Design of a high-impact survivable robot
出国访问留学的研修计划一例
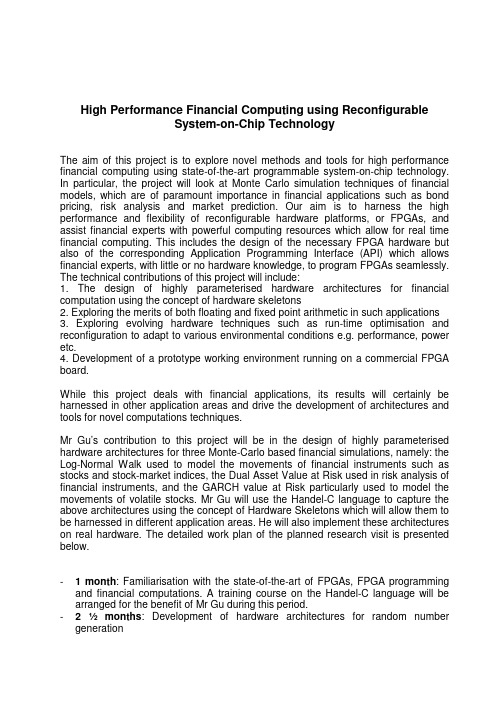
High Performance Financial Computing using ReconfigurableSystem-on-Chip TechnologyThe aim of this project is to explore novel methods and tools for high performance financial computing using state-of-the-art programmable system-on-chip technology. In particular, the project will look at Monte Carlo simulation techniques of financial models, which are of paramount importance in financial applications such as bond pricing, risk analysis and market prediction. Our aim is to harness the high performance and flexibility of reconfigurable hardware platforms, or FPGAs, and assist financial experts with powerful computing resources which allow for real time financial computing. This includes the design of the necessary FPGA hardware but also of the corresponding Application Programming Interface (API) which allows financial experts, with little or no hardware knowledge, to program FPGAs seamlessly. The technical contributions of this project will include:1. The design of highly parameterised hardware architectures for financial computation using the concept of hardware skeletons2. Exploring the merits of both floating and fixed point arithmetic in such applications3. Exploring evolving hardware techniques such as run-time optimisation and reconfiguration to adapt to various environmental conditions e.g. performance, power etc.4. Development of a prototype working environment running on a commercial FPGA board.While this project deals with financial applications, its results will certainly be harnessed in other application areas and drive the development of architectures and tools for novel computations techniques.Mr Gu’s contribution to this project will be in the design of highly parameterised hardware architectures for three Monte-Carlo based financial simulations, namely: the Log-Normal Walk used to model the movements of financial instruments such as stocks and stock-market indices, the Dual Asset Value at Risk used in risk analysis of financial instruments, and the GARCH value at Risk particularly used to model the movements of volatile stocks. Mr Gu will use the Handel-C language to capture the above architectures using the concept of Hardware Skeletons which will allow them to be harnessed in different application areas. He will also implement these architectures on real hardware. The detailed work plan of the planned research visit is presented below.- 1 month: Familiarisation with the state-of-the-art of FPGAs, FPGA programming and financial computations. A training course on the Handel-C language will be arranged for the benefit of Mr Gu during this period.- 2 ½ months: Development of hardware architectures for random number generation- 3 ½ months: Development of hardware architectures for Monte-Carlo simulations.These will be harnessed for three financial computations, namely: Log-Normal Walk, Dual Asset Value at Risk, and the GARCH Value at Risk.- 4 months: Implementation of the above architecture on a real hardware platform.This will include the design of Input/Output data transfer mechanisms as well as a high level data and results manager- 1 month: Final report write-upMr Gu will be supervised by Dr. Khaled Benkrid who is a Lecturer in the Institute of Micro and Nano Systems, School of Engineering and Electronics, at the University of Edinburgh.。
新技术人工智能英语作文

Artificial intelligence AI has been a topic of great interest and debate in recent years. As a rapidly evolving field, AI has the potential to revolutionize various aspects of our lives, from healthcare and education to transportation and entertainment. In this essay, I will discuss the impact of AI on society and the benefits and challenges it presents.Firstly, AI has the power to transform the way we work and live. With the ability to analyze large amounts of data and make decisions based on patterns and trends, AI can help improve efficiency and productivity in various industries. For example, AIpowered robots can perform repetitive and dangerous tasks, reducing the risk of accidents and injuries to human workers. Additionally, AI can assist in diagnosing diseases and developing personalized treatment plans, which can lead to better health outcomes for patients.However, the rise of AI also brings about certain challenges. One major concern is the potential loss of jobs due to automation. As AI systems become more advanced, they may replace human workers in certain roles, leading to unemployment and social unrest. To address this issue, it is crucial for governments and businesses to invest in education and training programs that help workers adapt to the changing job market and acquire new skills.Another challenge is the ethical implications of AI. As AI systems become more intelligent and autonomous, questions arise regarding their decisionmaking processes and potential biases. It is essential to ensure that AI systems are designed and programmed with fairness, transparency, and accountability in mind to prevent any harmful consequences.Moreover, the integration of AI into our daily lives raises privacy concerns. With AI systems collecting and analyzing vast amounts of personal data, there is a risk of misuse or unauthorized access to sensitive information. Therefore, it is vital to establish robust data protection measures and regulations to safeguard individual privacy.In conclusion, the development and application of AI hold immense potential for improving various aspects of our lives. However, it is crucial to address the challenges and ethical concerns associated with AI to ensure its responsible and beneficial use. By fostering collaboration between governments, businesses, and researchers, we can harness the power of AI to create a better future for all.。
IATA AHM目录
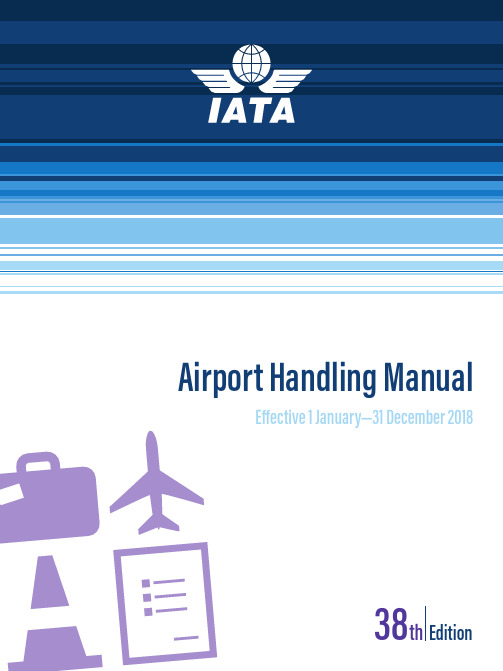
Airport Handling ManualEffective 1 January—31 December 201838NOTICEDISCLAIMER. The information contained in thispublication is subject to constant review in the lightof changing government requirements and regula-tions. No subscriber or other reader should act onthe basis of any such information without referringto applicable laws and regulations and/or withouttak ing appropriate professional advice. Althoughevery effort has been made to ensure accuracy, theInternational Air Transport Association shall not beheld responsible for any loss or damage caused byerrors, omissions, misprints or misinterpretation ofthe contents hereof. Furthermore, the InternationalAir Transport Association expressly disclaims anyand all liability to any person or entity, whether apurchaser of this publication or not, in respect ofanything done or omitted, and the consequencesof anything done or omitted, by any such person orentity in reliance on the contents of this publication.Opinions expressed in advertisements appearing inthis publication are the advertiser’s opinions and donot necessarily reflect those of IATA. The mentionof specific companies or products in advertisementdoes not imply that they are endorsed or recom-mended by IATA in preference to others of a simi-lar nature which are not mentioned or advertised.© International Air Transport Association. AllRights Reserved. No part of this publication maybe reproduced, recast, reformatted or trans-mitted in any form by any means, electronic ormechanical, including photocopying, record-ing or any information storage and retrieval sys-tem, without the prior written permission from:Senior Vice PresidentAirport, Passenger, Cargo and SecurityInternational Air Transport Association800 Place VictoriaP.O. Box 113Montreal, QuebecCANADA H4Z 1M1Airport Handling ManualMaterial No.: 9343-38ISBN 978-92-9229-505-9© 2017 International Air Transport Association. All rights reserved.TABLE OF CONTENTSPage Preface (xv)Introduction (xvii)General (1)AHM001Chapter0—Record of Revisions (1)AHM011Standard Classification and Numbering for Members Airport Handling Manuals (2)AHM012Office Function Designators for Airport Passenger and Baggage Handling (30)AHM020Guidelines for the Establishment of Airline Operators Committees (31)AHM021Guidelines for Establishing Aircraft Ground Times (34)AHM050Aircraft Emergency Procedures (35)AHM070E-Invoicing Standards (53)Chapter1—PASSENGER HANDLING (91)AHM100Chapter1—Record of Revisions (91)AHM110Involuntary Change of Carrier,Routing,Class or Type of Fare (92)AHM112Denied Boarding Compensation (98)AHM120Inadmissible Passengers and Deportees (99)AHM140Items Removed from a Passenger's Possession by Security Personnel (101)AHM141Hold Loading of Duty-Free Goods (102)AHM170Dangerous Goods in Passenger Baggage (103)AHM176Recommendations for the Handling of Passengers with Reduced Mobility(PRM) (105)AHM176A Acceptance and Carriage of Passengers with Reduced Mobility(PRM) (106)AHM180Carriage of Passengers with Communicable Diseases (114)AHM181General Guidelines for Passenger Agents in Case of SuspectedCommunicable Disease (115)Chapter2—BAGGAGE HANDLING (117)AHM200Chapter2—Record of Revisions (117)AHM210Local Baggage Committees (118)AHM211Airport Operating Rules (124)Airport Handling ManualPageChapter2—BAGGAGE HANDLING(continued)AHM212Interline Connecting Time Intervals—Passenger and Checked Baggage (126)AHM213Form of Interline Baggage Tags (128)AHM214Use of the10Digit Licence Plate (135)AHM215Found and Unclaimed Checked Baggage (136)AHM216On-Hand Baggage Summary Tag (138)AHM217Forwarding Mishandled Baggage (139)AHM218Dangerous Goods in Passengers'Baggage (141)AHM219Acceptance of Firearms and Other Weapons and Small Calibre Ammunition (142)AHM221Acceptance of Power Driven Wheelchairs or Other Battery Powered Mobility Aidsas Checked Baggage (143)AHM222Passenger/Baggage Reconciliation Procedures (144)AHM223Licence Plate Fallback Sortation Tags (151)AHM224Baggage Taken in Error (154)AHM225Baggage Irregularity Report (156)AHM226Tracing Unchecked Baggage and Handling Damage to Checked and UncheckedBaggage (159)AHM230Baggage Theft and Pilferage Prevention (161)AHM231Carriage of Carry-On Baggage (164)AHM232Handling of Security Removed Items (168)AHM240Baggage Codes for Identifying ULD Contents and/or Bulk-Loaded Baggage (169)Chapter3—CARGO/MAIL HANDLING (171)AHM300Chapter3—Record of Revisions (171)AHM310Preparation for Loading of Cargo (172)AHM311Securing of Load (174)AHM312Collection Sacks and Bags (177)AHM320Handling of Damaged Cargo (178)AHM321Handling of Pilfered Cargo (179)AHM322Handling Wet Cargo (180)AHM330Handling Perishable Cargo (182)AHM331Handling and Protection of Valuable Cargo (184)AHM332Handling and Stowage of Live Animals (188)AHM333Handling of Human Remains (190)Table of ContentsPageChapter3—CARGO/MAIL HANDLING(continued)AHM340Acceptance Standards for the Interchange of Transferred Unit Load Devices (191)AHM345Handling of Battery Operated Wheelchairs/Mobility AIDS as Checked Baggage (197)AHM350Mail Handling (199)AHM351Mail Documents (203)AHM353Handling of Found Mail (218)AHM354Handling of Damaged Mail (219)AHM355Mail Security (220)AHM356Mail Safety (221)AHM357Mail Irregularity Message (222)AHM360Company Mail (224)AHM380Aircraft Documents Stowage (225)AHM381Special Load—Notification to Captain(General) (226)AHM382Special Load—Notification to Captain(EDP Format and NOTOC Service) (231)AHM383Special Load—Notification to Captain(EDP NOTOC Summary) (243)AHM384NOTOC Message(NTM) (246)Chapter4—AIRCRAFT HANDLING AND LOADING (251)AHM400Chapter4—Record of Revisions (251)AHM411Provision and Carriage of Loading Accessories (252)AHM420Tagging of Unit Load Devices (253)AHM421Storage of Unit Load Devices (263)AHM422Control of Transferred Unit Load Devices (268)AHM423Unit Load Device Stock Check Message (273)AHM424Unit Load Device Control Message (275)AHM425Continued Airworthiness of Unit Load Devices (279)AHM426ULD Buildup and Breakdown (283)AHM427ULD Transportation (292)AHM430Operating of Aircraft Doors (295)AHM431Aircraft Ground Stability—Tipping (296)AHM440Potable Water Servicing (297)AHM441Aircraft Toilet Servicing (309)Airport Handling ManualPageChapter4—AIRCRAFT HANDLING AND LOADING(continued)AHM450Standardisation of Gravity Forces against which Load must be Restrained (310)AHM451Technical Malfunctions Limiting Load on Aircraft (311)AHM453Handling/Bulk Loading of Heavy Items (312)AHM454Handling and Loading of Big Overhang Items (313)AHM455Non CLS Restrained ULD (316)AHM460Guidelines for Turnround Plan (323)AHM462Safe Operating Practices in Aircraft Handling (324)AHM463Safety Considerations for Aircraft Movement Operations (337)AHM465Foreign Object Damage(FOD)Prevention Program (340)Chapter5—LOAD CONTROL (343)AHM500Chapter5—Record of Revisions (343)AHM501Terms and Definitions (345)AHM503Recommended Requirements for a New Departure Control System (351)AHM504Departure Control System Evaluation Checklist (356)AHM505Designation of Aircraft Holds,Compartments,Bays and Cabin (362)AHM510Handling/Load Information Codes to be Used on Traffic Documents and Messages (368)AHM513Aircraft Structural Loading Limitations (377)AHM514EDP Loading Instruction/Report (388)AHM515Manual Loading Instruction/Report (404)AHM516Manual Loadsheet (416)AHM517EDP Loadsheet (430)AHM518ACARS Transmitted Loadsheet (439)AHM519Balance Calculation Methods (446)AHM520Aircraft Equipped with a CG Targeting System (451)AHM530Weights for Passengers and Baggage (452)AHM531Procedure for Establishing Standard Weights for Passengers and Baggage (453)AHM533Passengers Occupying Crew Seats (459)AHM534Weight Control of Load (460)AHM536Equipment in Compartments Procedure (461)AHM537Ballast (466)Table of ContentsPageChapter5—LOAD CONTROL(continued)AHM540Aircraft Unit Load Device—Weight and Balance Control (467)AHM550Pilot in Command's Approval of the Loadsheet (468)AHM551Last Minute Changes on Loadsheet (469)AHM561Departure Control System,Carrier's Approval Procedures (471)AHM562Semi-Permanent Data Exchange Message(DEM) (473)AHM564Migration from AHM560to AHM565 (480)AHM565EDP Semi-Permanent Data Exchange for New Generation Departure Control Systems (500)AHM570Automated Information Exchange between Check-in and Load Control Systems (602)AHM571Passenger and Baggage Details for Weight and Balance Report(PWR) (608)AHM580Unit Load Device/Bulk Load Weight Statement (613)AHM581Unit Load Device/Bulk Load Weight Signal (615)AHM583Loadmessage (619)AHM587Container/Pallet Distribution Message (623)AHM588Statistical Load Summary (628)AHM590Load Control Procedures and Loading Supervision Responsibilities (631)AHM591Weight and Balance Load Control and Loading Supervision Training and Qualifications (635)Chapter6—MANAGEMENT AND SAFETY (641)AHM600Chapter6—Record of Revisions (641)AHM610Guidelines for a Safety Management System (642)AHM611Airside Personnel:Responsibilities,Training and Qualifications (657)AHM612Airside Performance Evaluation Program (664)AHM615Quality Management System (683)AHM616Human Factors Program (715)AHM619Guidelines for Producing Emergency Response Plan(s) (731)AHM620Guidelines for an Emergency Management System (733)AHM621Security Management (736)AHM633Guidelines for the Handling of Emergencies Requiring the Evacuation of an Aircraft During Ground Handling (743)AHM650Ramp Incident/Accident Reporting (745)AHM652Recommendations for Airside Safety Investigations (750)AHM660Carrier Guidelines for Calculating Aircraft Ground Accident Costs (759)Airport Handling ManualChapter7—AIRCRAFT MOVEMENT CONTROL (761)AHM700Chapter7—Record of Revisions (761)AHM710Standards for Message Formats (762)AHM711Standards for Message Corrections (764)AHM730Codes to be Used in Aircraft Movement and Diversion Messages (765)AHM731Enhanced Reporting on ATFM Delays by the Use of Sub Codes (771)AHM780Aircraft Movement Message (774)AHM781Aircraft Diversion Message (786)AHM782Fuel Monitoring Message (790)AHM783Request Information Message (795)AHM784Gate Message (797)AHM785Aircraft Initiated Movement Message(MVA) (802)AHM790Operational Aircraft Registration(OAR)Message (807)Chapter8—GROUND HANDLING AGREEMENTS (811)AHM800Chapter8—Record of Revisions (811)AHM801Introduction to and Comments on IATA Standard Ground Handling Agreement(SGHA) (812)AHM803Service Level Agreement Example (817)AHM810IATA Standard Ground Handling Agreement (828)AHM811Yellow Pages (871)AHM813Truck Handling (872)AHM815Standard Transportation Documents Service Main Agreement (873)AHM817Standard Training Agreement (887)AHM830Ground Handling Charge Note (891)AHM840Model Agreement for Electronic Data Interchange(EDI) (894)Chapter9—AIRPORT HANDLING GROUND SUPPORT EQUIPMENT SPECIFICATIONS (911)AHM900Chapter9—Record of Revisions (911)AHM901Functional Specifications (914)AHM904Aircraft Servicing Points and System Requirements (915)AIRBUS A300B2320-/B4/C4 (917)A300F4-600/-600C4 (920)A310–200/200C/300 (926)A318 (930)A319 (933)Table of ContentsPageChapter9—AIRPORT HANDLING GROUND SUPPORT EQUIPMENT SPECIFICATIONS(continued) AHM904Aircraft Doors,Servicing Points and System Requirements for the Use of Ground Support Equipment(continued)A320 (936)A321 (940)A330-200F (943)A330-300 (948)A340-200 (951)A340-300 (955)A340-500 (959)A340-600 (962)Airbus350900passenger (965)AIRBUS A380-800/-800F (996)ATR42100/200 (999)ATR72 (1000)AVRO RJ70 (1001)AVRO RJ85 (1002)AVRO RJ100 (1003)B727-200 (1004)B737–200/200C (1008)B737-300,400,-500 (1010)B737-400 (1013)B737-500 (1015)B737-600,-700,-700C (1017)B737-700 (1020)B737-800 (1022)B737-900 (1026)B747–100SF/200C/200F (1028)B747–400/400C (1030)B757–200 (1038)B757–300 (1040)Airport Handling ManualPageChapter9—AIRPORT HANDLING GROUND SUPPORT EQUIPMENT SPECIFICATIONS(continued) AHM904Aircraft Doors,Servicing Points and System Requirements for the Use of Ground Support Equipment(continued)B767—200/200ER (1041)B767—300/300ER (1044)B767—400ER (1048)B777–200/200LR (1051)B777–300/300ER (1055)Boeing787800passenger (1059)BAe ATP(J61) (1067)Bombardier CS100 (1068)Bombardier CS300 (1072)CL-65(CRJ100/200) (1076)DC8–40/50F SERIES (1077)DC8–61/61F (1079)DC8–62/62F (1081)DC8–63/63F (1083)DC9–15/21 (1085)DC9–32 (1086)DC9–41 (1087)DC9–51 (1088)DC10–10/10CF (1089)DC10–30/40,30/40CF (1091)EMBRAER EMB-135Regional Models (1092)EMBRAER EMB-145Regional Models (1094)Embraer170 (1096)Embraer175 (1098)Embraer190 (1100)Embraer195 (1102)FOKKER50(F27Mk050) (1104)FOKKER50(F27Mk0502) (1106)Chapter9—AIRPORT HANDLING GROUND SUPPORT EQUIPMENT SPECIFICATIONS(continued) AHM904Aircraft Doors,Servicing Points and System Requirements for the Use of Ground Support Equipment(continued)FOKKER70(F28Mk0070) (1108)FOKKER100(F28Mk0100) (1110)FOKKER100(F28Mk0100) (1112)IL-76T (1114)MD-11 (1116)MD–80SERIES (1118)SAAB2000 (1119)SAAB SF-340 (1120)TU-204 (1122)AHM905Reference Material for Civil Aircraft Ground Support Equipment (1125)AHM905A Cross Reference of IATA Documents with SAE,CEN,and ISO (1129)AHM909Summary of Unit Load Device Capacity and Dimensions (1131)AHM910Basic Requirements for Aircraft Ground Support Equipment (1132)AHM911Ground Support Equipment Requirements for Compatibility with Aircraft Unit Load Devices (1136)AHM912Standard Forklift Pockets Dimensions and Characteristics for Forkliftable General Support Equipment (1138)AHM913Basic Safety Requirements for Aircraft Ground Support Equipment (1140)AHM914Compatibility of Ground Support Equipment with Aircraft Types (1145)AHM915Standard Controls (1147)AHM916Basic Requirements for Towing Vehicle Interface(HITCH) (1161)AHM917Basic Minimum Preventive Maintenance Program/Schedule (1162)AHM920Functional Specification for Self-Propelled Telescopic Passenger Stairs (1164)AHM920A Functional Specification for Towed Passenger Stairs (1167)AHM921Functional Specification for Boarding/De-Boarding Vehicle for Passengers withReduced Mobility(PRM) (1169)AHM922Basic Requirements for Passenger Boarding Bridge Aircraft Interface (1174)AHM923Functional Specification for Elevating Passenger Transfer Vehicle (1180)AHM924Functional Specification for Heavy Item Lift Platform (1183)AHM925Functional Specification for a Self-Propelled Conveyor-Belt Loader (1184)AHM925A Functional Specification for a Self-Propelled Ground Based in-Plane LoadingSystem for Bulk Cargo (1187)Chapter9—AIRPORT HANDLING GROUND SUPPORT EQUIPMENT SPECIFICATIONS(continued) AHM925B Functional Specification for a Towed Conveyor-Belt Loader (1190)AHM926Functional Specification for Upper Deck Catering Vehicle (1193)AHM927Functional Specification for Main Deck Catering Vehicle (1197)AHM930Functional Specification for an Upper Deck Container/Pallet Loader (1201)AHM931Functional Specification for Lower Deck Container/Pallet Loader (1203)AHM932Functional Specification for a Main Deck Container/Pallet Loader (1206)AHM933Functional Specification of a Powered Extension Platform to Lower Deck/Container/ Pallet Loader (1209)AHM934Functional Specification for a Narrow Body Lower Deck Single Platform Loader (1211)AHM934A Functional Specification for a Single Platform Slave Loader Bed for Lower DeckLoading Operations (1213)AHM936Functional Specification for a Container Loader Transporter (1215)AHM938Functional Specification for a Large Capacity Freighter and Combi Aircraft TailStanchion (1218)AHM939Functional Specification for a Transfer Platform Lift (1220)AHM941Functional Specification for Equipment Used for Establishing the Weight of aULD/BULK Load (1222)AHM942Functional Specification for Storage Equipment Used for Unit Load Devices (1224)AHM950Functional Specification for an Airport Passenger Bus (1225)AHM951Functional Specification for a Crew Transportation Vehicle (1227)AHM953Functional Specifications for a Valuable Cargo Vehicle (1229)AHM954Functional Specification for an Aircraft Washing Machine (1230)AHM955Functional Specification for an Aircraft Nose Gear Towbar Tractor (1232)AHM956Functional Specification for Main Gear Towbarless Tractor (1235)AHM957Functional Specification for Nose Gear Towbarless Tractor (1237)AHM958Functional Specification for an Aircraft Towbar (1240)AHM960Functional Specification for Unit Load Device Transport Vehicle (1242)AHM961Functional Specification for a Roller System for Unit Load Device Transportation on Trucks (1245)AHM962Functional Specification for a Rollerised Platform for the Transportation of Twenty Foot Unit Load Devices that Interfaces with Trucks Equipped to Accept Freight ContainersComplying with ISO668:1988 (1247)AHM963Functional Specification for a Baggage/Cargo Cart (1249)AHM965Functional Specification for a Lower Deck Container Turntable Dolly (1250)AHM966Functional Specification for a Pallet Dolly (1252)Chapter9—AIRPORT HANDLING GROUND SUPPORT EQUIPMENT SPECIFICATIONS(continued) AHM967Functional Specification for a Twenty Foot Unit Load Device Dolly (1254)AHM968Functional Specification for Ramp Equipment Tractors (1256)AHM969Functional Specification for a Pallet/Container Transporter (1257)AHM970Functional Specification for a Self-Propelled Potable Water Vehicle with Rear orFront Servicing (1259)AHM971Functional Specification for a Self-Propelled Lavatory Service Vehicle with Rear orFront Servicing (1262)AHM972Functional Specifications for a Ground Power Unit for Aircraft Electrical System (1265)AHM973Functional Specification for a Towed Aircraft Ground Heater (1269)AHM974Functional Specification for Aircraft Air Conditioning(Cooling)Unit (1272)AHM975Functional Specifications for Self-Propelled Aircraft De-Icing/Anti-Icing Unit (1274)AHM976Functional Specifications for an Air Start Unit (1278)AHM977Functional Specification for a Towed De-Icing/Anti-Icing Unit (1280)AHM978Functional Specification for a Towed Lavatory Service Cart (1283)AHM979Functional Specification for a Towed Boarding/De-Boarding Device for Passengers with Reduced Mobility(PRM)for Commuter-Type Aircraft (1285)AHM980Functional Specification for a Self-Propelled Petrol/Diesel Refueling Vehicle forGround Support Equipment (1287)AHM981Functional Specification for a Towed Potable Water Service Cart (1289)AHM990Guidelines for Preventative Maintenance of Aircraft Towbars (1291)AHM994Criteria for Consideration of the Investment in Ground Support Equipment (1292)AHM995Basic Unit Load Device Handling System Requirements (1296)AHM997Functional Specification for Sub-Freezing Aircraft Air Conditioning Unit (1298)Chapter10—ENVIRONMENTAL SPECIFICATIONS FOR GROUND HANDLING OPERATIONS (1301)AHM1000Chapter10—Record of Revisions (1301)AHM1001Environmental Specifications for Ground Handling Operations (1302)AHM1002Environmental Impact on the Use of Ground Support Equipment (1303)AHM1003GSE Environmental Quality Audit (1305)AHM1004Guidelines for Calculating GSE Exhaust Emissions (1307)AHM1005Guidelines for an Environmental Management System (1308)Chapter11—GROUND OPERATIONS TRAINING PROGRAM (1311)AHM1100Chapter11—Record of Revisions (1311)AHM1110Ground Operations Training Program (1312)Appendix A—References (1347)Appendix B—Glossary (1379)Alphabetical List of AHM Titles (1387)IATA Strategic Partners..............................................................................................................................SP–1。
exploringthemoti...

468Y.Zhao and J.Tanghallmark of ACG subculture.From human-computer interaction perspective,the ele-ments of user-centered design and(sub)culture-centered design are well represented in the design process of danmaku websites.Zhang(2008)proposes the motivational affordance theory to elaborate on the positive design principle for ICT adoption and use. Hamari et al.(2014)indicate that gamification is a desired way to support user engagement and enhance positive patterns in service use.Deterding et al.(2011) highlight that the affordances implemented in gamification will lead to some positive outcomes of product/service use.We argue game elements embedded in the human-focused design process enable the motivational affordances of an IT artifact.To our best knowledge,few studies or research models explain the psychological and behavioral aspects of user behavior in danmaku websites(Shen et al.2014).Our study is thefirst attempt to investigate the motivational affordances of Chinese danmaku websites. Therefore,we would like to explore what motivates digital natives to use danmaku websites,especially the driving factors for their contributing behavior.In this paper,we posit to adopt gamification design as a theoretical lens and view the game elements in danmaku websites as a reflection of related motivational affordances.We conducted an exploratory investigation on four Chinese Danmaku video sharing websites,i.e.,AcFun, Bilibili,Tudou,and Kankan,to answer the following research question: What is the current status for the gamification design in Chinese danmaku websites and how it relates to the underlying motivational affordances?2Motivational Affordances via Gamification Design2.1Motivational AffordanceFrom the design science research paradigm,Zhang(2008)adapts the concept of affor-dance and proposes the concept of motivational affordance to examine the positive design of ICT,arguing that people tend to use and continue to use ICT to fulfill various psy-chological,cognitive,social,and emotional needs.Therefore,features or functions of an IT artifact that support these internal motivational needs can influence whether,how,and how much this artifact will be used(Zhang2008).The design principles of motivational affordances are proposed for ICT design in general to fulfill thefive different motivational sources,including psychological(autonomy and self),cognitive(competence and achievement),social&psychological(relatedness),leadership and followership,and emotional(emotion and affect).We consent that the motivational affordance framework and design principles can and should be selectively applied to enhance the motivation of ICT users.In this study,danmaku video sharing website is one kind of social information systems,which targets at a unique user group and reflects an obvious hedonic charac-teristic of usage.Thus,the design and support of the motivational affordances is an important determinant of the successful adoption and continual use of danmaku websites.2.2Reviewing Motivational Affordance in Gamification Design ProcessIn recent years,gamification has drawn the attention of academics and practitioners in various domains,such as business,education,information systems,health informatics,Exploring the Motivational Affordancesof Danmaku Video Sharing Websites:Evidence from Gamification DesignYuxiang Zhao1(&)and Jian Tang21School of Economics and Management,Nanjing University of Science&Technology,Nanjing,China**************.com2School of Information,Central University of Finance and Economics,Beijing,China*********************Abstract.Danmaku video sharing website is a kind of popular social mediaused by digital natives in China.Very few existing studies or research modelsexplain the psychological and behavioral aspects of user behavior in danmakuwebsites.The paper aims to explore the motivational affordances of Chinesedanmaku websites from the gamification design ing the quali-tative Delphi method and follow-up interviews,we leveraged the knowledgeand experience of18panel members who were labelled as“UP主”in the ACGcommunities.Some key researchfindings have been drawn from the analysis.Keywords:DanmakuÁMotivational affordanceÁGame elementsÁGamificationÁDelphi analysis1IntroductionSocial media have promoted the emergence and development of diverse subcultures among the younger generation who are labeled as digital natives(Prensky2001).ACG (Animation,Comic,and Game)is such an adolescent subculture that is fascinating to a group of digital natives,named Otaku.This subculture wasfirst found in Japan. Through various media it spread to other Asian countries(e.g.,China)and even to the United States.Danmaku video sharing website is a kind of important social media for those fans of Otaku to communicate and collaborate in virtual pared with regular user-generated content websites such as Youtube,users can synchronously post comments when watching ACG video on danmaku websites,and these comments will immediately slide over videos in the form of commentary subtitle(Shen et al. 2014).So far,danmaku websites receive great attention and interest from digital natives and rapidly accumulate a large number of users in a short time period.Danmaku websites allow users to communicate and collaborate with each other while watching videos.This shared watching experience may lead to a strong perceived social presence and sense of virtual community.Danmaku websites,as an emerging UGC style,have been welcomed by mass digital natives,especially those who have a©Springer International Publishing Switzerland2016M.Kurosu(Ed.):HCI2016,Part III,LNCS9733,pp.467–479,2016.DOI:10.1007/978-3-319-39513-5_44。
站在巨人肩膀上,助力学术科研(2)

检索功能
期刊内检索
可在科学周刊、每 日科学、信号转导 环境和所有 HighWire平台期刊 中检索
高级检索
直接检索 关键词查询
作者查询 限定发布时间
限定查询专题
检索结果
保存检索式、 订阅检索匹配通知、 加入收藏夹等。
HTML格式全文
加入个人收藏夹 下载引文管理数据 文章引用提醒 Email这篇文章 浏览PubMed收录情况
参考文献链接
可免费浏览 Highwire平台上 85万多篇全文 信息
提供PubMed、ISI和Highwire平 台上面760种科学期刊的链接
被其他文献引用
编辑提供的 延伸阅读的建议
Highwire平台上检索
medicine
检索结果
引用树图
目录邮件推送和RSS Feeds服务
RSS Feeds服务
期刊投稿
期刊投稿详细说明书
——插图格式
8、插图必须是PS, EPS, TIFF, 或PDF格式单独上传;正文中 的插图以(a), (b)等标示顺序; 9、插图的大小必须符合正文大 小;单栏是3&5/16英尺,双栏 是7英尺; 10、线条的粗细必须在0.5磅或 以上,否则很难清除显示出; 11、line art图片分辨率选择600; halftone图片分辨率选择264; line art+halftone图片分辨率选 择600;line art图片要选择黑白 的位图,而不是灰体,其他图 片选择灰体; 12、彩图要选择300的分辨率, 格式选择TIFF或PS等,模式选 择RGB或CMYK. 13、插图或表格的说明需以2倍 行距编辑在参考文献之后。
• 参考文献有限/过时
– 也不要太多; 避免过多的自身引用
BIM技术在高桩码头设计阶段的应用

2021 年 3 月第3期总第580期水运工程Port & Waterway EngineeringMar. 2021No. 3 Serial No. 580BIM 技术在高桩码头设计阶段的应用蔡波(1.中交武汉港湾工程设计研究院有限公司,湖北武汉430040;2.海工结构新材料及维护加固技术湖北省重点实验室,湖北武汉430040)摘要:针对传统的高桩码头二维设计过程存在的不足,结合盐城港重件码头工程BIM 技术的实践应用,从协同服务器 搭建、族库建设以及多专业协同3个方面详细阐述了 BIM 协同设计方法,并提出了构件参数化设计、工程量明细统计、复杂节点参数化设计、工程出图标准化的BIM 设计阶段应用点。
研究表明:BIM 技术的应用实现了模型元素信息的联动与共享,提升了多专业协同的参与度,工程设计表达的准确性、协同效率也随之提高。
关键词: BIM ; 高桩码头; 协同服务器; 模型构件库; 协同设计中图分类号:U 652. 7文献标志码:A 文章编号:1002-4972(2021)03-0174-06Application of BIM technique in the design of high-piled wharfCAI Bo 1,2(1. CCCC Wuhan Harbor Engineering Design and Research Co., Ltd., Wuhan 430040, China; 2.Hubei Key Laboratory of Advanced Materials & Reinforcement Technology Research for Marine Environment Structures, Wuhan 430040, China)Abstract : Given the shortcomings of the traditional high-piled wharf two-dimensional design process, combinedwith the practical application of BIM technology in Yancheng Port's heavy-duty wharf project, this paper elaborates theBIM collaborative design method from three aspects: collaborative server construction, family library construction, and multi-disciplinary collaboration, and puts forward the application points of BIM design stage of component parameterized design, detailed statistics of engineering quantities, parameterized design of complex nodes, andstandardization of engineering drawings. Studies have shown that the application of BIM technology has realized the linkage and sharing of model element information, and has improved the participation of multi-disciplinarycollaboration, and the accuracy of engineering design expression and collaboration efficiency have also been improved.Keywords : building information modeling; high-piled wharf; collaboration server; model component library;collaborative design传统的高桩梁板式码头基于AutoCAD 二维设计过程中,主要存在以下问题:1)设计过程中存在信息孤岛。
科技英语课后习题 中-英句子
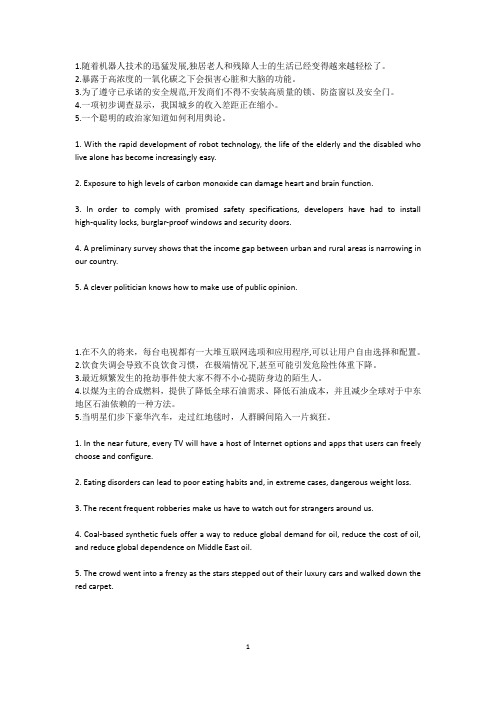
1.随着机器人技术的迅猛发展,独居老人和残障人士的生活已经变得越来越轻松了。
2.暴露于高浓度的一氧化碳之下会损害心脏和大脑的功能。
3.为了遵守已承诺的安全规范,开发商们不得不安装高质量的锁、防盗窗以及安全门。
4.一项初步调查显示,我国城乡的收入差距正在缩小。
5.一个聪明的政治家知道如何利用舆论。
1. With the rapid development of robot technology, the life of the elderly and the disabled who live alone has become increasingly easy.2. Exposure to high levels of carbon monoxide can damage heart and brain function.3. In order to comply with promised safety specifications, developers have had to install high-quality locks, burglar-proof windows and security doors.4. A preliminary survey shows that the income gap between urban and rural areas is narrowing in our country.5. A clever politician knows how to make use of public opinion.1.在不久的将来,每台电视都有一大堆互联网选项和应用程序,可以让用户自由选择和配置。
2.饮食失调会导致不良饮食习惯,在极端情况下,甚至可能引发危险性体重下降。
3.最近频繁发生的抢劫事件使大家不得不小心提防身边的陌生人。
4.以煤为主的合成燃料,提供了降低全球石油需求、降低石油成本,并且减少全球对于中东地区石油依赖的一种方法。
鸡蛋实验的英语作文400字

鸡蛋实验的英语作文400字Egg Drop Experiment.Introduction.The egg drop experiment is a classic science experiment that demonstrates the principles of physics, particularly the laws of motion and energy conservation. The objective of the experiment is to design and construct a protective device that will prevent an egg from breaking when dropped from a specified height.Materials.Egg.Cardboard.Tape.Other materials as desired (e.g., straws, bubble wrap, cotton balls)。
Procedure.1. Design the protective device: Brainstorm ideas and sketch out plans for a protective device that will shield the egg from impact. Consider the materials available and the principles of physics that will be at play.2. Build the protective device: Carefully assemble the protective device using the materials chosen. Pay attention to the strength and durability of the structure, as well as its ability to absorb and distribute impact forces.3. Prepare the egg: Gently place the egg inside the protective device and secure it in place. Ensure that the egg is adequately protected from all sides.4. Drop the device: From the specified height,carefully drop the protective device with the egg inside. Observe the behavior of the device and the condition of theegg after the drop.Data Collection and Analysis.Egg condition: After the drop, check the condition of the egg. Was it broken, cracked, or undamaged?Protective device performance: Evaluate the effectiveness of the protective device in preventing the egg from breaking. Consider the materials used, the design, and the overall impact absorption capabilities.Variables: Identify the variables that may have influenced the outcome of the experiment, such as the height of the drop, the mass of the egg, and the design of the protective device.Conclusion.The egg drop experiment provides valuable insights into the principles of physics and engineering. By designing and building a protective device that successfully protects anegg from breaking, students can demonstrate their understanding of impact forces, energy conservation, and the importance of structural design. The experiment also encourages creativity, problem-solving skills, and the ability to test and evaluate hypotheses.。
- 1、下载文档前请自行甄别文档内容的完整性,平台不提供额外的编辑、内容补充、找答案等附加服务。
- 2、"仅部分预览"的文档,不可在线预览部分如存在完整性等问题,可反馈申请退款(可完整预览的文档不适用该条件!)。
- 3、如文档侵犯您的权益,请联系客服反馈,我们会尽快为您处理(人工客服工作时间:9:00-18:30)。
Design of a high-impact survivable robotD.O’Halloran,A.Wolf *,H.ChosetBiorobotics Lab,Department of Mechanical Engineering and the Robotics Institute,Carnegie Mellon University,Newell-Simon Hall,5000Forbes AV,Pittsburgh,PA 15213,USAReceived 12April 2004;received in revised form 12December 2004;accepted 11February 2005Available online 7April 2005AbstractThis paper presents the design,construction,and testing of a two-wheeled low-cost mobile robot plat-form that has high survivability when subjected to large impact forces and general rough handling.The design of the drive transmission system and integrated suspension system is developed,along with general equations of motion describing their dynamics.Analyses were conducted to insure stability of the various subsystems and optimize parameters for the desired vibration characteristics.Equations of motion were also developed to describe the rocking chassis phenomenon inherent to the two-wheeled design.A flywheel compensation scheme which helps eliminate the rocking chassis problem is also outlined.An impact anal-ysis combining theory and empirical data was used to predict the survivability threshold.Finally,three ser-ies of experiments were conducted,with the first two followed by design improvements.In contrast to currently available commercial robots,our new design employs a flexible mechanical platform capable of absorbing energy during high load impacts.This design was substantiated during the final tests when the robot survived a third story drop without any damage.Ó2005Elsevier Ltd.All rights reserved.Keywords:Two wheel robot;Survivable robot;Robot design0094-114X/$-see front matter Ó2005Elsevier Ltd.All rights reserved.doi:10.1016/j.mechmachtheory.2005.02.004*Corresponding author.Tel.:+14125785368.E-mail addresses:dmo@ (D.O ÕHalloran),alon.wolf@ (A.Wolf),choset@ (H.Choset)./locate/mechmtMechanism and Machine Theory 40(2005)1345–1366Mechanism and Machine Theory1346 D.O’Halloran et al./Mechanism and Machine Theory40(2005)1345–1366 NomenclatureW component weightm component massS spring forcek spring constantd spring displacementN normal force or bearing forceT tension in drive beltL belt section lengthr component radiush angle between componentsH tire bearing forceC spring collar bearing forceB chassis bearing forceM moment or torqueA motor reaction forceH C angle of chassis with respect to vertical axisQ countering force provided by some balancing system(such asflywheel)M Q countering moment provided by some balancing systemI moment of inertiaa angular accelerationa C,y linear acceleration of chassis in y-directionSubscriptsX In x-directionY In y-directionP pulleyS springi idlerC chassis1.IntroductionUrban search and rescue(USAR)robots have recently become much more widely accepted as a vitalfield tool in emergency situations.Recent past events such as the Mexico City earthquake in 1985,the1995Oklahoma City bombing,and the September11attack on the World Trade Center have shown that dangerous and inaccessible regions are major problems during a rescue opera-tion.In Mexico City earthquake,135rescue workers were killed,65of the135died while trying to search and rescue while going through confined spaces which wereflooded trapping the rescue workers inside[1,2].The roles of robots also continue to expand in military reconnaissance mis-sions,such as in the search for terrorist cells hidden deep inside caves in Afghanistan during2001–D.O’Halloran et al./Mechanism and Machine Theory40(2005)1345–13661347 2002.However,the effectiveness of current robot designs in these environments is limited by numerous factors.One such factor is the inherent fragility of many of the current robots,which makes these robots susceptible to failure due to rough handling or impacts which occur during these missions.This paper presents a design for a mobile robot platform that improves the robots survivability when subjected to high impact forces and general rough handling,is compact,and can fulfill the role of a search and rescue or reconnaissance aid robot.A limited amount of previous work has been done on researching the primary factors which contribute to robot survivability.Cameron and Arkin[3]studied the survival rate and behavior of falling cats to better understand the characteristics that allow these animals to survive falls of great height so that they might formulate a set of criteria that should be satisfied for robots to survive similar falls.Two of their conclusions of interest are that the robot must be able to sit-uate itself in a manner in which its locomotion actuators(wheels,legs,etc.)impact the ground first,and secondly that compliance is necessary to absorb the energy of impact.In other research Arkin[4]describes various ways control and redunancy can be used to increase the fault tolerance of a robot under harsh operating conditions.In actual practical application,two other key robots have been deployed for similar missions and are touted for their impact survivability.The PackBot,developed by the iRobot Corporation [5],is a tracked robot with a small main chassis profile.Product specifications claim that the robot is capable of surviving a fall from up to2m onto concrete,as well as tumbling down stairs.The robot has a height of only about8in.and weighs in approximately50lbs.This robot has seen extensive real-worldfield deployment at both the WTC disaster site and during military missions in Afghanistan.The second robot for comparison is the Dragon Runner developed at the National Robotics Engineering Consortium at Carnegie Mellon University[6].Dragon Runner weighs about16pounds and has four large wheels which extend above and below the base chassis profile.While this robot is still in development,in its current form the designers claim it to be able to survive impacts at full speed or from a third story drop.These two robots will be used as base-lines for comparison to evaluate the performance of the new robot design outlined within this paper,with our goal to build a robot capable of surviving a third story drop but at costing a mag-nitude less than these two designs.The work presented here specifically details the mechanical design of the general robot config-uration and its drive system.A rudimentary remote control system was used to control the robot during experiments,though the robot is made to accommodate more sophisticated control elec-tronics at a later phase.Additionally,the mechanical design incorporates measures to minimize the shock loads that would be transmitted to the current and possible future electronic components.This paper is organized as follows:Section2presents an overview of the general robot con-figuration used for the design,including a discussion of the advantages and limitations of this configuration.Section3details the conceptual design of the transmission system while Section 4covers the development of the unique suspension system.Section5will address in detail the general motion limitations of the robot configuration and the proposed compensation scheme.Section6details theoretical predictions for the impact capability of the design,while Section7discusses the actual experimental drop tests and the subsequent design improve-ments.Finally,the conclusions of this robot design and experimentation project are covered in Section8.1348 D.O’Halloran et al./Mechanism and Machine Theory40(2005)1345–13662.General configurationOne of thefirst general design decisions that had to be made was the locomotion scheme for the robot.Each of the standard locomotion choices,legged,wheeled,and tracked,have their advan-tages and disadvantages.However,given the primary goal of this robot to survive impacts, wheeled locomotion is the best choice.It offers reasonably good traction on most terrains and more importantly has the best shock absorption capability of the three choices mentioned above due to the intrinsic elasticity of most tires.More specifically this design will utilize pneumatic tires due to their superior shock absorption capabilities.The primary metric used in evaluating each of the robot design choices was that the robot must be capable of withstanding a fall from at least9.1m,so as to equal or improve upon the perfor-mance of the best commercially available platforms.The reason for desiring a robot that can with-stand such falls is that is it is conceivable that a robot acting in a search and rescue or military reconnaissance capacity might inadvertently or even intentionally be driven offa ledge.Consider-ing the potential for such an event adds a significant complicating factor in designing an impact-survival mechanical platform.In general the orientation of the robot upon impact with the ground cannot be known with any certainty;therefore the robot must be protected from impact in all directions.Even if the assump-tion is made that lateral disturbances acting on the robot during its fall are negligible enough that the robot will not topple about an axes orthogonal to the drive axles,the propensity for the robot to spin about an axes parallel to the drive axles will still exist,meaning the robot could land in an orientation upside down from its usual driving state.Therefore the general configuration must at a minimum provide protection against impact in all directions orthogonal to the drive axles. Given that pneumatic tires are being used as afirst line of defense against impact,it makes sense to design the robot so that the tires will be thefirst component to contact the ground regardless of robot orientation.To this end,the robot chassis has been designed so that itfits entirely within the outer profile of the tires as seen in Fig.1.A four wheeled robot could fulfill this criterion;how-ever,this design carries with it several disadvantages.First,while a differential drive could in the-ory be used for steering it would not be as efficient as on a two wheeled robot due to the extra friction forces created by the extra two tires.Second,if the more typical and efficient rack-and-andpinion steering scheme were used for a four wheeled robot,this would add components Array Fig.1.Two-wheel suspended chassis configuration.D.O’Halloran et al./Mechanism and Machine Theory40(2005)1345–13661349 complexity to the overall robot which would therefore increase the number of failure points.Also, in a four wheeled scheme the section of chassis extending between the two wheels is laterally unprotected and could potentially be impacted by obstacles whichfit between the wheels.Finally, the extra two wheels add size and mass to the overall robot leading to higher impact forces and decreasing the robotÕs portability.Due to these limitations,this design employs a two wheeled driving scheme,shown in Fig.1which does not suffer from the above mentioned problems. Alas,a two wheeled robot has limitations of its own.In a four wheeled robot when the motors drive two of the wheels,the other two wheels provide a reaction force with the ground which pre-vents the chassis from spinning about the drive axle as opposed to the wheels.Other robots have employed this two wheel scheme,though none strictly in the manner of this robot.The nBot bal-ancing robot developed by Anderson actually carries its chassis above its drive shafts like an in-verted pendulum,thus having active control of the balance in the absence of any structure to provide a reaction force[7].Most conventional two-wheeled robots,such as those often used by hobbyist or research robots such as the Nomad Scout always have an inert third caster wheel or dragging structural piece which provides the reaction force and maintains the balance of the robot.However,in this design there is no component extending beyond the wheel profile to pro-vide a ground reaction force.Therefore,when the motors apply torque to the drive shafts there will be a battle between the chassis and the wheels to see which one actually rotates.This means that for accelerations beyond a certain threshold the chassis will spin rather than the wheels.This phenomenon along with a compensation scheme will be more fully detailed and explored in Section5.3.Drive transmission designA number of power transmission options were examined in order to determine the optimal transmission scheme for this robot design.The main criteria in evaluating these different options were the transmissionsÕcapability of minimizing the shock and vibration transmitted to the motors,simplicity of the system which translates to minimizing potential failure points,and mechanical efficiency of the system.Thefirst option,a spur gear transmission has the advantages of simplicity and minimal com-ponent count,as well as high mechanical efficiency[8].A bevel gear transmission is similarly sim-ple though slightly less efficient than a spur gear transmission.It does however allow the motors to be mounted vertically which helps to minimize the width of the chassis and henceforth the overall robot size.A worm gear transmission would also allow for the motors to be mounted vertically and offers high gear ratios,though they are expensive and relatively inefficient.All three of these geared transmissions suffer from a similar major disadvantage in that they are poor at absorbing shock.Another option is a chain drive transmission.A chain drive providesflexibility in the place-ment of the motors so as to minimize the overall chassis size,has better shock absorption capa-bilities than gear transmissions,and still has high efficiency.However,a chain drive requires lubrication for smooth operation and contains numerous links which each represent additional failure points.Thefinal option is a belt drive transmission.This system has the sameflexibility of motor placement as the chain drive and better shock absorption capabilities due to the inherent elasticity of timing belts.Additionally this system is efficient,quiet,and requires no lubrication.1350 D.O’Halloran et al./Mechanism and Machine Theory40(2005)1345–1366Therefore,the belt drive system was chosen as the initial transmission scheme based on the eval-uation criteria.4.Suspension designTheflexible nature of the belt drive system allowed us to include a unique suspension system shown in Fig.2,which would further enhance the overall shock absorption capability of the trans-mission.In order to discuss the details of this suspension,we shallfirst define afixed coordinate system whose z-axis points from the wheel towards the chassis and whose y-axis points upward with respect to the ground.The drive shaft connected to the wheel is mounted to the chassis via a spherical bearing which allows the shaft limited rotation(10°offof perpendicular axis)about the x and y axes,in addition to the typical z-axis rotation that allows transmission of torque to the wheels.A pulley(p2)is mounted at the end of the shaft internal to the chassis.The timing belt wraps around pulley p2,a pulley(p1)attached to a drive motor mounted to the chassis,and a free spinning idler pulley(p3).The idler pulley is attached to a shaft connected to a pair of springs which allow the pulley to move in order to compensate for motion of pulley p2,thus preserving the overall length of the belt and the tension in the belt that allows for the transmission of torque. Three suspension springs attached at opposite ends to the chassis and to a free spinning shaft col-lar provide the centering force which keeps the shaft horizontal under static conditions.We also considered substituting a membrane for the three springs.A membrane would have easily added dampening to the system[9].However,due to the configuration of the system the membrane would need to have non-axisymmetrical properties which would not be easilyachieved. Array Fig.2.Belt transmission/chassis suspension.D.O’Halloran et al./Mechanism and Machine Theory40(2005)1345–136613514.1.General suspension equationsIn order to analyze and optimize the detail design of the suspension system,general equations of motion(EOM)were developed for each component of the system.In total37equations are needed to describe the general motion of the suspension system.One of the key components in the system is the drive shaft,shown in Figs.3–5,since it is di-rectly responsible for translating torques out to the wheel from the motor and for back propagat-ing the motion from the wheel caused by an impact.The particular equations for the shaft are shown below,where the force balance in the x-direction is given by Eq.(1),the y-direction Eq.(2),the moment balance about the z-axis Eq.(3),about the y-axis Eq.(4)and about the x-axis Eq.(5),with all three moment equations passing through the shaft center of gravity(see Nomenclature).N p2;xþC xÀB xÀH xÀW S sin h C¼m S€x Sð1ÞH yÀN p2;yþC yÀB yÀW S cos h C¼m S€y Sð2ÞM SÀM W¼I S;z a s;zð3Þ1=2C xðL1þL2ÀL3ÞÀ1=2N p2;xðL1þL2þL3ÞÀ1=2B xðL2þL3ÀL1Þþ1=2H xðL1þL2þL3Þ¼I S;y a s;yð4Þ1=2N p2;yðL1þL2þL3ÞÀ1=2C yðL1þL2ÀL3ÞÀ1=2B yðL2þL3ÀL1Þþ1=2H yðL1þL2þL3Þ¼I S;x a s;xð5ÞThe other key component in analyzing the behavior of the suspension system is the chassis shown in Figs.6and7,since this component ties the shaft,drive system,and suspension system together.The EOM for this part are presented below.Note that the moment equation is taken with respect to the drive shaft axis.S R ;2sin h R ;S2Àd ÀS R ;3sin h R ;S3Àd ÀS L ;2sin h L ;S2Àd þS L ;3sin h L ;S3Àd ÀB R ;xþB L ;x ÀA L ;x þA R ;x þQ x ÀW C sin h C ¼m C a C ;xð6ÞS R ;2cos h R ;S2Àd þS R ;3cos h R ;S3Àd ÀS R ;1þS L ;2cos h L ;S2Àd þS L ;3cos h L ;S3Àd ÀS L ;1þB R ;y þB L ;y þ2S L ;i þ2S R ;i ÀW C cos h C þA L ;y þA R ;y ÀQ y ¼m C a C ;yð7ÞS R ;2d s ;y sin h R ;S2Àd ÀS R ;3d s ;y sin h R ;S3Àd ÀS R ;2d c ;w cos h R ;S2Àd þS R ;3d c ;w cos h R ;S3ÀdÀS L ;2d s ;y sin h L ;S2Àd þS L ;3d s ;y sin h L ;S3Àd þS L ;2d c ;w cos h L ;S2Àd ÀS L ;3d c ;w cos h L ;S3ÀdÀS R ;1d c ;h sin h R ;S1Àd þS L ;1d c ;h sin h L ;S1Àd þA R ;x d A ;y ÀA L ;x d A ;y ÀA R ;y d A ;x þA L ;y d A ;xÀM R ;A ÀM L ;A þQ x d Q ¼I C ;z a C þm C ðd gc a C Þd gc ð8ÞFig.4.Drive shaft deflectiongeometry.Fig.5.CAD model of shaft system.1352 D.O’Halloran et al./Mechanism and Machine Theory 40(2005)1345–1366D.O’Halloran et al./Mechanism and Machine Theory40(2005)1345–13661353Fig.7.CAD model of chassis.With the general equations of motion derived,static equilibrium conditions can now be solved for;giving the starting point for developing the detailed configuration and design of the robotÕs various components.4.2.Static analysis and optimizationGiven the general equations of motion shown above,the next step in the design process was to solve for the various parameters under static conditions.Obviously since this is a static analysis allthe bodies are at rest.Given static equilibrium conditions,the tension in the belt should therefore be uniform[10].All weights,masses,lengths,and angles are known parameters.Using these assumptions along with various substitutions and algebraic manipulations of the general EOM derived above yields22static specific EOM.However,we are left with24un-knowns.Contrary to what this mightfirst indicate,the system is in fact not statically indetermi-nate.The reason being that some of the parameters,namely the spring forces,can be independently controlled since they depend solely on spring constants and deflection,two para-meters which can be chosen at will for each spring.The consequence of this result is that two of the spring forces become design parameters.In order to best control the performance of the overall system we pick spring forces from two different subsystems as the design parameters, namely the idler spring(Si)and the vertical suspension spring(S1).With the design parameters specified it is then possible to solve for all unknowns.While all the parameters are useful in evaluating maximum stresses in the various components,the spring forces(S1,S2,S3,S i)are of particular interest since they most directly will affect the suspension performance.The resulting equations,Eq.(9),and Eq.(10)for the dependent spring forces(S2, S3)are shown below in terms of only known parameters.S2¼S1À2ðS iþW i;SCÞþW i;SþW p3sin h p2þcos h p3ðsin h p1þcos h p3ÞþW p2L1þ2L3þL2L2ÀL1L22ðS iþW i;SCÞþW i;SþW p3sin h p2þcos h p3ðsin h p1Àsin h p2ÞÀW p1À2S iþ12W CþW SCÀL3L2ðW SÞÀW SCÀ2ðS iþW i;SCÞþW i;SþW p3sin h p2þcos h p3ðcos hp1þsin h p3ÞðL3þL2ÞL2cot h S3Âsin h S3sinðh S2þh S3Þð9ÞS3¼S2sin h S2À2ðS iþW i;SCÞþW i;SþW p3sin h p2þcos h p3ðcos h p1þsin h p3ÞL3þL2L21sin h S3ð10ÞFor maximum stability all springs should always remain in tension since a compressive state is inherently unstable.An analysis of a general range of values for the design spring parameters (S1,S i)gives the design space for which the dependent springs(S2,S3)remain in tension as shown in Figs.8and9.Using these graphs,we can insure that our choices of spring values for S1and Si result in a tensile state for S2and S3by checking that the corresponding point on the functional plane is above zero on the z-axis.4.3.Displacement analysisOnce the static parameters are known,the general motion of the suspension system,given some initial conditions or forcing functions,can be solved.This general disturbance analysis can also be used as afirst approximation of the system reaction to impact.1354 D.O’Halloran et al./Mechanism and Machine Theory40(2005)1345–1366In either an impact study or a general disturbance analysis it is reasonable to assume that the disturbance acts in only one radial direction since the tire theoretically makes line contact with the ground.Therefore,to simplify the analysis we will assume the disturbance acts in only a y-direc-tion.However,it should be noted that this disturbance in one direction may cause motion in both the y and x directions due to the configuration of the suspension system.Also to further simplify the geometry of the problem we will conduct the analysis with the chassis held stationary while the suspension system and the tire are free to move,while a equivalent ground force is applied to the tire in order to maintain initial static equilibrium.If we were instead to let all bodies move relative to afixed ground we would end up with additional time dependent terms to locate the point on the drive shaft which has zero displacement,thus complicating the ing the stationary chassis approach let us mandate that the point on the shaft passing through the spherical bearing of the chassis is always the point of zero displacement.This then allows us to easily relate all dis-placements back to the general displacement of the tire end of the shaft.For this analysis a more complete set of equations is needed to describe the elasticity of the tire and its influence on the overall suspension system.Modeling the tire as a simple spring(dampening will later be added to the model)as shown in Fig.10yields the following equation for the normal force acting on the wheel hub.N w¼k Tðy0Ày gðtÞþy1ðtÞÞð11ÞIn order to complete this analysis a number of geometric relationships must be developed(Fig.11).Thefirst relationship is that of the suspension spring displacements to the general shaft dis-placement as illustrated in Fig.12.Based on this diagram,the general spring displacements are given by Eqs.(12)–(14).d1Àd¼ffiffiffiffiffiffiffiffiffiffiffiffiffiffiffiffiffiffiffiffiffiffiffiffiffiffiffiffiffiffiffiffiffiffiffiffiffiffiffiffiffiffiffiffiffiffiffiffiffiffiffiffiffiffiffiffiffiffiffiffiffiffiffiffiffiffiffiffiffid1À0þy1L2L12þx1L2L12sð12Þd2Àd¼ffiffiffiffiffiffiffiffiffiffiffiffiffiffiffiffiffiffiffiffiffiffiffiffiffiffiffiffiffiffiffiffiffiffiffiffiffiffiffiffiffiffiffiffiffiffiffiffiffiffiffiffiffiffiffiffiffiffiffiffiffiffiffiffiffiffiffiffiffiffiffiffiffiffiffiffiffiffiffiffiffiffiffiffiffiffiffiffiffiffiffiffiffiffiffiffiffiffiffiffiffiffiffiffiffiffiffiffiffiffiffid2À0cos h S2Ày1L2L12þd2À0sin h S2þx1L2L12sð13Þd3Àd¼ffiffiffiffiffiffiffiffiffiffiffiffiffiffiffiffiffiffiffiffiffiffiffiffiffiffiffiffiffiffiffiffiffiffiffiffiffiffiffiffiffiffiffiffiffiffiffiffiffiffiffiffiffiffiffiffiffiffiffiffiffiffiffiffiffiffiffiffiffiffiffiffiffiffiffiffiffiffiffiffiffiffiffiffiffiffiffiffiffiffiffiffiffiffiffiffiffiffiffiffiffiffiffiffiffiffiffiffiffiffiffid3À0cos h S3Ày1L2L12þd3À0sin h S3Àx1L2L12sð14ÞAnother geometric relationship that must be developed is the motion of the idler spring and the overall profile of the transmission belt as a function of shaft displacement.The key to this rela-tionship is that the overall belt length must remain constant.As both a design and analysis sim-plification all three pulleys are chosen to have the same radius.Given this simplification,the total amount of belt wrapped around all three pulleys will always be equal to the circumference of one pulley.Therefore,the analysis can be simplified to analyzing simply the changing distances between pulley centers as illustrated by a deforming triangle as shown in Fig.13.This yields the followingfive equations which can be combined tofind a general equation for the idler pulley displacement,though that exact result is too lengthy to include here.L b3Àd¼L b3Ày3ð15ÞL b4Àd¼L b4þy ið16ÞL b1Àd¼ffiffiffiffiffiffiffiffiffiffiffiffiffiffiffiffiffiffiffiffiffiffiffiffiffiffiffiffiffiffiffiffiffiffiffiffiffiffiffiffiffiffiffiffiffiffiffiffiffiffiffiffiffiffiffiffiffiffiffiffiffiffiffiffiffiffiffiffiffiffiffiffiffiffiffiffiffiffiffiffiffiffiffiffiffiffiffiffiffiffiffiffiffiffiffiffiffiffiffiffiffiffiffiffiffiffiffiffiffiffiffiffiffiffiffiffiffiffiffiffiffiffiðL b1Þ2ÀðL b3Þ2þ2Áx3ffiffiffiffiffiffiffiffiffiffiffiffiffiffiffiffiffiffiffiffiffiffiffiffiffiffiffiffiffiffiðL b1Þ2þðL b3Þ2qþðx3Þ2þðL b3Ày3Þ2rð17ÞL b2Àd¼ffiffiffiffiffiffiffiffiffiffiffiffiffiffiffiffiffiffiffiffiffiffiffiffiffiffiffiffiffiffiffiffiffiffiffiffiffiffiffiffiffiffiffiffiffiffiffiffiffiffiffiffiffiffiffiffiðL b1Þ2ÀðL b3Þ2þðL b4þy iÞ2qð18ÞL b1þL b2þL b3þL b4¼L b1ÀdþL b2ÀdþffiffiffiffiffiffiffiffiffiffiffiffiffiffiffiffiffiffiffiffiffiffiffiffiffiffiffiffiffiffiffiffiffiffiffiffiffiffiffiffiffiffiffiffiffiffiffiðL b3ÀdþL b4ÀdÞ2þðy iÞ2qð19ÞWith these relationships derived,it is then possible to produce three coupled differential equa-tions,Eq.(20)–(22),describing the system.The overall system can therefore be characterized as a 3degree-of-freedom(DOF)vibration problem.It should be noted that the actual complexity of these equations is not fully illustrated here since some of the parameters are actually functions of the displacements and their derivatives and have not been fully expanded for the sake of compact-ness in the presentation of these equations.4L1ðL1þL2Þðk Tðy0Ày gðtÞþy1ðtÞÞÀW wÀm w€y1Þ¼2I S;x€y1ðL1þL2þL3ÞÀm S€y1ðL1ÀL2ÀL3ÞðL1þL2ÀL3Þþ2L1ð2B y L2þW SðL1þL2ÀL3ÞÀ2N p2;y L3Þð20Þ4L1ðL1þL2Þm w€x1¼2I S;y€x1L1ðL1þL2þL3Þþm S€x1ðL1ÀL2ÀL3ÞðL1þL2ÀL3ÞÀ4B x L1þ4L1N p2;xðL1þL2Þð21Þ€y1ðtÞ¼À€y gðtÞð22ÞWe then reduced the problem to a1-DOF vibration problem to get afirst approximation of the behavior of the system.To this end we will assume all displacement in the suspension sys-tem acts in the y-direction.Next,by removing the spring we will look at the displacement of the shaft independent of the stly,we will make a geometrical assumption that the dis-placement of the idler pulley(P3)is equal to the displacement of the shaft pulley(P2).Given。