烧结节能技术调研
陶瓷烧结砂的烧结工艺与能耗控制技术

陶瓷烧结砂的烧结工艺与能耗控制技术陶瓷烧结砂是一种重要的材料,在建筑、陶瓷等行业具有广泛的应用。
烧结工艺和能耗控制技术是提高陶瓷烧结砂质量和减少能源消耗的关键。
本文将探讨陶瓷烧结砂的烧结工艺以及相关的能耗控制技术。
一、烧结工艺1. 烧结原理陶瓷烧结砂的烧结是指将砂料在高温下进行加热、熔融、结晶等过程,使其形成致密的陶瓷材料。
烧结原理主要包括砂料颗粒的熔融、晶体生长与凝固等步骤。
通过合理控制烧结过程中的温度、时间和气氛等因素,可以获得需求的陶瓷烧结砂。
2. 烧结温度与时间烧结温度是影响陶瓷烧结砂质量的关键因素之一。
不同的陶瓷材料对烧结温度有不同的要求。
过低的温度会导致砂料未能完全熔融,烧结不充分;而过高的温度则可能导致烧结砂出现气孔或烧结不均匀的情况。
此外,烧结时间也需要根据具体的砂料种类和要求进行调整。
3. 烧结气氛控制烧结气氛是指烧结过程中的气氛环境。
常见的烧结气氛控制方式有氧化还原气氛、氮气保护氛、真空烧结等。
适当的烧结气氛控制可以改善陶瓷烧结砂的质量,减少氧化反应和气体生成,防止烧结砂的气孔和颜色变化等问题。
二、能耗控制技术1. 高效燃烧技术烧结砂的烧结还需要耗费大量的能源。
提高燃料的燃烧效率是减少能耗的重要方法之一。
采用高效燃烧技术,如预热燃烧器、流体床燃烧器等,可以提高燃料的利用率,降低烧结砂生产过程中的能源消耗。
2. 废热回收利用烧结砂的烧结过程中会产生大量的废热,如果能够有效地回收利用这些废热,将能够进一步降低能耗。
采用余热锅炉、余热换热器等设备,可以将烟气中的热量重新利用,为其他热工艺提供热能。
3. 节能设备应用在陶瓷烧结砂的生产过程中,适当引入节能设备也是一种有效的能耗控制技术。
例如,采用高效节能的窑炉设备、节能输送设备等,可以降低能源消耗,提高生产效率。
三、总结陶瓷烧结砂的烧结工艺和能耗控制技术是提高陶瓷烧结砂质量和减少能耗的重要手段。
通过合理控制烧结温度、时间和烧结气氛,可以获得符合要求的陶瓷烧结砂;采用高效燃烧技术、废热回收利用和节能设备应用等措施,能够有效地降低能耗。
最新烧结砖厂的技术节能

•烧结砖厂的技术节能•1. 概述建材工业是国民经济的重要原材料工业,属典型的资源依赖型工业。
我国是目前全球最大的建材生产和消费国,建材工业的年能耗总量位居我国各工业部门的第三位。
建材工业一方面大量消耗能源,同时又潜含着巨大的节能空间;在生产过程中既污染着环境,却又是全国消纳固体废弃物总量最多、为保护环境做出了重要贡献的产业。
我国砖瓦工业的产能约1万亿块(折烧结普通砖),实际产量约8500亿块(折烧结普通砖)。
如果按每kg成品耗热1600kJ(含干燥及焙烧)计算,全行业年消耗热量约8200万吨标煤(产品孔洞率平均按30%计),考虑到约有三分之一的热量来自煤矸石、粉煤灰等含能工业废渣,每年耗热折标煤仍达5700万吨,约占全国煤耗的1.8%。
砖瓦厂电耗贯穿于整个工艺过程,依破碎、陈化、成型、切码运、运转、热工系统设备选型不同,每万块成品电耗在350~650度,每年砖瓦工业耗电约400亿度。
由于全国绝大多数地区已将工业废渣作为焙烧的部分或全部燃料,因此,节煤的主要方向将转化为技术节能以及产品的转型节能。
随着烧结砖瓦工业技术水平和生产率的提高,国家产业政策的陆续出台,节能执法力度的加强,煤耗会有一个快速的下降,然后进入平台期;而电耗会有一个持续的增长,只有更先进的工艺、更高效的设备、更节能的电气才会有效地降低电耗。
本文仅对烧结砖厂在技术节能的措施方面给出一些讨论,希望引起业内的重视。
2. 用能标准和节能规范我国政府历来都非常重视能源的使用以及节能工作,颁布了一系列的能源政策以及节能的法律法规。
涉及到烧结砖瓦工厂的能源使用的法律法规有:1)、《中华人民共和国节约能源法》2007年10月28日修订;2)、《中华人民共和国清洁生产促进法》2002年6月29日通过;3)、《评价企业合理用电技术导则》GB/T3485-1998;4)、《评价企业合理用热技术导则》GB/T3486-1993;5)、《工业炉窑保温技术通则》GB/T16618-1996;6)、《设备及管道保温保冷技术通则》GB/T11790-1996;7)、《工业设备及管道绝热工程设计规范》GB50264-1997;8)、《设备及管道绝热设计导则》GB/T8175-2008;9)、《余热利用设备设计管理规定》YB9071-1992;10)、《节电措施经济效益计算与评价》GB/T13471-1992;11)、《综合能耗计算通则》GB/T 2589—2008;12)、《烧结砖瓦工厂设计规范》GB50701—2011;13)、《烧结砖瓦工厂节能设计规范》GB50528—2009;14)、《烧结砖瓦单位产品能源消耗限额》GBxxxxx—20xx;3. 节能措施3. 1.工艺系统节能3. 1.1. 原材料选择在建设烧结砖厂伊始,就应该对所用原材料进行较为详细的矿物学成分鉴别,确定其烧结特性以及一系列的工艺特征(如加工处理、成型、干燥等)。
烧结机节能环保新技术应用研究

烧结机节能环保新技术应用研究摘要:烧结是钢铁联合企业最重要的生产工艺环节之一,不仅能耗高,且产生大量高温有害烟气。
近年来烧结工艺通过不断的技术创新,电能、燃气、固体燃料等消耗不断下降,加之环冷机余热回收技术的发展,进一步降低了工序能耗,机头烟气的脱硫、脱硝以及二恶英治理技术也取得了突破性发展。
文章以国内某钢厂一台烧结机改造为例,汇总分析了主要节能技术和污染治理措施,并从环保角度提出了一些建议。
关键词:烧结;节能;环保一、前言随着钢铁工业的快速发展,烧结机规模也在不断扩大,2005 年 7 月国家发改委发布了《钢铁产业发展政策》,要求烧结机使用面积达到 180 m2 及以上,目前国内实际最大的烧结机已达 600 m2。
设备朝着大型化发展的同时,生产技术也逐步得到提高,这不仅体现在工艺的先进性,还表现在将节能技术贯穿于整个生产过程。
国家环保部于 2012 年发布了《钢铁烧结、球团工业大气污染物排放标准》(GB28662- 2012),对烧结机头烟气中多种有害物质以及机尾等设施颗粒物排放,均严格进行了浓度限值,这意味着钢铁企业必须在这几年完成对现有烧结系统的环保设施改造,新建的烧结机在设计时就需考虑选用高效的治理设施,确保达标排放。
二、工艺技术和设备方面的节能措施1、混合制粒技术设计采用三段式混合技术,一次混合为强力混合机,主要目的是混匀;二、三段混合均为圆筒混合机,主要目的是制粒。
总混合时间超过 8 min,使造球性能得到进一步提高,明显改善了烧结料层的透气性,并且燃料在圆筒混合机的作用下,均匀地粘在混合料表面,有助于强化烧结和降低固体燃耗。
2、厚料层烧结技术设计料层厚度 1000 mm,其中铺底料厚度控制在 20~40 mm,有利于保护台车篦条,增加烧结透气性。
烧结过程是从料层表面开始逐惭往下进行,因而沿料层高度方向就有明显的分层性,抽入烧结料层的空气经过热烧结矿层被预热,参与燃烧层的燃烧,燃烧后的废气又将下层的烧结料预热,因而料层越是向下,热量积蓄得越多,以至于达到更高的温度,这种积蓄热量的过程称为自动蓄热作用[1]。
基于钢铁厂烧结工艺的节能环保研究

基于钢铁厂烧结工艺的节能环保研究在钢铁厂的生产中,烧结工艺是能量消耗较多的环节之一,将该环节的工作进行相应的节能环保研究能够进一步提升钢铁厂的经济收益。
论文针对该问题进行了较为详尽的研究,并以烧结工艺概述作为切入点,提出了能够提升环保节能效果的应用技术。
【Abstract】In the production of iron and steel plant,the sintering process is one of the most energy-consuming links. The corresponding energy conservation and environmental protection research in this part of the work can further improve the economic benefits of the iron and steel plant. The paper makes a detailed research on this problem,and takes the summary of sintering process as the entry point,it puts forward the application technology that can improve the environmental protection and energy saving effect.标签:烧结工艺;节能;环保1 引言近年来,随着工业的繁荣发展,钢铁行业如雨后春笋般喷薄而生,日益激烈的竞争环境使其发展逐步艰难,并在惨淡的经济效益中有所体现,不仅对企业的发展构成威胁,对中国钢铁行业的发展造成了阻碍,也增添了国家节能、环保工作的压力,在钢铁厂各个工作环节中,主要的能量消耗环节之一是烧结工艺。
因此,本文在研究的过程中主要对该环节的工作进行了系统的分析、研究,并提出了相应的优化策略,对钢铁厂后续在节能环保方面的发展具有重要的指导作用。
浅谈烧结节能降耗的技术途径和措施
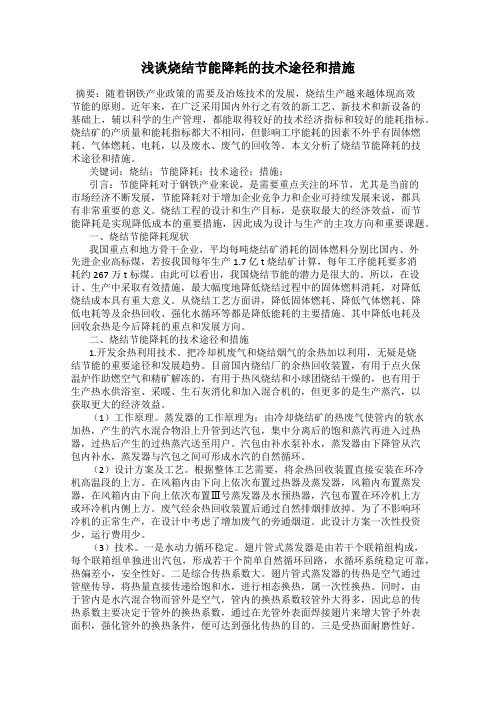
浅谈烧结节能降耗的技术途径和措施摘要:随着钢铁产业政策的需要及冶炼技术的发展,烧结生产越来越体现高效节能的原则。
近年来,在广泛采用国内外行之有效的新工艺、新技术和新设备的基础上,辅以科学的生产管理,都能取得较好的技术经济指标和较好的能耗指标。
烧结矿的产质量和能耗指标都大不相同,但影响工序能耗的因素不外乎有固体燃耗、气体燃耗、电耗,以及废水、废气的回收等。
本文分析了烧结节能降耗的技术途径和措施。
关键词:烧结;节能降耗;技术途径;措施;引言:节能降耗对于钢铁产业来说,是需要重点关注的环节,尤其是当前的市场经济不断发展,节能降耗对于增加企业竞争力和企业可持续发展来说,都具有非常重要的意义。
烧结工程的设计和生产目标,是获取最大的经济效益,而节能降耗是实现降低成本的重要措施,因此成为设计与生产的主攻方向和重要课题。
一、烧结节能降耗现状我国重点和地方骨干企业,平均每吨烧结矿消耗的固体燃料分别比国内、外先进企业高标煤,若按我国每年生产1.7亿t烧结矿计算,每年工序能耗要多消耗约267万t标煤。
由此可以看出,我国烧结节能的潜力是很大的。
所以,在设计、生产中采取有效措施,最大幅度地降低烧结过程中的固体燃料消耗,对降低烧结成本具有重大意义。
从烧结工艺方面讲,降低固体燃耗、降低气体燃耗、降低电耗等及余热回收、强化水循环等都是降低能耗的主要措施。
其中降低电耗及回收余热是今后降耗的重点和发展方向。
二、烧结节能降耗的技术途径和措施1.开发余热利用技术。
把冷却机废气和烧结烟气的余热加以利用,无疑是烧结节能的重要途径和发展趋势。
目前国内烧结厂的余热回收装置,有用于点火保温炉作助燃空气和精矿解冻的,有用于热风烧结和小球团烧结干燥的,也有用于生产热水供浴室、采暖、生石灰消化和加入混合机的,但更多的是生产蒸汽,以获取更大的经济效益。
(1)工作原理。
蒸发器的工作原理为:由冷却烧结矿的热废气使管内的软水加热,产生的汽水混合物沿上升管到达汽包,集中分离后的饱和蒸汽再进入过热器,过热后产生的过热蒸汽送至用户。
试析烧结工序节能降耗新技术发展趋势

试析烧结工序节能降耗新技术发展趋势摘要:钢铁企业长期的艰巨的任务是节能降耗,而具有极大节能潜力的是烧结工序节。
因此,在设计该工序时,节能降耗应放在首位,通过落后设备的改进和节能新技术以及新工艺的充分应用,以达到充分发挥出单体设备的节能效果,将整个系统的节能效果调配到最佳状态,以期提高生产能力的同时能源消耗得以降低,最终能够实现整个烧结工序节能降耗。
关键词:钢铁企业;烧结工序;节能降耗;新技术前言增加对用能的管理就是节能降耗,通过使用相应的措施(如:可行的技术、合理的费用和能被环境和社会接受的措施),将消耗和损失降低以及排放的污染物减少,促进能源从生产到消费的每个环节都能做到有效合理的使用。
我国可持续发展的经济、技术的提升、自然资源和环境的保护都受到节能降耗战略意义的影响。
作为能源消耗大户的钢铁企业仅烧结一项能耗就占10%-15%,因此,烧结过程中尽可能采取有效的方式降低能源消耗的意义是非常重大的。
1国内烧结工序节能技术现状1.1余热回收技术烧结烟气的余热和烧结矿显热的回收利用就是余热回收(如:余热发电、预热的混合料、预热空气点火和烧结废气循环等)。
烧结矿显热是早期余热回收研究和利用的重点(如:早期的民用热水、早期的冬季供暖和早期的试验研究等)。
同时,部分区段的热烟气在20世纪90年代左右被武钢和马钢烧结厂尝试着再次引入烧结循环过程中,这个尝试促进了利用烧结烟气余热的开启。
此外,烧结工序能耗和烟气余热回收问题在迈入新世纪后随着绿色环保理念的不断深化发展已成为“节能减排”发展中的重中之重。
国内钢铁企业采用了许多有效的措施(如:烟气循环、助燃空气预热点火、回收蒸汽利用余热和余热发电等),促使余热回收效率大大提高。
1.2厚料层烧结技术根据厚料层自身蓄热理论烧结实验发现烧结燃烧层一般情况下所需要的40%的热量就可以通过自蓄热作用提供,这种低碳操可以促进低价氧化铁氧化反应的增多,可以促进高价铁氧化物分解热耗的降低,从而实现固体燃料消耗的减少。
探究降低烧结工艺能耗的措施
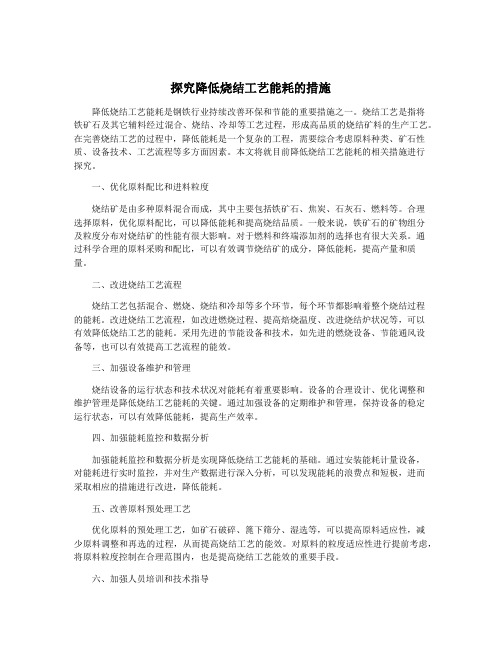
探究降低烧结工艺能耗的措施降低烧结工艺能耗是钢铁行业持续改善环保和节能的重要措施之一。
烧结工艺是指将铁矿石及其它辅料经过混合、烧结、冷却等工艺过程,形成高品质的烧结矿料的生产工艺。
在完善烧结工艺的过程中,降低能耗是一个复杂的工程,需要综合考虑原料种类、矿石性质、设备技术、工艺流程等多方面因素。
本文将就目前降低烧结工艺能耗的相关措施进行探究。
一、优化原料配比和进料粒度烧结矿是由多种原料混合而成,其中主要包括铁矿石、焦炭、石灰石、燃料等。
合理选择原料,优化原料配比,可以降低能耗和提高烧结品质。
一般来说,铁矿石的矿物组分及粒度分布对烧结矿的性能有很大影响。
对于燃料和终端添加剂的选择也有很大关系。
通过科学合理的原料采购和配比,可以有效调节烧结矿的成分,降低能耗,提高产量和质量。
二、改进烧结工艺流程烧结工艺包括混合、燃烧、烧结和冷却等多个环节,每个环节都影响着整个烧结过程的能耗。
改进烧结工艺流程,如改进燃烧过程、提高焙烧温度、改进烧结炉状况等,可以有效降低烧结工艺的能耗。
采用先进的节能设备和技术,如先进的燃烧设备、节能通风设备等,也可以有效提高工艺流程的能效。
三、加强设备维护和管理烧结设备的运行状态和技术状况对能耗有着重要影响。
设备的合理设计、优化调整和维护管理是降低烧结工艺能耗的关键。
通过加强设备的定期维护和管理,保持设备的稳定运行状态,可以有效降低能耗,提高生产效率。
四、加强能耗监控和数据分析加强能耗监控和数据分析是实现降低烧结工艺能耗的基础。
通过安装能耗计量设备,对能耗进行实时监控,并对生产数据进行深入分析,可以发现能耗的浪费点和短板,进而采取相应的措施进行改进,降低能耗。
五、改善原料预处理工艺优化原料的预处理工艺,如矿石破碎、篦下筛分、湿选等,可以提高原料适应性,减少原料调整和再选的过程,从而提高烧结工艺的能效。
对原料的粒度适应性进行提前考虑,将原料粒度控制在合理范围内,也是提高烧结工艺能效的重要手段。
微波烧结技术的研究及应用

微波烧结技术的研究及应用烧结技术作为现代工业制造的重要一环,在不同领域得到了广泛应用。
传统烧结技术需要高温、高能耗、高成本、高污染等问题一直存在着。
近年来,随着微波技术的发展,微波烧结技术逐渐受到研究者的重视。
本文将围绕微波烧结技术的研究及应用展开讨论。
一、微波烧结技术的基本原理微波烧结技术是利用微波场的电磁能量,使压力、温度等因素产生惊人变化,使物质发生化学反应、相变或者形态转化过程。
其基本原理是将微波能量转化为热能,使样品温度迅速升高,达到烧结温度,从而实现烧结。
在微波场的作用下,样品中的水分子和其他极性分子会旋转或者摆动,产生摩擦热,使样品温度升高。
对于非极性分子,由于其不具有旋转或者摆动的特性,所以对微波烧结的加热效果不明显。
因此,微波烧结技术有着选择性加热的特点。
二、微波烧结技术的研究进展目前,微波烧结技术在陶瓷材料、金属材料、无机非金属材料等领域得到了广泛应用。
其具有高效、环保、低损耗、无污染等特点,在新材料开发、仿生材料制备、能源材料制备等方面具有广阔的应用前景。
1.微波烧结技术在陶瓷材料领域的应用传统的陶瓷烧结技术需要高温环境,而微波烧结技术可以快速、均匀地加热样品,使得样品烧结时间缩短,节能环保,还可以有效控制样品微结构,提高陶瓷的品质和性能。
因此,在陶瓷材料的应用领域,微波烧结技术具有广泛的应用前景。
2.微波烧结技术在金属材料领域的应用相比于传统的金属材料烧结技术,微波烧结技术具有快速、均匀的热场分布,可以有效缩短样品的烧结时间,降低制造成本,提高生产效率。
同时,微波烧结技术可以对样品进行定向加热,从而降低热应力和变形程度,提高金属材料的性能和质量。
3.微波烧结技术在无机非金属材料领域的应用无机非金属材料中,微波烧结技术应用较为广泛,主要是因为微波烧结技术可以优化样品的微结构,提高材料的性能和质量。
例如,烧结氧化锆中,微波烧结技术可以对水份、低分子量物质进行去除,从而提高材料的致密性和强度。
- 1、下载文档前请自行甄别文档内容的完整性,平台不提供额外的编辑、内容补充、找答案等附加服务。
- 2、"仅部分预览"的文档,不可在线预览部分如存在完整性等问题,可反馈申请退款(可完整预览的文档不适用该条件!)。
- 3、如文档侵犯您的权益,请联系客服反馈,我们会尽快为您处理(人工客服工作时间:9:00-18:30)。
烧结节能技术调研我把CNKI中有关烧结节能的期刊文章都下载并阅读了(主要是《烧结球团》、《工业加热》、《科技信息》、《炼铁》、《中国钢铁业》、《上海节能》、《宝钢技术》、《钢铁》、《广西节能》、《节能》、《冶金能源》、《Energy for Metallurgical Industry》等杂志,及能找到的国内的一切学位论文),以及一些有关烧结的书籍,摘录、归类了其中的节能技术,并注明出处,重复的节能技术只摘录了一例。
稍后制作PPT。
烧结节能技术目录新烧结工艺 (4)热风烧结工艺技术 (4)从制粒入手节能 (4)小球烧结法 (4)完善燃料破碎系统 (4)强化混合料制粒 (5)改变混合料加水方式 (5)安装红外线水分控制系统 (5)控制FeO含量 (5)从布料入手节能 (9)增加烧结料层厚度 (9)铺底料烧结工艺 (9)改造烧结布料工艺 (9)从催化助燃剂入手 (11)使用SYP烧结增效剂 (12)使用ZW添加剂 (12)从燃烧入手节能 (13)采用节能型点火器 (13)燃料分加,改善固体燃料的燃烧条件 (14)从降低电耗和故障率入手 (16)降低配料除尘系统的电耗 (16)更换电子系统,配料准确计量 (17)调整烧结机冷烧比 (17)从回收利用入手 (20)回收利用废料、散料、废水等 (20)回收利用含碳工业散料 (20)合理配用各种冶金废料 (21)改变放灰方式,延长放灰时间 (21)生石灰污水消化及水幕除尘技术 (21)利用废气炉热废气预热烧结混合料温技术 (21)余热利用 (22)采用废气余热回收 (22)烧结余热发电....................................................................... 错误!未定义书签。
减少漏风. (18)改造烧结机台车滑板和机头机尾密封 (18)改造烧结机润滑系统 (19)加大烧结机抽风面积 (19)干预烧结过程..................................................................................... 错误!未定义书签。
新烧结工艺热风烧结工艺技术热风烧结工艺原理是将热空气送到烧结台车点火后的料面上进入烧结料层,使表面料层有相对长的高温保持时间,以改善烧结矿晶相发育的条件,减弱急冷应力作用使表面烧结矿脆化现象。
同时热空气自身带入的物理热也可降低烧结燃耗。
----《八钢烧结节能降耗新技术应用》本钢360 m2烧结机采用了无动力热风烧结技术,利用环冷鼓风的正压与烧结料面负压之压差,将环冷机一段的高温废气引到烧结机。
到达烧结台车料面的热风温度为260~380℃,风量达200 000 m3/h,热风罩内压力为-30~-50 Pa,热风烧结面积48 m2,热风送风时间4~6 min。
这一技术实施后,给生产带来了一系列强化作用:①增加了表面烧结所需的热量,有利于改善表层烧结矿质量,烧结矿筛分指数降低0²65%;转鼓强度提高0²2%。
②提高了保温段助燃空气的温度,有利于节省燃料和提高燃烧带温度,使烧结煤耗降低了0²5 kg/t左右。
③减少了内部循环返矿量3%~5%,烧结矿成品率提高0²5%~1%。
④提高了大烟道废气温度,改善了风机及电除尘系统的工况条件。
----《本钢三烧节能降耗的措施及效果》孙秀丽从制粒入手节能小球烧结法小球烧结法是在普通烧结法和球团法的基础上,开发出来的一种新的造块方法。
它将混合料造球,燃料两次分加,有很好的透气性和产品性能,可同时获得较高的生产率和明显的节能效果。
----《信钢烧结节能探讨》许世强郭子亮朱云奇完善燃料破碎系统在四辊破碎机前增加一台对辊破碎机,对无烟煤(焦粉)进行粗破,以改善粒度组成,减少小雨0.5mm的过粉碎量和大于3mm的粗粒级,满足烧结工艺要求。
强化混合料制粒首钢烧结所用原料主要为粒度极细的精矿,必须强化制粒,才能保证烧结过程中的料层透气性。
首钢通过不断摸索生产规律,调整混合机的长度、直径、及安装角度,使混合制粒效果得到改善。
一烧车间将二次混合机长度、直径由2.5m³6m改为3m³10m后,在筒体安装角度<2.5°的情况下,混合时间由原来的1 min延长到3.16 min,使混合料中>1 mm粒级由53.2%提高到88.67%,显著改善了料层透气性,在增加产量的同时,降低了工序能耗。
----《首钢烧结节能的实践》冯娟北京首钢股份有限公司炼铁厂改变混合料加水方式将原来的一次混合、二次混合加水,改为一混加95%的水,二混加5%的水或不加水,达到了使用污泥水,强化二混制粒的目的。
----《烧结厂节能降耗措施》乐国彪张汉泉安装红外线水分控制系统适宜而相对稳定的烧结料水分能为烧结过程热传递的相对稳定提供保证,可提高热能的利用率,不但有利于烧结过程的顺利进行,提高烧结矿的产质量,而且还有利于降低燃料的消耗。
为进一步稳定烧结料水分,2003年6月我厂在一烧结作业区试验安装了1台MM710-21CS水分测量控制系统。
系统配备了自动调节阀以实现给水量的自动控制。
试验期间,烧结矿产量提高的同时,固体燃耗和煤气消耗下降。
一烧作业区红外线水分控制仪试验期与基准期主要指标比较见表4。
红外线水分控制系统在一烧作业区取得试验成效后,2004年5月在二烧作业区混合料系统也安装了该设备,解决了人工测水劳动强度高、准确性差、不及时的问题,满足了烧结生产的需要。
----《烧结节能降耗技术》冯娟北京首钢股份有限公司炼铁厂控制FeO含量烧结矿中FeO含量随烧结料配碳量增加而升高,呈正强相关关系。
FeO下降1%.可节约固体燃料2~5kg/t。
在信钢目前的原料条件下,FeO控制在12%以下比较适宜,大约需降低3个百分点。
----《信钢烧结节能探讨》许世强郭子亮朱云奇烧结矿中FeO含量高,会造成燃料的“无益燃耗”及还原性变差。
包钢的实践表明,当FeO 含量在14%以下时, FeO每降低1%,煤耗可降低2%~3%。
因此,我们加强了对车间及岗位的考核(一烧、二烧FeO考核指标分别为10±12和9±12),要求其严格掌握配碳量。
攻关后,全厂的FeO稳定率有了明显的提高----《建龙本部烧结厂使用超低温烧结矿化节能添加剂的效果》降低钾、钠含量由于烧结矿中钾、钠的存在,导致其在燃料燃烧过程中对碳的气化反应有催化作用,造成废气中CO含量高,这也是包钢烧结固体燃耗高的主要原因之一。
减少自产精矿的配比能有效地降低烧结矿中钾、钠的含量(2000年烧结混合料中,自产精矿约占铁精矿的40%),并减少废气中CO含量。
----《建龙本部烧结厂使用超低温烧结矿化节能添加剂的效果》铁酸钙为主体的结晶相替代硅酸盐粘结相提高混合料温度烧结混合料温度较低时,水汽在料层中会形成过湿现象,使烧结料层透气性变坏。
提高混合料层温度,使其达到露点温度以上,可以显著减少或消除水汽在料层中的冷凝量,改善料层的透气性,使燃烧速度加快,提高台时产量,并且由于部分显热可部分代替固体燃料的燃烧热,因此也可以降低固体燃料的消耗。
混合料预热的主要手段有:热返矿,蒸汽预热,配加生石灰和使用烧结废气。
实践表明:生石灰配加量为2%~3%时,混合料温度提高4℃以上,固体燃耗可降低2~3kg/t。
改集中放灰为连续均匀放灰。
及时焊补和定期更换筛板,控制返矿粒度,减少返矿量。
调整水分添加量经攻关组和二烧车间对安钢现有原料进行多次试验,结果认为,一混水分应加足,使之达到6.5%~7.0%;此外,应将造球加水由原来的滴状改为雾状,水分达到7.0%~7.5%,最有利于造球。
----《安_阳_钢90m_2烧结机增产节能的措施》关红兵张宏伟王晓静机械因素90 m2烧结机系统采用了5台6000 mm的造球盘,其边高为600 mm,转速6.2~ 7.6 r/min,倾角为40°~55°。
为了根据物料性质和混合料处理量选择合理的转速和倾角,攻关小组进行了108组试验。
根据试验结果,将以前“五开三,备一,修一”和“五开四,备一”的设备制度改为五台全开,并确定了各台造球盘的合理倾角和转速。
生产操作中,为保证刮刀的正常运转,要求保持盘底平整、光滑,以稳定混合料在造球盘内的运动轨迹。
----《安_阳_钢90m_2烧结机增产节能的措施》关红兵张宏伟王晓静操作因素给水量和给料量合理及稳定与否是影响造球的主要操作因素。
通过攻关,我们认为,进入造球盘的混合料水分应稍低于适宜造球水分,同时应确定合理的给料量并保证给水量和给料量的稳定,使造球盘中的料流处于最佳造球状态。
当生产波动时,如果出现造球能力不够的现象,可以采取开四台机造球,另一台作漏斗上料,同样也能取得较好的效果。
通过上述造球攻关,混合料粒度组成大为改善(见表2),烧结料层也由原来的420 mm提高到480 mm左右。
----《安_阳_钢90m_2烧结机增产节能的措施》关红兵张宏伟王晓静改普通料仓为柔性料仓,确保料流畅通针对料仓粘料、堵料现象频繁,严重影响盘面供料的连续性和稳定性,并造成清理粘、堵料困难,增大了操作工劳动强度的情况,我们经过深入分析和认真研究,决定把料仓改为“柔性”料仓,即将料仓截为三段,段与段之间采用软连接,并垫上弹性胶垫。
这样改,可使料仓在料柱的移动过程中,借助弹性垫的弹性而自由伸缩,从而起到疏松料柱、消除死料柱的作用。
改造后的生产实践表明,柔性料仓解决了普通料仓粘、堵料严重的问题,保证了料流的畅通,能很好地满足造球机连续均匀供料的要求。
----《安(阳)钢90m2烧结机造球系统改造及实践》张宏伟陈伟关红兵王凯赵红杰造球盘安装高压雾化水喷头依据“滴水成球,雾水长大,无水紧密”的原则,我们对造球盘的加水装置进行了改进,在盘面上的生球成长区安装了高压雾化水喷头。
造球加水由滴状水和雾状水两种构成,大部分水以滴状加到料流上,少量水以雾状加在成长区的母球表面,紧密区禁止加水,以免降低生球强度和造成粘料。
----《安(阳)钢90m2烧结机造球系统改造及实践》张宏伟陈伟关红兵王凯赵红杰圆筒造球机内加水系统的改造根据圆筒造球机的造球机理,通过精确计算后,我们对筒内的加水系统进行了改造。
改造的方法是,在筒内的不同区域采取不同的加水方式,即在距筒体进料端约2 m处,添加大部分的滴状水,在筒体中部加少量雾化水,在筒体的出料端(约2²5m)不加水。
这样,既利于母球的形成,又能使母球迅速长大和密实。
----《安(阳)钢90m2烧结机造球系统改造及实践》张宏伟陈伟关红兵王凯赵红杰混合机均采用稀土含油尼龙衬板,有利于改善制粒效果本钢360m2烧结机采用三段混合工艺,三段混合设备均为圆筒混合机,混合时间达8 min 以上。