强度甚低如 图6-4(a),而球状石墨析出时的膨胀值却很大(每析出1% 的石墨,体积增加2%)。如果铸型的刚度不够,铸件的外 壳将向外胀大,造成金属液的不足,于是在铸件最后凝固 的部位产生缩孔和缩松如图6-4(a)。为防止上述缺陷,可 采取以下措施。 • ① 在铸件热节部位安置冒口或冷铁,对铸件进行补缩。 • ② 增加铸型刚度,防止铸件外形扩大。如增加型砂紧实 度,采用干型或水玻璃快干型,保证砂箱有足够的刚度, 并使砂箱间牢固地夹紧。
• 孕育处理后的铁水应尽快浇完,否则孕育效果衰退。
• 孕育铸铁的力学性能,特别是强度、硬度比普通 灰铸铁有显著提高。其抗拉强度为250~400MPa、 HB=170~270,含碳愈少、石墨愈细小,强度、 硬度愈高。由于孕育铸铁的石墨仍为片状,本质 仍属于灰铸铁,所以其塑性、韧性仍然很低。
• 孕育铸铁的另一优点是,组织和性能的均匀性较 高,壁厚敏感性很小;冷却速度对其组织和性能 的影响较小,这就使得在铸件的厚大截面上的性 能较均匀,如图6-1所示。
• 为了取得较好的孕育效果,必须从以下条件入手:
• 碳、硅含量均低的原始铁水(2.7%一3.3%C,1%一2%Si)
• 废钢加入量25%一50%
• 铁水出炉温度 约为1400~1450℃
• 孕育剂含硅量为75%的硅铁,块度为3一lOmm,硅铁的 加入量为铁水重量的0.25%—0.6%(厚壁铸件取下限)。
• 由于铁水经球化和孕育处理温度要降低50—1OO℃,为 防止浇注温度过低,出炉的铁水温度必须高达1400℃以上。
• 2.选择恰当的球化剂和孕育剂 这是制造 球铁的关键,必须严格掌握。
• 球化剂的作用是使石墨结晶时呈球状析出。 • 球化剂:镁、稀土镁合金。 • 孕育剂:含硅量75%的硅铁 • 球化处理方法 冲入法,如图6-2所示 • 型内球化法,如图6-3所示。
• 灰铸铁的浇注温度较低(1200~1350℃), 因而对型砂的要求比铸钢低,中小型铸件 多采用经济、简便的湿型来铸造。
• 二、球墨铸铁
• 球墨铸铁是对一定成分的铸铁铁水进行球化和孕育处理 后得到的。与灰铸铁相比,球墨铸铁件的生产有如下特点。
• 1.严格控制原铁水的化学成分
• 制造球墨铸铁所用的铁水与灰铸铁原则相同,但成分要 求较严格,其硫含量愈低愈好.硫应控制在0.07%以下。 磷使球墨铸铁的塑性,韧性急剧降低,且易冷裂,因此, 含磷量应小于0.1%。有时还要求低的含锰量,低锰、低 磷可提高球墨铸铁的塑性和韧性。此外,铁水含碳量应高 些(一般为3.6%~4.0%),以改善铸造性能和球化效果。