振动监测与故障诊断系统简介
电梯振动监测与诊断技术研究

电梯振动监测与诊断技术研究电梯是现代楼宇的必备组成部分,其使用频繁,对于人们的日常生活产生了非常大的便利。
然而,在电梯的使用过程中,经常会出现各种问题,其中一种主要的问题是电梯振动。
虽然有一些电梯已经具备了振动保护功能,但是由于各种因素的影响,电梯振动问题却一直存在。
为了更好地解决电梯振动问题,电梯振动监测与诊断技术应运而生。
电梯振动监测与诊断技术是指对电梯在运行中的振动信号进行实时监测、采集、处理和分析,并利用专业的技术手段,对电梯的振动状态进行诊断和判定,及时发现并解决振动问题。
该技术的研究和应用可以大大提高电梯的安全性和可靠性。
一、振动传感器的选择和安装振动传感器是电梯振动监测与诊断技术的核心部分,其主要功能是对电梯在运行中的振动信息进行采集。
因此,在选择振动传感器时,需要根据电梯的使用情况和振动特征进行选择,以确保传感器采集到的振动数据具有较高的精度和可靠性。
同时,在振动传感器的安装过程中,还需要注意安装位置和固定方式,以避免因传感器松动或振动信号失真而导致的采集误差。
二、振动特征参数的提取和分析振动参数是评价电梯振动状况的重要指标,包括加速度、速度、位移等参数。
在采集到电梯振动信号后,需要对其进行特征参数提取和分析,以确定电梯振动的频率、振幅等特征,从而为后续的诊断、控制和维护工作提供依据。
三、振动信号的诊断和故障判定电梯振动信号的诊断和故障判定是电梯振动监测与诊断技术的重要环节。
在振动信号分析的基础上,可以通过信号处理、模式识别等方法,判断电梯振动是否正常,并诊断是否存在各种故障。
通过对振动信号的分析和诊断,可以及时发现电梯运行过程中的问题,并采取相应的措施,避免意外事故的发生。
四、电梯振动的控制和维护除了诊断和判定电梯振动问题外,电梯振动监测与诊断技术还可以用于电梯振动的控制和维护。
通过分析电梯振动的特征参数,可以实时调整电梯的运行状态和速度,从而使电梯运行更加稳定。
另外,在振动监测的过程中,还可以对电梯设备进行定期的维护和检修,以确保设备的稳定运行和安全使用。
基于振动监测的风机传动链故障诊断

摘要:能源是经济持续健康发展的关键。
煤炭、石油、天然气等石化能源已不再符合绿色、清洁、环保、可持续发展的需要,用可再生新能源替代传统石化能源是我国能源可持续发展的必然选择。
风能由于具有绿色、清洁、可再生等优势,近年来随着风力发电技术的成熟越来越得到国家重视,已成为我国改善能源供给结构的重要支撑。
然而风电机组一般所处的自然环境恶劣,常在变速变载条件下工作,工况极为复杂,随着风机运行年限的增长,故障频发。
除电气外,易发故障的部件主要在传动系统,包括主轴、齿轮箱、发电机、轴承等,而风机传动系统故障大多又与振动异常相关,由此造成的损失也更大。
因此,对风电机组传动链振动进行监测、分析与诊断,对故障提前预警,有助于风机的预防性运维,保障机组可靠稳定运行。
本文在对振动测试相关理论和时域分析、频谱分析、包络分析等振动信号分析处理技术阐述基础上,结合风机结构特点,对传动链中如何实施振动监测、如何对采集的振动信号进行有效分析,以及如何依靠监测数据快速准确诊断机组故障进行了论述。
关键字:振动监测;风机;传动链;故障诊断人类生存和发展需要能源的支撑,风能作为一种清洁可再生资源,近二十来年受到世界各国的高度关注,已成为解决能源危机、响应环境保护的重要能源。
在政府的大力扶持下,我国风力发电行业得到快速发展,到2020年底,并网风电场近5000座,累计装机容量将突破2.6亿kW,在运风力发电机组超过13万台。
风电的快速发展给新能源行业带来市场机会的同时,也带来了巨大的运检挑战。
由于大多数风电场建在深山、草原、海岛、高原等自然环境恶劣区域,风力发电机组需长期在雨雪、风沙、雷电、冰冻等环境中运行,风速、风向又具有极大的不稳定性与不确定性,大多在变速变载条件下工作,工况极为复杂。
伴随风电场投运年限增长,风力发电机组内部传动部件易发生故障,实际上由于机械部件的不平衡、疲劳、磨损、断裂、胶合等问题引起的故障目前已成为风力发电机组的主要故障。
减速器故障振动的监测与诊断
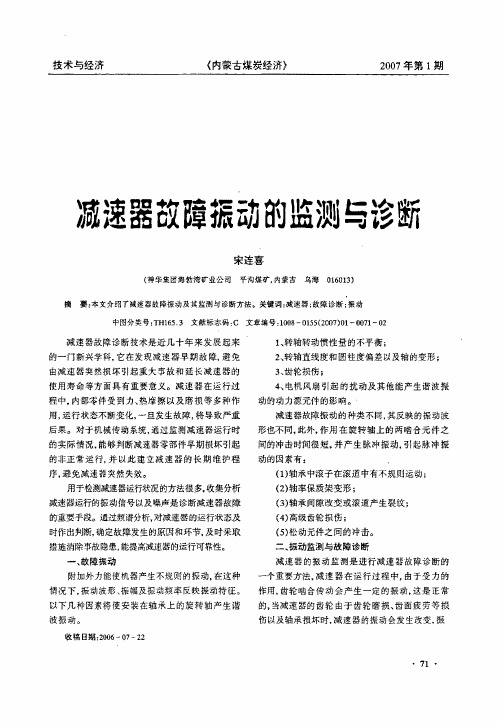
动的振幅、 频率、 速度及加速度等值均会发生变化。 齿数有关的啮合周期. 从而影响减速器的固 有颇率、 当齿轮所有的 轮齿 均匀磨损, 而使齿侧隙 增加时, 啮合频率及基频率分量的变化。 会 使振动加剧, 而且产生的冲击振动的振幅比 其他振 (4)当齿轮轴出现不平衡, 对中性不好和松动等 动大得多。 冲击振动的振幅具有几乎相同的振频, 缺陷时, 当 将出现减速器固有频率的低次频波。 发生齿轮轮齿折摄、 局部齿面磨损等局部异常时, 会 (5)当齿轮有角速度波动时, 会出现调 颜现象。 在高颇域产生非线性振动的跳跃现 即脉冲振动。 象, (6}当齿圈偏心时, 除振幅增大外, 现与偏 将出 减速器某些特征测点处的振动响应频谱可作为某些 心有关的高频调幅信号。 故障诊断的依据。以下是各类故障在频域中的显 轴承故障一般作为产生脉冲振动的因素, 而不 示。 作为产生谐波振动的因素。轴承发生故障时, 将产 ( 1) 当齿轮磨损时, 频率的振幅大小会变化, 生脉冲 高 振动, 脉冲的强度反映了撞击的程度。 通过 次 频率分量的幅道将明显增大。 检测袖承内 滚子与滚道撞击产生的振动 即可 判断 (2)当齿廓有 变形或齿根有裂纹时, 啮合频率的 轴承的 工作状态. 脉冲振动值随着轴承损伤程度的 幅值变大, 频分量也增加。 其谐 恶化而增加。
减速器 故障诊断技术是近几十年来发展起来 的一门新兴学科, 它在发现减速器早期故障, 避免
由减速器突然损坏引起重大事故和延长减速器的
1、 转轴转动惯性量的不平衡; 2、 转轴直线度和圆柱度偏差以及轴的变形;
使用寿命等方面具有重要意义。减速器在运行过 程中, 内部零件受到力、 热摩擦以及磨损等多种作 用, 运行状态不断变化, 一旦发生故障, 将导致严重
技术与经济
( 内蒙古煤炭经济》
振动检测仪表原理及故障处理.ppt

中国石油辽阳石化公司版权所有
一、电涡流传感器系统
探头及延伸电缆的标签
中国石油辽阳石化公司版权所有
一、电涡流传感器系统
二、工作原理 电涡流传感器由平绕在固体支架上的铂金丝线圈构
成,用不锈钢壳体和耐腐蚀的材料将其封装,再引出同轴电 缆猪尾线和前置器的延伸同轴电缆相连接。如图1-5所示传 感器系统连接图。
中国石油辽阳石化公司版权所有
一、电涡流传感器系统
中国石油辽阳石化公司版权所有
一、电涡流传感器系统
根据麦克斯韦尔电磁场理论,趋近传感器线圈中通入高 频电流之后,线圈周围会产生高频磁场,该磁场穿过靠近它 的转轴金属表面时,会在其中感应产生一个电涡流。根据楞 次定律,这个变化的电涡流又会在它周围产生一个电涡流磁 场,其方向和原线圈磁场的方向刚好相反,这两个磁场相叠 加,将改变原线圈的阻抗。
一、电涡流传感器系统
中国石油辽阳石化公司版权所有
一、电涡流传感器系统
只要设置一个测量变换电路,将阻抗的变化测出,并转 换成电压或电流输出,再用二次表显示出来,即可以反映间 隙的变化。
电涡流传感器在监测径向振动的同时又能监测轴向位移, 其监测原理基于电涡流传感器探头测出的与瞬时位移量X(t) 正比的输出信号,包含有直流分量X和交流分量S(t) 如图 1—7所示电涡流传感器测量曲线。
振动监测及分析系统(VMAS)在发电厂的应用

振动监测及分析系统(VMAS)在发电厂的应用摘要:振动状态监测及分析系统自动连续地采集与设备安全有关地主要状态参数:机组的振动、摆度、键相/转速、轴振、瓦振、轴位移、胀差、偏心、机组轴承负荷及温度、压力和开关量等,并自动形成各种数据库。
它能够自动识别设备的运行状态,预测和诊断设备的故障;能够促进设备维修方式向预知维修(状态维修)的转变,确保设备安全稳定地运行。
关键词:振动状态监测及分析系统(VMAS);信号处理;诊断。
0. 引言随着对发电厂主要设备可靠性、稳定性、以及对电厂设备寿命要求的提高,越来越多的监测和诊断分析系统应用到实际电厂项目中。
汽轮机、发电机、以及主要高压电动机设备作为发电厂的主要运行设备,更是成为监测和诊断的重要对象。
随着先进信号处理技术以及诊断技术的发展,振动监测及分析系统(VMAS)能在故障出现的早期阶段及时地预告故障的存在和发展,避免灾难性事故发生,并可以将现有的周期预防性维修改为预知性的维修, 选择最佳停修时间,提高机组可利用率。
1. 振动状态监测及分析系统(VMAS)的定义振动状态监测及分析系统,英文全称是Vibration monitoring and analyze system ,缩写为VMAS。
振动状态监测及分析系统的主要功能是用于主辅机(通常包括汽轮机、发电机、以及主要的高压设备)状态监测与故障诊断,实现监测、控制、报警、诊断功能。
而在早期,振动状态监测和分析系统主要应用于汽轮发电机组,叫做旋转机械诊断监测管理系统,英文TDM (Turbine diagnosis management) ,在电厂中一般是指汽轮发电机组振动在线状态监测和分析系统。
实际上,这两个叫法是针对一套系统,只是监测的范围不同。
2. 振动状态监测及分析系统基本配置振动状态监测及分析系统是以计算机为平台的旋转机械振动状态在线监测及故障诊断系统,用于对汽轮机、发电机、电动机、风机、泵等设备的振动、转速、压力、流量、温度等信号进行连续监测。
结晶器液压伺服振动系统状态监测与故障诊断

收稿 日期 :0 51。9 2 0 —l1
控制器( U)主控制器再将这些参数分配给从控制 MC , 器( 流控制器 S )从控制器每隔 1 将最新参数 铸 C, ms
维普资讯
20 0 6年 第 5期
液压 与气动
8 1
结 晶器 液压 伺 服 振 动 系统 状 态 监 测 与故 障诊 断
陈新元 张安龙 陈奎生 朱学彪 杨 , , , , 伟 S a u o i rn n u tDig o i S se f rt e t t sM n t i g a d Fa l o a n ss y t m o h
控制 结 晶器 按设定 波 形进 行振 动是 连铸 生产 中的
关键技术之一。电液伺服系统驱动的结晶器振动装置 可根据连铸工艺 实时调节振 幅、 频率 、 波形等振 动参 数, 方便高效 , 是当前最先进的驱动方式 。某炼钢厂的
2 小方 坯 连 铸 机 生 产 线 上 就 采 用 了 这种 全 液 压 5流 X 电液伺 服 非正 弦 振 动结 晶器 , 果很 好 。但 电 液伺 服 效 振动 系统 由于工 作在 结 晶器 附 近 , 度 高 、 尘 多 , 温 粉 空 间狭 小 , 技术 人员 难 以近距 离 检查测 试 , 以相对 于传 所 统 的机 械振 动系统 而 言存 在故 障率 高 、 障隐蔽 性大 、 故
上增加的设备。信号类型选取原则是原系统信号电压 采样 , 新增设备信号电流传输电压采样 , 所有信号都通 过 光 电隔离后 由数据 采 集 卡 采 样 , 入 故 障 诊 断计 算 进 机, 使工作现场与故障诊断系统 可靠隔离 , 互不影响 ,
机械制造中的智能监测与故障诊断
机械制造中的智能监测与故障诊断智能监测与故障诊断系统在现代机械制造领域发挥着越来越重要的作用。
随着技术的不断进步和自动化的不断提高,机械制造中的智能监测与故障诊断已经成为了提高生产效率和降低故障率的关键手段。
本文将探讨智能监测与故障诊断在机械制造中的应用,并介绍一些相关的技术和方法。
一、智能监测的概念与原理智能监测是指通过传感器、数据采集系统和分析算法对机械设备进行实时的、全面的监测和数据采集,并通过数据分析来评估设备的运行状态和健康状况。
智能监测所采用的传感器可以检测设备的振动、温度、压力等物理量,还可以监测设备的电流、电压、功率等电气量。
通过对这些数据的实时采集和分析,可以及时发现设备的异常行为和潜在故障,从而预测设备的寿命和提前采取维修措施。
智能监测的原理主要包括数据采集、特征提取和故障诊断。
数据采集是通过传感器将设备运行数据转换成电信号,并传输给数据采集系统。
特征提取是对所采集的数据进行预处理和特征提取,将其转换为有用的信息。
故障诊断是通过分析处理过的数据,识别设备的异常行为和潜在故障,并给出相应的维修建议。
二、智能监测与故障诊断的应用在机械制造中,智能监测与故障诊断系统被广泛应用于各种设备和机械部件。
例如,在机床制造中,智能监测系统可以实时监测机床的振动和温度,通过分析振动和温度的变化,可以判断机床是否存在松动、摩擦等故障,并提醒操作人员进行相应的维修。
在汽车制造中,智能监测系统可以监测发动机的温度、油压等参数,并根据这些数据判断发动机是否存在故障,并提醒驾驶员进行检修。
智能监测与故障诊断系统还可以应用于电力设备、飞机制造、轨道交通等领域。
三、智能监测与故障诊断的技术和方法智能监测与故障诊断系统采用了许多先进的技术和方法,包括机器学习、人工智能、模式识别等。
其中,机器学习是一种基于数据的统计建模方法,通过对大量的历史数据进行学习和训练,可以建立预测模型,实现对设备未来状态的预测和故障诊断。
振动检测仪表与系统
光电传感器
被测量 光 光信号 电信号 可用信号
光源
测量头
光电元件
电子线路
图1-22 光电式传感器基本结构框图
模数转换(A/D转换)
(1)A/D转换过程:1)采样,2)量化, 3)编码。
2)量化
量化步长 R=A/D A=10V D=256
量化误差
3)编码
A RD R ai 2i
i n m
2)三角函数窗——应用三角函数,即正弦或余弦函数等 组合成复合函数,例如汉宁窗、海明窗等;
3)指数窗——采用指数时间函数,例如高斯窗等.
(2) 常用的窗函数
(a) 矩形窗
u
优点是主瓣比较集中;
缺点是旁瓣较高,并有负旁瓣,导致变换中带进了高频 干扰和泄漏,甚至出现负谱现象
u
(b) 三角窗
三角窗与矩形窗比较,主瓣宽约等于矩形窗 的两倍,但旁瓣小,而且无负旁瓣
Z Z ( , , , )
线圈与金属的距离 金属体的电阻率、 导磁率、 线圈的激磁电流角频率。
测量电路:
(a) 阻抗分压式调幅电路;
(b) 调频电路
使用优点:接构简单,使用方便,不受油污、介质影响。 应 用:涡流式位移、力、振动测量,NDT,测厚,材质判别。
序号 测量参数
数据图表显示
知识库
故障诊断
图4-3 状态监测、分析及故障诊断系统
振动监测仪表
振动测量仪 频谱分析仪 汽轮机安全监视仪表(TSI)
振动测量仪
模拟式振动表
交流输出 振动信号 直流输出
图抗变化
衰减
放大
普通滤波
检波
图4-4 测振表的原理框图
数字测振表
数字测振表的原理框图与模拟仪表基本相同, 其差别在于将采集的电压进行模数转换后使用数 字电路对信号进行处理。 目前,数字测振表一般都具有以下功能 1) 可以储存多组测点的数; 2) 能与微机进行通讯; 3) 能够进行趋势分析。 一般振动测量的值有:1)通频幅值,2)基 波频率的幅值与相位,即1X幅值,3)跟踪测量 基波或某高次谐波的幅值(通常时2X幅值)与相 位。
小神探点检管理系统—振动分析介绍
“小神探”点检管理系统——振动分析功能介绍1 系统结构在电力、冶金等行业,存在着数量庞大价值昂贵的旋转机械,振动测量与分析作为预知旋转机械运行状态的主要手段之一,在这些行业获得了很好的应用,并取得了良好的经济效益。
“小神探”点检管理系统为用户提供了振动分析的从原始数据采集到计算机软件振动分析的一整套解决方案。
填补了在线监测系统所不能触及到的测量监控盲点,同时也为设备振动原始数据的积累提供了一个有效的管理平台。
在测量现场,振动测量分析模块与点检仪为点检人员提供了加速度、速度、位移测量功能,同时也提供了建议的频谱分析功能。
在计算机端,系统提供了趋势分析、指标计算、时域波形、频谱分析、瀑布图等多种分析形式,便于振动专家基于这些原始数据进行故障的分析与诊断。
同时数据库的应用,也极大的方便了局域网内多名专家共同对同意问题进行分析。
图12 硬件介绍测振模块是专门与小神探点检仪配合使用的机械振动测量分析模块。
该模块通过RS232接口实现模块与点检仪本体间的通信(见图2)。
可以进行加速度、速度、位的测量,由于其内部集成了高精度的模数转换器与数字信号处理器,从而具有频谱分析功能,可以进行简易的振动故障诊断。
用户可以在点检仪的“随机测量”菜单中选择测量类型(位移、速度、加速度或是频谱分析),模块经过测量计算后将测量结果上传点检仪并在液晶屏上显示;也可以在编制计划的时候定义“测振类”的数据类型,当点检到该计划时,可以将测振数据保存到点检仪中,并上传到计算机的数据库中,以供进一步的分析。
由于采用传感器与测量线路一体化的设计以及点接触式的测量方法,使用方便,很适合于工矿企业针对旋转机械的线路点检与故障诊断。
图22.1 技术参数2.2 测量模式下的参数2.2.1 测量范围加速度:0.1-200.0 m/s2(峰值)速度:0.1-200.0 mm/s(真有效值)位移:0.001-2.000 mm(峰峰值)2.2.2 频率范围加速度:10Hz-1KHz1KHz-15KHz速度:10Hz-1KHz位移:10Hz-1KHz2.3 频谱分析模式下的参数2.3.1 表格数据输出以数据的方式显示幅值最大的两个点的对应频率及幅值。
汽机振动和故障诊断系统(TDM) 合同附件
山西永济“上大压小”热电联产工程(汽机振动和故障诊断系统(TDM))合同附件买方:山西漳电蒲洲热电有限公司卖方:北京华科同安监控技术有限公司设计院: 中国能源建设集团山西省电力勘测设计院二〇一四年一月十五日目录附件1 技术规范 (1)附件2 供货范围 (10)附件3 技术资料及交付进度 (14)附件4 设备监造(工厂检验/试验) (17)附件5 性能验收试验 (20)附件6 性能保证违约金 (21)附件7 技术服务和联络 (22)附件8 交货进度 (26)附件9 分包商/外购部件情况 (27)附件10 大部件情况 (28)附件1 技术规范1. 总则1.1本技术协议适用于山西永济“上大压小”热电联产工程的汽机瞬态数据管理(振动监测和故障诊断)系统。
它提出了该系统的功能设计、结构、性能、安装和试验等方面的技术要求。
1.2本技术协议技术规范除附件1所述内容以外,附件2、3、4、5、6、7均为技术规范的要求。
如买方有除本协议以外的其他要求,应以书面形式提出。
如卖方没有对其提出书面异议,买方则可认为卖方提供的产品完全满足本协议书的要求。
1.3本技术协议所提及的要求和供货范围都是最低限度的要求,并未对一切技术细节做出规定,也未充分地详述有关标准和规范,卖方应保证提供符合本技术协议和相关工业标准的功能齐全的优质产品及其相应服务。
对国家有关安全、环保等强制性标准必须满足其要求。
并在已有的同等技术条件下有成功运行经验的优质产品。
卖方须执行本协议所列标准。
有矛盾时,按较高标准执行。
对国家有关安全、环保等强制性标准必须满足其要求。
1.4如卖方没有以书面形式对本协议的条文提出异议,或虽提出异议但未取得买方认可,买方则可认为卖方完全接受和同意本技术协议的要求。
1.5本工程采用KKS标识系统。
卖方在中标后提供的技术资料(包括图纸)和设备的标识必须有KKS编码。
系统的编制原则由买方提出,在设计联络会上讨论确定。
1.6卖方对整套系统和设备(包括辅助系统与设备)负有全责,即包括分包(或采购)的产品。
- 1、下载文档前请自行甄别文档内容的完整性,平台不提供额外的编辑、内容补充、找答案等附加服务。
- 2、"仅部分预览"的文档,不可在线预览部分如存在完整性等问题,可反馈申请退款(可完整预览的文档不适用该条件!)。
- 3、如文档侵犯您的权益,请联系客服反馈,我们会尽快为您处理(人工客服工作时间:9:00-18:30)。
数据采集子系统与气轮机组在线监测故障诊断主系统集成工作的原理如图2-2所示。
图2-2数据采集子系统的工作原理
2.
一体化设计,功能完善,结构合理,商品化的产品。
采用模块化和多CPU主从结构设计,数据采集、处理能力强大,组装、维护方便。
主CPU板和各智能模拟量信号采集板通过内存进行数据交换,数据交换速度高,吞吐量大。
标准VT100终端接口,用户可以方便对装置进行远方检测和在线配置。
工业标准设计,能够工作于各种恶劣环境。
采用电磁兼容(EMC)技术,抗电磁脉冲干扰(EMI)性能强,装置运行稳定可靠。
对敏感信号进行屏蔽。
输入信号采用光电隔离。
内部器件均选用优秀的工业级产品。
不需要特殊的加热器或冷却装置。
充分的可靠性设计,严格的质量检验,为用户提供了可靠的保证。
汽轮机振动在线监测与故障诊断
系统介绍
1
系统采用分布式结构,前端采用嵌入式结构,用于数据采集、预处理和临时存储;后端采用PC机+数据库用于数据存储、监测、分析和诊断,并作为网络服务器供其他计算机通过网络访问。
图1-1为该系统的结构图。
图1-1系统结构图
其中前端数据采集设备从TSI接入信号,并对信号做预处理,临时存储在设备内部的硬盘或其他存储设备上,然后通过网络将数据发送到网络服务器上;服务器接受数据并将其存储在数据库中,同时服务器将数据库中的信息通过动态网站的形式发布在电厂局域网上,电厂局域网用户可以通过浏览器直接访问网站,查看实时或历史数据,进行分析诊断。
键相信号(脉冲信号)接入装置后,需要光电隔离、滤波整形处理。键相信号调理电路由光电隔离器和滤波整形两部分组成。
智能模拟量信号采集板的组成如图2-4所示。
图2-4智能模拟量信号采集板
硬同步六通道同时交流采样电路由锁相环电路、六通道同时A/D转换器和运算放大器三部分组成。锁相环电路自动跟随主CPU分配的键相信号,自动产生32倍频的方波信号,这个方波信号自动启动八通道同时A/D转换器进行交流信号采样,实现在一个周期内对六个振动信号进行同时、等间隔32次采样。六通道同时A/D转换器采用BB公司的AD8364。AD8364内置6个差分采样保持放大器、6个独立工作的16位A/D转换器,可以对6路模拟量信号同时进行采样保持、分别进行A/D转换,6路A/D转换的时间为3.7us。A/D转换完成之后,AD8364向CPU提出中断请求信号。CPU响应AD8364提出的中断请求,读取6路A/D转换的结果。硬同步六通道同时交流采样电路原理如图2-5所示。
图2-7数据采集子系统正视图
2.
接线端子、接插座等安排在装置机箱的后板上。后板的布置如图2-8所示。
图2-8数据采集子系统后视图
2.
2.
4路键相信号,采集转速信号,根据配置参数由程序控制选择键相信号来启动A/D转换器工作。
24路模拟量信号,每路模拟量信号可以自由配置为路振动信号,采集振动传感器(电涡流传感器、速度传感器)输出的信号;或缓变量信号,采集位移、偏心、胀差、温度等信号。
2.
装置自动对重要可编程芯片、数据采集系统等进行在线检测,检测结果通过人机接口界面、告警记录等告知维护人员,帮助维护人员快速定位异常和故障部位。
2.
具有两级密码设置和权限管理,防止非法操作。
2.
装置的硬件和软件均经过严格的安全测试,确保不会影响现场设备的安全运行和不会危及运行人员的人身安全。
3
3.
网络服务器部分的核心是数据库,其他各部分运行都是与数据库相关的,运行原理如图3-1所示
2.
电源板是专门为数据采集子系统定制的交直流两用开关电源。主要参数如下:
输入:AC220V或DC220V输出:+来自V3A+24V1A
+24V1A
2.
主CPU板是数据采集子系统的核心,主要实现数据集中、分析、处理、储存,人机接口,键相信号调度,与上位机的网络通信等功能。主CPU板采用ATMEL公司出品的高速ARM系列32位RISC微控制器AT91RM9200作为CPU,主频为228MHz,速度高,数据处理能力强。板上扩展有大容量的程序存储器和数据存储器,用于程序和数据保存;实现了两路UART串行接口、一路USB接口、一路10Base-T网络接口,用于外部设备通信;另外,板上设计有MMC大容量FLASH存储器接口,用于历史数据保存。主CPU板通过总线底板与IAI模板连接,总线驱动电路与控制逻辑电路安装在CPU板上。主CPU和IAI模板之间采用内存数据交换进行通信,通信速度快,数据吞吐量大,保证了整个采集系统的实时性
图3-1服务器工作流程示意图
图3-1中箭头反映数据的宏观流向,其中每两个相邻模块之间也有信息的交互。
服务器先接收前端数据采集器通过网络发送过来的数据,在这里进行相应的处理,然后转存到数据库中。而IIS服务器是一个Web站点服务器,通过它我们将数据库中的信息加工处理,制作成动态网页,通过网站的形式发布到局域网中,其他用户就可以通过浏览器访问Web网站来进行监测、分析和诊断。同时,我们也可以通过Internet远程访问IIS服务器对电厂的机组进行远程诊断。
电源、信号入出口均有保护措施,并与主控电路隔离。
各模板地线、电源布局合理。
电源去耦滤波。
具有看门狗及数据掉电保护功能。
产品的研制、生产、检验严格按照ISO9001质量体系标准进行。
2.
数据采集子系统采用模块化和多CPU主从结构设计,由电源板、主CPU板、智能模拟量信号采集板、人机接口板等组成。数据采集系统的组成如图2-1所示。
2.
(1)输入信号是电压信号,进行FFT变换后输出,并得到相位。
(2)对于不同的传感器信号,可以选择不积分、一次积分或两次积分。
(3)根据不同的传感器设定不同的灵敏度系数。
2.
数据输出存储为一定的数据库的格式。
(1)瞬态
从100r/min开始存储数据,转速每变化△rpm存储一组数据,3000r/min以内转速不变的时候(程序判断机组处于暖机阶段),每△t存储一组数据。
2
2.
2.
(1)键相信号(脉冲电压信号)
(2)涡流传感器输出信号(电压信号)
(3)速度传感器输出信号(电压信号,可采用软件积分)
(4)有功和无功信号(直流电压信号)
(5)膨胀、差胀(补偿探头输出的直流电压)
2.
(1)瞬态
日期、时间、转速、振动、间隙电压、膨胀、差胀
(2)稳态
日期、时间、转速、振动、间隙电压、膨胀、差胀、有功和无功
软件自动判断起停机过程,每次起停机的数据存储在单独的数据包里。
(2)稳态
从定速(一般为3000r/min)开始存储,每△t存储一组数据。
(3)报警和危机
无论在瞬态和稳态过程中,当振动超过ALARM-1时,启动超限存储,同时存储波形和频谱。
以第一组警报数据为基准,当振动量超过△c时,存储当前数据,并将其作为新的基准,依次类推,进行存储;
当超过△t时,无论振动变化量有没有超过△c,均按时间顺序存储。
当振动超过ALARM-2时,启动危机事件列表存储。
2.
数据采集子系统负责采集振动信号、键相信号及缓变量信号等,并对采集的信号进行实时处理、分析及储存。数据采集子系统采用模块化和多CPU主从结构设计,确保对振动信号进行高速、高精度、同时采样。该子系统由开关电源板、主CPU板、智能模拟量信号采集板、人机接口板组成。主CPU板采用高速ARM系列32位RISC微控制器作为CPU,速度高,数据处理能力强,负责子系统的数据集中、分析、处理、储存,人机接口,键相信号调度,与上位机的网络通信等。智能模拟量信号采集板自带CPU,开机后自动从主CPU获取配置信息,根据配置要求采集各振动信号(电涡流传感器、速度传感器)和缓变量信号(位移、偏心、胀差等),对采集到的信号进行初步处理(积分或FFT),将采集和生成的数据上报主CPU;同时智能模拟量信号采集板也实现对键相信号的调理、采集。主CPU板和各智能模拟量信号采集板通过内存进行数据交换,数据交换速度高,吞吐量大,各智能模拟量信号采集板采集和生成的数据可以快速转储到主CPU的内存,确保采集系统的实时性能。
2.
以监视图、棒表、曲线等方式实时动态显示所监测的数据和状态;
2.
瞬态:从转速100r/min开始,每△rpm存储一组数据,连续纪录所有监测数据。
稳态:从定速(3000r/min)开始,每△t存储一组数据。
报警:当振动超过ALARM-1时,启动超限存储,同时存储波形和频谱,并以第一组警报数据为基准,当振动量超过△c时,存储当前数据,当超过△t时,按时间顺序存储。
2.
(1)采用组合式卡件,每个卡件可以输入6个振动信号,6个缓变量信号和一个键相信号。
(2)若干个卡件组合成一个采集器,每个采集器可以输入24个振动信号。
(3)键相信号的触发可以自由组合。即采集器的所有振动信号可以采用一个键相信号触发,也可以采用各自卡上的键相信号触发,或者某几个卡件的振动信号采用其中的任何键相信号触发。
一个10Base-T网络接口和两个RS-232接口。
支持TCP/IP和UDP/IP网络协议。
支持与多主站独立通信。
现场检测和远方检测兼备,为装置的诊断和维护提供方便。
装置自动对已注册运行的设备、重要可编程芯片、数据采集系统等进行在线检测,检测结果通过人机接口界面、告警记录等告知维护人员,帮助维护人员快速定位异常和故障部位。
主CPU板的组成原理如图2-3所示。
图2-3主CPU板的组成原理
2.
智能模拟量信号采集板采用Philps公司出品的ARM系列32位RISC微控制器LPC2138作为CPU,主要用于键相信号、振动信号和缓变量模拟信号的采样。为了保证振动信号采样的同时性,模板上采用6通道同时采样A/D转换器实现模拟量采集。每块模拟量信号采集板上设计了两片A/D转换器,完成12路模拟量采样。控制两片A/D转换器进行模数转换的键相信号由主CPU根据配置参数分配,既可以是两路独立的键相信号,也可以是同一个键相信号,这使得模拟量信号采集板的使用非常灵活方便。模拟量信号采集板通过内存交换与主CPU通信,获得主CPU的配置参数,同时将采集和处理生成的信息上报给主CPU。另外,模拟量信号采集板的数据采集和数据处理按照主CPU下发的配置参数进行,确保模拟量信号采集板与主CPU协调一致。