case盖(工艺参数优化)
壳盖注塑件模具结构优化设计及翘曲优化

时间、熔体温度和冷却时间。
关键词:优化设计;翘曲值;正交试验;工艺参数
中图分类号:TQ320.66
文献标识码:A
文章编号:1009-0134(2019)06-0110-04
0 引言
当塑料件与其他零件有配合关系时,为了保证配合 的精度,对产品的翘曲有很高的要求。塑料制品成型过 程是一个动态的多因素非线性耦合的过程,该过程中各 个因素的变动都对产品的质量产生一定的影响。在生产 塑料件的模具结构中,浇注系统和冷却系统直接影响着 产品的质量,因此能够设计出合理的浇注和冷却系统成 为产品质量的基础保证[1]。在确定模具结构后,设计合 理的工艺参数是进一步提高产品质量的方法。传统的设 计方法很难解决这些问题,CAE技术则可在模具制造前 对模具设计方案和注塑成型工艺参数进行模拟分析,从 而预测出产品可能存在的缺陷,避免了传统的模具制造 完后在注塑机上反复试模和修模的困境[2]。
2.2 冷却系统优化设计
冷却系统设计直接影响着塑料产品的生产效率和产 品质量,因此,设计合理的冷却系统具有极其重要的意 义。在冷却系统中,管道数量、管道直径、管道与制品 的距离、管道中心距以及排列方式等直接影响着冷却系 统的冷却效果。为了得到相对合理的冷却系统,通过采 用控制变量法,把多因素问题转变成单因素问题。每次 改变其中一个因素,而控制其余几个因素不变,以此研 究被改变因素对研究对象的影响大小。本项目共设计了 九种不同的冷却方案,具体方案如下:管道数从两条、 四条、六条和八条进行布置;管道直径设计了10mm和 12mm;管道与制品距离设计了25mm和20mm;管道中 心距从50mm、30mm到15mm进行布置,排列方式设计 了Y向和X向。具体参数如表2所示。
方案1 方案2 方案3 方案4 方案5
多功能文具盒上盖注塑模设计附CAD图纸

多功能文具盒上盖注塑模设计附CAD图纸多功能文具盒上盖注塑模设计(附CAD图纸)多功能文具盒上盖塑模设计【摘要】分析了多功能文具盒上盖的结构和工艺特点,介绍了注塑模的结构与工作过程,设计了内侧抽芯多功能文具盒上盖注塑模,包括结构设计、参数计算和主要部件设计。
【关键词】注塑模、多功能文具盒上盖、内侧抽芯、。
【Abstract】The structure and technological process characteristics of the cover on the multi-function writing case,the structure and working process of the injection mould were introduced,the inside pull out the core mould for the cover on the multi-function writing case was designed,including design of the structure、parameter calculation and designing methods of main parks。
【Key word】injection mould、the cover on the multi-function writing case、the inside pull out the core。
引言近年来,随着塑料工业的飞速发展,塑料成型模具增长十分迅速。
高效率、自动化、大型、微型、精密、高寿命的模具在整个模具产量中所占的比重越来越大,塑料模具的地位也越来越重要,因此,对模具设计人员的要求也越来越高。
已有传统的平面设计转向三维设计和计算机辅助,设计周期也越来越短。
模具设计人员一般是在接到一部分图纸、一个样品或现在还很少使用的产品的模型后,便开始进行新模具的设计。
李洪涛_乘用车行李箱盖结构分析流程自动化

乘用车行李箱盖结构分析流程自动化李洪涛史建鹏东风汽车公司技术中心武汉430056摘要:本文利用HyperWorks二次开发接口,采用TCL语言开发了乘用车行李箱盖结构分析流程自动化,规范了乘用车行李箱盖CAE操作,显著提高了工作效率。
通过对比行李箱盖手工操作分析与流程自动化分析验证了二次开发的可靠性。
开发过程具有通用性与推广性。
关键词:HyperWorks二次开发TCL脚本语言乘用车行李箱盖1. 引言汽车CAE仿真是一个庞大的系统,分析工况种类繁多,边界条件复杂多变。
建模、仿真及后处理过程中若采用手工操作不但费时费神而且易出错,这给分析工程师们带来诸多不便,不能够把更多的精力投入到研发当中。
分析工程师们希望能够把分析流程进行自动化,规范化以提高分析效率。
Altair HyperWorks软件提供了丰富的二次开发接口,涉及到前、后处理各个方面,为用户进行自主开发从而实现流程自动化带来了极大的方便。
本文开发了乘用车行李箱盖结构分析流程自动化,开发过程具有通用性,可以推广到其他方面的应用。
2. 流程自动化开发过程HyperWorks二次开发是采用TCL脚本语言结合HyperWorks软件特有的命令语言进行编程来实现流程自动化。
TCL语言是一种比C/C++语言有着更高抽象层次的解释执行脚本语言,其简明,高效,可移植性好。
TCL几乎在所有的平台上都可以解释运行,功能强大。
特别是在信息产业、自动控制、机械电子等领域应用广泛。
TCL目前已成为自动测试中事实上的标准。
HyperWorks中的HyperMesh软件及HyperView软件自带有对象创建、查询、修改等命令,及图形界面工具包可以方便快捷的建立图形界面,这些都给流程自动化开发节省了大量时间。
2.1前处理流程自动化前处理流程自动化有两种途径一种是使用HyperMesh软件的宏(macro)功能结合HTML 语言及TK语言建立流程自动化,另外一种途径是使用HyperWork中的Process Studio建立流程自动化模板然后采用Process Manager加挂到HyperMesh软件菜单中。
高质量低成本的MuCell微发泡注塑成形技术
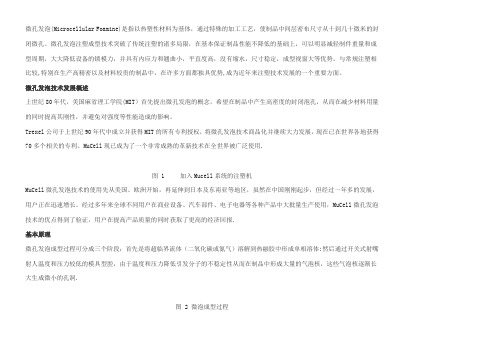
微孔发泡(Microcellular Foamine)是指以热塑性材料为基体,通过特殊的加工工艺,使制品中间层密布尺寸从十到几十微米的封闭微孔。
微孔发泡注塑成型技术突破了传统注塑的诸多局限,在基本保证制品性能不降低的基础上,可以明显减轻制件重量和成型周期,大大降低设备的锁模力,并具有内应力和翘曲小,平直度高,没有缩水,尺寸稳定,成型视窗大等优势。
与常规注塑相比较,特别在生产高精密以及材料较贵的制品中,在许多方面都独具优势,成为近年来注塑技术发展的一个重要方面。
微孔发泡技术发展概述上世纪80年代,美国麻省理工学院(MIT)首先提出微孔发泡的概念,希望在制品中产生高密度的封闭泡孔,从而在减少材料用量的同时提高其刚性,并避免对强度等性能造成的影响。
Trexel公司于上世纪90年代中成立并获得MIT的所有专利授权,将微孔发泡技术商品化并继续大力发展,现在已在世界各地获得70多个相关的专利。
MuCell现已成为了一个非常成熟的革新技术在全世界被广泛使用.图 1 加入Mucell系统的注塑机MuCell微孔发泡技术的使用先从美国、欧洲开始,再延伸到日本及东南亚等地区,虽然在中国刚刚起步,但经过一年多的发展,用户正在迅速增长。
经过多年来全球不同用户在商业设备、汽车部件、电子电器等各种产品中大批量生产使用,MuCell微孔发泡技术的优点得到了验证,用户在提高产品质量的同时获取了更高的经济回报.基本原理微孔发泡成型过程可分成三个阶段:首先是将超临界流体(二氧化碳或氮气)溶解到热融胶中形成单相溶体;然后通过开关式射嘴射人温度和压力较低的模具型腔,由于温度和压力降低引发分子的不稳定性从而在制品中形成大量的气泡核,这些气泡核逐渐长大生成微小的孔洞.图 2 微泡成型过程发泡后的制品横切面放大图如下,我们从中可以明显看到表层还是未发泡的实体层,这是由于模具温度较低,表面树脂冷却迅速,细胞核没有成长的时间,所以还是未发泡的实体。
WB焊线工艺技术资料
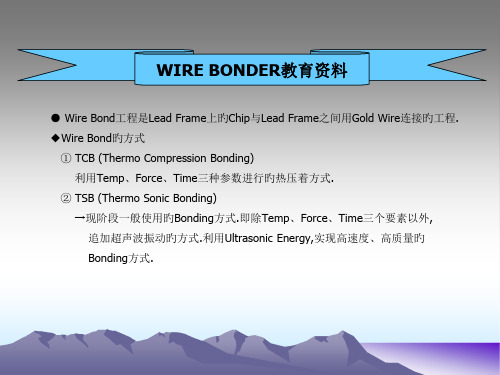
⑴ 参数设定
KEY
MAIN
1.BONDING SET UP
如下设定:
CLAMP CLOSE: [ **] g [ 80] g
⑵ Manual模式下,使用W/C键 执行闭合Clamp旳操作.
⑶ 调整VR2 使Tension Gauge旳测量成果到达”80g±5g”.
⑷ 参数设定
CLAMP CLOSE: [ **] g [ 10] g
超声波 发生器
*主要:超声波振動旳安定化 Torque Wrench
装配Capillary时拧紧Screw,管理 Torque Tool冶具
管理安装Capillary旳長度,专用JIG.
4 . Cut Wire Clamp & Spark Rod调整
4-1. Wire Clamp调整措施
1.准备 必要JIG: Tension Gauge (150g) : 示波器 : 扩展板 (HDV-550 )
按下列条件模拟设定
KEY SUB MAINTENNANCE
W/C OPEN: [ ①] g [ 60] g CLOSE: [ ②] g [ 80] g Interval: [ 100] ms
HEAD1
4-1-5-1. Cut Clamp OPEN 调整
将①旳值分别设定为”-20,-15,-10,-5,0,5,10,15,20”这九个数值来确认波形.从中选定波形振幅最小旳所 相应旳数值. 再将选定旳数值±2g 反复进行波形确认,从而选定最适合旳参数值.
Tension Gauge
⑴ 参数设定
KEY
MAIN
1.BONDING SET UP
如下设定: CLAMP OPEN: [ **] g [ 60] g
基于正交试验的汽车油箱口盒冲压成形工艺参数优化

基于正交试验的汽车油箱口盒冲压成形工艺参数优化采用正交试验设计方法综合评估了冲压过程中的压边力、模具间隙和板材尺寸对汽车油箱口盒冲压成形质量的影响,通过对试验数据的分析,找到最优的工艺参数组合,所得结论对汽车油箱口盒冲压工艺的设计具有指导意义。
标签:汽车油箱口盒;冲压工艺参数;正交试验引言汽车覆盖件的可成形程度和成形质量主要取决于其模具系统(凸模、凹模、压边圈、拉深筋等)和冲压工艺参数(润滑油、压边力、冲头速度、凸凹模间隙等)[1-2]。
实际生产中,当模具系统的参数已确定时,则仅能对冲压工艺参数进行调节。
由于冲压工艺参数对汽车覆盖件成形质量具有较大影响,人们对此已展开了大量的研究[ 3-5]。
以有限元为理论基础的金属板材冲压成形CAE分析技术已经在汽车设计制造中得到广泛应用,通过数值模拟技术可对汽车覆盖件冲压工艺做出定性指导并得出一些有益结论。
文献[6]运用Dynaform进行有限元模拟分析了压边力、凹模圆角半径、凸模圆角半径对汽车油箱成形极限的影响。
文献[7]利用有限元模拟方法,研究了压边力、摩擦系数、冲压速度及板料尺寸对汽车后端板加强件成形质量的影响。
文献[8]利用自主开发的商品化冲压成形CAE软件研究了汽车外覆盖件表面破裂缺陷产生的原因并进行精确预示。
目前,汽车覆盖件冲压工艺数值模拟技术尚存在缺乏定量精度等不足,为获得质量优异的汽车覆盖件,仍然需要进行反复的试验调整,而合理的试验设计方法在一定程度上可以减少反复试凑的盲目性,能以较少的试验次数得到试验范围内较优的工艺组合。
文章以一汽海马汽车有限公司某车型的油箱口盒为例,采用正交试验进行优化研究,以提高产品的质量及合格率,从而降低生产成本。
1 正交试验方案设计正交试验设计利用数理统计学与正交性原理从大量的试验点中挑选适量的具有代表性、典型性的点,应用正交表合理安排试验。
正交试验设计方法中所选择的试验对每个因素和因素的每个水平都为均匀分配,此外,还需保证每个因素的水平以相同的次数出现,且任何两个因素的搭配出现的次数相同。
易拉盖制作及应用

4。EOE成型过程:
第1站:波模、代号刻字(D1/D2)
第2站:纽模、止划点、手指槽
第3站:纽模整形
第4站:加强樑成型
第5站:切线成型、拉环成型
第6站:拉环组装
第7站:凸、刻字
第8站:起拱(汽水盖)
第三部分 . 易开盖的应用
1、“3片罐”及热充填饮料工艺:
偏小– 轧头将CH拉会保证罐盖深度,使CH太短,无法确保 卷封的密封性。
2)卷缘高度:
偏大 – CH太长,导致CH划破BH,造成泄露。 偏小 – CH太短,无法确保卷封的密封性。 同时,对卷封下盖时有影响。
3)卷缘外径:
偏大 – 下盖时卡盖,也可能CH太短,无法确保卷封的 密封性,。
偏小 – 可能CH太短,也可能无法使罐与EOE配合好。
规格 应用 开启形式
用途及一般工艺特点
206 平盖
209
RPT SOT
FA
A.配套空罐为马口铁焊接而成---俗称“三片罐”。
B.饮料需要高温充填(95℃)和高温杀菌(121℃,30分钟)
C.需要承受常温下饮料罐内部的真空而不瘪罐。
D.饮料成份较复杂,通常使用空罐卷封EOE后采取抗腐蚀处理 ---- 补涂 。对EOE之内涂层完整性要求高。
第一部分
基础知识
1. 易开盖名称
Easy Open End---- 易开盖
简称: EOE
Basic Shell ---- 基本盖
简称: BS
Ring Pull Type ---- 拉环型
简称: RPT
Stay On Tab ---- 保留型(环保盖) 简称: SOT
Full Appearance ----全开型
舱口盖制作工艺介绍

舱口盖制作工艺介绍1. 概述舱口盖是一种用于密封船舶、飞机、火车或工业设备舱口的覆盖物,通常由金属或复合材料制成。
舱口盖的主要功能是保护舱口免受外部环境的侵犯,并确保舱内压力保持稳定。
在本文中,我们将介绍舱口盖的制作工艺,包括材料选择、制作流程以及主要的检验标准。
2. 材料选择舱口盖的制作材料可以根据具体的应用需求进行选择。
常见的舱口盖材料包括金属和复合材料。
金属舱口盖通常由铝合金、不锈钢或钛合金制成。
这些材料具有较高的强度和耐腐蚀性能。
复合材料舱口盖的制作材料主要是碳纤维或玻璃纤维增强的环氧树脂。
复合材料具有优异的强度和轻量化的特点,适用于需要减轻重量的舱口盖应用。
3. 制作流程舱口盖的制作流程包括以下几个关键步骤:3.1 设计和制定工艺方案在制作舱口盖之前,需要进行详细的设计和工艺方案制定。
设计人员需要根据舱口的尺寸、形状和功能要求进行设计,并制定相应的制作工艺方案。
3.2 材料准备根据设计要求,选择合适的材料,并进行切割和加工。
金属材料可以通过切割机和折弯机进行加工,而复合材料则需要进行纤维预浸、层压和固化等工艺步骤。
3.3 制作舱口盖外壳根据设计图纸,使用相应的工具和设备进行舱口盖外壳的制作。
金属材料可以进行切割、焊接和折弯等工艺,而复合材料则需采用热压或自动层压机进行制作。
3.4 安装密封件和连接件在舱口盖外壳制作完成后,需要根据设计要求将密封件和连接件安装到舱口盖上。
密封件的选择应根据舱口盖的使用环境和要求进行,常见的密封方式包括橡胶密封条、实心橡胶垫片和涂层密封等。
3.5 表面处理和涂装舱口盖的表面处理和涂装可以提高其耐腐蚀性和外观质量。
金属材料可以进行除锈、喷砂和喷涂等处理,而复合材料则通常采用涂覆树脂或进行光面抛光。
3.6 检验和质量控制制作完成的舱口盖需要进行严格的检验和质量控制。
常用的检验方法包括外观检查、尺寸测量和压力测试等。
根据相关标准和规范,确保舱口盖的性能和质量符合要求。
- 1、下载文档前请自行甄别文档内容的完整性,平台不提供额外的编辑、内容补充、找答案等附加服务。
- 2、"仅部分预览"的文档,不可在线预览部分如存在完整性等问题,可反馈申请退款(可完整预览的文档不适用该条件!)。
- 3、如文档侵犯您的权益,请联系客服反馈,我们会尽快为您处理(人工客服工作时间:9:00-18:30)。
Φ14mm 长60mm Φ10mm 长38mm Φ8mm 长40mm
Φ12mm 长100mm Φ12mm 长80mm Φ6mm 长75mm
4
塑胶材料介绍 Hostalen GD 6250 HDPE
热 传 导 率: 最大剪切率: 最大剪切力: 熔 融 密 度: 比 热: 熔融指数: 0.2700 W/m/degC 65000 1/s 0.220000 MPa 0.73817 kg/cm^3 3000 J/kg/degC 1.85 g /10min 最小料温: 180.000000 最大料温: 280.000000 推荐料温: 220.000000 推荐模温: 40.000000 止流温度: 112.000000 顶出温度: 100.000000 deg.C deg.C deg.C deg.C deg.C deg.C
17
改善工艺方案介绍 (一)
18
工艺条件:
注塑温度:220度 模具温度:40度 最大流动速率:340cm^/sec 填充时间:0.6秒 保压压力:52Mpa
19
填充时间
改善工艺的填充时 间为0.6秒。
20
料流前锋分度分布:
提高填充速度,缩 短填充时间可以有效地 改善成型温度。 改善前温度112度, 现在是157度。
P V T 曲 线
粘 度 曲 线
5
工艺条件:
注塑温度:220度 模具温度:40度 填充时间:1.2秒 最大流动速率:170cm^/sec 保压压力:43Mpa
6
充填时间:
填充时间1.236秒, 图示的不同颜色表示流 动前锋到达该位置所需 的时间。 由于多型腔的布排 是完全对称的,因此, 流动过程中各型腔的平 衡性可以得到保证。 从图示还可以看出 单个型腔的流动也基本 平衡。
7
流动前沿温度分布:
最低温度112度, 出现在瓶盖的连接部分。 材料的止流温度112度, 因此,很有可能出现短 射现象,即便能够勉强 填充满整个型腔,相应 部位的产品质量也无法 得到保证。 分析原因:连接部 位最小壁厚只有0.15mm, 熔胶通过时热量损失较 大。
8
最大压力时刻:
所需的最大注射压 力为62Mpa,出现在0.8 秒熔胶通过连接部位时。
21
转换时刻压力分布:
所需的最大注射压 力为65.4Mpa,同样存 在连接处压力梯度大的 问题。
22
体积收缩率二)
24
工艺条件:
注塑温度:220度 模具温度:40度 最大流动速率:400cm^/sec 填充曲线: 400
cm^/sec
该段通过 连接部分
2
型腔结构介绍:
一模十六腔,自然平衡热 流道点浇口的浇注系统。
3
分析模型的简化处理:
为了保证分析 的准确度,单个型 腔的单元数高达六 千多个,再此运用 了软件的简化分析 功能(仅限型腔结 构对称),实践证 明该简化并不丧失 分析精度。 不同的颜色代 表熔胶流经的倍数。 因此,尽管只显示 两腔的结果,实际 反应的是十六腔的 真实情况。
52 1 1.6 1.9
sec
25
填充时间:
填充时间达到1.9秒, 但主要用在成型瓶盖的 两边,相反在通过连接 部位的时间更短。
26
料锋前沿温度:
由于速度提高到 400cm^/sec,连接部分 的温度较前两方案都高。
27
总
结
从以上分析我们可以得出一下结论: 产品存在的主要问题是熔胶通过连接部分时的温度下降太快,为 此我们分析其原因认为完全可以从工艺的角度解决问题——提高注塑 速率。 熔胶通过连接部分时的速率在350~400cm^3/sec时,可以保证相 应部位的成型温度。
瓶盖注塑分析报告
1
说明
分析目的:瓶盖热流道系统分析设计,确保产品质量 原始资料:产品三维模型、材料牌号
BP公司5102GB型HDPE LG公司B4020型HDPE
由于材料库中没有相应牌号的材料,根据材料熔融指数为2的 条件,找到最为接近的Targor公司的Hostalen GD 6250型HDPE(熔 融指数1.85)。可能会由于材料性能差异的原因引起一定的分析误 差。
通过连接部 分时刻
15
凝固时间:
产品成型周期大致 为10秒左右,浇口部位 最后冷却。
16
总
结
该产品的最大问题是连接部分的壁厚较薄(最薄处0.15mm),该 部位成型温度接近熔胶的不流动温度,填充较为困难,产品质量难以 得到保证。 针对以上问题我们提供一下改善方案: 1、工艺改善:提高注塑速率,尤其是熔胶通过连接处时的速率; 2、产品结构改善:适当增加连接处的厚度;
9
转换时刻压力分布:
压力损失主要出现在 连接部位,压力梯度大, 不利于最终产品的质量。
10
困气位置:
图示圆点为气泡可 能形成的的地方,大部 分都在产品的末端,有 利于排气。
11
熔接线:
A
该产品的主要熔接 线可能出现在图示的黑 色曲线部位,A区域的 成型温度有所下降,可 能会形成可见熔接线。
主要熔接线
12
填充结束时刻凝固率分布:
产品填充结束时刻 时,连接部分的凝固层 已达50%以上,上盖部 分较难正常保压。
13
体积收缩率:
上盖和下盖的收缩 率严重不均,主要原因 是产品结构造成的。 考虑到上盖收缩 率虽大但比较均匀的特 点,可以考虑尺寸缩放 进行解决。
14
锁模力:
最大锁模力115ton。 填充末时刻
考虑到改善的可操作性,我们仅从工艺的角度进行了深入分析。 至于一模的腔数问题,分析证明16腔没有问题,如贵公司认为太 少,可进一步验证。 当然如果条件允许适当增加连接处壁厚可从根本上解决填充困难 地问题。
28