电池片设计
210组件尺寸标准化

210组件尺寸标准化太阳能电池组件的标准化是确保光伏系统可互操作性、提高制造效率和降低成本的重要步骤之一。
210组件指的是太阳能电池组件的尺寸规格,其中“210”通常表示电池片的尺寸。
以下是关于210组件尺寸标准化的一般性介绍:1. 电池片尺寸1.1 210电池片规格描述了电池片的尺寸,包括长度、宽度和厚度等方面的具体规格。
1.2 电池片类型引入了不同类型的电池片,例如单结晶、多结晶或其他高效率电池片,以满足不同应用需求。
2. 组件尺寸2.1 210组件外形规定了整个太阳能电池组件的外形尺寸,确保其适用于标准安装和集成。
2.2 边框设计描述了组件边框的设计标准,包括边框的宽度、形状和颜色等方面。
3. 功率输出标准3.1 额定功率描述了210组件的额定功率,即在标准测试条件下的输出功率。
3.2 温度特性强调了组件在不同温度下的性能特性,确保在实际环境中也能提供可靠的电力输出。
4. 光电转换效率4.1 电池效率描述了210组件的电池效率,即光能转换为电能的效率。
4.2 系统效率引入了整个光伏系统的效率,包括电池组件、逆变器等其他组件的效率。
5. 标准安装和连接5.1 安装孔位和尺寸规定了210组件上安装孔的位置、数量和尺寸,以便于标准化安装。
5.2 连接盒设计描述了组件上连接盒的设计标准,确保安全、可靠地连接电池组件。
6. 耐环境性能6.1 耐候性介绍了210组件的耐候性能,包括在不同气候条件下的稳定性和长期耐用性。
6.2 防尘与防水性能强调了组件的防尘和防水设计,以适应各种环境条件。
结论210组件尺寸标准化有助于推动太阳能行业的发展,促进制造业的协同作业和技术创新。
通过制定统一的标准,不仅可以提高产品的质量和性能,还能够降低生产成本,推动太阳能光伏技术更广泛地应用于不同领域。
标准化的210组件尺寸也有助于简化设计、安装和维护过程,为太阳能行业的可持续发展奠定基础。
无网结网版印刷电池片说明

无网结网版印刷电池片说明
无网结网版由于副栅位置没有网结,印刷时透墨性更好,印刷的电池片细栅线性度更好,线宽拓宽小,线条高低起伏小。
其与常规电池片相比,差异很小。
具体如下
一、图形
无网结网版印刷的电池片常规网版印刷的电池片
从以上看,无网结网版印刷的电池片整体图形结构上与常规的无差异
二、外观
外观上基本一致,局部放大后,只有边框线稍有不同,其他一样。
无网结网版印刷的电池片常规网版印刷的电池片
边框线成锯齿波浪形边框线成直线形
设计成波浪形的原因是防止印刷时边框粗线不良产生,如果是直线形,边框线与网版的纬线会有相切,即边框线部分区域与钢丝相切,导致该处浆料下墨不均,引起粗细不均异常。
太阳能电池片丝网印刷

烘干和烧结
烘干和烧结的目的
烘干和烧结是为了使印刷在硅片表面的油墨或涂料干燥并 固定在适当的位置,同时使油墨或涂料发生必要的物理和 化学变化。
烘干和烧结工艺
烘干和烧结工艺应根据油墨或涂料的特性和太阳能电池片 的材料特性进行合理控制,包括温度、时间和气氛等参数。
烘干和烧结设备
烘干和烧结设备可以采用隧道式烘干机或烘箱,设备应具 备温度控制和时间控制功能,以确保烘干和烧结效果的一 致性和稳定性。
丝网质量
01
丝网的材质、目数、开口尺寸等参数直接影响印刷质量,选用
高质量的丝网是保证印刷精度的前提。
印刷参数
02
印刷压力、速度、刮刀角度和硬度等参数的设置对印刷线条的
宽度、高度和均匀性有触变性、干燥速度等性能参数对印刷效果和固化
过程有直接影响。
质量检测方法
目视检测
检测与修复
检测目的
检测与修复是为了确保太阳能电池片丝网印刷的质量和可靠性,及 时发现并处理存在的缺陷和问题。
检测方法
检测方法包括目视检测、自动光学检测和X射线检测等,应根据印 刷品的特性和质量要求选择适当的检测方法。
修复工艺
对于发现的缺陷和问题,可以采用适当的修复工艺进行处理,如局部 热处理、激光修复等,以确保太阳能电池片的质量和性能符合要求。
03 太阳能电池片丝网印刷工 艺流程
涂布感光胶
涂布感光胶
在丝网印刷前,需要在硅片表面涂布 一层感光胶,以增强丝网印刷的附着 力。
涂布方式
涂布厚度
感光胶的厚度应均匀,且需根据丝网 印刷的精度要求来控制,一般而言, 较薄的涂布厚度可以提高印刷线条的 精度。
感光胶可以采用喷涂、刷涂或浸涂的 方式进行涂布,具体涂布方式应根据 感光胶的特性和生产工艺要求而定。
光伏组件结构详解

光伏组件结构详解光伏组件,也被称为太阳能电池板,是将太阳光转化为电能的关键设备。
它的构造精巧且经过精心设计,以最大限度地转换太阳能光线为电能。
本文将对光伏组件的结构进行详细解析。
光伏组件的核心部分是太阳能电池片。
太阳能电池片由将光线转化为电能的半导体材料制成。
常用的半导体材料有单晶硅、多晶硅和非晶硅。
在电池片表面,覆盖着一层防反射玻璃。
这层玻璃的作用是减少光线的反射,从而提高光的吸收率。
光伏组件的背面通常由一块背板构成。
背板是用于支撑太阳能电池片的一个重要部分。
它可以保护电池片免受外界的损害,并提供稳固的支撑。
背板通常由铝制成,具有良好的耐腐蚀性和机械强度。
在背板之上,有一层背板胶。
背板胶的作用是将太阳能电池片与背板黏合在一起,确保组件的结构牢固。
背板胶通常使用丙烯酸胶或聚氨酯胶,具有良好的粘合性能和耐候性。
光伏组件的边框是将太阳能电池片封装在内的一个框架,通常由铝制成。
边框的主要作用是提供结构支持,并保护电池片不受外界因素的影响,例如风力和震动。
边框还可以增加光伏组件的稳定性和抗压能力。
最后,光伏组件的表面覆盖着一层防污染膜。
这层膜可以防止尘埃、水汽和其他杂质附着在组件表面,从而保持光伏组件的高效转换能力。
总结起来,光伏组件的结构由太阳能电池片、防反射玻璃、背板、背板胶、边框和防污染膜组成。
这些部分密切配合,共同实现太阳能光线转化为电能的过程。
通过不断的技术改进和创新,光伏组件的效率和性能得到了大幅提升,为可再生能源的发展做出了重要贡献。
注:本文所述内容仅为科普性质,不涉及具体产品和商业推广。
对于光伏组件的具体选择和使用,建议咨询专业人士或相关机构的意见。
电池盒设计注意事项

电池盒设计注意事项生活中的电子产品,有许多都会用到干电池作为电源。
结构设计中肯定会遇到这种电池盒的结构设计. 按装入电池的数量,可分为单节和多节电池盒按电池盒盖的样式,电池盒的种类可分为推式和掀盖式,见下图1,图2图1 图2首先,我们必须了解我们的设计对象:干电池的规格,型号(见下表1)与尺寸规格,尤其是尺寸标准。
这点我们可以根据IEC60086-2_2011(见附录A )查得干电池尺寸的相关规定。
表1 IEC 干电池型号对照表无论是1号电池,还是7号电池,设计时都要充分考虑电池盒能装入各种不同公差的电池。
下面以常见的两节并排的AA 电池盒为例子,简单介绍一下电池盒的设计过程。
1. 电池盒的尺寸设计因为AA 电池的总长度为50.5mm, 直径13.5—14.5mm所以我们必须以Ø14.5x50.5为设计尺寸.同时我们必须单边留0.1-0.2mm 的间隙。
电池盒的内高度:14.5+0.1+0.1=14.7mm(单边留0.1mm 间隙),见图3电池盒的内宽度:14.5x2+0.1+0.1=29.2mm(单边留0.1mm 间隙),见图4电池盒的内长度:50.5+正极片总高+负极片压缩后总高,见图3以上电池盒内长宽高度必须的最小尺寸,如果在电池盒底部起弧型骨限位每一节电池,电池之间还可以拉开适当的距离,见图5内长度 内宽度 内高度图3 图4图52. 电池极片设计电池极片一般有3种类型,一种是用纯弹簧做电池的正负极片,见图6;另一种是用五金弹片做正负极片,见图7,还有一种是五金片做正极,把弹簧压在五金片上做负极,见图8。
第一种:多用在弹簧可以直接焊在PCB 上情况下。
弹簧可以有很大的伸缩性,能容不同尺寸电池.因弹簧可以弯成多种形状,即使PCB 离得远一点,也可以把弹簧线引出去,这样装配会比较方便,省去焊接的工序。
因为弹簧没有卡位,务必注意弹簧的定位,防止装电池把弹簧挤出,从而造成接触不良。
缺点:与导线焊接不好焊。
电池片的加工工艺.PPT课件

根据所生产电池组件规格的不同,依据设 计图纸中所表示的尺寸加工相应的铝框待用。
二、单片焊接
做好准备工作后,首先进行单片焊接工艺,工 艺具体如下: 1、来料检查
对上道来料进行检查,并根据组件设计单片焊 接所需涂锡带的长度要求将涂锡带裁剪成规定尺寸 待用。将电池片一次取出,放入工作台上,准备焊 接。
2、装框 将组件放到打框机上,并且把组件放到铝合
金边框内,开启启动装置把铝合金边框压紧并在 组件与铝合金边缘四周上密封硅胶。 3、装接线盒
按图纸要求准备接线盒,并将接线盒放置在 正负电极引出线上,将引出的正负电极放置在接 线盒的电极上,用电烙铁焊接好。
七、成品终测 装框与装接线盒结束后,应对相应的电池组
对于由不同晶粒构成的铸造多晶硅片,由于硅片表 面具有不同的晶向,择优腐蚀的碱性溶液显然不再适用。 研究人员提出利用非择优腐蚀的酸性腐蚀剂,在铸造多 晶硅表面制造类似的绒面结构,增加对光的吸收。到目 前为止,人们研究最多的是HF和HNO3的混合液。其中 HNO3 作为氧化剂,它与硅反应,在硅的表面产生致密 的不溶于硝酸的SiO2层,使得HNO3 和硅隔离,反应停 止;但是二氧化硅可以和HF反应,生成可溶解于水的络 合物六氟硅酸,导致SiO2层的破坏,从而硝酸对硅的腐 蚀再次进行,最终使得硅表面不断被腐蚀。
的硅片表面具有更好的减反射效果,能够更好地 吸收和利用太阳光线。当一束光线照射在平整的 抛光硅片上时,约有30%的太阳光会被反射掉; 如果光线照射在金字塔形的绒面结构上,反射的 光线会进一步照射在相邻的绒面结构上,减少了 太阳光的反射;同时,光线斜射入晶体硅,从而 增加太阳光在硅片内部的有效运动长度,增加光 线吸收的机会。如图所示,为单晶硅制绒后的 SEM图,高10μm的峰时方形底面金字塔的顶。
电池片的加工工艺教学课件

电性能检测
总结词
电性能检测是评估电池片性能的重要手段, 主要测试电池片的电导率、内阻、填充因子 等参数。
详细描述
电性能检测通过专用的测试设备对电池片的 电性能参数进行测量和分析。电导率反映了 电池片的导电能力,内阻决定了电池片的能 量转换效率,填充因子则综合反映了电池片 的性能水平。电性能检测对于确保电池片的 质量和性能具有重要意义。
配料与涂布
配料
将所需成分按照配方比例混合,搅拌 均匀。
涂布
将配好的浆料均匀涂布在硅片上,控 制涂布厚度和均匀性。
激光切割
激光划片
使用激光技术将涂布好的硅片划成小片电池片。
激光刻蚀
对电池片表面进行刻蚀处理,去除不良部分。
印刷与烘干
丝网印刷
在电池片表面印刷电极图案,确保电极位置准确无误。
烘干
将印刷好的电池片进行烘干处理,使墨水固化。
可靠性检测
要点一
总结词
可靠性检测是评估电池片在长期使用过程中的稳定性和可 靠性的重要手段。
要点二
详细描述
可靠性检测通常采用加速老化或寿命测试等方法,模拟电 池片在实际使用过程中可能遇到的各种环境因素,如温度 、湿度、紫外线等,以加速电池片的性能衰减。通过可靠 性检测,可以评估电池片的寿命和可靠性,从而为实际应 用提供可靠的技术支持。
电池片种类
单晶硅电池片
由单晶硅棒切割而成,具有较高的光电转换效率 ,但制造成本较高。
多晶硅电池片
由多晶硅锭切割而成,光电转换效率略低于单晶 硅电池片,但制造成本较低。
薄膜太阳能电池
利用薄膜技术将太阳能转化为电能,具有轻便、 可弯曲等特点,但光电转换效率相对较低。
电池片的应用
光伏电站
电池组件结构设计与参数指标分析
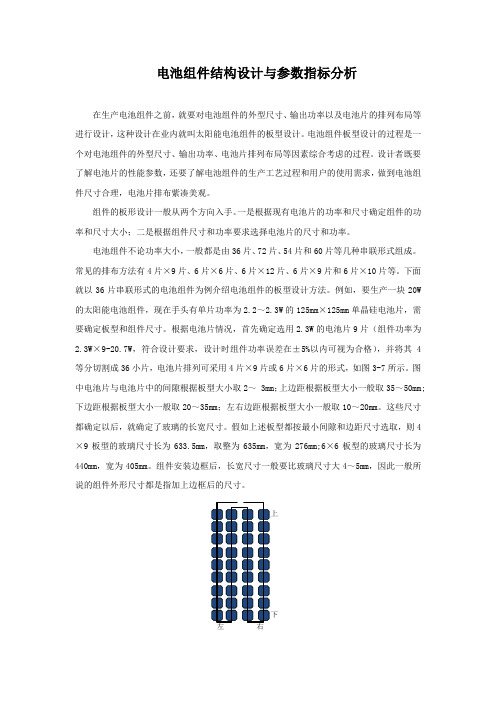
电池组件结构设计与参数指标分析在生产电池组件之前,就要对电池组件的外型尺寸、输出功率以及电池片的排列布局等进行设计,这种设计在业内就叫太阳能电池组件的板型设计。
电池组件板型设计的过程是一个对电池组件的外型尺寸、输出功率、电池片排列布局等因素综合考虑的过程。
设计者既要了解电池片的性能参数,还要了解电池组件的生产工艺过程和用户的使用需求,做到电池组件尺寸合理,电池片排布紫凑美观。
组件的板形设计一般从两个方向入手。
一是根据现有电池片的功率和尺寸确定组件的功率和尺寸大小;二是根据组件尺寸和功率要求选择电池片的尺寸和功率。
电池组件不论功率大小,一般都是由36片、72片、54片和60片等几种串联形式组成。
常见的排布方法有4片×9片、6片×6片、6片×12片、6片×9片和6片×10片等。
下面就以36片串联形式的电池组件为例介绍电池组件的板型设计方法。
例如,要生产一块20W 的太阳能电池组件,现在手头有单片功率为2.2~2.3W的125mm×125mm单晶硅电池片,需要确定板型和组件尺寸。
根据电池片情况,首先确定选用2.3W的电池片9片(组件功率为2.3W×9-20.7W,符合设计要求,设计时组件功率误差在±5%以内可视为合格),并将其4等分切割成36小片,电池片排列可采用4片×9片或6片×6片的形式,如图3-7所示。
图中电池片与电池片中的间隙根据板型大小取2~ 3mm;上边距根据板型大小一般取35~50mm;下边距根据板型大小一般取20~35mm;左右边距根据板型大小一般取10~20mm。
这些尺寸都确定以后,就确定了玻璃的长宽尺寸。
假如上述板型都按最小间隙和边距尺寸选取,则4×9板型的玻璃尺寸长为633.5mm,取整为635mm,宽为276mm;6×6板型的玻璃尺寸长为440mm,宽为405mm。