制程检验程序(二)
制程检验管理程序(含表格)

制程检验管理程序(ISO9001:2015)1.0 目的确定制程检验程序,确保制程产品质量符合顾客要求。
2.0 适用范围适用于本公司产品从样品到批量生产的整个过程。
3.0 职责3.1 品质部3.1.1 负责对品质问题进行审批、检查、总结和指示。
3.1.2 根据品质异常的状况,决定是否向责任部门发出《纠正和预防措施报告书》,并跟踪其执行和改善效果。
3.1.3 负责跟进生产过程中物料和工艺的更改。
3.2 品质部IPQC3.2.1 IPQC负责各生产部门制程内半成品巡检,并填写检查记录。
3.2.2 品质部FPQC负责制程内工序转移中半成品的检查,并填写检查记录。
3.3 QE3.3.1 根据各类记录汇总后编写品质周报、月报。
3.3.2 确保适当的SPC的采用。
3.3.3 《检验作业指导书》等标准和技术文件的编写。
3.3.4 组织和参加相关的品质会议,完善和维护制程内品质管理体系。
3.3.5 对产品品质问题及品质目标未达成时提出和建议解决办法。
3.4 各生产部门主管负责对应和改善制程内出现的品质问题。
4.0 定义4.1 制程:指从原材料投入生产,至最终成品纳入的整个过程,不包括外发加工过程。
4.2 IPQC:In-Procedure Quality Control的缩写,即从事制程内检验的人员。
4.3 OQC:Outgoing Quality Control的缩写,即从事成品检验和出货检验人员的人员。
4.4 QE:Quality Engineer品质工程师,即从事与品质管理相关的工程技术人员。
5.0 工作程序5.1 调机检查5.1.1 生产部门调机员调机过程中和调机完成后,须对调机产品进行初步检查,并将所有调机不合格产品放置在红色胶盆里,与待检品、OK品明确区分开,并标识清楚。
5.1.2 调机员或操作员自主检查合格后,应通知品质部IPQC作首件检查。
5.2 首件检查5.2.1 IPQC抽取第1件样本作首件检查,检测数据记录于《首件检查记录》中。
制程检验程序

制程检验管理程序(IATF16949/ISO9001-2015)1目的:1.1防止制程中品质变异提早发现不良原因避免不良品大量产生。
1.2增进作业人员对品质标准的认识,作为自主检查与巡回检查之基准,进而达到降低成本,提高市场竞争力。
2适用范围:自零、配件原料开始上线制造到成品包装入库完成为止均适用本办法,模具依『模具制程管理程序』。
3职责:3.1生管负责生产进度安排及物料、成品之发(领)料及保存。
3.2制造于制程中依制程作业标准书之规定做自主检查,并予以记录。
3.3品保对制程中或入库前作全程的品质检核,包括巡回检验及成品检验。
4名词定义:4.1发(领)料:仓库依生产计划发料至制造单位或由制造领料之作业。
4.2自主检查:作业人员对工作站制品自我检查并记录。
4.3巡回检查:品检人员于制程中作不定时依品质管制计划表的检查频率对现场及产品查核并予记录。
5制程检验内容:5.1作业程序5.2执行方法:5.2.1生管每月底前依客户需求排定生产计划。
5.2.2领发料作业:5.2.2.1生管依生产计划需求,以成套领发退料单依指定数量标示明确,发料至现场指定区,并经制造单位签收。
5.2.2.2.螺丝帽等法定标准件或指定物料制造单位就现场库存需求,以领料单向生管领取。
5.2.3生产作业:制造单位每日依生产计划派工,并查核所需人力、材料、设备条件等是否正确,合格后即依制程作业标准书进行生产作业及首件检查、自主检查。
5.2.4自主检查:5.2.4.1首件检查之时机:每日开机后之首件换线后之首件设备修理后之首件作业人员更换后之首件作业条件变更后之首件停电后再开机之首件。
5.2.4.2专机(线)生产之产品或生产期间长,中途有休息停机者均需做首中件检查,作业员于每日上、下午开机时做首件检查,中间休息后再开机生产时做中件检查,小批量短期间生产之产品则做首末件检查。
5.2.4.3首中件检查由作业员检查壹件,依检查项目实施并记录于自主检查表中,并在检查部品上签名,注明时间,放置于检具上或易于目视之规定处,至中件检查后再放入料架中,中件检查作业亦同,至末件检查时放入料架中。
制程检验程序

制程检验程序一、目的明确制程检验作业程序,对产品进行首件检验,首三件检验以及巡回检验,以确保生产过程中产品质量得到严格监控。
二、适用范围适用于首件、首三件以及巡回检验各过程。
三、职责生产部:负责制程定点检验区域的检验和记录,以及品质不良的改善与纠正措施的执行。
负责产品制程中首件、首三件,巡回检验及“三检制”的执行和记录。
注:“三检制”即自检、互检、巡检三道检验程序。
四、工作程序1、首件检验A、首件投入制做前,技术工艺部应首先组织工艺员,质检员,生产厂长开产前准备会,由技术工艺部主管主持讲解工艺技术要求及制做要领。
注意重点及难点,并提醒小样制做中不足和应改善之处,共商改善方略。
B、由生产厂长组织承制车缝组开产前准备会,由工艺员讲解“车缝工艺单”及工艺要求,注意事项。
C、车缝组长组织本组人员按样衣及“车缝工艺单”制做首件样板(必须全组人员共同完成)。
D、首件生产制做完成后,车缝组长自检后,负责该组的质检员依“车缝工艺单”、“后整工艺单”、《服装检验手册》及样衣对首件进行全面检查,测量,将检验结果详细记录在“首件检验记录表”上,然后由质检员将首件样衣及“首件检验记录表”送交工艺员进行复检,复检意见记录在“首件检验记录表”相应栏内,并依程序交技术质量主管得行复查及批示。
E、首件核查后,再次由工艺员组织相关车缝组,质检员开产前生产会,由工艺员主持讲解工艺要求,质检员将检验中发现的质量问题予以提示,共商改善措施。
只有首件审核完成,车缝组才可正式生产大货。
2、首三件检验A、首件检验完成后,车缝组按“首件检验记录表”及产前会的意见和生产要求去改进大货产品质量,大货应于一天内生产出三件成品,由车缝质检员进行全面检查测量。
首三件审核完成后,车缝组长须根据审核意见,督导员工生产。
B、若一天无法生产出成品,经生产部核准后可延长首三件产出时间。
C、大货生产时,操作工应做好自检和互检。
3、裁房每日须对裁剪、分包、配片、粘补,执行巡回检验,依据“裁剪工艺单”、“粘补工艺单”、《服装检验手册》进行判定,将检验结果记录于“裁房巡检日报表”并及时反馈给前准备部各组长、主管。
制程检验工作流程
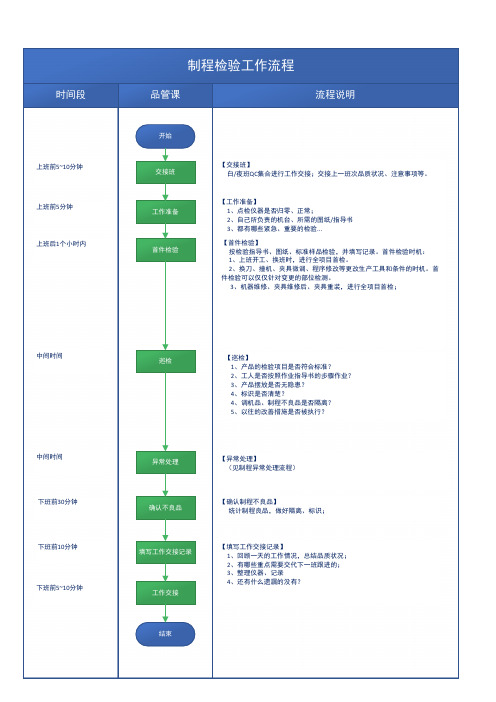
制程检验工作流程
品管课时间段流程说明
【工作准备】 1、点检仪器是否归零、正常;
2、自己所负责的机台、所需的图纸/指导书
3、都有哪些紧急、重要的检验...
交接班开始
工作准备【首件检验】
按检验指导书、图纸、标准样品检验,并填写记录。
首件检验时机:
1、上班开工、换班时,进行全项目首检。
2、换刀、撞机、夹具微调、程序修改等更改生产工具和条件的时机。
首
件检验可以仅仅针对变更的部位检测。
3、机器维修、夹具维修后、夹具重装,进行全项目首检; 【巡检】
1、产品的检验项目是否符合标准?
2、工人是否按照作业指导书的步骤作业?
3、产品摆放是否无隐患?
4、标识是否清楚?
4、调机品、制程不良品是否隔离?
5、以往的改善措施是否被执行?
【异常处理】
(见制程异常处理流程)
【确认制程不良品】
统计制程良品,做好隔离、标识;
【交接班】 白/夜班QC 集合进行工作交接;交接上一班次品质状况、注意事项等。
上班前5~10分钟上班前5分钟首件检验
上班后1个小时内巡检确认不良品下班前30分钟填写工作交接记录
下班前10分钟工作交接
下班前5~10分钟结束中间时间异常处理中间时间【填写工作交接记录】 1、回顾一天的工作情况,总结品质状况; 2、有哪些重点需要交代下一班跟进的; 3、整理仪器、记录 4、还有什么遗漏的没有?。
制程检验作业流程

3.11如果相关部门对让步接收出现争议,由转入技术部。
3.12技术部对让步接收进行裁决。
重点:
1对不合格品的处理应记录在相应检验记录中
2对不合格品处理的记录由品质部保存并按《记录管理程序》管理。
标准:
记录的完整性
即时
当月底
3个工作日
《不合格信息单》
《处罚通报》
《质量索赔单》
《纠正预防措施报告》
3.3.2如通过修理达到要求,可进行修理,以达到预期使用要求
3.4对不合格品经返工、修理后需重新检验,合格后方可流入下工序或入仓。
3.5对出现不合格品的产生原因,品质部应组织相关单位分析并落实责任单位和责任人,同时对责任单位和责任人作出相关处理。
3.6责任单位和责任人根据分析的不合格品产生原因提出改善措施上交品质部并实施
制程检验规范
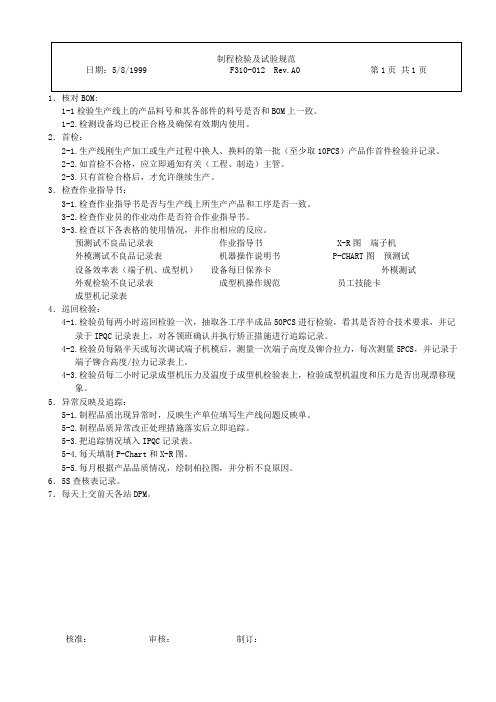
1.核对BOM:1-1检验生产线上的产品料号和其各部件的料号是否和BOM上一致。
1-2.检测设备均已校正合格及确保有效期内使用。
2.首检:2-1.生产线刚生产加工或生产过程中换人、换料的第一批(至少取10PCS)产品作首件检验并记录。
2-2.如首检不合格,应立即通知有关(工程、制造)主管。
2-3.只有首检合格后,才允许继续生产。
3.检查作业指导书:3-1.检查作业指导书是否与生产线上所生产产品和工序是否一致。
3-2.检查作业员的作业动作是否符合作业指导书。
3-3.检查以下各表格的使用情况,并作出相应的反应。
预测试不良品记录表作业指导书 X-R图端子机外模测试不良品记录表机器操作说明书 P-CHART图预测试设备效率表(端子机、成型机)设备每日保养卡外模测试外观检验不良记录表成型机操作规范员工技能卡成型机记录表4.巡回检验:4-1.检验员每两小时巡回检验一次,抽取各工序半成品50PCS进行检验,看其是否符合技术要求,并记录于IPQC记录表上,对各领班确认并执行矫正措施进行追踪记录。
4-2.检验员每隔半天或每次调试端子机模后,测量一次端子高度及铆合拉力,每次测量5PCS,并记录于端子铆合高度/拉力记录表上。
4-3.检验员每二小时记录成型机压力及温度于成型机检验表上,检验成型机温度和压力是否出现漂移现象。
5.异常反映及追踪:5-1.制程品质出现异常时,反映生产单位填写生产线问题反映单。
5-2.制程品质异常改正处理措施落实后立即追踪。
5-3.把追踪情况填入IPQC记录表。
5-4.每天填制P-Chart和X-R图。
5-5.每月根据产品品质情况,绘制柏拉图,并分析不良原因。
6.5S查核表记录。
7.每天上交前天各站DPM。
核准:审核:制订:。
制程检验规程

-制程检验规程编制/日期:审批/日期:受控状态/受控号:持有人:颁布日期: 2004. 05. 28 生效日期: 2004. 06. 01 分发范围:文件更改记录1.目的为本公司产品生产过程检验制定作业原则,尽可能防止批量报废。
2.范围适用于本公司产品生产过程检验的控制。
3. 职责3.1 品保部负责本文件的全面实施;3.2 生产部负责各生产工序的自检工作。
4. 内容4.1 由品保部主管/研发部主管负责,准备并向检验员提供以下检验标准:A、产品/零件的技术标准,如图纸、样品等;B、相应的《SOP》。
4.2 生产调试、自检、首检开始生产前,必须进行调试,由有资格的操作工进行或由领班进行;调试合格后,由操作者自检3件并作标识;然后及时通知制程检验员进行“首件检验”(即“首检”)。
制程检验员“首检”3件,只有3件产品均合格后,取1件做“首件”,才能开始批量生产,否则应重新执行调试、自检和首检程序,直到3件产品均合格为止。
领班对操作者“自检”合格/不合格的真实性负责;品保部主管对检验员“首检”合格/不合格的真实性负责。
4.3 生产工序“自检”和“巡检”批量生产开始后,由该工序操作者自己进行不定时“自检”,制程检验员按“控制计划”及相关文件的规定进行定期“巡检”。
对曾有批量不合格发生或有不良较高记录的产品、不稳定的机器设备、不理想的(如:特采)材料、第一次生产的新机种、新的操作人员等一些不稳定的因素巡检时必须特别注意。
必须确保操作人员的作业与SOP完全相符,若有任何不符必须做好记录,并且要让当班领班签名确认,以防止类似情形再次发生。
若是因SOP不符现状(必要的质控点没有、作业方式会降低生产效率等)需要修改SOP时,制程检验员要求即刻修改:将该站正确的作业方法写入该站SOP中并经原文件核准人签全名及修改日期后有效。
此批生产完毕,必须按《文件控制程序》中规定的文件修改流程执行。
一旦“自检”和“巡检”发现不合格品,制程检验员应对适当时段内的产品进行复检;必要时,由操作者进行全检。
制程检验流程

1、目的:为确保公司内部加工零件质量符合公司品质要求,避免因加工过程中的不合格零件流入下道工序而影响模具的制作周期与品质。
2、适用范围适用公司内部各工序加工的零件与装配中的模具。
3、定义:无4、职责:4.1 各工序操作员对本工序的加工零件自检并填写《工件尺寸检测记录表》以及报检,加工组长复查后并签名。
4.2 钳工组长负责加工后以及装配过程中工件的复检。
4.3 品质部制程检验员负责零件加工完成的检验制程巡检和关键零件终检, 监督纠正预防措施的实施。
4.4品质部文员负责将《异常处理单》及时交相关人员签批并将签批完成后的《异常处理单》复印给相关部门。
4.5品质工程师负责《异常处理单》的审核以及每月制程异常数据的统计与分析。
5.程序内容:5.1 操作员报检、制程检验员巡检5.1.1 各工序操作员在该工序加工完成后,严格按照加工要求以及零件图对外观、重点尺寸进行自检并填写好《工件尺寸检测记录表》,自检确认合格将《工件尺寸检测记录表》交加工组长审核后放置于指定位置报检。
5.1.2 制程检验员不停对机台巡检,收到机台操作员的报检信息或发现待检验区有已加工完成的零件根据加工要求和零件图,结合电脑3D图对其外观、尺寸进行详细的检测。
5.1.3如零件较复杂需要超过一小时的检测时间,需提前与制模组长沟通,以防止模具因非加工、装配停留的时间过长而延误交期;检验完成后,《工件尺寸检测记录表》由品质部制程检验组保存。
5.2 检验标准与测量方法5.2.1车床、钻床、铣床检验标准与测量5.2.2 CNC与数控车加工检验标准与测量方法5.2.3 EDM加工检验标准与测量方法5.2.4 线割加工检验标准与测量方法5.3品质判定5.3.1经过检验若零件外观、尺寸、性能等均符合加工要求则判定该零件此加工工序的品质状态为合格。
5.3.2经过检验若零件外观、尺寸、性能等有一项或多项不符合加工要求则判定该零件此加工工序的品质状态为不合格。
5.4 品质标识检验完成后,根据其零件的品质状态在物料上做好相应的品质状态标识(物料质量合格贴绿色“QC.PASS”标签,不合格贴红色“QC.REJ”标签),必要时在物料上用油性笔标识好模号、零件号等信息。
- 1、下载文档前请自行甄别文档内容的完整性,平台不提供额外的编辑、内容补充、找答案等附加服务。
- 2、"仅部分预览"的文档,不可在线预览部分如存在完整性等问题,可反馈申请退款(可完整预览的文档不适用该条件!)。
- 3、如文档侵犯您的权益,请联系客服反馈,我们会尽快为您处理(人工客服工作时间:9:00-18:30)。
文件名称:制程检验程序
文件编号: MF-QP-18
版本: 00
发行日期: 2009年11月02日
1.0 目的
对过程检验和试验进行控制,控制程产品质量,预防品质事故的发生,及确保未经检验和试验合格的过程产品流入下工序.
2.0 适用范围
适用本公司所有生产工序的过程产品检验。
3.0 定义
IQC: 来料品质检验
IPQC: 制程中品质检验
OQC: 最终成品品质检验
CAPA: 纠正预防措施
4.0 权责
4.1 品质部:负责制程产品的首件检验、制程中产品检验,制程巡回质量检验及控制、及转序
前的抽检
4.2 生产部:负责过程产品的全检与关键工序的专检。
4.3 工程部:签样,及对制程异常的分析及整改措施,相关工具字具的制作及管理。
制作
相关工艺流程及作业指导书。
5.0 程序
5.1. 首件产品检验
5.1.1在新产品试产阶段,或放产以后生产条件变化,材料变更,工艺变更,设计变更,客人要求变更
时,生产部需将通过自检及IPQC检测合格的产品送工程部签样。
5.1.2 在因如上原因未作首件或首件签定不合格的情况下,生产部不可安排生产。
5.1.3 按要求完成首件检验记录。
(记录:产品首件检查报告)。
5.2, 制程中检验
5.2.1品质部根据控制计划,在关键岗位设定检查点,由IPQC 在重要检验岗位对产品100%检测。
5.2.2 生产线组长,IPQC需及时监控不良率状况,在不良率超过5%时,生产线组长或IPQC需出CAPA
给生产部及工程师分析,并要求给出整改措施。
IPQC需跟进改善效果。
(记录:纠正预防措报
告)
5.3, 过程控制
5.3.1 PQC 需按照相关指引对生产过程中用到的物料,手工,过程方示,检验治具,生产条件进行核
查, 并作相应记录(记录:制程巡查记录表)。
5.3.2 IPQC根据“IPQC工作指引”按规定的时间及频次对生产现场进行巡视检查,并将巡检结果填写
在《巡查报告》上, 巡查所发现的问题需通知生产部及时整改。
5.3.3 过程半品/成品测试
a. 现场能独立完成,如涂层附着力测试,掟箱测试由IPQC完成。
b. 当测试结果为不合格时,IPQC应即时通知生产部隔离相同批次的所有物料或半品,并向上一
批次之产品进行追溯及测试,直至测试合格为至。
5.3.5, 生产异常控制
a. IPQC检查报告显示不良率超过控制比率时, 见5.2.2
b. 制程中出现其它重大质量事故时,IPQC按照相应规定出《品质异常报告书》给责任部门整
改。
c. 重大质量事故,如:
ⅰIPQC检查不良率超过10%,无法在现场及时改善。
或者按CAPA方式进行生产2个小时,仍无明显的改善效果。
ⅱ无参照样办,无作业指导书。
ⅲ关键工位缺少必要的检查工具或字具,并且无法用手工完成的工作。
ⅳ用错物料
d. 在出现诸如以上的质量事故时,IPQC 需通知品质主管,生产主管,PMC,工程部(若因技
术问题时)审批后停产。
5.4. 最终成品抽样检验
5.4.1, OQC对制程中生产成品按照相关规定对其进行抽样检验。
并作相应记录。
(记录:最终成品检
验报告)
5.4.2, 检验合格的成品,PMC需报数给客户QC验货。
5.5. 制程检验中的不合格品确认及控制。
5.5.1 IPQC 需按照“不合格品控制程序”,对制程中经IPQC 选出的不良品进行退仓前确认。
5.5.2 如若IPQC选出的不良品经确定属实,可以退仓,退上工序返工,或报废。
若不良品中有被误判,
则需按“不合格品控制程序”中的相关规定要求重新检查或测试。
5.5.3 制程中经确认的不良品需按照“不合格品控制程序”及“标识和可追溯性控制程序”进行标识及
隔离。
并填写《不合格品处理单》
5.6. 标识
5.6.1, 生产部对制程中物料,半品,成品,按照“标识和可追溯性控制程序”进行标识。
5.6.2,IPQC按照“标识和可追溯性控制程序”及对物料,半品,成品的检验状态进行标识。
6.0.表格及记录
6.1 首件检查报告
6.2 纠正预防措施要求单
6.3 制程巡查记录表
6.4 成品检验报告
6.5 品质异常报告书
6.6 不合格品处理单
7.0.相关资料
7.1标识和可追溯性控制程序MF -QP-12
7.2纠正与预防措施控制程序MF -QP-23
7.3不合格品控制程序MF- QP-21。