段取改善ステップ(中文)
ポカヨケ改善(中文)

部件选择 错误
一致化
部件选择
部件及夹具的颜色、记号、保管地、 出错
形状、大小、方向、距离等一致
将部件共 通化减少
种类
将指示单 和部件箱
的记号 一致
分业化•专业化
同种的操作整理后分别进行 (将容易混淆的操作分散)
装反了
要安装的 部件事先 统一方向
均一化
部件或工具的形状、放置方法统一 (减少动作的种类)
本质安全化
除去设备或部件内在的危险
危险物的拦截
伤害制品的东西与受伤害 制品之间设置隔离物
作业点的分离
伤害制品的东西与受伤害 制品的场所离远一点, 使不需要注意
不良例子
对策
忘了部件 做成一体
的安装
成型
忘了夹紧
做成固定 式的夹具
从高处坠 改变操作
落
物的位置
检查错误
改变工序 使不产生 不良品
漏电、 带电
把交流式 换成干电 池式
失误发生率 0.0001 0.001
0.95
0.001 0.005 0.003
意识状态程度与失误发生率
状态度 意识的模式
0 没有意识、失神
Ⅰ 意识朦胧
Ⅱ
正常 放松状态
Ⅲ
正常 明晰的状态
Ⅳ 兴奋状态
生理状态
睡眠 疲劳、打盹 休息时、 常规操作时 积极活动时
慌慌张张时 一片混乱时
失误发生率
1
0.1以上
综合性地 考虑
各原理的“对策的对象”是什么?
原理
对策的对象
排除
操作对象•场所等条件之中含有操作及其禁止事项 的必要项目
代替化
操作者完成的机能(记忆、知觉•判断、动作)之 中,由于不能贴切地完成而产生失误的项目
TPS 精益生产用语及解释

後工程引取りジャストインタイム生産をするための3つの基本原則の1つであり、後工程が必要なときに、必要なものを必要なだけ前工程から引取ってくることをいう。
(⇒後補充生産:3頁)后工程拿取方式为了进行JIT生产所要遵循的3个基本原则之一、当后工程需要时、在必要的时候只从前工程拿取必要的东西的方法.称为后工程拿取方式.(⇒后补充生産:3页)後補充(生産)前工程が、最小限のその工程の完成品在庫(店)をもち、後工程に引取られた分だけ、種類毎に造って補充する方法をいう。
(⇒後工程引取り:1頁)后补充(生产)前工程,只保持其工程的最小限度的完成品在库、只提供后工程所需要的部分、逐个品种的制造并进行补充的方法.叫做后补充.(⇒后工程拿取:1頁)アンドン関係者へのアクションを促すための情報の窓で、現時点の異常場所を一目で判断できるようにした電光表示盤である。
異常表示のほかに、作業の指示(品質チェック、刃具交換、部品運搬など)、進度表示をするものもある。
(⇒目で見る管理:155頁)信号灯是催促相关者采取行动的情报窗口,一看就能够判断出现在有异常发生之场所的电光表示板.除异常之外、也有用来表示作业指示(品质确认、更换刀具、部品搬运等) 、作业进度的.(⇒目视管理:155頁)一個流し(生産)工程順に一個又は、一台ずつ加工・組み付けをし、一個ずつ次工程に流すやり方をいう。
(⇒工程の流れ化:39頁)一个流程(生产)工程的顺序是逐个或逐台地进行加工或组装、并一个一个地流给下一个工程的做法叫作一个流程.(⇒工程的流程化:39页)内段取り段取り替え作業のうち、ラインや機械整備の運転を止めなければできない型・刃具・そして治具類の交換などの作業をいう。
(⇔ 外段取り:77頁)(⇒ 段取り替え時間:89頁) 内段取在段取更换作业中,如果不停止生产线及机器设备的运转就无法进行模型 刀具以及治具类交换等的作业称为内段取.(⇔ 外段取:77页)(⇒ 段取更换时间:89页)AB 制御工程間あるいは工程内の標準手持ち量が、常に一定量に保持されるように、各搬送機の、動いてもよい条件及び、工程から製品を搬出できる条件を、2個所(A 点、B 点)の製品の有無により制御する仕組みをいう。
6-段取り时间短缩の取り组み
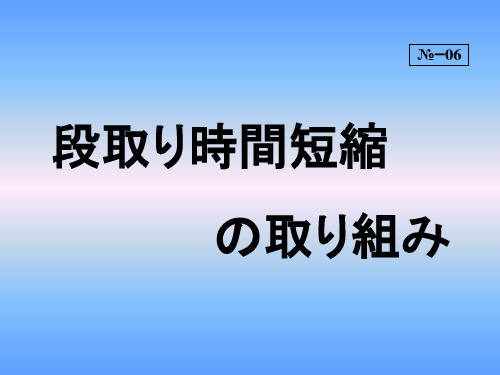
作業分類
内段 調整 外段
20“ 20“ 3‘10“ 10“ 1‘10“ 10“ 1‘30“ 30“ 1‘05“ 05“ 0‘50“ 50“ 2‘15“ 15“ 1‘55“ 55“ 0‘40“ 40“ 3‘45“ 45“
個別
1 2 3 4 5 6 7 8 9 10 11 12
型の取り付け部をエアーで払う をエアーで払 段取り用工具を 段取り用工具を運んでくる 型の取り付けネジを外す けネジを外 クレーンを持 クレーンを持ってくる ワイヤーを持ってきて掛ける ワイヤーを持ってきて掛 型を吊り上げる 型置き 型置き場に置く 次の仕掛け型にワイヤーを掛ける 仕掛け にワイヤーを掛 型を吊り上げる マシーンに型 マシーンに型を置く ワイヤーを外 ワイヤーを外しかたずける 型を仮り締めする
資料№ 06-6
段取り手順の要素作業を 段取り手順の要素作業を記録
手順 要 素 作 業 時 間
読み
20“ 20“ 3‘30“ 30“ 4‘40“ 40“ 6‘10“ 10“ 7‘15“ 15“ 8‘05“ 05“ 10‘20“ 10‘20“ 12‘15“ 12‘15“ 12‘55“ 12‘55“ 16‘40“ 16‘40“ 17‘30“ 17‘30“
資料№ 06-4
段取り時間の短縮、 段取り時間の短縮、 取り組み順序2 順序2
① 動作改善(分担化含む) 動作改善(分担化含む 治具等の ② 治具等の構造改善 ③ 設備改善 改善費用の 改善費用の捻出要
資料№ 06-5
段替え短縮の 段替え短縮の進め方
何処から 何処までが段取りか から、 までが段取りか決 ① 何処から、何処までが段取りか決める 段取り手順の要素作業を記録(VTR撮影可) (VTR撮影可 ② 段取り手順の要素作業を記録(VTR撮影可) 動作経路図の ③ 動作経路図の作成 要素作業毎の ④ 要素作業毎の時間測定 要素作業の分類(内段/外段) ⑤ 要素作業の分類(内段/外段) 改善案の ⑥ 改善案の作成 改善案の ⑦ 改善案の実施 実施した した後 確認する ⑧ 実施した後を確認する
トヨタ生产方式と継続的改善活动

「なぜ」を5回繰り返す 問題の真因を探る
1.なぜ機械が止まったか⇒過剰負荷でヒューズが切れる 2.なぜ過剰負荷がかかったのか⇒軸受の潤滑が悪い ⇒ 3.なぜ潤滑が悪くなったのか⇒潤滑ポンプの性能落ちている 4.なぜ潤滑ポンプの性能が落ちてるのか ⇒ポンプの軸が磨耗して機能が落ちている 5.なぜ磨耗したのか⇒濾過器がないので鉄粉が混入した
8
標準作業表
作業内容 タイヤ置き場に向かう タイヤを持ち上げる タイヤをラインに移動させる ・・・・・ 所要時間(秒) 3 4 10 8
合計
55
9
トヨタ生産方式の二本柱
1.ジャスト・イン・タイム (JIT) 必要な時に必要な物を必要な量だけ作る 2.自働化 ①欠陥品(故障)が出ると自働的に機械 (作業)が止まること ②一つの作業が完了すると機械が止まる こと
10
ジャスト・イン・タイム 市場の変化に応じて生産すること
市場の多様化や変動にフレキシブルに対応し、 売れるものを売れるだけ売れる速度で作るこ とによって、つくりすぎのムダ等を徹底的に排 除すること 平準化が大前提
11
ジャストインタイム実現のために
後工程引き取り方式(Pullシステム) ・最終工程(組立工程)に生産計画を指 示し、後工程(組立工程)が使った分だ け前工程(部品工程)に引き取りに行き、 前工程(部品工程)は引き取られた分だ け生産する
1 7 2 8 3 9 4 5 6 10 11 12
16
トヨタ生産方式の二本柱
2.自働化 ②一つの作業が完了すると自働的に機械) が止まる (1)人の仕事と機械の仕事の分離が可能
手作業(据付等) 見張り? 手作業(取り外し等)
(2)一人の作業者による多台持ちが可能 (3)少人化(省人化)が可能
第1回 方法改善は 「4つのポイント」を见逃さないことがコツ

実践!インダストリアル・エンジニアリング(IE)~方法改善の技術(1)方法改善は「4つのポイント」を見逃さないことがコツ!!1:IEにおける「方法改善」とは?IE(インダストリアル・エンジニアリング:Industrial Engineering)とは何かの説明にはいろいろとありますが、おおむね、「生産の3要素である「人(Man)」「設備(Machine)」「モノ・材料(Material)」を効果的に統合し、最良の「Q(Quality)」「C (Cost)」「D(Delivery)」いわゆる「良いモノを、安く早く作る」を獲得するために、工学的な手法を利用し最適な生産システムの設計・改善・構築に関する技術・技法の体系」と定義付けられるのではないでしょうか。
「作業測定の技術」と「方法改善の技術」は、工場や職場の(科学的)管理には欠かせない技術IEは、テーラー(Frederick Winslow Taylor:1856-1915)の時間研究(Time St udy)の結果から得られた「作業測定の技術(Work Measurement)」と、ギルブレス(Frank Bunker Gilbreth:1868-1924)の動作研究(Motion Study)の結果から得られた「方法改善の技術(Method Engineering/Study)」が、IEの二大柱といえますが、この「作業測定の技術」と「方法改善の技術」は、それぞれが単独で活用される技術ではなく、相互に関連性を持たせながら作業改善を進めていくべきものです。
例えば、標準作業や標準時間の設定がなければ、生産システムが立案できないばかりか、生産の負荷量や余力の把握もできません。
このようなことから、「作業測定の技術」と「方法改善の技術」は、工場や職場の(科学的)管理には欠かせない技術であるといえます。
「方法改善の技術」は、改善そのものの技術ですが、「作業測定の技術」は、工場や職場の(科学的)管理のための基準設定の技術であると同時に、その改善における効果量の測定技術でもあるわけです。
改善(日语解释 kaizen)

改善出典: フリー百科事典『ウィキペディア(Wikipedia)』移動: ナビゲーション, 検索改善(かいぜん)の一般的意味は悪い状態を改めて善くすることであるが、製造業で用いられる用語としての改善は、工場の作業者が中心となって行うボトムアップ活動のことである。
概要[編集]改善活動の内容は生産設備の改造や工具の新作、ポカヨケの製作など業務効率の向上や作業安全性の確保、品質不具合防止など生産に関わる範囲全てにわたる。
改善は上からの命令で実行するのではなく作業者が自分で知恵を出して変えていく事が大きな特徴で、企業側はQCサークルなどの形で活動を支援することが多い。
また、改善は一度行ったら終わりではなく次々と改善を行っていく持続性、継続性が重視されている。
QCサークルの活動と相まって、日本の製造業では多くの企業で行われている。
実際の事例トヨタ生産方式では、改善は基本概念の一つに数えられる。
例えば、下記のような事例が挙げられ、トヨタ生産方式の様々なエピソードに深く関わっている。
∙改善活動により、作業者の知恵を生産設備に織り込むことで、同じ設備を使う他社に差をつける。
∙不足するものをすぐに買うのではなく、自分達で製作・改造することで、投資を抑制することを狙ったりする。
カイゼン[編集]改善は、今日ではしばしカイゼンと表現される。
これは、一般的な改善の意味と区別するためであったり、海外でも通用する言葉であることを強調するために意図的に用いられている。
日本の製造業が海外へ工場を展開した際に、日本から派遣された作業トレーナーが現地従業員に教えたり、また1980年代にMITが中心になって行った日本の製造業の強さの研究、などを通じて日本の製造業の重要な要素の一つとして海外でも広まり、結果Kaizenとして世界でも通用する言葉となった。
問題点[編集]改善の主な問題点として以下の項目が指摘されている。
1.近年では、過度の競争から生産現場の諸条件を考慮せず、またボトムアップ活動であるべき改善を安易にトップダウンで押し付けようとする言葉だけの「カイゼン」が乱用される傾向が見られ、これが現場従事者にとっては逆に「改悪」と化す例が続出し、結果としてトラブルの温床と化しているとの批判もある。
金型迅速交换(シングル段取)

金型迅速交換(シングル段取)2008-03-30来源:网络【大中小】评论:1条收藏自動車作業のコストを低減と、生産車種の多様化が進み、溶接作業、塗装作業、組立作業などの合理化、省力化が図られ、当然プレス作業、鋳造作業、ダイカスト作業および樹脂成型作業など、金型を用いて製品を作り出す工程の合理化が検討された。
この中で、一つの工程の作業サイクルは、タイムスタディなどのIE技術で急速に合理化が進んだ。
反面、作業の段取には、かなり多くの時間を費していた。
.一方、コスト低減から不要の在庫は一斉持たないようにして、必要なものを必要なだけ作ろうという考え方が生まれ、生産工程の合理化はもちろん、段取作業を合理化しようという試みがなされた。
これがいわゆる看板方式の生産体制がら生まれたシングル段取である。
シングル段取りの名称が示すように、一台、つまりす数分以内に段取作業を尾和得ようとする考えである。
ダイカスト作業において、この段取作業は、金型交換作業であり、一般に次のような順序で行われている。
鋳造作業終る→金型掃除→タイバーナットを緩める→金型取り外し(押出しロッドの段取はすし、コアプラ取り外し。
冷却ホース等の取り外し、金型固定金具の取り外し)→金型搬出→スリープなどの交換→次に鋳造する金型搬入→金型取付け(締付け金具、コアプラ取付け、押出しロッドの締付け、冷却ホース等の取付け)→ダイハイト調整→ダイバーナット締付け→金型予熱→鋳造開始これらの作業は、必ずしも金型交換作業のときでなければできないものばかりではない、金型交換作業に際し。
事前に準備できない作業を内段取という。
金型交換作業の中で、この外段取りの部分の割合を増し、同時に内段取の合理化をすれば、大巾に短縮されるわけで、そのために次の事柄を工夫、改善すべきである。
1. 金型の大きさの標準化(外形、スリープの規格化、押出しストロークの標準化など)2. 金型搬出入装置の開発(コロコンベア、金型迅速交換装置等)3. 金型締付け金具、金具の工夫、改善(ウンタッチで締付けなど)4. 金型の押出し盤と機械の押出し機構の接合装置の工夫、改善5. 冷却ホースの取付け、取り外しの方法の工夫、改善<集中冷却装置、クィックガプラなど)6. 金型の予熱装置の工夫(外段取で行う)7. 工場の整理、整頓译文:模具快速交换(快速调试)汽车产业的成本降低,生产车种的多样化的进行,焊接作业,喷漆作业,组装作业的合理化,省力化在被安排着。
元桥一之 2009 IT イノベーションと経済成长:マクロレベル生产性におけるムーアの法则の重要性
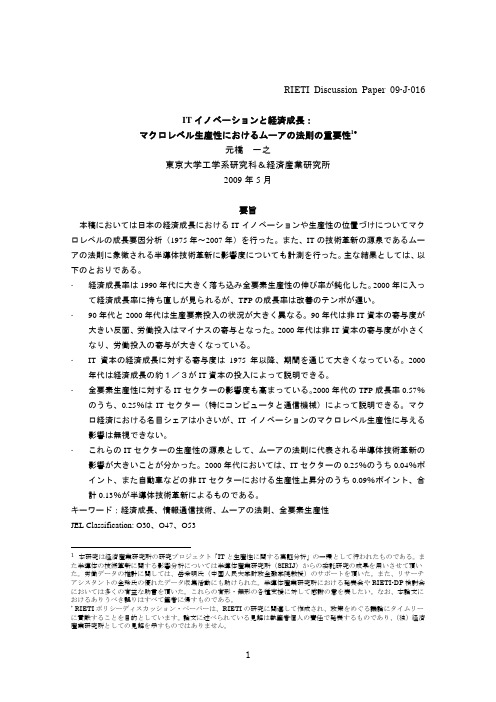
RIETI Discussion Paper 09-J-016ITイノベーションと経済成長:マクロレベル生産性におけるムーアの法則の重要性1∗元橋 一之東京大学工学系研究科&経済産業研究所2009年5月要旨本稿においては日本の経済成長におけるITイノベーションや生産性の位置づけについてマクロレベルの成長要因分析(1975年~2007年)を行った。
また、ITの技術革新の源泉であるムーアの法則に象徴される半導体技術革新に影響度についても計測を行った。
主な結果としては、以下のとおりである。
x経済成長率は1990年代に大きく落ち込み全要素生産性の伸び率が鈍化した。
2000年に入って経済成長率に持ち直しが見られるが、TFPの成長率は改善のテンポが遅い。
x90年代と2000年代は生産要素投入の状況が大きく異なる。
90年代は非IT資本の寄与度が大きい反面、労働投入はマイナスの寄与となった。
2000年代は非IT資本の寄与度が小さくなり、労働投入の寄与が大きくなっている。
x IT資本の経済成長に対する寄与度は1975年以降、期間を通じて大きくなっている。
2000年代は経済成長の約1/3がIT資本の投入によって説明できる。
x全要素生産性に対するITセクターの影響度も高まっている。
2000年代のTFP成長率0.57%のうち、0.25%はITセクター(特にコンピュータと通信機械)によって説明できる。
マクロ経済における名目シェアは小さいが、ITイノベーションのマクロレベル生産性に与える影響は無視できない。
xこれらのITセクターの生産性の源泉として、ムーアの法則に代表される半導体技術革新の影響が大きいことが分かった。
2000年代においては、ITセクターの0.25%のうち0.04%ポイント、また自動車などの非ITセクターにおける生産性上昇分のうち0.09%ポイント、合計0.13%が半導体技術革新によるものである。
キーワード:経済成長、情報通信技術、ムーアの法則、全要素生産性JEL Classification: O30、O47、O531本研究は経済産業研究所の研究プロジェクト「ITと生産性に関する実証分析」の一環として行われたものである。
- 1、下载文档前请自行甄别文档内容的完整性,平台不提供额外的编辑、内容补充、找答案等附加服务。
- 2、"仅部分预览"的文档,不可在线预览部分如存在完整性等问题,可反馈申请退款(可完整预览的文档不适用该条件!)。
- 3、如文档侵犯您的权益,请联系客服反馈,我们会尽快为您处理(人工客服工作时间:9:00-18:30)。
什么是段取?
段取定义
GO
A部品生産
段取中
B部品生産
为什么这样定义
段取是指A部品生産完后B部品品质确认后, 判定为良品时开始生产。顺间由于段取产生 的时间称为停止时间
部品产生付加価値是在 设备稼动生产的时候
段取時間短縮必要性
为什么要改善段取时间?
《段取時間短縮必要性!》 不进行段取操作最好、但是现状多款部品都是小批量生产。 因此为了对应生产,在需求时间内安排对应生产,这样一 来,增加了段取次数。 也就是说、现状无法对应段取时间时,都是通过扩大生产 批量来对应。 过剩生产造成浪费! 必需要减少段取時間,实现需求数量在需求时间段生产、 必需短缩改善段取時間!
开始调查
段取阶段3
1)分析基准
①作业分析中最小限的項目 作業項目・作業時間・設備吨数・使用材料・换模前的作业内容 ②作業項目分類 上模下模・調整・清扫・品質(试生产) ③区分作业(原本要段取几处) 前段取・内段取・後段取 ④理清問題点。 ※每个作业中的问题点不仅一个,有很多个问题点。 ⑤改善検討。 ⑥设定納期。 短期→2周以内 中期→1个月程度 長期→1个月以上 ⑦选定担当者。
段取分为4大类
分析前注意3
≪区分作业(原本段取有几处)≫ 前段取⇒段取实施前的准备作业中,不用停止设备也能完成的作业 内段取⇒设备不停机就无法完成的作业。 段取改善、既短缩作业时间。 後段取⇒生产开始时才能作的工作、后续清扫及设备周边的整理整頓等。 ≪理清问题点≫ ①现在的作业、不进行内段取就无法作业吗? ②在设备的3m以内进行段取作业吗? ③工具及设备周边、有进行整理整頓吗? ④现在的作业过程中、有浪费的作业环节吗?(7个浪费) 例:去取(歩行及搬运)・手持・位置移动(調整)・异常処理等 ≪改善検討≫ 请转换一下思维方式。先不要想那是理由当然的作业。在成员当中选取 没有做过段取作业的人员,一同参与。原因是因为专业团队的成员、大家 提出的好的方案后多数都会被否定。 为了能够实现各种各样的好方案、最好是招集各个部门的成员一同检讨。 ≪納期≫ 短期⇒2周左右能实施的項目(可以自己实现) 中期⇒一个月程度完成项目(需要其它部支援) 長期⇒一个月以上完成项目(需要客户许可及要投入设备)
分析开始
之前作成检查确认一览表!
分析前注意1
調査項目详细步骤説明
≪作业分析中最小限的項目≫
作业項目⇒1不是对每个作业内容进行分析,而是分析作业流程并记录(动作内容是什么进行分析) 1動作 :①拿螺丝扳手。②拧紧螺丝。③扳手放置台車上 作业流程:①取扳手、拧螺丝、扳手放回台车
作业時間⇒1、2秒误差不用太在意、但是开始多种作业时,要明确算出什么操作用了多久时间。 设备吨数⇒相同设备进行对比 使用材料⇒条件设定由于材料关系不同吗、或材料条件设定不同、以后的生产计划中在检讨减少 条件设定方法时在使用。特殊模具要注意 换模前的作业内容⇒段取根据换模前的操作,段取作业内容及段取时间会不同。
段取時間実况調査
実况調査必要性
为什么要调查?
稼动设备有几台? 每月段取次数是多少? 毎次段取的时间有多久?
自身的技能水平、及対象部品目标设定 方面都会有帮助噢!
調査注意点 ①段取时间不平均!(MAX・MIN・获取平均) ②不需要撑握每台设备的时间,撑握各部品及各工程時間。 同时撑握换模前的部品! ③判断分析段取过程时、要认真仔细的记录! ※段取人員・工程名(场所)・設備吨数・使用材料等
段取阶段1
1)段取成员編成
段取不是任何人都能操作的工作。在段取时要 考虑设备操作,换模时的操作安全。 也就是说、有段取经验的人员最好!PR⇒各設備一台1名 MO⇒設備一台2名程度。
2)改善対象部品及设备选定
并不能说哪款部品都可以。要结合确认改善实际 状况、生产数量少的部品确认时间最长。 另外、小设备中的一些改善项目不能水平展开大 设备上。(大的可以展开到小到) 加入像这样的问题进行分析后选定。
如果不注意!
分析前注意2
≪作业項目分类≫ 安装取下⇒作业项目为取下A部品模具、安装B部品模具。 这项操作在段取作业中要调整到最低限度。 調整作业⇒整模具位置、传感器位置调整等作业。 清扫作业⇒模具放置位置、整理、清洗模具等作业。 品質确认⇒确认设定条件条件、模具状态、规格尺寸等是否达到要求 、要试打几模进行确认作业。(量产前的品质确认作业)
不能忘记担当者
能先改善的先实施
段取時間短縮方面
段取时间短縮是由各种各样细微的改善积累成的。 因此尽量叫多数成员参与并提出好方案。 但是、方案提出后先不要否定方案。 方案在开展实现活动时,不能判定的事找其它部门的人员共同 商量后再决定。能实现的要实现、不能实施的进行修改后再实施。 段取改善、不仅是内段取、前段取及後段取都要改善。 最后规范并实现标准化作业,让任何人都能够在段取时间内完成。
段取阶段2
段取时间实际调查
调查现状的作业基准是由谁来担当段取作业。 調査同时、请用DV录制片段。 理由 ①每个作业基准的时间能容易算出。 ②调查时的作业基准能被大家多次利用。 ③改善前・改善後的作业基准可以进行对比
DV录制的注意事项
①作业员区分DV录制。(PR固定一台!) ②2台以上的DV录制时、撮影開始時刻が判る様に、 同じ時計の時刻を撮影しておき、撮影が 開始されたら段取りが 完了するまで、停止させない。
内段取⇒不停机无法操作 外段取⇒机械稼动中也可操作(前・後段取)