saej864v001
SAE_J1128_2000_(中文版)_低压初级电缆

3
S.P.L CABLE
SAE J1128-2000
5 一般要求 对于每种型号的电缆 成品应满足图表 2 规定的所有试验的要求
图表 2 一般要求 条款 5
条款
项目
要求 TWP GPE HDT
STS HTS
TWE GTE HTE
TXL GXL SXL
5 一般要求
5.1 导体
5.2 绝缘
5.3 外径
*
1 适用范围 本 SAE 标准适用于额定直流电压 60V(交流 25V)或以下地面车辆电气系统用低压初级电缆 文中的试
验旨在检验电缆在有限流体和物理应力的作用下正常使用时的质量
2 参考文献 2.1 适用出版物 -下列出版物因被本标准引用而成为本标准的一部分 除非另有规定 SAE 出版物应使用 最新版本 2.1.1 SAE 出版物
ES1A-ES1J PDF规格书

NUMBER OF CYCLES AT 60 Hz
FIG. 4-TYPICAL REVERSE CHARACTERISTICS
1,000
100
10
TJ=100 C 1
0.1 TJ=25 C
0.01 0
20
40
60
80
100
PERCENT OF PEAK REVERSE VOLTAGE,%
FIG. 6-TYPICAL TRANSIENT THERMAL IMPEDANCE
FIG. 5-TYPICAL JUNCTION CAPACITANCE
200
100
TJ=25 C
10
1
0.1
1.0
10
100
REVERSE VOLTAGE,VOLTS
TRANSIENT THERMAL IMPEDANCE, C/W
INSTANTANEOUS REVERSE CURRENT, MICROAMPERES
SYMBOLS ES1A ES1B ES1C ES1D ES1E ES1G ES1J
Maximum repetitive peak reverse voltage Maximum RMS voltage Maximum DC blocking voltage Maximum average forward rectified current at TL=55 C Peak forward surge current 8.3ms single half sine-wave superimposed on rated load (JEDEC Method) Maximum instantaneous forward voltage at 1.0A Maximum DC reverse current TA=25 C at rated DC blocking voltage TA=100 C Maximum reverse recovery time (NOTE 1) Typical junction capacitance (NOTE 2)
优倍G系列仪表 - 产品样本及技术手册(2022)说明书

关于优倍安全栅国家标准主编单位中石化安全栅框架协议单位工信部两化融合贯标单位工信部智能工厂标准化示范验证单位江苏省电涌保护器工程技术研究中心南京优倍电气有限公司成立于2002年,江苏省高新技术企业。
公司致力于安全栅、隔离器、温度变送器、电涌保护器、安全继电器等工业信号接口仪表的研发制造,并为以上产品国标组组长单位,主持起草《隔离式安全栅》等国家标准。
优倍电气是国内该专业市场的主要供应商之一,品牌及品质享受盛誉。
公司为工信部两化融合体系贯标试点单位、工信部智能工厂标准化示范验证单位、江苏省、南京市首批示范智能工厂。
先后被江苏省省委、省政府授予百家江苏省优秀企业、江苏制造突出贡献奖优秀企业、江苏科技小巨人企业等光荣称号。
公司总部及新建并投产运营的优倍智造园均位于南京江宁经济技术开发区,占地面积30亩,全公司现有员工160余名,建有江苏省研究生工作站、江苏省电涌保护器工程技术研究中心、南京市工程应用研究中心,在工业测控领域有着深厚的科研基础及广泛的应用经验,产品获得多项国内、国际认证。
SILIEC 61508目录G系列隔离式安全栅(端子供电)通用型温度变送(常用产品型号)NPEXA-G01 (单通道,1路4 ~ 20mA输出,智能型)NPEXA-G011 (单通道,2路4 ~ 20mA输出,智能型)NPEXA-G0D11 (双通道,2路有源/无源4 ~ 20mA输出,智能型)热电偶输入(常用产品型号)NPEXA-G11 (单通道,1路4 ~ 20mA输出,智能型)NPEXA-G111 (单通道,2路4 ~ 20mA输出,智能型)NPEXA-G1D11 (双通道,2路有源/无源4 ~ 20mA输出,智能型)NPEXA-G11L (单通道,1路4 ~ 20mA输出,回路供电,智能型)热电阻输入(常用产品型号)NPEXA-G21 (单通道,1路4 ~ 20mA输出,智能型)NPEXA-G211 (单通道,2路4 ~ 20mA输出,智能型)NPEXA-G2D11 (双通道,2路有源/无源4 ~ 20mA输出,智能型)NPEXA-G27 (单通道,1路1:1电阻输出,智能型)NPEXA-G277 (单通道,2路1:1电阻输出,智能型)NPEXA-G21L (单通道,1路4 ~ 20mA输出,回路供电,智能型)电流输入(常用产品型号)NPEXA-GM31 (单通道,1路4 ~ 20mA输出,HART通过型)NPEXA-GM311 (单通道,2路4 ~ 20mA输出,HART通过型)NPEXA-GM3D11 (双通道,2路有源/无源4 ~ 20mA输出,HART通过型) NPEXA-G31 (单通道,1路4 ~ 20mA输出,智能型)NPEXA-G311 (单通道,2路4 ~ 20mA输出,智能型)NPEXA-G3D11 (双通道,2路有源/无源4 ~ 20mA输出,智能型)NPEXA-GM31L (单通道,1路4 ~ 20mA输出,回路供电)NPEXA-GM3D11L (双通道,2路4 ~ 20mA输出,回路供电)NPEXA-G31L (单通道,1路4 ~ 20mA输出,回路供电,智能型)模拟量输出(常用产品型号)NPEXB-GM31 (单通道,1路4 ~ 20mA输出,HART通过型)01 01 0203 03 04 0506 06 07 08 08 0910 10 11 12 12 13 14 14 1516INPEXB-GM311 (单通道,2路4 ~ 20mA输出,HART通过型)NPEXB-GM3D11 (双通道,2路4 ~ 20mA输出,HART通过型)NPEXB-GM31L (单通道,1路4 ~ 20mA输出,回路供电)NPEXB-GM3D11L (双通道,2路4 ~ 20mA输出,回路供电)电压信号输入(常用产品型号)NPEXA-G41 (单通道,1路4 ~ 20mA输出,智能型)NPEXA-G411 (单通道,2路4 ~ ~20mA输出,智能型)NPEXA-G4D11 (双通道,2路有源/无源4 ~ 20mA输出,智能型)开关量输入NPEXA-G511 (单通道,1路继电器触点输出)NPEXA-G5111 (单通道,2路继电器触点输出)NPEXA-G5D111 (双通道,2路继电器触点输出)NPEXA-G512 (单通道,1路晶体管输出)NPEXA-G5122 (单通道,2路晶体管输出)NPEXA-G5D122 (双通道,2路晶体管输出)开关量输出NPEXB-G512 (单通道,1路45mA电流输出)NPEXB-G5D12 (双通道,2路45mA电流输出)NPEXB-G512L (单通道,1路45mA电流输出,回路供电)NPEXB-G5D12L (双通道,2路45mA电流输出,回路供电)频率量输入(常用产品型号)NPEXA-G61P2 (单通道,1路4 ~ 20mA输出)NPEXA-G611P2 (单通道,2路4 ~ 20mA输出)NPEXA-G67P2 (单通道,1路1:1频率输出)NPEXA-G677P2 (单通道,2路1:1频率输出)数字通讯输入(常用产品型号)NPEXA-G711Z (单通道,1路RS-485输入,1路RS-485输出,9V/140mA) NPEXA-G711 (单通道,1路RS-485输入,1路RS-485输出,可调配电) NPEXA-G713 (单通道,1路RS-485输入,1路RS-422输出,可调配电) NPEXA-G731 (单通道,1路RS-422输入,1路RS-485输出,可调配电) NPEXA-G733 (单通道,1路RS-422输入,1路RS-422输出,可调配电)16 16 17 1718 18 1920 20 21 22 22 2324 24 25 2526 26 27 2728 29 30 31 32II电位器输入NPEXA-G91 (单通道,1路4 ~ 20mA输出)NPEXA-G911 (单通道,2路4 ~ 20mA输出)G系列模块表(端子供电)温度变送器毫伏中继器电位器变送器模拟量输入隔离器信号智能隔离器开关量输入隔离器频率变送器频率中继器产品附录组态工具33 3334 37 38 40 42 46 47 4849III01*注:电压输出接线参照电流接线 5+、6-, 7+、8-。
SAEJ2332v001
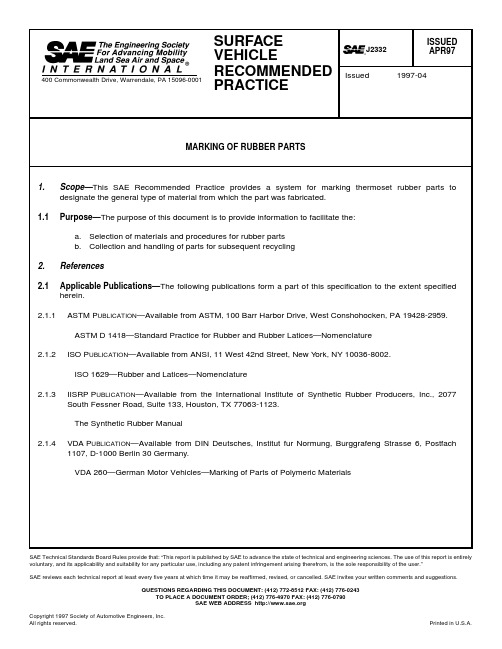
SAE Technical Standards Board Rules provide that: “This report is published by SAE to advance the state of technical and engineering sciences. The use of this report is entirely voluntary, and its applicability and suitability for any particular use, including any patent infringement arising therefrom, is the sole responsibility of the user.”SAE reviews each technical report at least every five years at which time it may be reaffirmed, revised, or cancelled. SAE invites your written comments and suggestions.QUESTIONS REGARDING THIS DOCUMENT: (412) 772-8512 FAX: (412) 776-0243TO PLACE A DOCUMENT ORDER; (412) 776-4970 FAX: (412) 776-0790SAE WEB ADDRESS 2.2Related Publications—The following publications are provided for information purposes only and are not arequired part of this document.2.2.1ISO P UBLICATIONS—Available from ANSI, 11 West 42nd Street, New Y ork, NY 10036-8002.ISO 1043-1—Plastics—Symbols—Part 1: Basic polymers and their special characteristicsISO 1043-2—Plastics—Symbols—Part 2: Fillers and reinforcing materialsISO 11469—Plastics—Generic identification and marking of plastic products3.Description3.1The system is based on standard symbols for terms relating to rubber (ISO 1629). Most commonly usedsymbols, including some not covered by ISO are shown in Table 1. In addition, symbols for commerical rubber materials are shown in Table 2, derived from the latest version of the Synthetic Rubber Manual and symbols for commonly used automotive fillers/reinforcements derived from ISO 1043-2 are shown in Table D1.3.2If additional symbols are required to cover new materials, the form in Appendix A shall be completed andsubmitted to SAE. New symbols will be included in the next revision to this document.TABLE 1—SYMBOLS FOR MARKING RUBBER PARTSElastomeric “Family” NameChemical Composition of Polymer Chain Common Name(1)StandardSymbol(Previous)(2)(3)Class MCopolymers of ethyl or other acrylate and a small amount of monomerwhich facilitates vulcanizationACMCopolymers of ethyl and other acrylates and ethylene AEM Copolymers of ethyl or other acrylate and acrylonitrile ANM Chloro-polyethylene CM Polychloro-trifluoro-ethylene CFM Chloro-sulfonyl-polyethylene CSM Terpolymer of ethylene, propylene, and a diene with the residualunsaturated portion of the diene in the side chainEPDM Copolymers of ethylene and propylene EPM Copolymers of ethylene and vinyl acetate EVM Copolymer of tetrafluoroethylene and propylene FEPM Perfluoro rubbers of the polymethylene type having all substituent groupson the polymer chain either fluoro, perfluoroalkyl, or perfluoroalkoxy groupsFFKMFluoro rubber of the polymethylene type having substituent fluoro andperfluoroalkyl or perfluoroalkoxy groups on the polymer chainFKM Styrene-ethylene/butylene SEBM Styrene-ethylene/propylene SEPM Class OPolychloromethyl oxirane (epichlorohydrin polymer).CO Ethylene oxide (oxirane) and chloromethyl oxirane (epichlorohydrincopolymer)ECO Epichlorohydrin-ethylene oxide-allylglycidylether terpolymer GECO Polypropylene oxide and allyl glycidyl ether GPOClass QSilicone rubber having fluorine, vinyl, and methyl substitute groups on the polymer chain.FVMQ Silicone rubbers having both methyl and phenyl, and vinyl substituent groups on the polymer chainPMQ Silicone rubbers having both methyl and phenyl substituent groups on the polymer chainPVMQ Silicone rubbers having only methyl substituent groups on the polymer chainMQ Silicone rubber having both methyl and vinyl substitute groups on the polymer chain VMQClass RAcrylate-butadiene ABR Bromo-isobutene-isoprene BIIR ButadieneBR Chloro-isobutene-isoprene CIIR ChloropreneCR Hydrogenated acrylonitrile-butadiene HNBR Isobutene-Isoprene IIR Isoprene, synthetic IR Acrylonitrile-butadiene NBR Acrylonitrile-chloroprene NCR Acrylonitrile-isoprene NIR Natural rubberNR Vinylpyridine-butadiene PBR Vinylpyridine-styrene-butadiene PSBR Sytrene-butadiene SBR Sytrene-chloroprene SCR Styrene-isoprene rubbers SIR Carboxylic-styrene-butadiene XSBR Carboxylic-acrylonitrile-butadieneXNBR Carboxylic-hydrogenated-acrylonitrile-butadiene XHNBR Class TRubber having either a -CH 2-CH 2-O-CH 2-O-CH 2-CH 2- group oroccasionally a -R-group, where R is an aliphatic hydrocarbon between the polysulfide linkages in the polymer chainOT Rubber having either a -CH 2-CH 2-O-CH 2-O-CH 2-CH 2- group and -R-groups that are usually -CH 2-CH 2- but occasionally other aliphatic groups between the polysulfide linkages in the polymer chain EOTClass UTerpolymer of tetrafluoroethylene, trifluoronitrosomethane, and nitrosoperfluorobutyric acid AFMU Polyester urethane AU Polyether urethaneEU TABLE 1—SYMBOLS FOR MARKING RUBBER PARTS (CONTINUED)Elastomeric “Family” NameChemical Composition of Polymer ChainCommon Name (1)Standard Symbol(Previous)(2)(3)Class ZRubber having a -P=N-chain and having fluoroalkoxy groups attached to the phosphorus atoms in the chainFZ Rubber having a -P=N-chain and having aryloxy (phenoxy and substituted phenoxy) groups attached to the phosphorus atoms in the chain PZmon names and trademarks for each plastic “family” name are shown in Appendix C, and are intended as a guide to aid the user in selecting the correct standard symbol for the material under consideration.2.(Previous)—SAE JXXXX or other commonly used marking parts.3.Symbols listed as (“Previous Symbols”) are former designations and should not be used.TABLE 2—SYMBOLS FOR COMMERCIAL RUBBER MATERIALSCommercial MaterialsStandard Symbol(Previous)Class MACRALEN, A, BayerACMEUROPRENE AR, C, L & R, EniChem Elastomeri S.r.I.JSR, Japan Synthetic RubberCROSLENE, T akeda Chemical Industries ACRON, T ohpe Corp.HYTEMP , NIPOL AR, Zeon Chemicals Inc.VAMAC, DuPont Dow Elastomers AEM ANM TYRIN, DuPont Dow Elastomers CM KEL-F , DYNEONCFM HYP ALON, DuPont Dow Elastomers CSM BUNA EP , Bayer Buna GmbH, Bayer Corp.EPDM KELTAN, DSM Elastomers Europe B.V ., DSM Copolymer Inc.NORDEL, DuPont Dow Elastomers DUTRAL TER, EniChem Elastomeri S.r.I.VIST ALON, Exxon Chemical Co., Butyl Americas HERLENE, Herdillia Unimers Ltd.MITSUI-EPT, Mitsui Petrochemical Industries, Inc.NITRIFLEX EP , Nitriflex S.A.ESPRENE, Sumitomo Chemical Co., LTD.ElastoFlo, Union Carbide Corporation ROYALENE, Uniroyal Chemical Co.SUPRENE, Yukong Ltd.Keltan, DSM Copolymer Inc., DSM Elastomers Europe B.V .EPM DUTRAL CO., EniChem Elastomeri S.r.I.VIST ALON, Exxon Chemical Co., Societe du Caoutchouc BUNA EP , Bayer Corp.TOT AL EP , Societe du Caoutchouc Butyl ElastoFlo, Union Carbide Corporation ROYALENE, Uniroyal Chemical Co.SUPRENE, Yukong Ltd.LEVAPREN, Bayer AG EVM EAMAFLAS ™TFE, DYNEONFEPM FFKMTABLE 1—SYMBOLS FOR MARKING RUBBER PARTS (CONTINUED)Elastomeric “Family” NameChemical Composition of Polymer ChainCommon Name (1)Standard Symbol(Previous)(2)(3)TABLE 2—SYMBOLS FOR COMMERCIAL RUBBER MATERIALS (CONTINUED) Commercial Materials Standard Symbol(Previous)FLUOREL, DYNEON FKM?, Kazan NPO Zavod SKSYLUN, Shin-Etsu Chemical Co., Ltd.TECHNOFLON, MontifluosVITON, DuPont Dow ElastomersSEBMSEPMClass OHYDRIN, Zeon Chemicals Inc.COGECHRON, Nippon Zeon Co. Ltd.HYDRIN, Zeon Chemicals Inc.ECOGECHRON, Nippon Zeon Co. Ltd.GECHRON, Nippon Zeon Co., Ltd.GECOHYDRIN, Zeon Chemicals Inc.PAREL, Zeon Chemicals Inc.GPOClass QSILASTIC, Dow Corning Corporation FVMQSILPLUS, General Electric Company?, Kazan NPO Zarod SKPOWERSIL, Wacker-Chemie GmbHSILASTIC, Dow Corning Corporation PMQSILASTIC, Dow Corning Corporation PVMQ?, Kazan NPO Zarod SKPOWERSIL, Wacker-Chemie GmbHSILASTIC, Dow Corning Corporation MQTUFGL, General Electric CompanySILASTIC, Dow Corning Corporation VMQSILPLUS, General Electric Company?, Kazan NPO Zarod SKElastosil, Wacker Silicones Corp., Wacker-Chemie GmbHElektorguard, Wacker Silicones Corp.Powersil, Wacker Silicones Corp.SILOPREN, Bayer AG QClass RBUTAKON, Doverstrand Ltd.ABRPOL YSAR Bromobutyl, BROMOBUTYL, Bayer Rubber Inc.BIIREXXON BROMOBUTYL, EXXON SB BROMOBUTYL, Exxon ChemicalBROMOBUTYL, Japan Butyl Company, Ltd.CISDENE, American Synthetic Rubber Corporation BRE-BR, Ameripol Synpol CompanyADADENE, Asahi Chemical Industry Co., Ltd.AUSTRAPOL, Australian Synthetic Rubber Co., Ltd.BUNA CB, BUNA VI, BayerCOPERFLEX BR, Companhia Pernambucana de BorrachaSintetica (COPERBO)?, Efremov Synthetic Rubber EnterpriseEUROPRENE CIS, Enichem Elastomeri S.r.I.EUROPRENE NEOCIS, Enichem Elastomers S.p.A.DIENE, Firestone Synthetic Rubber & Latex CompanyTABLE 2—SYMBOLS FOR COMMERCIAL RUBBER MATERIALS (CONTINUED) Commercial Materials Standard Symbol(Previous)BUDENE, Goodyear Tire & Rubber CompanyCISAMER, Indian Petrochemicals Corporation, Ltd.ASAPRENE, Japan Elastomer Co., Ltd.JSR, Japan Synthetic Rubber Co., Ltd.BRAFDENE, NEODENE, Karbochem Division of Sentrachem Ltd.KRASOL, Kaucuk Elastomers Div.AUSTRAPOL, Kemcor AustraliaBUNA, Kombinat VEB, Chemische WerkeKOSYN, Korea Kumho Petrochemical Co., Ltd.SOLPRENE, Negromex, S.A., de C.V.NIPOL, Nippon Zeon Co., Ltd.PETKAUCUK, Petkim Petrokimya A.S.FINAPRENE, Petrochim N.V.TAKTENE, Bayer Corp.CALPRENE, Repsol Quimica S.A.BUTAKON, Revertex Ltd.CARIFLEX BR, Shell Chemicals EuropeTAIPOL, Taiwan Synthetic Rubber CorporationUBEPOL-BR, UBEPOL-VCR, UBE Industries, Ltd.KER, Zaklady Chemiczne OswiecimCHLOROBUTYL, Bayer Rubber Belguim CIIREXXON CHLOROBUTYL, EXXON SB CHLOROBUTYL, ExxonChemical InternationalPOL YSAR Chlorobutyl, Bayer Rubber Inc.CHLOROBUTYL, Japan Butyl Company, Ltd.BAYPREN, Bayer CRDenka Chloroprene, Denki Kagaku Kogyo, K.K.BUTACLOR, DISTUGILNEOPRENE, DuPont Dow ElastomersSkyprene, TOSOH CorporationTHERBAN, Bayer Corporation HNBRZETPOL, Zeon Chemicals Inc.BUTYL, POL YSAR BUTYL, Bayer IIREXXON BUTYL, EXXON SB BUTYL, Exxon ChemicalAmericasJSR BUTYL, BUTYL, Japan Butyl Co., Ltd.JSR, Japan Synthetic Rubber Co., Ltd.NATSYN, Goodyear Tire & Rubber Company IRAFPRENE, Karbochem Division of Sentrachem Ltd.KURARA Y, Kuraray Company Ltd.?, NizhnekamskneftechimPERBUNAN N, Bayer NBRKRYNAC, BayerHYCAR EMULSION, B.F. GoodrichBREON, Zeon Chemicals Europe, Ltd.BUTAKON, Doverstrand Ltd.Nysyn, Nysynblak, DSM Elastomers Europe B.V., DSMCopolymer, Inc.CHEMIGUM, Goodyear Tire & Rubber Company, GoodyearChemicals EuroperEUROPRENE N, EniChem Elastomeri S.r.I.TABLE 2—SYMBOLS FOR COMMERCIAL RUBBER MATERIALS (CONTINUED) Commercial Materials Standard Symbol(Previous)HUMEX, Huels Mexicanos, S.A.NBRJSR, Japan Synthetic Rubber Co., Ltd.BUNA, Buna GMBHKOSYN, Korea Kumho Petrochemical Co., Ltd.?, Krasnoyarsk SR Plant Co.NITRIFLEX N & NP, Nitriflex S.A. Industria e ComercioNIPOL, Nippon Zeon Co., Ltd.DAREX, Organic Chem. Div., W.R. Grace & Co.ARNIPOL, P ASA S.A.TYLAC, Reichhold Chemicals, Inc.REVINEX, Revertex Ltd.CHEMAPRENE, Synthetics & Chemicals Ltd.SAVINEX, Synthetic Latex Company (Pty.) Ltd.CROSLENE, T akeda Chemical IndustriesPARACRIL, Uniroyal Chemical Company, Inc.NCRNIRNRPBR? Omsk Kanchuk Co.PSBRAMERIPOL, SYNPOL, TRAXOL, MICROBLAK, ROVENE,SBRAmeripol Synpol Corp.TUFDENE, Asahi Chemical Industry Co., Ltd.AUSTRAPOL, Australian Synthetic Rubber Co., Ltd.BUTANOL, BASF Corp.BUNA BL, SL, VSL, POL YSAR S, SS, KRYLENE SBR, KRYNOL, BayerBORG-WARNER LATEX, Borg-Warner (Australia) Ltd.BUNA, Buna GmbHKRALEX, Chemopetrol-KaucukCAROM, Combinatul Petrochimic BorzestiCOPERFLEX SBR, COPERBOCOPO, CARBOMIX, DSM Elastomers Europe B.V., DSMCopolymer, Inc.REVINEX, Doverstrand Ltd.GENTRO, GENTRO-JET, Dynagen, Inc.EUROPRENE, HS, EUROPRENE SOL, SOL S, EniChemElastomeri S.r.I.DURADENE, STEREON, Firestone Synthetic Rubber & Latex CompanyPLIOLITE, PLIOFLEX, Goodyear Tire & Rubber CompanyBUNATEX, LIPOLAN, LITEX, Hüls AGHUMEX, Hüls Mexicanos, S.A.ARLA TEX, Industrias Resistol S.A.ASAPRENE, Japan Elastomer Co., Ltd.JSR, Japan Synthetic Rubber Co., Ltd.SBRAFPOL, AFSOL, Karbochem Division of Sentrachem Ltd.?, Kauchuk Co.KRALEX, Kaucuk a.s. Elastomers DivisionAUSTRAPOL, KEMCOR AustraliaKOSYN, Korea Kumho Petrochemical Co., Ltd.TABLE 2—SYMBOLS FOR COMMERCIAL RUBBER MATERIALS (CONTINUED) Commercial Materials Standard Symbol(Previous)ROVENE, Mallard Creek PolymersDIAPOL, Mitsubishi Chemical CorporationBULTEX, NeftochimSOLPRENE, Negromex, S.A., de C.V.NITRIFLEX, Nitriflex S.A. Industria e ComércioNIPOL, Nippon Zeon Co., Ltd.?, Omsk Kauchuk Co.ARPOL, PASA S.A.PETKAUCUK, Petkim Petrokimya A.S.FINAPRENE, Petrochim N.V.PETROFLEX, PETROLATEX, Petroflex Industria e Comercio S.A.TYLAC, Reichhold Chemicals, Inc.CALPRENE, Repsol Quimica S.A.REVINEX, Revertex Ltd.CARIFLEX S, Shell Nederland ChemieSUMITOMO SBR, Sumitomo Chemical Company Ltd.NAUGATEX, PYRA TEX, SN, Sumitomo Naugatuck Co., Ltd.SYNAPRENE, Synthetics & Chemicals Ltd.AFTEX, Synthetic Latex Company (Pty.) Ltd.TAIPOL, Taiwan Synthetic Rubber Corporation?, Togliattisyntezkauchuk Co.?, Voronezhsyntezkachuk Co.KER, LBS, Zaklady Chemiczne OswiecimDAREX, W.R. GraceSCRSIRJSR, Japan Synthetic Rubber XSBRKOSYN, Korea Kumho Petrochemical Co., Ltd.NIPOL, Nippon Zeon Co., Ltd.NITRIFLEX NTL, VP, Nitriflex S.A. Industria e Comércio?, Omsk Kauchuk Co.SYNTHOMER, Synthomer Chemie GmbH?, Voronezhsyntezkachuk Co.LBSK, Zaklady Chemiczne OswiecimCHEMIGUM, Goodyear Tire & Rubber Co.XNBRNIPOL, Nippon Zeon Co. Ltd.XHNBROTEOTClass UAFMUUREP AN, Bayer AG AUESTANG TPU, The B.F. Goodrich Co.VIBRA THANE, Uniroyal Chemical Company Inc.ADIPRENE, Uniroyal Chemical Company Inc.ESTANG TPU, The B.F. Goodrich Co.EUVIBRA THANE, Uniroyal Chemical Company Inc.ADIPRENE, Uniroyal Chemical Company Inc.e of Marking Symbols4.1In view of the wide variety of parts used in substantially different assembly situations, this document does not prescribe the location, and/or method of marking; however, the following guidelines should be followed:4.1.1Field service people should be informed regarding the material from which the part is made so suitable recycling procedures may be used.4.1.2Wherever practicable, the marking should be located where it may be observed while the part is in use.Consideration should be given to the use of multiple markings on large or complex-shaped parts.4.1.3From the standpoint of field service people, marking on the outside surface of the part (in an unobtrusive location from the viewpoint of the owner) is preferred.4.1.4Markings applied with inks, dyes, or paints, should not bleed, run, smudge, or stain other materials which may come in contact with the marking.4.1.5Marking should be designed to remain legible during the entire life of the part.4.1.6Markings which are molded into the part are preferred since they are permanent and do not require separate manufacturing operations as do those applied to the surface of the part after molding. Molded in markings should not create a stress concentration site which could result in premature cracking of the part.4.1.7The recommended practice for the standard marking symbol (Figure 1) is consistent with ISO 11469 and VDA 260. Dimensions are suggested guidelines. Markings should be proportional to part size.FIGURE 1—STANDARD MARKING SYMBOL4.1.8E XAMPLES —See Figure 2.FIGURE 2—EXAMPLES OF STANDARD MARKING SYMBOLS4.1.9For small parts that cannot accommodate the 3.0 mm letter guidelines, the use of smaller letters should be considered in lieu of not marking the part at all.Class ZFZ PZTABLE 2—SYMBOLS FOR COMMERCIAL RUBBER MATERIALS (CONTINUED)Commercial MaterialsStandard Symbol(Previous)4.2For parts using rubber materials containing 10% or more by mass fillers/reinforcements, use the samedesignation for the “family name” as defined in Table 1 and, in addition, alpha codes from ISO 1043-2, followed by a numeric value representing the nominal percentage of filler/reinforcer. The polymer family codes shall be separated from the filler/reinforcement codes and value by use of a hyphen.4.2.1E XAMPLES—See Figure 3.FIGURE 3—EXAMPLES OF STANDARD MARKING SYMBOLS FOR RUBBER WITH FILLEROR REINFORCEMENT LEVELS ≥10% BY WEIGHT4.3Parts fabricated from two or more materials, some of which are not readily visible, may be marked so theprimary visible material is identified first by the system specified in 3.1 followed by the identification of the other material(s) where the individual identification(s) is separated by a comma. Identify the main mass component by underlining.4.3.1E XAMPLES—For a product made of two components, see Figure 4.FIGURE 4—EXAMPLES OF STANDARD MARKING SYMBOLS FOR MIXED/BLENDED5.Notes5.1Additional Information—Appendices C and D are cross reference listings designed to assist the user inrelating SAE marking symbols to common rubber names and supplier trademarks.PREPARED BY THE SAE COMMITTEE ON AUTOMOTIVE RUBBER SPECIFICATIONSAPPENDIX AREQUEST TO ADD NEW MARKING SYMBOLS AND/OR TRADEMARKSA.1The following procedure is to be utilized to apply for inclusion of new marking symbols and/or trademarks intoSAE JXXXX.A.1.1Complete Form A1. See Figure A1.FIGURE A1—REQUEST TO ADD NEW MARKING SYMBOLS AND/OR TRADEMARKS FORMAPPENDIX BPROCESS FLOW CHART—ADDING NEW SYMBOLS TO JXXXXPreface—The procedure shown in Appendix B will be used to process requests for addition of new symbols.Requests to add trademarks to cross reference listings will be handled as editorial changes.B.1See Figure B1.FIGURE B1—PROCESS FLOW CHART—ADDING NEW SYMBOLS TO JXXXXAPPENDIX CCROSS REFERENCE—SYMBOLS TO COMMON NAMES/TRADEMARKSC.1See Table C1.TABLE C1—CROSS REFERENCE—SYMBOLS TO COMMON NAMES/TRADEMARKS Standard Symbol Previous Example of Common Names and/or Trademarks(1)ABRACM Polyacrylic/ACRON ACRALEN A, CROSLENE, EUROPRENE, HYTEMP, NIPOL AR AEM EEA Ethylene/Acrylic/VAMACAFMUANMAU Urethane/ADIPRENE, ESTANG TPU, VIBRA THANE, UREP ANBIIR Bromobutyl/Exxon and PolysarBR Polybutadiene/AUSTRAPOL, ASADENE, ASAPRENE, BUDENE, BUNA, CALPRENE,CARIFLEX, CISAMER, COPERFLEX, DIENE, EUROPRENE CIS, FINAPRENE, INTENE,INTOLENE, JSR, KER, KOSYN, NIPOL, PETKAUCUK, SOLPRENE, TAKTENE, T AIPOL,UBEPOLCIIR Chlorobutyl/Exxon and PolysarCFMCM Chloronated Polyethylene, TYRINCR Neoprene or Chloroprene/BAYPREN, BUTACLOR, CHLOROPRENE, DENKA-USA,NEOPRENE, SKYPRENECSM Chlorosulfonated Polyethylene/HYP ALONECO Epichlorohydrin (copolymer)/HYDRINEOTEPDM Ethylene Propylene/BUNA AP, DUTRAL TER, EPsyn, ESPRENE, KELTAN, MITSUI-EPT,NITRIFLEX EP, NORDEL, POLYSAR EPDM, ROYALENE, SUPRENE, TOTAL EP,VISTALONEPM Ethylene propylene (copolymer)/DUTRAL, KELTAN, POL YSAR EPM, ROYALENE,SUPRENE, TOTAl EPEVM/LEVAPRENEU Urethane/ADIPRENE, VibrathaneFEPM/AFLAS™ TFEFFKMFKM Fluorocarbon, Fluoroelastomer/FLUOREL™ , SYLUN, VITON™FVMQ Fluorosilicone, Fluoro-vinyl-methyl silicone/SILASTIC, SILPLUSGPO/PARELHNBR Hydrogenated Nitrile/THERBAN, ZETPOLIIR Butyl/Polysar BUTYL/Exxon BUTYLIR Synthetic Polyisoprene/KURARAY, NA TSYNMQ Methyl silicone/TUFGL, SILASTICNBR Nitrile/ARNIPOL, CHEMIGUM, KRYNAC, KOSYN, NIPOL, NYSYN, PARACRIL,PERBUNAN N, TYLACNCRNIRNR NaturalOTPBRPMQ Methyl-phenyl siliconePSBRTABLE C1—CROSS REFERENCE—SYMBOLS TO COMMON NAMES/TRADEMARKS (CONTINUED) Standard Symbol Previous Example of Common Names and/or Trademarks(1)PVMQ Methyl-phenyl-vinyl siliconePZSBR Styrene-Butadiene/AFPOL, AFSOL, AMSYN, AMERIPOL, ARPOL, COPO, CARBOMIX,DAREX, DIAPOL, DURADENE, GENTRO, GENTRO-jet, HUMEX, KRYLENE, KRYNOL,NITRIFLEX, NIPOL, PLIOFLEX, PLIOLITE, SOLPRENE, STEREON, SYNPOL, TYLAC SCRSEBMSEPMVMQ Methyl-Vinyl Silicone/ELASTOSIL, POWERSIL, SILASTIC, SILPLUSXSBR Carboxylated styrene-butadiene/KOSYN, LBSK, NITRIFLEX NTL, SYNTHOMERXNBR Carboxylated nitrile/CHEMIGUM/NIPOLXHNBR Carboxylic-hydrogenated-acrylonitrile-butadiene1.The trademarks listed are intended as a guide to aid the user in selecting the correct standard SAE symbol for the materialunder consideration. It is not intended or implied that the listing is a material apoproval for any given specification or appli-cation nor is the listing complete for any one plastic “family” name since additional materials may be available which are not marketed under a trademark.APPENDIX DSYMBOLS FOR FILLERS AND REINFORCING MATERIALSD.1See Table D1.TABLE D1—SYMBOLS FOR FILLERS AND REINFORCING MATERIALSFillers and Reinforcing Materials (1)1.Mixtures of fillers may be shown in parentheses by combining the relevant symbolswith the “+” sign.Standard Symbol (Previous)Aramid fibersAF Carbon fibersCF Glass fibersGF Glass matGM Metal MRationale—Not applicable.Relationship of SAE Standard to ISO Standard—Not applicable.Application—This SAE Recommended Practice provides a system for marking thermoset rubber parts to designate the generaly type of material from which the part was fabricated.Reference SectionASTM D 1418—Standard Practice for Rubber and Rubber Latices—NomenclatureISO 1043—1—Plastics—Symbols—Part 1: Basic polymers and their special characteristicsISO 1043—2—Plastics—Symbols—Part 2: Fillers and reinforcing materialsISO 1629—Rubber and latices—NomenclatureISO 11469—Plastics—Generic identification and marking of plastic productsThe Synthetic Rubber ManualVSA 260—German Motor Vehicles—Marking of Parts of Polymeric MaterialsDeveloped by the SAE Committee on Automotive Rubber Specifications。
SAEJ158v001

SAE Technical Standards Board Rules provide that: “This report is published by SAE to advance the state of technical and engineering sciences. The use of this report is entirely voluntary, and its applicability and suitability for any particular use, including any patent infringement arising therefrom, is the sole responsibility of the user.”SAE reviews each technical report at least every five years at which time it may be reaffirmed, revised, or cancelled. SAE invites your written comments and suggestions.QUESTIONS REGARDING THIS DOCUMENT: (412) 772-8512 FAX: (412) 776-0243TO PLACE A DOCUMENT ORDER; (412) 776-4970 FAX: (412) 776-0790SAE WEB ADDRESS 3.Grades—The specified grades, hardness range, and final heat treatment are shown in Table 1.4.Hardness4.1The area or areas on the casting where hardness is to be checked shall be established by agreement between supplier and purchaser.4.2The foundry shall exercise the necessary controls and inspection techniques to insure compliance with the specified hardness range. Brinell hardness shall be determined according to ASTM E10, Test for Brinell Hardness of Metallic Materials, after sufficient material has been removed from the casting surface to insure representative hardness readings. The 10 mm ball and 3000 kg load shall be used unless otherwise agreed upon.5.Microstructure5.1The microstructure of Grade M3210 malleable iron shall consist of temper carbon nodules distributed in a matrix of ferrite. The rim or surface layer (see A.3.3) shall not exceed 127 mm (0.050 in).Unless otherwise specified, the material below the rim can contain some pearlite; however, it shall not exceed the amount shown in Figure 1.5.2The microstructure of the other grades shall consist of temper carbon nodules distributed in a matrix of ferrite and tempered pearlite in air quenched castings and in a matrix of tempered martensite in liquid quenched castings. All grades shall be substantially free of primary graphite or primary cementite.6.Quality Assurance—Sampling plans are a matter of agreement between supplier and purchaser. The supplier shall employ adequate equipment and controls to insure that parts conform to the agreed upon requirements.TABLE 1—GRADES OF MALLEABLE IRONGrade Casting HardnessRange atLocations Shown on DrawingHeat Treatment M3210156 HB max or as agreed (4.8 BID min)AnnealedM4504163–217 HB or as agreed (4.7-4.1 BID)Air quenched and tempered (1)1. Liquid quenching and tempering or alloying may be used to produce this grade if agreed upon between supplier and purchaser.M5003187-241 HB or as agreed (4.4-3.9 BID)Air quenched and tempered (1)M5503187–241 HB or as agreed (4.4-3.9 BID)Liquid quenched and tempered M7002229–269 HB or as agreed (4.0-3.7 BID)Liquid quenched and tempered M8501269–302 HB or as agreed (3.7-3.5 BID)Liquid quenched and temperedN OTE :Brinell impression diameter (BID) is the diameter in millimeters (mm) of the impression of a10mm ball at 3000 kg load.FIGURE 1—REFERENCE PHOTOMICROGRAPH OF ALLOWABLE MAXIMUM PEARLITE IN GRADE M3210 IRON (100X, 2% NIT AL ETCH), TYPICAL MICROSTRUCTURE7.General7.1Castings furnished to this standard shall be representative of good foundry practice and shall conform todimensions and tolerances specified on the casting drawing.7.2Minor imperfections usually not associated with the structural function may occur in castings. Theseimperfections often are repairable; however, repairs shall be made only in areas and by methods approved by the purchaser.7.3Additional casting requirements, such as vendor identification, other casting information, and special testing,may be agreed upon by the purchaser and supplier. These should appear as additional product requirements on the casting drawing.8.Notes8.1Marginal Indicia—The change bar (l) located in the left margin is for the convenience of the user in locatingareas where technical revisions have been made to the previous issue of the report. An (R) symbol to the left of the document title indicates a complete revision of the reportPREPARED BY THE SAE IRON AND STEEL T ECHNICAL COMMITTEE DIVISION 9—AUTOMOTIVE IRON AND STEEL CASTINGSAPPENDIX AMALLEABLE IRON—(A material description not a part of the standard)A.1Definition and Classification—Malleable iron is a cast iron in which the graphite is present as temper carbonnodules, instead of flakes as gray iron or spherulites as in ductile iron.The term malleable iron refers to all grades, including those with a ferritic, pearlitic, tempered pearlitic, or tempered martensitic matrix.A.2Chemical Composition—The chemical composition of malleable iron generally conforms to the followingranges:a.Total Carbon—2.20 to 2.90%b.Silicon—0.90 to 1.90%c.Manganese—0.15 to 1.25%d.Sulfur—0.02 to 0.20%e.Phosphorus—0.02 to 0.10%Individual foundries will produce to narrower ranges than those shown above. The composition is controlled such that the molten iron solidifies with all the carbon in the combined form, producing a "white iron" structure which is heat treated to specifications.A.3MicrostructureA.3.1The microstructure of malleable irons covered in this standard consist of temper carbon nodules in a matrix offerrite, pearlite, tempered pearlite, or tempered martensite or certain combinations of these. The structure of the matrix is controlled by heat treatment and/or composition.A.3.2The matrix of the M3210 grade of malleable iron is essentially ferritic but a small amount of pearlite ispermitted. The matrices of the other grades of malleable iron contain combined carbon as pearlite, tempered pearlite, or tempered martensite.A.3.3Because of reaction with the annealing furnace atmosphere, some depletion of carbon and silicon occurs atthe surface of the castings. This usually results in a rim which, if excessive, can result in poor machinability.The rim on M3210 malleable iron can consist of coarse pearlite underlying a graphite-free layer sometimes containing more or less combined carbon than the underlying material.A.3.4Typical microstructure of the various grades of malleable iron are shown in Figures A1 to A6.FIGURE A1—M3210, APPROXIMA TE 143 HB (100X), TYPICAL MICROSTRUCTUREFIGURE A2—M4504, APPROXIMA TE 207 HB (100X), TYPICAL MICROSTRUCTUREFIGURE A3—M5003, APPROXIMA TE 229 HB (100X), TYPICAL MICROSTRUCTUREFIGURE A4—M5503, APPROXIMA TE 229 HB (100X), TYPICAL MICROSTRUCTUREFIGURE A5—M7002, APPROXIMA TE 262 HB (100X), TYPICAL MICROSTRUCTUREFIGURE A6—M8501, APPROXIMA TE 285 HB (100X), TYPICAL MICROSTRUCTUREA.4Mechanical Properties—The mechanical properties listed in Table A1 are intended as guidelines; but, sinceproperties may vary with location in a given casting, the suitability of a particular metal for an intended use is best determined by laboratory or service tests.The mechanical properties with microstructure and hardness. For optimum mechanical properties, especially in the liquid quenched and tempered grade, section size should generally not exceed 19 mm (3/4 in) to insurea uniform structure.A.5Typical ApplicationsA.5.1M3210 is used where good machinability and ductility are important, such as steering gear housings, carriers,and mounting brackets.A.5.2M4504 is used where slightly higher strength and hardness than M3210 are required, such as certaincompressor crankshafts and hubs.A.5.3M5003 is used where moderate strength and/or selective hardening are required for parts such as planetcarriers, certain transmission gears, and differential cases.A.5.4M5503 is used where better machinability and/or improved response to induction hardening than M5003 arenecessary for parts requiring moderate strength.A.5.5M7002 is used for parts where high strength is required such as connecting rods and universal joint yokes.A.5.6M8501 is used where high strength and/or wear resistance are required, such as certain gears.TABLE A1—TYPICAL MECHANICAL PROPERTIES FOR MALLEABLE IRONSGrade HardnessRange(1)1.Brinell impression diameter (BID) is the diameter in millimeters (mm) of the impression of a 10 mm ball at 3000 kg load.Heat Treatment Tensile Strength,MPa (psi)Yield Strength 0.2% Offset,MPa (psi)Elongation,% In 2 InModulus of Elasticity,106 psi (GPa)M3210156 HB max Annealed3452241025(4.8 BID min)(50 000)(32 000)(172)M4504163–217 HB Airquenched and tempered448310 426(4.7-4.1 BID)(65 000)(45 000)(179)M5003187-241 HB Air517345326(4.4-3.9 BID)quenched and tempered (75 000)(50 000)(179)M5503187–241 HB Liquidquenched and tempered517379 326(4.4-3.9 BID)(75 000)(55 000)(179)M7002229-269 HB Liquid621483226(4.0-3.7 BID)quenched and tempered (90 000)(70 000)(179)M8501269–302 HB Liquidquenched and tempered724586 126(3.7-3.5 BID)(105 000)(85 000)(179)Note:These properties were obtained on separately cast test bars and may vary in various sections of a casting depending on composition and cooling rate.Rationale—Not applicable.Relationship of SAE Standard to ISO Standard—Not applicable.Application—This SAE Standard covers the hardness and microstructural requirements for malleable iron castings - ferritic, pearlitic, tempered pearlitic, and tempered martensitic grades used in automotive and allied industries. Castings shall be heat treated to meet this SAE Standard. The Appendix provides general information on the application of malleable iron castings and their chemical composition to meet hardness, microstructure, and other properties needed for particular service conditions. The mechanical properties in the Appendix are provided for design purposes.Reference SectionASTM E10—Test for Brinell Hardness of Metallic MaterialsASTM STP-455—Gray, Ductile, and Malleable Iron Casting Current CapabilitiesCast Metals Handbook, American Foundrymen’s Society, Des Plaines, ILMalleable Iron Castings, Malleable Founders Society, Cleveland, OHMetals Handbook, Vol. 1, 8th Edition, American Society for Metals, Metals Park, OHModeran Pearlitic Malleable Castings Handbook, Malleable Research and Development Foundation, Dayton, OHH. D. Angus, Physical and Engineering Properties of Cast Iron, British Iron Research Association,Birmingham, England, 1960G .N. J. Gilbert, Engineering Data on Malleable Cast Iron, British Cast Iron Research Association,Birmingham, England, 1968Developed by the SAE Iron and Steel Technical Committee Division 9—Automotive Iron and Steel Castings Sponsored by the SAE Iron and Steel Technical Committee。
SAE J 864用锉刀做表面硬度测试

SAE J 864用锉刀做表面硬度测试前言--此文件的重申被更改只是反应新的SAE技术标准委员会格式。
1.范围--锉刀做的硬度测试基本上包括金属件表面的切削和研磨,且接近触摸的硬度,或扩展到锉刀咬进表面。
“锉刀硬”表示测试的零件表面硬度使新的锉刀无法切削要测试材质的表面。
1.1 适用-- 此SAE操作规程建议描述了用锉刀进行各种铁及钢零件的表面硬度测试技术,作为工程条件。
在呈现此程序时,意识到它是主观的,须由操作员方在有可观的判断下使用。
锉刀硬度测试在表面深度对于传统压痕硬度测试方法来说太浅时,来检测在硬化或表面硬化零件上的软表面状态的出现,或检查压痕硬度测试方法无法预见反应的烧结零件的硬度。
此方法在生产控制中有用。
2.参考--无指定的参考文件。
3.需要仪器3.1 标准锉刀-- 手工锉刀符合以下要求:a.150 或200 mm (6 or或8 in)柱b.No. 1瑞士双线切割c.26切口/cm(66/in)d.锉刀硬度65 - 68 HRC(洛氏硬度)指定No. 6561 - 63 HRC(洛氏硬度)指定No. 6257 - 59 HRC(洛氏硬度)指定No. 5854 - 56 HRC(洛氏硬度)指定No. 5549 - 51 HRC(洛氏硬度)指定No. 50e.化学成分碳-1.20 - 1.40%锰-0.20 - 0.40%磷-0.40%硫-0.05%硅-0.10 - 0.20%3.2标准检验样-标准钢铁或铁试样,直径50 mm (2 in),厚约6 mm (1/4 in),硬化及回火至每个标准锉刀范围的较低限的硬度,是测试标准锉刀的要求。
检验样应用废弃的锉刀锉,去除任何会干扰测试精度的硬质或软质皮层。
硬化到表1内范围且超过中间值的类似检验样可用于证明锉刀可切下且不超过指定的锉刀硬度。
1)用低于65HRC的回火的锉刀不太精确,因此,操作者须对零件做进一步判断,因为锉刀硬度减小。
锉刀测试由测试锉刀通过检验样6 mm (1/4 in)厚表面进行。
SAEJ1086v001

SAE Technical Standards Board Rules provide that: “This report is published by SAE to advance the state of technical and engineering sciences. The use of this report is entirely voluntary, and its applicability and suitability for any particular use, including any patent infringement arising therefrom, is the sole responsibility of the user.”SAE reviews each technical report at least every five years at which time it may be reaffirmed, revised, or cancelled. SAE invites your written comments and suggestions.QUESTIONS REGARDING THIS DOCUMENT: (412) 772-8512 FAX: (412) 776-0243TO PLACE A DOCUMENT ORDER; (412) 776-4970 FAX: (412) 776-0790http:\\Copyright 1995 Society of Automotive Engineers, Inc.2.References2.1Related Publications—The following publications are provided for information purposes only and are not arequired part of this document.2.1.1SAE P UBLICATIONS—Available from SAE, 400 Commonwealth Drive, Warrendale, PA 15096-0001.SAE HS-1086—Metals and Alloys in the Unified Numbering System2.1.2ASTM P UBLICATIONS—Available from ASTM, 100 Barr Harbor Drive, West Conshohocken, PA 19428-2959.ASTM E 527—Practice for Numbering Metals and Alloys (UNS)ASTM Publication No. DS-56—Metals and Alloys and the Unified Numbering System3.Description of Numbers (or Codes) Established for Metals and Alloys3.1The unified numbering system (UNS) establishes 18 series of numbers for metals and alloys, as shown inTable 1. Each UNS number consists of a single letter-prefix followed by five digits. In most cases the letter is suggestive of the family of metals identified, for example, A for aluminum, P for precious metals, S for stainless steels. T able 2 shows the secondary division of some primary series of numbers.3.2Whereas some of the digits in certain of the UNS number groups have special assigned meaning, each seriesis independent of the others in such significance; this practice permits greater flexibility and avoids complicated and lengthy UNS numbers. (See 6.3.)TABLE 1—PRIMARY SERIES OF NUMBERSUNS Series MetalNonferrous metals and alloysA00001-A99999Aluminum and aluminum alloysC00001-C99999Copper and copper alloysE00001-E99999Rare earth and rare earth-like metals and alloys (18 Items, see Table 2)L00001-L99999Low melting metals and alloys (14 Items, see Table 2)M00001-M99999Miscellaneous nonferrous metals and alloys (12 Items, see Table 2)N00001-N99999Nickel and nickel alloysP00001-P99999Precious metals and alloys (8 Items, see Table 2)R00001-R99999Reactive and refractory metals and alloys (14 Items, see Table 2)Z00001-Z99999Zinc and zinc alloysFerrous metals and alloysD00001-D99999Specified mechanical properties steelsF00001-F99999Cast ironsG00001-G99999AISI and SAE carbon and alloy steels (except tool steels)H00001-H99999AISI H-steelsJ00001-J99999Cast steels (except tool steels)K00001-K99999Miscellaneous steels and ferrous alloysS00001-S99999Heat and corrosion resistant (stainless) steelsT00001-T99999Tool steelsWelding filler metalsW00001-W99999Welding filler metals, covered and tubular electrodes, classified by weld deposit composition (seeTable 2)TABLE 2—SECONDARY DIVISION OF SOME SERIES OF NUMBERSUNS SeriesMetalUNS SeriesMetalE00001-E99999 Rare earthand rare earthlike metals and alloys P00001-P99999 Precious metals and alloys E00000-E00999Actinium P00001-P00999Gold E01000-E20999CeriumP01001-P01999Iridium E21000-E45999Mixed rare earths (1)1.Alloys in which the rare earths are used in the ratio of their natural occurrence (that is, unseparated rare earths). In this mixture, cerium is the most abundant of the rare earth elements.P02001-P02999Osmium E46000-E47999Dysprosium P03001-P03999Palladium E48000-E49999Erbium P04001-P04999Platinum E50000-E51999Europium P05001-P05999Rhodium E52000-E55999Gadolinium P06001-P06999Ruthenium E56000-E57999Holmium P07001-P07999SilverE58000-E67999Lanthanum E68000-E68999Lutetium R00001-R99999 Reactive and E69000-E73999Neodymium refractory metals and alloysE74000-E77999Praseodymium E78000-E78999Promethium R01001-R01999Boron E79000-E82999Samarium R02001-R02999Hafnium E83000-E84999Scandium R03001-R03999Molybdenum E85000-E86999T erbium R04001-R04999Niobium (Columbium)E87000-E87999Thulium R05001-R05999T antalum E88000-E89999Ytterbium R06001-R06999Thorium E90000-E99999YttriumR07001-R07999T ungsten R08001-R08999Vanadium F00001-F99999 Cast ironsGray, malleable, pearlitic R10001-R19999Beryllium malleable, and ductile (nodular)R20001-R29999Chromium cast ironsR30001-R39999Cobalt R40001-R49999Rhenium K00001-K99999 Miscellaneous R50001-R59999Titanium steels and ferrous alloys R60001-R69999ZirconiumL00001-L99999 Low-melting W00001-W99999 Welding filler metals and alloys metals, classified by weld L00001-L00999Bismuth deposit composition L01001-L01999Cadmium W00001-W09999Carbon steel with no significant L02001-L02999Cesium alloying elementsL03001-L03999Gallium W10000-W19999Manganese-molybdenum low L04001-L04999Indium alloy steelsL06001-L06999Lithium W20000-W29999Nickel low alloy steels L07001-L07999Mercury W30000-W39999Austenitic stainless steels L08001-L08999Potassium W40000-W49999Ferritic stainless steels L09001-L09999Rubidium W50000-W59999Chromium low alloy steels L10001-L10999Selenium W60000-W69999Copper base alloys L11001-L11999Sodium W70000-W79999Surfacing alloys L13001-L13999Tin W80000-W89999Nickel base alloys L50001-L59999LeadZ00001-Z99999 Zinc and zinc alloysZincM00001-M99999 Miscellaneous nonferrous metals and alloys M00001-M00999Antimony M01001-M01999Arsenic M02001-M02999Barium M03001-M03999Calcium M04001-M04999Germanium M05001-M05999Plutonium M06001-M06999Strontium M07001-M07999T ellurium M08001-M08999Uranium M10001-M19999Magnesium M20001-M29999Manganese M30001-M39999Silicon3.3Wherever feasible, identification "numbers" from existing systems are incorporated into the UNS numbers. Forexample: The carbon steel which is presently identified by "AISI 1020" (American Iron & Steel Institute) is covered by "UNS G10200" and the nickel alloy presently identified by "M252" is covered by "UNS N07252." 3.4Welding filler metals fall into two general categories: those whose compositions are determined by the fillermetal analysis (e.g., solid bare wire or rods and cast rods), and those whose composition is determined by the weld deposit analysis (e.g., covered electrodes, flux-cored and other composite wire electrodes). The latter are assigned to a new primary series with the letter W as shown in Table 1. The solid bare wire and rods continue to be assigned in the established number series according to their composition.(Readers are cautioned not to make their own "assignments" of numbers from such listings, as this can result in unintended and unexpected duplication and conflict.)3.5The ASTM and the SAE periodically publish up-to-date listings of all UNS numbers assigned to specific metalsand alloys, with appropriate reference information on each. (See 6.6.) Many trade associations also publish similar listings related to materials of primary interest to their organizations.anization for Administering Unified Numbering System for Metals and Alloys4.1The organization for administering the UNS consists of: (1) an advisory board, (2) several number-assigningoffices, (3) a corps of volunteer consultants, and (4) staffs at ASTM and SAE. In addition, SAE and ASTM committees dealing with various groups of materials may be consulted.4.1.1The Advisory Board has approximately 20 volunteer members who are affiliated with major producing andusing industries, trade associations, government agencies, and standards societies, and who have extensive experience with identification, classification, and specification of materials. The Board is the administrative arm of SAE and ASTM on all matters pertaining to the UNS. It coordinates thinking on the format of each series of numbers and the administration of each by selected experts. It sets up ground rules for determining eligibility of any material for a UNS number, for requesting such numbers, and for appealing unfavorable rulings. It is the final referee on matters of disagreement between requesters and assigners.4.1.2UNS number assigners for certain materials are set up at trade associations which have successfullyadministered their own numbering systems; for other materials, assigners are located at the offices of SAE and ASTM. Each of these assigners has the responsibility for administering a specific series of numbers, as shown in T able 3. Each considers requests for assignment of new UNS numbers, and informs applicants of the action taken. Trade association UNS number assigners also report immediately to both SAE and ASTM details of each number assignment. ASTM and SAE assigners collaborate with designated consultants when considering requests for assignment of new numbers.4.1.3Consultants are selected by the Advisory Board to provide expert knowledge of a specific field of materials.Since they are utilized primarily by the Board and the SAE and ASTM number assigners, they are not listed in this document. At the request of the ASTM or SAE number assigner, a consultant considers a request fora new number in light of the ground rules established for the material involved, decides whether a newnumber is justified, and informs the ASTM or SAE number assigner accordingly.This utilization of experts (consultants and number assigners) is intended to insure prompt and fair consideration of all requests. It permits each decision to be based on current knowledge of the needs of a specific industry of producers and users.TABLE 3—NUMBER ASSIGNERS AND AREAS OF RESPONSIBILITYThe Aluminum Association Aluminum and aluminum alloys900 19th Street, NW, Suite 30UNS Number Series: A00001-A99999 Washington, DC 20006Telephone: (202) 862-5100American Society for T esting and Materials Rare earth and rare earth-like metals and alloys 100 Barr Harbor Drive UNS Number Series: E00001-E99999West Conshohocken, P A 19428-2959Attention: Office for Unified Numbering System for Metals Cast ironsTelephone: (215) 299-5400UNS Number Series: F00001-F99999Cast steelsUNS Number Series: J00001-J99999Miscellaneous steels and ferrous alloysUNS Number Series: K00001-K99999Low melting metals and alloysUNS Number Series: L00001-L99999Miscellaneous nonferrous metals and alloysUNS Number Series: M00001-M99999Precious metals and alloysUNS Number Series: P00001-P99999American Welding Society Welding filler metals550 N.W. LeJeune Road UNS Number Series: W00001-W99999P.O. Box 351040Miami, FL 33135Attention: Office for Unified Numbering SystemTelephone: (800) 443-9353Fax: 303-443-7559Copper Development Association Copper and copper alloys260 Madison Avenue UNS Number Series: C00001-C99999New Y ork, NY 10016-2401Attention: Office for Unified Numbering System for MetalsTelephone: (212) 251-7200SAE (Society of Automotive Engineers)Carbon and alloy steels400 Commonwealth Drive UNS Number Series: G00001 - G99999 Warrendale, PA 15096-0001Attention: Office for Unified Numbering System for Metals H-steelsTelephone: (412) 776-4841UNS Number Series: H00001-H99999Nickel and nickel alloysUNS Number Series: N00001-N99999Heat and corrosion resistant (stainless) steelsUNS Number Series: S00001 - S99999Tool steelsUNS Number Series: T00001 - T99999Zinc Institute, Inc.Zinc and zinc alloys292 Madison Avenue UNS Number Series: Z00001 - Z99999New Y ork, NY 10017Attention: Office for Unified Numbering System for MetalsTelephone: (212) 578-47504.1.4Staff members at SAE and ASTM maintain duplicate master listings of all UNS numbers assigned.4.1.5Established SAE and ASTM committees which normally deal with standards and specifications for thematerials covered by the UNS, and other knowledgeable persons, are called upon by the Advisory Board for advice when considering appeals from unfavorable rulings in the matter of UNS number assignments.5.Procedure for Requesting Number Assignment to Metals and Alloys Not Already Covered by UNS Num-bers (or Codes)5.1UNS numbers are assigned only to metals and alloys which have a commercial standing (as defined in6.1). 5.2The need for a new number should always be verified by determining from the latest complete listing of alreadyassigned UNS numbers that a usable number is not available. (See 6.4.)5.3For a new UNS number to be assigned, the composition (or other properties, as applicable) must besignificantly different from those of any metal or alloy which has already been assigned a UNS number.5.3.1In the case of metals or alloys that are normally identified or specified by chemical composition, the chemicalcomposition limits must be reported.5.3.2In the case of metals or alloys which are normally identified or specified by mechanical (or other) properties,such properties and limits thereof must be reported. Only those chemical elements and limits, if any, which are significant in defining such materials need be reported.5.4Requests for new numbers shall be submitted on "Application for UNS Number Assignment" forms (Figure 1).Copies of these are available from any UNS number assigning office (Table 3) or facsimiles may be made of the one herein.5.5All instructions on the printed application form should be read carefully and all information provided asindicated. (See 6.5.)5.6To further assist in assigning UNS numbers, the requester is encouraged to suggest a possible UNS number ineach request, giving appropriate consideration to any existing number presently used by a trade association, standards society, producer, or user.5.7Each completed application form shall be sent to the UNS number assigning office having responsibility for theseries of numbers which appears to most closely relate to the material described on the form (Table 3).FIGURE 1A—APPLICATION FORM FOR UNS NUMBER ASIGNMENT (FRONT)FIGURE 1B—APPLICATION FORM FOR UNS NUMBER ASSIGNMENT (BACK)6.Notes6.1The terms "commercial standing," "production usage," and others, are intended to portray a material in activeindustrial use, although the actual amount of such use will depend, among other things, upon the type of materials. (Obviously gold will not be used in the same "tonnages" as hot rolled steel.)Different standardizing groups use different criteria to define the status that a material has to attain before a standard number will be assigned to it. For instance, the American Iron and Steel Institute requires for stainless steels "two or more producers with combined production of 200 tons per year for at least two years";the Copper Development Association requires that the material be "in commercial use (without tonnage limits)"; the Aluminum Association requires that the alloy must be "offered for sale (not necessarily in commercial use)"; the SAE Aerospace Materials Division calls for "repetitive procurement by at least two users."While it is apparent that no hard and fast usage definition can be set up for an all-encompassing system, the UNS numbers are intended to identify metals and alloys that are in more or less regular production and use.A UNS number will not ordinarily be issued for a material which has just been conceived or which is still in onlyexperimental trial.6.2Organizations that issue specifications should report to appropriate UNS number assigning offices (see 4.1.2)any specification changes which affect descriptions shown in published UNS listings.6.3This arrangement of alphanumeric six character numbers is a compromise of the thinking that identificationnumbers should indicate many characteristics of the material, and the thinking that numbers should be short and uncomplicated to be widely accepted and used.6.4In assigning UNS numbers, and consequently in searching complete listings of numbers, the predominantelement of the metal or alloy usually determines the prefix letter of the series to which it is assigned. In certain instances where no one element predominates, arbitrary decisions are made as to what prefix letter to use, depending upon the producing industry and other factors.6.5The application form is designed to serve also as a data input sheet to facilitate processing each requestthrough to final printout of the data on electronic data processing equipment and to minimize transcription errors at number-assigning offices and data processing centers.6.6One such listing is ASTM Publication No. DS-56 and SAE Handbook Supplement HS-1086 (a joint ASTM-SAEpublication).6.7Marginal Indicia—The change bar (l) located in the left margin is for the convenience of the user in locatingareas where technical revisions have been made to the previous issue of the report. An (R) symbol to the left of the document title indicates a complete revision of the report.PREPARED BY THE SAE UNIFIED NUMBERING SYSTEM ADVISORY BOARDRationale—The only change to the document was in Table 3—Copper Development Association’s address changed.Relationship of SAE Standard to ISO Standard—Not applicable.Application—This SAE Recommended Practice describes a unified numbering system (UNS) for metals and alloys which have a "commercial standing" (see 6.1), and covers the procedure by which such numbers are assigned.Section 2 describes the system of alphanumeric designations or "numbers" established for each family of metals and alloys.Section 3 outlines the organization established for administering the system.Section 4 describes the procedure for requesting number assignment to metals and alloys for which UNS numbers have not previously been assigned.The UNS provides a means of correlating many nationally used numbering systems currently administered by societies, trade associations, and individual users and producers of metals and alloys, thereby avoiding confusion caused by use of more than one identification number for the same material;and by the opposite situation of having the same number assigned to two or more entirely different materials. It provides, also, the uniformity necessary for efficient indexing, record keeping, data storage and retrieval, and cross referencing.A UNS number is not in itself a specification, since it establishes no requirements for form, condition,quality, etc. It is a unified identification of metals and alloys for which controlling limits have been established in specifications published elsewhere. (See 6.2.)Reference SectionSAE HS-1086—Metals and Alloys in the Unified Numbering SystemASTM E 527—Practice for Numbering Metals and Alloys (UNS)ASTM Publication No. DS-56—Metals and Alloys and the Unified Numbering SystemDeveloped by the SAE Unified Numbering System Advisory Board。
PS04LTVA1 ESD压Suppressor数据手册说明书

Product featuresPS04LTVA1ESD suppressor•Low trigger voltage and clamping voltage delivers enhanced ESD protection of very sensitive ICs•Ultra-low capacitance (0.05pF typ.) ideal for high speed data applications•Provides ESD protection with fast response time(<1ns) allowing equipment to pass IEC 61000-4-2 level 4 test•Single line, bidirectional device for placement flexibility •Low profile 0402/1005 design for board space savings •Low leakage current (<0.1nA typ.) reduces power consumption•RoHS compliant, halogen free and lead free for global acceptance•Tested to meet automotive specifications (AEC-Q200)PbApplications•Satellite / digital radio •Mobile phones •GSM Modules •HDTV Equipment •A/V Equipment •DMB Modules•Test and measurement equipment•Portable game systems •Personal media playersPackaging•10,000 pieces in paper tape on 7 inch diameter (178mm) reel.Surface Mount Device•Security equipment•Broadband network equipment•Other RF applications •High speed data portso USB 2.0/3.0o IEEE 1394o DVIo High speedethernet1.Per IEC61000-4-2,Level 4 waveform (8kV direct,30A) measured 30nS after initiation of pulse.2.Trigger measurement made using Transmission Line Pulse (TLP) method.3.Minor shifting in characteristics may be observed over multiple ESD pulses at very rapid rate.Device MarkingPS04LTVA1 ESD Suppressors are marked on the tape and reel packages, not individually. Since the product is bi-directional and symmetrical, no orientation marking is required.Design ConsiderationThe location in the circuit for the PS04LTVA has to be carefully determined. For better performance, the device should be placed as close to the signal input as possible and ahead of any other component. Due to the high current associated with an ESD event, it is recommended to use a “0-stub” pad design (pad directly on the signal/data line and second pad directly on common ground).EatonElectronics Division 1000 Eaton Boulevard Cleveland, OH 44122United States/electronics © 2017 EatonAll Rights Reserved Printed in USA Publication No. 4083 BU-SB10613 June 2017Eaton is a registered trademark.All other trademarks are property of their respective owners.Life Support Policy: Eaton does not authorize the use of any of its products for use in life support devices or systems without the express written approval of an officer of the Company. Life support systems are devices which support or sustain life, and whose failure to perform, when properly used in accordance with instructions for use provided in the labeling, can be reasonably expected to result in significant injury to the user.Eaton reserves the right, without notice, to change design or construction of any products and to discontinue or limit distribution of any products. Eaton also reserves the right to change or update, without notice, any technical information contained in this bulletin.Technical Data 4083Effective June 2017PS04LTVA1 ESD suppressorDimensions - mm (in)0.400.70(0.028)Recommended Pad Layout - mm (in)Soldering Recommendations•Compatible with lead and lead-free solder reflow processes •Peak reflow temperatures and durations:-IR Reflow = 260°C max for 10 sec.max -Wave Solder = 260°C max.for 10 sec.max •Recommended IR Reflow Profile:Environmental Specifications:•High Temperature Exposure: MIL-STD-202 Method 108•Temperature Cycling: 1000 Air to Air cycles -40°C to +125°C JESD22 Method JA-104•Moisture Resistance Test: MIL-STD-202 Method 106G, 10 cycles•Biased Humidity: MIL-STD-202 Method 103, 1,000hours +85°C, 85%RH •Thermal Shock: MIL-STD-202, Method 107G Air-to-Air -55°C to +125°C, 10 cycles•Vibration Test and Mechanical Shock Test: MIL-STD-202 Method 204 and Method 213•Resistance to Solvent: MIL-STD-202 Method 215•Operating and Storage Temperature Range: -55°C to +125°C。
- 1、下载文档前请自行甄别文档内容的完整性,平台不提供额外的编辑、内容补充、找答案等附加服务。
- 2、"仅部分预览"的文档,不可在线预览部分如存在完整性等问题,可反馈申请退款(可完整预览的文档不适用该条件!)。
- 3、如文档侵犯您的权益,请联系客服反馈,我们会尽快为您处理(人工客服工作时间:9:00-18:30)。
SAE Technical Standards Board Rules provide that: “This report is published by SAE to advance the state of technical and engineering sciences. The use of this report is entirely voluntary, and its applicability and suitability for any particular use, including any patent infringement arising therefrom, is the sole responsibility of the user.”SAE reviews each technical report at least every five years at which time it may be reaffirmed, revised, or cancelled. SAE invites your written comments and suggestions.QUESTIONS REGARDING THIS DOCUMENT: (724) 772-8512 FAX: (724) 776-0243TO PLACE A DOCUMENT ORDER; (724) 776-4970 FAX: (724) 776-0790SAE WEB ADDRESS SURFACE VEHICLE400 Commonwealth Drive, Warrendale, PA 15096-0001RECOMMENDED PRACTICEAn American National StandardJ864REAF.MAY93Issued 1963-06Reaffirmed1993-05Superseding J864 DEC88SURFACE HARDNESS TESTING WITH FILESForeword—This Reaffirmed Document has been changed only to reflect the new SAE Technical Standards Board Format.1.Scope—Hardness testing with files consists essentially of cutting or abrading the surface of metal parts, and approximating the hardness by the feel, or extent to which, the file bites into the surface. The term "file hard"means that the surface hardness of the parts tested is such that a new file of proven hardness will not cut the surface of the material being tested.1.1Application—This SAE Recommended Practice describes the technique of using a file for testing the surface hardness of miscellaneous iron and steel parts as designated by engineering specifications. In presenting this procedure, it is recognized that it is subjective and that it must be used with considerable judgment on the part of the operator. File hardness tests may be used when case depth is too shallow for conventional indentation hardness methods, to detect the presence of a soft surface condition on hardened or case-hardened parts, or to check the hardness of sintered parts that may not respond predictably to indentation hardness methods.The method is useful in production control.2.References—There are no referenced publications specified herein.3.Apparatus Required3.1Standard Files—Hand files meeting the following requirements:a.150 or 200 mm (6 or 8 in) pillarb.No. 1 Swiss double cutc.26 cuts per cm (66 per in)d.Hardness of File65 to 68 HRC designated No. 6561 to 63 HRC designated No. 6257 to 59 HRC designated No. 5854 to 56 HRC designated No. 5549 to 51 HRC designated No. 50e.Chemical CompositionCarbon—1.20 to 1.40%Manganese—0.20 to 0.40%Phosphorus—0.40% max Sulfur—0.05% max Silicon—0.10 to 0.20%3.2Standard Prover—Standard steel or iron test pieces, 50 mm (2 in) dia and approximately 6 mm (1/4 in) thick,hardened and tempered to the hardness of the lower limit of each standard file range, are required for testing the standard files.The prover shall be filed with a discarded test file to remove any hard or soft skin that will interfere with the accuracy of the test. Similar provers hardened to the ranges in Table 1 and above the medians can be used to prove the file will cut below and not above the designated file hardness.Testing of files is performed by passing the test file across the 6 mm (1/4 in) thick face of the prover.A 6 mm (1/4 in) prover is specified because at the higher hardnesses, the surface area contacted affects the cutting area considerably. Narrow areas can be cut more readily than wide areas due to the concentration of pressure that may be obtained.3.3Standard Test Pieces—Standard test pieces (of the same contour, steel or iron composition, and heat treatment) varying in hardness by small increments, with which the parts being inspected can be compared,are recommended. In the case of steels, each family of SAE steels, namely, 10XX, 20XX, 30XX, and the like should be used. They can be heat treated to compare with the operation, such as carburized, quenched, and temper or carbonitrided, quenched, and temper.These pieces will enable the operator to learn, with fair accuracy, the feel of the file as it cuts, or does not cut,in relation to the Rockwell hardness.Table 1—CHART OF FILES AND PROVERSFile No.Standard ProverHardnessProver Cutting HardnessProver NoncuttingHardnessUntempered6565 HRC63 HRC67 HRCTempered (1)ing tempered files below 65 HRC is less accurate and, therefore, more judg-ment on the part of the operator must be exercised as the hardness of the file decreases.6261 HRC 60 HRC 64 HRC 5857 HRC 56 HRC 60 HRC 5554 HRC 53 HRC 57 HRC 5049 HRC48 HRC52 HRC4.Surface Condition—In testing high surface hardnesses with a file, experience has shown that surfacecondition is important; very smoothly ground surfaces cannot be touched with a file as readily as surfaces that have been filed. Sometimes a testing file will cut a prover of a certain steel at, for example, 64 HRC, yet when the file is applied to a smoothly ground part made of the same steel and at the same hardness, the part feels harder. It is important when comparisons are made that the surface smoothness of the parts being tested be the same as the standard test piece. The standard test pieces can be made in a series of microfinish of 0.5,1.5, 3.2, and 5 µm (20, 60, 125, and 200 µin).On surfaces with a microfinish, the direction of the test filing across or parallel with the finish direction affects results. When filing, the direction of the file in relation to the microfinish should always be the same as the standard test piece.5.Testing Hardness5.1Check file against standard prover.5.2Apply the file to the surface of the part being tested at such an angle that only a few teeth will engage thesurface at once. Use slow, firm strokes in an effort to feel the manner in which the file cuts or does not cut. To prolong the life of the file, use as short a stroke as possible.NOTE—To standardize pressure, attach specimen to a balance scale platform and measure the file effort against specimen in kilograms (pounds). Application should be between 4.5 and 5.5 kg (10 and 12 lb).5.3Compare the parts with a standard test piece with a known hardness range. This will assist in determiningwhether the part falls within the range specified by the engineering specifications. File hardness should not replace conventional methods where penetrators will not break through surface hardened areas.NOTE—During the testing of a batch of parts, the files must not be allowed to become so dull as to cause difficulty in discriminating between parts within specification and those below specification. This canbe prevented by frequent checking against the standard part or prover.5.4The hardness should be specified according to the Rockwell reading of the file as to the surface requirementsof an iron or steel part. The designation should be "file hard - 65" for 65 HRC surface; "file hard - 62" for 62HRC and so on.6.Sources of Test Files6.1Simonds Cutting Tools, Newcomerstown, Ohio. Available through distributors in boxes of 10 files per hardnesslevel.6.2Nicholson Files, Raleigh, North Carolina. Available in minimum quantities of 600.PREPARED BY THE SAE IRON AND STEEL TECHNICAL COMMITTEE 3—TEST PROCEDURESRationale—Not applicable.Relationship of SAE Standard to ISO Standard—Not applicable.Application—Hardness testing with files consists essentially of cutting or abrading the surface of metal parts, and approximating the hardness by the feel, or extent to which, the file bites into the surface. The term "file hard" means that the surface hardness of the parts tested is such that a new file of proven hardness will not cut the surface of the material being tested.Reference Section—There are no referenced publications specified herein.Developed by the SAE Iron and Steel Technical Committee 3—Test ProceduresSponsored by the SAE Iron and Steel Executive Committee。