浇道压头法设计浇注系统
浇注系统设计
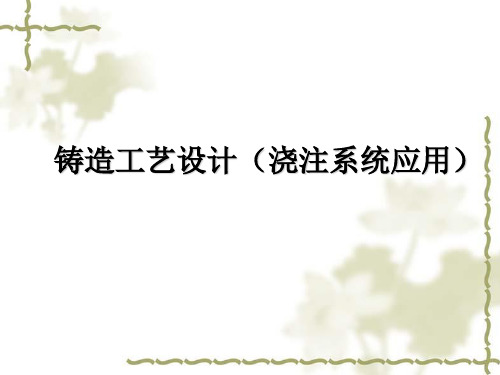
浇注系统设计
一、浇注系统构成 浇注系统由浇口杯(外浇口)、直浇道、横浇道和内浇道等构成。其构造见下图
1—浇口杯;2—直浇道;3—横浇道;4—内浇道
注意点:内浇道形状(提议使用Ⅰ型) ❖ Ⅰ型扁平内浇道易于清理,能提升横浇道旳挡渣效果。当使用宽度受限制时,可
用Ⅱ型。 ❖ Ⅲ型内浇道用于铸件垂直壁处或不宜冲刷处。 ❖ Ⅳ型和Ⅴ型内浇道用于需内浇道凝固较慢旳场合,其清理较困难。 ❖ Ⅵ型内浇道冷却较快、轻易清理。
老式浇系极难胜任三大功能旳两项:挡渣和降低紊流
浇注系统旳主要功能:1. 提供金属液进入型腔旳通道;2. 金属液尽量平稳;3.阻止渣/砂和其他反应产物进入型腔;
过滤器应用
带过滤器旳浇系
The controlling crosssection阻流截面
Downsprue : Runner Bar
:
Runner Bar : Ingate
带有过滤器旳浇注系统
❖ 内浇道和横浇道高度比
1. 内浇道形状扁平梯型;
2. H横=(5-6)H内—预防吸动作用产生杂质进型腔(针对放置在横浇道底部) ❖ 内浇道与横浇道连接方式
1. 放置在横浇道底部(在同一平面)---合用于封闭式浇注系统 2. 放置在横浇道顶部(不在同一平面)—封闭-开放式浇注系统
又称“缓流封闭式”。故充型旳平稳性及对型腔旳冲刷力都好于封闭式; ❖ 用于各类灰铸铁件及球铁件
浇注系统设计
(4) 封闭- 开放式---(推荐使用) ❖ F杯>F直<F横<F内 ❖ F杯>F直>F集渣包出口<F横后<F内 ❖ F直>F阻<F横后<F内 ❖ F直>F阻<F内<F横 ❖ 阻流截面设在直浇道下端,或在横浇道中,或在集渣包出口处,或在内浇道之
9-浇注系统的设计

图23 浇注系统
(1)主流道:从注塑机喷嘴与模具接触位 起,到分流道为止的这一段流道。作用是 负责将塑料熔体输往分流道。
主流道的设计事项:
1)主流道进口端与喷嘴头部接触处应 做成球面凹坑。如图24所示通常主流道进 口端凹坑的球面半径Sr要比喷嘴球面半径 Sr大1~2mm,凹入深度约5mm,为了补偿主 流道与喷嘴的对中误差,主流道进口端的 直径D应比喷嘴出口直径d大0.5~1mm。
2)主流道的锥角取2°~4°,对流性差的 塑料可增加大到 6°左右
3)主流道表壁的表面粗糙度取 Ra0.8∽0.4μm 。
4)主流道出口端应与分流道之间呈圆 滑过渡, R为0.3~3mm。
5)浇口套与安装孔应为过渡配合。
6)浇口套与定模板之间的连接力必须足够。
7)采用定位圈定位法.定位圈与定位孔的配 合长度:中小型模具8~10mm,大型模具 15mm左右。
图26 分流道的断面形状
2)分流道的布置形式
分流道的布置形式有:平衡式和非平衡而 平衡式布置为较佳。
A、所谓平衡式布置就是将通往各个型腔 的分流道的断面形状、大小及分流道长 度都取作一致。如图27所示。
图27 平衡式布置的分流道
B、非平衡式布置分流道如图28所示。
图28 非平衡式布置的分流道
浇注系统的设计
定义:浇注系统是塑料熔体从注塑机喷嘴出来后, 到达模腔之前在模具中流经的通道。
一.浇注系统的组成及其设计原则:重点内容
1、作用:将熔体平稳地引入型腔,使之充满型 腔内各个角落,在熔体填充和凝固过程中,能充分 地将压力传递到行腔的各个部位,获得组织致密、 外形清晰、尺寸稳定的塑件。
2、浇注系统由主流道、分流道、浇口、冷却穴组 成如图23所示
第八章 浇注系统设计

Fmin
G 0.0443 H P
用上式计算浇注系统最小截面积时需仔细确定式中各因素的数值。
在计算的铸件确定以后,即已确定。铸件图上一般已标出了铸 件的重量(未标时根据铸件图可估算出铸件重量),再加上浇注系 统和冒口的重量即为G值。
影响µ值的因素很多,难于用数学计算方法确定,一般都按生产 经验和参考实验结果选定。对于航空铝、镁合金铸件所用的扩张式浇 注系统,其µ值可在0.3~0.7之间选取。实际铸造时可根据铸件合金种 类、浇注温度和铸件结构选择。
(1) 应在一定的浇注时间内,保证充满铸型 (2) 应能控制液体金属流入型腔的速度和方向 (3) 应能把混入金属液中的熔渣和气体挡在浇注系统里 (4) 应能控制铸件凝固时的温度分布
(5) 浇注系统结构应力求简单,简化造型,减少清理工作量和 液体金属的消耗。
(1)承接来自浇包的金属液,防止金属液飞溅和溢出,便于浇注;
H
p
P2 H 2C
用上式计算平均静压头有下列三种情况 (1) 采用底注式浇注系统时,因为P=C(图中(a)),所以有: HP=H-C/2 (2) 采用顶注式浇注系统时(图中(b)),因为P=0,所以有: HP=H (3) 采用中注式浇注系统时(图中(c)),HP可用上面的HM的计 算公式来计算。 HP=H-C/8
内浇道流量不均匀现象对铸件质量有显著影响: ① 对大型复杂铸件和薄壁铸件易出现浇不足和冷隔缺陷
② 在流量大的内浇道附近会引起局部过热、破坏原来所 预计的铸件凝固次序,使铸件产生氧化、缩松、缩孔
和裂纹等缺陷。பைடு நூலகம்
为了克服内浇道流量不均匀带来的弊病,通常采用如下方法
(1)尽可能将内浇道设置在横浇道的对称位置; (2)将横浇道断面设计成顺着液流方向逐渐缩小形式; (3)采用不同断面内浇道,缩小远离直浇道的内浇道断两积; (4)设置浇口窝等。
浇注系统设计

基本组元的作用:
④ 横浇道 向内浇道分配洁净的金属液; 储留最初浇入的低温金属液和渣液; 使金属液平稳流动,阻渣浮气。
浇注系统设计
基本组元的作用:
⑤ 内浇道 控制金属液的充型速度和方向; 合理分配金属液; 调解铸件各部位的温度和凝固顺序。
浇注系统设计
3.1.2 浇注系统中液体金属的流动状态
各类灰口和球墨铸铁件
浇注系统设计
3.2.1 按组元的断面比例关系分类
④ 封闭开放式浇注系统 F阻 = F横
浇注系统的阻流段为横浇道或横浇道上设置的阻流装置。
形式:
F杯孔 ≥ F直 > F横 < F内
在这种浇注系统中,浇注时金属液是先封闭后开放。
浇注系统设计
浇注系统设计
3.2.1 按组元的断面比例关系分类
⑤ 结构和分布要便于造型和清理,节约金属。
浇注系统设计
2.5.2 机械加工余量
机械加工余量按GB/T6414-1999 确定。
国家标准GB/T6414-1999 中规定,机械加工余量代号为RMA, 等级由精到粗分为A、B、C、D、E、F、G、H、J 、K 10个 等级。
浇注系统设计
浇注系统设计
浇注系统设计
形式:
F杯孔 ≤ F直 < F横 < F内
在这种浇注系统中,浇注时金属液一般是非充满状态。
浇注系统设计
3.2.1 按组元的断面比例关系分类
② 开放式浇注系统(非充满式)
特点: 阻渣效果差,易卷气;
充型平稳,金属氧化轻。
适用: 有色件、球铁件
漏包浇注的铸钢件
浇注系统设计
3.2.1 按组元的断面比例关系分类
③ 半封闭式浇注系统 F阻 = F内
浇注系统

一般地,要求主流道进口处的位置应尽量与模具中心重合。 注意:如果受产品排位的限制要求浇口套偏离模具中心,那相 应的顶棍孔也要改成和浇口套同心。
第一节 主浇道的设计方式
主流道的形状一般为圆形
(1).垂直式主浇道及其设计参数:
D -d =0.5~1.0 (mm) R >r α =1~3°
(2)、倾斜式主浇道
PE
PP
PC
PS
PA
POM
ABS PMMA
表2
第五节:冷料井的设计
一. 定义及作用 冷料井是为除去因喷嘴与低温模具接触而在料流前锋产生的冷料进入型腔而设 置。它一般设置在主流道的末端,分流道较长时,分流道的末端也应设冷料井, 如图15。
H=(1~1.5)D ¢D
2
缺点:
特大的水口瑕媲,须要特别小心加工方法去除水口。 浇口尺寸公式计算如下:(公制单位) L=1.3-2MM T=成品壁厚 H1=NT N=塑料常数(表1)
H1
注:浇口面积不能大过流道切面 面积
L
图2
W
D
(4)潜水浇口
热塑性塑胶料分主要结晶体(Crystalline),非结晶体(Amorphous)和半结晶体(Semicrystalline)三大类。因分子结构不同,导致其收缩率因走水方向,及胶料厚薄不同面有不同收缩率。
0.
优点: -水口冷却快,生产周期短 -容易加工,经济
0.5t
t
D
a
PL
5t
(二)潜顶针:
h
0.8~1*L2
h
做脱模斜度
L2
L1
计算潜顶针入水面步骤:
i. 首先用普通潜水公式计算所需的浇口面积。 ii. 用所需的浇口面积计算h的尺寸(h<1/3D) iii. d=1至1.5倍普通潜水之入水面积
第七章 浇注系统设计

m:制品重量(g) :制品重量( L:分流道长度(mm) :分流道长度(
2)长度:在结构允许的前提下,尽量短; 2)长度:在结构允许的前提下,尽量短; 3)布置:总的要求型腔同时充满,且用料要少。 3)布置:总的要求型腔同时充满,且用料要少。
2011年12月 2011年12月9日 第 10页 10页
2011年12月 2011年12月9日 第 21页 21页
6)潜伏浇口(隧道式浇口): 6)潜伏浇口(隧道式浇口)
α = (5 − 20)o β = (20 −50)o γ = (10 −30)o d 1=φ(3−6) d =φ(0.7 − 2.5)
x max = 50 y max = 2
γ α
β
3)搭接式浇口: 3)搭接式浇口:
~ ~
~
特点:可防止粗大制品的重摸喷射现象,但加工、 修整、去除困难、制件上留有明显痕迹。 设计:面长c:小制品 0.5~0.8 0.5~ 大制品 1~2
c1 = h +b/2
2011年12月 2011年12月9日 第 17页 17页
4)膜状浇口: 4)膜状浇口:
α=(2o~4o)
4)2011年12月 2011年12月9日 第 6页
d
H
h
D2
d
H
h
2011年12月 2011年12月9日 第 7页
H
h
5)其它: 5)其它:
R=R1+1; R=R1+1; d=d1+1 α=(2o~4o) r=1 r2=(1~2) =(1~ D(H7/m6):由结构确定; L:由结构确定;
特点:塑件无熔合线,对强度 无影响。 适用:单型腔、管状薄壁制品。 设计:面长c:0.75~1 0.75~
浇注系统设计41858

.
浇口杯中的流动
16
.
浇口杯中的流动
浇注方向的影响见图3-4-8。逆向浇注较 顺向浇注为佳,侧向浇注介乎两者之间。
17
.
18
.
浇口杯的挡渣
19
.
直浇道中的流动
直浇道的功用:
➢从浇口杯引导金属向下,进入横浇道、内 浇道或直接导入型腔。
➢提供足够的压力头,使金属液在重力作用 下能克服各种流动阻力,在规定时间内充满 型腔。
20
.
二、液态金属在直浇道中的流动
1.直浇道入口处的形状影响液流分布 2.直浇道形状影响液流的内部压力。
21
.
(二)直浇道的吸气问题
22
金属液在直浇道中的流动的特点
.
1)液态金属在直浇道中存在两种流态:充满式流动或非充满式
流动。
2)在非充满的直浇道中,金属液以重力加速度向下运动,流股
呈渐缩形,流股表面压力接近大气压力,微呈正压。流股表面
10
.
11
二、按浇铸系统各基本组元截面积比例分类
封闭式浇注系统:
阻流-在一个浇注系统中截面积最小的浇道 ∑S内≤∑ S横≤ S直,例如1: 1.2 : 1.5 或半封闭式:S内≤ S直≤ S横
.
封闭式浇注系统可理解为正常浇注条件下,
所有组元能被金属液充满的浇注系统,也
称为充满式浇注系统。(因全部截面上的
缺点:
易造成冲砂缺陷金属, 液下落过程中接触空气, 出现飞溅、氧化、 卷入
空气等现象,使充型不 平稳
易产生砂孔、铁豆、气 孔和氧化夹杂物缺陷, 大部分浇注时间,内浇 道工作在非淹没状态,
横浇道阻渣条件相对较
差
5
.
塑料件模具设计--浇注系统设计

(6)轮辐式浇口
轮辐式浇口的适用范围类似 于盘形浇口,带有矩形内 孔的塑件也适用,但是它 将整个周边进料改成了几 小段直线进料。这种浇口 切除方便,流道凝料少, 型芯上部得到定位而增加 了型芯的稳定性。
31
(7)护耳式浇口
它在型腔侧面开设耳槽,熔体通过浇口冲击在 耳槽侧面上,经调整方向和速度后再进入型 腔,因此可以防止喷射现象,是一种典型的 冲击性浇口,它可减少浇口附近的内应力, 对于流动性差的塑料极为有效,浇口应设置 在塑件的厚壁处。
这种浇口的去除比较 困难,痕迹大
32
(8)点浇口
点浇口又称针点浇口或菱形浇口,是一 种截面尺寸很小的浇口,俗称小浇口。 这类浇口由于前后两端存在较大的压力 差,能较大地增大塑料熔体的剪切速率 并产生较大的剪切热,从而导致熔体的 表观粘度下降,流动性增加,有利于型 腔的充填。
33
(8)点浇口的设计形式
图a所示为直接式,直径为d的圆锥形的小端直接与塑件相 连。
图b所示为圆锥形的小端有一段直径为d、长度为l的点浇口 与塑件相连。这种形式的浇口直径d不能太小,浇口长度l 不能大长,否则脱模时浇口凝料会断裂而堵塞住浇口,影 响注射的正常进行。上述两种形式的点浇口制造方便,但 去除浇口时容易相伤塑件,浇口也容易磨损,仅适于批量 不大的塑件成型和流动性好的塑料。
非限制性浇口是整个浇口系统中截面尺寸最大的部位,它主 要对中大型筒类、壳类塑件型腔起引料和进料后的施压作用。
21
1、浇口的类型
(1)直接浇口(又称主流道形浇口)
在单型腔模中,熔体直接流入型腔,因 而压力损失小,进料速度快,成型比 较容易,对各种塑料都能适用。它传 递压力好,保压补缩作用强,模具结 构简单紧凑,制造方便。
- 1、下载文档前请自行甄别文档内容的完整性,平台不提供额外的编辑、内容补充、找答案等附加服务。
- 2、"仅部分预览"的文档,不可在线预览部分如存在完整性等问题,可反馈申请退款(可完整预览的文档不适用该条件!)。
- 3、如文档侵犯您的权益,请联系客服反馈,我们会尽快为您处理(人工客服工作时间:9:00-18:30)。
铸造技术 04/2011
生产技术与经验交流
生产技术与经验交流 Production T echn ology an d Experience E xchange
浇道压头法设计浇注系统
王 剑
(保定长城内燃机制造有限公司,河北保定072650)
Design of Gating System Using Pressure Head on Gating
W ANG Jian
(Great Wall Baoding Internal Combustion Engine Manufacturing Co.,Ltd.,Baoding 072650,China)
中图分类号:T G24 文献标识码:B 文章编号:1000 8365(2011)04 0569 02
浇注系统的设计是铸造工艺设计中重要的一项,
设计合理的浇注系统可以保证金属液在合理的浇注时间内以合理的流速充满型腔,且浇道内呈充满形态,避免产生气孔、夹渣、夹砂、冷隔等缺陷。
确定了浇注系统的类型、形式及布置之后,则需要计算浇注系统各单元的尺寸。
1 目前常用计算方法
目前常用的方法有阻流截面设计法、截面比设计法等。
1.1 阻流截面设计法
该方法认为浇注系统各单元中截面积最小单元为浇注系统阻流截面,根据小孔出流托里拆利定律,计算阻流截面积A 阻,按照预定截面比,进一步计算其余各
单元截面积。
[1]
A 阻=
G
2gH p
(1)
式中 G 流经阻流截面的金属总质量;
金属液的密度;
浇注系统阻流截面的流量因数; 充填型腔的总时间;
H p 充填型腔时的平均计算压力头。
这种方法存在流量因数可选取范围过大,最终结果误差大等缺点。
1.2 截面比设计法
截面比设计法运用大孔出流理论[2]很好地解决了这一问题,其首先计算有效截面比k 1、k 2:
k 1=
1A 1 2A 2(2)
k 2= 1A 1
3A
3(3)
式中 1、 2、 3 直浇道、横浇道、内浇道流量因
数;
A 1、A 2、A 3 直浇道、横浇道、内浇道截面积。
然后计算出横浇道、内浇道处的实际压头h 2、h 3
(见图1):
h 2=k 2
1+k 2
2
1+k 21+k 22H (4)h 3=k 221+k 21+k 22
H (5)
式中 H 直浇道几何压头。
图1 四单元浇注系统实际压头内浇道中心标注法
用压头h 3所推算出来的平均压头h p 代替式(1)中的H P 。
计算内浇道截面积A 3。
A 3=
G
3 2gh p
(6)
最后根据预定的截面比计算A 1、A 2。
h p 和h 3的关系可用做功法求出,即
h p =h 3-p
2
2c
(7)
式中 c 铸件型腔的高度;
p 内浇道以上铸件的高度,顶注,p =0;中
注,p =c 2
;底注,p =c 。
这种方法对于不同类型的浇注系统,流量因数的选取均在一个较小的范围内,大大提高了计算的准确性,且可以定量计算出浇注系统的充满程度。
h 2代表直浇道正压充满程度,可以判断是否会产生吸气。
h 3为横浇道是否充满的判据,可以评价档渣效果,而且决定了内浇道流速。
然而这些计算方法均为先依据经验选取浇注系统
569
生产技术与经验交流
铸造技术 04/2011
截面比,对于不同类型的浇注系统,结果可能使内浇道、横浇道实际压头不在合理范围内,则需要重新选取截面比来进行计算。
2 浇道压头法设计浇注系统
既然根据浇注系统截面比可以计算出横浇道、内浇道的实际出流压头,那是否也可以由预定的压头来计算截面比呢?
2.1 预定浇道压头的计算方法
由式(4)、式(5)可以导出:
k 1=h 2-h 3
H -h 2
(8)
k 2=
h 3
H -h 2
(9)
由此可见,可以预先选定横浇道、内浇道的压头,进而计算出最为合理的有效截面比,以及浇注系统各单元的截面积。
2.2 浇道压头法的设计步骤
由上述思路整理出的新方法计算步骤如下。
(1)设计浇注系统方案,确定直浇道的高度(几何压头)H ;
(2)根据不同的铸件材质、重量、壁厚、型腔高度和液面上升速度等条件选取最为合理的浇注时间 ;
(3)选取横浇道、内浇道的预定压头h 2、h 3;(4)按式(8)、式(9)计算有效截面比k 1、k 2
(5)选取流量因数 1、 2、 3;
(6)按照内浇道的引入位置,确定平均压头h p ;(7)按式(6)计算内浇道截面积A 3:(8)计算直浇道、横浇道截面积A 1、A 2:
A 1=k 2 3A 3
1(10)A 2=
1A 1k 1 2
(11)
3 结语
运用浇道压头法可以免去由设计者根据经验选取截面比,使浇道截面积的计算更具合理性。
同时可以免去对横浇道、内浇道压头的校核,快速准确地计算出各种不同形式浇注系统的截面积。
对新产品开发及原有工艺改进都有着积极的意义。
参考文献
[1] 中国机械工程学会铸造分会.铸造手册 铸造工艺卷
[M ].北京:机械工业出版社,2003.
[2] 魏 兵,袁 森,张卫华.铸件均衡凝固技术及其应用
[M ].北京:机械工业出版社,1998.
收稿日期:2010 12 17; 修订日期:2011 02 20
作者简介:王 剑(1982 ),河北定州人,学士学位,工程师.主要从事
铸造技术工作.
Email:w j0312@
对球铁石墨漂浮和灰斑问题的控制
诸海鸿,华 国
(苏州沙特卡铸造有限公司,江苏苏州215143)
Controlling of the Graphite Flotation and Dark Spot in Ductile Iron
ZHU Hai hong,HUA Guo
(Suzhou Satca Foundry Co.,Ltd.,Suzhou 215143,C hina)
中图分类号:TG251 文献标识码:B 文章编号:1000 8365(2011)04 0570 03
我公司(以下简称STK)利用扩建新厂的机会,将树脂砂大件车间熔炼方式由冲天炉改为电炉熔炼,电炉为2台熔化率7t/h 的中频感应炉。
感应炉熔炼铸铁与冲天炉相比,有利于获得低硫铁液,此点对于生产球铁具有冲天炉所无法比拟的优越性,但如果控制不当,也会产生一些在冲天炉熔炼所不易产生的问题。
比如在STK 电炉试生产初期,在一些老产品上就出现了在冲天炉熔炼从未产生过的石墨漂浮和灰斑缺陷,造成批量性的报废。
1 事情经过
多年来,STK 利用冲天炉生产球铁时,对于炉料
含C 量的配料基本按固定统一配比,而很少根据铸件结构的不同而专门对含碳量进行控制,通常配碳量为3.3%~3.5%左右,这是由于冲天炉熔炼,在特定炉况下,通常有一个 碳平衡 ,即低碳铁料,增碳率高,而高碳铁料增碳率低,甚至有脱碳现象,抽检原铁液含碳量一般是3.4%~ 3.6%。
一般只是将含Si 量控制在3.0%以下,此时CE 小于4.5%,而壁厚小于100mm 的普通球铁件石墨漂浮碳当量临界值为4.5%~4.6%,按ST K 传统生产方法,通常CE 是合适的,故多年来未曾出现过石墨漂浮问题。
570。