塑料异型材双色共挤出技术
浅议PVC双色共挤异型材挤出技术(精)

成的三元聚合物,也可以作为双色共挤型材的外层。&&树脂与$’(共挤生产的彩色塑料型材有较高耐候性和丰富稳定的色彩,但原材料的价格比较昂贵。&&具有优良的低温抗冲击性能,在1
2*3仍能保持4.5的常温抗冲击,也正是由于&&的抗低温性很强,材质较软,使得&&在加工及
目前,在市场上彩色门窗的生产较为流行的三种生产方式主要是#双色共挤、覆膜和静电喷涂。双色共挤的表面共挤层按不同材质有:$%%&、
加工过程中的磕碰、切割都会造成大块裂纹和崩角,从而大量产生废品,增加成本。另外,$’(1
$%%&双色共挤型材按白色型材标准检测时,此种
型材易出现分层现象,在使用过程中分层现象亦不可避免,大大影响共挤型材的使用寿命。
!%&—!%&粉料双色共挤型材从近几年的应用
来看,无论从质量还是从耐候性上均取得较好的效果。另外,型材主体与共挤层为同一种原料,配方类似,又同为粉料,加工起来非常容易,而且成本较低,有很大的市场竞争力,得到了用户的广泛接受。
基于上述情况,久利公司于二十世纪末期开发出了!%&—!%&粉料双色共挤型材,上述问题迎刃而解。生产共挤型材需用两台挤出机:一台为生产普通型材的螺杆直径较大的双螺杆挤出机(包括定型及牵引等附属设备),用于挤共挤型材的主体;另一台为螺杆直径较小的双螺杆挤出机,用于挤共挤型材的彩色表面。模具可以购置新模具或改造现有模具。通常保留原单色型材模具,后加做机头或机头的一部分实现共挤彩色表面。共挤模具与原单色型材模具最大不同在于口模板上的共挤流道,共挤层材料由共挤辅机进入口模板上共挤流道,实现型材的彩色表面。不制作彩色表面时,共挤模具仍可恢复生产单色型材。
PVC型材挤出工艺
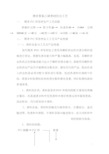
硬质聚氯乙烯型材挤出工艺一、硬质PVC异型材生产工艺流程原辅料过筛配方称量高速热混冷混过筛储料风送挤出定型牵引检验入库二、硬质PVC异型材加工工艺及产品性能(一)、混料设备与工艺及产品性能现代硬质PVC异型材加工使用双螺杆挤出机对混合粉料直接进行挤出,其塑化混合能力和产量大幅提高。
但是,双螺杆挤出机的正位移输送能力远大于螺杆的混合能力,直接用双螺杆挤出机挤出产品仍不能得到分散良好、塑化均匀的产品,因此在进入挤出机前必须对配方原料进行预混,包括热混和冷混两个阶段,使混合料取得较好的的预分散和塑化效果,同时取得较高的表观密度。
1、混料的目的:混料就是将PVC和助剂按配方要求经准确计量后,在高速混合机中经热混和冷混后使其达到半凝胶度高,流动性好,均匀密实的干混料。
2、混料设备:原材料的输送与储存部分、计量部分、盒式输送带,热混和冷混锅、干混料存储与输送部分、动力风机和中央控制部分组成。
3、混料的流程:PVC储罐 PVC秤群青辅料罐热混冷混缓冲罐筛分机辅料秤干混料罐微料罐中间仓4、混料工艺:混料过程中一方面是助剂的均匀分散,另一方面则是使树脂半凝胶化,凝胶化:PVC树脂即有颗粒细化,粒径均匀的形态变化,形成松散的粉料。
它的工艺控制点、加料量、冷却水温度、混料温度和时间等是控制干混料质量和产量的关键因素。
A、加料量与升温速度有一定的关系,即热混机中物料的热量只是搅拌叶片剪切和物料之间产生产热量。
所以投料量有一个的最佳值,如果加料量太多,物料翻腾阻力大影响升温速度,致使转速下降,给混料带来不利。
加料量少内部剪切热达不到,混料时间长直接影响混料效率。
经实验控制在70%左右为最佳。
B、混料温度:混料温度的影响干粉料性能的主要因素之一。
热混温度在一般为120℃左右冷混卸料温度一般低于40℃。
原料的含水量必须合乎优质品的要求,并应通过排气以除去物料中的水分。
C、冷却水温度:冷混缸的冷却水温度通常控制在13~15℃。
异型材挤出成型—异型材成型工艺(塑料挤出成型课件)
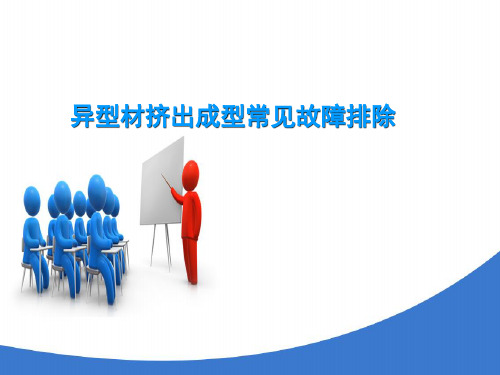
机头 压力 不足
定型段 物料 入机头 配方中 物料 分料筋 挤出 长度 未充分 料流 外润滑性 流动性 处熔体 速度 不足 汇流 偏低 过强 太差 温度偏低 太快
调整 物料 流量
增加 机头 压力
增加 定型段 长度
在模芯 支架后 设置 物料池
增大机头 入口处的 树脂流道
降低 混料的 外润滑性
采用 流动性好 的物料
冷却水对 型材冷却过快
关小冷却水
真空压力过大
定型模与冷却水箱 不在同一直线上
减小真空吸力
调整定型模与水箱 在同一水平直线上
异型材挤出成型工艺规程
异型材挤出工艺规程
1、开机前准备 检查水电供应、辅机是否正常,辅助工具
是否准备齐全,人员是否到位。
2、升温 升温并观察温度变化,打开螺杆油温,开启水阀,
(2)待停机料挤出后,依次关闭定型真空、风机,停止主 机螺杆,关闭螺杆油泵、冷却油泵。牵引机待料条牵引完 毕后关闭;
(3)后退定型台,松动模头紧固螺丝,松开连接法兰螺丝, 整体拆下模头,模具交付模具工清理;
(4)松开定型模底脚紧固丝,关闭主水阀,拔掉水、气管。 (5)关闭总电源,收拾工具,打扫现场卫生。 注:停机清理定型模执行(1)(2),清理模头还需执行
比如850r/min左右,低速排料, 转 速150r/min左右。
(4)混合温度:视冷热混合情况而定。 (5)混合时间:一般为5-15min。
二、异型材成型工艺控制
物料混合包括热混和冷混。
热混的目的是将物料中各个组
分颗粒达到最大程度的分布,使 物料升温,达到预塑化,如PVC 热混温度控制在115~120℃。
挥发物含量过多 产生分解气体
大
增加螺杆压缩比, 使排气完全
彩色PVC异型材简介
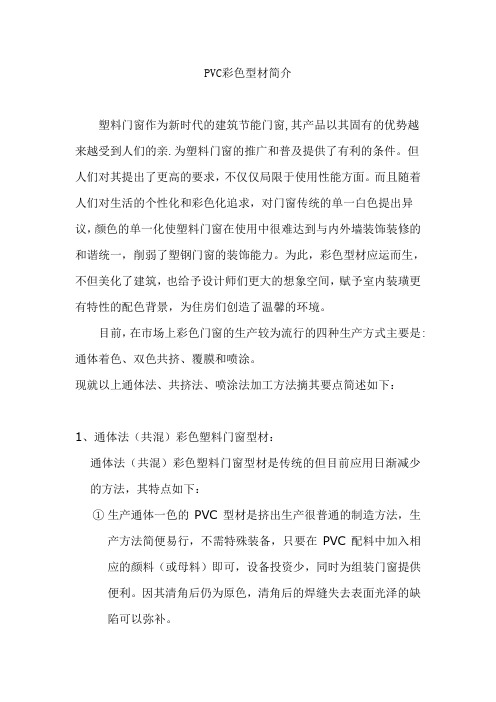
PVC彩色型材简介塑料门窗作为新时代的建筑节能门窗,其产品以其固有的优势越来越受到人们的亲.为塑料门窗的推广和普及提供了有利的条件。
但人们对其提出了更高的要求,不仅仅局限于使用性能方面。
而且随着人们对生活的个性化和彩色化追求,对门窗传统的单一白色提出异议,颜色的单一化使塑料门窗在使用中很难达到与内外墙装饰装修的和谐统一,削弱了塑钢门窗的装饰能力。
为此,彩色型材应运而生,不但美化了建筑,也给予设计师们更大的想象空间,赋予室内装璜更有特性的配色背景,为住房们创造了温馨的环境。
目前,在市场上彩色门窗的生产较为流行的四种生产方式主要是:通体着色、双色共挤、覆膜和喷涂。
现就以上通体法、共挤法、喷涂法加工方法摘其要点简述如下:1、通体法(共混)彩色塑料门窗型材:通体法(共混)彩色塑料门窗型材是传统的但目前应用日渐减少的方法,其特点如下:①生产通体一色的PVC型材是挤出生产很普通的制造方法,生产方法简便易行,不需特殊装备,只要在PVC配料中加入相应的颜料(或母料)即可,设备投资少,同时为组装门窗提供便利。
因其清角后仍为原色,清角后的焊缝失去表面光泽的缺陷可以弥补。
②颜料在高速搅拌时与各组分原材料一起加入,一般情况下混合效果能满足制品要求。
③型材及生产线产生的废料均可清净后回收使用。
不足之处:①最小产量受限制,是其最大的缺憾,因PVC型材组装门窗的特点,每一系列的门窗至少需要6种以上型材方能组装成成品,所以模具更换频繁使原材料、动力、人工费等消耗提高,成本提高,劳产率降低。
②混料系统、挤出成型系统清洗繁重、耗时、费工。
③制造彩色型材用颜料与PVC基材组分一起经过热历程与剪切作用,要求颜料不仅有优秀的热、光稳定性,还要耐HCL,因此对颜料的选用比较苛刻。
④在挤出机排气口加入色浆使PVC型材着色的方法,有些色浆的加入会影响制品的热变形温度及阻燃性。
⑤制造彩色型材特别是符合客户要求的颜色时,需要有相应的工艺技术人员,需要有调色装置或实验手段,企业才能有自主权。
关于共挤出工艺

共挤出工艺英文名称:coextrusion定义:使用数台挤出机向一个复合机头同时供给不同塑胶熔融料流、汇合复合成多层混合制品的挤出工艺。
共挤出工艺的几种类型:用多种方法可以制取多组分的复合材料制品,采用共挤出工艺是最简便易行的一种方法。
它已成为当代最先进的塑料成型加工方法之一。
高聚物共挤出工艺是一种使用数台挤出机分别供给不同的熔融料流,在一个复合机头内汇合共挤出得到多层复合制品的加工过程,团粒机。
它能够使多层具有不同特性的物料在挤出过程中彼此复合在一起,使制品兼有几种不同材料的优良特性,塑料造粒机,在特性上进行互补,从而得到特殊要求的性能和外观,如防氧和防湿的阻隔能力、着色性、保温性、热成型和热粘合能力,pet瓶片价格,及强度、刚度、硬度等机械性能。
这些具有综合性能的多层复合材料在许多领域中有极其广泛的应用价值。
此外,它可以大幅度的降低制品成本、简化流程、减少设备投资,复合过程不用溶剂、不产生三废物质。
因此共挤出技术被广泛用于复合薄膜、板材、管材、异型材和电线电缆的生产。
下面着重讨论近年来得到广泛应用的复合管材、复合薄膜、平膜和流延膜、PVC芯层发泡复合管、板、异型材共挤出技术。
复合管材共挤出铝塑复合管集塑料和金属优点为一体,具有无毒、平滑、耐腐蚀、质地轻、强度高、耐热性能好、脆化温度低、安装方便、外观大方、使用寿命长等优点,可用于冷热水及饮用水管道、地面及地下暖气管道、煤气管道、石油化学工业中的腐蚀液体和腐蚀气体的输送,压缩空气输送以及食品工业中饮料、酒和牛奶等液体的输送等,在近期内有可能逐步取代镀锌管、铜管、塑胶管。
在工业发达国家,铝塑复合管在管材中的占有率约为15%。
该项技术1974年由英国工程师Itzhak Barnoach提出申请专利,而后荷兰Kitech公司、德国Unicor公司和克劳勃公司等对管材结构、加工设备和制造技术等方面进行了改进,塑料机械,使其性能不断得到完善,在20世纪90年代初开始在欧洲和澳洲进行商品化应用。
硬PVC门窗异型材挤出成型工艺报告
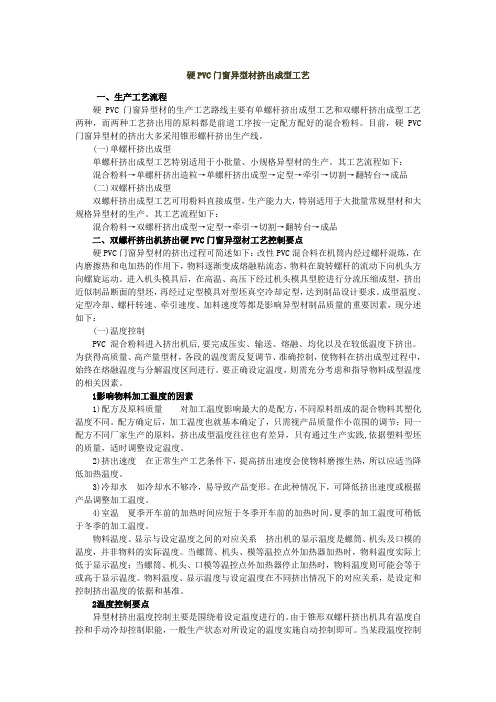
硬PVC门窗异型材挤出成型工艺一、生产工艺流程硬PVC门窗异型材的生产工艺路线主要有单螺杆挤出成型工艺和双螺杆挤出成型工艺两种,而两种工艺挤出用的原料都是前道工序按一定配方配好的混合粉料。
目前,硬PVC 门窗异型材的挤出大多采用锥形螺杆挤出生产线。
(一)单螺杆挤出成型单螺杆挤出成型工艺特别适用于小批量、小规格异型材的生产。
其工艺流程如下:混合粉料→单螺杆挤出造粒→单螺杆挤出成型→定型→牵引→切割→翻转台→成品(二)双螺杆挤出成型双螺杆挤出成型工艺可用粉料直接成型,生产能力大,特别适用于大批量常规型材和大规格异型材的生产。
其工艺流程如下:混合粉料→双螺杆挤出成型→定型→牵引→切割→翻转台→成品二、双螺杆挤出机挤出硬PVC门窗异型材工艺控制要点硬PVC门窗异型材的挤出过程可简述如下:改性PVC混合料在机筒内经过螺杆混炼,在内磨擦热和电加热的作用下,物料逐渐变成熔融粘流态,物料在旋转螺杆的流动下向机头方向螺旋运动。
进入机头模具后,在高温、高压下经过机头模具型腔进行分流压缩成型,挤出近似制品断面的型坯,再经过定型模具对型坯真空冷却定型,达到制品设计要求。
成型温度、定型冷却、螺杆转速、牵引速度、加料速度等都是影响异型材制品质量的重要因素,现分述如下:(一)温度控制PVC混合粉料进入挤出机后,要完成压实、输送、熔融、均化以及在较低温度下挤出。
为获得高质量、高产量型材,各段的温度需反复调节、准确控制,使物料在挤出成型过程中,始终在熔融温度与分解温度区间进行。
要正确设定温度,则需充分考虑和指导物料成型温度的相关因素。
1影响物料加工温度的因素1)配方及原料质量对加工温度影响最大的是配方,不同原料组成的混合物料其塑化温度不同。
配方确定后,加工温度也就基本确定了,只需视产品质量作小范围的调节;同一配方不同厂家生产的原料,挤出成型温度往往也有差异,只有通过生产实践,依据塑料型坯的质量,适时调整设定温度。
2)挤出速度在正常生产工艺条件下,提高挤出速度会使物料磨擦生热,所以应适当降低加热温度。
双层共挤挤出机原理
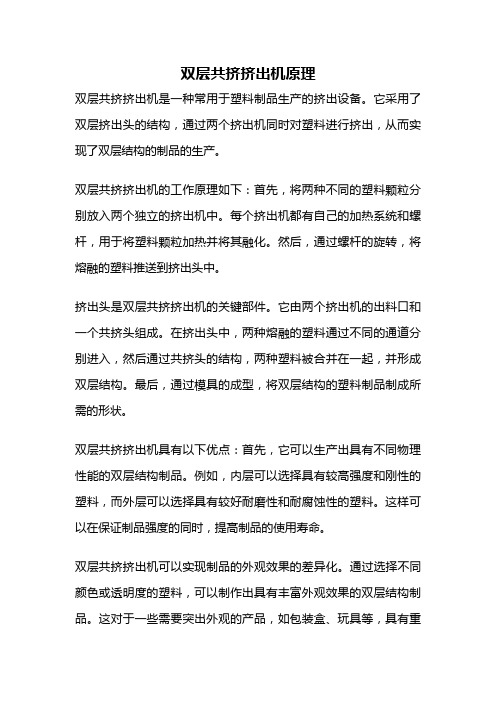
双层共挤挤出机原理双层共挤挤出机是一种常用于塑料制品生产的挤出设备。
它采用了双层挤出头的结构,通过两个挤出机同时对塑料进行挤出,从而实现了双层结构的制品的生产。
双层共挤挤出机的工作原理如下:首先,将两种不同的塑料颗粒分别放入两个独立的挤出机中。
每个挤出机都有自己的加热系统和螺杆,用于将塑料颗粒加热并将其融化。
然后,通过螺杆的旋转,将熔融的塑料推送到挤出头中。
挤出头是双层共挤挤出机的关键部件。
它由两个挤出机的出料口和一个共挤头组成。
在挤出头中,两种熔融的塑料通过不同的通道分别进入,然后通过共挤头的结构,两种塑料被合并在一起,并形成双层结构。
最后,通过模具的成型,将双层结构的塑料制品制成所需的形状。
双层共挤挤出机具有以下优点:首先,它可以生产出具有不同物理性能的双层结构制品。
例如,内层可以选择具有较高强度和刚性的塑料,而外层可以选择具有较好耐磨性和耐腐蚀性的塑料。
这样可以在保证制品强度的同时,提高制品的使用寿命。
双层共挤挤出机可以实现制品的外观效果的差异化。
通过选择不同颜色或透明度的塑料,可以制作出具有丰富外观效果的双层结构制品。
这对于一些需要突出外观的产品,如包装盒、玩具等,具有重要意义。
双层共挤挤出机还可以实现制品的功能差异化。
通过在内层和外层选择不同的塑料材料,可以实现制品在不同环境下的不同功能。
例如,在制作水管时,内层可以选择耐高温的塑料,而外层可以选择耐寒的塑料,从而使水管在不同季节都能正常使用。
双层共挤挤出机是一种高效、灵活的塑料制品生产设备。
它通过双层结构的制品生产,实现了制品物理性能、外观效果和功能的差异化。
在塑料制品行业中,双层共挤挤出机具有广泛的应用前景,并为制品的开发和创新提供了有力支持。
彩色共挤塑料异型材的工艺控制

彩色共挤塑料异型材的工艺控制PMMA与ASA双色共挤塑料异型材的工艺比单色塑料异型材工艺复杂,涉及面广,其中需要重点控制的是共挤机工艺温度,机头压力以及共挤机挤出速度与主机挤出、牵引速度的匹配与协调。
两种聚合物材料之间的黏度和流速不同,单流道与汇合流道中流动物料的速度分布曲线是不同的。
当两种熔融物汇入同一流道中时,其黏度必将对共挤界面流动性产生很大影响。
因共挤料与基料熔体黏度差异大,两种黏度不同的聚合物熔体在复合流道中流动时,黏度较低的聚合物熔体总有把黏度较高的聚合物熔体包覆在中间的趋势,低黏度熔体总是向高剪切区流动,会在共挤出界面上产生不稳定流动;表面共挤型材的共挤方式是在生产单色型材的模具的基础上,增加共挤流道,在单色型材的表面覆合一层只有0.2~0.3毫米厚度的彩色共挤料,仅是基料厚度的8.69%~13.6%左右。
两种不同厚度料层的流动属于不对称流动,随其体积流量增大,压力损失减少,高黏度熔体被低黏度熔体所包围并随黏度比的增大而加快;在不对称的流动中,两个熔体除共有流动界面外,另一界面均与模具壁接触、摩擦。
界面的流动状态不仅与熔体黏度、压力损失及流率有关,还与机头流道的长径比有关。
长径比越大,高黏度熔体被低黏度熔体包围的速度和范围越大。
两种不同黏度的聚合物在口模内的流动差异,则会影响共挤层厚度与两相界面之间的黏接强度。
鉴于不同聚合物熔体黏度不同,流动性是可以通过温度和压力调整的。
要想获得理想的共挤出制品,就要合理设定与控制挤出主机与共挤机的工艺温度、给料与挤出速度,并通过对共挤料流道进行合理设计,使高黏度熔体所受到的压力尽可能大一些,使共挤料和基料在不同温度和压力作用及塑化良好的前提下,熔体黏度及流动速率相互匹配,基本一致,从而利于控制好共挤层厚度,提高共挤制品界面黏接强度。
使用相对分子质量分布窄的聚合物,可以通过增加口模间隙和提高温度消除界面的不稳定性。
使用相对分子质量分布宽的聚合物时,减少界面不稳定性的惟一方法就是增加共挤层的厚度,改变层比或者更换共挤料。