Structure and mechanical properties of ZrO2-mullite nano-ceramics in SiO2-Al2O3-ZrO2 system
不锈钢表面氮化dlc涂层复合改性研究

Stay on nitriding/coating composite modification of stainless steelby plasma-enhanced arc ion platingAbstractSince stainless steel was invented by the English metallurgist Henry Blair during the First World War,it became one of the most popular green material for its advantages,such as the long serving life,the low life cycle cost,recyclable material and the pleasing appearance. Now it has been widely used in every area.Recently aerospace industry,marine machineries and energy industry have developed rapidly,so stainless steel need to have better performance,especially its wear-friction properties.The experiment was operated in the arc ion plating system,1Cr17Ni2martensitic stainless steel and18-8model304austenitic stainless steel were performed surface plasma nitriding by a wire reinforced plasma,the surface morphology,composition,phase structure and mechanical properties of nitrided sample were characterized and analysised,expect to get gradually reinforced surface y the foundation for the further reinforcing.Then the DLC coating was deposited using the carbon target in the arc ion plating system to get the modified layer with high hardness and low friction coefficient to improve the surface overall properties.At first,1Cr17Ni2martensitic stainless steel was performed surface plasma nitriding by a wire reinforced plasma in the arc ion plating system.The surface morphology,composition, phase structure and mechanical properties of nitrided sample were characterized and analysised.The results showed the surface hardness of the nitrided stainless steel sample improved from3.67GPa to9.25GPa,and kept above7.32GPa at the depth range below50μm,which was attributed to the formation of new phases such as CrN and Fe2N.While compared to the substrate,the friction coefficient of nitrided sample only decreased from1.1 to0.9,failed to get the expected tribological behavior;the nitrided304austenitic stainless steel also has the reinforced properties,the surface hardness of the nitrided stainless steel sample improved from3.67GPa to6.13GPa,kept above5.32GPa at the depth range below 30μm,the surface friction coefficient only decreased from1.1to0.8,failed to get the expected tribological behavior,either.Then,on the basic of nitrided pretreatment,the DLC coating was deposited on the two kinds of stainless steel using the carbon target in the arc ion plating system.The resultsshowed when the composite treatment was conducted,high quality DLC coating with a thickness of1.5μm was successfully synthesized.The nitrided pretreatment made the surface hardness improve gradually,the hardness further increased to17.06GPa and the friction coefficient significantly reduced to0.09,obtained obvious results on strength and friction-reducing properties;so the same as304austenitic stainless steel,the surface hardness improved gradually at the depth range below31.5μm,improved from3.64GPa to5.31GPa and then to15.83GPa,the friction coefficient significantly reduced to0.08,obtain the desired properties.Key Words:stainless steel;surface modification;arc ion plating;plasma enhanced;nitriding/DLC coating composite modification目录摘要 (II)Abstract (III)1绪论 (1)1.1不锈钢分类及应用 (1)1.2不锈钢表面改性研究现状 (3)1.3论文研究内容及意义 (7)2实验设备及表征方法 (11)2.1实验设备及方法 (11)2.2表征方法 (13)2.2.1X射线衍射结构分析 (13)2.2.2扫描电镜形貌分析 (13)2.2.3电子探针成分分析 (14)2.2.4拉曼光谱成分分析 (15)2.2.5努氏表面显微硬度分析 (16)2.2.6摩擦磨损试验机摩擦性能分析 (16)31Cr17Ni2马氏体不锈钢表面氮化/DLC涂层复合改性研究 (17)3.11Cr17Ni2马氏体不锈钢氮化处理研究 (17)3.1.1氮化处理表面SEM形貌 (18)3.1.2氮化处理表面XRD相结构 (19)3.1.3氮化处理表面EPMA成分 (20)3.1.4氮化处理表面力学性能 (22)3.21Cr17Ni2马氏体不锈钢氮化/DLC涂层复合处理研究 (24)3.2.1氮化/DLC复合处理表面SEM形貌 (25)3.2.2氮化/DLC复合处理表面拉曼光谱分析 (26)3.2.3氮化/DLC复合处理表面力学性能 (27)3.3小结 (27)4304奥氏体不锈钢表面氮化/DLC涂层复合改性研究 (29)4.1304奥氏体不锈钢表面氮化处理研究 (29)4.1.1氮化处理表面SEM形貌 (30)4.1.2氮化处理表面XRD相结构 (31)4.1.3氮化处理EPMA成分 (32)4.1.4氮化处理表面力学性能 (33)4.2304奥氏体不锈钢表面氮化/DLC涂层复合改性研究 (35)4.2.1氮化/DLC涂层复合改性表面SEM形貌 (36)4.2.2氮化/DLC涂层复合改性表面拉曼光谱分析 (37)4.2.3氮化/DLC涂层复合改性表面力学性能 (38)4.3小结 (38)结论 (40)展望 (41)参考文献 (42)攻读硕士学位期间发表学术论文情况 (46)致谢 (47) (48)1绪论当前,人们正面临着信息化和科技化的时代,坚持社会可持续发展是这个时代的重大责任。
铁的氧化物的热膨胀系数及导热系数

Physical Properties of Iron-Oxide Scales on Si-Containing Steelsat High TemperatureMikako Takeda1,Takashi Onishi1,Shouhei Nakakubo1and Shinji Fujimoto21Materials Research Laboratory,Kobe Steel,Ltd.,Kobe651-2271,Japan2Graduate School of Engineering,Osaka University,Suita565-0871,JapanThe mechanical properties of oxide scales at high-temperature were studied in order to improve the surface quality of commercial Si-containing high strength steels.Specific oxides of Fe2O3,Fe3O4,FeO and Fe2SiO4were synthesized by powder metallurgy.The Vickers hardness,thermal expansion coefficient and thermal conductivity were measured at high-temperatures.A series of measurements confirmed that the physical properties of the synthesized oxides were different each other.From the Vickers hardness measurements,it was verified that the hardness of each synthesized oxide was identical with the naturally-formed iron oxide,as observed in the cross-section of oxide scales on steels. The influence of the Fe2SiO4formed on Si-containing steels on the scale adhesion at high temperature and the surface property is discussed on the basis of the physical properties of the oxides.[doi:10.2320/matertrans.M2009097](Received March18,2009;Accepted June4,2009;Published August25,2009)Keywords:high-temperature oxidation,oxide hardness,oxide thermal expansion coefficient,oxide thermal conductivity,silicon-containing steel,FeO,Fe3O4,Fe2O3,Fe2SiO4,adhesion,surface property1.IntroductionThe iron oxide scales that form on billets and slabs of hot-rolled steels are usually detached using a hydraulic descaling process.However,residual primary scales or secondary scales that form after the descaling process remain on the steel surface through subsequent hot-and cold-working,then influence the surface quality of thefinal products by modifying its mechanical properties,such as deformation, fracture and spalling.The residual scales may induce non-uniform surface temperature,which affects thefinal scale structure and mechanical properties of the steel.Hence,it is of great importance to examine/understand the physical and mechanical properties of iron oxide scales in order to control their formation and properties,and ultimately to improve the quality of steels.The oxide scales that form on steels include Fe2O3,Fe3O4, FeO,which form in lamellar strata from the substrate towards the outer layer.In the case of Si-containing steels,which are widely used for automobile bodies and frames in the form of high-tensile steel sheets,the inner-most layer,mainly composed of fayalite(Fe2SiO4)and FeO,can form at the interface between scale and steel.1–4)Therefore,the high-temperature physical properties such as hardness,thermal expansion coefficient,thermal conductivity,etc.of each oxide species need to be clarified in order to understand the deformation and fracture behaviour of scale and its influence on the surface properties after rolling.The high-temperature deformation and fracture behaviour of these oxide species are not yet well summarised in the literature.Amano et al.5)reported the Vickers hardness of Fe2O3,Fe3O4,FeO and Fe2SiO4at RT(room temperature) and at1000 C,as measured by employing micro-indenta-tion.6)In this study,5)Vickers hardnesses were measured for the lamellar constituent oxides in cross-sections of Si-containing steels.In terms of the deformation behaviour of oxides,Hidaka et al.reported on the deformation of Fe2O3, Fe3O4and FeO at600–1250 C by measuring stress-strain curves.7,8)In these studies,tensile-test specimens of pure iron were completely oxidized underfixed conditions and tensile tests atfixed strain rates were conducted to obtain the deformation and fracture behaviour.Although knowledge of such high-temperature mechanical properties of oxide scales is beneficial,their mechanical properties have been less extensively studied because high-purity specimens of specific iron oxides are required in order to measure these parameters with sufficient accuracy.This paper focuses on the hardness,thermal expansion coefficients and thermal conductivities at high-temperatures of Fe2O3,Fe3O4,FeO and Fe2SiO4which were prepared by powder metallurgy and oxidation under a controlled atmo-sphere.Furthermore,the influence of the Fe2SiO4formed on the Si-containing steel on the scale adhesion at high-temperature,and surface property were investigated.2.Experimental2.1Preparation of specific oxide specimensIn this study,pure high-density FeO,Fe3O4,Fe2O3and Fe2SiO4were prepared by powder metallurgy and oxidation under a controlled atmosphere.Sintered compacts of each oxide were used as test specimens to measure the physical properties at high temperature.Each synthesized specific oxide of iron-oxide was prepared using the following process.FeO forms on Fe under limited oxygen partial pressures, ranging from2:8Â10À13Pa(equilibrium oxygen pressure of Fe2SiO4/FeO at850 C)to2:6Â10À13Pa(equilibrium oxygen pressure of FeO/Fe3O4at850 C).FeO is the stable phase at temperatures of570 C and above,but is not stable below570 C.9)Therefore,FeO may decompose into Fe and Fe3O4at RT.FeO that is formed at high temperature can be ‘frozen-in’by quenching,but this type of material is not suitable for measuring the mechanical properties in the high-temperature phase because numerous pores are present in such FeO specimens.Materials Transactions,Vol.50,No.9(2009)pp.2242to2246 #2009The Japan Institute of MetalsIn order to prepare an FeO specimen,finely-powdered Fe and Fe3O4were mixed in the ratio8:10by weight,and were then formed into blocks,55mm square by8mm thick.The shaped blocks were compacted by cold isostatic pressing under a constant load of150MPa,and then sintered at 1100 C for3.6ks in an Ar atmosphere.The sintered blocks were pressed in a graphite mould at900 C for3.6ks in vacuum,under a constant load of50MPa.Dense sintered compacts of pure FeO werefinally obtained.On the other hand,Fe3O4forms on Fe over a wide range of oxygen pressures from2:6Â10À13Pa(equilibrium oxy-gen pressure of FeO/Fe3O4at850 C)to4:1Â10À3Pa (equilibrium oxygen pressure of Fe3O4/Fe2O3at850 C). Fe3O4is relatively stable,but can be oxidized to Fe2O3 under high partial pressures of oxygen,and is reduced to FeO under low oxygen partial pressures.In addition,Fe2O3 forms on Fe under limited partial pressures of oxygen above 4:1Â10À3Pa(equilibrium oxygen pressure of Fe3O4/Fe2O3 at850 C).Fe2O3is stable in high partial pressures of oxygen,but is unstable and can be reduced to Fe3O4under low partial pressures of oxygen,e.g.,in an inert atmosphere. The blocks offinely-powdered Fe3O4and Fe2O3were compacted by cold isostatic pressing under a constant load of300MPa,and then sintered at1100 C for3.6ks.The Fe3O4and Fe2O3were sintered in atmospheres of Ar and air,respectively.Si-containing steels promote the formation of lamellar fayalite:Fe2SiO4forms between the FeO layer and the steel substrate.Fe2SiO4forms in a narrow range of oxygen pressures between2:7Â10À14Pa(equilibrium oxygen pressure for SiO2/Fe2SiO4at850 C)and2:8Â10À13Pa (equilibrium oxygen pressure for Fe2SiO4/FeO at850 C), and therefore it is difficult to obtain pure Fe2SiO4by the oxidation of Si-containing steels.Therefore,Fe2SiO4was prepared by the sintering of fayalite powder.The natural fayalite minerals were powdered and classified into the appropriatefineness(below150mesh),then formed into blocks.The shaped blocks were compacted by cold isostatic pressing under a constant load of150MPa,and were sintered at1130 C for3.6ks in vacuum.2.2Quantitative analysis of purity and sintering densityof synthesized specific oxide specimensThe synthesized oxide specimens were identified and were quantitatively analyzed by X-ray diffraction.In the quanti-tative analysis of the synthesized oxides,the main peaks of the X-ray diffraction spectra werefitted to Gaussian curves, and the intensities of the main peaks were obtained.The relative concentrations of the synthesized specific oxide were calculated by substitution in the following equation for the peak intensity.C n¼A nÂY nÆðA iÂY iÞð1Þwhere C n is the relative concentration of component n,A n is the relative sensitivity coefficient of component n,and Y n is the peak intensity of component n.The synthesized oxide specimens were machined and their densities were obtained at room temperature by measuring the volume-to-weight ratio.2.3Measurements of physical properties2.3.1HardnessThe synthesized oxides,Fe2O3,Fe3O4,FeO and Fe2SiO4, were machined into work-pieces with dimensions of 10Â20Â3mm3,and then polished with a series of emery papers up to1500grit,buffed,finally degreased in acetone. The hardnesses of the work pieces were measured by a high-temperature micro indenter(Nikon MQ type)at temperatures up to1000 C using square-based diamond and sapphire pyramids.A load of50g was applied for30s,and3 impressions were recorded for each sample.Oxide scales that were formed on iron and steel substrates were also prepared as reference standards,and the hardnesses of these scales were also measured similarly.10mmÂ20mmÂ2mm work-pieces of high-purity Fe(99.99%)and an Fe-3.0mass%-Si alloy were oxidized at1000 C for1.8ks in an O2atmosphere.Oxide scales of about600m m in thickness were formed under the oxidation condition.The hardnesses of oxide scales were measured using the square-based diamond and sapphire pyramids as indenters for the lamellar oxides in a cross section.5)2.3.2Thermal expansion coefficientThe synthesized oxides were formed into3:5mmÂ3:5mmÂ18mm blocks,and were degreased in acetone. The thermal expansion coefficients of the work pieces were measured between room temperature and1000 C using a thermo-mechanical analyzer(Rigaku TMA8140type)at a heating rate of5 C/min.A fused quartz bar was used as a reference in this measurement.The thermal expansion coefficients of the synthesized oxides were measured in the air for Fe2O3,in an Ar atmosphere for Fe3O4and FeO,and in a He atmosphere for Fe2SiO4.2.3.3Thermal conductivityThe synthesized oxides were machined into work pieces with dimensions of 10mmÂ1:5mm,and were degreased in acetone prior to measurements.The thermal conductivities were measured at up to1000 C using a laserflash analyzer (ULVAC-RIKO TC-7000type).The specific heats were measured by differential scanning calorimetry in an Ar atmosphere.The thermal conductivities of the synthesized oxides were calculated using the thermal diffusion coeffi-cient,the specific heat and the sintering density.3.Results and Discussion3.1Purity and sintering density of iron oxide specimens The synthesized oxides were identified from X-ray diffraction spectra.Typical X-ray diffraction patterns of the synthesised oxides are shown in Figs.1to4.It was confirmed that the synthesised Fe2O3,Fe3O4and Fe2SiO4were composed of a pure single phase.Although,slight inclusions of residual -Fe and Fe3O4were indicated for the synthesized FeO as shown in Table1,FeO was the predominant compound because the concentration of Fe3O4was below 2.0mass%.From these results,we could assume that the synthesized oxides were essentially composed of single oxide species.The densities of the synthesized oxides of Fe2O3, Fe3O4,FeO and Fe2SiO4were4.69gÁcmÀ3,5.08gÁcmÀ3, 6.27gÁcmÀ3and4.08gÁcmÀ3,respectively.Considering thatPhysical Properties of Iron-Oxide Scales on Si-containing Steels at High Temperature2243the densities of Fe 2O 3,Fe 3O 4,FeO and Fe 2SiO 4noted in the literature are 5.27g Ácm À3,5.18g Ácm À3,5.70g Ácm À3and 4.34g Ácm À3respectively,the sintering density of our synthesized Fe 2O 3was slightly low and that of the synthesized FeO was slightly high compared with the values available in the literature.10)3.2HardnessThe hardnesses of synthesized iron oxides at room-and high-temperatures are shown in Fig.5.The hardnesses of all of the oxides decrease with increasing temperature,with the magnitude of the decrease occurring approximately in the following order:Fe 2SiO 4,Fe 2O 3,Fe 3O 4and FeO.In particular,the hardnesses of Fe 2SiO 4and Fe 2O 3are remarkably high at room temperature,but are equivalent to the other oxides above 400 C.The hardness of FeO is lower than the other oxides in the range between room temperature and 1000 C.The hardness of Fe 2SiO 4can not be exactly measured at 1000 C because the melting point of Fe 2SiO 4is 1170 C and the material begins to soften at 1000 C.In order to confirm the validity of these results,they were compared with the hardnesses of oxide scales formed on steels.The hardnesses of the synthesized iron oxides and of cross-sectional oxide scales on pure Fe and a Fe-3.0mass%Si alloy are listed in Table 2.Variation of hardness of the synthesized oxides is similar to that of scales formed on steels.Furthermore,the order of magnitude of thehardnessFig.1X-ray diffraction pattern of Fe 2O 3specimen.Fig.4X-ray diffraction pattern of Fe 2SiO 4specimen.Fig.2X-ray diffraction pattern of Fe 3O 4specimen.Fig.3X-ray diffraction pattern of FeO specimen.Table 1Concentration of oxide phase in FeO specimen (vol%).Fe 2O 3Fe 3O 4FeO -Fe 01.986.811.3Fig.5Hardness of the synthesized iron oxides at high-temperature.Table 2Comparison of Vickers hardness (GPa)of the respective iron oxide scales and the cross-sectional oxide scales on iron.TemperatureSample formSintered specimenScale formed on ironFeO RT 1.67 3.501000C 0.04360.05Fe 3O 4RT 1.64 4.001000 C 0.05050.08Fe 2O 3RT 3.27 6.701000 C 0.07340.53Fe 2SiO 4RT 3.29 5.501000 C—0.632244M.Takeda,T.Onishi,S.Nakakubo and S.Fujimotoof the synthesized oxides is consistent with that formed on the steels.However,the hardness of Fe 2O 3formed on the steel is much larger than synthesized Fe 2O 3at 1000 C.It is considered that the hardness of Fe 2O 3formed on the steel could not be measured precisely because its thickness is a few or several tens of m m .Therefore,it is concluded that the properties of synthesized iron oxides that had been fabricated with high purity and density corresponds to that of oxide scales formed on steels.3.3Thermal expansion coefficientAs shown in Fig.6,the thermal expansion coefficients of all of the synthesised oxides increase with increasing temperature,with magnitudes approximately in the following ascending order:FeO,Fe 3O 4,Fe 2O 3and Fe 2SiO 4.In particular,FeO exhibits the highest thermal expansion coefficient in the temperature range below 400 C.The thermal expansion coefficient of FeO abruptly increases at 600–700 C.This phenomenon may be caused by a stabiliza-tion of FeO,because FeO is becomes stable above 570 C.3.4Thermal conductivityThe temperature dependence of the thermal conductivity of the synthesized iron oxides is shown in Fig.7.The thermal conductivity is reduced approximately in the following ascending order:FeO,Fe 2O 3,Fe 3O 4and Fe 2SiO 4.A prominent feature is that FeO has the highest conductivity and Fe 2SiO 4shows the lowest in the temperature range between room temperature and 1000 C.The following is also noteworthy.The thermal conductivity of Fe 2O 3is the highest at RT,but changes remarkably smaller at high-temperature,while Fe 2SiO 4exhibits extremely reduced thermal conduc-tivity compared with FeO.3.5Influence of the physical properties of iron-oxide scales at high temperature on the surface properties of the Si-containing steelIt was shown in section 3.1–3.4that the high-temperature physical properties,such as hardness,thermal expansion coefficient,and thermal conductivity,are significantly differ-ent for each oxide species.The scale structure and oxidation behaviour on the Si-containing steel have been described in many literatures.1–4)On the Si-containing steel,inner-most layer consisting of FeO–Fe 2SiO 4mixture is formed beneath the outer FeO layer.1–4)However,Fe 2SiO 4in the inner-most layer,the amount of which increases as the Si content increases,suppresses the outward diffusion of Fe ions from steels and hence the inner diffusion of oxygen ions predominates in the oxide growth.11)Therefore,as the Si content increase,the composition of outer scale layer changes from FeO to Fe 3O 4and Fe 2O 3.11)These results show that the fayalite (Fe 2SiO 4)affects the structure of the outer and inner scale layers on Si-containing steel.In the following section,the influence of the fayalite (Fe 2SiO 4)formed on the high-Si steel on the scale adhesion at high temperature and surface properties are discussed on the basis of physical properties of iron-oxide scale.3.5.1The scale adhesion at high temperature of theSi-containing steelThe thermal stress generated by the difference in the thermal expansion coefficient between inner-most layer and steel causes a spalling and cracking of the scale during the hot-rolling process.As described above,the inner-most layer on the high-Si steel is mainly composed of Fe 2SiO 4.Therefore,the scale adhesion of high-Si steel is influenced by the difference in the thermal expansion coefficient between the Fe 2SiO 4and steel.As shown in Fig.6,the thermal expansion coefficient of Fe 2SiO 4increases as the temperature increases.The thermal expansion coefficient of Fe 2SiO 4at 1000 C is nearly equal to that of Fe(14:6Â10À6/ C at 800 C).12)By contrast,the difference in the thermal expansion coefficient of FeO and Fe is large at 1000 C.It is also reported that the scale adhesion of Fe 2SiO 4on steel at high temperature is greater than that of FeO.11)Therefore,the Fe 2SiO 4might strongly adhere to the substrate steel and is not detached by the descalingprocess.Fig.6Thermal expansion coefficients of the synthesized iron oxides athigh-temperature.Fig.7Thermal conductivities of the synthesized iron oxides at high-temperature.Physical Properties of Iron-Oxide Scales on Si-containing Steels at High Temperature 22453.5.2Surface property of the Si-containing steel afterrollingAs described above,the Fe2SiO4strongly adheres to the substrate steel,resulting in the deterioration of the descal-ability.The remaining Fe2SiO4suppresses the outward diffusion of Fe ions from the steel and hence the inner diffusion of oxygen ions predominates in the oxide growth.11) It is also shown in Fig.7that the thermal conductivity of Fe2SiO4is lower than that of other oxides.This result suggests that the remaining Fe2SiO4on the substrate steel brings about a reduction in the cooling rate and a rising of the surface temperature.As a result,the thick Fe2O3,which is a higher order oxide,is formed as the outer-most scale layer on the Fe2SiO4-coated substrate steel.Therefore,the fracture and deformation behaviour of Fe2O3may directly affect the surface properties of high-Si steel.It is shown in Fig.5that the hardness of Fe2O3is greater than that of the other oxides at800 C.It is also reported that the ability to deform Fe2O3is lower than that of FeO.7,8)As a result,the outer-most scale surface,mainly composed of Fe2O3,is crushed because of its hardness and stiffness at 800 C,corresponding to the hot-rolling temperature.Finely-ground Fe2O3is often observed on high-Si steels,which frequently form red scales on their surfaces and degrade the surface property of the high-Si steel.4.ConclusionIn the present study,we measured the high temperature physical properties of various iron oxides,constituents of oxide scales on steels,in order to clarify the dynamic behavior of the oxide scales that occur on practical steels. We selected FeO,Fe3O4,Fe2O3and Fe2SiO4as typical oxide species that formed on Si-containing steels,and synthesized artificial specimens of each type of oxide.The specimens were composed of a single oxide species,and were used to measure the hardness,the thermal expansion coefficient and the thermal conductivity over the temperature range between RT and1000 C.As a result,it was found that the physical properties of the synthesized iron oxides differed significantly from each other.The hardness of the synthe-sized iron oxides was identical with the naturally-formed corresponding iron oxide observed in cross-sectional oxide scales on practical steels.The experimental results from this study are confirmed as reflecting the physical properties of the oxide scales that form on practical steels. Moreover,we discussed the relationship between the physical properties of oxides at high temperature and surface property after rolling the Si-containing steel.It is possible that Fe2SiO4affects the high-temperature adhesion,surface temperature,and surface property of the Si-containing steel after rolling.REFERENCES1) C.W.Tuck:Corros.Sci.5(1965)631–643.2)W.W.Smeltzer,L.A.Morris and R.C.Logani:Can.Metall.Quart.9(1970)513–519.3)R.C.Logani and W.W.Smeltzer:Oxid.Met.3(1971)15–32.4)K.Yanagihara,S.Suzuki and S.Yamazaki:Oxid.Met.57(2002)281–296.5)T.Amano,M.Okazaki,Y.Takezawa,A.Shino,M.Takeda,T.Onishi,K.Seto,A.Ohkubo and T.Shishido:Mater.Sci.Forum522–523 (2006)469–476.6)G.R.Anstis,P.Chantikul,wn and D.B.Marshall:J.Am.Ceram.Soc.64(1981)533–538.7)Y.Hidaka,T.Anraku and N.Otsuka:Mater.Sci.Forum369–372(2001)555–562.8)Y.Hidaka,T.Anraku and N.Otsuka:Oxid.Met.59(2003)97–113.9)L.S.Darken and W.R.Gurry:Physical Chemistry of Metals,(McGrow-Hill Book Company,New York,1953)p.351.10)K.H.Hellwege ed.:Landolt Borstein numerical data tables,Group3,12,(Springer-Verlag,Berlin,1980)p.8.11)M.Takeda and T.Onishi:Mater.Sci.Forum522–523(2006)477–488.12)Metals Data Book,4th Edition,(Maruzen)p.14.2246M.Takeda,T.Onishi,S.Nakakubo and S.Fujimoto。
丝瓜络结构仿生材料的制备及其缓冲性能研究

丝瓜络结构仿生材料的制备及其缓冲性能研究研究生姓名:刘林指导教师姓名、职称:谢勇教授学科专业:材料加工工程研究方向:产品包装设计及制造湖南工业大学二〇一八年六月三日丝瓜络结构仿生材料的制备及其缓冲性能研究Preparation of luffa sponge structural bionic materials and its cushioning property research研究生姓名:刘林指导教师姓名、职称:谢勇教授学科专业:材料加工工程研究方向:产品包装设计及制造论文答辩日期答辩委员会主席湖南工业大学二〇一八年六月三日湖南工业大学学位论文原创性声明本人郑重声明:所呈交的学位论文,是本人在导师的指导下,独立进行研究工作所取得的成果。
除文中已经注明引用的内容外,本论文不含任何其他个人或集体已经发表或撰写过的作品成果。
对本文的研究做出重要贡献的个人和集体,均已在文中以明确方式标明。
本人完全意识到本声明的法律结果由本人承担。
作者签名:日期:年月日湖南工业大学论文版权使用授权书本人了解湖南工业大学有关保留、使用学位论文的规定,即:学校有权保留学位论文,允许学位论文被查阅和借阅;学校可以公布学位论文的全部或部分内容,可以采用复印、缩印或其他手段保存学位论文;学校可根据国家或湖南省有关部门规定送交学位论文。
作者签名:导师签名:日期:年月日摘要缓冲材料广泛应用于产品包装中,以减少产品在储运过程中受到的冲击和振动损伤。
但现阶段所使用的缓冲包装材料,大部分依然存在消耗不可再生资源、废弃后难以降解、缓冲性能较差等问题,因此探索和开发性能优良的新型绿色化、轻量化缓冲材料势在必行。
研究表明,丝瓜络是一种具有优异能量吸收特性的天然材料,它的这一特性源自其独特的多级孔隙结构。
受此启发,本文以天然丝瓜络为仿生对象,通过深入剖析其结构特征,及其结构与性能之间的关系,提取具有代表性的丝瓜络结构模型,选用更易获得的自然棕丝纤维材料进行丝瓜络仿生结构的设计,并在此基础上开展仿生结构成型工艺方法的研究和实验验证,以制备具有优良缓冲性能的环境友好型缓冲材料。
高温对含氢DLC_涂层的微观结构及力学性能的影响
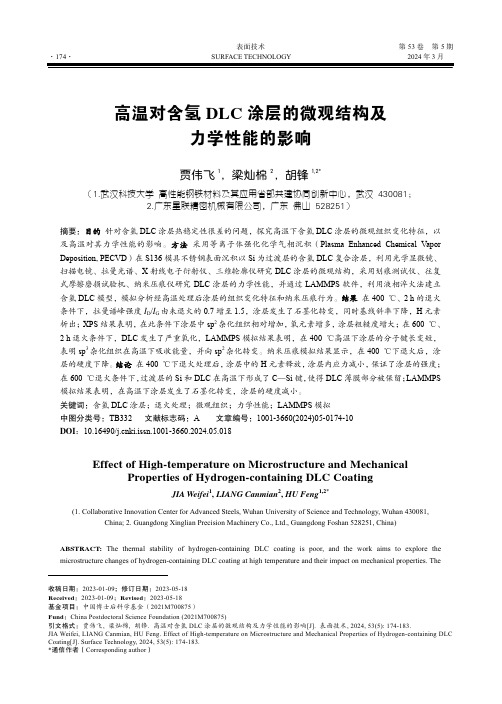
表面技术第53卷第5期高温对含氢DLC涂层的微观结构及力学性能的影响贾伟飞1,梁灿棉2,胡锋1,2*(1.武汉科技大学 高性能钢铁材料及其应用省部共建协同创新中心,武汉 430081;2.广东星联精密机械有限公司,广东 佛山 528251)摘要:目的针对含氢DLC涂层热稳定性很差的问题,探究高温下含氢DLC涂层的微观组织变化特征,以及高温对其力学性能的影响。
方法采用等离子体强化化学气相沉积(Plasma Enhanced Chemical Vapor Deposition, PECVD)在S136模具不锈钢表面沉积以Si为过渡层的含氢DLC复合涂层,利用光学显微镜、扫描电镜、拉曼光谱、X射线电子衍射仪、三维轮廓仪研究DLC涂层的微观结构,采用划痕测试仪、往复式摩擦磨损试验机、纳米压痕仪研究DLC涂层的力学性能,并通过LAMMPS软件,利用液相淬火法建立含氢DLC模型,模拟分析经高温处理后涂层的组织变化特征和纳米压痕行为。
结果在400 ℃、2 h的退火条件下,拉曼谱峰强度I D/I G由未退火的0.7增至1.5,涂层发生了石墨化转变,同时基线斜率下降,H元素析出;XPS结果表明,在此条件下涂层中sp2杂化组织相对增加,氧元素增多,涂层粗糙度增大;在600 ℃、2 h退火条件下,DLC发生了严重氧化,LAMMPS模拟结果表明,在400 ℃高温下涂层的分子键长变短,表明sp3杂化组织在高温下吸收能量,并向sp2杂化转变。
纳米压痕模拟结果显示,在400 ℃下退火后,涂层的硬度下降。
结论在400 ℃下退火处理后,涂层中的H元素释放,涂层内应力减小,保证了涂层的强度;在600 ℃退火条件下,过渡层的Si和DLC在高温下形成了C—Si键,使得DLC薄膜部分被保留;LAMMPS 模拟结果表明,在高温下涂层发生了石墨化转变,涂层的硬度减小。
关键词:含氢DLC涂层;退火处理;微观组织;力学性能;LAMMPS模拟中图分类号:TB332 文献标志码:A 文章编号:1001-3660(2024)05-0174-10DOI:10.16490/ki.issn.1001-3660.2024.05.018Effect of High-temperature on Microstructure and MechanicalProperties of Hydrogen-containing DLC CoatingJIA Weifei1, LIANG Canmian2, HU Feng1,2*(1. Collaborative Innovation Center for Advanced Steels, Wuhan University of Science and Technology, Wuhan 430081,China; 2. Guangdong Xinglian Precision Machinery Co., Ltd., Guangdong Foshan 528251, China)ABSTRACT: The thermal stability of hydrogen-containing DLC coating is poor, and the work aims to explore the microstructure changes of hydrogen-containing DLC coating at high temperature and their impact on mechanical properties. The收稿日期:2023-01-09;修订日期:2023-05-18Received:2023-01-09;Revised:2023-05-18基金项目:中国博士后科学基金(2021M700875)Fund:China Postdoctoral Science Foundation (2021M700875)引文格式:贾伟飞, 梁灿棉, 胡锋. 高温对含氢DLC涂层的微观结构及力学性能的影响[J]. 表面技术, 2024, 53(5): 174-183.JIA Weifei, LIANG Canmian, HU Feng. Effect of High-temperature on Microstructure and Mechanical Properties of Hydrogen-containing DLC Coating[J]. Surface Technology, 2024, 53(5): 174-183.*通信作者(Corresponding author)第53卷第5期贾伟飞,等:高温对含氢DLC涂层的微观结构及力学性能的影响·175·hydrogen-containing DLC composite coating with Si as the transitional layer was deposited on the surface of S136 stainless steel by plasma enhanced chemical vapor deposition (PECVD). The microstructure of DLC coating was investigated by optical/scanning electron microscopy, Raman spectroscopy, XPS (X-ray photoelectron spectroscopy) and three-dimensional profiler, the mechanical properties of DLC coating were studied by scratch, reciprocating friction wear and nano-indentation experiment, and the nano-indentation experiment behavior of DLC coating was simulated by LAMMPS to analyze the microstructure characteristics in annealing. The coating was subject to annealing conditions of 400 ℃for 2 hours and 600 ℃for 2 hours. Under the former condition, Raman spectroscopy showed an increase in the intensity ratio of the I D/I G peaks from0.7 to 1.5, indicating graphitization transition, accompanied by a decrease in baseline slope and H element segregation. XPSanalysis revealed an increase in sp2 hybridization and oxygen content in the coating under this condition, as well as an increase in surface roughness. At 600 ℃, severe oxidation of the DLC coating was observed. Under that condition, the matrix stainless steel was also oxidized. Molecular dynamics simulations using LAMMPS suggested a decrease in molecular bond length at 400 ℃high temperature. The three-dimensional profile test showed that the roughness under the unannealed condition was mainly from the large particles produced during deposition. At 400 for 2℃h, the coating had the minimum surface roughness. At this time, some large particles in the coating structure fell off, and the coating was basically completely damaged at 600 for℃ 2 h. The roughness was mainly from the original stainless steel roughness. The scratch test showed that under the condition of 400 for℃2 h, due to the release of the internal stress of the coating and the tighter bonding of the transition layer, the coating had the bestbonding effect with the substrate and was the least likely to fall off. The statistical results of LAMMPS simulation showed that the chemical bonds of the original DLC model tended to become shorter after annealing at high temperature. Relative to the unannealed DLC coating, the mechanical properties of DLC coating were best under 400 for℃ 2 h. Under this condition, the precipitation of mixed H elements in the coating led to the transformation of the original C—H sp3 structure, which occupied a large space to the smaller C—C sp3 and C—C sp2 structure, releasing internal stress in the coating, while ensuring the strength.The nano-indentation experiments showed that the elastic recovery and hardness of the coating were the highest at 400 for℃ 2 h, compared with that at other annealing temperature. The structure of the DLC coating containing hydrogen changed due to the precipitation of H element at 400 ℃. On the one hand, the coating structure changed from sp3 to sp2 due to high temperature, and on the other hand, the precipitation of H element changed the original C—H sp3 to C—C sp3, reducing the internal stress of the coating and improving the mechanical properties. The coating is basically damaged at 600 for 2 h, but the substrate still℃retains part of the coating. This is because the transition layer Si reacts with the coating to improve the heat resistance of the remaining coating. Molecular dynamics simulations using LAMMPS showed that the coating undergoes a graphitization transition at high temperature, leading to a reduction in its hardness.KEY WORDS: hydrogen-containing DLC coating; annealing treatment; microstructure; mechanical properties; LAMMPS simulationDLC(Diamond-Like Carbon,类金刚石碳,简称DLC)涂层材料具有超高硬度、低摩擦因数、优良化学稳定性等特点,广泛应用于机械、电子、生物医学等领域[1-3]。
文献名称

日本冷成型弹簧钢丝浅述一、冷成型弹簧钢丝分类弹簧钢丝1)冷拔钢丝:JISG3522琴钢丝(SWP-A、SWP-B、SWP -C、) JISG3521高碳钢丝(SWA、SWB、SWC、) JISG4314 弹簧用不锈钢丝(sus302-WPA、WPB、sus304-WPA、WPB、sus316-WPA、su3631J1-WPC) 2)热措置赏罚赏罚钢丝:JISG3560 弹簧用碳素油淬火钢丝SWD-A、SWD-B JISG3561 阀门弹簧用碳素油淬火钢丝SWD-V JISG3565 阀门弹簧用铭钒油淬火钢丝SWDCV-V JISG3566 阀门弹簧用硅铭油淬火钢丝SWDSC-V JISG3567 弹簧用硅锰油淬火钢丝SWDSM-A、SWDSM-B、SWDSM-C JSMA.NO.11 弹簧用硅铭淬火钢丝SWDSC 二、琴钢丝和高碳钢丝琴钢丝是由杂质元素(P、S、Cu)含量少的以及发纹脱碳等外貌缺陷有严厉规定的线材出产的优质弹簧原料,凡是用这种钢丝生产慎密弹簧。
高碳钢丝与琴钢丝对照,虽不要求严厉的委顿强度和弹簧特征,但与琴钢丝的差距并不年夜。
三、油淬火钢丝出产汽车阀门用弹簧钢丝有SWP -V、SWO-V、SWOCV和SWOSC-V。
连年来,跟着策念头转数的高速化和使用温度高的高温化,对淬火钢丝耐委顿机能、耐火机能又提出了更高的要求。
悬架簧向高应力,轻量化标的目的成长,今朝传统原料50CW A、SUP12、SuP7、SAE9259难以胜任1100Mpa 以上应力,趋向裁减而它们的更换品SAE9254TV、SRS60、UHS1900 UHS2000趋于普及使用。
四、弹簧用不锈钢丝弹簧出产对不锈钢丝也有严厉的要求。
除了应具有不锈耐蚀的特点外,此刻要求不锈钢丝应具有更高的抗拉强度,而委顿寿命应与琴钢丝对比美。
沉淀硬化型不锈弹簧丝具有更普及的远景。
而跟着拉丝救援原料的开发,使这统统正在慢慢实现。
五、外貌措置赏罚赏罚钢丝1)各类镀层钢丝:一样寻常情形下弹簧成型后再度层,会影响弹簧的机能而授与先镀后拉生产的钢丝可以在必然程度上淘汰这种情形。
Effect of B addition on the microstructures and mechanical properties of Nb–16Si–10Mo–15W alloy

Materials Science and Engineering A384(2004)377–384Effect of B addition on the microstructures andmechanical properties of Nb–16Si–10Mo–15W alloyC.L.Ma a,b,∗,J.G.Li a,Y.Tan b,R.Tanaka b,S.Hanada ca School of Materials Science and Engineering,Shanghai Jiao Tong University,Shanghai200030,PR Chinab Japan Ultra-high Temperature Materials Research Institute,Ube755-0001,Japanc Institute for Materials Research,Tohoku University,Sendai980-8577,JapanReceived29March2004;received in revised form14June2004AbstractNb-silicide based,hypoeutectic Nb–16Si–10Mo–15W alloys doped with various amounts of boron from0to10at.%were prepared by arc melting and annealing.Microstructures and mechanical properties of these alloys were investigated by X-ray diffraction(XRD)analysis, scanning electron microscopy(SEM),electron probe X-ray microanalysis(EPMA),Vickers hardness measurement and compression test. The eutectic reaction L→Nb ss(Nb solid solution)+silicide(W5Si3-type,D8m)exists in B contents less than1at.%,while a new eutectic reaction L→Nb ss+␣silicide(Cr5B3-type,D8l)does in B contents higher than1at.%.The␣silicide is also found in0.44at.%(500wt.ppm) and1at.%B-added alloys.silicide completely transforms into␣silicide after annealing treatment at1700◦C for48h.The lattice parameter of␣silicide decreases with increasing boron content.Boron addition increases the hardness of silicide phase,but yield no appreciable change of hardness in Nb ss.Moreover,boron addition greatly improves the high-temperature strength.©2004Elsevier B.V.All rights reserved.Keywords:Silicide;Phase transformations;Mechanical properties;Casting1.IntroductionNiobium silicide(Nb5Si3)possesses attractive properties, such as high melting point[1],excellent high-temperature strength and creep resistance[2,3],required for advanced gas turbine engine uses.However,the intrinsic brittleness of Nb5Si3at ambient temperature inhibits its practical ap-plications.To overcome this critical issue,ductile Nb solid solution(Nb ss)in equilibrium with Nb5Si3up to very high temperatures has been incorporated into an Nb5Si3matrix in an in situ manner to produce composites based on the concept of ductile-phase toughening of brittle-compounds[4,5].Al-though the toughness of such multiphase alloys,so-called in situ composites,has been greatly improved,as compared to the Nb-silicide single-phase alloys[6],the high-temperature strength of Nb-silicide was decreased by the Nb ss incorpo-∗Corresponding author.Tel.:+81-22-215-2840;fax:+81-22-215-2841.E-mail address:clma2001@(C.L.Ma).ration.Moreover,the oxidation resistance of the compos-ites was degraded because of poor oxidation resistance of constituent Nb ss at elevated temperatures.Not only to in-crease high-temperature strength and low-temperature tough-ness but also to improve oxidation resistance,compositional and microstructural control is indispensable[7].Many efforts have been devoted to looking for alloying elements and opti-mizing their content so as to meet the demands.Alloying ele-ments such as Hf,Ti,Cr,Al and Ta have been investigated,for example[8].Recently,we have studied the high-temperature strength of Nb ss/Nb-silicide in situ composites alloyed with Mo and W[9–12].Of the various alloy compositions investi-gated,Nb–16Si–10Mo–15W was found to exhibit extremely high strength and excellent creep resistance at temperatures up to1500◦C[11].However,the fracture toughness and ox-idation resistance of this alloy were still insufficient for the requirements of practical applications.Boron has been re-ported to be effective in enhancing the oxidation resistance in the Mo–Si–B system at temperatures as high as1500◦C0921-5093/$–see front matter©2004Elsevier B.V.All rights reserved. doi:10.1016/j.msea.2004.06.058378 C.L.Ma et al./Materials Science and Engineering A 384(2004)377–384due to the formation of thin film of borosilicates on alloy surface,which inhibit oxygen atoms from penetrating into the metal [13].It is very interesting to know whether a sim-ilar effect appears in B-doped Nb ss /Nb-silicide in situ com-posites.Some research results have been reported recently that the Nb 5Si 3B 2exhibits a batter oxidation resistance than Nb 5Si 3at 1250◦C [14].Our preliminary study,unfortunately,showed only a small improvement of oxidation resistance in B-doped Nb ss /Nb-silicide in situ composites at 1500◦C.It was found,however,that the strength of silicide was sig-nificantly increased,while the ductility of Nb ss was not so degraded by B addition.This feature is very attractive for producing Nb ss /Nb-silicide in situ composites with a good balance of high-temperature strength and low-temperature toughness.The aim of the present paper is to demonstrate the effect of B addition on mechanical properties of Nb ss /Nb-silicide in situ composites.Solidification behavior,phase relationship and phase stability were also investigated for comprehensive understanding of the B effect.Based on the obtained results the potential of B as an alloying element to Nb ss /Nb-silicide in situ composites is discussed.2.Experimental procedureNb–16Si–10Mo–15W is used as the base composition,which is a hypoeutectic containing primary Nb ss particles and a eutectic structure silicide +Nb ss at a solidification condi-tion.The silicide transforms to a stable ␣silicide through annealing.The microstructural features and mechanical prop-erties of this alloy have been reported elsewhere [11].Various amounts of boron,from 0to 10at.%,were added to the base composition by substitution of Nb.The detailed alloy compositions are listed in Table 1.The high-purity el-emental powders Nb,Mo,W,Si and B were used as raw materials.Alloy ingots were prepared by arc melting on a water-cooled copper crucible under an ultra high-purity argon atmosphere.Each ingot was remelted three times to ensure compositional homogeneity.Heat treatment was conducted at 1700◦C for 48h,followed by furnace cooling to room temperature.Microstructures of cast and heat-treated sam-ples were characterized using SEM,XRD and EPMA.The hardness of constituent phases was measured using a Vickers hardness tester.The high-temperature strength was evaluated by compression tests using specimens with a di-mension of 3mm ×3mm ×pression tests wereTable 1Compositions and constituent phases identified by XRD Alloys CompositionsPhases in cast alloys Phases in annealed alloys HA Nb–16Si–10Mo–15W-Nb 5Si 3,Nb ss␣-Nb 5Si 3,Nb ss HA05Nb–16Si–10Mo–15W–0.44B -Nb 5Si 3,␣-Nb 5Si 3,Nb ss ␣-Nb 5Si 3,Nb ss HA1Nb–16Si–10Mo–15W–1B -Nb 5Si 3,␣-Nb 5Si 3,Nb ss ␣-Nb 5Si 3,Nb ss HA5Nb–16Si–10Mo–15W–5B ␣-Nb 5Si 3,Nb ss ␣-Nb 5Si 3,Nb ss HA10Nb–16Si–10Mo–15W–10B␣-Nb 5Si 3,Nb ss␣-Nb 5Si 3,NbssFig.1.X-ray diffraction patterns of as cast B-doped Nb/Nb-silicide alloys as a function of B content.carried out at an initial strain rate of 3×10−4s −1in an argon atmosphere using an Instron-type testing machine to a plastic strain of 16%.3.Results3.1.Microstructures3.1.1.Cast structuresXRD patterns of cast Nb–16Si–10Mo–15W alloys doped with various amounts of B are shown in Fig.1.The corre-sponding cast structures are illustrated in Fig.2.The diffrac-tion peaks on these XRD profiles were indexed based on the JCPDS databases and denoted with various marks to indicate the corresponding phases.The identified phases in each alloy are summarized in Table 1.It is evident from the table and these figures that the cast structure strongly depends on the B content.For the B-free alloy (HA),two phases of bcc Nb ss and W 5Si 3-type silicide ()are indexed on its XRD curve.The backscattered electron image (BEI),as shown in Fig.2(a),re-veals the two phases,which have bright and dark contrasts in BEI,distribute as dendritic primary particles and a two-phase mixture of a dark matrix and irregular lamellar bright parti-cles.The EPMA analysis revealed that the bright dendritic and irregular lamellar particles have an average composition of Nb–13.5Mo–31.4W–1.9Si and the dark matrix phase has an average composition of Nb–2.5Mo–1.2W–37Si,indicat-ing that the bright phase is Nb ss and the dark phase is silicide.Thus the lamellar structure is (Nb ss +).Note that a core behavior of W distribution in some large Nb ss particlesC.L.Ma et al./Materials Science and Engineering A 384(2004)377–384379Fig.2.Cast microstructures of Nb/Nb–Si alloys with various B additions:(a)0at.%B;(b)0.44at.%B;(c)1at.%B and (d)5at.%B.is observed,i.e.,the W content is slightly higher in the center area than that in the out area of Nb ss particles.For the low B content alloys (HA05and HA1),besides the Nb ss and silicide,a Cr 5B 3-type silicide (␣)was also detected on the XRD patterns.The cast structures,as can be seen in Fig.2(b)and (c),consists of large primary dendritic particles and a very fine interdendritic multiphase mixture.The primary dendritic particles are easily recognized to be Nb ss by their bright contrast.The silicide is also easily rec-ognized by its dark contrast.Some small bright Nb ss particles dispersed on phase and composed (+Nb ss )two-phase structure.Note that this (+Nb ss )two-phase structure is lo-cated at the interdendritic areas that finally solidified during solidification.Around the primary Nb ss particles are other two-phase mixtures consisting of small bright particles and gray paring the (+Nb ss )structure,the phase boundaries in these areas are not compositionally sharp,sug-gesting the atom distributions in the two phases are far from equilibrium state.The small particles are recognized to be Nb ss by their bright contrast while the gray phase is believed to be ␣silicide,as confirmed by the XRD analysis.The mix-ture around primary Nb ss particles is (␣+Nb ss ).For the high B content alloys (HA5and HA10),only ␣and Nb ss diffraction peaks are detected on the XRD patterns,while no silicide peak is seen.Fig.2(d)shows the cast structure of HA5,which contains bright dendritic particles and a two-phase mixture of small bright particle and a gray matrix.The large dendritic particles and small dendritic par-ticles on a gray matrix are easily recognized as Nb ss from the bright contrast,which was confirmed by EPMA analysis.Then the gray matrix was identified as ␣silicide based on the XRD analysis result.Note that,here,the ␣silicide solid-ifies directly from the molten alloys doped with boron.But in boron-free alloys,including Ni–Si binary and Nb–Mo–Si,Nb–W–Si and Nb–Ti–Si ternary as well as Nb–Mo–W–Si quaternary alloys,the ␣silicide is a low-temperature phase and forms through a solid–solid reaction.It is worthy to note that,here,no boride phase was identi-fied by XRD and EPMA analyses,though the boron addition is as high as 10at.%.Fig.3(a)and (b)show a BEI of HA10alloy and the corresponding B mapping image,positional mapping using EPMA reveals that B is pref-erentially solved in ␣-type silicide.Additionally,as can be seen in Fig.1,the diffraction peaks from Nb ss shift to the high angle side,implying a decrease in lattice parameter.This is consistent with our previous re-sults [11,12].Some cracks and pores are also observed in the cast microstructures of high B content alloys,which may be introduced by thermal stress during solidification and cooling.380 C.L.Ma et al./Materials Science and Engineering A 384(2004)377–384Fig.3.Mapping image of B distribution in cast HA10alloy:(a)BEI of selected area and (b)the corresponding mappingpattern.Fig.4.X-ray diffraction patterns of annealed B-doped Nb/Nb-silicide alloys as a function of B content.3.1.2.Annealed microstructuresX-ray diffraction patterns of alloys annealed at 1700◦C for 48h are shown in Fig.4.The dashed lines in thefigureFig.5.Typical annealed microstructures of alloys with B:(a)1at.%and (b)5at.%.represent the diffraction peak positions of binary ␣silicide (Nb 5Si 3).It is clear from these X-ray profiles that all the al-loys contain Nb ss phase and ␣silicide after annealing.No silicide peaks are found,indicating that this metastable phase completely transforms to stable ␣silicide.Since no discernible diffraction peak from another phase is observed,Nb ss phase and ␣silicide are equilibrium in these compo-sitions.The typical annealed microstructures of HA1and HA5alloys are shown in Fig.5(a)and (b).No apparent change is seen in the primary Nb ss phase,whereas the mi-crostructure of the multiphase matrix is slightly coarsened after the annealing treatment.The silicide volume fraction is estimated to be 47%for HA1alloy and 51%for HA5alloy.The EPMA analysis reveals a Nb ss in the B-free alloy having a composition of Nb–14.8Mo–25.3W–0.5Si and an ␣silicide of Nb–1.5Mo–0.8W–37.5Si.It clearly indicates that the solubility of Si in Nb ss as well as the Mo and W in ␣is very low.Similar results have also been reported for Nb–Mo–Si [15],Nb–W–Si [16].No core behavior is seen for annealedC.L.Ma et al./Materials Science and Engineering A384(2004)377–384381Table2Lattice parameters of␣-type silicide and Nb ss in annealed alloysAlloys Nb ss␣-Type silicidea a c a/c␣-Nb5Si3 6.569811.8870.5527 HA 3.2359 6.554811.8860.5514 HA5 3.2185 6.452211.7990.5495 HA10 3.2119 6.437111.7650.5471alloys,indicating a homogenous distribution of component elements in each phase.Some measurement errors easily occur when analyzing the light element B in constituent phases using the present EPMA method,which give rise to underestimates of B concentra-tion in␣silicide.The compositions of constituent phases in boron-doped alloys are not given here.But it is worthy to point out that the Mo and W solubility measured in B-doped ␣silicide is very low(<3at.%)though having some measure-ment error,which is comparable to that in B-free␣silicide. The distribution of B in two phases is qualitatively analyzed by measuring the compositional map using EPMA.The re-sult is similar to that obtained for cast alloys shown in Fig.3, revealing that B is preferentially solved in␣silicide.The lat-tice parameters of␣silicide and Nb ss are calculated by XRD analysis.The results are summarized in Table2,where data of binary␣Nb5Si3are also listed for comparison.It is ev-ident from the table that the lattice parameters of␣silicide and Nb ss decrease with increasing B content.3.2.Mechanical properties3.2.1.Vickers hardnessVickers hardness measurements were conducted on the constituent phases in annealed alloys containing various B concentrations.At least10points were measured for each case and the results are summarized in Table3.Though there is considerable scatter in the measured data due to the brit-tleness of silicide and relatively inhomogeneous microstruc-tures,it is evident from Table3that the hardness of Nb ss phase is not so sensitive to B content,while that of silicide phase is significantly increased by the boron additions.3.2.2.High-temperature strengthCompression tests were conducted on annealed alloys to examine the boron effect on the high-temperature strength. Three samples were tested for each alloy.The average yieldTable3Vickers hardness of constituent phases in annealed alloys as a function of B contentAlloys Nb ss␣-Type silicide HA6501050HA05(500ppm)6541158HA1(1at.%)6441159HA5(5at.%)6771372HA10(10at.%)675pressive strength of B-doped alloys at1500◦C as a function of Bcontent.parison of high-temperature strength of present alloys with some advanced Nb/Nb-silicide multi phase alloys.strengths are summarized in Fig.6.No significant differ-ence in compressive yield strengths at1500◦C is found at B contents less than5at.%,while the maximum yield strength of880MPa is obtained at5at.%B addition.Temperature dependence of yield strength was examined for5at.%B-doped alloy HA5.The results are shown in Fig.7,where data for some advanced binary,ternary and high order multi-component Nb-silicide in situ composites are also included for comparison.Note that the HA5alloy exhibits the highest strength at high temperatures.At1600◦C,the HA5alloy still maintains its high compressive stress of670MPa.4.Discussion4.1.Phase separation path4.1.1.B-free alloyThe cast structure of B-free(HA)alloy consists of Nb ss primary phase and a two-phase mixture of(Nb ss+),indi-cating that this alloy locates on an Nb ss-rich side of Nb ss+eutectic valley.The solidification sequence of this alloy can382 C.L.Ma et al./Materials Science and Engineering A 384(2004)377–384be described as follows:L →Nb ss +L 1thenL 1→silicide+Nb ssThe eutectic reaction is similar to that observer in Nb–Mo–Si and Nb–W–Si ternary systems.But it does not exist in Nb–Si binary [1]and Nb–Si–Ti ternary system,which were exten-sively studied recently [17].Using this simple eutectic reac-tion,one can control the microstructure of Nb ss /Nb-silicide in situ composites in a liquid–solid process,e.g.,a directional solidification process.4.1.2.B-added alloysBoron addition greatly changes the phase relationship and phase separation mechanism.The cast structures of HA5and HA10alloys consist of primary Nb ss phase and a two-phase mixture of (␣+Nb ss ),indicating that these alloys locate on an Nb ss -rich side of Nb ss +␣eutectic valley.The solidifi-cation sequence of these high boron-contained alloys can be described as follows:L →Nb ss +L 1thenL 1→␣silicide+Nb ssNote that the ␣silicide is a low-temperature phase in Nb–Si binary as well as Nb–Mo–Si,Nb–W–Si and Nb–Ti–Si ternary systems and forms through a solid–solid transforma-tion.In the present case,the ␣silicide solidifies directly from melt via a eutectic reaction,indicating the existence of a pri-mary ␣phase field in this Nb–Mo–W–Si–B system.In the composition region studied here,the Nb–Mo–W–Si–B system is reasonably thought as a pseudo-ternary system (Nb,Mo,W)–Si–B because the Nb forms a continuous solid solution with Mo and W.On the basis of the structural observation,a liquidus projection of (Nb,Mo,W)-rich zone in the pseudo-ternary (Nb,Mo,W)–Si–B system is proposed in Fig.8.As revealed in the cast structure of B-free (HA)alloy,there is a eutectic reaction e 1,L →+Nb ss ,on the (Nb,Mo,W)-SisideFig.8.Schematic representation of partial liquidus surface of (Nb,Mo,W)-rich zone in pseudo-ternary (Nb,Mo,W)–Si–B system.near the (Nb,Mo,W)point.The eutectic groove extends from the eutectic point into the (Nb,Mo,W)-rich zone interior and divides this region into two parts of and Nb ss primary phase fields.The fact of the coexistence of Nb ss ,␣and phases in low boron-content alloys (Fig.2(b)and (c))indicates that a ␣primary phase field must adjoin the Nb ss and regions,which generates a phase boundary bU between and ␣phase fields and eU between the Nb ss and ␣phase fields,as well as a transition reaction at triple point U.The eutectic structure of (␣+Nb ss )observed in HA5and HA10indicates the boundary line eU is eutectic.The nature of boundary line bU could not be determined by the present data.But we can know that the temperate falls from b to U,because the U is on the eutectic groove ee 1.As revealed in Fig.2(b)and (c),the eutectic structure of (+Nb ss )locates at the finally solidified interdendritic region in the low boron-content alloys.It indicates that the eutectic reaction L →+Nb ss occurs at a lower temperature than that of the eutectic reaction L →␣+Nb ss .In other words,the temperature falls from e to e 1.The temperature fallen directions of phase boundaries are denoted by arrows in the partial liquidus diagram.Though the nature of boundary line bU is unclear,the transition reaction at U can be determined to be peritectic by the temperature fallen direction of the phase boundaries,which intersect at triple point U.Based on the projection diagram,the solidification sequence occurred in low boron-content alloys can be described as follows:L →Nb ss +L 1followed byL 1→␣+Nb ss +L 2followed byL 2+␣→+Nb ss +L 3thenL 3→+Nb ssIt is note that the transition reaction is peritectic and would occur on the ␣surface when the liquid composition reaches the transition point.Since the arc-melted ingot is rapidly cooled on the water-cooled copper crucible,atom diffusion in a solid phase will be suppressed or retarded.It is the reason that no clear microstructural evidence of transition reaction is seen in the cast structure of low boron-content alloys.From the above discussion,it is clear that B concentration at the transition reaction point is lower than 0.44at.%because ␣silicide appears along with silicide and Nb ss in cast HA05alloy containing 0.44at.%B.In other words,the solubility of B in silicide will be less than 0.44at.%.4.2.Phase stability at 1700◦CThe present result reveals that the silicide completely transforms to ␣silicide after annealing treatment at 1700◦C for 48h.␣Silicide and Nb ss are equilibrium at this tempera-ture.As shown in Table 2,the lattice parameters of Nb ss and ␣silicide decrease with increasing boron content.C.L.Ma et al./Materials Science and Engineering A384(2004)377–384383In the present study,boron is added to the base alloy (Nb–16Si–10Mo–15W)by substituting for Nb.Moreover, the compositional mapping revealed that B preferentially solved in␣-type silicide.B-doped alloys have low Nb con-tent in Nb ss,compared to B-free alloy.It is known that the dissolution of Mo and W in Nb results in a decrease in lattice constant because the atomic radii of Mo and W are smaller than of Nb[12].Hence,the decrease of Nb ss lattice constant is mainly contributed by the dissolution of Mo and W in Nb.On the other hand,the solubility of Mo and W in␣silicide is very low,suggesting that the decrease in lattice constant of␣silicide is due to the boron addition.Boron atoms may occupy interstitial or substitutional positions in a␣lattice. The latter will result in decrease of lattice parameter.The fact that quite a large mount of boron dissolves in␣silicide and does not increase the lattice constant indicates that the boron atoms mainly occupy the substitutional bining the result of little Mo and W solved in this silicide,the␣silicide could be denoted as␣(Nb,Mo,W)5(Si,B)3.Perepezko et al.suggested that a T2phase(Nb5SiB2)ex-ists in Nb–Si–B ternary system,forming a continuous phase from Nb5SiB2to Mo5SiB2(Cr5B3-type)in Nb–Mo–Si–B quaternary system[18].However,the phase boundary has not been well defined in this system.Therefore,the phase relationship between␣-Nb5Si3and Nb5SiB2is still unclear at present.4.3.High-temperature strengthOne of the most interestingfindings in this study is that the high-temperature strength of Nb-silicide based alloys is remarkably increased by boron additions,as shown in Fig.7. The strengthening mechanism is not clearly understood at present,but there are some possible explanations for the strengthening.Thefirst is the solid solution hardening of␣silicide by B.As shown in Fig.3,B atoms are preferentially solved in␣silicide and locate predominantly at substitutional sites in␣lattice,which decrease the lattice parameters.The crystal lattice distortion caused by B dissolution in␣sili-cide may greatly increase the resistance to deformation.It is the reason for the increase of Vickers hardness of␣sili-cide at room temperature(see Table3).Moreover,diffusion-controlled high-temperature deformation of␣silicide may be suppressed by the B addition leading to the decrease in lattice constants.According to Subramanian et al.,creep de-formation in binary Nb5Si3is controlled by bulk diffusion of Nb in Nb5Si3[19].Although their deformation conditions are different from ours,it will be reasonable to assume that high-temperature deformation in this study is controlled by bulk diffusion of Nb.Both the geometrically decreased unit cell of Nb-silicide arising from the decrease in lattice pa-rameters due to B dissolution and the electrochemically in-creased binding force among the atoms in␣silicide due to the B being more electronegative than Si[20]will retard the bulk diffusion of Nb at high temperature,thereby increasing the high-temperature strength of␣silicide.Another impor-tant factor is concerned with the silicide volume fraction.Asmentioned above,the silicide phase in5at.%B-doped alloy(HA5)is about51vol.%,which is slightly higher than thatof B-free alloy,in which the silicide phase is about47vol.%.As expected by the rule of mixture for strength of compositematerial,the increase of silicide volume fraction will raisethe high-temperature strength of these composites.High-temperature strength of Nb ss/Nb-silicide in situcomposites has been found to increase remarkably by alloy-ing with Mo and W.However,the low-temperature toughnessof these materials was degraded by the alloying due to theductility loss of Nb ss.This work reveals that B alloying in-creases high-temperature strength of Nb ss/Nb-silicide in situcomposites through solid solution strengthening of␣-typesilicide(see Table3and Figs.6and7).In addition,B hasextremely low solubility in Nb ss,implying that ductility ofNb ss is not degraded by alloying with B.Although no evi-dence is presented in this study concerning fracture toughnessof B-doped alloys,B has a high potential to improve high-temperature strength and room temperature fracture tough-ness simultaneously.5.ConclusionsMicrostructures and mechanical properties of hypoeu-tectic Nb–16Si–10Mo–15W alloys doped with0–10at.%Bwere investigated.There exist two simple eutectic reactions:L→Nb ss+silicide(B content≤1at.%),and L→Nb ss+␣silicide(B content>1at.%).The␣silicide is also found in 0.44and1at.%B-doped alloys.No boride phase is identifiedeven in high boron-content alloys in both cast and annealedconditions.silicide completely transformed into␣silicideafter annealing at1700◦C for48h.The lattice parametersof␣silicide decrease with increasing boron additions.Nodistinct hardening of Nb solid solution is observed by boronadditions,but the hardness of silicide phase is increased.Thehigh-temperature yield stress is increased by boron additionto about880MPa at1500◦C and670MPa at1600◦C forNb–16Si–10Mo–15W–5B.References[1]T.B.Massalski,H.Okamoto,P.R.Subramanian,L.Kacprzak,BinaryAlloy Phase Diagrams,ASM,Metals Park,Ohio,1992.[2]R.M.Nekkanti,D.M.Dimiduk,High-temperature ordered intermetal-lic alloys IV,MRS Symp.Proc.194(1990)175.[3]P.R.Subramanian,M.G.Mendiratta,D.M.Dimiduk,JOM48(1996)33.[4]K.S.Chan,High-temperature ordered intermetallic alloys VI,MRSSymp.Proc.364(1995)469.[5]K.S.Chan,Metall.Trans.A27A(1996)2518.[6]M.G.Mendiratta,J.J.Lewandowski,D.M.Dimiduk,Metall.Trans.A22A(1991)1573.[7]S.Hanada,Reports of the123committee on heat-resisting metalsand alloys,JSPS38(1997)299.384 C.L.Ma et al./Materials Science and Engineering A384(2004)377–384[8]B.P.Bewlay,M.R.Jackson,H.A.Lipsitt,Metall.Trans.A27A(1996)3801.[9]C.L.Ma,Y.Tan,H.Tanaka,A.Kasama,R.Tanaka,Y.Mishima,S.Hanada,Reports of the123committee on heat-resisting metals and alloys,JSPS40(1999)335.[10]C.L.Ma,Y.Tan,H.Tanaka,A.Kasama,R.Tanaka,Y.Mishima,S.Hanada,Reports of the123committee on heat-resisting metals and alloys,JSPS40(1999)349.[11]C.L.Ma,Y.Tan,H.Tanaka,A.Kasama,R.Tanaka,Y.Mishima,S.Hanada,High-temperature ordered intermetallic alloys IX,MRS Symp.Proc.646(2000)N5–N39.[12]Y.Tan,H.Tanaka,C.L.Ma,A.Kasama,R.Tanaka,Y.Mishima,S.Hanada,J.Jpn.Inst.Metals64(2000)566.[13]C.T.Lu,Proceedings of the14th International Symposium on Ultra-High Temperature Materials,Japan,2000,p.157.[14]T.Murakami,C.N.Xu,A.Kitahara,M.Kawahara,Y.Takahashi,H.Inui,M.Yamaguchi,Intermetallics7(1999)1043.[15]C.L.Ma,Y.Tan,H.Tanaka,A.Kasama,R.Tanaka,Y.Mishima,S.Hanada,Mater.Trans.JIM41(2000)1329.[16]C.L.Ma,Y.Tan,A.Kasama,S.Hanada,Mater.Trans.JIM43(2002)668.[17]B.P.Bewlay,M.R.Jackson,H.A.Lipsitt,J.Phase Equilib.18(1997)264.[18]J.H.Perepezko,R.Rakidja,S.Kim,High-temperature ordered in-termetallic alloys IX,MRS Symp.Proc.646(2001)N4–N5. [19]P.R.Subramanian,T.A.Parthasarathy,M.G.Mendiratta, D.M.Dimiduk,Scripta Metall.Mater.32(1995)1227.[20]N.Tetuji,Physical Dictionary,Committee of Physical DictionaryEdition,Japan,1992,p.1380.。
Interfacial microstructure and mechanical properties of

Interfacial microstructure and mechanical properties of aluminium –zinc-coated steel joints made by a modifiedmetal inert gas welding –brazing processH.T.Zhang a,⁎,J.C.Feng a ,P.He a ,H.Hackl baState Key Laboratory of Advanced Welding Production Technology,Harbin Institute of Technology,Harbin 150001,Heilongjiang Province,PR ChinabFronius.Internation GMBH,A4600Wels-Thalheim,AustriaReceived 10May 2006;accepted 4July 2006AbstractThe microstructure and properties of aluminium –zinc coated steel lap joints made by a modified metal inert gas CMT welding –brazing process was investigated.It was found that the nature and the thickness of the high-hardness intermetallic compound layer which formed at the interface between the steel and the weld metal during the welding process varied with the heat inputs.From the results of tensile tests,the welding process is shown to be capable of providing sound aluminium –zinc coated steel joints.©2006Elsevier Inc.All rights reserved.Keywords:Welding –brazing;Heat input;Intermetallic compound1.IntroductionIn order to reduce pollution and save energy,it is attractive to make car bodies lighter by introducing some aluminium parts as substitutes for the previous steel structures [1,2].Therefore,joining aluminium to steel has become a major problem,requiring resolution.Direct solid-state joining can be used to make these dissimilar metal joints by controlling the thickness of the interme-tallic compound layer that develops within a few micrometers of the joint interface [3–9].However,the shape and size of such solid-state joints are extremely restricted.Thus,the joining of aluminium to steel byfusion welding methods has been widely studied.As is well known,the joining of aluminium to steel by fusion welding is difficult because of the formation of brittle interface phases which can deteriorate the mechanical properties of the joints.However,Kreimeyer and Sepold [10]have shown that if the layer is less than 10μm thick,the joint will be mechanically sound.In addition,the authors also deem that the existence of a zinc coating increases the wettability of the Al to the steel substrate.As another approach,Achar et al.[11]reported that the thickness of the intermetallic compound layer formed during TIG arc welding of Al to steel is decreased by the use of an Al alloy filler metal containing Si.Murakami et al.[12]and Mathieu et al.[13]both point out that the temperature probably determines the thickness of the intermetallic compound layer of the joint and recom-mended the use of lower heat input to obtain a sound joint.Materials Characterization 58(2007)588–592⁎Corresponding author.Tel.:+8645186412974;fax:+8645186418146.E-mail address:hitzht@ (H.T.Zhang).1044-5803/$-see front matter ©2006Elsevier Inc.All rights reserved.doi:10.1016/j.matchar.2006.07.008The cold metal transfer process,identified here as CMT,is a modified metal inert gas welding process which invented by the Fronius Company.The principal innovation of this method is that the motions of the welding wire have been integrated into the welding process and into the overall control of the process.Every time the short circuit occurs,the digital process-control both interrupts the power supply and controls the re-traction of the wire.The wire retraction motion assists droplet detachment during the short circuit,thus greatlydecreasing the heat input during welding.In this study,we selected the CMT process to join aluminium to zinc-coated steel using a lap geometry. The main purpose of this effort was to reveal the rela-tionship between heat input and the microstructure of the joint.Hardness testing was also used to characterize the phases formed during the welding process.In ad-dition,the quality of the joints was assessed by tensile testing.2.ExperimentalDeep drawn sheets of hot-dip galvanized steel and sheets of pure Al1060with thickness of1mm were used in the welding experiments.An Al sheet was lapped over a Zn-coated steel sheet on the special clamping fixture, and the ending of the weld wire was aimed at the edge of the aluminium sheet,as shown in Fig.1.The MIG welding–brazing was carried out using the CMTwelding source with an expert system and1.2-mm-diameter Al–Si filler metal wire.Argon was used as the shielding gas at a flow rate of15L/min.The surface of the samples was cleaned by acetone before welding.Two sets of welding parameters of different heat inputs were selected,as shown in Table1.The heat input,J,is calculated using the equation:J=(60×UI)/v,where U is the mean welding voltage,I is the mean welding current and v is the welding speed.Typical transverse sections of the samples were observed using optical microscopy(OM)and scanning electron microscopy(SEM).The composition of the intermetallic compound layer at the interface between the steel and the weld metal was determined by energy dispersive X-ray spectroscopy(EDX).Hardness values were obtained using a microindentation hardness tester with a load of10g,and a load time of10s.In addition, the samples were cut in10mm widths,and transverse tensile tests(perpendicular to the welding direction) were used to measure the joint tensilestrength.Fig.1.Schematic plan of the welding process.Table1The welding parametersSamplenumberMeanweldingcurrent(A)Meanweldingvoltage(V)Wire feedrate(m/min)Weldingspeed(mm/min)Weldheatinput(J/cm)Sample A6611.8 3.9762613.2Sample B11013.3 5.4913961.5Fig.2.Front(upper)and back(lower)appearances of typical jointswith different heat inputs:(a)Sample A;(b)Sample B.589H.T.Zhang et al./Materials Characterization58(2007)588–5923.Results and discussion 3.1.Macro-and microstructuresThe appearance of the weld seams for different heat inputs are shown in Fig.2.For all welding cases,a smooth weld seam was made.The molten metal wetted the steel better when using lower heat input,i.e.,compare Sample A at lower heat input to Sample B.This may be related to the different degree of evapo-ration of the zinc coating at different heat inputs.While improving the heat input,the greater evaporation of zinc reduces the wettability of the molten metal on the steel.Fig.3shows a typical cross-section of the joints.Higher heat input (Sample B)resulted in a decrease in the contact angle between the steel and the weld metal.Meanwhile,a special zone with lighter colour at the toe of the weldments can be found (designated by white arrows in Fig.3).Optical micrographs shows that a visible intermetallic compound layer has formed be-tween the steel and weld metal during the welding process,Fig.4.The thickness of the intermetallic com-pound layer changes not only with the location within a given joint but also with the varying heat input between different joints.The thickness of the intermetallic compound layer in the center is greater than at the edge of the seam within one joint.For Sample A,the maximum thickness of the compound layer is about 10μm but is 40–50μm for Sample B.The microstructure of the intermetallic compound is shown in greater detail in the SEM micrographs inFig.5.At lower heat input (Sample A),the inter-metallic compound presents a serrated shape oriented toward the weld metal.When the heat input was increased (Sample B),the compound layer became much thicker and grew into the weld metal with tongue-like penetrations.Anisotropic diffusion is a possible explanation for this irregularity.The intermetallic compounds that form under these conditions generally have an orthorhombic structure (see below).Because of the high vacancy concentration along the c -axis of the orthorhombic structure,Al atoms can diffuse rapidly in this direction and cause rapid growth of the inter-metallic compound.EDX analysis was used to determine the phases of the intermetallic compound layer.The results show that the intermetallic compound layer of the joint made by lower heat input consists entirely of Fe 2Al 5.But when the heat input is increased,the intermetallic compound layer consists of two different phases,the FeAl 2phase near the steel surface and a FeAl 3phase which penetrates toward the weld metal.Thus it is clearthatFig.4.Optical microstructures of interface between steel and weld metal:(a)Sample A;(b)SampleB.Fig.3.Cross-section image at limit of penetration in the joint,showing change in contact angle with increased heat input.Arrows point to an intermetallic compound at the tip of the weld metal:(a)Sample A;(b)Sample B.590H.T.Zhang et al./Materials Characterization 58(2007)588–592the intermetallic compound layer that forms is closely related to the heat input during the welding process.With regard to the special zone designated by white arrows in Fig.3,dendritic-appearing structures can be distinguished on a high-magnification SEM micrograph (Fig.6).EDX analysis results show that such dendrite-shaped crystals of an Al-richα-solid solution containing residual zinc routinely formed at this location.3.2.Hardness measurementsHardness testing results also confirm the presence of a hard intermetallic compound layer.The hardness of the interface layer is much higher than that of the base metal and the weld metal and is found to vary for the corresponding intermetallic compound phases.For the high heat input weld(Sample B)the hardness is much higher,Fig.7.Fig.8.The location where the fracture occurred during tensile testing (designated by white arrows):(a)Sample A;(b)SampleB.Fig.7.Microindentation hardness test results of the joints made using different heatinputs.Fig.6.Dendrite crystal structure at the toe of the weldment(SampleB).Fig.5.SEM micrograph of interface between steel and weld metal:(a)Sample A;(b)Sample B.591H.T.Zhang et al./Materials Characterization58(2007)588–5923.3.Tensile test resultsThe tensile tests were performed to provide a qualitative measure of the joint strength and behavior. These results show that the bond strength is excellent, with the fractures occurring in the HAZ of the Al even when the thickness of the intermetallic compound layer was greater than40μm,Fig.8.From a general view-point,the thickness of the intermetallic compound layer should be controlled to less than10μm in order to obtain a sound joint.This implies that the joint made with higher heat input should have a lower intrinsic strength than the other because of the thicker brittle intermetallic compound layer.However,the intrinsic strength of the joints cannot be determined when the fracture occurs in the HAZ of the pure Al.Nevertheless, according to the thickness of the compound layer,we can presume that the intrinsic strength of the joints should be decreased when increasing the welding heat input.4.ConclusionsBased on the experimental results and discussions, conclusions are drawn as follows1)Dissimilar metal joining of Al to zinc-coated steelsheet without cracking is possible by means of a modified metal inert gas(CMT)welding–brazing process in a lap joint.2)Fe–Al intermetallic compound phases were formedat the interface between the steel and the weld metal.The thickness and the composition of the interme-tallic compound layer varied with weld heat input.3)Despite the formation of the intermetallic compoundphases,the interface between steel and weld metal is not the weakest location of the joints.Tensile tests of the joints caused fractured in the Al HAZ,even when the intermetallic compound layer thickness exceeded 40μm.AcknowledgementsThe authors wish to acknowledge the financial support provided by the National Natural Science Foundation under Grant No.50325517for this work. References[1]Schubert E,Klassen M,Zerner I,Walz C,Sepold G.Light weightstructures produced by laser beam joining for future applications in automobile and aerospace industry.J Mater Process Technol 2001;115:2.[2]Schubert E,Zernet I,Sepold ser beam joining of materialcombinations for automotive applications.Proc SPIE 1997;3097:212.[3]Oikawa H,Ohmiya S,Yoshimura T.Resistance spot welding ofsteel and aluminium sheet using insert metal sheet.Sci Technol Weld Join1999;2:80.[4]Czechowski M.Stress corrosion cracking of explosion weldedsteel–aluminum joints.Mater Corros2004;6:464.[5]Fukumoto S,Tsubakino H.Friction welding process of5052aluminium alloy to304stainless steel.Mater Sci Technol 1999;9:1080.[6]Ochi H,Ogawa K,Suga Y,Iwamoto T,Yamamoto Y.Frictionwelding of aluminum alloy and steel using insert metals.Keikinzoku Yosetsu1994;11:1.[7]Shinoda T,Miyahara K,Ogawa M,Endo S.Friction welding ofaluminium and plain low carbon steel.Weld Int(UK) 2001;6:438.[8]Uzun H,Donne CD.Friction stir welding of dissimilar Al6013-T4to X5CrNi18-10stainless steel.Mater Des2005;1:41. [9]Adler L,Billy M,Quentin G.Evaluation of friction-weldedaluminum-steel bonds using dispersive guided modes of a layered substrate.J Appl Phys2001;12:6072.[10]Kreimeyer M,Sepold ser steel joined aluminium-hybridstructures.Proceedings of ICALEO'02,Jacksonville,USA;2002.[11]Achar DRG,Ruge J,Sundaresan S.Joining aluminum to steel,with particular reference to welding(III).Aluminum1980;4:291.[12]Murakami T,Nakata K.Dissimilar metal joining of aluminum tosteel by MIG arc brazing using flux cored wire.ISIJ Int 2003;10:1596.[13]Mathieu A,Mattei S,Deschamps A.Temperature control in laserbrazing of a steel/aluminium assembly using thermographic measurements.NDT&E Int2006;39:272.592H.T.Zhang et al./Materials Characterization58(2007)588–592。
纳米铜抗菌聚酰胺纤维的结构与力学性能

纤维良好的抗菌性,但也会对纤维结构和性能产生
ΔH f
w × ΔH 0
× 100%
(1)
一定的影响 [7] 。
式中: △H f 为样品熔融焓,J / g;△H 0 为纤维 100%
易得等优点,已成为原纤维法常用的抗菌剂之一。
酰胺纤维△H 0 值取 190 J / g [4] 。
铜系抗菌剂因其良好的抗菌、抗病毒性和廉价
carbon content is lower. The antibacterial polyamide fiber has higher melting point, crystallization
temperature and crystallinity, smaller crystal size, larger crystal surface spacing, higher tensile strength
通聚酰胺纤维进行了表征,并探究了纤维结构与纤维机械拉伸性能间的关系。 结果表明:负载纳米铜不影响聚酰
胺纤维化学结构;聚酰胺纤维中少量小分子物质可在纳米铜作用下加速分解;与普通聚酰胺纤维相比,纳米铜抗菌
聚酰胺纤维主要分解起始温度较高,残炭含量较少,熔点、结晶温度和结晶度较高,晶粒尺寸较小,晶面间距较大,
为衍射角,( °) 。
图 1 为普通聚酰胺纤维与纳米铜抗菌聚酰胺纤
峰, 2 938 cm -1 为 CH2 伸 缩 振 动 峰, 2 907 cm -1 和
1 637 cm -1 为 C—N—H 中 N—H 弯 曲 振 动 峰,
20 mm,拉伸速率 20 mm / min。 每种纤维测试 50 个
1 537 cm -1 和 1 267 cm -1 为 C O 平 面 振 动 峰 和