装配线平衡计算
装配线平衡计算

3
9
7.8
20
20
71
7
装配线效率=
完成作业所需时间总和/(实际工作站总数*时间周期)
K= t /C 式中: K—最少工作站数; t —完成作业所需时间总量。 组织工作站需满足的条件:
保证各工序之间的先后顺序。 每个工作站的作业时间不能大于节拍。 每个工作站的作业时间应尽量相等和接近节拍。 应使工作站的数目最少。
工序同期化的措施有:
提高设备的生产效率。可以通过改装设备、改变设备型号同
按萨尔凡森提出在规定的装配线速度下使总的空闲时在规定的装配线速度下使总的空闲时间最少或使做一额定工作量的操作人数最少以使平衡延迟间最少或使做一额定工作量的操作人数最少以使平衡延迟最少最少的原则进行装配线平衡调整
1.流水线生产平衡
(1)生产线平衡的定义
生产线的平衡:要根据产品设定工作站数目,再将各工作
作业
紧前工序 说明
1
-
吊运
2
25
1
3
20
2
4
30
2
放入
5
25
3.4
安装
6
25
5
安装
7
12
6
8
14
6
栓螺母
பைடு நூலகம்
9
20
7.8
安装
作业时间(s) 50
装入 放入前
拧紧螺 拧紧螺
箱体定位 齿轮 浮动膜片 后膜片 后盖
前盖 栓螺母
连接盘
表 某部件装配顺序
解
1) 画出其先后次序图和先后次序矩阵表。 依照装配程序表的要求可以画出先后次序图。图中圆圈为作业, 箭头为操作顺序。
(2)生产周期的确定
装配线的平衡具体计算题-文档资料
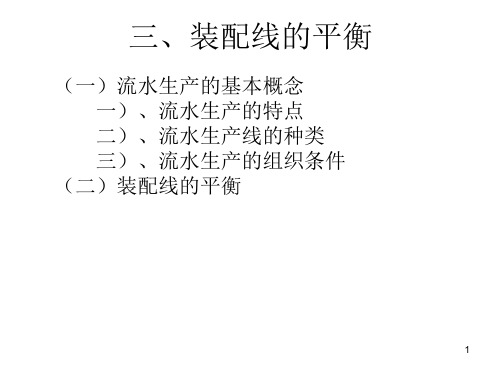
问题:如果市场要求每天生产100台电风扇,节 拍时间如何确定?
答案:
需要的节拍时间= 每天的生产时间 每天的生产量
= 420分钟/天 100台/每天
=4.2分钟/台
9
装配线平衡例-确定理论最少的工作站数量(2 )
问题:这个装配线,工作站的最少数目是多少?
答案:
理论最大工作站数目为Nt,则:
Nt= 工艺总时间 节拍时间
3
1
2
1.2
2
0.5
1
1
1
1
0
1.4
工作站 2
工作站 3
C (4.2-3.25)=.95
16
2
1.2
1
A
B
G
C
D
E
3.25
1
.5
工作站 1
A (4.2-2=2.2) B (2.2-1=1.2) G (1.2-1= .2)
空闲= .2
1.4 H
F 1
工艺 A C D B E F G H
后续工艺数 时间 (Mins)
7
装配线平衡例:
• 下面是一个电风扇装配工序:
工艺 A B C D E F G H
时间 (Mins) 工艺说明
2
安装座架
1.2 安装开关
3.25 装配电机罩
1
将电机罩装上座架
0.5
安装叶片
1
装配安全罩
1
装电缆
1.4
测试
总时间
11.35
前工艺
无
A
无
A, C D E B
F, G
8Hale Waihona Puke 装配线平衡例-确定节拍时间(1 )
汽车装配线平衡方法的

汽车装配线平衡方法汇报人:日期:•装配线平衡问题概述•装配线平衡问题的基本理论•遗传算法在装配线平衡问题中的目录应用•模拟退火算法在装配线平衡问题中的应用•基于粒子群优化算法的装配线平衡问题求解方法•实例分析目录01装配线平衡问题概述装配线是一种将零部件组装到一起的生产线,通常包括多个工作站和工序。
装配线的定义装配线具有高效、连续、重复性高的特点,能够快速大量地生产产品。
装配线的特点装配线的定义与特点装配线平衡问题的定义装配线平衡问题是指如何安排工作站和工序的顺序和时间,以使整个装配线的生产效率最高。
装配线平衡问题的重要性良好的装配线平衡可以提高生产效率、降低生产成本、减少工人的疲劳程度,提高产品质量。
装配线平衡问题的定义与重要性多目标性装配线平衡问题通常需要考虑多个目标,如生产效率、生产成本、工人的疲劳程度等,需要在这些目标之间进行权衡和折衷。
复杂性装配线平衡问题是一个复杂的组合优化问题,需要考虑多种因素,如工作站的数量、工序的顺序、工人的技能水平、设备的可用性等。
动态性装配线的生产情况是动态变化的,需要根据市场需求、产品类型、生产计划等因素进行调整,因此需要动态地进行装配线平衡。
装配线平衡问题的挑战02装配线平衡问题的基本理论装配线平衡问题的数学模型定义与公式01装配线平衡问题可以定义为在满足一系列约束条件下,寻找使得生产线总运行时间最短的工站排列组合方式。
数学模型通常涉及线性规划、整数规划、动态规划等。
变量与参数02数学模型中涉及的变量和参数包括工站数量、每个工站的工作时间、生产节拍、工作站的约束条件等。
适用范围与局限性03数学模型适用于求解具有明确数学表达形式的装配线平衡问题,但对于一些复杂问题可能需要采用更先进的求解方法。
优化目标装配线平衡问题的优化目标通常是最小化生产线的总运行时间,以提高生产效率。
此外,还可以考虑其他优化目标,如最小化生产线成本、提高产品质量等。
约束条件装配线平衡问题的约束条件包括工人的操作时间、设备的加工能力、生产计划的安排等。
装配线平衡问题
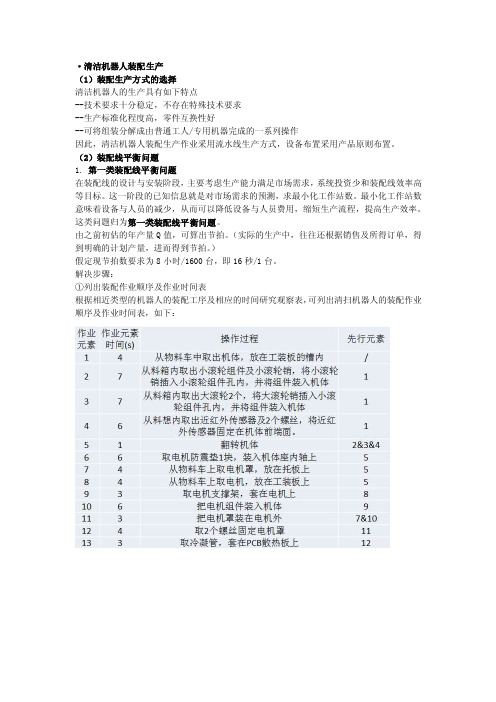
·清洁机器人装配生产(1)装配生产方式的选择清洁机器人的生产具有如下特点--技术要求十分稳定,不存在特殊技术要求--生产标准化程度高,零件互换性好--可将组装分解成由普通工人/专用机器完成的一系列操作因此,清洁机器人装配生产作业采用流水线生产方式,设备布置采用产品原则布置。
(2)装配线平衡问题1.第一类装配线平衡问题在装配线的设计与安装阶段,主要考虑生产能力满足市场需求,系统投资少和装配线效率高等目标。
这一阶段的已知信息就是对市场需求的预测,求最小化工作站数。
最小化工作站数意味着设备与人员的减少,从而可以降低设备与人员费用,缩短生产流程,提高生产效率。
这类问题归为第一类装配线平衡问题。
由之前初估的年产量Q值,可算出节拍。
(实际的生产中,往往还根据销售及所得订单,得到明确的计划产量,进而得到节拍。
)假定现节拍数要求为8小时/1600台,即16秒/1台。
解决步骤:①列出装配作业顺序及作业时间表根据相近类型的机器人的装配工序及相应的时间研究观察表,可列出清扫机器人的装配作业顺序及作业时间表,如下:②绘制装配优先顺序图③平衡搜索过程工作站分配原则——后续作业最多的优先安排;(第一规则)后续作业时间最长的优先安排;(第二规则)第一规则优于第二规则工位一:先分配作业元素1,1的作业时间4秒,节拍为16秒,剩余时间12秒。
作业元素1被分配后可安排的作业元素有2、3、4,作业时间分别为7秒、7秒、6秒。
其后续作业数相同,故先排2,在2被分配后剩余时间为12-7=5秒。
剩余时间不足,3、4无法分配到工位一。
至此工位一分配结束。
工位二:工位一分配完毕后,有资格被分配的作业元素有3、4。
剩余时间3秒,之后分配作业元素5,剩余时间2秒。
之后作业元素6、7、8有资格被分配,但剩余时间不足。
至此工位二分配结束。
工位三:作业元素6、7、8中,8的后续作业元素最多。
9的先行元素为8,因此先排8、9。
剩余时间16-4-3=9秒。
装配线平衡模型

§7综合举例
例 求解非线性方程组
其LINGO代码如下:
model:
xA2+yA2=2;
2*xA2+x+yA2+y=4;
end
计算的部分结果为
Feasible solution found at iteration: 0
Variable Value
X
Y
例 装配线平衡模型 一条装配线含有一系列的工作站, 在最终产品的加工过程中每个 工作站执行一种或几种特定的任务。装配线周期是指所有工作站完成分配给它们各自的任 务所化费时间中的最大值。平衡装配线的目标是为每个工作站分配加工任务,尽可能使每 个工作站执行相同数量的任务,其最终标准是装配线周期最短。不适当的平衡装配线将会 产生瓶颈——有较少任务的工作站将被迫等待其前面分配了较多任务的工作站。
这样我们把TSP转化成了一个混合整数线性规划问题。
显然,当城市个数较大(大于30)时,该混合整数线性规划问题的规模会很大,从而
给求解带来很大问题。TSP已被证明是NP难问题,目前还没有发现多项式时间的算法。对于小规模问题,我们求解这个混合整数线性规划问题的方式还是有效的。
TSP是 一个重要的组合优化问题,除了有直观的应用外,许多其它看似无联系的优化问 题也可转化为TSP例如:
钢铁工业是国家工业的基础之一,铁矿是钢铁工业的主要原料基地。许多现代化铁矿 是露天开采的,它的生产主要是由电动铲车(以下简称电铲)装车、电动轮自卸卡车(以 下简称卡车) 运输来完成。 提高这些大型设备的利用率是增加露天矿经济效益的首要任务。
工业工程中的装配线平衡与优化
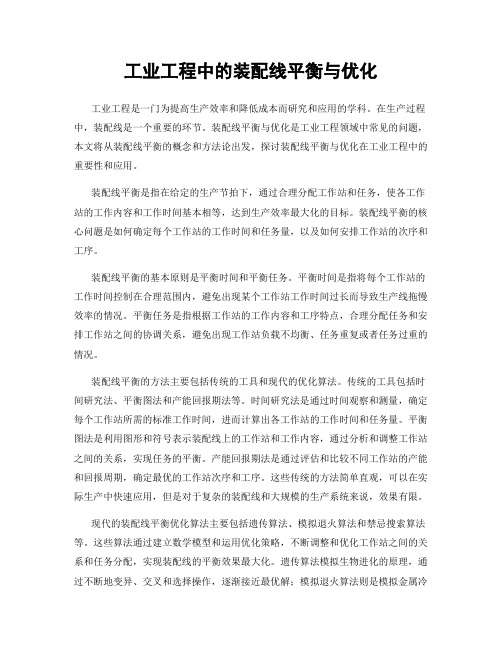
工业工程中的装配线平衡与优化工业工程是一门为提高生产效率和降低成本而研究和应用的学科。
在生产过程中,装配线是一个重要的环节。
装配线平衡与优化是工业工程领域中常见的问题,本文将从装配线平衡的概念和方法论出发,探讨装配线平衡与优化在工业工程中的重要性和应用。
装配线平衡是指在给定的生产节拍下,通过合理分配工作站和任务,使各工作站的工作内容和工作时间基本相等,达到生产效率最大化的目标。
装配线平衡的核心问题是如何确定每个工作站的工作时间和任务量,以及如何安排工作站的次序和工序。
装配线平衡的基本原则是平衡时间和平衡任务。
平衡时间是指将每个工作站的工作时间控制在合理范围内,避免出现某个工作站工作时间过长而导致生产线拖慢效率的情况。
平衡任务是指根据工作站的工作内容和工序特点,合理分配任务和安排工作站之间的协调关系,避免出现工作站负载不均衡、任务重复或者任务过重的情况。
装配线平衡的方法主要包括传统的工具和现代的优化算法。
传统的工具包括时间研究法、平衡图法和产能回报期法等。
时间研究法是通过时间观察和测量,确定每个工作站所需的标准工作时间,进而计算出各工作站的工作时间和任务量。
平衡图法是利用图形和符号表示装配线上的工作站和工作内容,通过分析和调整工作站之间的关系,实现任务的平衡。
产能回报期法是通过评估和比较不同工作站的产能和回报周期,确定最优的工作站次序和工序。
这些传统的方法简单直观,可以在实际生产中快速应用,但是对于复杂的装配线和大规模的生产系统来说,效果有限。
现代的装配线平衡优化算法主要包括遗传算法、模拟退火算法和禁忌搜索算法等。
这些算法通过建立数学模型和运用优化策略,不断调整和优化工作站之间的关系和任务分配,实现装配线的平衡效果最大化。
遗传算法模拟生物进化的原理,通过不断地变异、交叉和选择操作,逐渐接近最优解;模拟退火算法则是模拟金属冷却的原理,通过温度降低和能量下降,逐步趋近最优解;禁忌搜索算法则是根据禁忌表和禁忌准则,避免陷入局部最优解,全面搜索最优解的可能性。
实验二装配生产线平衡实验
实验二装配生产线平衡实验一、实验任务1.对玩具小车装配过程进行装配生产线平衡;2.在实验室生产模拟系统上模拟玩具小车装配生产线运行过程,并分析平衡效果。
二、实验目的及训练要点1.训练学生合理设计和实施一个工序平衡的生产线。
2.学会装配线平衡的基本方法和步骤。
3.在实验室生产线模拟系统上进行实际模拟,检验数据的准确性,同时掌握生产线模拟系统的操作过程。
另外,训练学生组织活动的能力。
三、实验原理1.定义工作站——操作者为了完成指定的装配作业在装配线上的工作位置。
有时候也把工作站称为“工位”或“工序”。
作业单元——作业的最小单元,一般情况下,这些操作单元不能再分。
对于很复杂的装配作业,例如汽车装配,作业单元如果划分得过细,会使整个平衡过程十分复杂,划分的过粗,又会使平衡难以很好进行,因此,必须寻找一个最佳尺度。
作业单元时间——完成某一个作业单元所用的标准时间,一般是经过工作研究和作业测定的操作时间。
节拍或周期——流水线上生产出一个产品所需要的时间,即相当于从装配线上出来成品的时间间隔。
工作站时间——完成分配给一个工作站的全部作业单元所需要的时间。
工作站空闲时间——在节拍内完成分配给一个工位的全部作业后所剩余的时间,它等于节拍减去工作站时间。
总作业时间——完成整个产品装配过程所需要时间,它等于所有作业元素时间之和。
总空闲时间——整个装配过程汇中,所有工作站空闲时间之和。
平衡效率——是衡量装配线上各工作站间均衡程度好与差的指标。
后续作业——从该作业单元出发沿着装配优先顺序图上所有路径前进直道终点所遇到的所有作业。
先行作业——从该作业开始逆路径方向而行直至起点所遇到的所有作业。
2.流水线平衡的基本步骤(1)完成初步的工艺流程的设计与优化。
制订初步的装配工艺过程,然后利用工艺程序分析方法、5W1H以及ECRS(取消、合并、重排、简化)四大准则对工艺程序进行改善,利用动作研究改善各操作单元的动作等。
改善的目的是为了消除工艺流程中存在的各种不合理的现象、减少浪费等。
装配线平衡计算ppt
-12
2
3.4 5
6 6 7.8
说明
吊运 装入 放入前 放入 安装 安装 拧紧螺 拧紧螺 安装 箱体定位 齿轮 浮动膜片 后膜片 后盖 前盖 栓螺母 栓螺母 连接盘
表 某部件装配顺序
-Leabharlann 解 1) 画出其先后次序图和先后次序矩阵表。 依照装配程序表的要求可以画出先后次序图。图中圆圈为作业, 箭头为操作顺序。
2 3 2 116 20
50 28
2 5 3.4 96 25
75 3
3 6 5 71 25
25 53
3 8 6 34 14
39 39
3 7 6 32 12
51 27
3 9 7.8 20 20
71 7
-
装配线效率= 完成作业所需时间总和/(实际工作站总数*时间周期)
9
Ti
i1 221 94.44% K •C 378
0 +1 +1 +1 +1 +1 +1 +1 171
3 20 4 30 5 25 6 25
0 0 +1 +1 +1 +1 +1 116 0 0 +1 +1 +1 +1 +1 126
0 +1 +1 +1 +1 96 0 +1 +1 +1 71
7 12 8 14 9 20
0 0 +1 32 0 0 +1 34
-
例题
现拟在传送带上组装某部件。该部件每天需组装369台,每天 的生产时间480min。装配顺序及装配时间如下表。根据周期 时间和作业顺序限制,求工作站数最少情况下的平衡流动及装 配线效率。
线平衡率简介
线平衡率简介
如果不是一个工站而是一条流水线,要计算其产能时就不能仅靠每个工站的标准工时,事实上以上标准工时制定步骤仅仅对于单个工站是有效的,但要评估整条线时,需要一个新概念--线平衡。
线平衡是标准工时之后生产中最基本的一个概念,精益生产方式中一个流生产的基础就是线平衡。
一条流水线是由许多任务站,许多机器/人组成的,如果这些工站的工作周期完全一致,那么我们就认为这条线的各工站是节拍平衡的,即这条生产线是平衡的,没有平衡损失,否则就是不平衡的,有平衡损失。
线平衡性的衡量标准是平衡率,平衡率最高是100%,但实际很难实现。
一条规划不好的线往往只有60%-75%的平衡率,一般我们认为线平衡率至少要达到85%才可以量产,如果要推行精益生产方式的一个流的生产方式,平衡率至少要95%以上。
一、装配线平衡的意义:
总的来说,提升装配线平衡可以给企业降本增效,是工业工程工作开展的重点,是制造型企业的基础核心之一。
1、产品生产效率高,每个产品的制造时间断,产品的工时定额低;
2、均衡生产,产线产出稳定,有利于作业标准化,提升员工士气和产品质量;
3、减少工序件的在制品数量。
二、线平衡率如何计算:
实例:装配车间某个产品在L1线分为ABCD 4个工位,其中A工位:1人作业,工位节拍50秒;B工位:2人作业,工位节拍45秒;C工位:2人作业,工位节拍48秒;D工位:1人作业,工位节拍42秒。
问,该产品线平衡率是多少?
正确答案:(50+45+48+42)/(50*4)=92.5%
三、线平衡率的评价标准:。
平衡率
2.4 装配线平衡效果的评价方法
设定一个定量值来直观地衡量装配线平衡的好坏。
一般采用装配线的平衡率、平衡损耗和平滑性指数等几个指标。
(1) 装配线的平衡率计算公式:
式中:
P :装配生产线的平衡率,表示整个或部分装配生产线的平衡状况。
:第 i 作业元素的作业时间。
:第 k 工作站的作业时间。
K :需要评价的整个或部分装配生产线的工作站数量。
:表示所有工作站中最大的作业时间。
表示所有工作站中最大的作业时间。
K :需要评价的整个或部分装配生产线的工作站数量
d :空程时间比率。
它是由于装配生产线上工作站之间作业分配不均导致的,d 值越大表示工位损失时间越多。
(3) 装配线的平滑指数计算公式:
式中:
CT :装配生产线的生产节拍。
T k :第 k 工作站的作业时间。
K :需要评价的整个或部分装配生产线的工作站数量。
SI :负荷均衡程度。
它用来表示工作站之间的工作负荷程度,SI 越小表示装配生产线工作站的负荷越均衡。
%100)max(1⨯⨯=∑=T t k n
i i k p k CT SI k k k T ∑=-=1
2)(。
- 1、下载文档前请自行甄别文档内容的完整性,平台不提供额外的编辑、内容补充、找答案等附加服务。
- 2、"仅部分预览"的文档,不可在线预览部分如存在完整性等问题,可反馈申请退款(可完整预览的文档不适用该条件!)。
- 3、如文档侵犯您的权益,请联系客服反馈,我们会尽快为您处理(人工客服工作时间:9:00-18:30)。
按位置权值递减的次 工作站 单元 紧前
序,在满足先后次序 K
i 单元
位置 单元时 工作站 平衡延迟 权值 间Ti 时间∑Ti 78-∑Ti
限制的条件下,指派 1 1 - 221 50
50 28
尽可能多的单元至一 工作站,直至接近该
1
21
171 25
75 3
站的周期时间。
2 4 2 126 30
30 48
B
5
工序同期化的措施有:
提高设备的生产效率。可以通过改装设备、改变设备型号同 时加工几个制件来提高生产效率; 改进工艺装备。采用快速安装卡具、模具,减少装夹零件的 辅助时间; 改进工作地布置与操作方法,减少辅助作业时间;提高工人 的工作熟练程度和效率; 详细地进行工序的合并与分解。
B
6
例题
现拟在传送带上组装某部件。该部件每天需组装369台,每天 的生产时间480min。装配顺序及装配时间如下表。根据周期 时间和作业顺序限制,求工作站数最少情况下的平衡流动及装 配线效率。
装配线平衡步骤 确定装配线节拍(生产周期) 计算装配线上需要的最少工作站的数目 组织定
➢确定工作周期时间C C=H/Q
式中:H—每天(计划期内)有效生产时间; Q—每天在H时间内要求的产量;
例题1 某流水线计划日产量为150件,采用两班制,每班规定有21 分钟停歇时间,计划不合格品率为2%,计算该流水线的节拍。
0 +1 +1 +1 +1 +1 +1 +1 171
3 20 4 30 5 25 6 25
0 0 +1 +1 +1 +1 +1 116 0 0 +1 +1 +1 +1 +1 126
0 +1 +1 +1 +1 96 0 +1 +1 +1 71
7 12 8 14 9 20
0 0 +1 32 0 0 +1 34
8125061002.01226分
B
4
(3)工作站数目的确定
➢确定最少工作站(工作地点)数目K, K= t /C
式中: K—最少工作站数; t —完成作业所需时间总量。
组织工作站需满足的条件: ➢保证各工序之间的先后顺序。 ➢每个工作站的作业时间不能大于节拍。 ➢每个工作站的作业时间应尽量相等和接近节拍。 ➢应使工作站的数目最少。
B
13
作业
1 2 3 4 56 7 8 9
作业时间(s) 50 25 20 30 25
紧前工序
-12
2
3.4
说明
吊运 装入 放入前 放入 安装 箱体定位 齿轮 浮动膜片 后膜片 后盖
25 12 14 20
5
6 6 7.8
安装 拧紧螺 拧紧螺 安装 前盖 栓螺母 栓螺母 连接盘
表 某部件装配顺序
B
7
解
1) 画出其先后次序图和先后次序矩阵表。 依照装配程序表的要求可以画出先后次序图。图中圆圈为作业, 箭头为操作顺序。
1.流水线生产平衡
(1)生产线平衡的定义
➢生产线的平衡:要根据产品设定工作站数目,再将各工作 单元分配到工作站,并使各工作站分配的工作量大致平衡, 而每个操作工人在工作站上完成指定工作单元的工作,同时 要使得生产线所需得工作地和用工人数最少的方案。
➢按萨尔凡森提出“在规定的装配线速度下,使总的空闲时 间最少,或使做一额定工作量的操作人数最少以使平衡延迟 最少”的原则进行装配线平衡调整。
0 20
图14B 位置权值矩阵
10
3)确定周期时间与最少工作站数
周期时间C: C=H/Q=480*60/369=78 秒 用下式计算满足周期时何要求的最少工作站数: K= t/C=(50+25+20 +30+25+25+12+14+20)/78 =2.83≈3 故最少需3个工作站。
B
11
4)分配各工作站的作业,进行装配线平衡
2 3 2 116 20
50 28
2 5 3.4 96 25
75 3
3 6 5 71 25
25 53
3 8 6 34 14
39 39
3 7 6 32 12
51 27
3 9 7.8 20 20
71 7
B
12
装配线效率=
完成作业所需时间总和/(实际工作站总数*时间周期)
9
Ti
i1 221 94.44% K •C 378
图12 装配前后次序图
B
8
先后次序矩阵表。
延后-1
无先后关系0
领先+1
图13 先后次序矩阵图
B
9
2)完成位置权值矩阵 作业的位置权数等于该作业及其后续作业( +1 )的时间总和。
Ti 1 2 3 4 5 6 7 8 9 PWa
1 50 0 +1 +1 +1 +1 +1 +1 +1 +1 221
2 25
B
1
为什么生产线平衡? 5分/件
2
3
2.8
2.5
4.5
1
2
3
4
5
➢浪费时间资源; ➢忙闲不均,引起矛盾;生产线平衡 ➢浪费人力资源。
➢节省时间; ➢提高效率; ➢降低成本。
B
2
装配线平衡(工序同期化) 流水线的节拍确定以后,要根据节拍来调节工艺过程,使各道 工序的时间与流水线的节拍基本相等或成整数倍比例关系。