五大工具之一_SPC统计过程控制
IATF16949五大核心工具简介及五大工具关系总结
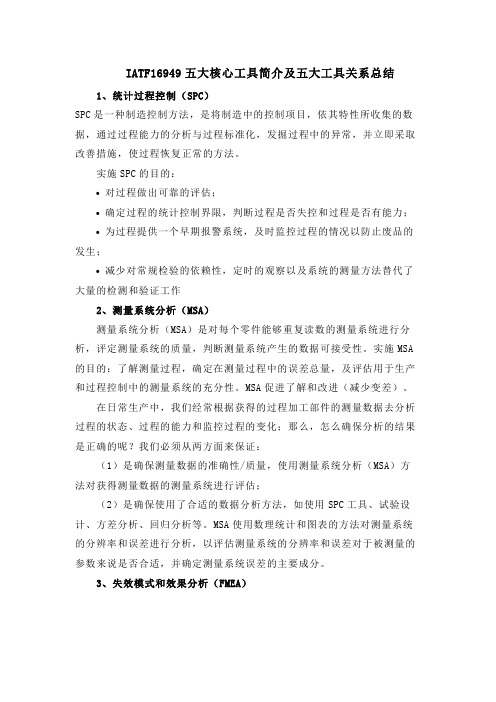
IATF16949五大核心工具简介及五大工具关系总结1、统计过程控制(SPC)SPC是一种制造控制方法,是将制造中的控制项目,依其特性所收集的数据,通过过程能力的分析与过程标准化,发掘过程中的异常,并立即采取改善措施,使过程恢复正常的方法。
实施SPC的目的:•对过程做出可靠的评估;•确定过程的统计控制界限,判断过程是否失控和过程是否有能力;•为过程提供一个早期报警系统,及时监控过程的情况以防止废品的发生;•减少对常规检验的依赖性,定时的观察以及系统的测量方法替代了大量的检测和验证工作2、测量系统分析(MSA)测量系统分析(MSA)是对每个零件能够重复读数的测量系统进行分析,评定测量系统的质量,判断测量系统产生的数据可接受性。
实施MSA 的目的:了解测量过程,确定在测量过程中的误差总量,及评估用于生产和过程控制中的测量系统的充分性。
MSA促进了解和改进(减少变差)。
在日常生产中,我们经常根据获得的过程加工部件的测量数据去分析过程的状态、过程的能力和监控过程的变化;那么,怎么确保分析的结果是正确的呢?我们必须从两方面来保证:(1)是确保测量数据的准确性/质量,使用测量系统分析(MSA)方法对获得测量数据的测量系统进行评估;(2)是确保使用了合适的数据分析方法,如使用SPC工具、试验设计、方差分析、回归分析等。
MSA使用数理统计和图表的方法对测量系统的分辨率和误差进行分析,以评估测量系统的分辨率和误差对于被测量的参数来说是否合适,并确定测量系统误差的主要成分。
3、失效模式和效果分析(FMEA)潜在的失效模式和后果分析(FMEA)作为一种策划用作预防措施工具,其目的是发现、评价产品/过程中潜在的失效及其后果;找到能够避免或减少潜在失效发生的措施并不断地完善。
实施FMEA的目的:能够容易、低成本地对产品或过程进行修改,从而减轻事后修改的危机。
•找到能够避免或减少这些潜在失效发生的措施;4、产品质量先期策划(APQP)APQP是用来确定和制定确保产品满足顾客要求所需步骤的结构化方法。
IATF16949五大核心工具APQP、FEMA、MSA、PPAP和SPC的关系

这里需要说明的是控制计划,是APQP策划的结果,在这个结果中必然要用到测量工具,而这些测量工具是否能满足对过程测量的需要,需要用MSA来进行分析。
简单地说控制计划中所涉及的测量器具都应该做MSA,然后在最初的控制计划中,也就是试生产的控制计划中,策划的测量工具或所选用的SPC未必能有好的效果,因些可能会进行调整和改进,最后形成正式生产的控制计划。
APQP是在向整车厂提供新产品的时候,作为零部件公司必须要做的一项工作,意在产品未进行生产之前把所有的问题解决掉,所以它是个复杂的过程,也是需要几个来回反复才会成为最后策划的结果。
FMEA则是在APQP的二三阶段时进行的失效模式分析,包括产品和过程,这里最重要的一点是这个时候产品并未生产出来;
而是一种潜在的可能性分析,很多企业总是不习惯这一点,总是把它当成已经在生产的产品去分析。精益生产促进中心。
五大质量工具是TS16949的核心,是经过证明适用于汽车行业的质量工具,对于提高汽车行业的质量管理水平和竞争力,将起到重要作用。
第二、IATF16949 五大工具的关系
这个话题如果没有实践的人一定是弄不清楚的,就算是有实践的人也未必能弄清楚,因为他们的相互交错。
福特用了一百年的时间画出的经典的APQP网络图,可见其用心之最。在这里我对五大工具做简单的描述希望能给大家一个基本的概念。
5、生产件批准程序(PPAP)
生产件批准程序为一种实用技术,其目的是在第一批产品发运前,通过产品核准承认的手续,验证由生产工装和过程制造出来的产品符合技术要求。
实施PPAP的目的:
·确定供方是否已经正确理解了顾客工程设计记录和规范的所有要求。
五大工具-SPC

28
11. MINITAB输出图(一次性取样)
路径: 统计/质量工具/ 能力分析/正态
PPM: Parts Per Million 百万分之一
虽然样本数据都在规格内, 但Cpk=0.83, PPM>USL竟然能达到22605.39
TS16949五大工具
TS16949五大工具 1. 产品质量先期策划(APQP) 2. 潜在失效模式与后果分析(FMEA) 3. 测量系统分析(MSA)
4. 统计过程控制(SPC)
5. 生产件批准程序
1
SPC(统计过程控制) Statistical Process Control
2
ห้องสมุดไป่ตู้
一.SPC的定义
37
15
二.Cpk工序能力
16
1. 定义及目的
CP,CPK---短期过程能力指数,
用作评估工序操作状态稳定性及工序能力能否符合规格要求的指標, 即将过程能力定量化评估出来的尺度。
目的: 1.改善工序生产力及产品质量. 2.帮助了解工序制造公差. 3.评估设备工序能力能否达到要求. 4.比较不同设备之工序能力.
ID1060成品内阻, USL=35
ID971成品内阻, Cpk=1.51
实际均值=12.1
Average=L=380,
但后面出现小柱形分布,异常点无法识别出导致流出!
规格需要更加的合理!
均值=263.45, 标准差=13.9, 那么合理的上限应该是
=263.45+3*13.9=305
16. 案例分享2
17
2. 正态分布
过程能力指数是在假设质量特征分布在正态分布的条件下 进行的。
TS16949五大工具之五SPC
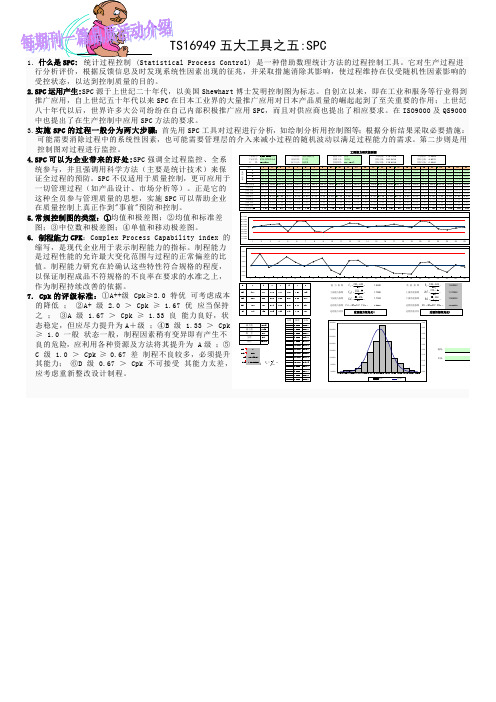
1.什么是SPC:统计过程控制(Statistical Process Control)是一种借助数理统计方法的过程控制工具。它对生产过程进行分析评价,根据反馈信息及时发现系统性因素出现的征兆,并采取措施消除其影响,使过程维持在仅受随机性因素影响的受控状态,以达到控制质量的目的。
2.SPC运用产生:SPC源于上世纪二十年代,以美国Shewhart博士发明控制图为标志。自创立以来,即在工业和服务等行业得到推广应用,自上世纪五十年代以来SPC在日本工业界的大量推广应用对日本产品质量的崛起起到了至关重要的作用;上世纪八十年代以后,世界许多大公司纷纷在自己内部积极推广应用SPC,而且对供应商也提出了相应要求。在ISO9000及QS9000中也提出了在生产控制中应用SPC方法的要求。
5.常规控制图的类型:①均值和极差图;②均值和标准差图;③中位数和极差图;④单值和移动极差图。
6.制程能力CPK:Complex Process Capability index 的缩写,是现代企业用于表示制程能力的指标。制程能力是过程性能的允许最大变化范围与过程的正常偏差的比值。制程能力研究在於确认这些特性符合规格的程度,以保证制程成品不符规格的不良率在要求的水准之上,作为制程持续改善的依据。
3.实施SPC的过程一般分为两大步骤:首先用SPC工具对过程进行分析,如绘制分析用控制图等;根据分析结果采取必要措施:可能需要消除过程中的系统性因素,也可能需要管理层的介入来减小过程的随机波动以满足过程能力的需求。第二步则是用控制图对过程进行监控。
4.SPC可以为企业带来的好处:SPC强调全过程监控、全系统参与,并且强调用科学方法(主要是统计技术)来保证全过程的预防。SPC不仅适用于质量控制,更可应用于一切管理过程(如产品设计、市场分析等)。正是它的这种全员参与管理质量的思想,实施SPC可以帮助企业在质量控制上真正作到"事前"预防和控制。
PPAP-SPC-MSA-FEMA-APQP五大质量工具简介

1、分析过程 · 本过程应做些什么? 2、维护过程 · 会出现什么错误 · 监控过程性能 · 本过程正在做什么? · 查找偏差的特殊 · 达到统计控制状态? 原因并采取措施 · 确定能力 计划 实施 计划 实施 措施 研究 措施 研究 计划 实施 措施 研究 3、改进过程 · 改进过程从而更好地 理解普通原因变差 · 减少普通原因变差
APQP各阶段(过程)输入输出
产品设计和开发阶段:
2.产品设计 和开发
1.DFMEA 2.可靠性和装配设计 3.设计验证 4.设计评审 5.制造样件—— 控制计划 6.工程图纸 7.工程规范
1.设计目标 2.可靠性和 质量目标 3.初始材料清单 4.初始过程流程图 5.特殊产品和过程 特性的初始清单 6.产品保证计划 7.管理者支持
PPAP,SPC,MSA,FEMA,APQP五大质量工具简介
五大核心工具简称
1.APQP: Advanced Product Quality Planning and Control Plan 产品质量先期策划和控制计划 2. FMEA: Potential Failure Mode and Effects Analysis 潜在的失效模式与后果分析 3. SPC: Statistical Process Control 统计过程控制
失效链
水箱支架断裂
水箱后倾
水箱与风扇碰撞
水箱冷却水管被风扇刮伤
水箱冷却液泄漏
冷却系统过热
发动机气缸损坏
汽车停驶
FMEA
潛在失效模式與后果分析作業序列
項目 /功能(要求)
潛在 失效模式
潛在 失效后果
潛在原因/ 失效機制
現行設計 (製程)管制
质量五大工具
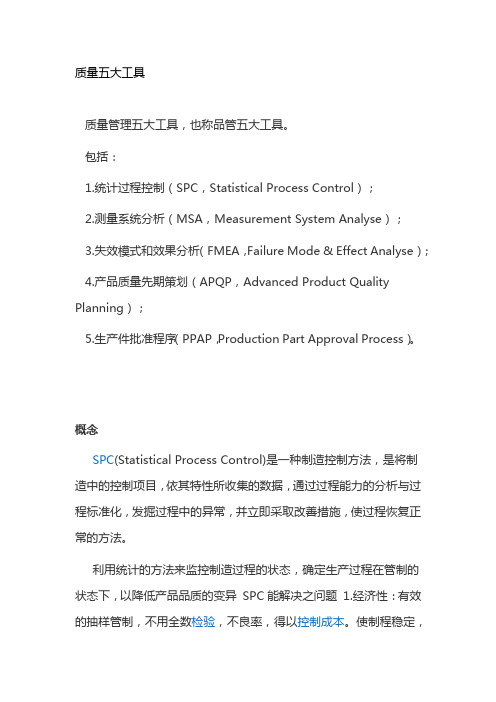
质量五大工具质量管理五大工具,也称品管五大工具。
包括:1.统计过程控制(SPC,Statistical Process Control);2.测量系统分析(MSA,Measurement System Analyse);3.失效模式和效果分析(FMEA,Failure Mode & Effect Analyse);4.产品质量先期策划(APQP,Advanced Product Quality Planning);5.生产件批准程序(PPAP,Production Part Approval Process)。
概念SPC(Statistical Process Control)是一种制造控制方法,是将制造中的控制项目,依其特性所收集的数据,通过过程能力的分析与过程标准化,发掘过程中的异常,并立即采取改善措施,使过程恢复正常的方法。
利用统计的方法来监控制造过程的状态,确定生产过程在管制的状态下,以降低产品品质的变异SPC能解决之问题1.经济性:有效的抽样管制,不用全数检验,不良率,得以控制成本。
使制程稳定,能掌握品质、成本与交期。
2.预警性:制程的异常趋势可即时对策,预防整批不良,以减少浪费。
3.分辨特殊原因:作为局部问题对策或管理阶层系统改进之参考。
4.善用机器设备:估计机器能力,可妥善安排适当机器生产适当零件。
5.改善的评估:制程能力可作为改善前後比较之指标。
目的·对过程做出可靠有效的评估;·确定过程的统计控制界限,判断过程是否失控和过程是否有能力;·为过程提供一个早期报警系统,及时监控过程的情况以防止废品的发生;·减少对常规检验的依赖性,定时的观察以及系统的测量方法替代了大量的检测和验证工作计算表Pp 和Ppk不合格率MSA测量系统分析(MSA)是对每个零件能够重复读数的测量系统进行分析,评定测量系统的质量,判断测量系统产生的数据可接受性。
MSA(MeasurementSystemAnalysis)使用数理统计和图表的方法对测量系统的分辨率和误差进行分析。
质量管理五大工具表格模板

质量管理五大工具是指在质量管理领域中常用的五种工具,包括统计过程控制(SPC)、测量系统分析(MSA)、失效模式和效果分析(FMEA)、产品质量先期策划(APQP)和生产件批准程序(PPAP)。
以下是一些质量管理五大工具的表格模板:
1.
统计过程控制(SPC)表格模板:
2.
1.
测量系统分析(MSA)表格模板:
2.
1.
失效模式和效果分析(FMEA)表格模板:
2.
1.
产品质量先期策划(APQP)表格模板:
2.
1.生产件批准程序(PPAP)表格模板:
生产件批准程序(PPAP)表格模板通常包括以下内容:产品名称、顾客名称、零件编号、零件名称、提交时间、生产地点、生产数量、审核结论、审核员签名和备注等。
根据实际需要,还可以添加其他相关信息。
统计过程控制(SPC)在质量控制中的应用

统计过程控制(SPC)在质量控制中的应用摘要:随着全球经济的飞速发展,为了在越来越激烈的市场竞争中脱颖而出,企业必须不断提高产品质量、降低生产成本并提升生产效率。
统计过程控制(SPC)做为质量管理五大工具之一的重要工具,可以事前预防产品在生产中产生的缺陷,提醒管理人员采取有效的措施来排除异常,从而保证产品的质量。
作为一种有效的质量控制方法,已得到广泛应用。
本文简述了SPC的发展及实施必须经过的两个阶段,帮助企业理解SPC在实施中的挑战策略和企业实施SPC的益处。
关键词:统计过程控制,质量控制,过程能力分析0引言SPC是统计过程控制(Statistical Process Control)的简称,就是应用统计方法对过程中的各个阶段进行监控,从而达到改进与保证质量的目的。
它强调通过过程的预防来减少或避免出废品、次品。
它着眼于全系统、全过程,要求全员参加;它要求用科学方法(主要是统计技术,尤其是控制图理论)来保证全过程的预防,不仅用于生产过程,而且可用于服务过程和一切管理过程。
1统计过程控制(SPC)发展美国休哈特博士是SPC的奠基人,他在20世纪20年代首创过程控制理论以及监控过程的工具之一控制图,将统计学应用于质量控制,构建了控制图的基本框架,推动了质量控制的革新。
休哈特的同事戴明博士提出戴明循环,也称PDCA 循环,强调持续改进的过程。
它将SPC与持续改进紧密结合,成为质量管理的重要工具。
而国际标准化组织(ISO)也将 SPC 作为 ISO9000质量体系改进的重要内容,QS9000 认证也将SPC列为一项重要指标。
SPC处于六西格玛DMAIC五个阶段中的最后一个阶段,C(Control)阶段,即控制阶段,它在六西格玛理论中占有非常重要的地位。
现今,SPC 理论已经发展与计算机技术的结合日益紧密,在企业内已经非常广泛、深入统计过程控制的应用。
SPC不仅仅用于监控和控制生产过程,还可应用于改进和优化业务流程。
- 1、下载文档前请自行甄别文档内容的完整性,平台不提供额外的编辑、内容补充、找答案等附加服务。
- 2、"仅部分预览"的文档,不可在线预览部分如存在完整性等问题,可反馈申请退款(可完整预览的文档不适用该条件!)。
- 3、如文档侵犯您的权益,请联系客服反馈,我们会尽快为您处理(人工客服工作时间:9:00-18:30)。
五大工具之一_SPC统计过程控制
CPK与PPK的区别?
在制造行业中,大家肯定不乏听到顾客要求过程能力达到CPK≥1.33或PPK≥1.67的要求,但
是,CPK具体代表什么,PPK又具体代表什么,它们各自在什么时候进行使用最佳.Cpk 与Ppk 的区别
到底是什么呢?
一、CPK是过程能力指数,也就是说它所表示的是过程本身所具有的能力,是一种理想的状态(正
态分布)下的指数。
PPK是SPC中控制图中用来计算工序能力或叫过程能力的指数,是指考虑过程有偏差时,样本
数据的过程性能。
它们虽然两者都是依据过去所策划的方法所收集的数据计算出来的,但PPK是为了获得过去一
段时间内的过程的表现,考虑了所有数据之间的变差;而CPK则提出了子组内数据之间的变差(通过
使用子组均值来剔除),仅考虑子组之间的变差。说得通俗易懂一点,PPK和CPK的区别就好像是
一个人的工作表现和工作能力之间的差别。
二、有些书籍或有人说CPK是短期能力指数,PPK是长期性能指数, 也有人说, CPK是长期
能力指数,PPK是短期性能指数;又有人说PPK是初始能力指数,因为在生产初期需要计算PPK值
以评估过程能力,可生产初期一般是较短的时期,等等的说法,其实,过程能力的长短之说,早已经是
过去时,现在也没有人刻意的这样去说.并没有什么实际意义.
三、Cpk是要求过程系统在稳态条件下进行计算(前提);(如果不是在稳态条件进行计算,那么
将计算出非真实的过程能力,告诉我们一个虚假或者说错误的能力值);而Ppk不一定要求在稳态条件
下计算,也可以反映出系统当前的实际过程能力状态。
其实我们要想真正明白它们的区别,那还得从其计算公式谈起,CPK如下公式:
只有当过程是稳态统计受控时才可以用这种经验公式,所以计算CPK之前要进行稳定性分析。
(MINITAB可以快速实现,传统的EXCEL表格较难实现,目前主流的EXCEL格式并未进行正态分析) 。
当过程处于非稳定统计受控时就不能用这经验公式去计算其过程能力,这时就用总的标准差去计
算PPK值,如下公式:
总的标准差公式对任何数组都可以使用,因此任何过程的数据都可以计算PPK,包括过程不稳定
状态,当然如果我们已经确认过程是受控状态,我们可以用经验公式计算CPK是更容易些,实际上当
过程处理统计受控状态时,计算出的CPK与PPK值是相差很小的。
当然,也经常有用EXCEL表格中的“STDEV”公式去算标准差,再用它去计算“CPK”,实际上这
时计算出的不是过程CPK而是PPK。
所以,CPK与PPK不是从短期或长期角度来区分。而是看其计算时的标准差是怎么得来的,是
经验公式(指数使用查表得出)计算,还是总标准差公式计算。经验公式计算CPK是有条件的,即过程
是稳态的,但PPK是不需要条件的不管是短期还是长期,稳态还是非稳态。
通常来讲生产初期过程一般不稳定,所以计算PPK, 长期来讲一个过程也是不稳的,所以也用
PPK来衡量过程能力。当生产过程中某个短时间段是稳态时就可以计算CPK。
当然,无论是统计过程的CPK,还是PPK,重要的前提条件是MSA必须是受控状态,否则,所做的一切
都是惘然!
四、实例说明
1.以下是传统EXCEL表格计算的该抽样数据的CPK值
图一
通过查看上面(图一)CPK值及最终给出的结论,该过程CPK是1.57,判定过程可接受!(未对数据进
行正态性检验,就假想为过程处于稳态).
2.以下是Minitab软件计算的该抽样数据的CPK及PPK值:
a.首先查验数据是否服从正态分布:
图二
从以上图二可以看出,P值<0.005.故该数据不服从正态分布.不可以进行CPK数据分析.
先试看以下假想该数据是服从正态分布时的CPK值:
图三
从上图三可以看出,假想该数据是服从正态分布时,计算出CPK =1.77;PPK=0.85.
b.前面已通过对该组数据过正态性检验,P值<0.05,那么该过程不服从正态分布,想计算出该数据
的真正过程能力PPK值,如下图所示:
图四
从上图四可以看到,该过程统计的实际PPK=0.59.