Definition and Test Method of EPM20135S_20110115
碳13红外光谱仪示值误差测量不确定度评定

基金项目:重庆市市场监督管理局科研项目(项目编号:CQZJKY2018003)作者简介:宋海龙,男,高级工程师。
碳13红外光谱仪示值误差测量不确定度评定宋海龙 徐 阳 王耀弘 张亚军(重庆市计量质量检测研究院,重庆401123)摘 要:碳13红外光谱仪是一种测量幽门螺杆菌的医用测量仪器,其主要原理是通过测量人服药前后呼出气体中碳同位素丰度比的变化,来表征该人是否感染幽门螺杆菌。
本文通过对碳13红外光谱仪示值误差的不确定度进行分析评定,为该仪器的校准结果的可靠性提供参考依据。
关键词:碳13红外光谱仪;示值误差;不确定度中图分类号:P414 8 文献标识码:A 国家标准学科分类代码:460 4030DOI:10.15988/j.cnki.1004-6941.2020.10.036EvaluationofUncertaintyinMeasurementofIndicationErrorofCarbon13InfraredSpectrometerSONGHailong XUYang WANGYaohong ZHANGYajunAbstract:Carbon13infraredspectrometerisamedicalmeasuringinstrumentformeasuringHelicobacterpylori ItsmainprincipleistomeasurewhetherthepersonisinfectedwithHelicobacterpyloribymeasuringthechangeofcar bonisotopeabundanceratioinexhaledgasbeforeandaftertakingmedicine Thispaperanalyzesandevaluatestheuncertaintyoftheindicationerrorofthecarbon13infraredspectrometertoprovideareferenceforthereliabilityofthecalibrationresultsoftheinstrumentKeywords:carbon13infraredspectrometer;indicationerror;uncertainty0 引言碳13红外光谱仪是一种专用于测量幽门螺杆菌的仪器,其原理是利用同位素示踪原理以及红外探测原理进行测量的。
BERMAN-IRK-RUS-2013

Main Components of IDSS
Состав системы Case-based expert system
Rule-based expert system
Case-base
Rules
Data Base of equipment
Main Functions
Основные функции
Выявление причинно-следственного комплекса факторов обусловивших текущее состояние
Planning work to refine the causes for the current state, if necessary
The symbolic scheme of production process
Problems of Investigation
Задачи исследования
Wizards* for solution of problems
Мастера для решения задач
Case-based reasoning Прецедентный подход
Rule-based reasoning Продукционный подход
A set of rules
Decision-making by analogy
Принятие решения по аналогии
Множество продукций
и диагностирования.
• Definition the causes of failures and emergencies.
Определение возможных причин отказов и аварий.
EIA-364-13C_插拔力测试标准

EIA STANDARD TP-13C M ATING AND UNMATING FORCE TEST PROCEDURE FOR ELECTRICAL CONNECTORSEIA/ECA-364-13C (Revision of EIA-364-13B) JUNE 2006THE ELECTRONIC COMPONENTS SECTOR OF THE ELECTRONIC INDUSTRIES ALLIANCE ANSI/EIA-364-13C-2006NOTICEEIA Engineering Standards and Publications are designed to serve the public interest through eliminating misunderstandings between manufacturers and purchasers, facilitating interchangeability and improvement of products, and assisting the purchaser in selecting and obtaining with minimum delay the proper product for his particular need. Existence of such Standards and Publications shall not in any respect preclude any member or nonmember of EIA from manufacturing or selling products not conforming to such Standards and Publications, nor shall the existence of such Standards and Publications preclude their voluntary use by those other than EIA members, whether the standard is to be used either domestically or internationally.Standards and Publications are adopted by EIA in accordance with the American National Standards Institute (ANSI) patent policy. By such action, EIA does not assume any liability to any patent owner, nor does it assume any obligation whatever to parties adopting the Standard or Publication.This EIA Standard is considered to have International Standardization implication, but the International Electrotechnical Commission activity has not progressed to the point where a valid comparison between the EIA Standard and the IEC document can be made.This Standard does not purport to address all safety problems associated with its use or all applicable regulatory requirements. It is the responsibility of the user of this Standard to establish appropriate safety and health practices and to determine the applicability of regulatory limitations before its use.(From Standards Proposal No. 5136 formulated under the cognizance of the CE-2.0 National Connector Standards Committee.Published by©ELECTRONIC INDUSTRIES ALLIANCE 2006Technology Strategy & Standards Department2500 Wilson BoulevardArlington, VA 22201PRICE: Please refer to the currentCatalog of EIA Electronic Industries Alliance Standards and EngineeringPublicationsor call Global Engineering Documents, USA and Canada (1-800-854-7179)International (303-397-7956)All rights reservedPrinted in U.S.A.PLEASE !DON'T VIOLATETHELAW!This document is copyrighted by the EIA and may not be reproduced without permission.Organizations may obtain permission to reproduce a limited number of copies through entering into a license agreement. For information, contact:Global Engineering Documents15 Inverness Way EastEnglewood, CO 80112-5704 or callUSA and Canada (1-800-854-7179), International (303-397-7956)CONTENTSClause Page (1)1 Introduction (1)1.1 Scope (1)resources2 Test (1)2.1 Equipment3 Test specimen (1) (1)A3.1 Method (2)3.2 MethodB (2)procedure4 TestA (2)4.1 MethodB (2)4.2 Method5 Details to be specified (3) (3)6 Testdocumentation(This page left blank)TEST PROCEDURE No. 13CMATING AND UNMATING FORCE TEST PROCEDUREFORELECTRICAL CONNECTORS(From EIA Standards Proposal No. 5136, formulated under the cognizance EIA CE-2.0 Committee on National Connector Standards, and previously published in EIA-364-13B.)1 Introduction1.1 ScopeThis standard establishes a method to determine the forces required to mate and unmate electrical connectors or protective caps with connectors, connectors/sockets with gages or devices. Unless otherwise specified in the referencing document, method A shall be used.2 Test resources2.1 EquipmentThe test equipment shall consist of:2.1.1 Mounting fixtures that allow the specimens to be mounted in their normal manner.2.1.2 Force or torque gages, of suitable range for the connector size under test, so that readings will be in the middle 50% of the scale, where practicable, with a nominal full scale accuracy of +2%.2.1.3 Attachments and accessory type equipment as required to mate the test specimens and attach the force or torque gages (arbor press, etc.).2.1.4 Gage(s) or device(s) to mate the connector/socket with (applicable to method B only).3 Test specimen3.1 Method AThe specimen shall consist of a plug and a receptacle with all applicable contacts in place. All applicable hardware shall be assembled to the specimen including skirts, hoods, cable clamps, jackscrews, guide pins or sockets unless otherwise specified. The specimen shall not be lubricated or cleaned in any manner unless otherwise specified in the referencing document. If applicable the specimen shall be terminated as specified in the referencing document.3.2 Method BThe specimen shall consist of the connector/socket and the gage(s) or device(s) as specified in the referencing document. Unless otherwise specified in the referencing document, all applicable contacts and hardware shall be installed including skirts, hoods, cable clamps, guide pins, etc. The specimen shall not be lubricated or cleaned and active latches are to be deactivated unless otherwise specified in the referencing document. If applicable, the specimen shall be terminated as specified in the referencing document.4 Test procedure4.1 Method AUnless otherwise specified, the specimen shall be mounted to mounting fixtures by the normal mounting means.4.1.1 Mating force4.1.1.1 The two mating connectors shall be brought to a position where mechanical mating begins and the force or torque gage is at zero indication.4.1.1.2 The connectors shall then be fully mated or coupled at a rate of 25.4 millimeters/minute, unless otherwise specified in the referencing document, and the peak force or torque required for mating shall be recorded.4.1.2 Unmating forceThe mated connectors shall be fully unmated at a rate of 25.4 millimeters/minute, unless otherwise specified in the referencing document, and the peak force or torque required shall be recorded. 4.2 Method BThe fixtures required to hold the specimen and the specimen shall be attached to the force measuring system then the system shall be zeroed.4.2.1 Mating force4.2.1.1 The two mating components shall be brought to a position just before mechanical mating begins and the force measuring system is indicating zero.4.2.1.2 The gage/device shall then be fully mated to the connector/socket at a rate of 25.4 millimeters/minute, unless otherwise specified in the referencing document. The peak force required for mating prior to bottoming shall be recorded.4.2.2 Unmating forcesThe gage/device shall then be fully unmated from the connector/socket at a rate of 25.4 millimeters/minute unless otherwise specified in the referencing document. The peak force required for unmating shall be recorded.5 Details to be specifiedThe following details shall be specified in the referencing document:5.1 Number of specimens to be tested5.2 Measurements to be made; mating force, unmating force, or both5.3 Rates of mating and unmating, if other than specified in 4.1.1.2, 4.1.2, 4.2.1.2 and 4.2.25.4 Depth of mating if applicable5.5 Lubrication or cleaning, if required5.6 Wire type, gage, and length if applicable5.7 Applicable hardware5.8 Force or torque requirements5.9 Test conditions, if other than standard atmospheric5.10 Applicable to method B only: Details of the device(s) or gage(s) to be used for mating/unmating to the connector/socket, as well as the method and frequency of cleaning, if required6 Test documentationDocumentation shall contain the details specified in clause 5, with any exceptions, and the following:6.1 Title of test6.2Specimen description including part number if applicable6.3 If applicable, fixturing, gage details and gage part number6.4 Test equipment used, and date of last and next calibration6.5 Test procedure and method, if other than method A6.6 Values and observation6.7 Name of operator and date of testEIA Document Improvement ProposalIf in the review or use of this document, a potential change is made evident for safety, health or technical reasons, please fill in the appropriate information below and mail or FAX to:Electronic Industries AllianceTechnology Strategy & Standards Department – Publications Office2500 Wilson Blvd.Arlington, VA 22201FAX: (703-875-8906)Revision HistoryRevision letter Projectnumber Additions, changes and deletionsC SP-5136Original test procedure is now method A.Added Method B and paragraph 2.1.4, 3.2, 4.2, 5.10and 6.3.Revised paragraph 1.1, 4.1.1.2, 4.1.2, 5.2, 5.3, 6.2and 6.5.。
IEC 62321-5-2013 - 中文版
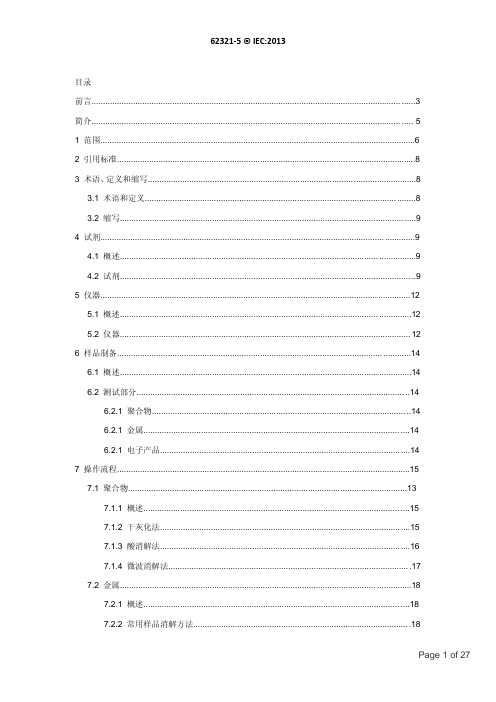
目录前言 (3)简介 (5)1范围 (6)2引用标准 (8)3术语、定义和缩写 (8)3.1术语和定义 (8)3.2缩写 (9)4试剂 (9)4.1概述 (9)4.2试剂 (9)5仪器 (12)5.1概述 (12)5.2仪器 (12)6样品制备 (14)6.1概述 (14)6.2测试部分 (14)6.2.1聚合物 (14)6.2.1金属 (14)6.2.1电子产品 (14)7操作流程 (15)7.1聚合物 (13)7.1.1概述 (15)7.1.2干灰化法 (15)7.1.3酸消解法 (16)7.1.4微波消解法 (17)7.2金属 (18)7.2.1概述 (18)7.2.2常用样品消解方法 (18)7.2.3含有Zr,Hf,Ti,Ta,Nb,W的样品 (19)7.2.4含有Sn的样品 (19)7.3电子产品 (19)7.3.1概述 (19)7.3.2王水消解 (20)7.3.3微波消解法 (20)7.4试剂空白溶液制备 (21)8校准 (21)8.1概述 (21)8.2校准溶液制备 (21)8.3建立校准曲线 (22)8.4样品测试 (23)9计算 (23)10精密度 (23)11质量控制 (26)11.1概述 (26)11.2检测限(LOD)和定量限(LOQ) (27)国际电工委员会__________电工产品—相关物质测定前言1)国际电工委员会(IEC)是一个世界性的标准化组织,它是由各个国家的电工委员会组成。
IEC 的目的是在电子电气领域内标准化有关的所有问题促进国际间合作。
为了实现这一目标和其它的活动,IEC公开出版国际标准、技术规范、技术报告、公开发行规范(PAS)和指导(此后均称作“IEC出版物”)。
它们的制订工作委托给技术委员会;任何国家对此项目感兴趣的IEC委员会均可参与制订工作。
与IEC相关联的国际组织、政府组织或非政府组织也可以参与制订工作。
IEC同国际标准化组织(ISO)根椐双方签立的协议,进行密切的合作。
ECE R13 第6版 第4次修订

}Rev.1/Add.12/Rev.6/Amend.4E/ECE/324E/ECE/TRANS/50530 December 2009AGREEMENTCONCERNING THE ADOPTION OF UNIFORM TECHNICAL PRESCRIPTIONSFOR WHEELED VEHICLES, EQUIPMENT AND PARTS WHICH CAN BE FITTEDAND/OR BE USED ON WHEELED VEHICLES AND THE CONDITIONS FOR RECIPROCAL RECOGNITION OF APPROVALS GRANTED ON THE BASIS OFTHESE PRESCRIPTIONS ∗/(Revision 2, including the amendments that entered into force on 16 October 1995)_________Addendum 12: Regulation No. 13Revision 6 - Amendment 4Supplement 2 to the 11 series of amendments: Date of entry into force: 24 October 2009UNIFORM PROVISIONS CONCERNING THE APPROVAL OF VEHICLES OF CATEGORIES M, N AND O WITH REGARD TO BRAKING_________UNITED NATIONS∗/ Former title of the Agreement:Agreement Concerning the Adoption of Uniform Conditions of Approval and Reciprocal Recognition of Approval for Motor Vehicle Equipment and Parts, done at Geneva on 20 March 1958.GE.09-}Rev.1/Add.12/Rev.6/Amend.4E/ECE/324E/ECE/TRANS/505Regulation No 13page 2Add new paragraphs 2.35. and 2.36., to read:"2.35. "Subject trailer" is a trailer representative of the trailer type for which type approval is sought.2.36. The "brake factor (B F)" is the input to output amplification ratio of the brake."Add a new paragraph 12.1.8., to read:"12.1.8. As from the official date of entry into force of Supplement 2 to the 11 series of amendments to this Regulation, no Contracting Party applying this Regulation shallrefuse to grant approval under this Regulation as amended by Supplement 2 tothe 11 series of amendments."Add a new paragraph 12.2.7., to read:"12.2.7. As from 48 months after the date of entry into force of Supplement 2 to the 11 series of amendments to this Regulation, Contracting Parties applying this Regulation shallgrant approvals only if the vehicle type to be approved meets the requirements of thisRegulation as amended by Supplement 2 to the 11 series of amendments."Add a new paragraph 12.3.2., to read:"12.3.2. Starting 84 months after the entry into force of Supplement 2 to the 11 series of amendments to this Regulation, Contracting Parties applying this Regulation mayrefuse first national registration (first entry into service) of a vehicle which does notmeet the requirements of Supplement 2 to the 11 series of amendments to thisRegulation."Annex 11,Paragraph 2., amend to read:"2. The term "identical", as used in paragraphs 1.1., 1.2. and 1.3. above, means identical as regards the geometric and mechanical characteristics and the materials used forthe components of the vehicle referred to in those paragraphs.In the case of trailers, these requirements are deemed to be fulfilled, with respect toparagraphs 1.1. and 1.2. above, if the identifiers referred to in Appendix 2,paragraph 3.7. of this Annex for the axle / brake of the subject trailer are contained ina report for a reference axle / brake.A "reference axle / brake" is an axle / brake for which a test report mentioned inAppendix 2, paragraph 3.9. of this annex exists."E/ECE/324E/ECE/TRANS/505}Rev.1/Add.12/Rev.6/Amend.4Regulation No 13page 3Annex 11 - Appendix 1,Table I, amend to read (including footnote 1/):"Axles of the vehicle Reference axlesStatic mass (P) 1/Brakingforce neededat wheelsSpeed Test mass(P e) 1/Brakingforcedeveloped atwheelsSpeedkg N km/h kg N km/h Axle 1Axle 2Axle 3Axle 41/ See paragraph 2.1. of Appendix 2 to this annex"Table III, third row, amend to read (including the deletion of footnote 2/):"REFERENCE AXLE .......………….REPORT NO. ......…… Date .........……..(copy attached)Type-I Type-III Braking force per axle (N)(see paragraph 4.2.1., Appendix 2)Axle 1 Axle 2 Axle 3 T1= ....... % F eT2= ....... % F eT3= ....... % F eT1= ...... % F eT2= ...... % F eT3= ...... % F e… … …" Annex 11 – Appendix 2,Insert a new paragraph 1.2.2., to read:"1.2.2. Tests carried out in accordance with this appendix prior to Supplement 2 to the 11 series of amendments to this Regulation which, together with any supportingdata from the vehicle/axle/brake manufacturer, provide sufficient information tomeet the requirements of Supplement 2 to the 11 series of amendments can be usedfor a new report or the extension of an existing test report without the need to carry-out actual tests."}Rev.1/Add.12/Rev.6/Amend.4E/ECE/324E/ECE/TRANS/505Regulation No 13page 4Paragraph 1.4.1., amend to read:"1.4.1. In the case of air ... shall be adjusted to:s0 > 1.1 · s re-adjust (the upper limit … by the manufacturer),"Paragraph 2., amend to read:"2. SYMBOLS AND DEFINITIONS2.1. SymbolsP = part of the vehicle mass borne by the axle under static conditionsF = normal reaction of road surface on the axle under static conditions = P·gF R= total normal static reaction of road surface on all wheels of trailerF e= test axle loadP e= F e / gg = acceleration due to gravity: g = 9.81 m/s2C = brake input torqueC0= brake input threshold torque, definition see paragraph 2.2.2.C0,dec = declared brake input threshold torqueC max= declared maximum brake input torqueR = tyre rolling radius (dynamic)T = brake force at tyre/road interfaceT R= total brake force at tyre/road interface of the trailerM = brake torque = T·Rz = braking rate = T/F or M/(R·F)s = actuator stroke (working stroke plus free stroke)s p= see Annex 19, Appendix 7Th A= see Annex 19, Appendix 7l = lever lengthr = internal radius of brake drums or effective radius of brake discsp = brake actuation pressureNote: Symbols with the suffix "e" relate to the parameters associated with the reference brake test and may be added to other symbols as appropriate.2.2. Definitions2.2.1. Mass of a disc or drum2.2.1.1. The "declared mass" is the mass declared by the manufacturer which is arepresentative mass for the brake identifier (see paragraph 3.7.2.2. of this appendix).2.2.1.2. The "nominal test mass" is the mass which the manufacturer specifies for the disc ordrum with which the relevant test is carried out by the Technical Service.}Rev.1/Add.12/Rev.6/Amend.4E/ECE/324E/ECE/TRANS/505Regulation No 13page 52.2.1.3. The "actual test mass" is the mass measured by the Technical Service prior to thetest.2.2.2. "Brake input threshold torque":2.2.2.1. The brake input threshold torque "C0" is the input torque necessary to produce ameasurable brake torque. This torque may be determined by extrapolation ofmeasurements within a range not exceeding 15 percent braking rate or otherequivalent methods (e.g. Annex 10, paragraph 1.3.1.1.).2.2.2.2. The brake input threshold torque "C0,dec" is the brake input threshold torque declaredby the manufacturer which is a representative brake input threshold torque for thebrake (see paragraph 3.7.2.2.1. of this appendix) and is needed to produce diagram 2of Annex 19.2.2.2.3. The brake input threshold torque "C0,e" is determined by the procedure as defined inparagraph 2.2.2.1. above, measured by the Technical Service at the end of the test. 2.2.3. "External diameter of a disc":2.2.3.1. The "declared external diameter" is the external diameter of a disc declared by themanufacturer which is a representative external diameter for the disc (seeparagraph 3.7.2.2.1. of this appendix).2.2.3.2. The "nominal external diameter" is the external diameter which the manufacturerspecifies for the disc on which the relevant test is carried out by the TechnicalService.2.2.3.3. The "actual external diameter" is the external diameter measured by the TechnicalService prior to the test.2.2.4. The "effective length of the cam shaft" is the distance from the centre line of theS-cam to the centre line of the operating lever."Paragraph 3.4., amend to read:"3.4. Test conditions (general)"Paragraphs 3.7. to 3.7.3., should be deleted.Insert new paragraphs 3.7. to 3.9.4., to read:"3.7. Identification}Rev.1/Add.12/Rev.6/Amend.4E/ECE/324E/ECE/TRANS/505Regulation No 13page 63.7.1. The axle shall carry in a visible position at least the following identificationinformation grouped together, in any order, in a legible and indelible manner:(a) Axle manufacturer and/or make;(b) Axle identifier (see paragraph 3.7.2.1. of this appendix);(c) Brake identifier (see paragraph 3.7.2.2. of this appendix);(d) F e identifier (see paragraph 3.7.2.3. of this appendix);(e) Base part of test report number (see paragraph 3.9. of this appendix).An example is given below:Axle Manufacturer and/or make ABCID1-XXXXXXID2-YYYYYYID3-11200ID4-ZZZZZZZ3.7.1.1. A non-integrated automatic brake adjustment device shall carry in a visible positionat least the following identification information grouped together, in a legible andindelible manner:(a) Manufacturer and/or make;(b) Type;(c) Version.3.7.1.2. The make and type of each brake lining shall be visible when the lining/pad ismounted on the brake shoe / back plate in a legible and indelible manner.3.7.2. Identifiers3.7.2.1. Axle identifierThe axle identifier categorizes an axle in terms of its braking force/torque capabilityas stated by the axle manufacturer.The axle identifier shall be an alphanumeric number consisting of the four characters"ID1-" followed by a maximum of 20 characters.3.7.2.2. Brake identifierThe brake identifier shall be an alphanumeric number consisting of the fourcharacters "ID2-" followed by a maximum of 20 characters.A brake with the same identifier is a brake which does not differ with regard to thefollowing criteria:}Rev.1/Add.12/Rev.6/Amend.4E/ECE/324E/ECE/TRANS/505Regulation No 13page 7(a) Type of brake (e.g. drum (S-cam, wedge, etc.) or disc brake (fixed, floating,single or twin disc, etc.));(b) Base material (e. g. ferrous or non ferrous) with respect to calliper housing,brake carrier, brake disc and brake drum;(c) Dimensions with the suffix "e" according to figures 2A and 2B of Appendix 5of this annex;(d) The basic method used within the brake to generate the braking force;(e) In the case of disc brakes, the friction ring mounting method: fixed or floating;(f) Brake factor B F;(g) Different brake characteristics with respect to the requirements of Annex 11which are not covered by subparagraph 3.7.2.2.1.3.7.2.2.1. Differences allowed within the same brake identifierThe same brake identifier may include different brake characteristics with regard tothe following criteria:(a) Increase in maximum declared brake input torque C max;(b) Deviation of declared brake disc and brake drum mass m dec: ± 20 per cent;(c) Method of attachment of the lining / pad on the brake shoe / back plate;(d) In the case of disc brakes, increase of maximum stroke capability of the brake;(e) Effective length of the cam shaft;(f) Declared threshold torque C0,dec;(g) ± 5 mm from the declared external diameter of the disc;(h) Type of cooling of the disc (ventilated/non-ventilated);(i) Hub (with or without integrated hub);(j) Disc with integrated drum – with or without parking brake function;(k) Geometric relationship between disc friction surfaces and disc mounting;(l) Brake lining type;(m) Material variations (excluding changes in base material, see paragraph 3.7.2.2.) for which the manufacturer confirms that such a material variation does notchange the performance with respect to the required tests;(n) Back plate and shoes.3.7.2.3. F e identifierThe F e identifier indicates the test axle load. It shall be an alphanumeric numberconsisting of the four characters "ID3-" followed by the F e value in daN, without the"daN" unit identifier.E/ECE/324E/ECE/TRANS/505}Rev.1/Add.12/Rev.6/Amend.4Regulation No 13page 83.7.2.4. Test report identifierThe test report identifier shall be an alphanumeric number consisting of the fourcharacters "ID4-" followed by the base part of the test report number.3.7.3. Automatic brake adjustment device (integrated and non-integrated)3.7.3.1. Types of automatic brake adjustment deviceThe same type of automatic brake adjustment device does not differ with regard tothe following criteria:(a) Body: base material (e. g. ferrous or non ferrous, cast iron or forged steel);(b) Maximal permitted brake shaft moment;(c) Adjustment operating principle, e.g. stroke (travel) dependent, force dependentor electronic/mechanical.3.7.3.2. Versions of automatic brake adjustment device, with respect to the adjustmentbehaviourAutomatic brake adjustment devices within a type that have an impact on the runningclearance of the brake are considered to be different versions.3.8. Test criteriaThe testing shall demonstrate compliance with all the requirements laid down inAppendix 2 of this annex.In the case that a new test report, or a test report extension, is required for a modifiedaxle/brake within the limits specified in paragraph 3.7.2.2.1. the following criteriaare used to determine the necessity for further testing taking into account worst caseconfigurations agreed with the Technical Service.Abbreviations shown below are used in the subsequent table:CT (complete test) Test according to Annex 11, Appendix 2:3.5.1.: Supplementary cold performance test3.5.2.: Fade test (Type-I test) */3.5.3.: Fade test (Type-III test) */Test according to Annex 19:4.: Cold performance characteristics for trailer brakes*/FT (fade test) Test according to Annex 11, Appendix 2:3.5.1.: Supplementary cold performance test3.5.2.: Fade test (Type-I test) */3.5.3.: Fade test (Type-III test) */*/ If applicableE/ECE/324E/ECE/TRANS/505}Rev.1/Add.12/Rev.6/Amend.4Regulation No 13page 9Differences according toparagraph 3.7.2.2.1. aboveTest criteria(a) Increase in maximum declared brakeinput torque C maxChange allowed without additional testing(b) Deviation of declared brake disc andbrake drum mass m dec: ± 20 per cent CT: The lightest variant shall be tested if the nominal test mass for a new variant deviates less than 5 per cent from a previously tested variant with a higher nominal value then the test of the lighter version may be dispensed with.The actual test mass of the test specimen may vary ± 5 per cent from the nominal test mass.(c) Method of attachment of the lining /pad on the brake shoe / back plate The worst case specified by the manufacturer and agreed by the Technical Services conducting the test(d) In the case of disc brakes, increase ofmaximum stroke capability of thebrakeChange allowed without additional testing(e) Effective length of the cam shaft The worst case is considered to be the lowest cam shaft torsional stiffness and shall be verified by either:(i) FT or(ii) Change allowed without additional testing if by calculation the influence with respect to stroke and braking force can be shown. In this case the test report shall indicate the following extrapolated values: s e, C e, T e, T e/F e,(f) Declared threshold torque C0,dec It shall be checked that the brake performance remains within the corridors of Diagram 2 of Annex 19.(g) ± 5 mm from the declared externaldiameter of the disc The worst case test is considered the smallest diameterThe actual external diameter of the test specimen may vary ± 1 mm from the nominal external diameter specified by the axle manufacturer.(h) Type of cooling of the disc(ventilated/non-ventilated)Each type shall be tested(i) Hub (with or without integrated hub) Each type shall be tested(j) Disc with integrated drum – with orwithout parking brake functionTesting is not required for this feature (k) Geometric relationship between discfriction surfaces and disc mountingTesting is not required for this feature (l) Brake lining type Each type of brake liningE/ECE/324E/ECE/TRANS/505}Rev.1/Add.12/Rev.6/Amend.4Regulation No 13page 10Differences according toparagraph 3.7.2.2.1. aboveTest criteria (m) Material variations (excludingchanges in base material, seeparagraph 3.7.2.2.) for which themanufacturer confirms that such amaterial variation does not changethe performance with respect to therequired testsTest not required for this condition(n) Back plate and shoes Worst case test conditions */:Back plate: minimum thickness Shoe: lightest brake shoe*/ No test is required if the manufacturer can demonstrate that a change does not effect the stiffness3.8.1. If an automatic brake adjustment device deviates from a tested one according toparagraphs 3.7.3.1. and 3.7.3.2. an additional test according to paragraph 3.6.2. ofthis appendix is necessary.3.9. Test report3.9.1. Test report numberThe test report number consists of two parts: a base part and a suffix which identifiesthe issue level of the test report.The base part, consisting of a maximum of 20 characters, and suffix shall be clearlyseparated from each other using e.g. a dot or slash.The base part of the test report number shall only cover brakes with the same brakeidentifier and the same brake factor (according to paragraph 4. of Annex 19 to thisRegulation).3.9.2. Test codeIn addition to the test report number a "test code" consisting of up to eight characters(e.g. ABC123) shall indicate the test results applicable to the identifiers and the testspecimen, which is described by the details given in paragraph 3.7. above.3.9.3. Test results3.9.3.1. The result of tests carried out in accordance with paragraphs 3.5. and 3.6.1. of thisappendix shall be reported on a form, a model of which is shown in Appendix 3 tothis annex.3.9.3.2.In the case of a brake installed with an alternative brake adjustment device the results of tests carried out in accordance with paragraph 3.6.2. of this appendix shall be reported on a form, a model of which is shown in Appendix 4 to this annex. 3.9.4. Information documentAn information document, provided by the axle or vehicle manufacturer, containing at least the information defined in Appendix 5 to this annex shall be part of the Test Report.The information document shall identify, if applicable, the various variants of the brake/axle equipment with respect to the essential criteria listed in paragraph 3.7.2.2.1. above."Paragraph 4.1., amend to read: "4.1. Verification of componentsThe brake specification of the vehicle to be type approved shall comply with the requirements laid down in paragraphs 3.7. and 3.8. above"Paragraphs 4.1.1. to 4.1.7., should be deleted. Paragraph 4.3.1.4., the formula, amend to read:()F 0.01RR C C C C F 0.01T T eoe e o e e ⋅+⋅−−⋅−=Paragraph 4.3.2., the formula, amend to read:F T = F T RRΣΣpage 12Annex 11 – Appendix 3, amend to read (including the deletion of figures 1A, 1B, 2A and 2B):"Annex 11 – Appendix 3MODEL TEST REPORT FORM AS PRESCRIBED IN PARAGRAPH 3.9.OF APPENDIX 2 TO THIS ANNEXTEST REPORT No. ………Base part: ID4- ………Suffix: ……………1. General1.1. Axle manufacturer (name and address): ..........................................................................1.1.1. Make of axle manufacturer:..............................................................................................1.2. Brake manufacturer (name and address): .........................................................................1.2.1. Brake identifier ID2-:........................................................................................................1.2.2. Automatic brake adjustment device: integrated/non-integrated 1/1.3. Manufacturer's Information Document: ...........................................................................2. Test RecordThe following data has to be recorded for each test:2.1. Test code (see paragraph3.9.2. of Appendix 2 of this annex): ........................................2.2. Test specimen: (precise identification of the variant tested related to theManufacturer's Information Document. See also paragraph 3.9.2. of Appendix 2 of thisannex)2.2.1. Axle2.2.1.1. Axle identifier: ID1-..........................................................................................................2.2.1.2. Identification of tested axle: .............................................................................................2.2.1.3. Test axle load (Fe identifier): ID3-............................................................................daN 2.2.2. Brake2.2.2.1. Brake identifier: ID2-........................................................................................................2.2.2.2. Identification of tested brake: ...........................................................................................2.2.2.3. Maximum stroke capability of the brake 2/:.....................................................................2.2.2.4. Effective length of the cam shaft 3/:.................................................................................2.2.2.5. Material variation as per paragraph3.8 (m) of Appendix 2 of this annex: ......................2.2.2.6. Brake drum / disc 1/2.2.2.6.1. Actual test mass of disc / drum 1/: ...................................................................................2.2.2.6.2. Nominal external diameter of disc 2/: ..............................................................................2.2.2.6.3. Type of cooling of the disc ventilated/non-ventilated 1/2.2.2.6.4. With or without integrated hub 1/2.2.2.6.5. Disc with integrated drum – with or without parking brake function 1/ 2/2.2.2.6.6. Geometric relationship between disc friction surfaces and disc mounting:......................2.2.2.6.7. Base material:....................................................................................................................2.2.2.7. Brake lining or pad 1/2.2.2.7.1. Manufacturer:....................................................................................................................2.2.2.7.2. Make:................................................................................................................................2.2.2.7.3. Type:.................................................................................................................................2.2.2.7.4. Method of attachment of the lining / pad on the brake shoe / back plate 1/: ...................2.2.2.7.5. Thickness of back plate, weight of shoes or other describing information(Manufacturer's Information Document) 1/:.....................................................................2.2.2.7.6. Base material of brake shoe / back plate 1/:......................................................................2.2.3. Automatic brake adjustment device (not applicable in the case of integrated automaticbrake adjustment device) 1/2.2.3.1. Manufacturer (name and address): ...................................................................................2.2.3.2. Make:................................................................................................................................2.2.3.3. Type:.................................................................................................................................2.2.3.4. Version:.............................................................................................................................2.2.4. Wheel(s) (dimensions see Figures 1A and 1B in Appendix 5 of this annex)2.2.4.1. Reference tyre rolling radius (R e) at test axle load (F e): ..................................................2.2.4.2. Data of the fitted wheel during testing:Tyre size Rim size X e (mm) D e (mm) E e (mm) G e (mm) 2.2.5. Lever length le: ................................................................................................................2.2.6. Brake actuator2.2.6.1. Manufacturer: ...................................................................................................................2.2.6.2. Make: ...............................................................................................................................2.2.6.3. Type: ................................................................................................................................2.2.6.4. (Test) Identification number: ...........................................................................................2.3. Test results (corrected to take account of rolling resistance of 0.01·F e)2.3.1. In the case of vehicles of categories O2 and O3Test type: 0 IAnnex 11, Appendix 2, paragraph: 3.5.1.2. 3.5.2.2./3. 3.5.2.4.Test speed km/h 40 40 40Brake actuator pressure p e kPa -Braking time min - 2.55 -Brake force developed T e daNBrake efficiency T e/F e-Actuator stroke s e mm -Brake input torque C e Nm -Brake input threshold torque C0,e Nm -page 142.3.2. In the case of vehicles of category O4Test type: 0 III Annex 11, Appendix 2, paragraph: 3.5.1.2. 3.5.3.1. 3.5.3.2.Test speed initial km/h 60 60Test speed final km/hBrake actuator pressure p e kPa -Number of brake applications - - 20 -Duration of braking cycle s - 60 -Brake force developed T e daNBrake efficiency T e/F e-Actuator stroke s e mm -Brake input torque C e Nm -Brake input threshold torque C0,e Nm -2.3.3. This item is to be completed only when the brake has been subject to the testprocedure defined in paragraph 4. of Annex 19 to this Regulation to verify the coldperformance characteristics of the brake by means of the brake factor (B F).2.3.3.1. Brake factor B F:2.3.3.2. Declared threshold torque C0,dec Nm2.3.4. Performance of the automatic brake adjustment device (if applicable)2.3.4.1. Free running according to para. 3.6.3. of Annex 11, Appendix 2: yes / no 1/3. Application rangeThe application range specifies the axle/brake variants that are covered in this testreport, by showing which variables are covered by the individual test codes.4. This test has been carried out and the results reported in accordance with Appendix 2to Annex 11 and where appropriate paragraph 4. of Annex 19 to Regulation No. 13 aslast amended by the ... series of amendments.At the end of the test defined in paragraph 3.6. of Annex 11, Appendix 2, 4/ therequirements of paragraph 5.2.2.8.1. of Regulation No. 13 were deemed to be fulfilled/ not fulfilled. 1/Technical Service 5/ carrying out the testSigned: ....................................... Date: ........................................5. Approval Authority 5/Signed: ....................................... Date: ........................................。
DFMEA样稿 20131015

3
汽车电池
汽车电池消耗快
产品安装上汽车后,用户发现停放车辆时电池 出现消耗快问题
7
10
在产品设计时,使用合适电路确保整机待机电流达到 PHILIPS标准≤3mA.
1
70
4
USB电路
USB ESD
产品在安装和使用过程出现功能错乱,死机现 象
4
产品安装使用过程,被 静电打坏元器件
4
1.产品设计时要在关键电路上加入ESD管和ESD保 护电路,防止静电打坏元器件. 2.产品在设计过程应能通过PHILIPS ESD标准的测 试.
其它按钮手感已经ok顶面增加触点的按钮第二次试模样还未回来待验证9结构panel安装panel安装时硬压担心把扣位压断5安装没有按正常方法5把相关扣位加些骨位来增强安全性375把相关扣位加些骨位来增强安全性邓声亮开模后可看到改善结果验证ok10结构panel安装panel装上后担心有上下偏位4安装没有按正常方法4把原来的方形管位改成圆形管位232把原来的方形管位改成圆形管位邓声亮开模后可看到改善结果验证okxxxxxxxxapqp小组成员
4
64
选择衰减弱的高品质天 何有飞 wk 线 1017
更改验证OK
10
天线安装方式
天线安装方式不良
影响DAB接收灵敏度
4
5
天线要尽量要良好接地
5
100
更改验证OK
11
DAB模式
DAB不支持自动连接
用户需要自动转回收音模式
4
5
Need Frontier and KRS talking about how to fix this feature ; max~3 seconds need can auto received DAB
GBT11345-2013 新老标准对照

GB/T11345-2013标准新标准与老标准的主要变化情况一、修改了范围(第一章)厚度不变(8mm)新增温度(0~60C°)检测材料声速(纵波5920±50、横波3255±30)m/s新标准中将检测等级分为ABCD四个等级,D为特殊等级(老标准A、B、C三个等级)检测结果的评定或验收基于两个因素:(1)、基于显示长度和回波幅度;(2)基于显示特性和显示尺寸(探头移动技术二、修改了规范性引用文件由于年份的迁移,很多标准都进行了更改,另外中国加入WTO后很多标准要求尽量与ISO标准接轨。
三、修改了术语定义与符号这些内容全部列在表1中,确实这些术语与定义与老标准完全不同。
四、增加了总则(第4章)运用本标准时涉及的两个标准(GB/T29711和GB/T29712基于验收要求)五、增加了合同协议项目内容(这是国际惯例)、检测前所必要的信息和书面检测工艺规程等信息。
六、修改了人员和设备要求(第6章)在这一章节中,对仪器、试块、探头要求比老标准更严格:(一)、仪器1、采购和维修的规范化2、性能指标要求:(1)、温度稳定性(环境温度变化5C°,信号幅度不大于±2%,位置变化不大于全屏宽度的±1%)(2)、显示稳定性(频率增加1Hz,信号幅度不大于±2%、信号位置变化不大于全屏宽度的±1%)(3)、水平线性偏差不大于全屏宽度的±2%(老标准±1%)(4)、垂直线性的测试值与理论值偏差不大于±3%(老标准±5%)除此之外,要求仪器到有资质的检测机构进行性能测试,周期为一年一次(12个月)3、系统性能测试主要是指仪器和探头连接后测试,与老标准基本一致:(1)、入射点偏差±1mm(2)、折射角偏差±2°(3)、灵敏度雨量、分辨力和盲区视实际要求而定(主要是根据检测对象)(二)、探头参数1、检测频率2~5MHz(可高可低)最低可到1MHz2、折射角(35~70度之间)多探头使用时,探头间的角度差不小于10度3、晶片尺寸:从频率和声程考虑(6~12mm的用于短声程检测,直探头声程大于100mm或斜探头声程大于200mm的,选直径12mm~24mm或等效面积的矩形晶片)4、曲面检测时探头与工件底面间隙不大于0.5mm。
ASS-2013-1

Applied Surface Science 264 (2013) 633–635Contents lists available at SciVerse ScienceDirectApplied SurfaceSciencej o u r n a l h o m e p a g e :w w w.e l s e v i e r.c o m /l o c a t e /a p s u scInfluence of pulsed electron beam treatment on microstructure and properties of TA15titanium alloyYu-kui Gao ∗College of Aerospace Engineering and Applied Mechanics,Tongji University,No.100of Zhangwu Road,Shanghai 200092,Chinaa r t i c l ei n f oArticle history:Received 8June 2012Received in revised form 16July 2012Accepted 15October 2012Available online 23 October 2012Keywords:Pulsed electron beam treatment Grade characteristics Nanoindenta b s t r a c tThe surface of TA15titanium alloy was modified by pulsed electron beam and the hardness distribution along the treated surface layer was investigated by nanoindent technology.The grade characteristics were therefore analyzed by studying the distribution of hardness along surface layer of specimens.Moreover,the microstructure was investigated by OM,XRD and TEM techniques.Furthermore,the correlation of hardness to microstructure was analyzed.The results show that the grade fine grain microstructure is formed in the upper surface layer and the temperature grade or heat effect caused by pulsed electron beam treatment is the main reason to form grade fine grain microstructure in the surface layer.© 2012 Elsevier B.V. All rights reserved.1.IntroductionTitanium alloys are employed in aerospace industry because of their remarkable characteristics:the high ratio of strength to weight,excellent corrosion resistance and good fatigue perfor-mance.TA15titanium alloy is widely used in Chinese aircraft to make parts,which have lighter weight,longer life and good corro-sion properties [1].Surface determines performance and many components’prop-erties are affected by the surface.Wear,fatigue,and corrosion are the main properties of many metallic materials.The effect of sur-face integrity on fatigue was investigated by many researchers.Surface integrity is a comprehensive concept which includes the change of chemical and mechanical properties of materials at the surface layer.It has four main categories and microstructure is the critical one [2].The wear of TA15titanium alloy is bad due to its lower hardness and worse surface resistance to fretting.How to improve the wear property of TA15titanium alloy by increasing surface hardness is an important problem in its applications.Pulsed electron beam treatment is a new surface modifica-tion process and can be applied in many fields [3–7].There are many investigations on the effects of pulsed electron beam for measurements of properties and microstructures of the titanium alloys [8–12].Therefore,the wear property may be improved with increasing hardness in surface layer by finer grain modified by pulsed electron beam.The hardness is greater when the grain is∗Corresponding author.Tel.:+862165981290;fax:+862165983267.E-mail address:yukuigao@finer,therefore the wear property could be modified with the hard-ness increase of surface layer.However,the effect of surface fine grain microstructure by electron beam treatment on hardness has been less investigated and therefore it is interesting and impor-tant to study the change of hardness along surface layer by electron beam treatment and to obtain the characteristics of grade fine grain microstructure in surface layer with the nanoindent technology.2.Experimental material and methods2.1.Experimental materialTA15titanium alloy was employed in this investigation.Its chemical composition is listed in Table 1.The metal was annealed at 800◦C for 1h then had an air cooling.Its microstructure is mainly ␣phase and a little phase.The tensile property of TA15titanium alloy is listed in Table 2.2.2.Experimental methodsThe surfaces of specimens were pulsed electron beam treated by the Solo type pulsed electron beam machine.The parameters of pulsed electron beam treatment are the pulsed duration time,t =15s,pulsed times,N =3pulses,kinetic energy,E =10–40keV,and pulsed energy density,E S =15J/cm 2.The microstructure of pulsed electron beam treated specimens was analyzed by OM.The phases and their contents were deter-mined by the D/max-2500/PCX type XRD tester.Moreover,the fine grain characteristics were also analyzed by TEM method.0169-4332/$–see front matter © 2012 Elsevier B.V. All rights reserved./10.1016/j.apsusc.2012.10.083634Y.-k.Gao /Applied Surface Science 264 (2013) 633–635Table 1Chemical composition of TA15titanium alloy (wt.%).AlZrMoVFeSiONCTi5.9 2.1 1.71.90.210.110.080.020.09BalTable 2Tensile property of TA15titanium alloy.Tensile strengthYield strengthElongation 985MPa881MPa14%The hardness distribution along surface layer was determined by the Tribolndente nanoindent tester.The maximum applied load is 1N,and the grade characteristics were analyzed based on the hardness distribution along surface layer.3.Results and discussion3.1.Microstructures and phases of TA15titanium alloyThe microstructure of pulsed electron beam treated specimens is shown in Fig.1and there are three zones in Fig.1.The three zones are melted layer,heat affected layer and substrate [3]from the upper or top surface layer to matrix illustrated in Fig.1.Fig.1also shows two special zones,the melt layer and the affected layer along the cross section surface of pulse electron beam treated spec-imens.In the melt layer,fine grain microstructure can be found and the phase cannot be clearly seen because of great resistance of sin-gle ␣phase corrosion in fine grain microstructure layer,as shown in Fig.1.The fine grain microstructure is determined by XRD peak width illustrated in Fig.2and the size of the diffraction grain is about 168nm for the pulsed electron beam treated specimens.The size of the diffraction grain for the unmodified specimens is also deter-mined by XRD peak width as shown in Fig.3.The size of the diffraction grain is about 310nm for the unmodified annealed spec-imens.The finer grains or diffraction domains can increase the hardness and make surface have a good wear property.3.2.Nanoindent hardness and grade characteristicsTo determine the grade characteristics of fine grain microstruc-ture in surface layer and the effect of fine grain microstructure on hardness in surface layer of the pulsed electron beam treated specimens,the distribution of hardness along surface layer was determined by the nanoindent hardnessmeasurement.Fig.1.Microstructure of TA15titanium alloy treated by pulsed electronbeam.Fig.2.XRD of pulsed electron beam treated specimens.The hardness along the cross section surface of the pulsed elec-tron beam specimens is illustrated in Fig.4.The matrix hardness is about 4.62GPa and the surface hardness of pulsed electron beam specimens is about 7.11GPa,the increment of hardness is about 2.49GPa and the increase percentage is 53%.The grade characteristics of fine grain microstructure in the sur-face layer and the effect of fine grain microstructure on hardness in surface layer can be determined by nanoindentmeasurementFig.3.XRD of referenced annealedspecimens.Fig.4.Hardness along cross section surface of pulsed electron beam specimens.Y.-k.Gao/Applied Surface Science264 (2013) 633–635635Fig.5.TEM images of pulsed electron treated specimens.(a)BF image(b)SAED pattern(c)indexed diffraction pattern.technology.It can be seen that the gradient of hardness in surface layer about25m as shown in Fig.4is greater and this depth is equal to the depth of the melt layer,which is illustrated in Fig.1. The gradient of hardness beneath the melt layer between25m and50m is smaller and the gradient of hardness for the distance of50m from the surface to the distance of80m is about zero.The great increase in hardness of the surface melt layer should be related to the formation offine grain microstructure during pulsed electron beam treatment.The grain or domain size is gettingfiner induced by pulsed electron beam treatment;the hardness will be higher because of the higher yield strength.The smaller width of martensite lentil microstructure can be found in the melt layer,as shown in Fig.5.The width of some martensite lathes is about90nm and the SAED pattern in Fig.5shows the lattice distort and the finer grain which make the diffraction dots become the extended diffraction dots or even some short diffraction continue lines.The hardness is affected mainly by the factors offine grain microstructure and the heat effect during pulsed electron beam treating process.Thefine grain or small domain size can improve the hardness,and at the same time the surface melted layer has the less effect of heat after pulsed electron beam treatment due to short time,therefore,the gradient of hardness from surface to50m is great and mainly determined by thefine grain effect,althoughfine grains are formed through being re-melted with a high temperature induced by pulsed electron beam treatment.The gradient of hardness beneath the melt layer where from the surface between50m and80m is smaller and near to zero just because of a balance of thefine grain size effect and the heat effect induce by pulsed electron beam treatment.Thefine grain effect makes an increase in hardness,but the heat effect decreases hardness.The increase in hardness may also be related to the phase trans-formation,but the quantitative analysis of phases content by XRD illustrates that no any new phase occurs in the pulsed electron beam treated specimens and the change of phase content of both␣andis less than5%,therefore,the increase of hardness by pulsed electron modification should be mainly due to thefine grain size effect.4.Conclusions(1)Thefine grain microstructure can be formed in melt layerinduced by pulsed electron beam treatment.(2)The grade characteristics offine grain microstructure in surfacelayer and the effect offine grain microstructure on hardness can be determined by nanoindent technology.(3)The great increment of hardness in the surface melt layer shouldbe related to the formation offine grain microstructure during pulsed electron beam treatment.(4)The gradient of hardness beneath the melt layer is greater dueto thefine grain size effect.AcknowledgementThe author is grateful for the foundation support from Pro-gram of Ministry of Science and Technology of China(contract nos. 200473-3641and08-039577).References[1]J.Y.Wang,Z.M.Ge,B.Y.Zhou,Titanium Alloys in Aeronautical Application,Shanghai Science Press,Shanghai,1985,p.68.[2]Y.K.Gao,X.B.Li,Q.X.Yang,M.Yao,Influence of surface integrity on fatiguestrength of42CrNi2Si2MoVA steel,Mater.Lett.61(2007)466–469.[3]A.D.Pogrebnyak, D.I.Proskurovskii,Modification of metal surface layerproperties using pulsed electron beams,Phys.Status Solidi A145(1994) 9–49.[4]D.I.Proskurovsky,V.P.Rotshtein,G.E.Ozur,A.B.Markov,D.S.Nazarov,Pulsedelectron-beam technology for surface modification of metallic materials,J.Vac.Sci.Technol.A16(1998)2480–2488.[5]A.D.Pogrebnjak,Metastable states and structural phase change in metals andalloys exposed to high power pulsed ion beams,Phys.Stat.Sol.117A(1990) 17–35.[6]V.P.Rotshtein,D.I.Proskurovsky,G.E.Ozur,Yu.F.Ivanov,A.B.Markov,Surfacemodification and alloying of metallic materials with low-energy high-current electron beams,Surf.Coat.Technol.180–181(2004)377–381.[7]Y.K.Gao,Surface modification of TA2pure titanium by low energy highcurrent pulsed electron beam treatments,Appl.Surf.Sci.257(2011) 7455–7460.[8]A.D.Pogrebnjak,A.P.Kobzev,B.P.Gritsenko,Effect of Fe and Zr ion implantationand high-current electron irradiation treatment on chemical and mechanical properties of Ti–V–Al Alloy,J.Appl.Phys.87(2000)2142–2148.[9]A.D.Pogrebnjak,E.A.Bazyl,Modification of wear and fatigue characteristics ofTi–V–Al alloy by Cu and Ni ion implantation and high-current electron beam treatment,Vacuum64(2002)1–7.[10]A.D.Pogrebnjak,S.Bratushka,V.I.Boyko,et al.,A review of mixing processes inTa/Fe and Mo/Fe systems treated by high current electron beams,Nucl.Instrum.Meth.B B145(1998)373–390.[11]T.Grosdidier,J.X.Zou,B.Bolle,S.Z.Hao,C.Dong,Grain refinement,hardeningand metastable phase formation by high current pulsed electron beam(HCPEB) treatment under heating and melting modes,J.Alloys Compd.504S(2010) S508–S511.[12]X.D.Zhang,S.Z.Hao,X.N.Li,C.Dong,T.Grosdidier,Surface modification of puretitanium by pulsed electron beam,Appl.Surf.Sci.257(2011)5899–5902.。