冲压名词解释和简答题
冲压的概念
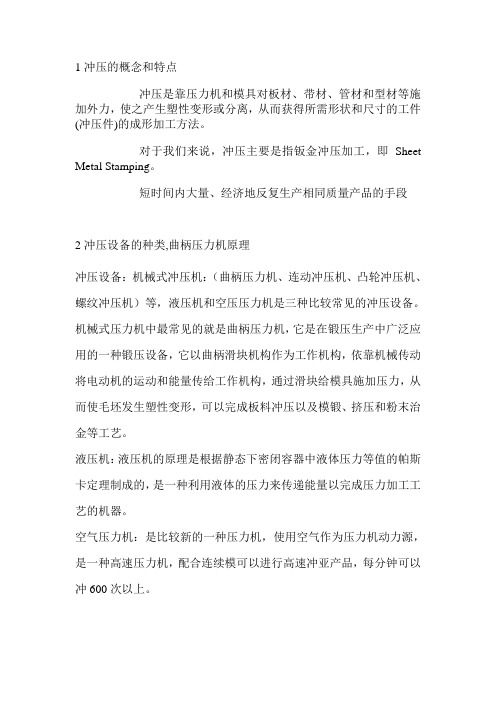
1冲压的概念和特点冲压是靠压力机和模具对板材、带材、管材和型材等施加外力,使之产生塑性变形或分离,从而获得所需形状和尺寸的工件(冲压件)的成形加工方法。
对于我们来说,冲压主要是指钣金冲压加工,即Sheet Metal Stamping。
短时间内大量、经济地反复生产相同质量产品的手段2冲压设备的种类,曲柄压力机原理冲压设备:机械式冲压机:(曲柄压力机、连动冲压机、凸轮冲压机、螺纹冲压机)等,液压机和空压压力机是三种比较常见的冲压设备。
机械式压力机中最常见的就是曲柄压力机,它是在锻压生产中广泛应用的一种锻压设备,它以曲柄滑块机构作为工作机构,依靠机械传动将电动机的运动和能量传给工作机构,通过滑块给模具施加压力,从而使毛坯发生塑性变形,可以完成板料冲压以及模锻、挤压和粉末治金等工艺。
液压机:液压机的原理是根据静态下密闭容器中液体压力等值的帕斯卡定理制成的,是一种利用液体的压力来传递能量以完成压力加工工艺的机器。
空气压力机:是比较新的一种压力机,使用空气作为压力机动力源,是一种高速压力机,配合连续模可以进行高速冲亚产品,每分钟可以冲600次以上。
6.在上面三种压力机中,最常见的就是曲柄压力机了,这里就说明一下他的工作原理:曲柄压力机的动力源来自于电动机,然后通过带轮和离合器,齿轮等将运动和能量传递给曲柄滑块机构,动画上的蓝色部分是曲柄轴,绿色的是连杆,黄色的这里写是冲头,按照我们这里的叫法应该是滑块,天然色的防滑装置,就是滑块的轨道,这样就将曲柄轴的旋转运动转化成了滑块的上下往复运动,在带轮这里其实还有一个离合器,前面提到过,因为在冲压加工时,有时要停下来,特别是但工程模和复合模加工大都采用人工操作的,离合器就是控制是否将带轮的运动传递给曲柄轴,当需要滑块运动时,离合器就结合,制动器脱开,当不需要滑块运动时,离合器脱开,制动器结合制动,使滑块停在某一位置。
由于冲压时,材料的塑性成型是一霎那的,在那一霎那工艺力,很大,所以曲柄压力机在一个工作周期中,就是滑块一个上下来回,只有在较短的时间内才会承受高峰负荷,而在绝大多数时间是无负荷运转,所以为了平衡整个周期内电动机的负荷,使其均匀,不要使电动机的功率过大,成本高,在压力机上装有转动惯量很大的飞轮,在压力机空载是,飞轮储存电动机提供的能量,工作时,滑块受到变形抗力的作用,使飞轮瞬间降速,产生很大的惯行力矩,能量释放,灰色的这个零件就是惯性轮。
冲压

第一章冲压冲压的定义:室温下,在压力机上通过模具对板料金属(非金属)加压,使之产生塑性变形或分离,从而获得一定尺寸、形状和性能的工件的加工方法,又叫冷冲压或板料冲压。
冲压工艺可用于加工,金属板料,非金属板料.冲压工艺特点:生产效率高;在大量生产中可获得稳定的质量;材料利用率高,生产成本低;可制造复杂形状的工件。
冲压生产的局限性:--制模成本高;--技术要求高;--不适用于单件、小批量生产。
加工硬化:在常温下,随着变形程度的增加,金属材料的强度指标增高,塑性指标降低的现象。
冲压分类:分离工序,成型工序分离工序:冲压过程中,使冲压件与板料在切应力或拉应力的作用下,沿一定的轮廓线相互分离。
分离工序主要指冲裁,包括落料、冲孔、切断、切边、剖切等工序。
普通冲裁:通过破坏分离方式所完成的冲压工序。
精密冲裁:以变形分离方式所完成的冲压工序。
成形工序:在冲压过程中,使毛坯在不破坏的条件下发生塑性变形,成为所需形状与尺寸的工件,同时冲压件应该满足尺寸精度方面的要求。
成形工序主要包括弯曲、拉伸、胀形、翻边等。
落料:用模具沿封闭轮廓线冲切,冲下部分是零件。
用于制造各种平板零件或者成形工序制坯冲孔:用模具沿封闭轮廓线冲切,冲下部分是废料。
用于冲制各类零件的孔形弯曲;把板料沿直线弯曲成各种形状,板料外层受拉伸力,内层受压缩力。
可加工形状复杂的零件毛坯区域的划分:变形区,传力区在成形过程中,毛坯的变形区和传力区是运动变化的,而且还会相互转化。
制定工艺时,必须保证:“弱区先变形,变形区应为弱区”对毛坯变形趋向性的控制,主要有以下几种方法:(1)合理确定毛坯和半成品尺寸(2)改变模具工作部分的几何形状和尺寸(3)改变毛坯与模具接触面之间的摩擦阻力(4)改变毛坯局部力学性能1、什么是冲压?它与其它加工方法相比有什么特点?2、冲压工序可分为哪两大类?他们的主要区别和特点是什么?3、如何控制冲压过程中的变形趋向?板料的冲压性能:指板料对冲压的适应能力、可成形能力间接试验:板料的受力情况和变形特点与实际冲压有一定差别,其试验结果只能间接反映板料的冲压性能。
冲压名词解释
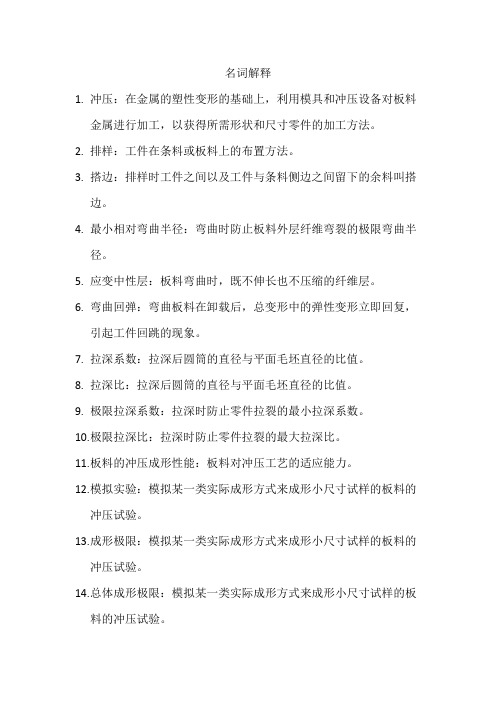
名词解释1.冲压:在金属的塑性变形的基础上,利用模具和冲压设备对板料金属进行加工,以获得所需形状和尺寸零件的加工方法。
2.排样:工件在条料或板料上的布置方法。
3.搭边:排样时工件之间以及工件与条料侧边之间留下的余料叫搭边。
4.最小相对弯曲半径:弯曲时防止板料外层纤维弯裂的极限弯曲半径。
5.应变中性层:板料弯曲时,既不伸长也不压缩的纤维层。
6.弯曲回弹:弯曲板料在卸载后,总变形中的弹性变形立即回复,引起工件回跳的现象。
7.拉深系数:拉深后圆筒的直径与平面毛坯直径的比值。
8.拉深比:拉深后圆筒的直径与平面毛坯直径的比值。
9.极限拉深系数:拉深时防止零件拉裂的最小拉深系数。
10.极限拉深比:拉深时防止零件拉裂的最大拉深比。
11.板料的冲压成形性能:板料对冲压工艺的适应能力。
12.模拟实验:模拟某一类实际成形方式来成形小尺寸试样的板料的冲压试验。
13.成形极限:模拟某一类实际成形方式来成形小尺寸试样的板料的冲压试验。
14.总体成形极限:模拟某一类实际成形方式来成形小尺寸试样的板料的冲压试验。
15.局部成形极限:板料失稳之前局部尺寸所能达到的最大变化程度。
16.成形极限图:板料在不同应变路径下的局部失稳极限应变构成的条带形区域或曲线。
17.贴膜性:板料在冲压过程中取得模具形状的能力。
18.定性形:板料在模具内既得形状的能力。
19.α破裂:因材料强度不足引起的破裂。
20.β破裂:因材料局部延伸率不足引起的破裂。
21.简单模:在压力机的一次行程内,只完成单一工序的模具。
22.复合模:在压力机的一次行程内,在模具的同一工位上完成多道冲压工序的模具。
23.连续模:在压力机的一次行程内,在模具的不同工位上完成多道冲压工序的模具。
24.模具压力中心:冲裁时的合力作用点或多工序模各工序冲压力的合力作用点。
25.模具闭合高度:模具在最后工作位置时上模板与下模板之间的距离。
冲压的名词解释是什么

冲压的名词解释是什么冲压,顾名思义,是一种通过冲击或压力将金属材料加工成所需形状的工艺。
在制造业中,冲压是一项常见且重要的金属加工方法,广泛应用于汽车、电子、家电、建筑和航空航天等领域。
概括来说,冲压是一种通过将金属材料置于模具中,并用冲击或压力力量对其施加,从而使其发生塑性变形的过程。
这种方法通常涉及将金属板料或带材经过一系列工序,包括冲孔、弯曲、拉伸等,以达到所需的几何形状。
冲压工艺的实施通常需要使用冲床,它是一种专门用于冲压加工的机械设备。
冲床的工作原理可以简单地解释为:金属材料被夹在两个模具之间,顶部的模具向下施加力量,使得金属板料在模具的作用下发生塑性变形。
这种变形通常是沿着模具的轮廓线或孔的位置发生的,最终得到所需的形状。
冲压的优势在于它能够快速、高效地加工大批量的零件,而且具有准确的尺寸控制和重复性。
与其他传统的金属加工方法相比,冲压能够有效地降低生产成本并提高生产效率。
此外,冲压还可以实现多种复杂的形状和细微的细节,以满足不同行业的需求。
冲压工艺的重要组成部分是模具,它是用于冲压过程的关键工具。
模具通常由高硬度的材料制成,如工具钢。
模具的设计和制造对于冲压过程的成功至关重要。
在设计阶段,需要考虑到材料的选择、模具的形状和结构、以及冲床的适配性等因素。
此外,模具的使用还需注意对其进行维护和保养,以确保其长期稳定的工作性能。
冲压工艺的应用范围非常广泛。
在汽车制造业中,冲压被广泛应用于车身和内部零部件的制造,如车门、引擎罩、车顶等。
在电子行业中,冲压用于制作电子设备的外壳,如手机、平板电脑等。
此外,冲压还在家电、建筑、航空航天等领域中发挥着重要作用。
尽管冲压工艺在制造业中具有广泛的应用和重要的地位,但也存在一些挑战和限制。
例如,对于复杂形状的部件,可能需要多次冲压和模具之间的配合,增加了生产的复杂性和成本。
此外,在冲压过程中,材料可能会出现变形、断裂和表面缺陷等问题,需要进行相应的控制和处理。
冲压名词解释和简答题

名词解释:1冷冲压:在室温下,利用安装在压力机上的模具对材料施加压力,使其产生塑性变形或断裂分离,从而获得所需冲压件的一种压力加工方法.2分离工序:在冲压过程中使冲压件与板料沿一定的轮廓线相互分离的工序。
3成型工序:毛坯在不被破坏的条件下产生塑性变形,形成所要求的形状和尺寸精度的制件。
4塑性:金属材料在外力作用下产生的永久变形而不破坏的能力。
5塑性变形:材料在外力作用下产生的永久变形。
5材料的变形抗力:金属材料在外力作用下抵抗塑性变形的能力。
6变形速度:指单位时间内应变的变化量,塑性成形设备的加载速度在一定程度上反映了金属的变形速度。
7强度极限:拉伸过程中条件应力应力曲线最高点的条件应力。
8硬化指数:板料在冷塑性变形中的硬化强度。
9塑性应变比:材料试棒在拉伸过程中宽度真实应变,与厚度应变之比。
10压力机闭合高度:指滑块在下止点时,滑块下平面到工作台上平面的距离。
11冲压变形:由冲压设备提供变形载荷,然后通过模具对毛坯施加外力进而转化为毛坯的内力,使之产生塑性变形。
12冲模闭合高度:工作行程终了时,模具上模座顶面到下模座底面之间的距离。
13压力机公称压力:滑块离下死点前某一特定距离或特定角度时,滑块上所允许承受的最大作用力。
14冲裁:安装在压力机上的冲裁模,使材料产生分离的工序。
15落料:制取所需要零件的外形尺寸的工序。
16冲孔:制取所需零件的内形尺寸的工序。
17冲裁件的工艺性:零件对冲裁工艺的适应性。
18排样:冲裁件在板料和条料上的布置方法。
19搭边:排样中相邻两个零件和余料或零件与条料侧边之间留下的工艺余料。
20步距:条料在模具上每次送进的距离。
21冲裁力:冲裁过程中凸模对板料的压力。
22卸料力:从凸模卸下紧箍的料所需要的力。
23推件力:将梗塞在凹模内顶出所需要的力。
24冲模压力中心:冲裁时冲裁力的合力作用点。
25压力中心:冲裁时冲裁力的合力作用点。
26单工序模:在一副模具中只完成一个工序的冲模。
冲压的名词解释

冲压的名词解释冲压,作为一种金属成形技术,广泛应用于工业生产中。
其主要通过将金属板或带料件置于冲模中,借助冲床的力量对材料进行冲击、剪切和弯曲等加工过程,以达到所需形状和尺寸。
冲压具有高效、精准、稳定的特点,广泛应用于汽车、家电、航空航天等诸多领域。
1. 冲压的历史渊源冲压技术的起源可以追溯到古代的铜器铸造,当时的铜器铸造采用了类似于现代冲压的工艺,通过摆动铸造模具来实现金属铸造。
随着工业革命的推进,冲压技术得到了进一步的发展和应用。
2. 冲压工艺的工作原理冲压工艺主要采用冲模和冲床的组合进行金属材料的成形。
冲模是一种由凹、凸两个模块组成的设备,其中凹模是放入冲床的下部固定模具,凸模则是通过连接杆件与一块可浮动的上部模板关联。
冲床通过电动或机械控制冲击凸模,使其对金属材料进行加工变形。
3. 冲压工艺的优势冲压工艺具有多项优势,首先是高效生产。
冲压工艺能够实现快速连续的成形加工,大大提高了生产效率。
其次是高精度。
冲压工艺在成形过程中,能够较为准确地控制产品的尺寸和形状,保证了产品的一致性。
此外,冲压工艺还具有稳定性好、材料利用率高的特点。
4. 冲压工艺的应用领域冲压工艺广泛应用于各个领域,尤其是汽车和家电行业。
在汽车工业中,冲压工艺被用于车身件、车门、车窗框等零部件的制造。
在家电产业中,冲压工艺则常被用于制造洗衣机外壳、冰箱门板等零部件。
此外,航空航天、建筑、工程机械等领域也广泛采用了冲压工艺。
5. 冲压工艺的发展趋势随着科技的不断进步,冲压工艺也在不断发展和创新。
一方面,随着数字化技术的广泛应用,冲压工艺开始采用先进的数控机床和自动化设备,以提高生产效率和产品质量。
另一方面,材料的革新也推动了冲压工艺的发展,例如高强度钢、铝合金等轻量化材料的使用,使得冲压件的质量更轻更坚固。
冲压工艺作为一种重要的金属成形技术,对于提高产品质量、降低生产成本具有重要意义。
随着工业的不断发展,相信冲压工艺还将面临更多的挑战和机遇,不断创新和完善,为各个领域的生产制造提供更好的解决方案。
冲压介绍

C、折弯的控制
冲压折弯是变化比较多一点,易产生折弯开裂/尺寸 不良/角度不良/平行度不良 折弯产生的问题比较多,产生原因是原材料/模具设 计有关。 品保员在控制折弯是注意折弯开裂/尺寸不良/角度 不良/平行度不良。 品保员在测量冲压折弯是一定多注意基准,一定选 对基准或者互换基准测量以减少测量误差。
D、拉深控制
• 拉深控制比较简单,主要是拉深起邹和拉
深开裂, • 拉深起邹和拉深开裂主要是冲压油、原材 料有关、模具设计有关。 • 对于品保员主要是控制拉深起邹和拉深开 裂两项不良现象。
E、形位公差的控制
• 形位公差控制大部分是汽车件冲压产品,
形位公差大部分是用三次元进行评价,所 以品保员只需要知道形位公差进行测量, 具体表示是什么意思就行。 • 对于这一部分主要是品保员识图能力,
刺 • 漏冲孔:大部分是由于SUS301/SUS304材料比较硬 导致冲子断形成漏冲孔, • 孔变小:大部分是由于材料太软形成孔内毛刺导致 孔变小,或者是冲子磨损严重使孔变小, • 对于冲压孔的控制一定注意孔变小/孔变形。
B、冲裁边的控制
• 对冲裁边控制:主要是接刀口变形和冲裁
边毛边或者是毛刺 • 对于现场品保员来讲主要是接刀口变形和 冲裁边毛边
四、品保员怎样能控制好冲压品质
• 作为一名品保员主要做好二点:
A、清楚标准和严格执行标准 B、做事一定仔细认真,严格按照首件管制办. 法执行; ★:如果在执行过程发现有超出标准时,一 定把问题反映给工程师和组长,让他们帮 你解决问题!
Lemtech产品常见不良现象
• FIN:
• COVER:
•
氧化,断裂,尺寸不良,压伤,松动,扇形
压伤,变形,划伤,断裂,铆合不良 • BLOCK/BASE/PLATE:氧化,压伤,变形,平整
冲压概述
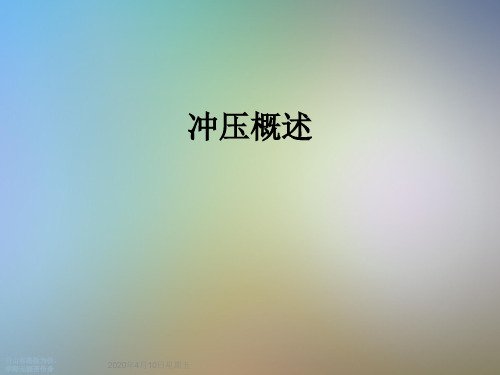
书山有路勤为径, 学海无涯苦作舟
•
一般的冲压机械(通用机)只单纯地进行冲头的反 复运动,因此做功的模具也当然只是上模具的直线 往返运动。
二、冲压模具的基本分类 说起模具,也有很多种。塑料模具、橡胶模具、
•
第二章 冲压机械
一、冲压机械概述
冲压机械有很多种类。在机械式冲压机中有曲柄 冲压机、连动冲压机、凸轮冲压机、螺纹冲压机等 。
使用油压的为油压冲压机、使用空气压力的为空 压冲压机。
利用人力完成的有脚踏冲压机(俗称:一脚踹)、 手动冲压机等种类。
在这里我主要讲一下常用的曲柄冲压机,以下我
统称为冲压机械。
模具由一对刀具(工具)组成。如果您联想一 下剪刀就不难理解了。
首先将一片刀具装在冲头上,另一片刀具固 定在垫枕部上。
将铁板放在刀具与刀具之间,冲头下降时铁 板就会被切断。这一对刀具就是模具。
示意图如下:
书山有路勤为径, 学海无涯苦作舟
•
书山有路勤为径, 学海无涯苦作舟
被装在冲头上的模具,理所当然就被称 为上方模具,即上模具。
垫枕部的模具就称为下模具。
上模具与下模具共同构成模具。
•
模具除可以切断钢板(剪断)以外,还可以弯、拧 铁板,使之发生永久的变形,得到想要得到的形状 。
直接使材料发生变形的东西就是模具。没有模 具就不能进行冲压加工。
模具的质量、性能直接影响到冲压加工的生 产性和冲压加工的质量,具有极为重要的作用,可 以说是冲压加工的生命。
玻璃模具等五花八门。其中用于冲压加工的称为冲 压模具。在这里我们将冲压模具称为模具。
- 1、下载文档前请自行甄别文档内容的完整性,平台不提供额外的编辑、内容补充、找答案等附加服务。
- 2、"仅部分预览"的文档,不可在线预览部分如存在完整性等问题,可反馈申请退款(可完整预览的文档不适用该条件!)。
- 3、如文档侵犯您的权益,请联系客服反馈,我们会尽快为您处理(人工客服工作时间:9:00-18:30)。
名词解释:1冷冲压:在室温下,利用安装在压力机上的模具对材料施加压力,使其产生塑性变形或断裂分离,从而获得所需冲压件的一种压力加工方法.2分离工序:在冲压过程中使冲压件与板料沿一定的轮廓线相互分离的工序。
3成型工序:毛坯在不被破坏的条件下产生塑性变形,形成所要求的形状和尺寸精度的制件。
4塑性:金属材料在外力作用下产生的永久变形而不破坏的能力。
5塑性变形:材料在外力作用下产生的永久变形。
5材料的变形抗力:金属材料在外力作用下抵抗塑性变形的能力。
6变形速度:指单位时间内应变的变化量,塑性成形设备的加载速度在一定程度上反映了金属的变形速度。
7强度极限:拉伸过程中条件应力应力曲线最高点的条件应力。
8硬化指数:板料在冷塑性变形中的硬化强度。
9塑性应变比:材料试棒在拉伸过程中宽度真实应变,与厚度应变之比。
10压力机闭合高度:指滑块在下止点时,滑块下平面到工作台上平面的距离。
11冲压变形:由冲压设备提供变形载荷,然后通过模具对毛坯施加外力进而转化为毛坯的内力,使之产生塑性变形。
12冲模闭合高度:工作行程终了时,模具上模座顶面到下模座底面之间的距离。
13压力机公称压力:滑块离下死点前某一特定距离或特定角度时,滑块上所允许承受的最大作用力。
14冲裁:安装在压力机上的冲裁模,使材料产生分离的工序。
15落料:制取所需要零件的外形尺寸的工序。
16冲孔:制取所需零件的内形尺寸的工序。
17冲裁件的工艺性:零件对冲裁工艺的适应性。
18排样:冲裁件在板料和条料上的布置方法。
19搭边:排样中相邻两个零件和余料或零件与条料侧边之间留下的工艺余料。
20步距:条料在模具上每次送进的距离。
21冲裁力:冲裁过程中凸模对板料的压力。
22卸料力:从凸模卸下紧箍的料所需要的力。
23推件力:将梗塞在凹模内顶出所需要的力。
24冲模压力中心:冲裁时冲裁力的合力作用点。
25压力中心:冲裁时冲裁力的合力作用点。
26单工序模:在一副模具中只完成一个工序的冲模。
27连续膜:在一副模具中的不同位置上完成两个或两个以上的工序,最后将冲件与条料分离的冲模。
28复合膜:在一副模具中的同一位置上完成几个不同工序的冲模。
29硬质合金冲裁模:冲裁模的凸模和凹模是合金材料。
30弯曲:将板料及棒料,管料,型材产生塑性变形,形成具有一定角度和一定曲率形状的冲压工序。
31自由弯曲:如果在板料和凸凹模万全贴紧后,凸模继续下行一段很小的距离。
32回弹:弯曲成形后,弹性变形的消失会导致工件朝与成形相反的方向变形。
33弯曲中性层:在弯曲变形中,内外层材料既不受拉也不受压,其长度保持不变的层材料。
34弯曲件的工艺性:在弯曲变形中,弯曲件的材料,形状,尺寸精度和技术要求等对弯曲工艺的适应程度。
35相对弯曲半径:在弯曲变形中,弯曲件的弯曲半径与板料厚度之比值。
36最小弯曲半径:为保证弯曲时,外层材料不致弯裂,弯曲件的弯曲半径能达到的最小值。
37最小相对弯曲半径:在自由弯曲时,保证材料最外层纤维不发生破裂的前提下,所能获得的弯曲件内表面最小圆角半径与材料厚度的比值。
38弯曲中心角:弯曲终了时,弯曲变形区所对应的圆心角。
39拉深:(又称拉延)是利用拉深模在压力机的作用下,将平板坯料或空心工序件制成开口空心零件的加工方法。
40拉身系数:指拉深后圆筒件的直径与拉深前毛坯(半成品)的直径之比。
41浅拉深:拉深行程小于压力机公称压力行程的拉深。
42深拉深:拉深行程大于压力机公称压力行程。
43拉深件工艺性:零件拉深加工的难易程度。
44胀形:将空心件或管状件沿径向向外扩张的成形工序。
45起伏:在平面或曲面坯料上使之凸起或凹进的成形工序。
46翻边:在模具的作用下,将坯料的孔边缘或外边缘翻成竖立直边的成形工序。
47翻孔系数:翻孔的变形程度。
48缩口:在冲压成形中,将筒形坯件的开口端直径缩小的方法。
49校平:将毛坯或零件不平整的面亚平。
50平面校平模:用于材料较薄,平直度要求较高且表面上容许有细痕的工件。
51整形:利用模具使弯曲或拉深后的冲压件局部或整体产生少量塑性变形以得到较准确的尺寸和形状,保证精度的冲压工序。
简答题1简述冲压加工的特点?答:优点:互换性好;可以获得壁薄,质量轻,刚性好,表面质量高,形状复杂的零件;节能省料;效率高。
缺点:噪声和振动大;模具要求高,制造复杂,周期长,制造费用高;零件精度要求过高,冲压生产难以达到要求。
2分离工序:落料冲孔切断切边冲槽剖切成形工序:弯曲拉深翻边胀形缩口挤压卷圈扩口校形3冲压工序分为那两大类?他们的区别是什么答:冲压工序分为分离工序和成形工序。
区别:分离工序:在冲压过程中使冲压件与板料沿一定的轮廓线相互分离的工序。
成形工序:毛坯在不被破坏的条件下产生塑性变形,形成所需求的形状和尺寸精度的零件。
4简述冷冲压加工的特点?答:冷冲压是少,无切屑加工方法之一所得的冲压件一般无需再加工.冷冲压是一种高效率加工方法.冷冲压所得的冲压件质量稳定,互换性好.冷冲压可以加工壁薄,质量轻,刚性好,形状复杂的零件.5冲压工艺对板料的基本要求包括那几个方面?答:1.机械性能的要求:一般来说,延伸率大,屈强比小,弹性模数大,硬化指数高,厚向异性系数大有利于各种冲压成形工序.2.化学成分的要求:2.金相组织的要求3.表面质量的要求4.材料厚度公差的要求.6变形速度对塑性变形的影响?答:1。
变形速度增高,变形抗力增加,出现晶间脆裂 2.由于热效应的原因,引起金属温度升高,金属的塑性又得到改善。
7什么是“屈服点”?”屈服点“有何影响?答;屈服点:“屈服平台“最低点出所对应的条件应力。
影响:材料的屈服点值小,材料易屈服,成形后回弹小,贴膜性和定形性较好。
对零件表面质量的影响:拉伸曲线出现屈服平台,屈服伸长较大,板料在屈服伸长之后,表面出现明显的滑移线痕迹,导致零件表面粗糙。
8凸耳系数△r对拉深工艺有何影响?答:1.在筒形件拉深中,由于板平面方向性使拉深件出现口部不齐的凸耳现象,方向性愈明显,凸耳也越高。
2.板平面方向性大时,在拉深,翻边,胀形等冲压过程中能够引起毛坯变形的不均匀,其结果不但可以因为局部变形程度过大,而是总体的极限变形程度减小,而且还可能引起壁厚不等而降低冲压件的质量,在生产中应该降低凸耳系数。
9冲裁件断面有哪几部分组成?冲裁间隙的大小如何影响这些部分的?答:间隙偏小,造成圆角变小,光亮带变宽,断裂带变小,毛刺小:间隙过大,造成圆角变大,光亮带窄,断面斜度变大,毛刺大;j间隙大小适中,圆角小,光亮带约占料厚的1/3~2/3,断裂带小,毛刺小;间隙大小适中,但不均匀时,间隙偏小处产生挤毛,间隙偏大处拉长毛刺。
10分析凸凹模刃口状态对冲裁件断面质量的影响?答:当模具刃口磨钝时,在冲裁件的边缘会产生很大的毛刺,当凸模刃口磨钝时,则会在冲孔边缘产生毛刺;当凹模刃口磨钝时,则会在落料件产生毛刺;当凸凹模刃口都磨钝时,则会在冲裁件边缘均产生毛刺。
11分析冲裁间隙对冲裁尺寸精度的影响?答;由于冲裁对工件受力而产生一定的弹性变形,冲裁结束后,工件发生弹性恢复现象,从而引起冲裁件与凸凹模刃口尺寸不符;当间隙过大,落料件尺寸减小,冲孔件尺寸增加;当间隙过小时,落料件尺寸减小;当间隙合理时,制件尺寸与模具刃口尺寸完全一样。
12影响冲裁件尺寸精度和断面质量的因素有哪些?如何提高尺寸精度和断面质量?答:影响冲裁件尺寸精度的因素:冲裁间隙,冲模制造精度,材料性质与厚度,冲裁剪的形状和尺寸。
提高尺寸精度的措施:1.冲模精度比冲件精度高IT3~4级2.选较软的冲压件材料3.选择合理的冲裁间隙4.冲裁件尽量设计得简单,对称。
影响断面质量的因素:材料的性能;冲裁间隙;凸凹模刃口状态。
提高断面质量的措施:1.选择塑性好的材料2。
选择合理的冲裁间隙3.凸凹模保持锋利的刃口。
13冲裁间隙对卸料力,推件力,顶件力的影响/答:间隙的增大,材料所受的拉应力增大,材料容易断裂分离,使冲裁件的光亮面变窄,落料尺寸小于凹模尺寸,冲孔尺寸大于凸模尺寸,因而使卸料力,推件力,顶件力减小,当间隙继续增大时,因为毛刺增大,引起卸料力,顶件力增大。
14间隙对模具寿命的影响?答:间隙增大,坯料对模具的摩擦磨损减小,因此,磨具寿命增大;但是,间隙过大,使毛刺增粗,增大;对模具的摩擦,磨损又会增大;影响模具寿命;间隙过小,坯料对磨具的摩擦,磨损增大,甚至胀裂凹模,使模具寿命缩短。
15确定合理间隙值得要求是什么?答:1.对冲裁件断面要求较高时,在间隙允许范围内,考虑采用较小的间隙。
2.当冲裁件的断面质量在没有特殊要求时,在间隙允许范围内,取较大的间隙是有利的。
3.冲裁间隙的选取,根据剪切断面的光亮带或断面质量要求按照表格中的数值选取。
16刃口尺寸的计算依据与原则?答;1.落料件尺寸由凹模尺寸决定,冲孔件尺寸由凸模尺寸决定。
2.落料时,应先确定凹模尺寸,其大小应取接近或等于落料件的最小极限尺寸;冲孔时,应先确定凸模尺寸,其大小应取接近或等于冲孔件的最大极限尺寸。
3.落料时以凹模刃口尺寸为设计基准,凸模刃口尺寸等于凹模刃口尺寸减去最小合理间隙值;冲孔时以凸模刃口尺寸为设计基准,凹模刃口尺寸等于凸模刃口尺寸加上最小合理间隙值。
3.冲压件的尺寸公差和凸凹模制造公差按入体原则标注单向公差。
(17)单配加工法的计算一个凸模或凹模同时存在三类不同性质的尺寸:第一类:凸模或凹模在磨损后会增大的尺寸。
第一类尺寸=(冲裁件上该尺寸的最大极限尺寸—x △)(1/4)0+∆相当于落料凹模尺寸。
第二类:凸模或凹模在磨损后会减小的尺寸。
第二类=(冲裁件上该尺寸的最小极限尺寸+x △)0(1/4)-∆相当于冲孔凸模尺寸。
第三类:凸模或凹模在磨损后基本不变的尺寸。
第三类=冲裁件上该尺寸的中间尺寸±(1/8)△。
(18)降低冲裁力的方法或措施?答:红冲(加热冲裁)加热到温度900℃;采用斜刃口冲裁;阶梯凸模的方式(采用阶梯冲裁的优点:降低冲裁力,减少振动,在冲裁过程中可以避免折断。
缺点:刃口修模困难)(19)确定冲裁压力中心的目的是什么?答:保证工作时,模具受力平衡,延长磨具寿命,保护压力机不受损坏。
(20)选择合理搭边值的原则?搭边的作用?合理搭边选择的依据?答:原则:搭边的最小宽度大于塑性变形区的宽度,一般可取等于板料的厚度。
作用:保证冲裁件质量,保证模具较长寿命,保证自动送料时不被拉弯拉裂条件下允许的最小值。
依据:决定于材料厚度,6材料种类,冲裁件的大小,冲裁件的轮廓形状。
(21)冲裁件的工艺性包括哪几个方面?影响冲裁件工艺性的因素有哪些?答:工艺性:冲裁件的形状;冲裁件的精度和表面粗糙度。
影响因素:1.冲裁件的形状尽量简单,最好是由规则几何形状或由圆弧与直线构成。
2.冲裁件的内外形转角处应避免尖角3.冲裁件的凸出悬壁和凹槽宽度不宜过小4.冲裁件孔与孔之间,孔与边缘之间的距离不应过小。