现场管理与改善-IE手法的活用(PPT 167页)
合集下载
现场管理与改善-IE手法的活用(续)(PPT 88页)

加工數、工順序、檢查數、 效率、產出率
8. 發現製品變異情形
品質數據、變異、數量
9. 發現試驗 檢查及品質情形
10. 發現報廢與重加工
11. 發現變動品質成本
成本
2019/12/30 1H2o. 發Ku現ei現場抱怨
工作容易度、滿意度、安全
Page21
製品工程分析記入項目例
UNION POWER
廠商 交貨
2019/12/30 Ho Kuei
Page13
流程分析制作與實例
UNION POWER
3.流程中不良或缺失的發掘
不合理
不正常
人員 蓋單的人太多
機械 設備
材料
只要復寫即可,卻 要填一大堆表
表單多浪費多
把異常當正常管理,不必凡 事找到廠長級 沒有電腦化,趕不上時代
表單不良
方法 計測 環境
作業者流程分析:以作業者作業的過程為對象主體的分 析法,通常係為發掘或改善以人為主 的作業過程,應用上都是對某一工作 (工程)為之,但有別於動作分析。
2019/12/30 Ho Kuei
Page19
UNION POWER
四、流程分析的用途分類
聯合工程分析:涉及「人與機」或「人與人」的 作業。
○人機(配合)分析:涉及人與機械設備同時配合作業。
2019/12/30 Ho Kuei
Page10
三、流程分析圖的製作與應用
UNION POWER
要點五 研究分析,問題發覺: 針對 1. 流程及順序
2. 分解的次一層級要素
研究分析是否合理恰當、可否改善
(可用大字報方式、集合眾智、收錄問題)
應用的方法,例如: 工作簡化、動作與時間研究、運搬與布置、動
IE改善实战技法培训教材(PPT 67张)

1.工序内的业务分工,责任区分的范围是否合理? 2.是否可以减少生产转换次数,或者是否可以减少 作业准备时间? 3.是否可以改变生产方式,流程状态?
1.改变形状会怎么样?导角、退刀槽、抓取容易程度; 2.改变精度会怎么样?完成公差,结合比率,完成面等 3.改变表面处理或喷涂标准怎么样? 4.对材料、部件、产品能否进行标准化?
和返工
IE七大手法之一 —— 动改法 动改法
意义: • 动改法又称动作分析法,是對人的作業動作進行 細微的分析,省去不合理的和浪費的動作,制定 出輕松、安全、正確、高效率的動作序,形成最 經濟的作業方法的一種分析技術。
应用范围: • 1.生活上个人及家庭内之工作改善. • 2.工厂或办公室,关于人体工作方面的改善.
就算增加检验工序,也不能提高产品质量! 检查工序在哪里、用什么方法、怎样反馈?
减少滞留量、次数、时间
分析能力,研究工序能力的平衡化; 制订标准日程,提高日程管理的精确程度; 提高库存管理的精度; 考虑改善搬运系统; 向流水作业方向的转换;
改善方法
•
•
《工序改善检查表》
《工序改善检查表》
在基本分析开始之前为了掌握调查程度或分析确认研讨 改善的不足时使用。
永远有个更好的方法!
IE的核心理念
大野耐一认为:
IE就是MIE(Money Industrial Engineering) = 赚钱的工业工程。
IE的核心理念就是“持续改善”
制造现场的七大浪费
• 什么是浪费?
• 浪费 Muda : 指耗用了资源但不创造价值的一切活动。
大野耐一列举了七大浪费……
考虑变更工序组合
组合:考虑将分离的工序合在一起; 分离:将结合的工序进行分解,达到分工化; 替换:考虑交替前后工序的顺序; 并行:考虑设备、作业内容的并行,同步作业
1.改变形状会怎么样?导角、退刀槽、抓取容易程度; 2.改变精度会怎么样?完成公差,结合比率,完成面等 3.改变表面处理或喷涂标准怎么样? 4.对材料、部件、产品能否进行标准化?
和返工
IE七大手法之一 —— 动改法 动改法
意义: • 动改法又称动作分析法,是對人的作業動作進行 細微的分析,省去不合理的和浪費的動作,制定 出輕松、安全、正確、高效率的動作序,形成最 經濟的作業方法的一種分析技術。
应用范围: • 1.生活上个人及家庭内之工作改善. • 2.工厂或办公室,关于人体工作方面的改善.
就算增加检验工序,也不能提高产品质量! 检查工序在哪里、用什么方法、怎样反馈?
减少滞留量、次数、时间
分析能力,研究工序能力的平衡化; 制订标准日程,提高日程管理的精确程度; 提高库存管理的精度; 考虑改善搬运系统; 向流水作业方向的转换;
改善方法
•
•
《工序改善检查表》
《工序改善检查表》
在基本分析开始之前为了掌握调查程度或分析确认研讨 改善的不足时使用。
永远有个更好的方法!
IE的核心理念
大野耐一认为:
IE就是MIE(Money Industrial Engineering) = 赚钱的工业工程。
IE的核心理念就是“持续改善”
制造现场的七大浪费
• 什么是浪费?
• 浪费 Muda : 指耗用了资源但不创造价值的一切活动。
大野耐一列举了七大浪费……
考虑变更工序组合
组合:考虑将分离的工序合在一起; 分离:将结合的工序进行分解,达到分工化; 替换:考虑交替前后工序的顺序; 并行:考虑设备、作业内容的并行,同步作业
现场IE改善(PPT47张)
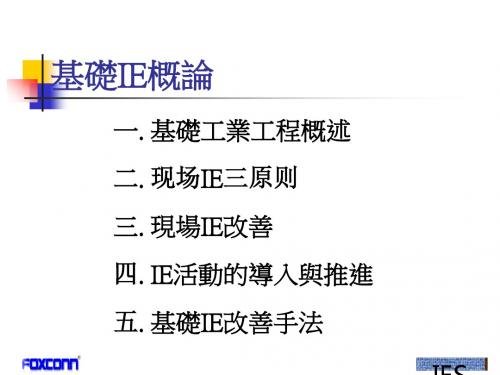
5、改善瓶颈岗位
(1)改善的4大原則
1)减少动作次数 2)同时使用双手 3)缩短移动距离 4)使动作变得轻松
(2) IE动作改善的4原则
ECRS原则 1、Eliminate 2、Combine 3、Rearrange 4、Simplify
——取消 ——合并 ——重排 ——简化
(3)ECRS法运用图示简介
四.基礎IE改善手法 1﹒何謂基礎IE手法
“基礎IE手法是以人的活動為中心 ﹐以事實為依據﹐用科學的分析方法對 生產系統進行觀察﹑記錄﹑分析﹐並對 系統問題進行合理化改善﹐最后對結果 進行標準化的方法”
IE手法一﹕動作改善法(作業標準化)
作業員須每隔28秒轉 身一次﹐取身后的膠 帶﹐這樣每小時須做 150次轉身無效轉身取 膠帶動作
3600<H> 节拍<TT>= 目标产量
二. 现场IE改善<3>
2.现场IE三原则 a、划节距线<25-30cm>,根据标准工时 调整拉速节拍<TT>。 b、保证每个节距有一个产品。 c、每个岗位不准堆积。
生产线平衡计算
平衡率=
(各工序的作业时间总和) * 100% 瓶颈岗位时间*人数<工位数>
改变观念
1、观念改变 2、行动改变 则 则 行动改变 习惯改变
3、习惯改变
则
命运改变
团队与集团的区别
集体
目标不一致
团队
目标一致
Q&A time
本課程到此告一段落﹐請大家就有疑問 的部分踴躍提問﹐謝謝﹗
• • • • • • • • • • • • • • • • • • • • • • • • • • • • • • • • • • • • • • • • • • • • • • • • • • • • • • • • • • • • • • • • • • • • • • • • • • • • • • • • • • • • • • • • • • • • • • • • • • • •
工业工程(ie)与现场改善.ppt

作业环境
整理整顿是否有效进行? 不良品放置是否容易区分? 各种标识是否明确? ……
30 2020/1/27
新方法展开
除去不要的项目明细。 尽可能的连接项目明细。 以更好的顺序编排作业。 对必要的项目简单化。 确保作业更安全适意。 借助协作的力量。 纪录新方法的项目明细。
4、尽量使用一个动作 就能控制机器的机构。
1、利用固定夹具 1、利用重力
来固定对象。
和机械力取
2、简单的作业或 出和运送材 需要用力气得作 料。
业。使用脚部来 2、机器的操
控制的机器。
作位置,设
3、考虑两手可以 置在身体最 同时作业的夹具。 容易进行的
部位。
1、利用夹具或导向装置,限制其运 动线路。
常用改善技术
5 2020/1/27
常用改善技术
一般性
5W2H法 脑力激荡法
QC7手法
层别法
柏拉图法
法 直方图法 管制图法
IE7手法
流程分析法 动作分析法
工作抽查法 人机配置法
愚巧法
比较法
特性要因图法 查检表
散步图
动作经济原则法
时间研究
6 2020/1/27
常用现场改善手法
解决问题的7步法
保留有效动作,减少辅助动作和无效动作
有效动作要素: 伸手、握取、移物、放手、装配、拆卸、使用 辅助动作要素: 寻找、选择、检查、持住、对准、定位 无效动作要素: 休息、迟延、故延、思考
动作经济原则
29 2020/1/27
项目明细设问(三)——作业安 全、环境适宜性
作业安全
存在安全隐患吗? 有否正确使用安全装置? ……
Method(方法、配置、设计)
整理整顿是否有效进行? 不良品放置是否容易区分? 各种标识是否明确? ……
30 2020/1/27
新方法展开
除去不要的项目明细。 尽可能的连接项目明细。 以更好的顺序编排作业。 对必要的项目简单化。 确保作业更安全适意。 借助协作的力量。 纪录新方法的项目明细。
4、尽量使用一个动作 就能控制机器的机构。
1、利用固定夹具 1、利用重力
来固定对象。
和机械力取
2、简单的作业或 出和运送材 需要用力气得作 料。
业。使用脚部来 2、机器的操
控制的机器。
作位置,设
3、考虑两手可以 置在身体最 同时作业的夹具。 容易进行的
部位。
1、利用夹具或导向装置,限制其运 动线路。
常用改善技术
5 2020/1/27
常用改善技术
一般性
5W2H法 脑力激荡法
QC7手法
层别法
柏拉图法
法 直方图法 管制图法
IE7手法
流程分析法 动作分析法
工作抽查法 人机配置法
愚巧法
比较法
特性要因图法 查检表
散步图
动作经济原则法
时间研究
6 2020/1/27
常用现场改善手法
解决问题的7步法
保留有效动作,减少辅助动作和无效动作
有效动作要素: 伸手、握取、移物、放手、装配、拆卸、使用 辅助动作要素: 寻找、选择、检查、持住、对准、定位 无效动作要素: 休息、迟延、故延、思考
动作经济原则
29 2020/1/27
项目明细设问(三)——作业安 全、环境适宜性
作业安全
存在安全隐患吗? 有否正确使用安全装置? ……
Method(方法、配置、设计)
现场改善IE七大手法培训教材(PPT 40张)

疲劳使工作更为舒适、更有效率,不要蛮干。
目的:以最小的动作投入,达到最高的工作效果。
动作经济的四项基本原则
1、动作简化原则:减少动作数量 2、省力动作原则:追求动作平衡
3、省时动作原则:缩短动作移动距离
4、动作舒适原则:使动作保持轻松自然的节奏
3、流程法
又称为工序分析/工程分析法:对工作流程加以
改善前
改善后
36
7、工作抽查法
工作抽查法是指应用统计学上的抽样原理来 研究工作中人员与机器设备的活动情形,它是一
个了解事实最有效的工具之一。它可在最短的时
间和最低的成本之下获得有关人与设备之间的有 用信息。
• 意义: 利用抽样原理,以推测人或物之作业真象,以利进行分析改 善. • 应用范围: 1.办公室人员工作时间所占之百分率. 2.机器设备之维修百分率或停机百分率. 3.现场操作人员从事有生产性工作之百分率. 4.决定标准工时之宽放时间百分率. 5.用以决定工作之标准工时. 6.商店顾客类别或消费金额或光顾时刻次数等之分配比例资料. 7.其它可应用抽样调查以收集资料的场合.
6、双手法
双手法的运用 1.研究双手的动作,以求其互 相平衡. 2.显现出伸手找寻,以及笨拙 而无效的动作. 3.发现工具、物料、设备等 不合适的位置. 4.改善工作布置. 5.协助操作技术的训练.
改善案例
1)要双手操作。 问题点:网印员将物料放左边,印完后放到右边,一只手将网板托 起,只能动一只手; 改善对策:将材料按左右分开两边放,将网印板设计为自动弹起式 ,双手同时将左右待印部件放到网板下。
现场改善&IE七大手 法
日期:2013年11月12日
课程大纲 第一部分:生产现场问题分析 第二部分:现场八大浪费 第三部分:现场改善 第四部分:IE现场改善七手法
《IE现场优化改善》课件

展望
未来企业应进一步拓展IE现场优化改 善的领域,加强与其他管理方法的融 合,实现更高效、更灵活、更智能的 生产模式。
谢谢观看
《IE现场优化改善》PPT课件
目录
• IE现场优化改善概述 • IE现场优化改善方法 • IE现场优化改善案例分析 • IE现场优化改善的未来发展 • 结论与建议
01
IE现场优化改善概述
定义与目标
定义
IE现场优化改善是一种通过系统地分析和改进生产现场的布局、操作流程、设 备及工装夹具等,以提高生产效率、降低成本、提升质量的管理方法。
费,提升产品质量和客户满意度。
动作分析
01
动作分析的定义
通过对作业过程中动作的分析和研究,寻找最优的动作方法和顺序。
02
动作分析的工具
动素分析、动作经济原则。
03
动作分析在IE现场优化中的应用
通过动作分析,消除多余和无效的动作,提高作业效率和生产线的平衡
,降低成本和浪费,提升产品质量和客户满意度。
制定标准、宣传培训、执行落实、检查考 核、持续改进。
通过5S管理,优化现场布局,提高作业效 率和生产线的平衡,减少浪费和不良品, 保障员工安全和健康。
流程优化
流程优化的定义
对现有流程进行分析、改进和优化,提高流程效率和效果。
流程优化的原则
明确目标、关注瓶颈、整体优化、持续改进。
流程优化的方法
流程图绘制、流程分析、流程改进、流程再造。
时间研究
时间研究的定义
通过对作业过程中所需时间的分析和研究,制定标准作业时间。
时间研究的工具
时间测量表、工作抽样。
时间研究在IE现场优化中的应用
通过时间研究,制定合理的生产计划和排程,提高生产效率和产能,降低成本和浪费,提 升产品质量和客户满意度。
未来企业应进一步拓展IE现场优化改 善的领域,加强与其他管理方法的融 合,实现更高效、更灵活、更智能的 生产模式。
谢谢观看
《IE现场优化改善》PPT课件
目录
• IE现场优化改善概述 • IE现场优化改善方法 • IE现场优化改善案例分析 • IE现场优化改善的未来发展 • 结论与建议
01
IE现场优化改善概述
定义与目标
定义
IE现场优化改善是一种通过系统地分析和改进生产现场的布局、操作流程、设 备及工装夹具等,以提高生产效率、降低成本、提升质量的管理方法。
费,提升产品质量和客户满意度。
动作分析
01
动作分析的定义
通过对作业过程中动作的分析和研究,寻找最优的动作方法和顺序。
02
动作分析的工具
动素分析、动作经济原则。
03
动作分析在IE现场优化中的应用
通过动作分析,消除多余和无效的动作,提高作业效率和生产线的平衡
,降低成本和浪费,提升产品质量和客户满意度。
制定标准、宣传培训、执行落实、检查考 核、持续改进。
通过5S管理,优化现场布局,提高作业效 率和生产线的平衡,减少浪费和不良品, 保障员工安全和健康。
流程优化
流程优化的定义
对现有流程进行分析、改进和优化,提高流程效率和效果。
流程优化的原则
明确目标、关注瓶颈、整体优化、持续改进。
流程优化的方法
流程图绘制、流程分析、流程改进、流程再造。
时间研究
时间研究的定义
通过对作业过程中所需时间的分析和研究,制定标准作业时间。
时间研究的工具
时间测量表、工作抽样。
时间研究在IE现场优化中的应用
通过时间研究,制定合理的生产计划和排程,提高生产效率和产能,降低成本和浪费,提 升产品质量和客户满意度。
IE技术与现场改善培训课件

布置与线路剖析--线路图、线图
4.顺序剖析符号
基本符号
序号 符号名称 符号
符号含义
备注
1
操作
表示对作业对象进行加工,装配,合成,包装, 处理等
搬运、移
2
动
表示对作业对象进行搬运,运输,输送等;或作 业人员作业位置的变化
3
检验
表示对作业对象进行数量或质量检验,或对某种 质量检验可用
操作执行情况的检查
❖ 影片剖析〔录像观察剖析〕:用摄影机将各个操作
3.举措剖析目的
❖ 找出举措中的效果点以及重复、多余、糜费的举措 ❖ 制定高效、合理、简捷的作业方法 ❖ 设定最适宜举措的夹具以及举措范围的最正确规划 ❖ 用记号、图表记载举措之后,对举措顺序的说明变 ❖ 可以将举措细分处置,并判定其良好与否,有助于
• 定义:顺序剖析以整个作业进程为对象,研讨剖析一个完整的作业进程 作业,顺序能否合理,搬运能否太多,等候能否太长等,进一步改善义务
• 目的: • 取消不用要的、有潜在效果的顺序〔工艺、操作、举措〕 • 兼并一些过于细分或重复的义务 • 找出中止、等候、闲暇、白干的工时 • 掌握作业顺序,各工序的大约时间以及工序的平衡外形 • 改动局部操作顺序,以防止重复 • 调整规划,以节省搬运 • 重排和简化剩余的顺序,重新组织一个效率更高的顺序
对任务的顺序停止重新陈列 〔4〕简化〔Simplification〕 指任务内容、步骤、设备、工具的简化,亦指举措的简 化,人力、时间、费用的节省。
3.义务研讨的顺序
5.改造 6.设计新的义务顺序和义务方法 7.定时 8.确定所选择方法的义务量及有关的作业时间,并用作业 9.评价 10.评价经过改造和改良的新义务方法 11.依据预先设定的目的,评价新义务方法在本钱、义务
IE工业工程与现场改善.pptx
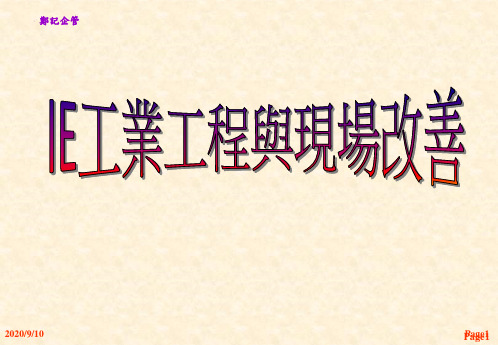
2. 問答:
(1)如此擺放您會放錯嗎?(請在“ □ ”內打“ˇ”作選
擇)
□會
□ 不會
(2) 您不會/會放錯的原因是什麼?
2020/9/10
Page18
鄭記企管 伍.1 IE手法說明 (防錯法/愚巧法)
3.防錯法 之
“三不” 構造原則
2020/9/10
Page19
鄭記企管 伍.1 IE手法說明 (防錯法/愚巧法)
(8)生產線平衡法
2020/9/10
Page10
鄭記企管
名稱
(1)防錯法 (2)動改法 (3)流程法
(4)五五法
2020/9/10
參、 手法之效能
目的
如何避免做錯事情,使工作第一次 就做好的精神能夠具體實現。
改善人體動作的方式,減少疲勞使工作 更為舒適、更有效率,不要蠻幹。 研究探討牽涉到幾個不同工作站或地 點之流動關系,藉以發掘出可資改善 的地方。 藉著質問的技巧來發掘出改善的構想
1 藉“共同”動作必須同時執行來完成。 2 藉“順序”動作來完成。 3 藉“交互”動作來完成。
2020/9/10
Page24
鄭記企管 伍.1 IE手法說明 (防錯法/愚巧法)
適 應性
不 斷
消除浪費降低成本
柔性生產提高競爭力
暴
露
問 題
JIT生產方式
,
不
看板管理
斷
改
善
均衡化生產
良好的外
部協作
2020/9/10
尊 重 人 性 , 發 揮 人 的 作 用
Page3
鄭記企管
IE與精益生產關聯圖
不
斷 暴
質量保證
小批量生產
同步化生產
(1)如此擺放您會放錯嗎?(請在“ □ ”內打“ˇ”作選
擇)
□會
□ 不會
(2) 您不會/會放錯的原因是什麼?
2020/9/10
Page18
鄭記企管 伍.1 IE手法說明 (防錯法/愚巧法)
3.防錯法 之
“三不” 構造原則
2020/9/10
Page19
鄭記企管 伍.1 IE手法說明 (防錯法/愚巧法)
(8)生產線平衡法
2020/9/10
Page10
鄭記企管
名稱
(1)防錯法 (2)動改法 (3)流程法
(4)五五法
2020/9/10
參、 手法之效能
目的
如何避免做錯事情,使工作第一次 就做好的精神能夠具體實現。
改善人體動作的方式,減少疲勞使工作 更為舒適、更有效率,不要蠻幹。 研究探討牽涉到幾個不同工作站或地 點之流動關系,藉以發掘出可資改善 的地方。 藉著質問的技巧來發掘出改善的構想
1 藉“共同”動作必須同時執行來完成。 2 藉“順序”動作來完成。 3 藉“交互”動作來完成。
2020/9/10
Page24
鄭記企管 伍.1 IE手法說明 (防錯法/愚巧法)
適 應性
不 斷
消除浪費降低成本
柔性生產提高競爭力
暴
露
問 題
JIT生產方式
,
不
看板管理
斷
改
善
均衡化生產
良好的外
部協作
2020/9/10
尊 重 人 性 , 發 揮 人 的 作 用
Page3
鄭記企管
IE與精益生產關聯圖
不
斷 暴
質量保證
小批量生產
同步化生產
- 1、下载文档前请自行甄别文档内容的完整性,平台不提供额外的编辑、内容补充、找答案等附加服务。
- 2、"仅部分预览"的文档,不可在线预览部分如存在完整性等问题,可反馈申请退款(可完整预览的文档不适用该条件!)。
- 3、如文档侵犯您的权益,请联系客服反馈,我们会尽快为您处理(人工客服工作时间:9:00-18:30)。
零 件 材 料
作 業 方 法
作 業 順 序
作 業 時 間
作 業 空 間
作 業 能 力
改 善 立 案
改 善 檢 討
改 善 試 行
成 果 確 認 評
調評
析
價
查價
方法 研究
程序分析
◎
○
動作分析
○◎
動作經濟原則
○◎◎
○
○○
○
○
○
◎◎◎◎ ◎
○
◎○
時間分析
◎○
◎
作業 測定
運轉率分析
PTS法
○◎ ◎
○○
○○
○
◎◎○○
中國大陸: 台合電子(廈門)、隆光音箱廠(深圳)、瑞泰電子(深圳)、加維公 司(大朗)等
2020/7/12
Page3
UN IO N PO W ER
課程大綱
壹、 現場的管理與改善 貳、 5W2H 參、 動作經濟原則 肆、 時間測定與標準時間 伍、 生產線平衡 附 錄: 工作衡量技法MOST的簡介
2020/7/12
2020/7/12
Page22
十、活用IE改善的七大手法的要點
UN IO N PO W ER
B. 發覺問題的指標
a. 因素指標(4M1E)
人 (MEN)
材料 (MATERIALS)
機械 (MACHINES)
方法 (METHODS)(規定或標準規格、程序)
環境 (ENVIRONMENT)
2020/7/12
聯 作 産 PTS 動 錄 雙 動 VTR 單 動 抽 連 MOST 直 搬 搬
合 作
業 流
品 工
法
素 分
像 分
手 作
作 優
分析
元 作
作 要
樣 分
續 運
技法
接 運運 觀 工路
業程藝
析 析 業化
業 素析 轉
測 藝線
分分分
分
時時 分
PTS 分 分
析析析
析
間間 析
分分
法 析析
析析
2020/7/12
“
一 個 流 ”
现场管理与改善-IE手法 的活用(PPT 167页)
UN IO N PO W ER
講師簡介 : 何信貴
現任: •聯碩企業管理顧問有限公司
•專案顧問師
學歷: •省立臺北工業專科學校(即臺北科技大學前身)
經歷: •臺灣松下電器(股)有限公司 製造工廠廠長(小家電産品、金屬加工、串激馬達等工廠) 製造體質改革推進經理(全公司推進約100個主題) 生産技術資深經理(電機、電化事業處) 製造研修所講師
拉 式
每在 一
選定的主題
月六 年 做個 內 產 改 產 產 產 產 產
六月 轉 品 善 品 品 品 品 品
項內 型 線 職 族 族 族 族 族
目標
改善標的
大成 改立
成 精
重能 組小
A 組
B 組
C 組
D 組
E 組
善產 實
組
目標節省 金額(當年)
活品 企 動小 業
組體
*
存貨降三千萬
*
* 品質成本降一千五佰萬
Page5
UN IO N PO W ER
前 言
二、企業的永續經營
1. 企業要永續經營必須滿足顧客的需求。
◎ 顧客的想法、需求天天都在改變、進步。 ◎ 對應的表現:多品種、高品質、低價格、短交期化。
2. 要永續經營必須持續的進行管理與改善。 ◎ 以顧客為導向的經營活動。
2020/7/12
Page6
UN IO N PO W ER
【舊 lE 七大手法】
1. 愚巧法 2. 動作分析 3. 流程分析法 4. 動作經濟原理 5. 5 ×5W1H法 6. 人機配置法 7. 工作抽查法
2020/7/12
Page21
十、活用IE改善的七大手法的要點
UN IO N PO W ER
A. 發覺問題的觀點
解剖的觀點
點的觀察法 面的觀察法 組合的觀點 流動的觀察法
圖上構成
簡單化
新生產體系的 開發設計
綜合性的運用IE、 VE、QC、生產 技術、製造技術、 生產管理等技法
次期商品的 展開
改善案 實施
2020/7/12
Page15
六、需要改善的現象:
UN IO N PO W ER
組成現場的因素,具有不合理、不均勻、 浪費的現象都是浪費,如:
1. 生產過多的浪費 2. 等待的浪費 3. 搬運的浪費 4. 加工本身的浪費 5. 庫存的浪費 6. 動作的浪費 7. 製造不良的浪費
人機配合、動作經濟、人因工程
(主要指標:時間、效率、舒適、安全可靠)
●作業效率 (ACTIVlTY EFFlClENCY)
搬運活性分析
(主要指標: 活性係數、距離、時間)
●共同的通用手法
5 ×5W1H
2020/7/12
Page26
第二部分:5W2H
2020/7/12
报告人:何信贵
27
UN IO N PO W ER
案例
例 : ●動作研究 (MOTlON STUDY)
生產線-工程(工作)-作業-動作-動素
(主要指標: 距離、時間、方法、人員)
●時間研究 (TIME STUDY)
工作抽查、工時測定、生產線平衡法
(主要指標: 時間、效率)
2020/7/12
Page25
UN IO N PO W ER
案例
●系統流程 (SYSTEMATIC LAYOUT)
2020/7/12
Page2
講師簡介 : 何信貴
UN IO N PO W ER
經 曆:
●先鋒企業管理發展中心特聘顧問師 ●中國生産力中心(CPC)特聘顧問師 ●財團法人中衛發展中心特聘顧問師 ●臺灣松下電器工程科技社特聘顧問師
1983年日本松下電器公司體質改革(RIAL)研修 1995年馬來西亞松下電器公司時間衡量(MOST)技法研修 授課及輔導廠商: 中國臺灣: 臺灣松下電器、友訊電子公司、臺灣山葉企業公司、百稼企業、 百塑企業、九德松益電機、天立電機、上光公司、台松工業等
Page32
UN IO N PO W ER
5 W 2 H法案例
5Why 實例:一台機器故障了
為什麼機器停了? 因為超負荷保險絲斷了 為什麼會超負荷? 因為軸承部分的潤滑不夠 為什麼潤滑不夠? 因為潤滑油Pump汲不上油來 為什麼汲不上油? 因為潤滑油Pump磨損間隙大 為什麼磨損了? 因為沒有安裝篩檢程式混進鐵屑
IE手法的目的: (1)有效的準確掌握生産活動的實際狀態;
(2)儘快發現浪費、不合理、不均勻的事物;
(3)對生産活動的改善和標準化進行系統的管理;
IE手法的特徵: (1)分析程式方法--客觀性;
(2)對實現狀態能定量分析--定量性;
(3)用相同的符號及圖表分析--通用性;
2020/7/12
Page18
簡化:把必要而複雜的簡單化 重組:把順序不佳的、有利的重新編組
2020/7/12
Page13
五、精實方針展開矩陣圖
UN IO N PO W ER
*
依產品族重組
*
*
* 創設生產力及品質改善機能 *
*
* * * 與協力廠成立精實企業體
*
*****
依引 大 產進 幅 品連 改 別續 善 確暢 品 認流 質 價化 值及 流后
2020/7/12
Page16
UN IO N PO W ER
七、改善的十大步驟
STEP 1
現場問題的發掘
2020/7/12
Page17
UN IO N PO W ER
八、 IE手法概要
IE手法是以人的活動爲中心,事實爲依據,用科學的分析方法, 對生産系統進行觀察、記錄分析,並對系統問題進行合理化改善, 最後對結果進行標準化的方法。
○
◎◎◎◎
◎○
配置分析
○○
◎○
○
配置 研究
搬運分析
○◎
Line
○
○
○
○
balancing
甘特圖
◎◎
202其0/他7/12 各種檢查表 逻辑分析法
○○○◎○○ ○○○
◎ 20
◎○
九、現場改善的lE七大手法
UN IO N PO W ER
【新 lE 七大手法】
1. 流程分析法 2. 動作分析 3. 運搬活性分析 4. 工作抽查法 5. 動作經濟原則 6. 生產線平衡法 7. 人因工程法
2020/7/12
Page30
UN IO N PO W ER
二、 何謂 5Why ?
就是:問5次「為什麼?」 就是:追根究底、打破砂鍋到底
Why?:人員 -->簡化 Why?:方法 -->變更 Why?:次序 -->重重 Why?:目的 -->排除 Why?:地点 -->合併 ◎ 把 5Why? 與 5W2H 合用叫做 5 ×5W2H法
课程大纲
一、 5 W 2 H法是什麼? 二、 何謂 5Why ? 三、 從自問開始 四、 5W1H 改善的整体結構 五、生 產 的 結 構 六、生產的5大要素與5W1H
2020/7/12
Page28
一、 5 W 2 H法是什麼?
UN IO N PO W ER
(追問原因時) When Where How What Who 何時、何地、如何的、發生何事、主角是誰、
單 元 生 産
19
IE現場改善中解決問題的程式與IE手法的關係
改善程序
分析
問題
推進
對象