Wirebond StrengthTesting
COB 的焊线及其焊线拉力解决方案

COB 的焊线及其焊线拉力解决方案当COB 的晶粒黏着好且烘烤完毕后,接下来就是最有趣的打线/焊线(Wire bonding)制程,这个制程与IC 封装稍有不同的地方是IC 用金线(gold wire),金相显微镜而COB 则用铝线(Aluminum wire) ,所以焊点的形状也就有所不同,其次是焊线的拉力也会不同。
一般来说金的延展性比其他金属来得好,所以金线的拉力就会比较高,也比较不易断,质量也就比较稳定。
以焊点的形状来区分的话,焊线制程可以分为『球型焊(Ball Bond)』及『楔型焊(Wedge Bond)』两种。
COB 通常采用铝线(Al wire)所以会是Wedge Bond。
金相显微镜根据经验及数据,球型焊的强度比楔型焊来得好,可是「金线」也比较贵。
一般的COB 制程都会再加购一台手动的焊线机来修补焊线,因为自动机台太贵了,如果停下来作修补将会影响到产出数量。
金相显微镜手动修补也比较有弹性,可以选择焊垫上没有点焊过的位置来重新焊线,这样也可以得到比较好的焊接强度。
COB 通常不建议做PCB 拼板(panelization),因为Wire Bonding 机台有最大尺寸的限制,而且比SMT 小很多,大部分Wire Bonding 焊头的移动范围也仅局限在4"x4"之内,如果要同时打超过两颗以上的COB 时,就需要特别留意其距离。
就我所知道COB 制程能力最小可以打到90um 的焊点间距,但是一般的COB 较能接受的是100~140um 的焊点间距。
也许现在已经有更新的制程能力了。
金相显微镜COB 的焊线打在PCB 上面,但是PCB 的镀金层基本上很难有非常平均的镀层,再加上有些因素造成焊线的不稳定,所以有时候会有打线不良的情形发生,这时候就需要有技巧的熟练作业员来挑掉原来的焊线,然后再打上新的焊线。
挑除焊点时可以拿细小的缝衣针,从线头的位置刺下去,然后往拉线的方向推就可以把整个焊点推起来,焊点最好要清除干净,以免重新焊线时干涉到或重迭造成不良。
wire bond在英语作文中的作用

wire bond在英语作文中的作用Wire bond is a critical component in the field of electronics and semiconductor manufacturing. It serves as a vital link, connecting various electronic components and enabling the flow of electrical signals and power. In the realm of English writing, the concept of wire bond can be metaphorically applied to draw parallels and provide insights into the structure and function of language.Much like the physical wire bond that connects different parts of an electronic circuit, the use of language in writing serves to establish connections between ideas, thoughts, and concepts. Just as a wire bond ensures the seamless transfer of electrical impulses, the strategic placement and arrangement of words, phrases, and sentences in a piece of writing facilitates the smooth conveyance of information, emotions, and narratives to the reader.One of the primary roles of wire bond in English writing is to create coherence and cohesion within the text. Much like the wire bond that physically binds components together, the use of various linguistic devices, such as transitional words, conjunctions, and referentialexpressions, helps to establish logical relationships between different parts of the written work. These connections guide the reader through the narrative, ensuring a clear and logical flow of ideas.For instance, the use of conjunctions like "and," "but," "because," and "therefore" serves to link related clauses and sentences, demonstrating the causal or contrastive relationships between them. Similarly, the strategic placement of adverbs and adverbial phrases can act as wire bonds, connecting different parts of a sentence or paragraph and guiding the reader's understanding of the temporal or spatial relationships within the text.Moreover, the concept of wire bond can be extended to the structure of individual sentences in English writing. The arrangement and positioning of words within a sentence can be likened to the interconnections created by wire bonds. The subject-verb-object structure, for example, can be seen as a fundamental wire bond that binds the various components of a sentence together, ensuring the coherent transmission of meaning.Just as a well-designed wire bond can enhance the efficiency and reliability of an electronic circuit, the judicious use of language in writing can elevate the overall quality and impact of the text. Skilled writers often employ a variety of syntactic structures, such as parallel constructions, subordinate clauses, and complex sentences, to createintricate wire bond-like connections between ideas, thereby enriching the depth and nuance of their writing.Furthermore, the concept of wire bond can be extended to the broader organizational structure of a written work. The introduction, body, and conclusion of an essay or article can be viewed as the primary wire bonds that hold the entire piece together, guiding the reader through the narrative and ensuring a cohesive and compelling overall experience.In the same way that a faulty or poorly designed wire bond can disrupt the functioning of an electronic circuit, the improper use of language in writing can lead to confusion, ambiguity, and a lack of coherence. Misplaced modifiers, dangling participles, and unclear pronoun references can be likened to weaknesses or breaks in the wire bond, hindering the smooth flow of ideas and the effective communication of the writer's message.Therefore, the concept of wire bond in English writing serves as a powerful metaphor, highlighting the critical role that language plays in connecting and structuring the various elements of a written work. Just as wire bonds are essential for the proper functioning of electronic devices, the strategic use of language is fundamental to the creation of coherent, compelling, and impactful written communication.In conclusion, the concept of wire bond in English writing can be seen as a unifying principle that underscores the importance of linguistic cohesion, syntactic structure, and organizational coherence in the craft of writing. By understanding and embracing the wire bond-like nature of language, writers can enhance their ability to effectively convey their ideas, emotions, and narratives to their readers, ultimately strengthening the overall impact and effectiveness of their written works.。
Wire Bonding 3rd Inspection (Bonding 限度样本)概论

不良名
不良照片
不良定义
SPEC / 判定基准
备注
Damage Wire (Wire 损伤不良)
Bonding後 Wire上痕 迹,断线, 弯曲及Wir e Bonding部位损伤.
Wire 直径 (1mil=0.025㎛) 25%以上的,减少发 生的 Damage Wire 处理为不良.
Chipping 不良 (碎裂不良)
Wire Bonding超过Die P ad区域的Bond
Bonding Pad里 75%未满 Bonding时不良处理. 单,75%以上、邻接活动 Metal接触时不良.
品質保證組
3rd Optical Inspection 基准及限度样本
不良名
不良照片
不良定义
SPEC / 判定基准
备注
C / 判定基准
备注
未按照Bonding
Diagram连接或错 误连接时处理为不 良.(任何情况下不 容许.)
Solder 溢出 (粘接材料溢 出不良)
Solder或 Epoxy在 Bonding Area或 别的致命区域溢 出.
Solder或 Epoxy侵 入 Bonding Area 时,任何情况都属 于不良.
品質保證組
3rd Optical Inspection 基准及限度样本
不良名
不良照片
不良定义
SPEC / 判定基准
备注
Lifted - Bond Bond 翘起
Lifted – Bond Pad或 Lead上 胶翘起
Lifted – Bond Pad或 Lead上50% 以上Bond 翘起时不良
Misplaced Bond Bond 位置不良
Wire-Bonding工艺介绍和Gold-Wire特性

金线焊接工具---劈刀
劈刀决定的一些参数: 1、Bond Pad Pitch
金线焊接工具---劈刀
T--Tip Diameter, BTNK—Bottleneck Height&Angle, CA—Cone Angle Will affect bond pad pitch.
2、1st Bond Diameter
Not move
affect Not affect
Go up with capillary
Form ball when 6000v on it
Not affect Not affect
金线球形焊接工艺介绍
Stage1
Stage2
Stage3
Stage4
Stage5
Stage6
Stage7
Stage8
H—Hole Diameter, ICA—Inner Chamfer Angle CD—Chamfer Diameter Will affect 1st bond diameter
金线焊接工具---劈刀
3、Wire Diameter
H—Hole Diameter
Hole diameter is usually 1.5X wire diameter
wire
Ultrasonic and force
Form ball when 6000v on it
Not affect
Go up to chamfer, affect touch die surface
Not move
Not affect
Form loop shape Not affect
Squashed and form 2nd bond
bonding wire电流能力 温度系数

键合线(bonding wire)是连接电子元件引脚和电路板上的焊盘的一种导线。
它通常用于连接芯片和PCB之间的引脚,以及连接其他电子元件之间的引脚。
在电子设备中,键合线的质量和性能对设备的可靠性和稳定性起着至关重要的作用。
键合线的电流能力取决于其材料和尺寸。
一般来说,键合线的电流能力应该足够大,以确保在正常工作条件下,电子元件之间的连接不会出现故障或损坏。
通常,键合线的电流能力应该大于电子元件的额定电流的2-3倍。
键合线的温度系数是指在不同温度下,键合线的电阻值发生变化的程度。
由于键合线通常用于连接电子元件,因此在高温环境下,键合线的电阻值可能会增加,从而导致电路中的电流下降。
因此,在选择键合线时,需要考虑其温度系数,并选择合适的材料和尺寸,以确保在不同温度下,电路的性能和可靠性都能得到保证。
总之,键合线的电流能力和温度系数是选择键合线时需要考虑的重要因素,它们对于确保电子设备的可靠性和稳定性至关重要。
(工艺流程)最简易的半导体制造工艺流程

半导体制造工艺流程N型硅:掺入V族元素--磷P、砷As、锑SbP型硅:掺入III族元素—镓Ga、硼BPN结:半导体元件制造过程可分为前段(FrontEnd)制程晶圆处理制程(WaferFabrication;简称WaferFab)、晶圆针测制程(WaferProbe);後段(BackEnd)构装(Packaging)、测试制程(InitialTestandFinalTest)一、晶圆处理制程晶圆处理制程之主要工作为在矽晶圆上制作电路与电子元件(如电晶体、电容体、逻辑闸等),为上述各制程中所需技术最复杂且资金投入最多的过程,以微处理器(Microprocessor)为例,其所需处理步骤可达数百道,而其所需加工机台先进且昂贵,动辄数千万一台,其所需制造环境为为一温度、湿度与含尘(Particle)均需控制的无尘室(Clean-Room),虽然详细的处理程序是随著产品种类与所使用的技术有关;不过其基本处理步骤通常是晶圆先经过适当的清洗(Cleaning)之後,接著进行氧化(Oxidation)及沈积,最後进行微影、蚀刻及离子植入等反覆步骤,以完成晶圆上电路的加工与制作。
二、晶圆针测制程经过WaferFab之制程後,晶圆上即形成一格格的小格,我们称之为晶方或是晶粒(Die),在一般情形下,同一片晶圆上皆制作相同的晶片,但是也有可能在同一片晶圆上制作不同规格的产品;这些晶圆必须通过晶片允收测试,晶粒将会一一经过针测(Probe)仪器以测试其电气特性,而不合格的的晶粒将会被标上记号(InkDot),此程序即称之为晶圆针测制程(WaferProbe)。
然後晶圆将依晶粒为单位分割成一粒粒独立的晶粒三、IC构装制程IC構裝製程(Packaging):利用塑膠或陶瓷包裝晶粒與配線以成積體電路目的:是為了製造出所生產的電路的保護層,避免電路受到機械性刮傷或是高溫破壞。
半导体制造工艺分类半导体制造工艺分类一双极型IC的基本制造工艺:A在元器件间要做电隔离区(PN结隔离、全介质隔离及PN结介质混合隔离)ECL(不掺金)(非饱和型)、TTL/DTL(饱和型)、STTL(饱和型)B在元器件间自然隔离I2L(饱和型)半导体制造工艺分类二MOSIC的基本制造工艺:根据栅工艺分类A铝栅工艺B硅栅工艺其他分类1、(根据沟道)PMOS、NMOS、CMOS2、(根据负载元件)E/R、E/E、E/D半导体制造工艺分类三Bi-CMOS工艺:A以CMOS工艺为基础P阱N阱B以双极型工艺为基础双极型集成电路和MOS集成电路优缺点半导体制造环境要求主要污染源:微尘颗粒、中金属离子、有机物残留物和钠离子等轻金属例子。
WireBonding
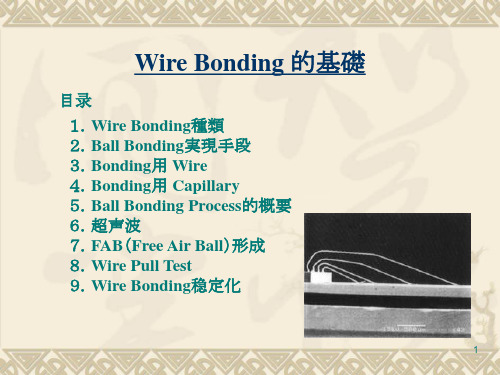
Fine Pad Pitch用上,为Control成小 的Ball Size、Wire径最好是小Hole 径,Wire径的大部分是1.3倍以下
H WD
8
Bond直接影響 Capillary寸法仕様 直接影響的 寸法仕様( 4-2 对Ball Bond直接影響的Capillary寸法仕様(2)
Chamfer径 Chamfer径(CD) Pad開口部→Ball Size→Chamfer径 Chamfer径过于大的话、Bonding強度有弱的傾向
Wire Bonding 的基礎
目录 1.Wire Bonding種類 種類 2.Ball Bonding実現手段 実現手段 3.Bonding用 Wire 用 4.Bonding用 Capillary 用 5.Ball Bonding Process的概要 的 6. 超声波 7.FAB(Free Air Ball)形成 ( ) 8.Wire Pull Test 9.Wire Bonding稳定化 稳
对Au Wire的要求、除純度以外 寸法的精度要高(用0.1um制御可能) 表面要圆滑、金属要有光泽 表面不能有灰尘、污染 具有拉伸强度、要有一定的弹性 Curl(卷曲性)要小 Au Wire前端形成的 Ball的形状要有一定的真圆性 等機能的要求
6
4.Bonding用 Capillary Bonding用
Smaller CD – Smaller MBD
Bigger CD – Bigger MBD
FAB の Centering
接合時的左右荷重・超 音波振動伝達
CD MBD CA:70(Degree)
CD MBD CA:120(Degree)
10
根据Bond Pitch所限制的Capillary的寸法仕様(参考) 所限制的Capillary 4-3 根据Bond Pitch所限制的Capillary的寸法仕様(参考)
金球推力国际标准Wire Bond Shear Test
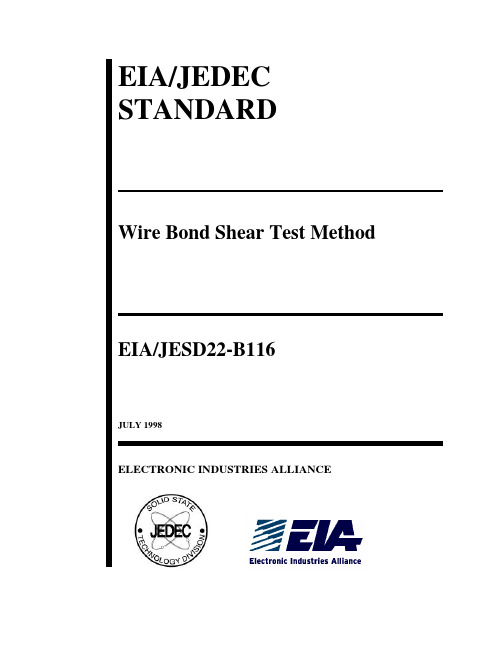
EIA/JEDEC STANDARDWire Bond Shear Test Method EIA/JESD22-B116JULY 1998ELECTRONIC INDUSTRIES ALLIANCENOTICEJEDEC standards and publications contain material that has been prepared, reviewed, and approved through the JEDEC Council level and subsequently reviewed and approved by the EIA General Counsel.JEDEC standards and publications are designed to serve the public interest through eliminating misunderstandings between manufacturers and purchasers, facilitating interchangeability and improvement of products, and assisting the purchaser in selecting and obtaining with minimum delay the proper product for use by those other than JEDEC members, whether the standard is to be used either domestically or internationally.JEDEC standards and publications are adopted without regard to whether or not their adoption may involve patents or articles, materials, or processes. By such action JEDEC does not assume any liability to any patent owner, nor does it assume any obligation whatever to parties adopting the JEDEC standards or publications.The information included in JEDEC standards and publications represents a sound approach to product specification and application, principally from the solid state device manufacturer viewpoint. Within the JEDEC organization there are procedures whereby a JEDEC standard or publication may be further processed and ultimately become an EIA standard.No claims to be in conformance with this standard may be made unless all requirements stated in the standard are met.Inquiries, comments, and suggestions relative to the content of this JEDEC standard or publication should be addressed to JEDEC Solid State Technology Division, 2500 Wilson Boulevard, Arlington, VA 22201-3834, (703)907-7560/7559 or \jedec.Published by©ELECTRONIC INDUSTRIES ALLIANCEEngineering Department2500 Wilson BoulevardArlington, VA 22201-3834"Copyright" does not apply to JEDEC member companies as they arefree to duplicate this document in accordance with the latest revision ofJEDEC Publication 21 "Manual of Organization and Procedure".PRICE: Please refer to the currentCatalog of JEDEC Engineering Standards and Publications or call Global Engineering Documents, USA and Canada (1-800-854-7179), International (303-397-7956)Printed in the U.S.A.All rights reservedJEDEC Standard 22-B116Page 1WIRE BOND SHEAR TEST(From JEDEC Council Ballot JCB-97-64, formulated under the cognizance of the JC-14.1 Subcommittee on Reliability Test Methods for Packaged Devices.)1 ScopeThis test provides a means for determining the strength of the bond between a gold ball bond on a die bonding surface or an aluminum wedge or stitch bond on a package bonding surface, and may be performed on pre-encapsulation or post-encapsulation parts. This measure of bond strength is extremely important in determining two features:1) the integrity of the metallurgical bond which has been formed.2) the quality of gold and aluminum wire bonds to die or package bonding surfaces.These test methods cover ball bonds made with small diameter (from 18 to 76 µm, or from 0.7 to 3 mil) wire and wedge bonds made with larger diameter (minimum of 3 mil) wire, of the type used in integrated circuits and hybrid microelectronic assemblies.These test methods can be used only when the ball height (at least 10.16 µm or 0.4 mil) and diameter for ball bonds, or the wire height (at least 1.25 mils in height at the compressed bonded area) of the wedge bond, are large enough and adjacent interfering structures are far enough away to allow suitable placement and clearance (above the bonding pad or leadframe post and between adjacent bonds) of the shear test chisel. This test method may also apply to gold wedge or stitch bonds if the wire is thick enough to allow shearing of the wire from the bonding surface without smearing similar to a shearing skip.The wire bond shear test is destructive. It is appropriate for use in process development, process control and/or quality assurance.2 Terms and DefinitionsThe terms and definitions shall be in accordance with the following paragraphs.2.1 Ball BondThe adhesion or welding of a thin wire, usually gold, to a die pad metallization, usually an aluminum alloy, using a thermosonic wire bond process. The ball bond includes the enlarged spherical, or nail head, portion of the wire (provided by the flame-off and first bonding operation in the thermal compression and thermosonic process, or both), the underlying bonding pad and the ball bond-bonding pad intermetallic weld interface.2.2 Bonding SurfaceEither 1) the die pad metallization or 2) the package surface metallization to which the wire is ball, wedge or stitch bonded.Test Method B116JEDEC Standard 22-B116Page 22 Terms and Definitions (cont’d)2.3 Bond ShearA process in which an instrument uses a chisel shaped tool to shear or push a ball or wedge bond off the bond pad (see Figure 1). The force required to cause this separation is recorded and is referred to as the bond shear force. The bond shear force of a gold ball bond, when correlated to the diameter of the ball bond, is an indicator of the quality of the metallurgical bond between the gold ball bond and the bond pad metallization. The bond shear force of an aluminum wedge bond, when compared to the manufacturer's tensile strength of the wire, is an indicator of the integrity of the weld between the aluminum wire and the bond pad or package surface metallization.Figure 1 — Bond Shear set-up2.4 Definition of Bond Shear Codes for Ball and Wedge Bonds (see Figure 2)2.4.1 Type 1 - Bond LiftA separation of the entire wire bond from the bonding surface with only an imprint being left on the bonding surface. There is very little evidence of intermetallic formation or welding, or disturbance of the bonding surface metallization.2.4.2 Type 2 - Bond ShearA separation of the wire bond where 1) A thin layer of the bonding surface metallization remains with the wire bond and an impression is left in the bonding surface, or 2) Intermetallics remain on the bonding surface and with the wire bond, or 3) A major portion of the wire bond remains on the bonding surface. Test Method B116JEDEC Standard 22-B116Page 3 2 Terms and Definitions (cont’d)2.4 Definition of Bond Shear Codes for Ball and Wedge Bonds (see Figure 2) (cont’d)2.4.3 Type 3 - CrateringA condition under the die pad metallization in which the insulating layer (oxide or interlayer dielectric) and the bulk material (silicon) separate or chip out. Separation interfaces which show pits or depressions in the insulating layer (not extending into the bulk) are not considered craters. It should be noted that cratering can be caused by several factors including the wire bonding operation, the post-bonding processing, and even the act of shear testing itself. Cratering present prior to the shear test operation is unacceptable.2.4.4 Type 4 - Arm Contacts Specimen (Bonding Surface Contact)The shear tool contacts the bonding surface to produce an invalid shear value. This condition may be due to improper placement of the specimen, a low shear height or instrument malfunction. This bond shear type is not acceptable and shall be eliminated from the shear data.2.4.5 Type 5 - Shearing SkipThe shear tool removes only the topmost portion of the ball or wedge bond. This condition may be due to improper placement of the specimen, a high shear height or instrument malfunction. This bond shear type is not acceptable and shall be eliminated from the shear data.2.4.6 Type 6 - Bond Pad (or Bonding Surface) LiftA separation between the bonding surface metallization and the underlying substrate or base material. There is evidence of bonding surface metallization remaining attached to the ball or wedge bond.Test Method B116JEDEC Standard 22-B116Page 4Test Method B1162 Terms and Definitions (cont’d)2.4 Definition of Bond Shear Codes for Ball and Wedge Bonds (see Figure 2) (cont’d)TYPE 1: Bond Lift TYPE 2: Bond Shear - Gold/AluminumTYPE 4: Bonding Surface ContactTYPE 3: Cratering TYPE 5: Shearing Skip TYPE 6: Bonding Surface LiftFigure 2 — Bond Shear CodesExamples shown here are for ball bonds. These same modes also apply to wedge and stitch bonds.JEDEC Standard 22-B116Page 5 2 Terms and Definitions (cont’d)2.5 Shear Tool or ArmA tungsten carbide, or equivalent, chisel with specific angles on the bottom and back of the tool to ensure a shearing action.underlying bonding pad, and the ball bond-bonding pad intermetallic weld interface.2.6 Wedge BondThe adhesion or weld of a thin wire, usually aluminum, to a package bonding surface, usually a plated leadframe post or finger, using an ultrasonic wire bonding process. A wedge bond is sometimes also called a stitch bond. The wedge bond includes the compressed (ultrasonically bonded) area of the wire and the underlying bonding surface. For bonding to an aluminum alloy die bond pad, there is no wedge bond-bond pad intermetallic because the two materials are of the same composition, but the two materials are recrystallized together by the ultrasonic energy of the welding process.3 Apparatus and materialThe apparatus and materials required for bond shear shall be as follows:3.1 Inspection EquipmentAn optical microscope system or scanning electron microscope providing a minimum of 70X magnification.3.2 Measurement EquipmentAn optical microscope/measurement system capable of measuring the bond diameter to within ± 0.0001 inch (0.1 mil).3.3 WorkholderFixture used to hold the part being tested parallel to the shearing plane and perpendicular to the shear tool. The fixture shall also eliminate part movement during bond shear testing. If using a caliper controlled workholder, place the holder so that the shear motion is against the positive stop of the caliper. This is to ensure that the recoil movement of the caliper controlled workholder does not influence the bond shear test.3.4 Bond Shear EquipmentThe bond shear equipment must be capable of precision placement of the shearing tool (±2.54µm or ±0.10 mil) above the substrate. The specified distance (h) above the topmost part of the bonding surface shall ensure the shear tool does not contact the surface of the die and shall be less than the distance from the topmost part of the bonding surface to the center line (C L) of the ball or wedge bond.Test Method B116JEDEC Standard 22-B116Page 63 Apparatus and material (cont’d)3.5 Bond Shear ToolRequired shear tool parameters include but are not limited to: flat shear face, sharp shearing edge, shearing width of a minimum of 1.2X the bond diameter or bond length. The shearing tool should be designed so as to prevent ploughing and drag during testing. The tool should be clean and free of chips or other defects that will interfere with the shearing test.4 Procedure4.1 CalibrationBefore performing the bond shear test, it must be determined that the equipment has been calibrated in accordance with manufacturer's specifications and is presently in calibration. Recalibration is required if the equipment is moved to another location.4.2 Visual Examination of Bonds to be Tested After DecapsulationIf performing bond shear testing on a part which has been opened using wet chemical and/or dry etch techniques, the bond pads shall be examined to ensure there is no absence of metallization on the bonding surface area due to chemical etching, and wire bonds are attached to the bonding surface. Those ball or wedge bonds on bond pads with significant chemical attack or absence of metallization shall not be used for ball shear testing. It is possible that wire bonds on bonding surfaces without degradation from chemical attack may not be attached to the bonding surface due to other causes (e.g., package stress). These wire bonds are considered valid and shall be included in the shear data as a zero (0) gram value. Bonds must also be examined to determine if adjacent interfering structures are far enough away to allow suitable placement and clearance (above the bonding surface and between adjacent bonds) for the shear test tool. 4.3 Sample SizesSample sizes shall be a minimum specified by SPC controls in effect for specific processes, or as specified in the applicable procurement document4.4 Measurement of the Ball Bond Diameter to Determine the Ball Bond Shear Failure Criteria Once the bonding surfaces have been examined and before performing bond shear testing, the diameter of all ball bonds to be tested shall be measured and recorded. For asymmetrical bonds, determine the average using both the largest (d large) and the smallest (d small) diameter values (see Figure 3). These ball bond diameter measurements shall be used to determine the mean, or average, diameter value. The resulting mean, or average, ball bond diameter shall then be used to establish the failure criteria as defined in Figure 4 and Table 1. If process monitor data has established the nominal ball bond diameter, then that value may be used to determine the failure criteria as defined in Figure 4 and Table 1.Test Method B116JEDEC Standard 22-B116Page 7Test Method B1164 Procedure (cont’d)4.4 Measurement of the Ball Bond Diameter to Determine the Ball Bond Shear Failure Criteria(cont’d)SYMMETRICAL ASYMMETRICALFigure 3 — Ball bond measurement (symmetrical vs. asymmetrical)MINIMUM SHEAR VALUESBALL BOND DIAMETER (mils)S H E A R S T R E N G T H (g r a m s )0102030405060708090100110Figure 4 — Minimum recommended individual and average ball bond shear values(see Table 1 for exact bond shear values)JEDEC Standard 22-B116Page 8Test Method B1164 Procedure (cont’d)Table 1 — Minimum recommended individual and sample average ball bond shear valuesDiameter(mils)Minimum Shear Average (grams)Minimum Individual Shear Reading (grams)2.012.6 5.72.114.0 6.82.215.58.12.317.19.52.418.810.92.520.612.42.622.414.02.724.415.62.826.517.42.928.619.23.030.821.13.133.223.13.235.625.13.338.127.23.440.729.43.543.431.73.646.234.13.749.136.53.852.139.13.955.241.74.058.344.34.161.647.14.265.050.04.368.452.94.471.955.84.575.659.04.679.362.14.783.165.34.887.068.64.991.072.05.095.175.5Note: These shear values are applicable to gold wire ball bonds on aluminum alloy bonding surfacesJEDEC Standard 22-B116Page 9 4.5 Performing the Bond Shear TestThe bond shear equipment shall pass all self diagnostic tests before beginning the test. The bond shear equipment and test area shall be free of excessive vibration or movement. Examine the shear tool to verify it is in good condition and is not bent or damaged. Check the shear tool to verify it is in the up position.Adjust the workholder to match the part being tested. Secure the part to the workholder. Make sure the surface of the die is parallel to the shearing plane of the shear tool. It is important that the shear tool does not contact the surface of the die or adjacent structures during the shearing operation as this will give incorrect high readings.Position the part so that the bond to be tested is located adjacent to the shear tool. Lower the shear tool, or raise the part depending upon shear equipment used, to approximately the surface from which the bond is to be sheared but not contacting the surface (approximately the thickness of the bond above the surface). Position the ball bond to be tested so that the shear motion will travel perpendicular to the surface edge. Position the wedge bond to be tested so that the shear motion will travel toward the long side of the wedge bond and is free of any interference (i.e. shear the outside bond first and then shear toward the sheared wedge bond). Position the shear tool within approximately one ball (for ball bonds) or wire diameter (for wedge/stitch bonds) of the bond to be shear tested and shear the bond.4.6 Examination of Sheared BondsAll bonds shall be sheared in a planned/defined sequence so that later visual examination can determine which shear values should be eliminated because of an improper shear. The bonds shall be examined using at least 70X magnification to determine if the shear tool skipped over the bond (type 5) or the tool scraped or plowed into the surface of the die (type 4). Readings in which either a type 4 or 5 defective shear condition occurred shall be eliminated from the shear data (see Figure 2).Sheared bonds in which a type 3 cratering condition has occurred shall be investigated further to determine whether the cracking and/or cratering is due to the bonding process or the act of shear testing. Cratering caused prior to the shear test operation is unacceptable. Cratering resulting from the act of shear testing shall be considered acceptable and included in the shear data.4.7 Footprint Inspection of Aluminum Wedge BondsAll wire bonding processes to both the die bond pad and the leadframe post shall have a bond footprint inspection performed. For wires too small for bond shear testing (less than 1.25 mils in height at the compressed bonded area), the wire shall be removed at the bond location using a small sharp blade. The removal of the wire shall be sufficient such that the bond interface can be visually inspected and the metallurgical bond area determined. For larger wires after bond shear testing, all devices shall be inspected to examine the failure mode and to determine the bond footprint coverage.Test Method B116JEDEC Standard 22-B116Page 104 Procedure (cont’d)4.8 Bond Shear DataData shall be maintained for each bond sheared. The data shall identify the bond (location, bond diameter, wire material, method of bonding, and material bonded to), the shear strength, and the shear code number.4.9 Shear CodesFor each bond sheared, a code as defined in Figure 2 shall be recorded.5 Failure criteriaThe following failure criteria are not valid for devices that have undergone environmental stress testing or have been desoldered from circuit boards.5.1 Failure Criteria for Ball BondsThe recommended minimum individual and sample average bond shear values are shown in Figure 4 and Table 1. This criteria is applicable to gold wire ball bonds on aluminum alloy bond pads. Other material combinations may require a new set of failure criteria.Alternate minimum bond shear values may be proposed by the supplier if supporting data justifies the proposed minimum values.5.2 Failure Criteria for Aluminum Wedge BondsThe wedge bonds on a part shall be considered acceptable if the minimum shear values are equal to or greater than the manufacturer's tensile strength of the bond wire.In addition, the percent of the bond footprint in which bonding should occur shall be no less than 50%. If it is necessary to control the wire bonding process using SPC for percent coverage, a Cpk value can be calculated to this limit.6 SummaryThe quality level and test conditions are contained within this document unless otherwise specified in the applicable Part Specification and/or Part Drawing.Test Method B116。
- 1、下载文档前请自行甄别文档内容的完整性,平台不提供额外的编辑、内容补充、找答案等附加服务。
- 2、"仅部分预览"的文档,不可在线预览部分如存在完整性等问题,可反馈申请退款(可完整预览的文档不适用该条件!)。
- 3、如文档侵犯您的权益,请联系客服反馈,我们会尽快为您处理(人工客服工作时间:9:00-18:30)。
Wire Bond Strength TestsFebruary 5, 2010Donna and many othersIntroductionWe found that the integrity of the wire bonds made at SiDet do not show signs of degradation after being temperature-cycled to ~20 K.The QUIET receiver modules will be operated at 20 K, so it is important to verify that the wire bonds can withstand temperature cycling from room temperature to cryogenic temperatures. This report presents the data that indicates Al wire bonds to Au are not degraded after temperature cycling six times to near 20 K.The set of bonds serving as “Control Bonds” were not be temperature cycled. This set was bonded and pull-tested as a preliminary study.A different board with the same type of bonding and pull testing as the Control Bonds served as the “Test Bonds”. The bonds will be pull tested at SiDet before and after temperature cycling at Lab 3 to measure bond strength as function of the number of cycle times.The outline of this report is:1. Description of wire bonder and pull-tester2. Description of test data3. Control Bonds3.1 Description of the Control Bond board3.2 Control Bond data analysis4. Test Bonds4.1 Cryostat test setup4.2 Pre-cooling test results4.3 Results from temperature-cycling the wire bonds5. Conclusion1. Description of bonding machine and pull-tester.A K&S 1478 wire bonder was used. The bonds are wedge bonds (not ball bonds).A Dage BT14 bond tester was used. The principle behind wire bond pull-testing is positioning of a hook underneath the wire and pulling in the vertical directions until the bond breaks (destructive testing)Fig. 1.1 (Cartoon) Illustration of pull-testing2. Description of test dataThe data for each pulled bond includes the force required to break the bond in grams and the type of break (0, 1, or 5). The type is described in the Fig. 2.1.Break type Description of break0First bond: foot lifted1First bond: part of foot lifted of tore2First bond: broke at heel3Center (wire) break4Second bond: broke at heel5Second bond: part of foot lifted or tore6Second bond: foot liftedFig. 2.1 Types of wire bond breaksThe raw data is shown in the Appendix. The results of the analyses of the raw data are in Sections 3 and 4.3. Control BondsThe control bonds will not be temperature cycled. They provide a control group should questions arise about the aging of the bonds.3.1 Description of the Control Bond boardThe bond wire was 25 um aluminum wire with 1% silicon. The wire was bonded to gold strips on an alumina substrate.3.2 Control Bond data analysisThe distribution of the Control Bond break forces is shown in Fig. 3.1. The bin size is 0.5 g.Fig. 3.1 Pull test results for all Control BondsIt was noticed that the type of break was a function of breaking force. Most of the bonds that broke with a lower force were type 0 (first bond lifted) while the bonds that broke with higher force were type 1 (first bond foot break). This can be seen in the raw data forthe Control Bonds in the Appendix. The data for the Control Bonds shown in theAppendix was sorted as a function of breaking force.4. Test BondsThe bond wire was 25 um aluminum wire with 1% silicon. The wire was bonded to gold strips. Boards from a previous CDF project were used for bonding. The bonds have been divided into 8 sections as shown in Fig. 4.1. Sections 1-6 are from the same lot of CDF boards. Sections 7 and 8 are on boards from a different lot.Sections 1 and 2 have two rows of bonds on each strip (Fig. 4.2). The others have one row of bonds per gold strip (Fig. 4.3).The bonds are about 1 mm long and about 130 um high as shown in Figs. 4.4 and 4.5.There are shorter bonds, orthogonal to the rows of bonds, bridging the gap between sections 1 and 2, which can be seen in Fig. 4.2. These are ~0.5 mm long and about 100 um high. Similarly, there are shorter bonds bridging the gap between the top and bottom halves of sections 7 and 8. These are different from the bonds between sections 1 and 2, for they bridge a gap with a shorter vertical step.All of the gap bonds are too short and do not have enough height to position the pull tester loop underneath them to permit a pull test.Fig. 4.1 Test bond layout Gap bondsGap bondsSection 1 Section 2Fig. 4.2 There are two rows of bonds per gold strip in sections 1 and 2. These are 1 mm long and 130 um high. Also shown are bonds bridging the gap between Sections 1 and Section 2. These are 0.5 mm long and 100 um high.Fig. 4.3 Sections 3-8 have only one row of bonds along each gold strip.Fig. 4.5 Another view of the wire bond dimensions.4.1 Cryostat test setupThe test bond assembly mounted is shown mounted int eh cryostat in Fig. 4.6. The temperature controller was a Lakeshore 325. The temperature sensors were Lakeshore silicon diodes, model DT-670C-SD.Fig. 4.6 Test bond assembly in the cryostat in lab 3, ready for cooling Note that the board was enclosed in a metal box (heat shield) before cooling4.2 Pre-cooling test resultsThe distribution of forces required to break the Test Bonds are shown in Fig. 4.6-4.8. Fig.4.6 includes data for all Test Bonds. It was noticed that the breaking force for groups 1-6 was lower (mean=6.11 g) than that for groups 7 and 8 (mean=7.43 g), so the data was also plotted separately for these and is shown in Figs. 4.7 and 4.8. Bin size is 0.5 g.Fig. 4.6 Pull test results for all Test Bond dataFig. 4.7 Pull test results for Test Bonds in Sections 1-64.3 Results from temperature-cycling the wire bondsA subset of the bonds in each section was pull-tested after each cooling cycle (or sometimes after 2 cooling cycles). The distributions of the forces required to break the bonds after each cooling (or sometimes after 2 cooling cycles) are shown in Fig 4.11. The mean breaking force is shown in the tables of Fig. 4.12. It can be seen that the average force required to break the bonds was nearly independent of the number of cooling cycles, indicating the bonds do not lose strength when cooled to cryogenic temperatures.According to the datasheet for the 25-um diameter 1% Si Al wire, the force required to break the wire (tensile strength) is between 14 and 20 grams, depending on the temper condition of the wire (Fig. 4.9).Fig. 4.9 Excerpt from the datasheet for 1% Si Al wireLink to datasheet: /datasheets/spm/Aluminum.pdfExamination of the force diagram shown in Fig, 4.10, it can be seen that the bond-breaking force measured by the Dage wire puller, F Dage, always corresponded to less than the 14 grams required to break the wire (Fig. 4.9), as expected.Fig. 4.10 Minimum force to break the wireFig. 4.11 Plots of wire bond breaking force for all sections (top), sections 1-6 (middle),and sections 7-8 (bottom).Fig. 4.12 Table of mean breaking force for all sections (top), sections 1-6 (middle), and sections 7-8 (bottom).APPENDIX。