车刀各部位名称及功能)
车 刀
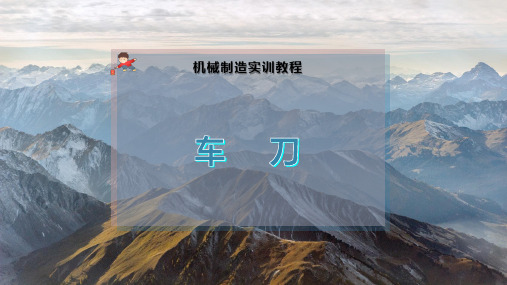
车刀
1.车刀的种类和用途:
按途分为:外圆车刀、端面车刀、切断或切槽刀、螺纹 车刀、 成形车刀等
按形状分为:直头或弯头车刀、尖刀或圆弧车刀、左 或右偏刀等 按材料分为:高速钢或硬质合金等车刀 按被加工表面精度的高低分:粗车刀和精车刀 按车刀的结构分:焊接式和机械夹固式 机械夹固式车刀按其能否刃磨又分为重磨式和不重磨 式(转位式)车刀
副偏角K’r : 它是进绐反方向与副切削刃在基面上投影之 间的夹角。 其作用是减少副切削刃同己加工表面间的摩 擦,以提高工件表面质量。一般选取 K’r=5°~15°。
4.车刀的材料:
对刀具材料的基本要求:硬度高、红硬性好、具有足 够的强度和韧性。
硬度高:刀具切削部分的材料应具有较高的硬度,最 低硬度要高于工件的硬度,一般在HRC62以上。硬 度越高,耐磨性越好。
一般选取γ0=-5°~20° 。其大小决定于工 件材料、刀具材料及粗、精加工等情况。 工件材料和刀具材料越硬, γ0取小值;精 加工时, γ0取大值。
主后角a0 : 在主剖面内切削平面与主后刀面之间的夹角。 其作用是减小车削时主后刀面与工件间的摩擦, 降低切削时的震动,提高工件表面上的加工质 量。
(1)磨主后刀面:按主偏角大小把刀杆向左偏斜,再将刀 头向上翘,使主刀面自下而上慢慢接触砂轮。
(2)磨副后刀面:按副偏角大小把刀杆向左偏斜,再将刀 头向上翘,使副刀面自下而上慢慢接触砂轮。
(3)磨前刀面:先把刀杆尾部下倾,再按前角大 小倾斜前刀面,使主切削刃于刀杆底面平行或倾斜 一定角度,再使前刀面自下而上慢慢接触砂轮。
2.车刀的组成:
车刀是由刀头和刀杆两部分组成 刀头是车刀的切削部分;刀杆时车刀的夹持部分。车刀的切 削部分由一尖、两刃、三面组成。
常用车刀简介.
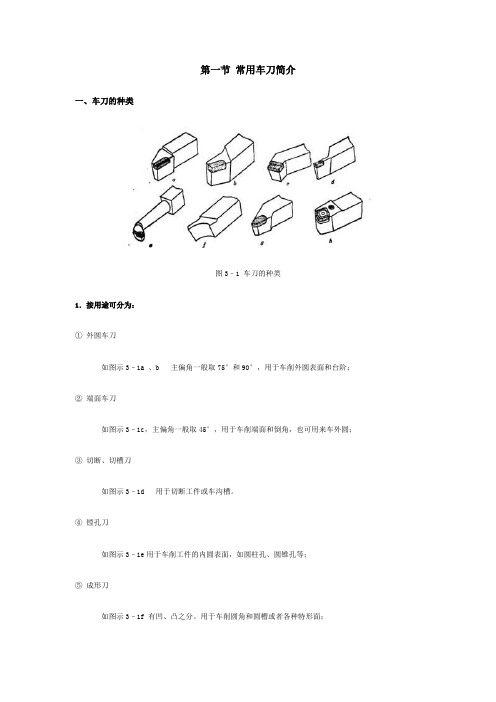
第一节常用车刀简介一、车刀的种类图3–1 车刀的种类1.按用途可分为:①外圆车刀如图示3–1a 、b 主偏角一般取75°和90°,用于车削外圆表面和台阶;②端面车刀如图示3–1c,主偏角一般取45°,用于车削端面和倒角,也可用来车外圆;③切断、切槽刀如图示3–1d 用于切断工件或车沟槽。
④镗孔刀如图示3–1e用于车削工件的内圆表面,如圆柱孔、圆锥孔等;⑤成形刀如图示3–1f 有凹、凸之分。
用于车削圆角和圆槽或者各种特形面;⑥内、外螺纹车刀用于车削外圆表面的螺纹和内圆表面的螺纹。
图3–1g为外螺纹车刀。
2.按结构可分为:①整体式车刀刀头部分和刀杆部分均为同一种材料。
用作整体式车刀的刀具材料一般是整体高速钢,如图3–1f 所示。
②焊接式车刀刀头部分和刀杆部分分属两种材料。
即刀杆上镶焊硬质合金刀片,而后经刃磨所形成的车刀。
图3–1所示a、b、c、d、e、g均为焊接式车刀。
③机械夹固式车刀刀头部分和刀杆部分分属两种材料。
它是将硬质合金刀片用机械夹固的方法固定在刀杆上的,如图3–1h所示。
它又分为机夹重磨式和机夹不重磨式两种车刀。
图3–2所示即是机夹重磨式车刀。
图3–3即是机夹不重磨车刀。
两者区别在于:后者刀片形状为多边形,即多条切削刃,多个刀尖,用钝后只需将刀片转位即可使新的刀尖和刀刃进行切削而不须重新刃磨;前者刀片则只有一个刀尖和一个刀刃,用钝后就必须的刃磨。
图3–2 机夹重磨式车刀图3–3 机夹不重磨式车刀目前,机械夹固式车刀应用比较广泛。
尤其以数控车床应用更为广泛。
用于车削外圆、端面、切断、镗孔、内、外螺纹等。
二、常用车刀的用途如图3–4所示:外圆车刀(90°偏刀、75°偏刀、 60°偏刀)车外圆和台阶;端面车刀(45°弯头刀)车端面;切刀切槽和切断;螺纹车刀车内外螺纹;镗孔刀车内孔;滚花刀滚网纹和直纹;圆头刀车特形面。
图3–4 车刀用途示意图三、车刀的组成图3–5b所示为车刀组成示意图。
1车刀各部分名称

高さ
敷垫板板
ホ刀ルダ柄
高
度
度
幅宽
・刀尖 处的表
示方法
-5° -6° 5° 6° 15° 15° 0.8mm
①
②
刀 ①倾 :角
侧 ②前 :角
③
④
⑤
⑥
⑦
前 ⑤偏 :角 侧 ⑥偏 :角
刀
尖
圆
前
弧
③后
⑦半
:角
:径
侧
④后
:角
■刃先 形状和 其影响
影响到刀尖形 状的因素
刃先形状的 种类
刃 尖 強 度
刃 尖 温 度
切 削 抵 抗
切 痕
工 具 寿 命
精 加 工 面
振 刀
出 方 向
切 屑 的 流
刀 倾 ①角 侧 前 ②角 后 ③角 前 偏 ④角 侧 偏 ⑤角 刀 尖 圆 弧 半 ⑥径
●
●
●
●●●●●
●
●
●●●●
●
●●
●
●
●
●●
●
●
●●●●
■车刀 的各部 名称
・车刀 各部名 称以及 刀尖诸 处名称 (代表 例:住 友
前前偏切角刃角
横 侧逃后げ角角
前前逃后げ角角
す前く面い面
横侧す前く角い角 切刀刃倾傾角き角
前前切切削刃刃
刀ノ尖ー圆ズ弧
半径
横侧切切刃削刃
切切込深み角角
横侧切偏刃角角
侧横后逃げ面
前前后逃角げ角
チ刀ッ片プ
長长さ度
刃先高さ
刀
尖 高
车刀

9车刀刃磨1简介车刀的工作部分就是产生和处理切屑的部分,包括刀刃、使切屑断碎或卷拢的结构、排屑或容储切屑的空车刀间、切削液的通道等结构要素。
车刀的切削部分由主切削刃、副切削刃、前刀面、主后刀面和副后刀面,刀尖角组成。
车刀的切削部分和柄部(即装夹部分)的结合方式主要有整体式、焊接式、机械夹固式和焊接-机械夹固式。
机械夹固式车刀可以避免硬质合金刀片在高温焊接时产生应力和裂纹,并且刀柄可多次使用。
机械夹固式车刀一般是用螺钉和压板将刀片夹紧,装可转位刀片的机械夹固式车刀。
刀刃用钝后可以转位继续使用,而且停车换刀时间短,因此取得了迅速发展。
车刀的切削部分由主切削刃、副切削刃、前刀面、后刀面和副后刀面等组成。
它的几何形状由前角γo、后角αo、主偏角κr、刃倾角γS、副偏角κr’和刀尖圆弧半径rε所决定。
车刀几何参数的选择受多种因素影响,必须根据具体情况选取。
前角γo根据工件材料的成分和强度来选取,切削强度较高的材料时,应取较小的值。
例如,硬质合金车刀在切削普车刀通碳素钢时前角取10°~15°;在切削铬锰钢或淬火钢时取-2°~-10°。
一般情况下后角取6°~10°。
主偏角κr根据工艺系统的刚性条件而定,一般取30°~75°,刚性差时取较大的值,在车阶梯轴时,由于切削方式的需要取大于或等于90°。
刀尖圆弧半径rε和副偏角κr'一般按加工表面粗糙度的要求而选取。
刃倾角γS则根据所要求的排屑方向和刀刃强度确定。
车刀前面的型式(图2)主要根据工件材料和刀具材料的性质而定。
最简单的是平面型,正前角的平面型适用于高速钢车刀和精加工用的硬质合金车刀。
2名称车刀的切削部分由主切削刃、副切削刃、前面、后面和副后面等组成。
车刀车刀前面的型式主要根据工件材料和刀具材料的性质而定。
负前角的平面型适用于加工高强度钢和粗切铸钢件的硬质合金车刀。
车刀的结构类型
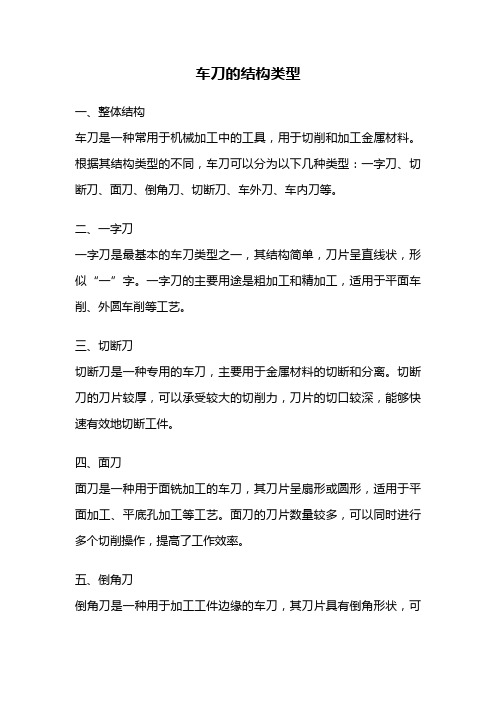
车刀的结构类型一、整体结构车刀是一种常用于机械加工中的工具,用于切削和加工金属材料。
根据其结构类型的不同,车刀可以分为以下几种类型:一字刀、切断刀、面刀、倒角刀、切断刀、车外刀、车内刀等。
二、一字刀一字刀是最基本的车刀类型之一,其结构简单,刀片呈直线状,形似“一”字。
一字刀的主要用途是粗加工和精加工,适用于平面车削、外圆车削等工艺。
三、切断刀切断刀是一种专用的车刀,主要用于金属材料的切断和分离。
切断刀的刀片较厚,可以承受较大的切削力,刀片的切口较深,能够快速有效地切断工件。
四、面刀面刀是一种用于面铣加工的车刀,其刀片呈扇形或圆形,适用于平面加工、平底孔加工等工艺。
面刀的刀片数量较多,可以同时进行多个切削操作,提高了工作效率。
五、倒角刀倒角刀是一种用于加工工件边缘的车刀,其刀片具有倒角形状,可以将工件边缘进行倒角处理,提高工件的外观质量和安全性。
六、切断刀切断刀是一种专用的车刀,其刀片具有切断刃,用于金属材料的切割和分离。
切断刀的刀片较薄,刀片的切口较浅,适用于薄板材料的切割。
七、车外刀车外刀是一种用于外圆车削的车刀,其刀片呈弧形,可以沿工件外圆表面进行切削。
车外刀适用于加工外圆孔、锥度等工艺,可以实现高精度的加工效果。
八、车内刀车内刀是一种用于内圆车削的车刀,其刀片呈圆弧形,可以沿工件内圆表面进行切削。
车内刀适用于加工内孔、倒角等工艺,可以实现高精度的加工效果。
九、总结车刀是机械加工中常用的工具,根据其结构类型的不同,可以实现不同的加工效果。
一字刀适用于平面车削;切断刀用于切断和分离;面刀用于面铣加工;倒角刀用于加工工件边缘的倒角;切断刀用于金属材料的切割;车外刀用于外圆车削;车内刀用于内圆车削。
选择合适的车刀类型可以提高加工效率和加工质量,确保工件的精度和表面质量。
机械加工行业的发展离不开各种类型的车刀的应用和改进,不断提高加工技术和工艺的水平。
车刀的结构类型的研究和创新将继续推动机械加工行业的发展。
车刀简介1

• (3) 刀杆不能重复使用,当刀片用完以后,刀杆也随之报废,
刀杆材料利用率低。 • (4) 在制造和刃磨时,由于硬质合金和刀杆材料(一般为中碳 钢) 的线膨胀系数不同,易产生焊接热应力、磨刀热应力 和裂纹。
3.焊接装配式车刀
焊接装配式车刀是将硬质合金刀片钎焊在小刀块上,再 将小刀块装配到刀杆上 。这种结构多用于重型车刀。重 型车刀体积和重量较大,采用焊接装配式结构以后,只 需装卸小刀块,刃磨省力,刀杆也可重复使用。
(a)
(b) (c) 图a~d 刃磨外圆车刀的一般步骤 a)磨前刀面 b)磨主后刀面 c)磨副后刀面 d)磨刀尖圆弧
(d)
2.磨刀注意事项
• 磨刀时,人应站在砂轮的侧前方,双手握稳车刀,用力 要均匀。 • 刃磨时,将车刀左右移动着磨,否则会使砂轮产生凹槽 。 • 磨硬质合金车刀时,不可把刀头放入水中,以免刀片突 然受冷收缩而碎裂。磨高速钢车刀时,要经常冷却,以 免失去硬度。
2.焊接车刀
所谓焊接式车刀,就是在碳钢刀杆上 按刀具几何角度的要求开出刀槽,用 焊料将硬质合金刀片焊接在刀槽内, 并按所选择的几何参数刃磨后使用的 车刀。焊接的硬质合金车刀,可用于 高速切削。
图 硬质合金焊接式车刀
• 硬质合金焊接车刀具的特点:
• (1) 结构简单、制造方便、使用灵活,一般工厂都可自制。 • (2) 可以根据切削条件和加工要求刃磨出所需的形状和角度, 硬质合金利用较充分。但其切削性能主要取决于工人刃磨 的技术水平,与现代化生产不相适应。
二 车刀的结构形式
车刀的结构形式,随着生产的发展和新 刀具材料的应用也在不断地发展。大致 可分为整体车刀、焊接车刀、焊接装配 式车刀和机夹车刀和可转位车刀。其中 可转位车刀的应用日益广泛,在车刀中 所占比例逐渐增加。
车刀基本知识介绍(全)
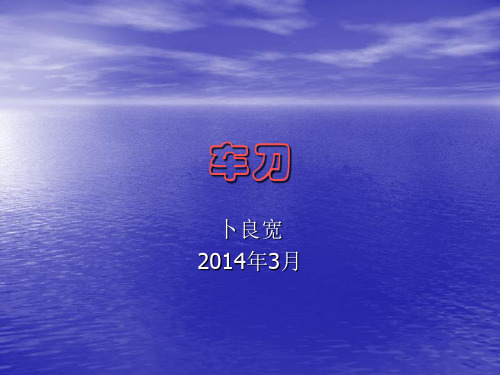
(3)切断刀 用来切断工件或在工件上切 槽。 (4)圆头刀 用来车削工件的圆弧面或成形 面。 (5)螺纹车刀 用来车削螺纹
2、车刀的用途
B.按结构可分为:
• ① 整体式车刀
刀头部分和刀杆部分均为同一种材料。用作整体 式车刀的刀具材料一般是整体高速钢。 • ② 焊接式车刀 刀头部分和刀杆部分分属两种材料。即刀杆上 镶焊硬质合金刀片,而后经刃磨所形成的车刀。 如上图所示均为焊接式车刀。
③硬质合金可转位(不重磨、机械 夹固式)车刀
刀头部分和刀杆部分分属两种材料。它是将硬质合 金刀片用机械夹固的方法固定在刀杆上的,如下图 所示。它又分为机夹重磨式和机夹不重磨式两种 车刀。两者区别在于:后者刀片形状为多边形, 即多条切削刃,多个刀尖,用钝后只需将刀片转 位即可使新的刀尖和刀刃进行切削而不须重新刃 磨;前者刀片则只有一个刀尖和一个刀刃,用钝 后就必须的刃磨。刀片采用机械夹固方式装夹在 刀杆上,当刀片上一个切削刃磨钝后,只需将刀 片转过一个角度即可继续切削,从而大大缩短了 换刀和磨刀的时间,并提高了刀杆的利用率。
• 3、主偏角Kr的作用是减小主偏角可改
善切削刃的散热性能. 主偏角的选择:当工件刚性较差时,应选 择较大的主偏角;车细长轴时,为减小径 向力应选较大的主偏角;工件硬度高选 较小主偏角.主偏角通常取45°--90°.
• 4、副偏角Kr′的作用主要是减小副切削刃与
工件之间的摩擦,并改善工件的表面粗糙度. 副偏角一般可取10°--15°. • 5、刃倾角λs
二、车刀的角度及其初步选择
1、车刀的组成 任何车刀都是由刀头(或刀 片)和刀体两部分组成的。刀头担负切削 工作,又叫切削部分。刀体用来装夹到车 床刀架上。
刀头是由若干个刀面和切削刃组成 (如下图)
常用车刀简介讲解
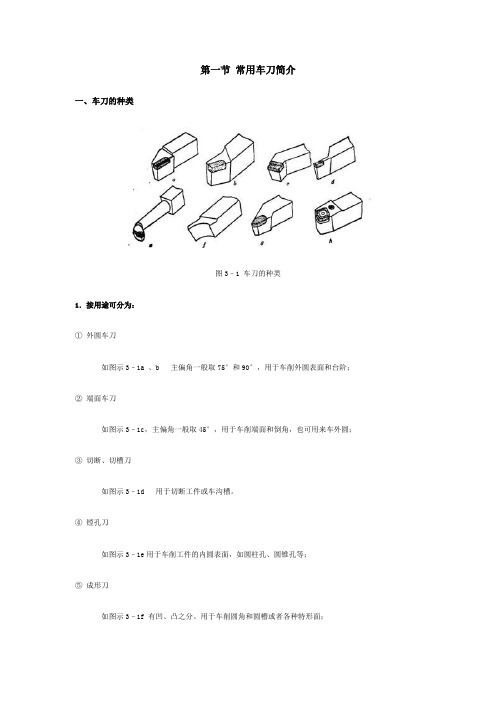
第一节常用车刀简介一、车刀的种类图3–1 车刀的种类1.按用途可分为:①外圆车刀如图示3–1a 、b 主偏角一般取75°和90°,用于车削外圆表面和台阶;②端面车刀如图示3–1c,主偏角一般取45°,用于车削端面和倒角,也可用来车外圆;③切断、切槽刀如图示3–1d 用于切断工件或车沟槽。
④镗孔刀如图示3–1e用于车削工件的内圆表面,如圆柱孔、圆锥孔等;⑤成形刀如图示3–1f 有凹、凸之分。
用于车削圆角和圆槽或者各种特形面;⑥内、外螺纹车刀用于车削外圆表面的螺纹和内圆表面的螺纹。
图3–1g为外螺纹车刀。
2.按结构可分为:①整体式车刀刀头部分和刀杆部分均为同一种材料。
用作整体式车刀的刀具材料一般是整体高速钢,如图3–1f 所示。
②焊接式车刀刀头部分和刀杆部分分属两种材料。
即刀杆上镶焊硬质合金刀片,而后经刃磨所形成的车刀。
图3–1所示a、b、c、d、e、g均为焊接式车刀。
③机械夹固式车刀刀头部分和刀杆部分分属两种材料。
它是将硬质合金刀片用机械夹固的方法固定在刀杆上的,如图3–1h所示。
它又分为机夹重磨式和机夹不重磨式两种车刀。
图3–2所示即是机夹重磨式车刀。
图3–3即是机夹不重磨车刀。
两者区别在于:后者刀片形状为多边形,即多条切削刃,多个刀尖,用钝后只需将刀片转位即可使新的刀尖和刀刃进行切削而不须重新刃磨;前者刀片则只有一个刀尖和一个刀刃,用钝后就必须的刃磨。
图3–2 机夹重磨式车刀图3–3 机夹不重磨式车刀目前,机械夹固式车刀应用比较广泛。
尤其以数控车床应用更为广泛。
用于车削外圆、端面、切断、镗孔、内、外螺纹等。
二、常用车刀的用途如图3–4所示:外圆车刀(90°偏刀、75°偏刀、 60°偏刀)车外圆和台阶;端面车刀(45°弯头刀)车端面;切刀切槽和切断;螺纹车刀车内外螺纹;镗孔刀车内孔;滚花刀滚网纹和直纹;圆头刀车特形面。
图3–4 车刀用途示意图三、车刀的组成图3–5b所示为车刀组成示意图。
- 1、下载文档前请自行甄别文档内容的完整性,平台不提供额外的编辑、内容补充、找答案等附加服务。
- 2、"仅部分预览"的文档,不可在线预览部分如存在完整性等问题,可反馈申请退款(可完整预览的文档不适用该条件!)。
- 3、如文档侵犯您的权益,请联系客服反馈,我们会尽快为您处理(人工客服工作时间:9:00-18:30)。
车刀各部位名称及功能日期:2009-9-28 来源:刀网[大中小]车刀属于单锋刀具,因车削工作物形状不同而有很多型式,但它各部位的名称及作用却是相同的。
一支良好的车刀必须具有刚性良好的刀柄及锋利的刀锋两大部份。
车刀的刀刃角度,直接影响车削效果,不同的车刀材质及工件材料、刀刃的角度亦不相同。
车床用车刀具有四个重要角度,即前间隙角、边间隙角、后斜角及边斜角。
1 前间隙角自刀鼻往下向刀内倾斜的角度为前间隙角,因有前间隙角,工作面和刀尖下形成一空间,使切削作用集中于刀鼻。
若此角度太小,刀具将在表面上摩擦,而产生粗糙面,角度太大,刀具容易发生震颤,使刀鼻碎裂无法光制。
装上具有倾斜中刀把的车刀磨前间隙角时,需考虑刀把倾斜角度。
高速钢车刀此角度约8~10度之间,碳化物车刀则在6~8度之间。
2 边间隙角刀侧面自切削边向刀内倾斜的角度为边间隙角。
边间隙角使工作物面和刀侧面形成一空间使切削作用集中于切削边提高切削效率。
高速钢车刀此角度约10~12度之间。
3 后斜角从刀顶面自刀鼻向刀柄倾斜的角度为后斜角。
此角度主要是在引导排屑及减少排屑阻力。
切削一般金属,高速钢车刀一般为8~16度,而碳化物车刀为负倾角或零度。
4 边斜角从刀顶面自切削边向另一边倾斜,此倾斜面和水平面所成角度为边斜角。
此角度是使切屑脱离工作物的角度,使排屑容易并获得有效之车削。
切削一般金属,高速钢车刀此角度大约为10~14度,而碳化物车刀可为正倾角也可为负倾角。
5 刀端角刀刃前端与刀柄垂直之角度。
此角度的作用为保持刀刃前端与工件有一间隙避免刀刃与工件磨擦或擦伤已加工之表面。
6 切边角刀刃前端与刀柄垂直之角度,其作用为改变切层的厚度。
同时切边角亦可改变车刀受力方向,减少进刀阻力,增加刀具寿命,因此一般粗车时,宜采用切边角较大之车刀,以减少进刀阻力,增加切削速度。
7 刀鼻半径刀刃最高点之刀口圆弧半径。
刀鼻半径大强度大,用于大的切削深度,但容易产生高频振动。
刀具材质的改良和发展是今日金属加工发展的重要课题之一,因为良好的刀具材料能有效、迅速的完成切削工作,并保持良好的刀具寿命。
不让拐角处出毛刺的数控车削方法日期:2009-9-28 来源:中国刀具信息网[大中小] 有些钢质工件要求拐角为直角,且不能有毛刺,采用数控车床加工,就能做到这点。
车刀刀尖放大看多呈圆弧型,见图8—2。
K是假想刀尖点,E、F分别是刃口圆弧与水平线和垂直线的切点。
如按图8—3和图8—4安排切削路线,会分别在外径和端面拐角处出毛刺。
如按图8—5安排,车完后工件上的毛刺与图8-4基本一样。
可见,以上三种常规的车削方法均出毛刺。
这三种车削的共同特点:切削刃有段时间离开工件轮廓线,这就给出毛刺提供了机会。
按图8—5车削此部分的程序为N4 G01 X100 F0.3:N5 Z-50:光看程序,似乎刀尖一直在工件轮廓线上,但程序中指令的是假想刀尖的位置。
从图8—5可以看到,在实际切削中,刀刃上的F点在工件上A到B点、E点在工件上C到A点间移动时,切削刃就离开了工件轮廓线。
以先车端面后车外径为例,看出毛刺的过程。
图8-6所示是刀尖向左切削,其上的E点接近A点时的状况。
这时A 点上侧的金属受到刃口向下的挤压,部分被挤到已车过的端面外侧,而成为毛刺。
毛刺的大小和刃口锋利的程度有关。
为了不让工件出毛刺,就采用了如图8-7所示的切削路线,其程序相应改变为N4G01 X96.8 F0.3;N44G03 X100 Z-1.6 K-1.6:N5 Z-50:这样,切削完后角部两侧就不会有毛刺。
程序虽比图8-5多了一段,但刀尖移动总距离反而短,即切削时间比图8-5少。
这当中,为保证工件拐角处车削无毛刺的效果好,车削前应选精密级的刀片。
若用自动编程机编程,即使规定了端面处向上、外径处向左的连续切削,它也只编(输)出图8-5路线的程序。
要想不让出毛刺,只有对输出的程序作人为的修改:将N4段中的X指令值改为96.8,并加入N44段。
要作图8-7的无毛刺切削,严格地说,在此处就不能使用刀尖R补偿机能,即不能用C42指令,可用如下编程:N3G42 x45 Z0:N4 G01 x100F0.5:N5 Z-50:则执行时仍按图8-5走而不会按图8-7走。
如这一程序段前后的程序都使用了G42,而编程员又不想在此处去掉G42,重算其它许多处的指令值,可编如下程序:N3G42 X45 Z0:N4G01 X99.998 F0.3:N44 G03 X100 Z-0.001 K-0.001:N5 Z-50:别看只加入了半径为1gm这个微小的值、对车出轮廓没有影响的圆弧,执行时就会按图8-7的路线走,就车削出拐角处无毛刺的工件。
图数控车编程实例数控编程采用假想刀尖编程。
数控车粗加工程序如表1所示,数控车精加工程序如表2所示。
表1 数控车粗加工程序表2 数控车精加工程序以下论述的小窍门小经验都是我们在生产中经历过的,总结这些经验对今后生产中会有所启迪与提高。
下面就从单个工种与个例工件加工方面进行介绍。
1.划线方面(1)如图1所示,工件很重很大,内外部都需划线,且内外部线有相关要求。
我们采用透明塑料管找水平的方法,确定内外线的位置相对称而达到目的。
方法是:按基准要求把工件找正,在一根足够长的透明塑料管内注满水。
一头水柱到工件要求的位置,另一头通过升降塑料管达到两头水柱同高即都在工件要求的位置,之后按水柱高把内部线划出。
(2)如图2所示,需要划内外部都要考虑到的同轴圆线(图中ψ为同心圆),内外共有5个要求同轴件,并且工件很大、很重。
我们在工件两端装上带顶丝可调的找正堵板,堵板中心有ψ1.2mm的小孔,ψmm钢丝串人两端小孔内,用重锤拉直,在里外测量中心钢丝到工件所要求件的同心度,通过调正两头堵板上的顶丝达到协调同心的目的,后以堵板上的孔为中心在大端圆上划出公共同心圆。
从20世纪60年代起,二硫化钼固体润滑剂在金属切削加工领域里的推广应用,在不断总结经验的基础上,使过去难于解决的问题得到解决,使切削水平提高,下面将应用的经验实例总结于后供参考。
(1)在车削方面。
在车削球墨铸铁小轮时,常规切削,一把硬质合金刀的耐用度只能车削(5~6)个轮,后来切削中在刀上涂二硫化钼作润滑剂,刀的耐用度提高了一倍以上。
精车蜗杆时,用含2.5%二硫僻目油剂,使蜗杆表面粗糙度由.Rα3.2降低到Rα1.6。
在65Mn钢上铰孔时,采用普通乳化液,铰出的孔粗糙度只有Rα6.3,在乳化液中加入0.5%~1%二硫化钼水剂后,表面粗糙度可达Rα3.2,而且也延长了刀具寿命。
(2)在铰孔方面。
在铰削不锈钢内孔,采用普通乳化液铰孔时,刀具磨损严重、表面粗糙高,后改用在原乳化液中添加3%二硫化钼水剂,上述问题得到解决。
(3)在磨削方面。
在外圆磨砂轮上涂上二硫化钼后,在原来的条件不变的情况下,工件表面粗糙度可降低一级。
这是因为砂轮上涂了二硫化钼后,使砂轮与工件的润滑条件有所改善的原故。
(4)在齿轮加工方面。
为了降低齿轮的齿面粗糙度,在原来硫化油中添加0.5%~1%二硫化钼油剂后,使切削过程中的刀瘤消除,齿面的表面粗糙度也降低了。
(5)在低速复杂刀具方面。
用螺旋花键推刀,推40Cr钢,硬度为HRC35,直径为ψ30mm的螺旋花键孔,在原来的切削液中添入15%~20%的二硫化钼油剂,使推刀的寿命提高了60倍左右,而且使表面粗糙度降低一级。
(6)在攻丝方面。
用挤压丝锥攻丝,唯有二硫化钼作润滑剂最好,不但内螺纹表面粗糙度低,而且挤压丝锥的寿命也延长。
(7)在锯切方面。
用弓锯锯切无缝钢管时往往噪声大,锯条易损坏。
这时在锯条上涂些二硫化钼,在其它条件不变的情况下,以上问题得到解决。
此外,由于二硫化钼具有优良的润滑性能,在金属切削的范围内得到广泛的应用。
如在切削钛合金、高温合金、奥氏体不锈钢及各种合金钢时,在刀具的前后面涂一层二硫化钼,会收到良好的切削效果。
铸铁的切削特性日期:2009-9-28 来源:中国刀具信息网[大中小]一般来说,铸铁的硬度和强度越高,金属切削性能越低,从刀片和刀具可预期的寿命越低。
用于金属切削生产的铸铁其大部分类型的金属切削性能一般都很好。
金属切削性能与结构有关,较硬的珠光体铸铁其加工难度也较大。
片状石墨铸铁和可锻铸铁有优良的切削属性,而球墨铸铁相当不好。
加工铸铁时遇到的主要磨损类型为:磨蚀、粘结和扩散磨损。
磨蚀主要由碳化物、沙粒参杂物和硬的铸造表皮产生。
有积屑瘤的粘结磨损在低的切削温度和切削速度条件下发生。
铸铁的铁素体部分最容易焊接到刀片上,但这可用提高切削速度和温度来克服。
在另一方面,扩散磨损与温度有关,在高切削速度时产生,特别是使用高强度铸铁牌号时。
这些牌号有很高的抗变型能力,导致了高温。
这种磨损与铸铁和刀具之间的作用有关,这就使得一些铸铁需用陶瓷或立方氮化硼(CBN)刀具在高速下加工,以获得良好的刀具寿命和表面质量。
一般对加工铸铁所要求的典型刀具属性为:高热硬度和化学稳定性,但也与工序、工件和切削条件有关;要求切削刃有韧性、耐热疲劳磨损和刃口强度。
切削铸铁的满意程度取决于切削刃的磨损如何发展:快速变钝意味着产生热裂纹和缺口而使切削刃过早断裂、工件破损、表面质量差、过大的波纹度等。
正常的后刀面磨损、保持平衡和锋利的切削刃正是一般需要努力做到的。
干式切削及其所用刀具材料的现状(1)日期:2009-9-25 来源:中国超硬材料网[大中小]内容摘要:干切削是切削加工的发展方向就在二十年前,切削液曾是非常便宜,在大多数加工过程的成本中,其所占比例不到3%。
可是,现在不一样了,切削液在车间生产成本中所占比例上升为15%,这就不得不引起生产经营者的极大关注。
特别是那些含油的切削液已经成为一项很大的支出。
再有,许多高速加工工序加了切削液会产生烟雾,环保部门也限制切削液烟雾释放量要在允许范围内,职业安全和职工健康管理部门为了降低切削液烟雾排放允许值,正在考虑一项咨询委员会的建议。
干切削是切削加工的发展方向就在二十年前,切削液曾是非常便宜,在大多数加工过程的成本中,其所占比例不到3%。
以至没有谁会对此多加注意。
可是,现在不一样了,切削液在车间生产成本中所占比例上升为15%,这就不得不引起生产经营者的极大关注。
特别是那些含油的切削液已经成为一项很大的支出。
更重要的是它的排放污染环境,国外环保部门要监控这些混合制剂的处理。
而且,许多国家和地区也把它们划归为危险废物,如果其中含有油和某些合金,还要采取更为严厉的控制措施。
再有,许多高速加工工序加了切削液会产生烟雾,环保部门也限制切削液烟雾释放量要在允许范围内,职业安全和职工健康管理部门为了降低切削液烟雾排放允许值,正在考虑一项咨询委员会的建议。
其中包括制定比较高的切削液的价格政策。
因此,越来越多的厂家开始采用干切,以避免这笔费用和与切削液处理相关连的麻烦。