螺母凸焊工艺参数优化
工贸有限公司企业标准 凸焊参数选择指导
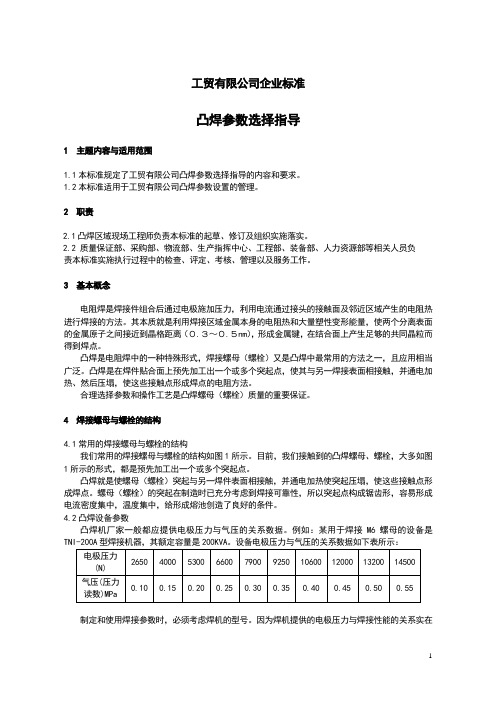
工贸有限公司企业标准凸焊参数选择指导1 主题内容与适用范围1.1本标准规定了工贸有限公司凸焊参数选择指导的内容和要求。
1.2本标准适用于工贸有限公司凸焊参数设置的管理。
2 职责2.1凸焊区域现场工程师负责本标准的起草、修订及组织实施落实。
2.2质量保证部、采购部、物流部、生产指挥中心、工程部、装备部、人力资源部等相关人员负责本标准实施执行过程中的检查、评定、考核、管理以及服务工作。
3 基本概念电阻焊是焊接件组合后通过电极施加压力,利用电流通过接头的接触面及邻近区域产生的电阻热进行焊接的方法。
其本质就是利用焊接区域金属本身的电阻热和大量塑性变形能量,使两个分离表面的金属原子之间接近到晶格距离(0.3~0.5nm),形成金属键,在结合面上产生足够的共同晶粒而得到焊点。
凸焊是电阻焊中的一种特殊形式,焊接螺母(螺栓)又是凸焊中最常用的方法之一,且应用相当广泛。
凸焊是在焊件贴合面上预先加工出一个或多个突起点,使其与另一焊接表面相接触,并通电加热、然后压塌,使这些接触点形成焊点的电阻方法。
合理选择参数和操作工艺是凸焊螺母(螺栓)质量的重要保证。
4 焊接螺母与螺栓的结构4.1常用的焊接螺母与螺栓的结构我们常用的焊接螺母与螺栓的结构如图1所示。
目前,我们接触到的凸焊螺母、螺栓,大多如图1所示的形式,都是预先加工出一个或多个突起点。
凸焊就是使螺母(螺栓)突起与另一焊件表面相接触,并通电加热使突起压塌,使这些接触点形成焊点。
螺母(螺栓)的突起在制造时已充分考虑到焊接可靠性,所以突起点构成锯齿形,容易形成电流密度集中,温度集中,给形成熔池创造了良好的条件。
4.2凸焊设备参数凸焊机厂家一般都应提供电极压力与气压的关系数据。
例如:某用于焊接M6螺母的设备是制定和使用焊接参数时,必须考虑焊机的型号。
因为焊机提供的电极压力与焊接性能的关系实在是太重大了。
各种型号的焊机的气缸不尽一致,同样的气压,不同的焊机所产生的压力是不会相同的。
凸焊的工艺特点和工艺参数

凸焊的工艺特点和工艺参数1、凸焊的工艺特点凸焊是点焊的一种变形,通常是在两板件之一上冲出凸点,然后进行焊接,由于电流集中,克服了点焊时熔核偏移的缺点,因此凸焊时工件的厚度。
比可以超过6:1。
凸焊时,电极必须随着凸点的被压溃而迅速下降,否则会因失压而产生喷溅,所以应采用电极随动性好的凸焊机。
多点凸焊时,如果焊接条件不适当,会引起凸点移位现象,并导致接头强度降低。
实验证明,移位是由电流通过时的电磁力引起的。
影响凸点移位的电磁力F与电流I的平方和凸点的高度h成正比,与点距Sd成反比,凸点移动向外偏斜是次级回路电磁力附加作用的结果。
在实际焊接时,由于凸点高度不一致,上、下电极平行度差,一点固定另一点移动要比两点同时移动的情况多。
为了防止凸点移位,除在保证正常熔核的条件下,选用较大的电极压力,较小的焊接电流外,还应尽可能地提高加压系统的随动性。
提高随动性的方法主要是减小加压系统可动部分的质量;以及在导向部分采用滚动摩擦。
多点凸焊时,为克服各凸点间的压力不均衡,可以采用附加预热脉冲或采用可转动电极的办法,特别适用于在同一个板件上焊接两个距离较大的零件,在上电极与上座板之间装有由多层铜箔制成的铜分路,目的是防止枢轴过热和两侧凸点电流不均衡。
2、凸焊的工艺参数凸焊的主要工艺参数是电极压力、焊接时间和焊接电流。
(1)电极压力凸焊的电极压力取决于被焊金属的性能、凸点的尺寸和一次焊成的凸点数量等。
电极压力应足以在凸点达到焊接温度时将其完全压溃,并使两工件紧密贴合。
电极压力过大会过早地压溃凸点,失去凸焊的作用,同时因电流密度减小而降低接头强度,压力过小又会引起严重喷溅。
(2)焊接时间对于给定的工件材料和厚度,焊接时间由焊接电流和凸点刚度决定。
在凸焊低碳钢和低合金钢时,与电极压力和焊接电流相比,焊接时间是次要的,在确定合适的电极压力和焊接电流后,再调节焊接时间,以获得满意的焊点。
如果想缩短焊接时间,就要相应增大焊接电流,但过分增大焊接电流可能引起金属过热和喷溅,通常凸焊的焊接时间比点焊长,而电流比点焊小。
【精品】焊接螺母凸焊专用下电极的改进
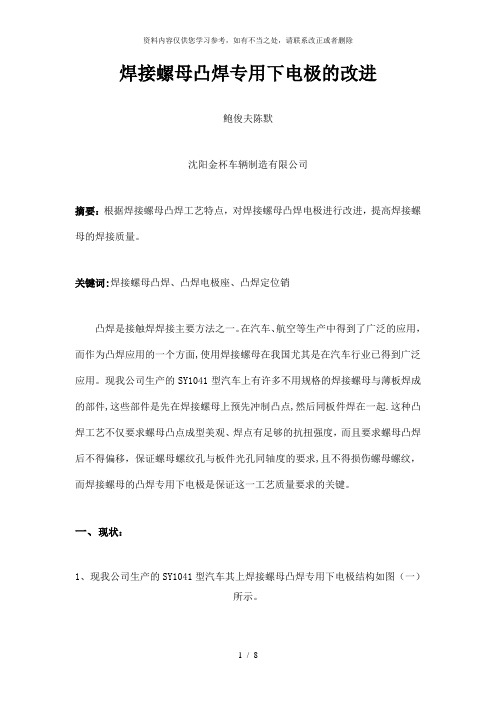
焊接螺母凸焊专用下电极的改进鲍俊夫陈默沈阳金杯车辆制造有限公司摘要:根据焊接螺母凸焊工艺特点,对焊接螺母凸焊电极进行改进,提高焊接螺母的焊接质量。
关键词:焊接螺母凸焊、凸焊电极座、凸焊定位销凸焊是接触焊焊接主要方法之一。
在汽车、航空等生产中得到了广泛的应用,而作为凸焊应用的一个方面,使用焊接螺母在我国尤其是在汽车行业已得到广泛应用。
现我公司生产的SY1041型汽车上有许多不用规格的焊接螺母与薄板焊成的部件,这些部件是先在焊接螺母上预先冲制凸点,然后同板件焊在一起.这种凸焊工艺不仅要求螺母凸点成型美观、焊点有足够的抗扭强度,而且要求螺母凸焊后不得偏移,保证螺母螺纹孔与板件光孔同轴度的要求,且不得损伤螺母螺纹,而焊接螺母的凸焊专用下电极是保证这一工艺质量要求的关键。
一、现状:1、现我公司生产的SY1041型汽车其上焊接螺母凸焊专用下电极结构如图(一)所示。
2、凸焊电极座2、压簧3、绝缘垫片4、绝缘衬套5、凸焊电极帽6、凸焊定位销图(一)实践表明,此焊接螺母凸焊专用下电极存在以下几方面的缺点:1、由于凸焊定位销与凸焊电极帽间无绝缘,螺母凸焊时有时凸焊定位销倾斜,与凸焊电极帽接触产生分流现象,影响螺母的焊接质量;2、由于凸焊过程中产生的飞溅、熔粘现象,造成凸焊时螺母螺纹损伤和凸焊定位销极易损坏、使用寿命低,操作者不得不对其经常进行修整,浪费大量的人力、物力和财力;3、由于凸焊定位销的定位部分为圆柱形,造成螺母凸焊时自调整作用差,操作者稍有不慎,螺母凸焊后就会偏移。
下表是对五个凸焊定位销的使用寿命和修整次数的测试结果:下表是对200个焊接螺母凸焊后,螺母螺纹损伤和螺母焊偏数的测试结果:二、改进措施针对以上螺母凸焊专用下电极存在的缺点,经过认真的分析研究,应对其进行以下几方面的改进:1、在凸焊定位销与凸焊电极帽间增设绝缘套,即避免分流现象的产生,又起导向的作用;2、对凸焊电极座进行改进.在其上开进气孔,与焊机上的压缩空气联接.凸焊时压缩空气把飞溅吹开,从而避免了定位销与工件接触部位的飞溅和熔粘现象的产生,使螺母螺纹损伤、定位销损坏现象得到解决;把凸焊定位销的定位部分改为锥形,根据不同规格的焊接螺母选择不同的锥度。
焊接工艺参数优化及焊接缺陷分析

焊接工艺参数优化及焊接缺陷分析随着现代工业的发展,焊接技术越来越受到重视。
作为一种连接材料的方法,焊接具有无需使用额外连接材料、连接强度高等特点,但同时也存在着焊接缺陷的问题。
为了解决这些缺陷问题,且提高焊接的质量和效率,焊接工艺参数的优化尤为重要。
首先,焊接工艺参数的选择对焊接质量和效率具有重要的影响。
在焊接过程中,工艺参数主要包括电流、电压、送丝速度、焊接速度等因素。
根据焊接的特点,确定合适的焊接工艺参数是提高焊接质量和效率的关键。
在实际工作中,焊接工艺参数的选择需要根据不同的焊接材料、厚度及结构进行多次试验来确定最佳参数。
因此,在进行焊接前应进行充分的试验和参数优化。
其次,焊接缺陷的分析和处理也是关键。
焊接缺陷主要包括焊接裂纹、夹杂、气孔、未熔合等问题。
这些缺陷不仅会影响焊接的质量,而且也可能对工件的性能产生负面影响。
因此,在焊接过程中,需要对焊接缺陷进行及时的分析和处理。
一般而言,焊接缺陷的处理主要包括重新焊接、填充及人工去除等方法。
无论哪种方法,都需要具有严密的焊接工艺参数来保证焊接质量。
最后,需要提醒的是,焊接工艺参数优化和焊接缺陷分析并不是简单的任务,需要有持续的尝试和探索,同时也需要熟练的操作技能。
作为焊接工作者,需要不断学习和掌握相关知识和技能,才能够提高焊接的质量和效率,并达到理想的效果。
简而言之,优化焊接工艺参数和处理焊接缺陷是提高焊接质量和效率的关键。
在实际焊接过程中,需要不断尝试和探索,同时熟练掌握相关技能和知识。
只有如此,我们才能够将焊接技术发挥到极致,实现高效、高质量的生产。
螺母凸焊工艺设计规范

螺母凸焊工艺设计规范2014-12-30发布 2015-1-1实施xxxxxxxxx发布1.范围本标准规定了本公司螺母凸焊焊接参数、定位孔尺寸及其公差等技术要求。
本标准适用于xxxxxxxx公司零部件及总成螺母凸焊工艺设计。
2.规范性引用文件下列文件对于本文件的应用是必不可少的,凡是注日期的引用文件,仅注日期的版本适用于本文件。
凡是不注日期的引用文件,其最新版本(包括所有的修改单)适用于本文件。
GB/T 19867.5 《电阻焊焊焊接工艺规程》HB/T5420-1989 《电阻焊电极与辅助装置用铜及铜合金》GB/T 5213-2008 《冷轧低碳钢板及钢带》GB/T 13680-1992 《焊接方螺母》HB 5363-1999 《焊接工艺质量控制》3.凸焊设备3.1唐山松下生产的YS-500R型电阻焊机4.对焊件的要求4.1焊件母材选用DC01、20钢、Q235等焊接性良好的低碳钢;4.2母材规格选用料厚3.0mm以下冷轧钢板;4.3凸焊螺母符合GB/T 13680规定,表面不做任何处理切验收合格;4.4在焊接状态下,焊件与焊机不得干涉或无法焊接。
焊件工艺要求见附表1焊件结构示意图附表1 焊件工艺要求4.6焊件凸焊螺母底孔可选用1.009.1+Φ和1.005.10+Φ两种规格,推荐选用1.005.10+Φ;4.7最大尺寸超过1.5m 且刚性差的工件不建议采用凸焊; 4.8焊件质量超过10Kg ,不建议采用凸焊。
5.凸焊电极、电极帽5.1电极、电极帽材料选用2类电极材料。
见附表25.2电极、电极帽端面平整无毛刺,电极工作部分尺寸应方便地到达焊接处和电极充分冷却,以及电极能可靠地安装于焊机上,并卸装方便。
6.凸焊参数规范:主要凸焊参数见附表3附表3 低碳钢板的凸焊参考规范7.焊接质量7.1外观质量:螺母螺纹孔无焊渣、螺母表面无压痕、变形等缺陷;7.2焊接方螺母与母材焊接的破坏力矩应100%≥70N·m;7.3螺纹尺寸:M8-6H螺纹100%通规通;7.4其余应符合HB 5363-1999焊接工艺质量控制。
焊接工艺参数优化及焊缝质量控制研究
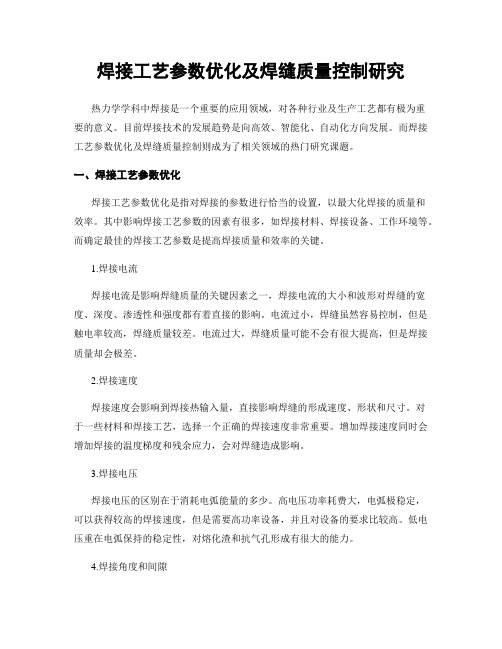
焊接工艺参数优化及焊缝质量控制研究热力学学科中焊接是一个重要的应用领域,对各种行业及生产工艺都有极为重要的意义。
目前焊接技术的发展趋势是向高效、智能化、自动化方向发展。
而焊接工艺参数优化及焊缝质量控制则成为了相关领域的热门研究课题。
一、焊接工艺参数优化焊接工艺参数优化是指对焊接的参数进行恰当的设置,以最大化焊接的质量和效率。
其中影响焊接工艺参数的因素有很多,如焊接材料、焊接设备、工作环境等。
而确定最佳的焊接工艺参数是提高焊接质量和效率的关键。
1.焊接电流焊接电流是影响焊缝质量的关键因素之一,焊接电流的大小和波形对焊缝的宽度、深度、渗透性和强度都有着直接的影响。
电流过小,焊缝虽然容易控制,但是触电率较高,焊缝质量较差。
电流过大,焊缝质量可能不会有很大提高,但是焊接质量却会极差。
2.焊接速度焊接速度会影响到焊接热输入量,直接影响焊缝的形成速度、形状和尺寸。
对于一些材料和焊接工艺,选择一个正确的焊接速度非常重要。
增加焊接速度同时会增加焊接的温度梯度和残余应力,会对焊缝造成影响。
3.焊接电压焊接电压的区别在于消耗电弧能量的多少。
高电压功率耗费大,电弧极稳定,可以获得较高的焊接速度,但是需要高功率设备,并且对设备的要求比较高。
低电压重在电弧保持的稳定性,对熔化渣和抗气孔形成有很大的能力。
4.焊接角度和间隙对于不同类型的焊接工艺,角度和间隙可能不同。
通常,必须根据实际的需求和焊接材料确定最佳的焊接角度和间隙,影响这些参数的因素有材料、构件型号和设备等。
二、焊缝质量控制研究焊缝质量控制是指通过合理的技术手段将焊接工艺加以控制,以实现良好的焊接质量。
焊缝质量的好坏关系到工件的结构耐久性和外观要求,因此,焊缝质量控制是焊接技术不可或缺的组成部分。
1.焊缝表面焊缝表面清洁非常关键。
在焊接工作时,需要注意焊接环境干净整洁且去除表面的油污或其他不干净物质。
对于焊接材料表面产生的氧化物、熔化渣、气孔、夹渣等问题,需要采取措施进行清除。
焊接工艺流程中的焊接参数优化策略
焊接工艺流程中的焊接参数优化策略在焊接工艺中,焊接参数的优化对于保障焊接质量和提高焊接效率至关重要。
本文将介绍焊接工艺流程中的焊接参数优化策略。
1. 材料准备和参数选择在进行焊接工艺流程之前,首先需要对材料进行准备。
选择合适的焊材和母材是确保焊接质量的关键。
同时,根据焊接工艺和焊接材料的不同,确定合适的焊接参数,如焊接电流、电压、焊接速度等。
这些参数需要根据焊接材料的特性、焊缝的要求以及设备的性能来选择。
2. 焊接参数的优化在焊接过程中,通过对焊接参数的优化,可以有效提高焊接效率和焊接质量。
2.1 焊接电流的优化焊接电流对焊接质量和焊接速度有着重要影响。
过高的焊接电流会导致焊缝过深,增加熔渣的形成并且增加焊接的热量,可能会引起焊缝的变形和裂纹。
过低的焊接电流则会导致焊缝不达标,焊接强度不够。
因此,需要根据焊接材料和焊缝要求来选择合适的焊接电流,以保证焊接质量和效率的平衡。
2.2 焊接电压的优化焊接电压对焊接弧的稳定性和焊缝形状有着重要影响。
过高的焊接电压会导致焊接弧过长,焊缝宽度过宽,焊接强度下降。
过低的焊接电压则会导致焊接弧过短,焊缝宽度不够,焊接效果不佳。
因此,在选择焊接电压时,需要根据焊接材料和焊缝要求来调节焊接电压,以获得稳定的焊接弧和合适的焊缝形状。
2.3 焊接速度的优化焊接速度对焊接质量和焊接效率有着重要影响。
过快的焊接速度会导致焊接熔渣无法完全排出,焊接强度低。
过慢的焊接速度则会导致焊接过热,焊缝变形和裂纹的概率增加。
因此,在选择焊接速度时,需要根据焊接材料和焊缝要求来调节焊接速度,以获得良好的焊接效果。
3. 焊接参数的监控和调整在焊接工艺流程中,焊接参数的监控和调整是确保焊接质量的重要措施。
通过监控焊接过程中的焊接电流、电压和温度等参数,及时发现异常情况并进行调整,可以避免焊接缺陷的出现。
此外,焊接参数的定期检验和调整也是保证焊接质量的重要手段。
4. 结论在焊接工艺流程中,焊接参数的优化对于提高焊接质量和效率至关重要。
20067221125329834_凸焊的焊接工艺及常用金属材料的
凸焊工艺与方法凸焊主要用于焊接低碳钢和低合金钢的冲压件。
凸焊的种类很多,除板件凸焊外,还有螺帽、螺钉类零件的凸焊、线材交叉凸焊、管子凸焊和板材T型凸焊等。
板件凸焊最适宜的厚度为0.5-4mm。
焊接更薄的板件时,凸点设计要求严格,需要随动性极好的焊机,因此厚度小于0.25mm的板件更易于采用点焊。
凸焊与点焊相比还具有以下优点:1)在一个焊接循环内可同时焊接多个焊点。
不仅生产率高,而且没有分流影响。
因此可在窄小的部位上布置焊点而不受点距的限制。
2)由于电流密度集于凸点,电流密度大,故可用较小的电流进行焊接,并能可靠地形成较小的熔核。
在点焊时,对应于某一板厚,要形成小于某一尺寸的熔核是很困难的。
3)凸点的位置准确、尺寸一致,各点的强度比较均匀。
因此对于给定的强度、凸焊焊点的尺寸可以小于点焊。
4)由于采用大平面电极,且凸点设置在一个工件上,所以可最大限度地减轻另一工件外露表面上的压痕。
同时大平面电极的的电流密度小、散热好,电极的磨损要比点焊小得多,因而大大降低了电极的保养和维修费用。
5)与点焊相比,工件表面的油、锈、氧化皮、镀层和其他涂层对凸焊的影响较小,但干净的表面仍能获得较稳定的质量。
凸焊的不足之处是需要冲制凸焊的附加工序;电极比较复杂;由于一次要焊多个焊点,需要使用高电极压力、高机械精度的大功率焊机。
由于凸焊有上述多种优点,因而获得了极广泛的应用。
凸焊电极、模具和夹具一、电极材料凸焊电极通常采用2类电极合金制造,因为这类电极合金在电导率、强度、硬度和耐热性等方面具有最好的综合性能。
3类电极合金也能满足要求。
二、电极设计凸焊电极有三种基本类型:1)点焊用的圆形平头电极2)大平头棒状电极3)具有一组局部接触面的电极,即将电极在接触部位加工出凸起接触面,或将较硬的铜合金嵌块用钎焊或紧固方法固定于电极的接触部位。
标准点焊电极用于单点凸焊时。
为了减轻工件表面压痕,电极接触面直径应不小于凸点直径的两倍。
大平头棒状电极用于局部位置的多点凸焊。
高强度钢储能螺母凸焊工艺非线性多元回归设计
妈據生产应用高强度钢储能螺母凸焊工艺非线性多元回归设计曹小兵1周照耀1邹春华2(1.华南理工大学机械与汽车工程学院,广州510640; 2.广州亨龙智能装备股份有限公司,广州510990)摘要通过正交试验法,研究了 22MnB5高强度钢与M8法兰焊接螺母电容储能焊工艺,以凸焊接头螺母顶出 力/为衡量接头质量的主要考察指标,以电极压力A、焊接电压A、电容容量&等三个主要焊接参数以及各参数间 的交互作用作为相互独立的考察因素,建立了一种描述工艺参数与接头质量之间关系的三元三次非线性回归模 型,通过遗传算法对模型进行了优化求解,并通过试验对模型进行了检验。
结果表明,回归模型值与试验值的误差 均在10%以内,模型具有较高的精度。
关键词:储能焊螺母凸焊非线性多元回归正交试验遗传算法中图分类号:TG457〇序言螺母凸焊是汽车焊装工艺中的一道必不可少的工 序,在车身柱梁、变速箱、发动机等关键部位应用广泛[1-2],焊接参数的选取直接影响接头的质量与稳定 性,进而影响零件装配系统乃至整车的可靠性与安全 性。
因此,研究车用高强度钢螺母凸焊工艺具有重要 的实用价值与理论指导意义。
车用高强度钢焊接性一直是焊接领域研究热点之 一,许多学者[>6]对钢板的点焊接头性能、组织、力学模 型及参数优化等做了大量研究工作。
高强度钢螺母凸焊 属于异种材料焊接范畴,焊接中常出现热影响区软化、飞 溅、螺母热变形严重等问题[7],加之焊接参数对焊接质量 的影响规律是一个交互、多维的复杂关系,试验数据较分 散,研究起来难度较大。
储能焊具有时间短、热影响区 窄、残余应力小等特点,特别适宜成分、熔点、导热性差异 较大的异种材料连接[8-9]。
目前,关于电容储能焊接高 强度钢的文献较为少见,采用储能焊的方式,进行高强 度钢螺母凸焊工艺是一种新的尝试。
文中探究了车用高强度钢22M H B5与M8法兰焊 接螺母的储能焊工艺,以螺母顶出力/为衡量接头质量 的主要指标,将电极压力、焊接电压、电容容量三个主收稿日期:2017 -08 -09基金项目:广东省科技计划项目(2016A010103006);广州市科技计划项目(201604016015)^要焊接参数及参数间的交互作用作为独立考察因素,基于正交试验与遗传算法优化,建立了描述接头质量 与工艺参数关系的三元三次非线性回归模型,并通过 试验对模型的精度进行了验证。
螺母和螺栓的凸焊_楼文质
而 且 凸点 的 外 形 要 求规
凸焊螺 母 或 凸 焊 螺 栓 连 同 被焊 板 件 一 起 放 在 一
大小 一 致
。
种 特殊 结 构 的 下 电 极 上
的焊 接接 头
。
上 电 极 采用平 电 极
,
然 后 选 择 一 种 合适 的 焊接 参数
就 能获 得 牢固
10
厂 一
-
平 均 每 台驾 驶室 上有
生 产 总成 本 只 有楔 形 螺 母 及 螺 栓 电 弧 焊 结
.
构的13 / 、 1 /
3
焊 点热 影 响 区 很 小
,
,
不 会 影 响螺 纹 精
。
粼去
度
,
不 会 象楔 形 螺母 那样 容 易 产 生 铆 接 变形
,
接 头 有足够 的抗 扭强 度
在 交 变载 荷 作用 下不
3
。
羊
帐d z
`
会松动
,
同时 在 高温 下 切掉 也不 会产 生 裂纹
。
多个 各
「 几
种规格 的 凸焊螺 栓 或 螺母 栓 电弧 焊 比 较
.
它 与楔 形螺 母 及 螺
:
,
瓜天
)
1
,
有 如下优 点,, Nhomakorabea翌
没有 弧 光 的
Il
1
没 有 震动 铆接 时 的 噪 音
照射
,
劳 动条 件好
.
L l
2
生 产 效率 高
4
;
节 省焊 条 及 大量 辅 助材
图 1
凸 俘 裸毋 结 构
料
,
效率 比 车 削 方法 提 高近 2 0 倍 锻 状态
- 1、下载文档前请自行甄别文档内容的完整性,平台不提供额外的编辑、内容补充、找答案等附加服务。
- 2、"仅部分预览"的文档,不可在线预览部分如存在完整性等问题,可反馈申请退款(可完整预览的文档不适用该条件!)。
- 3、如文档侵犯您的权益,请联系客服反馈,我们会尽快为您处理(人工客服工作时间:9:00-18:30)。
工方法达到。
(3)过渡层焊接材料:采用<1.2mm细丝C O2焊,焊丝牌号为H08Mn2SiA。
(4)炉内预热温度:350℃,保温2h。
(5)层间温度:≥150℃,采用在旋转的齿圈两侧点燃火焰喷炬的方法维持工件的层间温度。
(6)焊接工艺:焊接工艺参数见表2。
3.4 在过渡层上焊接齿轮辐板
过渡层焊接完成后,立即进炉内缓冷,炉内温度为150℃。
出炉后经目视检查和超声波100%探伤检查Ⅱ级合格后,采用机加工方法加工齿圈内径,使之与辐板达到合理的配合尺寸,进一步降低收缩拘束应力,然后将辐板与齿圈过渡层内径装配焊接。
焊接工艺参数见表2,但不必预热。
表2 堆焊过渡层工艺参数
电源极性焊接电流
I/A
电弧电压
U/V
焊接速度
v/cm·min-1
气体流量
Q/L·min-1
焊丝伸出长度
h/mm
焊丝直径
d/mm
熔滴过
渡形式
直流反接28032023382535202515 1.2喷射过渡
3.5 时效处理
对齿轮的所有主要受力焊缝进行20%超声波抽探,Ⅱ级合格后,对齿轮整体再进行消除应力时效处理。
4 工艺验证
按上述工艺规程,目前已生产出十几种产品的数十个合金钢齿轮,无论是齿轮焊后对焊缝的超声波检查,还是齿轮装到压力机后进行的压力机满负荷试验,均符合设计要求。
5 结束语
对于碳当量较高的42CrM o合金钢齿轮的焊接,采用在齿圈内径上堆焊过渡层的方法解决合金钢的焊接裂纹,不失为一有效途径。
过渡层可采用细丝C O2焊的传统焊接方法,焊接过程中要严格控制预热温度。
该方法也可供其它难焊材料焊接时借鉴。
(收稿日期 2001 06 13)作者简介: 王宏正,1960年生,大学本科,高级工程师。
螺母凸焊工艺参数优化
哈尔滨电影机械厂(150086) 李 娜
哈尔滨哈飞汽车制造有限公司(150060) 衣明海
螺母凸焊工艺就是利用螺母上预制的凸点焊到另一块面积较大的零件上。
因为是凸点接触,提高了单位面积上的压力与电流,可用于厚度比超过1:6的零件焊接。
螺母凸焊后有足够的抗扭强度,在交变载荷作用下不会松动,产品质量好,生产效率高。
1 焊接工艺对凸焊螺母质量的影响
螺母凸焊有凸点压溃这一不同于点焊的特殊的工艺过程,使其焊接工艺参数的选择较之点焊工艺更为重要。
在通电焊接时,凸点处的电流密度最高,它在加热过程中很快被完全压溃。
这时,凸点处熔核的形成与加热速度有很大关系。
由于焊件较薄,面积又大,又有下电极的强烈散热作用,往往造成凸点被熔化压溃,而板件却没有熔化,也没有熔核形成的结果。
为了使这种不均衡的散热影响减到最小,就必须采用大的焊接电流,短的焊接时间进行焊接。
2 选择试片
凸焊螺母选择规格为M8,板厚2.5mm,材质为08钢。
该件板料厚,凸焊质量不稳,焊接压力高达5500N,会将凸点压溃。
而零件接触面扩大,电流密度降低,造
·
7
3
·
焊接 2001(11)
成加热温度不足,易脱落。
若在大压力下进一步加大电流,螺母整体加热,导致焊渣,产生飞溅,焊渣还会堵塞螺纹。
3 试验过程及确定试验水平
试验采用正交试验法,从大量的试验中挑选出具有代表性、典型性的试验点,合理安排试验过程。
(1)试验的考核指标:采用剥离试验检查螺母凸焊的焊接强度,测定使螺母剥离所需要的扭矩,以剥离时的扭矩考核螺母的凸焊程度。
(2)因素位级表:见表1。
表1 因素位级表
位级焊接电流
I/kA
焊接时间
t1/s
焊接压力
P/N
预压时间
t2/s
18.50.120000.4
29.00.1230000.6
310.50.1440000.8
(3)选用正交表:根据试验中影响因素有4个,位级3个,决定选用L9(34)正交表。
(4)确定试验设备:
固定凸焊机: W DN-200
微电脑控制箱:W DK-1B
控制箱编程器:W DK
焊接参数测量仪:HC-05
力矩扳手:W N101-1
压力测试仪:RF-31P
4 试验结果分析
试验做完后,得到螺母脱焊的抗扭力矩值,见表2,并对其进行试验结果分析。
比较各列的Ⅰ、Ⅱ、Ⅲ的大小,以第一列为例,Ⅰ<Ⅱ<Ⅲ,大致说明了焊接电流这个因素以位级3为最好,位级2次之,位级1最差。
其余各因素的位级比较与上同。
级差R的大小用来衡量试验中相应因素作用的大小,级差大的因素(例如第三列焊接压力),意味着它的三个位级对于抗扭强度的影响较大,通常是重要因素,而级差小的因素往往是不重要因素(例如第四列预压时间)。
由此次试验可见,对于螺母凸焊后抗扭力矩的影响作用,焊接压力是最重要的因素,焊接电流次之,焊
表2 试验结果分析
试 验 计 划
试
验
号
焊接电流
I/kA
焊接时间
t1/s
焊接压力
P/N
预压时间
t2/s
第一列第二列第三列第四列
试验结果
抗扭强度
M/N·m
18.50.120000.459
28.50.1230000.683
38.50.1440000.870
49.50.130000.888
59.50.1240000.474
69.50.1420000.663
710.50.140000.678
810.50.1220000.865
910.50.1430000.493
Ⅰ212225187226
Ⅱ225222264224
Ⅲ236226222223
R244773
Ⅰ+Ⅱ+Ⅲ
=673
=总和
注:Ⅰ、Ⅱ、Ⅲ———代表各列3个位级的试验结果的总和
R———代表各列最大值与最小值之差。
接时间为第三,预压时间为第四。
计算得到的最佳焊接工艺参数为:焊接电流10.5kA,焊接时间0.14s,焊接压力3×103N,预压时间0.4s。
在本次试验中,好的工艺参数是焊接电流10.5kA,焊接时间0.14s,焊接压力3×103N,预压时间0.4s,与计算结果相同。
本次试验中有4个3位级因素,可产生34=81个试验条件,由正交表选出的9个条件只是其中的一部分,即1/9。
然而,凭借正交表的正交性,这9个条件均衡分散在这81个试验条件中,它们的代表性很强,所以,直观分析得到好的工艺参数在全体81个试验条件中的效果会是相当好的,本次试验也证明了这一点。
5 结 论
通过这次试验,成功找到在影响螺母凸焊质量的4个因素中影响最大的因素(焊接压力)及最优工艺参数配合,并用于指导生产实践,提高了螺母凸焊质量的稳定性。
(收稿日期 2001 04 12)作者简介: 李 娜,1972年生,大学本科,助理工程师。
·
8
3
·焊接 2001(11)。