装配流水线平衡率改善
流水线效率改善与方法

流水线平衡度计算公式
公式A: 【(各工序时间之和) / (瓶颈工序时间×工序数)】×100%
=【1157/(159× 10)】× 100% =72%
公式B: 【(各工序时间之平均) / 瓶颈工序时间】×100%
=【(1157/10)/159】× 100% =72%
流水线效率改善与方法
目录
第一部分:概念理解
1、生产平衡率 2、节拍
第二部分:流水线效率提升常用工具 第三部分:如何提高生产线效率
1、效率提升着眼点 2、效率改善实施步骤 3、如何评价效率改善得成果(P值得计算) 4、练习题 5、生产线效率提升思路演示模板
第一部分:基本概念
流水线平衡率 (LB) line balance
(2)改善后7月18日得P值就是多少?
P=63件除以12人再除以1、5小时 P后=63 ÷ (1、5*12)=3、5件/人·小时
(3)P值改善得幅度就是多少?
P提高了多少=(P后-P前)÷P前
P值提高了多少=(3、5-3、2) ÷3、2=0、093=9、3%
计算练习一:
假定座椅制造部成型3线直接投入人员固定为12人
依据总ST(标准时间)求出平均作业时间。 根据作业内容、作业时间、节拍(或者平均作业时间),重 新给每个作业者分配作业达到目标节拍(或者往平均作业时间 靠拢,效率越快越好)
二、改善浪费动作(针对被追赶得个别岗位)
1)改善瓶颈岗位得浪费动作(明显+细小)
2)改善每个岗位得浪费动作(明显→细小)
80
60
40
20
0
工序 1 2 3 4 5 6 7 8 9 10 11 12 13 14 15
【推荐】装配生产线平衡的改善
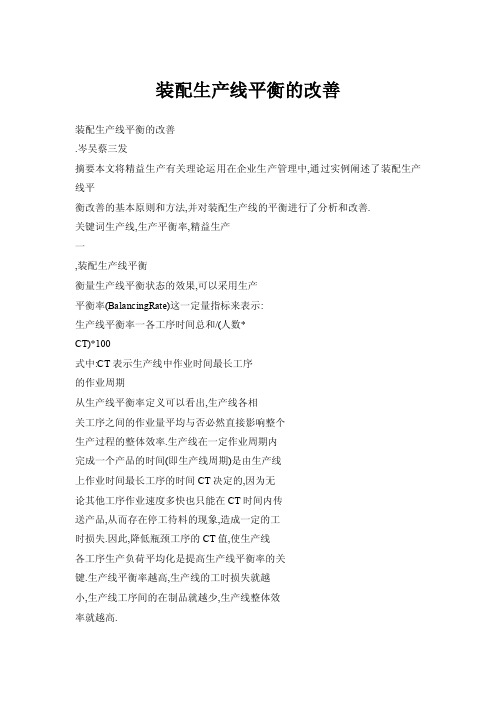
装配生产线平衡的改善装配生产线平衡的改善.岑吴蔡三发摘要本文将精益生产有关理论运用在企业生产管理中,通过实例阐述了装配生产线平衡改善的基本原则和方法,并对装配生产线的平衡进行了分析和改善.关键词生产线,生产平衡率,精益生产一,装配生产线平衡衡量生产线平衡状态的效果,可以采用生产平衡率(BalancingRate)这一定量指标来表示:生产线平衡率一各工序时间总和/(人数*CT)*100式中:CT表示生产线中作业时间最长工序的作业周期从生产线平衡率定义可以看出,生产线各相关工序之间的作业量平均与否必然直接影响整个生产过程的整体效率.生产线在一定作业周期内完成一个产品的时间(即生产线周期)是由生产线上作业时间最长工序的时间CT决定的,因为无论其他工序作业速度多快也只能在CT时间内传送产品,从而存在停工待料的现象,造成一定的工时损失.因此,降低瓶颈工序的CT值,使生产线各工序生产负荷平均化是提高生产线平衡率的关键.生产线平衡率越高,生产线的工时损失就越小,生产线工序间的在制品就越少,生产线整体效率就越高.装配线改善的基本原则和方法应该是:对瓶颈工序进行作业改善,如增加工装,工装自动化等;将瓶颈工序的作业内容分担给其它工序;增加作业人员,只要平衡率提高,人均产量也会提高, 单位产品成本会随之下降;合并相关工序,重新进行工序排布;分解作业时间较短的工序,将该工序拆分后并入其它工序;以顾客的需求CT为接近目标.装配生产线的平衡率分析和改善是装配型企业生产管理过程中的一项十分重要的工作,涉及到生产效率的提高,生产成本的降低,消除浪费, 准时化生产等生产指标的达成和不断改进. 二,精益生产精益生产的基本原理是:不断改进;消除对资源的浪费:协力工作;沟通.不断改进是精益生产的指导思想;消除浪费是精益生产的目标;协力工作和沟通是实现精益生产的保证.精益生产的主要内容包括工厂现场管理,新产品开发,与用户的关系,与供应厂家的关系等方面.对于现场管理,主要内容为如何通过看板系统来组织生产过程,实现准时化生产(JIT).准时化生产是指在顾客需要的时候,按顾客需要的量和产品品质,提供顾客需要的产品.准时化生产系统由一系列工具和方法构成:平衡生产周期;持续改进;一个流生产;单元生产;价值流分析;方法研究;拉动式生产;可视化管理;全面生产维护;快速换模.三,实例分析本文以某装配生产线(FIAT出风口装配线)为例,通过精益生产有关理论的运用,对该装配生产线的平衡进行分析和改进,取得了较好的效果.1.现状分析FIAT出风口装配线平面流程现状示意图如图1所示:园圈圈圉囡图圈圉曰图1装配线平面流程现状示意图FIAT出风口装配线一个组的作业密度及平作者简介:岑吴,同济大学经济与管理学院硕士研究生;蔡三发,同济大学经济与管理学院讲师.16《上海管理科学}2005年第5期衡分析如表1和图2所示:2.改善的对策和实施通过以上分析,可以提出该装配线改善的目标为:尽量接近顾客的CT一9.0秒;减少人员;提高平衡率;提高总产量和人均产量;降低生产成本.表1作业密度及平衡分析表工序号123456789装组装弹贴海工序名称装叶片装连杆装胶垫抹油打螺丝总装合件簧片绵垫作业5.693.505.184.505.144.867.386.983.50时间(秒)操作人数111111111CT(cycletime)一PT(pitchtime)一7.38s生产线平衡率一各工序时间总和/(人数*厘鲁平衡分析一厂1厂_]——..LIf.....—JLIrlIlr工序图2作业密度及平衡分析图因此,实施了如下工序作业改善对策表,见表2:3.改善前后对比经过改善,装配生产线平衡率得到了提高,见图3:表3有关数据也可以看出改善后和改善前对比的差距:CT)*100%一71.70%表2工序作业改善对策表NO工序作业时间改善措施PTS预置时间目的与效果1装叶片5.692装连杆3.5O合并为一道工序9.1减少一道工序3装组合件5.184装胶垫4.5O合并为一道工序9.6减少一道工序5装弹簧片5.14合并为一道工序9.8改变作业周期6贴海绵垫4.86增加作业内容,7抹油7.38将8的部分作业调整过来9.6平衡工序时间8打螺丝6.98与9合并8.26合并工序9总装3.5O取消省0.5人说明生产线由原来17人两组,改为15人=组,由此带来生产线平衡率,综合产能及人均产量上的提高厘蓝平衡分析姆图3改善后作业密度及平衡分析图表3改善前后的有关数据对比表项目改善前改善后变化量变化率人员数1715—2—12总产量870pcs/h98lpcs/h11113%人均产量51.265.414.228生产线平衡率71.7O%94.61%22.9%31.10%单件工时消耗70.3s55s——15s一21cycle7.389.80参考文献邱灿华,蔡三发,粟山.运作管理[M].上海;同济大学出版社,2004.刘胜军.精益生产方式现场IEEM].深圳:海天出版社,2002.周密.IE方法实战精解I-M].广州:广东经济出版社,2002.吴杰明.应用FOG方法提高生产线平衡率浅析EJ].上海电力学院,2004,6:49~53.ImprovementofAssemblyLineBalancingCenHaoCaiSanfaAbstract:Thispaperexplainstheapplicationsoflean productionknowledgeinenterpriseproductionmanagement, advancesthebasicprincipleandmethodofassemblylinehal—ancing,analysisandimprovementofoneassemblylinebal—ancing.Keywords:assemblyline;balancingrate;leanpro—duction17?。
装配线平衡问题分析

装配线平衡问题分析一、引言装配线平衡问题是指在生产流水线上,各个工序之间的任务分配不均衡,导致生产效率下降的情况。
这种问题在生产制造领域是非常常见的,解决装配线平衡问题对于提高生产效率和降低生产成本具有重要意义。
本文将从生产流水线的基本概念、装配线平衡的重要性和影响因素、以及常见的解决方法等方面进行分析和探讨。
二、生产流水线的基本概念生产流水线是指将生产过程按照一定的顺序划分为若干个工序,并将每个工序之间形成一个流水线的生产模式。
生产流水线的设计和优化可以大大提高生产效率和质量稳定性。
三、装配线平衡的重要性和影响因素装配线平衡是指在流水线上均衡地分配工作任务,以达到最大化生产效率的目标。
装配线平衡的重要性有以下几个方面:1. 提高生产效率:装配线平衡可以避免生产过程中的工序瓶颈和空闲,提高生产效率,减少生产周期。
2. 降低生产成本:通过合理的装配线平衡,可以避免不必要的等待和重复工作,减少能耗和人力成本。
3. 提高产品质量稳定性:均衡的装配线可以减少产品在不同工序间的拖延和等待,从而提高产品质量的稳定性和可控性。
装配线平衡受到以下几个主要因素的影响:1. 工序时间:不同工序的处理时间不同,可能会形成工序之间的瓶颈。
合理安排工序时间,可以减少瓶颈,提高生产效率。
2. 任务分配:将任务均衡地分配到各个工序中,避免某个工序任务过重或过轻,从而实现装配线的平衡。
3. 人力资源:充足的人力资源可以保证各个工序的顺利进行,缺乏人力资源会影响装配线平衡。
四、装配线平衡问题的解决方法为了解决装配线平衡问题,可以采取以下几种方法:1. 任务重分配:对不均衡的工序进行任务重分配,将任务均衡地分配到各个工序中。
这需要根据各个工序的处理能力和任务需求进行合理的评估和调整。
2. 工序优化:通过技术手段和工艺改进,缩短处理时间,提高工序的效率。
这可以通过引入自动化设备、改进工艺流程等方式来实现。
3. 人力资源管理:合理配置人力资源,确保各个工序有足够的人手,避免产生人力资源不足的问题。
装配流水线平衡率改善
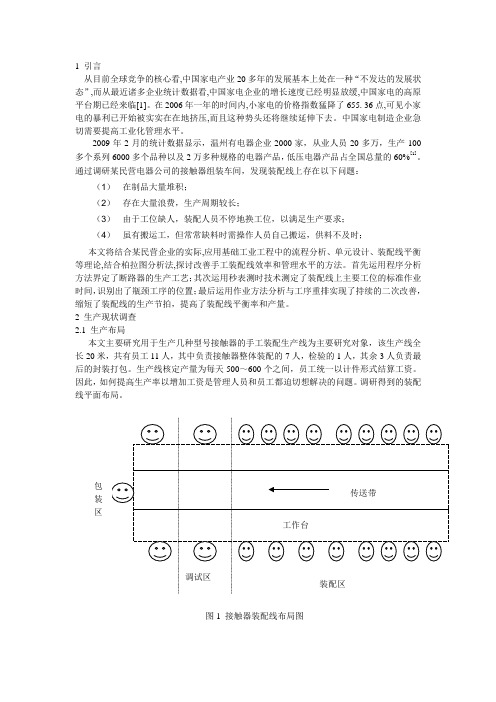
1 引言从目前全球竞争的核心看,中国家电产业20多年的发展基本上处在一种“不发达的发展状态”,而从最近诸多企业统计数据看,中国家电企业的增长速度已经明显放缓,中国家电的高原平台期已经来临[1]。
在2006年一年的时间内,小家电的价格指数猛降了655. 36点,可见小家电的暴利已开始被实实在在地挤压,而且这种势头还将继续延伸下去。
中国家电制造企业急切需要提高工业化管理水平。
2009年2月的统计数据显示,温州有电器企业2000家,从业人员20多万,生产100多个系列6000多个品种以及2万多种规格的电器产品,低压电器产品占全国总量的60%[1]。
通过调研某民营电器公司的接触器组装车间,发现装配线上存在以下问题:(1)在制品大量堆积;(2)存在大量浪费,生产周期较长;(3)由于工位缺人,装配人员不停地换工位,以满足生产要求;(4)虽有搬运工,但常常缺料时需操作人员自己搬运,供料不及时;本文将结合某民营企业的实际,应用基础工业工程中的流程分析、单元设计、装配线平衡等理论,结合柏拉图分析法,探讨改善手工装配线效率和管理水平的方法。
首先运用程序分析方法界定了断路器的生产工艺;其次运用秒表测时技术测定了装配线上主要工位的标准作业时间,识别出了瓶颈工序的位置;最后运用作业方法分析与工序重排实现了持续的二次改善,缩短了装配线的生产节拍,提高了装配线平衡率和产量。
2 生产现状调查2.1 生产布局本文主要研究用于生产几种型号接触器的手工装配生产线为主要研究对象,该生产线全长20米,共有员工11人,其中负责接触器整体装配的7人,检验的1人,其余3人负责最后的封装打包。
生产线核定产量为每天500~600个之间,员工统一以计件形式结算工资。
因此,如何提高生产率以增加工资是管理人员和员工都迫切想解决的问题。
调研得到的装配线平面布局。
图1 接触器装配线布局图2.2 生产工艺流程图为了对装配线进行改善,必须明确装配线上各个工位的作业单元,作业内容及作业的先后次序,于是运用工艺程序分析方法对断路器的装配工艺进行分析。
MOD法在装配流水线平衡中的应用
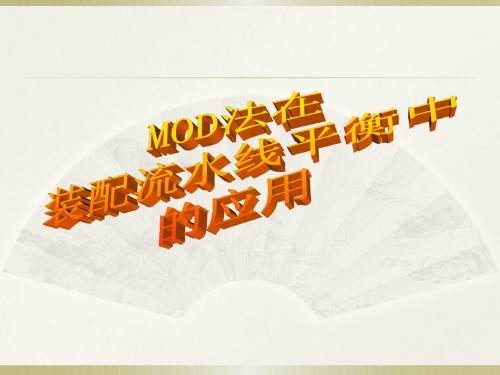
2.2 尽量放小动作幅度,减少M5、W5的使用 (1)No.15前道工序传来机体部件和前盖时应使两者水平 放置,可省去装配工人拿起前盖时的手臂伸直,M5动 作以M4代替;(2)No.29:装配好压缩机后可利用手臂 将其放到右后侧堆放区,无须转身走动,取消W5。实 际实验中,工人完全可以做到这点,但需要后续工序的 工人及时取走装配好的压缩机,以腾出空间放置继续装 配好的压缩机。
MOD法的应用
我公司装配线中的瓶颈工序之一是三大件装配。它纯粹 由人工操作完成,可操作性很大程度上取决于工人的熟 练程度。对此工序运用MOD法分析改进。首先,将三大 件工序分析细化为以下几个工步:1)定位后盖;2) 装密封垫;3)装导向杆;4)装阀板;5)装阀片;6) 装机体部件;7)放置轴封保护套;8)装配前盖;9) 取下轴封保护套;10)取6个螺栓;11)蘸油;12)装 配5个螺栓;13)取下导向杆并装最后一个螺栓;14) 拧2-3螺牙;15)放成品。
图1 工作流程图
3、MOD法 MOD法是预订时间标准(PTS)法的一种,它 不是通过直接观察和测定,而是利用预先 为各种动作制定的标准时间来确定操作所 需时间。传统的PTS法的优点在于不受作业 熟练度和评比者主观性的影响,相对客观 公正,但是也较耗时。MOD法则更为简练、 易于掌握,适合实际生产操作。
接下来,还需了解MOD法的动作分类及相应符号。 MOD法把操作动作分为5个移动动作(M1手指动作、 M2手腕动作、M3小臂动作、M4大臂动作、M5伸 直的手臂反覆多次的反射动作),6个终结动作 (G0碰接触、G1简单地抓、G3复杂地抓、P0简单 放置、P2较复杂放置、P5组装)及10个其他动作 (F3足踏板动作、W5走步动作、L1重量因素、E2 目视、R2校正、D3单纯地判断和反应、A4按下、 C4旋转动作、B17弯体动作、S30起身坐下)。代 码中第二个数字代表所需MOD单位时间值的多少, 例:M2代表手腕动作需要2个MOD时间。
装配生产线平衡问题的研究

目录摘要 (1)ABSTRACT (2)1 绪论 (3)1.1论文选题的背景及意义 (3)1.2国内外研究现状 (3)1.3研究思路及主要内容 (4)2 生产线平衡的基本原理 (5)2.1生产线平衡的目的和原则 (5)2.2生产线平衡要满足的约束条件 (5)2.3影响生产线平衡的主要因素 (5)2.3.1标准作业指导书的制定对生产线平衡的影响 (5)2.3.2 排线对生产线平衡的影响 (6)2.3.3员工责任心对生产线平衡的影响 (6)2.4生产线平衡问题的方法研究 (6)2.4.1程序分析 (6)2.4.2 操作分析 (7)2.4.3动作分析 (9)3 F公司整车流水线的情况概述 (10)3.1F公司概况 (10)3.2F公司装配生产线平衡的情况概述 (10)3.2.1F公司电动车生产流程现状 (10)3.2.2F公司电动车生产中存在的关键问题 (11)4 F公司整车流水线平衡的解决方案 (12)4.1F公司整车流水线平衡整改方案 (12)4.2整车线与吊挂方案对比 (14)5 结论 (16)致谢............................................................................................ 错误!未定义书签。
参考文献. (17)摘要在流水线生产模式下,如何提高生产线的整体效率,减少工序间的在制品,决定着企业设备、人员的利用率,并限制着生产线生产能力的提高。
目前,生产线平衡问题已被认为是生产流程设计及作业标准化过程中关键的一环。
制造业的生产多半是在进行细分化之后的多工序流水化连续作业生产线,此时由于分工作业,简化了作业难度,使作业熟练度提高了,从而提高了作业效率。
然而,经过了这样的作业细分化之后,各工序的作业时间在理论上、实践上都不能完全相同,这就势必存在工序间作业负荷不均衡的现象。
F公司在装配生产线中就经常遇到这种问题,作业负荷不平衡给F公司造成无谓的工时损失,还造成大量的工序堆积,严重时会造成生产线的中止。
生产线平衡改善(LOB)及生产线平衡率计算总结
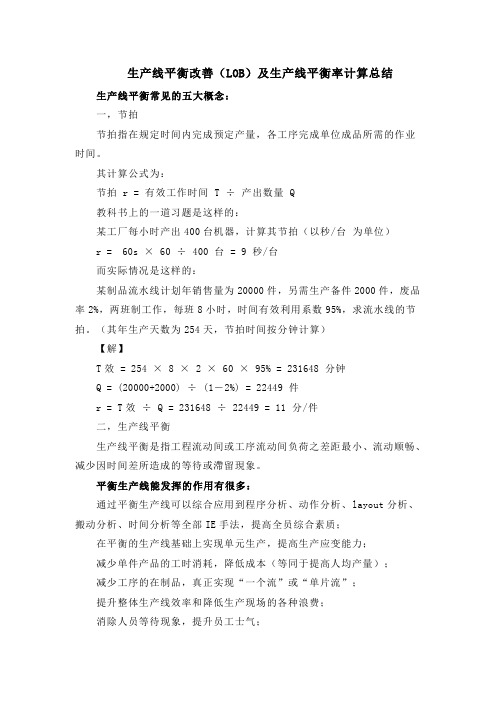
生产线平衡改善(LOB)及生产线平衡率计算总结生产线平衡常见的五大概念:一,节拍节拍指在规定时间内完成预定产量,各工序完成单位成品所需的作业时间。
其计算公式为:节拍 r = 有效工作时间 T ÷产出数量 Q教科书上的一道习题是这样的:某工厂每小时产出400台机器,计算其节拍(以秒/台为单位)r = 60s × 60 ÷ 400 台 = 9 秒/台而实际情况是这样的:某制品流水线计划年销售量为20000件,另需生产备件2000件,废品率2%,两班制工作,每班8小时,时间有效利用系数95%,求流水线的节拍。
(其年生产天数为254天,节拍时间按分钟计算)【解】T效 = 254 × 8 × 2 × 60 × 95% = 231648 分钟Q = (20000+2000) ÷ (1-2%) = 22449 件r = T效÷ Q = 231648 ÷ 22449 = 11 分/件二,生产线平衡生产线平衡是指工程流动间或工序流动间负荷之差距最小、流动顺畅、减少因时间差所造成的等待或滯留現象。
平衡生产线能发挥的作用有很多:通过平衡生产线可以综合应用到程序分析、动作分析、layout分析、搬动分析、时间分析等全部IE手法,提高全员综合素质;在平衡的生产线基础上实现单元生产,提高生产应变能力;减少单件产品的工时消耗,降低成本(等同于提高人均产量);减少工序的在制品,真正实现“一个流”或“单片流”;提升整体生产线效率和降低生产现场的各种浪费;消除人员等待现象,提升员工士气;减少工序间的在制品,减少现场场地的占用;可以稳定和提升产品品质。
它是生产流程设计与作业标准化中最重要的方法。
通过平衡生产,可以加深理解“一个流”生产模式及熟悉“单元化生产”的编制方法。
那么如何实现生产线平衡呢?保证各工序之间的先后顺序;组合的工序时间不能大于节拍;各工作地的作业时间应尽量接近或等于节拍;使工站数目尽量少。
装配现状分析与改善方案
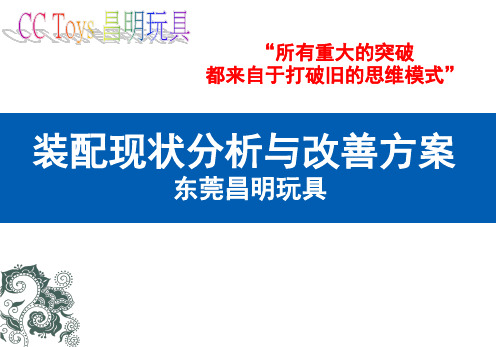
1、提升计划达成率(产品项目计划开始),
2、装配配料三天预警(提升配套率)
3、来料品质控制,增加临时检查工位(短期方案)
4、培训多技能工(焊线/打螺丝/喷胭脂/车位工);
5、快速换线(效率快速爬坡)
6、提升生产线平衡率
7、小拉化(少人化)
五、装配现状改善方案--外部因素
一、提升计划达成率
问题 分析
外发回货不及时 物料不配套 收发搬运等待 钉缝/装配衔接不稳定 生产工序不均衡 计划达成率低
结论 ➢ 等待浪费严重
Kk公仔 欠袋身
损失 ✓生产效率的损失
4
三、装配现状
案例2:装配流水线没有节拍、平衡率低 案例
没节拍
WIP堆 积严重
分析
问题 流水线没有节拍、平衡率 描述 低
问题 分析
1、按周四生产会议计划日期执行 2、配套生产 3、各车间对生产能力评估,满负荷须提前申
请外发/招工/增加设备/延长时间 4、客户意识,后工序就是前工序的客户
乱 流: 交叉 物流
层 流: 直线 物流
9
五、装配现状改善方案--外部因素 二、装配配料三天预警(提升配套率)
1、装配部安排三天领料计划 2、根据ERP系统打出套料单 3、领料数据记录 4、每日汇总欠料表 5、相关部门回复欠料跟进情况
品控部 注塑车间 装配车间 工程
总仓 喷油车间 车缝车间
* VOB:Voice Of Business (企业的需求与期望)
1、装配人工占 比重;
2、成品出货才 能实现价值,
是提升现金流 的重要部门。
三、装配现状
案例 1:装配欠料等待浪费严重,作业效率低 案例
39811 欠
- 1、下载文档前请自行甄别文档内容的完整性,平台不提供额外的编辑、内容补充、找答案等附加服务。
- 2、"仅部分预览"的文档,不可在线预览部分如存在完整性等问题,可反馈申请退款(可完整预览的文档不适用该条件!)。
- 3、如文档侵犯您的权益,请联系客服反馈,我们会尽快为您处理(人工客服工作时间:9:00-18:30)。
1 引言
从目前全球竞争的核心看,中国家电产业20多年的发展基本上处在一种“不发达的发展状态”,而从最近诸多企业统计数据看,中国家电企业的增长速度已经明显放缓,中国家电的高原平台期已经来临[1]。
在2006年一年的时间内,小家电的价格指数猛降了655. 36点,可见小家电的暴利已开始被实实在在地挤压,而且这种势头还将继续延伸下去。
中国家电制造企业急切需要提高工业化管理水平。
2009年2月的统计数据显示,温州有电器企业2000家,从业人员20多万,生产100多个系列6000多个品种以及2万多种规格的电器产品,低压电器产品占全国总量的60%[1]。
通过调研某民营电器公司的接触器组装车间,发现装配线上存在以下问题:(1)在制品大量堆积;
(2)存在大量浪费,生产周期较长;
(3)由于工位缺人,装配人员不停地换工位,以满足生产要求;
(4)虽有搬运工,但常常缺料时需操作人员自己搬运,供料不及时;
本文将结合某民营企业的实际,应用基础工业工程中的流程分析、单元设计、装配线平衡等理论,结合柏拉图分析法,探讨改善手工装配线效率和管理水平的方法。
首先运用程序分析方法界定了断路器的生产工艺;其次运用秒表测时技术测定了装配线上主要工位的标准作业时间,识别出了瓶颈工序的位置;最后运用作业方法分析与工序重排实现了持续的二次改善,缩短了装配线的生产节拍,提高了装配线平衡率和产量。
2 生产现状调查
2.1 生产布局
本文主要研究用于生产几种型号接触器的手工装配生产线为主要研究对象,该生产线全长20米,共有员工11人,其中负责接触器整体装配的7人,检验的1人,其余3人负责最后的封装打包。
生产线核定产量为每天500~600个之间,员工统一以计件形式结算工资。
因此,如何提高生产率以增加工资是管理人员和员工都迫切想解决的问题。
调研得到的装配线平面布局。
图1 接触器装配线布局图
2.2 生产工艺流程图
为了对装配线进行改善,必须明确装配线上各个工位的作业单元,作业内容及作业的先
后次序,于是运用工艺程序分析方法对断路器的装配工艺进行分析。
首先调研接触器的工艺流程程序,然后采用规范的作图方法绘制接触器的生产工艺程序图[2],如图2所示。
3 测定工序标准工时
3.1 确定观测次数
首先,在明确装配线上产品的生产工艺和相应的工位之后,进行作业分解,划分操作单元将各个工位的作业分解成可测量的作业单元,对作业单元按照秒表测时的规范方法进行测时。
采用连续秒表测时法首先对装配线的主要工位的作业试观测10次。
然后根据观测数据,运用d2值法计算每个作业单元的观测次数,取最大作业单元的观测次数进行观测。
文档来源为:从网络收集整理.word 版本可编辑.欢迎下载支持.
3文档来源为:从网络收集整理.word 版本可编辑.欢迎下载支持.
选观测次数最大值作为最后的观测次数,即应观测29次才能保证精度要求。
对每个工序按最大值进行测量,测完之后,对每组数据检察分析并剔除观测数值内的异常值。
若数值为σ3X ±之内则为正常值,之外为异常值。
在对异常值剔除后,运用剩余的合格数据分别求各单元观测时间的算术平均值,即为该单元的实际操作时间。
3.2 考虑评比系数和宽放率
采用平准化法确定平准系数,根据企业实际情况,经观察或计算得出各系数如下:
制定标准时间时,合理的确定宽放时间是很重要的,但又无法制定一种适合所有情况而被普遍接受的宽放时间,这里根据家有关资料对电器生产厂宽放率的研究,确定该线的总宽放率为10%。
根据观测数据,以及以上给出的评比系数和宽放率,确定工序的标准工时。
3.3 计算生产线平衡率
根据收集的生产线工序现状资料,计算装配线的平衡率。
由于包装的有3位操作人员,
因此该工位的工位工时=48.72/3=16.24s ,由于人员短缺,工位与工位之间经常出现作业交叉的情况,工位作业单元的划分比较复杂。
这里就按照人员配齐的情况进行计算。
平衡率%4.47
13*28.85
279.16100%*CT
*s T
i m
1
i i
==
=
∑=
式中,i T 指各个工位的工时,i s 指工位的个数,CT (Cycle Time) 指生产线上最长的作业时间。
根据计算得到的标准工时,绘制接触器装配作业工时柱状图。
接触器装配线作业工时柱状图(改善前)
5101520253035工位1工位2工位3工位4工位5工位6工位7工位8工位9工位10
工时 由上图,可以得到改善前的生产节拍为28.85S ,日产量=8x60x60/28.85=998只(按一天工作8小时计算)。
且各工位工时很不平衡,瓶颈工序的工时为28.85S ,远大于最短的工时15.6S 。
4 方法研究分析
运用5W1H 和ECRS ,对记录的现状进行全面分析,判断现有流程、作业、动作方法是否存在浪费、无效,并提出可能的改善方案。
分析提问过程:
1. 问能否把装辅助触头和打辅助触头螺钉合并?
能。
但问题是要经常性的换工具,所以最好是分开。
2.辅助触头和主触头能否一起组装?
不能。
因为还要在辅助触头上打上4个螺钉。
3.辅助触头能否和下辅助触头一起装配? 可以,但是装上之后由于未打螺钉容易掉。
4.电动螺丝刀为什么不吊着? 以前就是这样,就没改变过。
5.零件散乱的放在工作台上,为什么不放在工作盒内? 原来就是如此。
5 瓶颈工序分析
由瓶颈管理原则可知,瓶颈管理是平衡物流,不是平衡生产能力;瓶颈上1 h 的损失就是
整个系统的1 h损失,非瓶颈节省1 h无益于增加系统生产效率,非瓶颈的利用程度不是由其本身决定,而是由系统的瓶颈决定[4]。
因此若想提高生产效率,就应从该生产线的瓶颈入手,而造成生产线不平衡的因素正是瓶颈,因此要将总装车间最大浪费的因素———不平衡的浪费减少到最少[5]。
针对接触器装配线的平衡现状,提出改善方向为:①在满足装配线各工位作业顺序约束条件下,重排各工位的作业内容,实现各工位作业工时的基本一致,消除瓶颈,如可考虑将工位3的作业内容分担一些给工位1或者工位5;②对瓶颈工位进行作业方法改善,提高作业效率,缩短工时;③结合作业方法改善与工序重排,提高生产线平衡率。
流水线上工位3是装6个主触头和打6个M4x10的螺钉。
运用双手作业分析对该工位进行分析:。