钨钢为什么这么难割
精密钨钢制品的线割方法

精密钨钢制品的线割方法
本文整理:红铭钨钢
在工业时代的来临,现在的模具加工设备越来越先进,人工越来越贵的情况下,很多产品已经是尽量用设备来弥补技术的不足,比如现在的钨钢产品,多数精密一点点的都会采用慢走丝加工。
在加工的时候,我们还是要掌握一定的技巧,这样才能事半功倍,发挥设备的最大价值。
一、钨钢线割的掉料方式
线割钨钢与普通钢材最大的不同在于,钨钢的密度为14-15,而普通钢材的密度为7-8,钨钢的比重太大,如果按照普通的方式线割,会造成钨钢接刀位置拉伤,所以,一般需要在最后掉料的位置预留一个凸台,避免拉伤使用部分。
二、不同形状钨钢内孔的割法
1.圆形钨钢产品线切割,光洁度要求高,且精度要求高的情况下,一般采用割一修三,或是无削加工的方式,这样加
工出来的钨钢产品,就不会看到线痕,光洁度会更加高。
2.一些异形钨钢产品内孔加工,起刀尽量在转角处起刀,这样在不做无削加工的情况下比较容易隐藏线头,其实线头
还是存在,只是肉眼无法辨别,这样让客户觉得产品的光
洁度比普通的高些。
三、异形钨钢产品的外形切割方法
异形钨钢外形线割,起刀留在平面的位置,且留凸起线头,在修刀完毕之后,可进行磨床加工,将线头磨掉,既可保证精度,又可保证产品的光洁度。
钨及其合金的切削加工
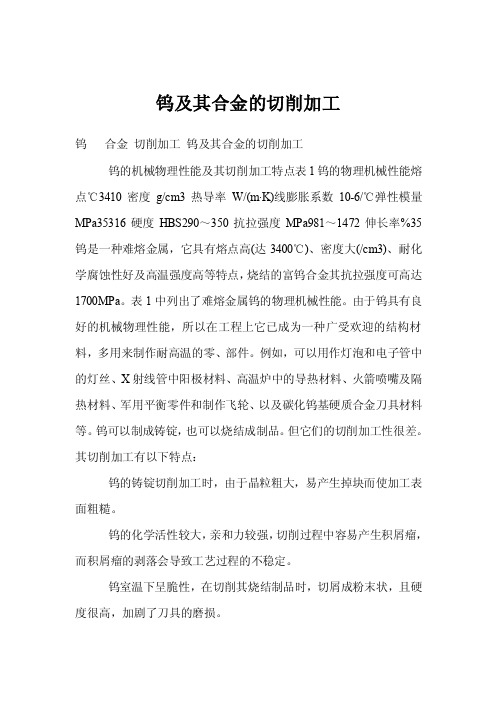
钨及其合金的切削加工钨合金切削加工钨及其合金的切削加工钨的机械物理性能及其切削加工特点表1钨的物理机械性能熔点℃3410密度g/cm3热导率W/(m·K)线膨胀系数10-6/℃弹性模量MPa35316硬度HBS290~350抗拉强度MPa981~1472伸长率%35钨是一种难熔金属,它具有熔点高(达3400℃)、密度大(/cm3)、耐化学腐蚀性好及高温强度高等特点,烧结的富钨合金其抗拉强度可高达1700MPa。
表1中列出了难熔金属钨的物理机械性能。
由于钨具有良好的机械物理性能,所以在工程上它已成为一种广受欢迎的结构材料,多用来制作耐高温的零、部件。
例如,可以用作灯泡和电子管中的灯丝、X射线管中阳极材料、高温炉中的导热材料、火箭喷嘴及隔热材料、军用平衡零件和制作飞轮、以及碳化钨基硬质合金刀具材料等。
钨可以制成铸锭,也可以烧结成制品。
但它们的切削加工性很差。
其切削加工有以下特点:钨的铸锭切削加工时,由于晶粒粗大,易产生掉块而使加工表面粗糙。
钨的化学活性较大,亲和力较强,切削过程中容易产生积屑瘤,而积屑瘤的剥落会导致工艺过程的不稳定。
钨室温下呈脆性,在切削其烧结制品时,切屑成粉末状,且硬度很高,加剧了刀具的磨损。
2钨棒及钨锭的切削加工钨具有高的抗拉强度,而钨的铸锭氧化层坚强又粗糙,使切削过程的冲击和振动增大,刀具容易崩刃、破损。
所以生产上须用强度和韧性较好的WC基(K类或M类)硬质合金刀具来加工。
粗加工可选用YG8(相当于K20)、YG8R(K30)、YG640(K30~K40)等牌号,半精加工用YG6(K10)。
由于硬质合金晶粒细化后,可提高合金的硬度、耐磨性、抗弯强度和抗崩刃性,而且高温硬度也有提高。
因此,用细晶粒(尺寸为1~μm)和超细晶粒(<μm)的硬质合金,如以Z30(相当于K30)、ZK30UF(K30)代替YG8,以YG6(K10)、YS8(K05~K10)、YG643(K05~K10,M10)、ZK10UF(K10)等牌号代替YG6,能够显著提高刀具的使用寿命。
难加工金属材料的切削加工性

难加工金属材料的切削加工性随着科学技术的发展,对机械电子、航空航天、兵器产品和化工设备及其零部件的性能有着各种新的要求。
有的需在高温、高应力状态下工作,有的要能耐腐蚀、耐磨损,有的要能绝缘,有的需有高的电导率。
故现代新型工程材料不断涌现。
不仅使用一般的碳素构造钢,而且使用了高强度、超高强度合金构造钢、高锰钢和不锈钢;不仅使用一般的灰铸铁、球墨铸铁和可锻铸铁,而且使用了合金耐磨铸铁和冷硬铸铁;不仅使用黑色金属,而且使用了钛合金、铜合金、铝合金及其他有色金属;不仅使用一般的铁碳合金,而且使用了多元合金如高温合金等;不仅使用以珠光体、铁素体为主的普通钢材,而且使用了以索氏体、托氏体为主的中硬调质钢和马氏体淬硬钢。
此外,还大量使用各种非金属材料和粉末冶金材料等。
在以上新工程材料中,有不少是属于难切削的,即所谓“难加工材料”。
难加工的原因一般是以下几个方面:①高硬度;②高强度;③高塑性和高韧性;④低塑性和高脆性;⑤低导热性;⑥有大量微观硬质点或硬夹杂物;⑦化学性质活泼。
这些特性一般都能使切削过程中的切削力加大,切削温度升高,刀具磨损加剧,刀具使用寿命缩短;有时还将使已加工表面质量恶化,切屑难以控制;终则使加工效率和加工质量降低,加工成本提高。
一、高强度、超高强度钢的切削加工性与普通碳素构造钢相比,高强度钢、超高强度钢的强度高(都比45钢高出l倍或l倍以上),导热系数偏低,故切削力大(为加工4.5钢的1.2—1.3倍),切削温度高(比加工45钢高出100—200℃),刀具磨损快,刀具使用寿命短,断屑亦稍难。
根据以上特点,必须采用耐磨性强的刀具材料。
按粗加工、半精加工、精加工的要求,应分别采用不同牌号的YT 类硬质合金,添加钽、铌的牌号。
高速精加工时,应采用高TiC含量并添加钽铌的YT类合金、TiC基和Ti(C,N)基硬质合金、涂层硬质合金和复合A1203陶瓷等。
刀具前角应较小,例如车削38CrNi3MoVA时,取γ。
难熔金属和纯金属的削切

难熔金属和纯金属的切削加工(上):株洲佳邦难熔金属有限公司http//:发布时间2011-06-151.常用难熔金属的力学物理性能有哪些?工业上常用的高熔点金属统称难熔金属,如钨、钼、钽、铌、锆等。
难熔金属熔点高、密度大,晶体结构稳定,激活能大,切削加工困难。
以难熔金属为主,添加其他合金元素构成难熔金属材料。
随着科学技术的发展,难熔金属在原子能、宇航、机械、电子、化工、医疗、纺织、轻工等领域得到了越来越广泛的应用。
常用难熔金属中钨的熔点最高(3380℃),密度最大(19.1g/cm³),而钼的弹性模量最大,达到343350MPa。
常用难熔金属的力学物理性能见表10-1。
难熔金属2.常用难熔金属的分类和用途有哪些?常用难熔金属中钨的熔点高,密度大,耐蚀性好,在冶金、电子、化工、核工业中常用来制作耐高温零部件,如电极、高温反应堆包套材料、平衡器件、医用X光管钨靶等。
钨可以制成铸锭,也可以制成烧结制品。
钨铸锭扒皮后可轧制成棒材或型材,也可以冷拔成丝;钨的烧结制品常做成高密度合金。
钼的熔点也很高(2695℃),密度适中,弹性模量极高,热膨胀系数小,导电、导热性好。
钼的结合性好,常用于喷涂钢件表面,以减小磨损,提高使用寿命。
钼还可以作为真空喷涂电极、真空蒸发金属、真空炉屏蔽板、发热体及高温构件;钼适于制作要求刚性、硬度高的部件,如镗刀杆、研磨轴等。
钼的耐蚀性好,常用来制作在熔融锌或锌蒸气中工作的泵、叶轮轴等。
钼及其合金有以下五种:①钼含量大于99.9%的纯钼材料。
②钼与钛的合金,如Mo—0.5Ti。
③TZM(Mo—0.6Ti—0.08Zr)合金。
④TZC(Mo—0.5Ti—0.03Zr—0.15C)合金。
⑤Mo—30W合金。
钽的熔点为2980℃,在常用难熔金属中仅次于钨(3380℃),密度为16.67g/cm³。
退火状态下,钽具有良好的塑性,高温下也比较稳定,能吸收并保持住气体。
钽耐酸,是生物适合性材料。
钨钢研磨方法

钨钢研磨方法一、前言钨钢是一种高硬度、高密度的金属材料,常用于制造刀具、模具等高强度工具。
由于其硬度极高,因此加工难度也相对较大。
研磨是钨钢加工中常用的一种方法,本文将介绍钨钢研磨的详细方法。
二、准备工作1.准备好研磨机和砂轮选择合适的砂轮对于钨钢的研磨至关重要。
通常情况下,选择颗粒较细的氧化铝砂轮或碳化硅砂轮较为适合。
同时,需要确保所选用的砂轮与所要加工的钨钢材料相匹配。
2.清洁表面在进行任何加工操作之前,需要先将待加工物表面进行清洁处理。
使用清洁剂或酒精擦拭表面可以去除灰尘和油污等杂质,从而提高后续操作的效果。
3.固定待加工物在进行加工操作时,需要将待加工物固定在台座上以防止其移动或旋转。
可以使用夹具或吸盘等固定工具进行固定。
三、研磨操作1.选择合适的转速在进行研磨操作时,需要根据所选用的砂轮和待加工物的硬度等因素选择合适的转速。
通常情况下,较硬的钨钢材料需要使用较高的转速。
2.调整砂轮位置在进行研磨操作之前,需要先将砂轮位置进行调整。
通常情况下,需要将砂轮对准待加工物表面并调整至合适位置。
在调整过程中,可以使用手动或自动调节机构来实现精确控制。
3.开始加工在进行加工操作时,需要将待加工物与旋转的砂轮接触,并以适当的压力推动待加工物沿着所需形状进行移动。
同时,在移动过程中需要保持一定的速度和方向以保证加工效果。
4.及时清理碎屑在进行加工操作时,会产生大量碎屑和金属粉末等杂质。
这些杂质会影响后续操作的效果,并且可能会对设备造成损坏。
因此,在加工过程中需要及时清理碎屑,并保持设备干净整洁。
5.检查加工效果在进行研磨操作之后,需要对加工效果进行检查。
可以使用显微镜等工具来观察表面的光洁度和平整度等指标。
如果发现问题,需要及时调整设备或更换砂轮等操作。
四、注意事项1.安全第一在进行任何加工操作之前,需要确保设备和操作环境的安全。
同时,在进行加工操作时需要佩戴防护眼镜、手套等个人防护装备以保障人身安全。
炼钢中的钨钢焊接技术

炼钢中的钨钢焊接技术随着现代工业技术的不断更新换代,高强度和高耐磨性的钢材需求不断增加,这种向强度、硬度和对磨损的抵抗力需求更高的钢材被称为钨钢。
然而,钨钢焊接技术的难度也随之增加。
本文将着重讨论炼钢中钨钢焊接技术及相关问题。
一、钨钢特点钨钢具有以下特点:1.高强度:钨钢比普通钢的强度要高。
2.高硬度:钨钢的硬度非常高,arg为HRC60以上。
3.高耐磨性:由于钨钢硬度高,因此它们具有更高的磨损抗性。
4.焊接困难:这是钨钢最大的问题之一。
二、钨钢的焊接问题钨钢具有一些困难的焊接问题,如下所述:1.氢脆性问题:钨钢容易在焊接环境中吸收氢气,从而导致焊缝脆性过高,影响焊接质量。
2.转换问题:钨钢的转换温度非常高,因此在这个温度之下,焊接需要采用特殊的焊接方法。
3.锁死问题:由于钨钢的硬度非常高,因此很难在焊接过程中进行位置调整,容易造成下料不准或锁死等问题,进而影响焊接质量。
三、炼钢中的钨钢焊接技术炼钢中的钨钢焊接技术需要牢记以下关键点:1.选择合适的焊接线:钨钢的连续焊接技术相对简单,但需要选择合适的焊接线和正确的电弧电流和内部水冷却系统。
2.采用正确的焊接方法:在钨钢焊接中,需要使用单面或双面焊接方法来确保焊接质量。
单面焊接用于板材和薄钢板,而双面焊接用于高厚度的钢板。
焊接时应注意把焊缝弄直,同时避免焊接面积太大。
3.博弈氢脆性问题:钨钢容易造成氢脆性问题,焊接时需要注意减少空气和污染物的接触。
使用特殊的焊接材料,并确保焊缝周围的温度保持一定的范围。
4.限制热影响区域:钨钢的结构比较紧密,最大的困难是在焊接时限制热影响区域。
使用水冷焊枪,焊接时枪管的冷却系统所形成的水幕,可以有效地限制热影响区域。
四、总结钨钢在现代工业中有着重要的应用,但是由于其高硬度、高强度和高耐磨性等特点,钨钢焊接技术也随之增加了难度。
因此,在炼钢中的钨钢焊接技术应用中,要特别注意钨钢的氢脆性问题,正确选择焊接线和焊接方法,同时要限制热影响区域以保证焊接质量。
1 切削过程中的难点及原因分析

1 切削过程中的难点及原因分析在零件试生产时,我们按车削普通碳钢的工艺方法对3Cr13不锈钢进行了车削试验,结果是刀具磨损非常严重,生产率极低,零件表面质量达不到要求。
比较3Cr13钢与40钢、45钢等碳素结构钢的机械性能可知,3Cr13钢的强度比40钢和45钢高,它是一种强度高、塑性好的中碳马氏体不锈钢。
由于切削时加工硬化严重,切削抗力大,切削温度高,导致刀具磨损严重,磨刀次数增多,增加了停机时间和机床调整时间,降低了生产率。
同时又容易粘刀,产生积屑瘤,引起工件尺寸的变化并影响表面粗糙度,而且切屑不易卷曲和折断,易损伤工件已加工表面,影响零件质量。
所以,不能用切削45钢的工艺来切削3Cr13,也不能把通用车床上的加工方法照搬到自动车床上来。
因为一般自动车床装刀较少,要求最好一次走刀就能使被加工表面达到要求的尺寸和表面粗糙度,以保证较高的生产率。
2 主要技术措施1.通过热处理,改变材料的硬度马氏体不锈钢在热处理后的不同硬度,对车削加工的影响很大。
表1是用YW2材料的车刀对热处理后不同硬度的3Cr13钢的车削情况。
可见,退火状0.10.10.1态的马氏体不锈钢虽然硬度低,但车削性能差,这是因为材料塑性和韧性大,组织不均匀,粘附,熔着性强,切削过程易产生刀瘤,不易获得较好的表面质量。
而调质处理后硬度在HRC30以下的3Cr13材料,车削加工性较好,易达到较好的表面质量。
用硬度在HRC30以上的材料加工出的零件,表面质量虽然较好,但刀具易磨损。
所以,在条件允许的情况下,可以在材料进厂后,先进行调质处理,硬度达到HRC25~HRC30,然后再进加工。
2.刀具材料的选择在自动车床上车削不锈钢,一般使用的硬质合金的刀具材料有:YG6、YG8、YT15、YT30、YW1、YW2等材料。
常用的高速钢刀具有:W18Cr4V、W6M05Cr4V2AL等材料。
我们在切削参数相同的条件下,对几种材料的刀具进行了车削对比试验,从表2可见:采用TiC-TiCN-TiN复合涂层刀片的外圆车刀,耐用度比较高,切削速度可取高,工件表面质量好,生产率高。
钨钢材料的性能特点

钨钢材料的性能特点钨钢是一种高强度、高硬度、高耐磨性的合金材料。
它由铁、钨、碳等成分组成,具有很好的耐磨性和高强度。
钨钢广泛应用于金属切削加工、模具制造、钣金成形等领域,在这些领域中扮演着重要的角色。
那么,钨钢材料的哪些性能使其成为理想的工业材料呢?以下是一些钨钢材料的性能特点。
1. 高硬度钨钢的硬度非常高,通常区间在63至67 HRC之间,这意味着它可以很容易地加工和磨削其他金属。
与其它钢材相比,它的硬度更高一些,所以在大多数需要高硬度的应用上它是首选的材料。
例如,在切削加工和制造模具和模板等方面,都会用到高硬度的钨钢材料。
2. 良好的耐磨性由于钨钢的高硬度,它在磨损和腐蚀等方面的性能非常出色。
在切割粘着材料时,它的耐磨性能非常突出。
其表面也可以通过抛光、磨削和磨齿等方法来增加耐磨性。
这种出色的耐磨性是钨钢材料被广泛应用于模具、钣金成形和汽车零部件等领域的主要原因之一。
3. 柔韧性高钨钢不仅具有高硬度和耐磨性,同时也具有非常好的柔韧性。
这种柔韧性表现为其具有很好的抗拉强度和可靠的断裂韧性。
这种组合使钨钢非常适合用于制造高质量的模具和模板等工具,以及需要高强度和高硬度但又不能牺牲柔韧性的应用。
4. 抗腐蚀能力强钨钢材料不仅具有很好的硬度和耐磨性,还非常抗腐蚀。
这是因为钨钢中的钨含量很高,钨具有很好的耐腐蚀性能。
此外,钨也具有非常高的密度,所以钨钢材料在高温和强腐蚀环境下非常耐用。
因此,钨钢不仅仅适用于低温环境和干燥环境下的应用,而且还在高温和潮湿环境下具有很好的性能。
5. 良好的导热性钨钢具有非常好的导热性,这使得它非常适合用于各种切削加工和金属加工应用场合。
导热性能也是决定切削加工质量和精度的因素之一。
综上所述,钨钢材料具有的高硬度、良好的耐磨性、柔韧性、抗腐蚀能力和良好的导热性,使其适用于各种加工、制造等领域。
只需要根据应用的不同要求选择不同的钨钢材料,就可以得到最佳的性能和效益。
- 1、下载文档前请自行甄别文档内容的完整性,平台不提供额外的编辑、内容补充、找答案等附加服务。
- 2、"仅部分预览"的文档,不可在线预览部分如存在完整性等问题,可反馈申请退款(可完整预览的文档不适用该条件!)。
- 3、如文档侵犯您的权益,请联系客服反馈,我们会尽快为您处理(人工客服工作时间:9:00-18:30)。
钨钢为什么这么难割?面对着网友的“钨钢”加工难题,有喜有忧,喜的是我们的同行能在中走丝上将“钨钢”的修刀切割水平推至到100MM厚度的切割,这也是值得庆贺的。
经常会在快走丝,中走丝,慢走丝加工中遇上钨钢线切割加工,钨钢的加工质量和加工速度水平是衡量机器性能好坏的一个重要指标,下面就钨钢难割在那里,钨钢的“线割德性”展开讨论,认识钨钢的“真面目”进而对我们的线割加工有所帮助。
钨钢只是我们五金行业的通俗叫法,学名另有称呼“硬质合金”。
在化学金属元素周期表中单独找不到硬质合金,它是我们人类用一些难熔金属的碳化物粉末<如WC,TiC>等类型的的物质加在粘结剂Co中混合,经物理加压成型,在真空烧结而成为我们所说的钨钢。
我们线切割中经常会用到,象上下线架上的电源导电快,车床上使用的刀片,五金高速连续模中的下模刀口镶件,冲子,材料拉伸模的成型口,这些是我们在工作上经常遇到的。
经常接触到的钨钢。
常见硬质合金标号有二大类:YGYT,在钨钢中高硬的成份是WC,用金属CO为粘结剂,还有一种是用TiC为主体,也是用Co为粘结剂,以上两种硬质合金物理性能根据使用侧重点不同,在性能上略有区分,还有一种在冶金行业称为“万能硬质合金”的,在他的组成成份中加入了一种“碳化钽”。
性能处于YGYT之间。
顾名思义:硬质合金硬字当头,对于用他做加工刀具是求之不得,而想加工硬质合金本身采用传统的机械切削方法是很困难的,但对于用电火花线切割来加工却是“较容易”的。
但是,在硬质合金的电加工可行性的条件下,在介绍硬质合金的组成成份上因线切割加工环境特殊性,随之会带来一些钨钢工件切割表面改变的不利影响,加工中钨钢的切割性能有别于一般各种五金塑胶模用钢的切割性能。
从衡量线割材料的物理性能指标:钨钢熔点,气化点,材质的热导率三个方面都比较高,不管是在快走丝,中走丝的乳化液中切割,还是在慢走丝的纯水中线割,对于钨钢的加工性能是,总体比较稳定,表面粗糙度值同比较小,而最不满意的是切割速度低,效率不高,丝损较大,“软质层”产生。
在对钨钢的切割中,象慢走丝因存在“电解”作用,会将钨钢中的粘合剂Co析出,在加工中,水对钨钢切割表面的电解作用,使钨钢中的结合剂Co成为Co离子状态溶解在水中,造成钨钢表面由“硬”变“软”。
笔者也在中走丝的钨钢切割中对比使用乳化液,和纯水溶性的线切割液进行钨钢的切割对比试验,以在为某电子厂五金连续模下模刀口的二种切割对比如下:乳化液加工一次钨钢镶件,用56倍光学放大镜观察,表面也有我们通常所说的疏松层和显微裂纹,需在镶件装配前用油石研模切割表面。
用水溶性纯水溶性对钨钢加工,同样,下模镶件的“割一修二”切割的表面。
在56倍的光学放大镜观察,表面粗糙度较用乳化液加工值要小0.5倍,但表面疏松层较用乳化液线割的“软质层”增大。
同样在用“庆鸿”慢走丝加工钨钢下模镶件“割一修二”有无电解电源,在56倍光学放大镜下观察,“软化层”几乎消失。
表面粗糙度值在Ra<0.6微米。
经过在快,中,慢三种机上采用乳化液,纯水溶性水质线割液,以及水质工作液的加工比较,不论是在中走丝中采用“纯水溶性线切割液,还是慢走丝中的水质工作液对钨钢加工,都会出现”工件表面的“软化层”现象。
而用乳化液和浙江“佳润”牌水基复合工作液钨钢表面的“软质层”相对较轻,特别是“佳润”牌水基复合工作液的实际钨钢切割效果更好一些<从客户使用实际冲压刀口次数比较>.我们知道在快走丝中加工表面有一变质层,从几微米到十几微米。
而特别是在水质工作液中<中走丝,慢走丝>严重影响模具质量的变质层基本是因在钨钢的“水质放电环境”中由“电解的对象Co的流失造成的。
下面就介绍一下“水质放电环境“中钨钢切割表面是怎样由Co的流失而生成“软质层”的。
我们的慢走丝加工所用的“纯水”实际并不“纯洁”经过离子交换树脂的交换后,在慢走丝的放电区水质还是有一定的导电性,而中走丝的水溶性水基工作液的导电性比慢走丝的水质导电性要更强一些。
通过去离子的处理和中走丝水箱的“过滤”,降低水的电导率,但多少在加工液中还有一定数量的自由离子存在,而我们线割加工的“极性效应”,工件接正极,钼丝或铜线接负极,在电场的作用下,在正极工件的表面OH—离子不断聚集,造成金属象铁,铜,铝,锌以及钨钢中的钛,钨的氧化并拌金属腐蚀,对于象钨钢中的CO在电场电解的作用下成Co离子状态溶解在水质加工液中,形成钨钢加工前的硬身变成加工后因“软化层”的出现而表面“失硬”变“软”。
所以我们见到现在的慢走丝都在介绍性能时宣称有防钨钢“脱Co的防电解电源,防电解电源是不同于我们现在“无变”的高频电源,采用交变脉冲,施加放电电压平均值为“零”,使工作液中引起电离作用的OH-离子处于电极丝和工件之间受“振荡状态”,不趋向工件和电极丝运动,防止工件材料的氧化,并使钨钢中的粘结剂“Co”流失最小,钨钢表面“变质层”小到不能影响工件的冲压性能。
而目前在中走丝的加工中,用水溶性水质的线割,电解电源效应对钨钢“脱Co“的作用没有引起注意,也没见这方面的研究报道消息,传统电源形成的电解金属现象继续存在,因大部分钨钢精密零件的线割还都是用慢走丝加工的,加工质量对于快走丝,中走丝的“脱Co”原因改善没有尝试。
中走丝,快走丝什么时候能运用高频平均电压为零的交流脉冲电源放电切割,以及采用高电阻的水基少“离子状态”的线割液加工,防电解对钨钢的作用值得好好思考。
钨钢切割实际效率低是因为他的材质所决定的。
前面说过:钨钢这种材质的汽化点相比常见金属要高几倍,热传导率比其他常见金属要低,在比热容,熔化热,汽化热等三方面的热力学特性比常见金属值大,同样在我们的快,中,慢走丝切割中能量的热效率比要大。
从线割加工中一个放电过程的完成来分析:每次脉冲放电时,在钼丝或铜丝与工件形成的正负放电通道内及各个沿钼丝或铜线的园周形成的正负放电点都在瞬时获得由电火花放电传来的热能,这些热能的加工,在放电通道中有二种转变过程,一部分消耗在工作液中,和钼丝或铜线杂质周围。
其余能量都作用在放电“切割区”。
这中间包括钼丝铜线本身,被加工工件的加热升温,熔化,熔融状态,以及工件电极的气化抛出。
对相同的放电高频参数能量,前面我讲到的材质各种热力学特性象钨钢的熔点,汽化点,熔化热,汽化热愈高。
则每次线切割电蚀量就少,加工的速度也就在宏观上表现较慢。
也就是我们在实际钨钢切割中看到的从薄到厚,越发越难切割,难度就大,这一点从快,中,慢的线割收费比普通材质的加工费高1.5倍到二倍也看得出来。
在相对加工稳定的状态,以我的实际切割经验,不用传统的乳化油,而改用水基性质的切割液,从不计钼丝的损耗来看,还不错的选择方法。
大家都知道:放电工作介质的作用主要是起到放电通道绝缘和压缩,排屑和冷却,等。
及时消电离也是一个重要项目。
对于线切割钨钢,水基工作液的密度和“粘度”大,有利于压缩在钨钢切割中的放电通道,提高放电的能量密度。
而且水基线切割液的钼丝粘附度好于乳化液,放电通道均匀,无“干烧放电区”,放电通道干净,放电切割蚀物送出方便。
割钨钢尽管比用乳化液的“电解作用”强,C o的离子析出多,但有利用加工工件后期的研磨处理,为了保证一定的切割效率还是可取的,而且用中走丝的多次切割工艺,总体技术指标能达到客户的钨钢加工要求。
一般在快走丝的单次切割中,我们常用空载电压100伏左右。
脉宽40左右,脉间5-8倍,实际加工电流2A-4A。
这种参数的能量对钨钢一次加工还不够,太有限了。
选用更好的高频电源,以及在现有高频电源上组合新的参数是我们在切割钨钢中要面对问题。
如果你在钨钢的加工中观察:会看到放电火花暗红深色,“放电声音小”加工电流值小,那都是放电能量对于钨钢的热力学特性相比能量不足的表现。
选用优质的钼丝,在加工几何形状允许的范围内,用大线径的钼丝,<不能太大,大了电蚀量增大了,又更加要能量,更慢>,建议不要超出0.22MM钼丝。
割钨钢丝损大。
也象我的博友来问中介绍的钼丝割一下“受不了”“起球断丝”本来100MM的正常加工做得很顺,现在突然不行,附来贴供大家讨论。
在钼丝最大工作电流承受的范围内。
提高切割钨钢的能量是一个好的主意。
这里因每个地方机台的切割现场“条件”差异,只能给出一些“笼统条件”,在大的原则框框内,钨钢具体的加工具体对待。
我认为没有“万能条件”。
以下是你在你用的机台现有高频参数内可以为钨钢的加工准备条件“原则”。
用你现有高频脉冲电源输出加工电压高的幅值,至少比加工钢件要高。
检查高频电源脉冲的“形状”,输出波形“前沿要陡峭”。
波形有“塌状”要更换相应元器件。
有时新的电源可以,过段时间不行也有高频板损坏的原因。
脉冲前沿陡峭,作用在线割区的能量放电爆破力大。
钨钢放电材质击穿快。
选用较大的脉宽与缩小脉冲间隙,在此组合基础上提供较大的输出加工电流,增加在钨钢的单个切割能量,对钨钢的蚀除效应也就大。
还有前面已经提到的在线切割中“水”介质的应用,慢走丝的重要性与修刀粗糙度,精度,切割速度影响很大,而在快,中走丝的钨钢加工中,一定要重视,有时我们的线切割液使用一定工作时间后,放电切割性能已不能达到割钨钢的要求,也不及时正确更换,在更换中调配比例不正确,机床清洗不彻底。
换后效果差,加工过程中“浓度”如何,切割的人没标准,速效检测跟踪线切割液的“性质”都是靠人工“经验”确定。
所以在快走丝,中走丝随机要配控制线切割液质量的工具,或不同生产线切割工作液的厂家提供,保证你的类似钨钢难切割问题也许在寻找好的工艺方法上有保证。
以下是我的一位网友在中走丝切割中加工钨钢的介绍,问题答案还在分析之中,谢谢各位有见解的“出谋划策”。
还真太微观了曾老师:我碰到这样的难题,我的2台中走丝经常割100高的钨钢,在开始4-5个月里速度又快,丝损很小,但过了几个月好时光后问题就来了,一割钨钢,钼丝就全是结点,凸起的,无论怎样都于事无补,我擦干净机床,换掉工作液,换掉所有导轮,换掉进电块,所有外部条件都改进,依然割不了钨钢,换割其它材料又一切正常,所有这些过程中没改变过电参数,真是非常奇怪的现象,钼丝起疙瘩的原理我也知道:《钼丝上出现烧伤点发生断丝。
一旦钼丝上出现“疙瘩”状的烧伤点,极易发生断丝现象。
一般认为,这是粘附在电极丝上的加工屑(阳极物质)所为,该粘附物起到了使放电集中在电极丝上的作用,此时若冷却散热条件差,就很可能使该处的温度升高,这样一来在连续的放电中就可能继续有其他加工屑粘附在该点附近,如此造成一种恶性循环,最后导致该处发生烧伤现象。
至于为何加工屑会粘附到电极丝上的问题,其主要原因与脉冲参数和放电间隙的冷却状况有关。
解决的办法是,可提高脉冲电源的空载电压幅值,或采用双脉冲法门类似于通常所说的分组脉冲),这样可减少加工屑粘附到电极丝上的可能性;加大冷却液流量,改善冷却条件。